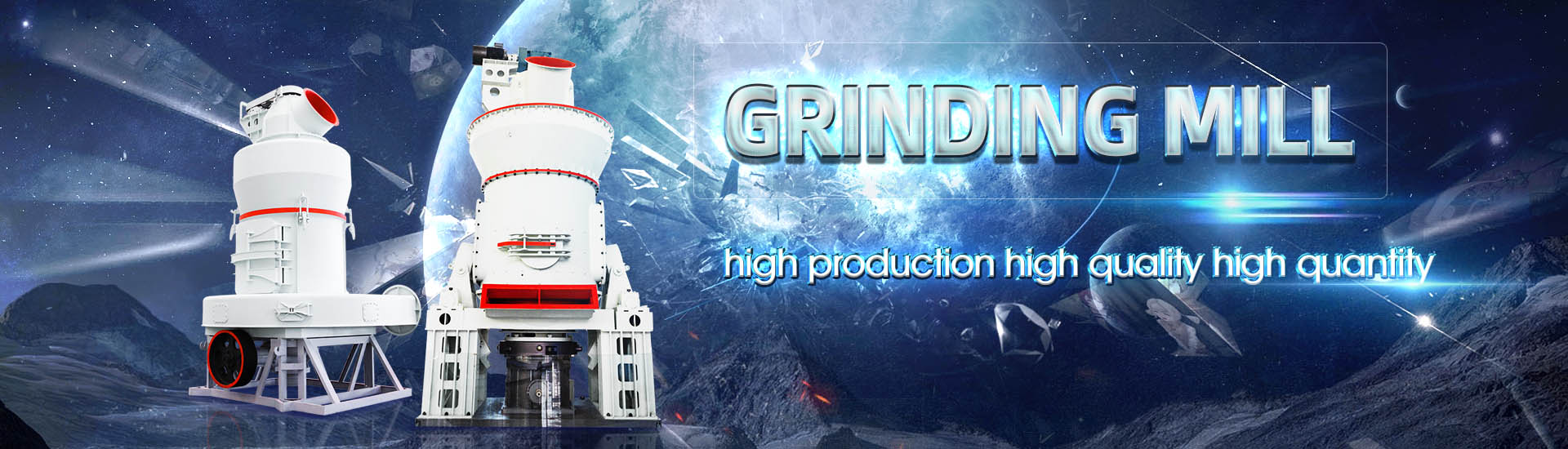
Dry spray coal powder equipment system
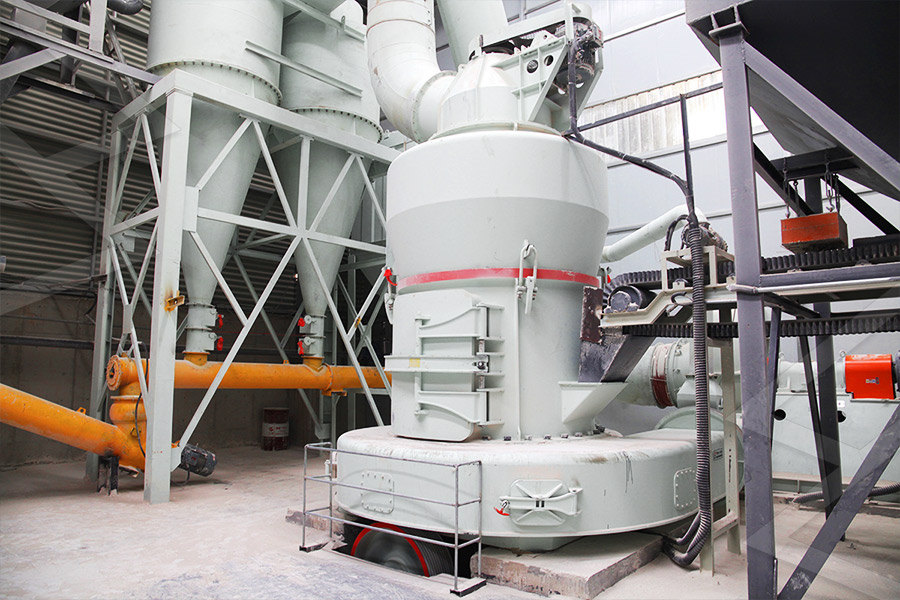
Spray Dryers GEA Dryers Particle Processing Plants
Specialized spray drying solutions for dairy powders, food ingredients, pharmaceuticals, instant coffee and chemicals No one knows more about spray drying than GEA Our expertise has been gained over close to a century, in Powder spray drying without compromise Our conventional NIRO® spray dryer is a costefficient system that is ideal for processing nonagglomerated high bulk density and very fine powders with particle sizes of 5300 μm, dependent on Conventional NIRO® spray dryer GEAProduce a dry powder on the SANOVO spray dryer Spray dry a wide range of proteins on a unique spray drying design 40 years of experience in spray dryingSpray Dryer Powder Processing SANOVOSpray Dryer Absorbers facilitate the removal of acidic pollutants, heavy metals, and dust from flue and offgases at fossilfuelled power plants, waste incinerators and industrial installationsSpray Dryer Absorber (SDA) GEA
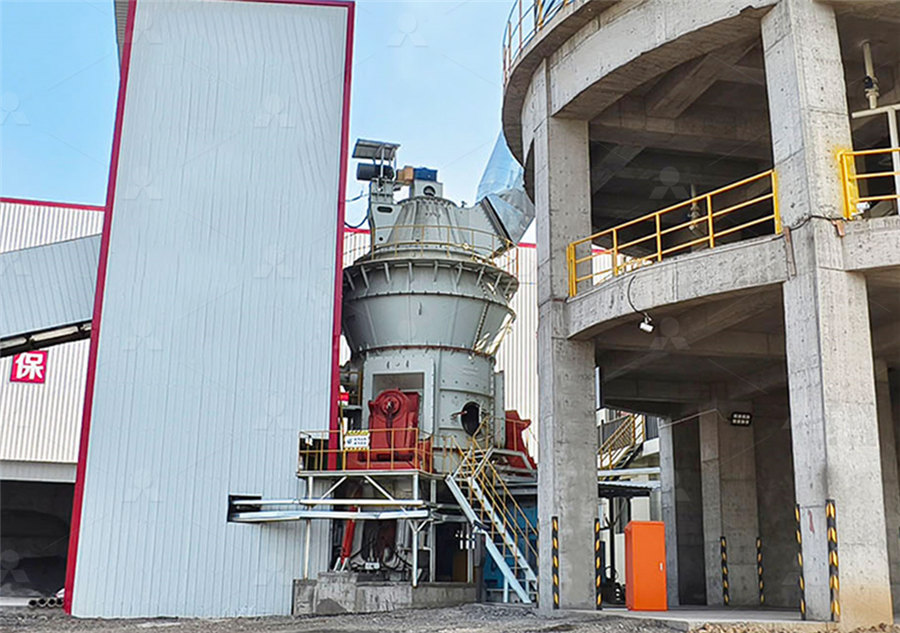
Spray Drying, spray dryer DORST Technologies
Spray drying of viscous suspensions combines efficient granulating by means of atomization with careful drying of the droplets in flight by means of a hot gas atmosphere This procedure enables to produce precisely conditioned powder Hosokawa Micron offers a wide range of innovative drying technologies for batch as well as continuous operations, including vacuum drying, freeze drying and flash drying of products Drying Systems for Powders Bulk Solids Processing Hosokawa One of the main advantages of spray drying is its ability to produce a freeflowing powder that is easy to handle and transport in one processing stage Spray drying itself is not the lowest cost method of production but it can produce a powder Spray Drying: Dryer Types, Advantages and Caloris designs spray dryers for food and beverage production with specific experience in spray and fluid bed dryers, and agglomerators for food dairy applications, as well as engineering application of powder handling, powder About Caloris Spray Drying Caloris Engineering LLC
.jpg)
Spray drying absorption for desulphurization: a review of recent
2021年3月17日 The performance improvement areas in a lime spray drying system include the use of inorganic salt additives, recycling of the dried product and the use of siliceous materials Baldwin OxyDry® electrostatic sprayer systems offer unparalleled performance in dispensing powder for sheetfed, commercial web, flexo, glass and industrial applications Baldwin Technology Industries Printing Corrugated Labels, OxyDry® Spray Powder System Baldwin The installation of the MAC ® system provides an increase in boiler efficiency within the range of 01÷06% (calculated within the framework of ASME PTC4), depending on actual coal properties and ash rates Much of the heat leaving Dry bottom ash handling system MagaldiMax Capacity 1,050 MW Max Inlet SO 2 Concentration 80,000 mg/Nm 3 (Coal fired) Max SO 2 Removal Efficiency 99% High Reliability The flue gas desulfurization (FGD) plant removes sulfur dioxides (SO 2) from flue gas produced by boilers, furnaces, and other sourcesMitsubishi Power effectively contributes to the prevention of air pollution through its wet limestone Mitsubishi Power Flue Gas Desulfurization (FGD) Plants
.jpg)
Air Pollution Control Technology Fact Sheet US EPA
700°F) (FETC, 1996) For spray dry systems, the temperature of the flue gas exiting the absorber must be 10°C to 15°C (20°F to 30°F) above the adiabatic saturation temperature Optimal temperatures for SO 2 removal for dry sorbent injection systems range from 150°C to 180°C (300°F to 350°F) Optimal temperatures for SO 2 removal when the heat source to spray dry FGD wastewater The use of hot flue gas to spray dry liquid feed solutions is a proven technology and is in use in many manufacturing processes Coal fired furnaces generate an excess amount of heat which is not used for electric generation A portion of that heat could be utilized to operate a spray drying systemA Pilot Demonstration of Spray Dryer Evaporation as a Method to 2015年3月15日 Spray dry absorption is the second most popular FGD system worldwide (11%) and mostly used for relatively small to medium capacity boilers using low to medium S (15 wt%) coal [16] In the dry FGD systems ( Fig 2 ), SO 2 reacts with CaO or Ca(OH) 2 sorbent, which is mixed with an excess of water or is slaked to produce lime slurryStatus of Flue Gas Desulphurisation (FGD) systems from coal A spray drying process also presents the advantage to produce a powder whose granulometry can be adjusted within limits and therefore greatly increases the properties and easiness of handling of the dried material if the spray drying system is well tuned, to dry heat sensitive components 3 How does spray drying workSpray drying process : overview, fundamentals of spray drying
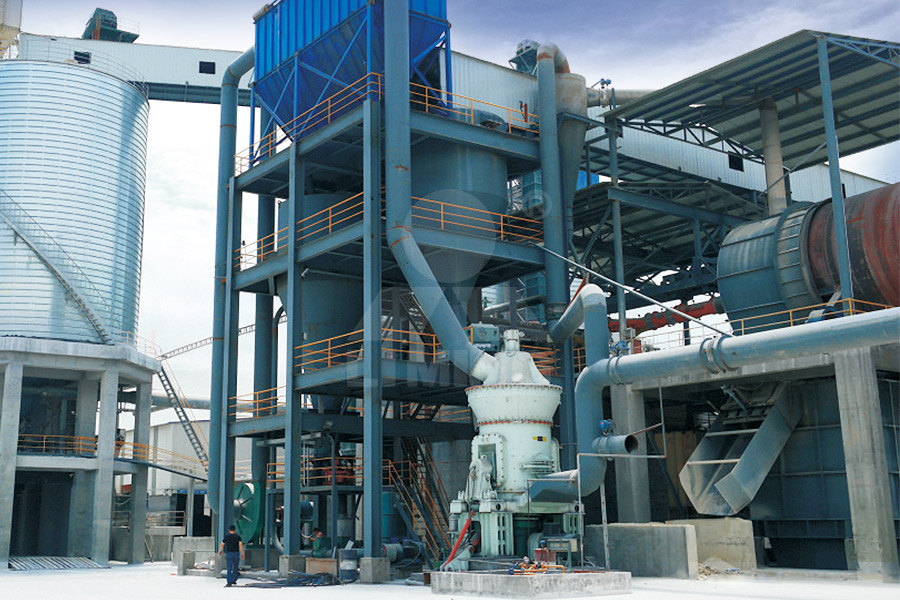
Increasing SO2 Removal Efficiencies in Dry Sorbent Injection Systems
2010年3月31日 By Tom Patnaik William Brown Hosokawa Micron Powder Systems More than half the electric power used in the United States is generated by coalfired power plants, consuming about a billion metric tons of coal a year that emit about a third of the SO 2 gas from all sources As such, the roughly 1500 coalburning power plants are the single biggest 2024年8月15日 Highquality coating machines and industrial spray coating equipment are essential for ensuring that the coating is applied evenly and consistently Additionally, the use of powder coating systems for sale has made it easier for manufacturers to implement powder coating processes inhouse, thereby reducing reliance on thirdparty service providersElectrostatic Coating Systems Powder Coating Equipment1995年1月1日 This amounts to close to 24 percent of the total US coalfired source air pollution monitoring and control systems, equipment and spray dryers and dry injection systemsScrubber myths and realities Power EngineeringSpray dry processes 97–100% of operation reliability, The major system 6 IEA Coal Research Table 2 Environments encountered in the FGD system as shown in Figure 1 (Mathay, 1994; Plant and Mathay, 1999) equipment Other separate support systems include limestoneMaterials for FGD systems ICSC
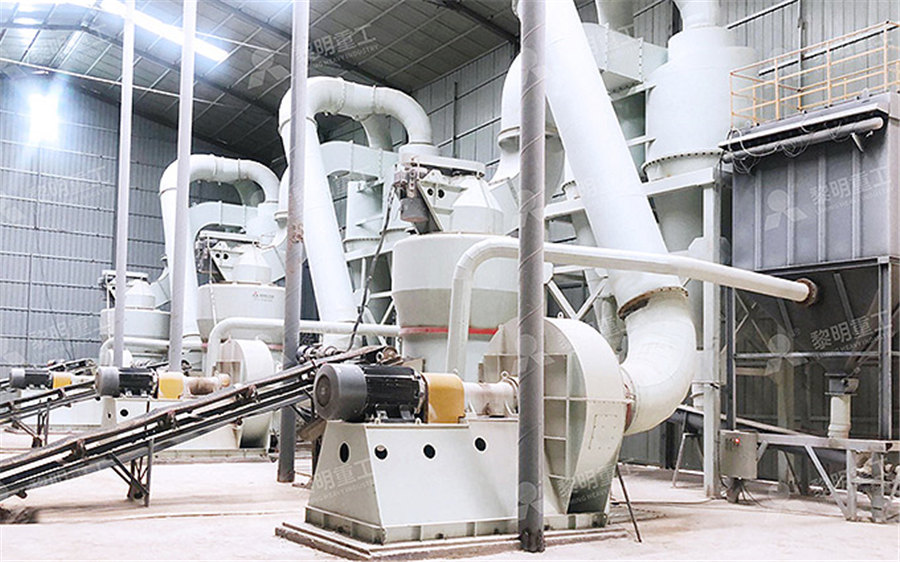
Coalfired power plants equipment machinery
With 230+ systems installed worldwide, Magaldi dry ash conveyor systems have proven to be the Best Available Technology (BAT) for performance and reliability They embody the company's commitment to sustainability and to the 2020年11月21日 Abstract Dust suppression system plays a significant role in mining and allied industries It has become an integral part of the environmental management system Dust emission from mining and mineral processing industries poses environmental and health problems to workers and surrounding people Dust creates a reliability issue in machinery and Intelligent dry fog dust suppression system: an efficient The Spray Drying Absorption process – a semidry flue gas desulphurization and cleaning process – facilitates a reaction efficiently transforming gaseous pollutants such as eg SO 2, SO 3, HCl, Hg, and dioxins into a slaked lime Ca(OH) 2 absorbent to form a stable and dry powdery product that is easy to store and transport Every Spray Drying Absorption process is tailored Spray Dryer Absorber (SDA) GEAA CFBS can keep solids in the system from 20 to 30 minutes This is a sufficient period of time for the sorbent to react with the acid gases Two independent control systems maintain the dry flue gas at optimum temperature and at adequate removal efficiency by controlling the amount of water added and the amount of fresh sorbent added separatelyCirculating fluidized bed scrubber vs spray dryer absorber
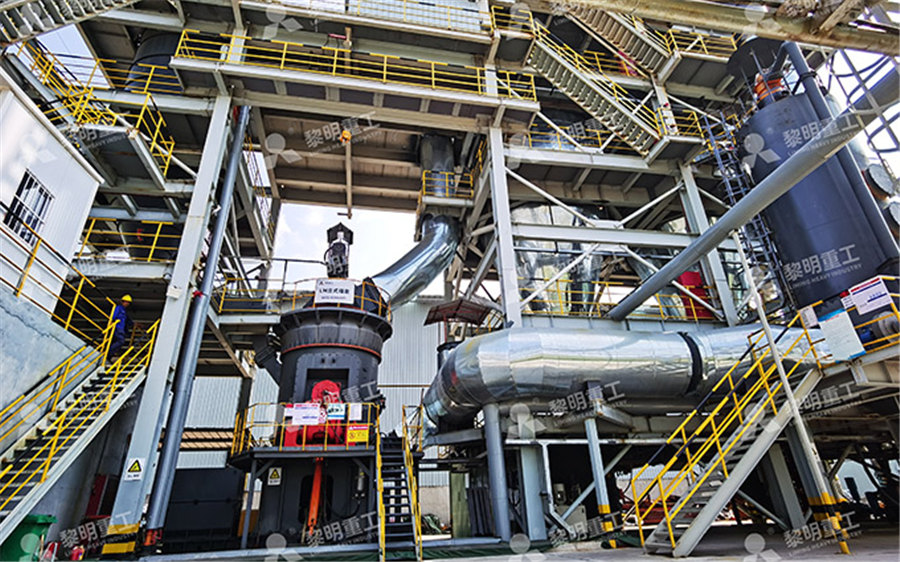
COOLING TECHNIQUES AT ESKOM POWER STATIONS
Three types of cooling systems are employed at Eskom’s power plants The most common and older type is wet cooling, but there are also direct and indirect dry cooling systems Before we discuss cooling systems, we must understand why there is a need for cooling What do we cool? The turbines at coal fired power stations are steam drivenThe Kidde Fire Systems IND Dry Chemical System provides 24hour fire protection for a wide variety of industrial processes, equipment, machinery and paint spray booth applications The IND Dry Chemical system offers the choice of two dry chemical agents effective on Class A, IND™ Dry Chemical Fire System Kidde Fire Systems2015年3月9日 Reliant's powder coating equipment includes blast booths pots, spray booths, coating curing ovens Reliant Finishing Systems has thousands of powder coating equipment systems across the United States and around They provide optimal manual cleaning and phosphatizing by applying chemistry in a jet of wet or dry steamPowder Coating Equipment Reliant Finishing SystemsHighvelocity water spray systems are used for the protection of fire hazards at transformers, circuit breakers, turboalternators, lube oil systems, oilfired boilers and similar hazards that contain heavy oils/flammable liquids (flash point above 65C) Medium Velocity water spray systems are used in flammable liquid (flash point below 65C) and paint storage areas, EMACO Water Spray Fixed System For Fire Protection
.jpg)
Dry Polymer MakeDown Systems Clearwater Industries, Inc
Dry polymer systems require smart simplicity for limited operator requirements and efficient polymer preparation We achieve this with a few standard features on our MSeries line First, our dry polymer feed systems automatically introduce the polymer granules to maintain a programmed solution strengthApplication: LPG and LNG Working Pressure: 10~16Mpa Dry Chemical Powder Tank: 500~10000L Opening Ways: Pneumatic or Manual Driven Gas: N2 Volume of N2 Bottle: 4/40/50/68L Certificate: CCS,BV,RINAMarine Fixed Dry Chemical Powder System Pros Spray Dry Flue Gas Desulfurization Systems Proven spray drying absorption process reliably provides SO 2 • Powder River Basin (PRB) coal • Lignite • Bituminous coal system and integration with existing or new emissions control equipmentSpray Dry Flue Gas Desulfurization SystemsHeat sources range from steam, thermic oil, electric, gas, liquid fuel burner systems and coalfired fluid bed combustors All equipment is tailor designed to suit the processing requirements Materials processed: copper or nickel sulphide slurries, ironbased catalysts, pigments, milk, coffee creamer, coffee, washing soap detergents, caramel, cheeses, spirulina to name a fewSpray Dryers DryTech International
.jpg)
Dry Scrubber an overview ScienceDirect Topics
Combustion fundamentals and energy systems YenHsiung Kiang, in Fuel Property Estimation and Combustion Process Characterization, 2018 9132 Dry Scrubber The dry scrubber system consists of a dry absorber chamber, a bag house filter, a regent feeding tank, a reagent feeding system, and a fly ash discharge system The reagents used are normally dry hydrated lime 2011年11月1日 WFGD can be effective in removing SO 2 from any coalfired unit, but a heretofore ruleofthumb guideline suggests that circulating dry scrubbers are limited to a maximum SO 2 concentration of up Circulating Dry Scrubbers: A New Wave in FGD? Power Engineering2022年4月12日 Conclusion Implementing a wellstructured maintenance schedule is vital for the smooth operation and longevity of your powder coating plant By focusing on preventive and predictive maintenance, documenting activities, and involving your team, you can reduce downtime, improve efficiency, and maintain highquality production standardsAutomatic Powder Coating Equipment Industrial Spray SystemDry mist dust suppression system Mattel Spray's dry mist system is highly stable and modular The core of the system lies in our high quality nozzle ultrasonic air atomizing nozzle, which is also what we usually call dry fog generator Through research and experimentation, Mattel spray designs the optimal mechanical resonator, also known as the ultrasonic oscillatorDry Fog Mist System For Dust Control Suppression Mistec Spray
.jpg)
NonRecovery Spray Booths Powder Coating Booths Spray Systems
These powder coating booths are designed with a 3Stage Filter System that captures the powder overspray, allowing clean air to recirculate back into your plant This eliminates the need for exhaust stack with expensive air replacement systems NonRecovery Powder Booths are ideal for “spray to waste” batch operationsThe vast majority of spray booths in the industrial manufacturing industry utilize dry exhaust filtration systems, which are less expensive than water wash systems Water wash booths trap paint overspray with curtains of water and deposit them into a collection tank, which must be cleaned of sludge periodicallyDifference between Water Wash and Dry Filter Systems Spray SystemsPDF On May 2, 2018, Daniel Santos and others published Spray Drying: An Overview Find, read and cite all the research you need on ResearchGate(PDF) Spray Drying: An Overview ResearchGateYes! Caloris has technical experience with spray dryers (Niro, DeLaval, Damrow , Filtermat brand), tall form spray dryers, multistage spray dryers, falling film evaporators (MVR TVR), retail powder packaging lines, (Colby Albro), About Caloris Spray Drying Caloris Engineering LLC
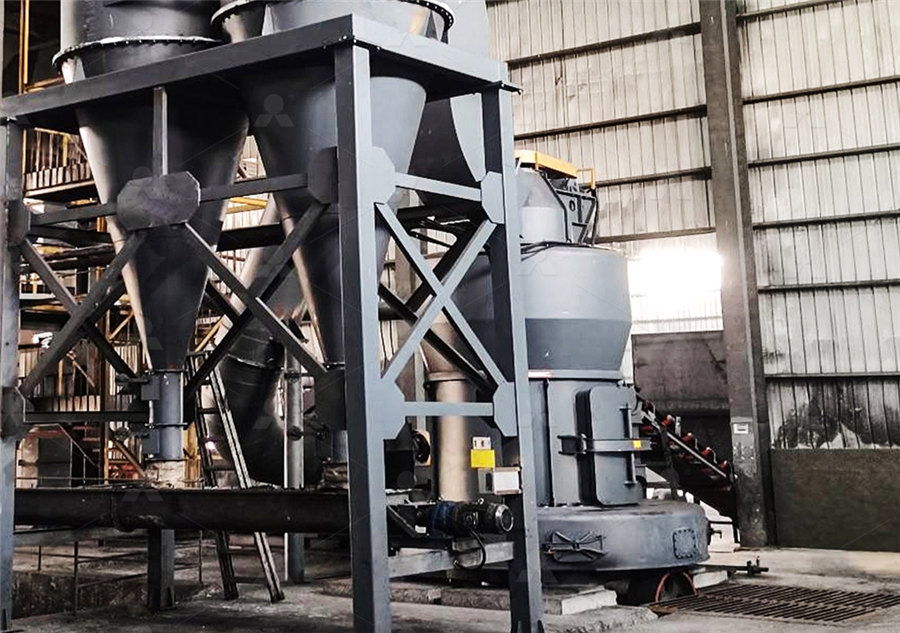
Section 5 SO and Acid Gas Controls US Environmental
the capital and operating costs for wet and dry/semidry FGD systems Section 13 focuses on wet packed tower scrubbers and presents a detailed methodology for determining the design parameters and estimating the capital and operating costs for typicalThey employ dry chemical powder to extinguish fires, with commonly used powders including: Sodium bicarbonate; Potassium bicarbonate; Monoammonium phosphate; Urea complex; Their primary drawback is the considerable powder discharge at the hazard site, necessitating cleanup However, this minor inconvenience pales in comparison to the life Fire Safety with NFPA 17 Dry Chemical Extinguishing Systems2018年8月6日 Though Dry Fork is fueled by lowsulfur Powder River Basin (PRB) subbituminous coal, sourced from the Dry Fork Mine via a conveyer system just a mile away, its emissions of major pollutants fall way below federal and state requirements It consumes little water and is a zeroliquid discharge facilityUSA: Dry Fork: A Model of Modern US Coal Power ICSC2022年1月19日 Experimental study on the treatment of desulfurization wastewater from coalfired power plant by spray evaporation January 2022 DOI: 1021203/rs3rs/v1(PDF) Experimental study on the treatment of ResearchGate
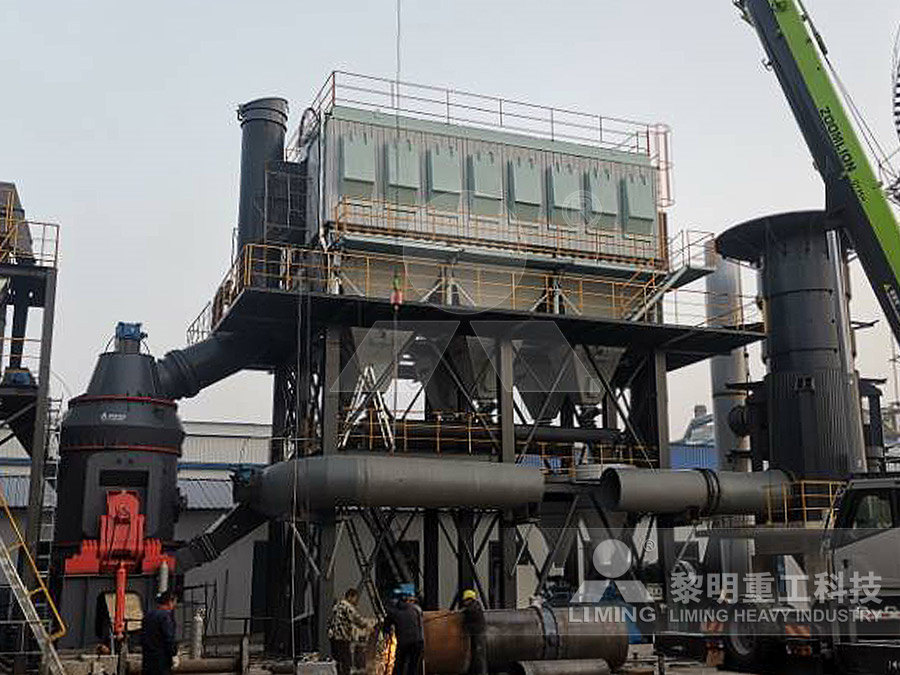
Detergent Spray Drying Tower: A Complete Production Solution
The most reliable way to produce such lightweight puffed detergent powder is a spray drying process Compared to Dry Mixing and Agglomeration processes, Spray Drying delivers a superior outcome Besides weight, the spraydried detergent powder is almost perfectly dehydrated, which prevents agglomeration and caking of the final productAlthough all spray systems need equipment to collect overspray, one of the benefits of a powder system is the ability to reclaim and reuse oversprayed powder In a nonrecovery powder booth or a spraytowaste system , the powder is simply collected for disposal —colors are intermixed and the powder cannot be reusedKey Decisions for Powder Coatings: Batch or Spray Systems, IncThe FlueGas Desulfurization (FGD) process utilizes a set of technologies to remove sulfur dioxide (SO 2) from the flue gas emissions of coalfired power plantsFGD systems were developed as a response to the exhaust – flue gases – from fossil fuelburning plants, principally coalburning, that posed both an environmental and human health hazardThe Flue Gas Desulfurization Process Micronics Engineered What Is Air Swept Coal Mill The airswept coal mill is also called a coal grinder It is the main equipment of the cement plant, used for drying and pulverizing coal powderIt mainly consists of the feeding device, main bearing, rotary part, transmission device, discharging device, highpressure starting device, and lubrication systemAir Swept Coal Mill Coal Mill In Cement Plant AGICO GROUP
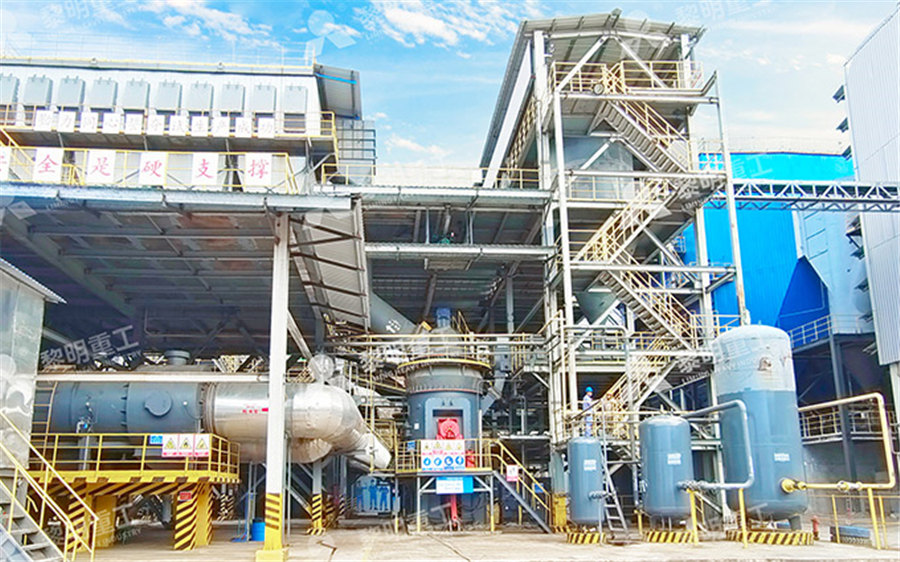
Multiobjective optimization of milk powder spray drying system
2022年10月1日 The research is innovative in three aspects compared with the previous research on the performance optimization of milk powder equipment: (1) A multiobjective optimization model of the MPSD system is raised, and the optimal parameters of the system are determined in terms of the conflict between the environmental performance, economic