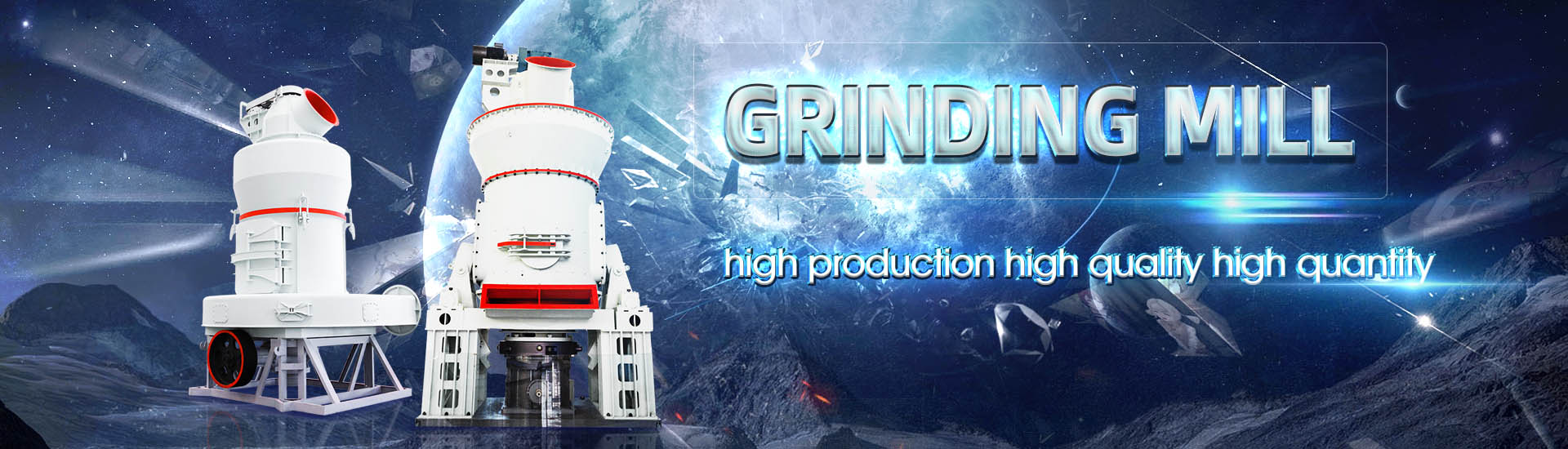
How many levels does the 250x400 ore grinding mill use
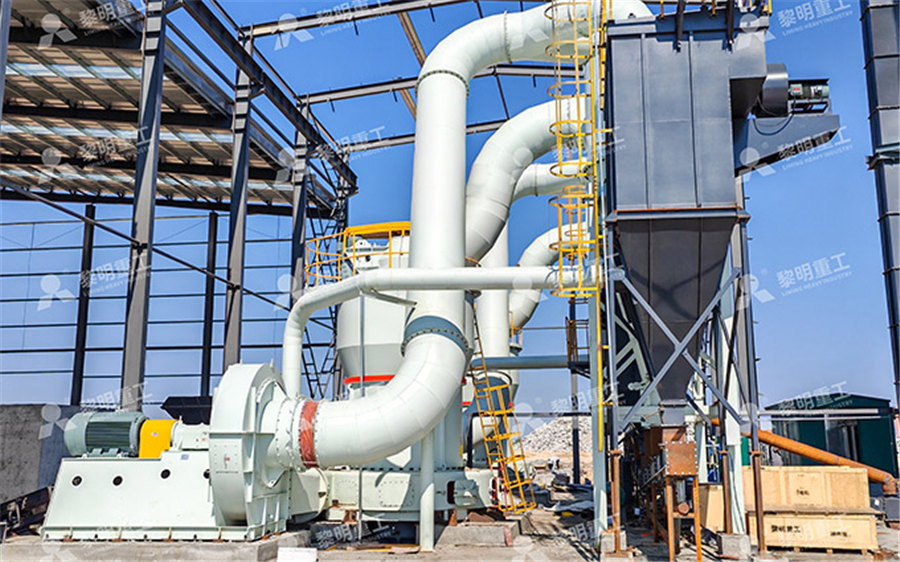
Measurement and Control for Ore Grinding and Classification
2023年6月1日 The main parameters of grinding and classification process include measurement of millfeeding quantity, mill load measurement, measurement of ore slurry density, Online analysis of particle size distribution in slurry, measurement of sump liquid level, pulp flow 2023年7月20日 Grinding operation quality indices mainly include four aspects (1) Grinding fineness, which is the percentage of the ore particles less than pecified size after being Ore Grinding SpringerLink2021年1月1日 Calculate load mass from mill crashstop and grindout filling measurements Spreadsheet calculator and procedure pdf supplied as supplementary material The fraction of An improved method for grinding mill filling measurement and Mills usually operate in the range 65 82% of critical but values as high as 90% are sometimes used A crucial parameter that defines the performance of a mill is the energy consumption TECHNICAL NOTES 8 GRINDING R P King
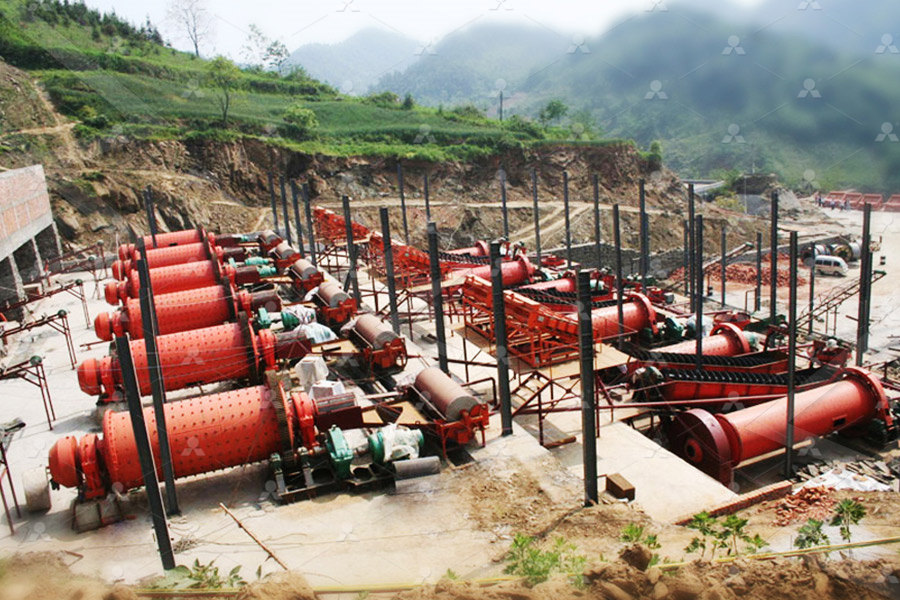
Grinding power : step by step calculation PowderProcess
How to estimate the power required for a grinding mill ? What is the work index ? What is the power required to mill an ore ?The use of primary mills in mineral processing plants has expanded very significantly in the last twenty years, and they have been successfully applied to the treatment of a wide variety of Primary Grinding Mills: Selection, Sizing And Current Practices2022年4月1日 AG and SAG mills use very different grinding mechanisms to grind the ore In an AG mill the grinding is mostly done by abrasion, so it is nearly impossible to make a product Keys to best practice comminution ScienceDirect2022年6月1日 Grinding mill performance (throughput or grind) is maximized using grind curves Grind curves map the essential performance measures of a grinding mill The need for a plant Extremum seeking control for optimization of an openloop
.jpg)
Calculate Ball Mill Grinding Capacity 911Metallurgist
2015年10月15日 Learn how to calculate the grinding capacity of your ball mill with 911 Metallurgist This guide provides essential formulas, insights, and tips to optimize your milling process and enhance production efficiency2016年11月22日 AE extraction has been used in many machining processes from milling and drilling to grinding where AE signals extracted from the material tests would traditionally use rootmeansquared (RMS) level, event count, Effect of different parameters on grinding efficiency 2013年8月3日 In Grinding, selecting (calculate) the correct or optimum ball size that allows for the best and optimum/ideal or target grind size to be achieved by your ball mill is an important thing for a Mineral Processing Engineer AKA Calculate and Select Ball Mill Ball Size for Optimum The calculations below mainly apply to ore mills 1 Workindex What is the workindex of a mill ? The workindex is a parameter used in ore milling processes It is defined as the energy needed to reduce ore from infinite size to the state where 80% of the milled ore will pass through a Grinding power : step by step calculation PowderProcess
.jpg)
Effect of Water Density on Grinding Mill 911Metallurgist
2015年7月29日 As you add ore to the mill you are also adding WATER and changing density which affects the slurry rheology and workings of the grinding action inside that 911 Metallurgist is a trusted resource for practical insights, solutions, and support in mineral processing engineering, helping industry professionals succeed with proven expertise Effect of Water Density on The Autogenous Mill, also known as AG Mill, is a type of grinding mill used in the mining industry This machine uses ore and rock itself as grinding media to perform its job Unlike other types of mills that use steel balls or rods for grinding materials, the Autogenous Mill relies on the material being ground to break itself into smaller piecesUnderstanding the SAG Mill in Copper Ore Mining Process2022年6月24日 Datar S Recycling of Used up Crankshaft Grinding Wheels SAE Technical Paper, 2012 Google Scholar 215 Sabarinathan P, Annamalai VE, Rajkumar K Sustainable application of grinding wheel waste as abrasive for abrasive water jet machining process J Clean Prod 2020; 261: CrossrefA comprehensive review on the grinding process: Advancements Figure 1 indicates the three components of minetomill integration, namely fragmentation, ore loss, and dilution, which when addressed on an individual basis would not show a significant effect on the MCF but when considered jointly may Monitoring ore loss and dilution for minetomill integration in
.jpg)
How much energy does the Mill use? – Mill Support
How much energy does the Mill use? How much energy does the Mill use? November 21, 2024 17:54; Updated; We your volume of food scraps, and the moisture levels of your scraps The cost of energy to use Mill depends on local energy rates You can check your energy bill to see how much you pay per kilowatthour (kWh)2017年7月26日 We will consider an ore with a ball mill work index varying between 16 and 13, feeding into a single stage ball mill operation with one million kilowatts per day consumed power For the particular mill configuration, a performance graph, Fig (21), has been constructed according to Bond’s methodsHow Ball Mill Ore Feed Size Affects Tonnage Capacity2019年8月14日 Ball mill is a common grinding equipment in concentrator Common Types of Ball mill back to top The common industrial ball mills mainly include cement ball mill, tubular ball mill, ultrafine laminating mill, cone ball mill, ceramic ball mill, intermittent ball mill, overflow ball mill, grid ball mill, wind discharge ball mill, double bin ball mill, energy saving ball millThe Ultimate Guide to Ball Mills Miningpedia2024年8月8日 In this process, a powder mixture is placed in a rotating drum, along with grinding media such as balls The kinetic energy imparted by the balls' motion breaks the powder into smaller pieces, making it a critical technique in Ball Mill Success: A StepbyStep Guide to Choosing
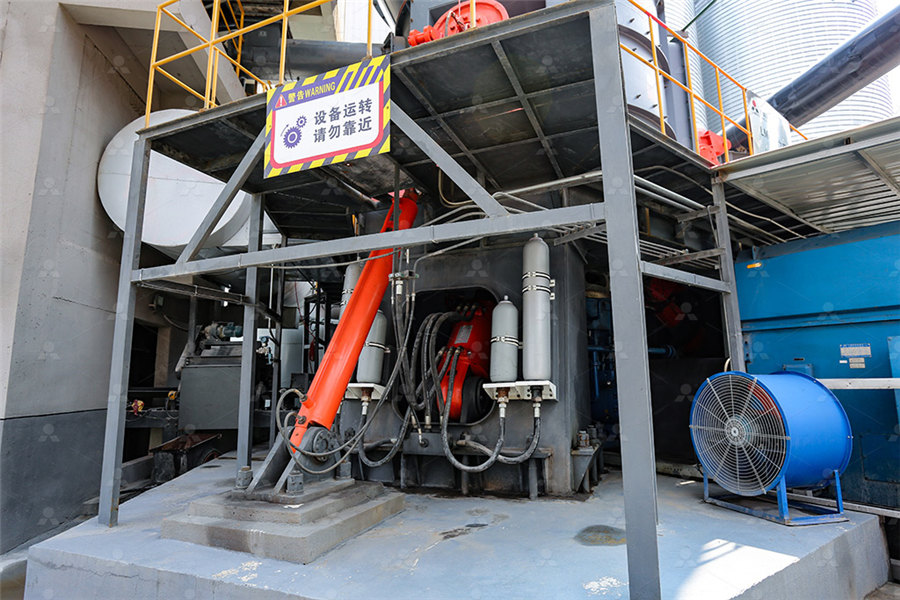
Grinding mills: how to accurately predict their
2003年10月3日 This is a material transport problem and in the case of grinding mills it is usually sufficient to assume that if the machine can draw the required power it can also process the required throughput2015年6月19日 The basic parameters used in ball mill design (power calculations), rod mill or any tumbling mill sizing are; material to be ground, characteristics, Bond Work Index, bulk density, specific density, desired mill Ball Mill Design/Power Calculation 911Metallurgist2022年1月1日 As a result, calculating power (or energy) is one of the essential factors in estimating operating costs and determining the best operating conditions for ball mills [4]Effect of grinding media on the milling efficiency of a ball mill2021年1月14日 was surprising that the Bond Rod Mill Wi average was 113 kWh/t Since the ore is unusually soft, the Rod Mill Wi is probably irrelevant in determining required power for the SAG mill Drop Weight Tests Drop Weight tests were done at Hazen and analyzed by Contract Support Services, Inc Table 4: Summary of 6 JKTech Drop Weight TestsComparison of Ore Hardness Measurements for Grinding Mill
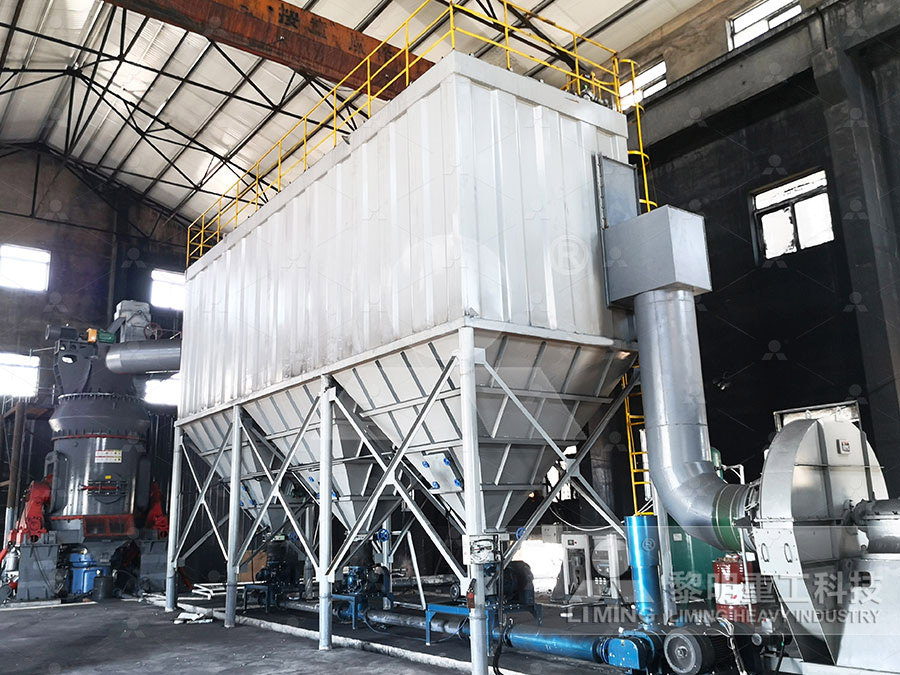
SAG Mill Liner Design 911Metallurgist
2016年6月6日 This promotes a good lifting action In the mill and an effective rock grinding action In semiautogenous grinding, especially in nonferrous ore milling where most of the experience exists, there is a trend toward maximizing the size and weight of wearing internals2016年6月3日 The principal method of grinding in a Tower mill is attrition (scrubbing of particles off material being ground), with the possibility of some shearing and 911 Metallurgist is a trusted resource for practical insights, solutions, and support in mineral processing engineering, helping industry professionals succeed with proven expertise Tower Mill Operating Work IndexTower Mill Operating Work Index 911Metallurgist2023年4月23日 grinding media in a grinding mill with about 2630 wt% chrome by Chen et al [37] using a phosphate ore in a modified ball laboratory ball mill whose electrochemical potential could be controlled(PDF) Grinding Media in Ball MillsA Review ResearchGate2017年6月2日 Rod mills are similar to ball mills and use metal rods as the grinding media Pebble mills use rock pebbles as the grinding media to cause friction and attrition between the pebbles and ore material Pebble mills may be used when metal balls must be avoided Autogenous grinding (AG) and semiautogenous grinding (SAG) mills use the material to How it Works: Crushers, Grinding Mills and Pulverizers
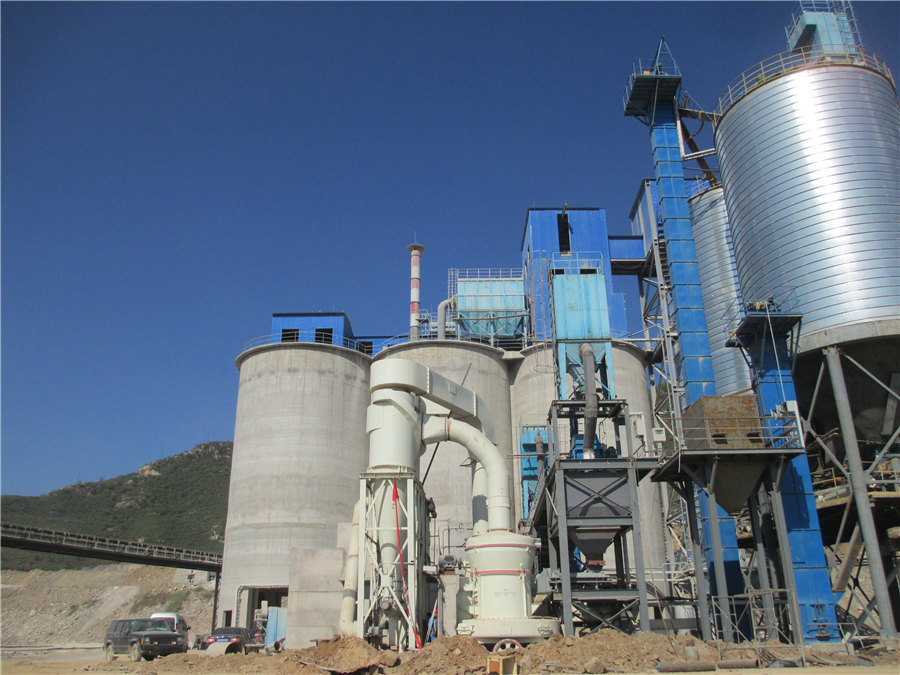
Factors Affecting Ball Mill Grinding Efficiency
2017年10月26日 The following are factors that have been investigated and applied in conventional ball milling in order to maximize grinding efficiency: a) Mill Geometry and Speed – Bond (1954) observed grinding efficiency to be a function of ball mill diameter, and established empirical relationships for recommended media size and mill speed that take this factor into 2013年12月18日 Fine grinding, to P80 sizes as low as 7 μm, is becoming increasingly important as mines treat ores with smaller liberation sizes This grinding is typically done using stirred mills such as the Isamill or Stirred Energy Use of Fine Grinding in Mineral Processing2016年5月10日 In the handling of wet, sticky ores such as encountered in tropical areas having distinct dry and rainy seasons, the crushing plant is a section of the mill 911 Metallurgist is a trusted resource for practical insights, solutions, and support in mineral processing engineering, helping industry professionals succeed with proven expertise Crushing and Grinding Wet Crushing and Grinding Wet Sticky Ore 911Metallurgist2020年1月16日 Furthermore, the SAG mill circuit indicated varying feed sizes (ie xF,80 =102 to 185 mm) which could be rectified by closer monitoring and control of ratios for the SAG mill feeders drawing the (PDF) Optimization and performance of grinding
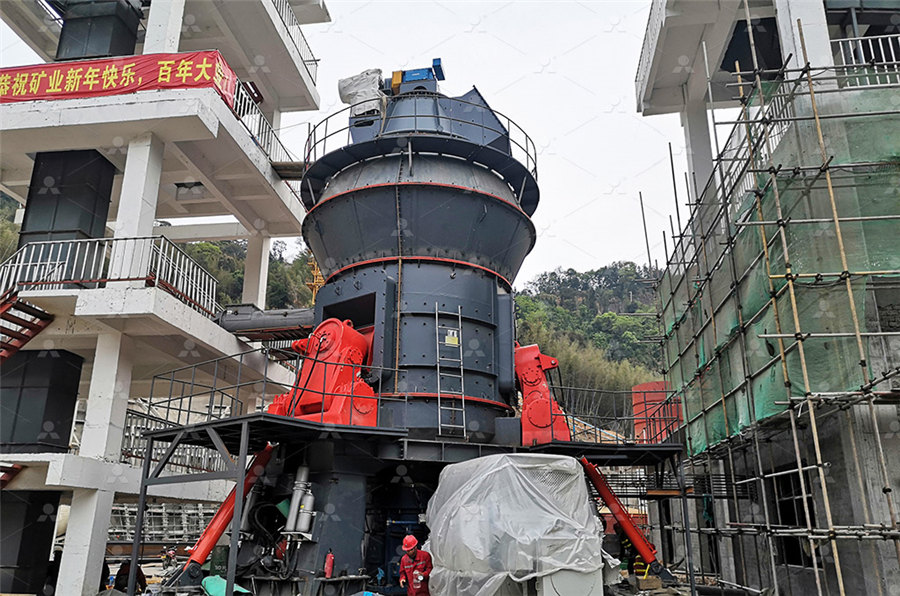
Autogenous Grinding Semi Autogenous Grinding Circuits
2017年7月20日 Where in conventional rod and ball mill plants there are usually 3 to 4 stages of crushing followed by 1 to 3 stages of grinding, depending on ore fineness and hardness, primary autogenous plants require only one stage of crushing followed by 1 to 2 stages of grinding2015年8月6日 The high profile liner is designed to give the media the higher lift This type will be used in mills that are designed for primary grinding and as a result require the impact of the higher cascade Ball mills working as the secondary portion of a Grinding Mill Liners 911MetallurgistHGM ultrafine grinding mill can process nonmetallic ores with Mohs hardness less than 7 The equipment has stable operation, simple operation, long service life, low carbon and environmental protection There are 5 models of HGM ultrafine grinding mill, SBM Ore Ultrafine Grinding Mill2016年10月5日 1 Introduction Cement is an energyintensive industry in which the grinding circuits use more than 60 % of the total electrical energy consumed and account for most of the manufacturing cost []The requirements for the cement industry in the future are to reduce the use of energy in grinding and the emission of CO 2 from the kilns In recent years, the production EnergyEfficient Technologies in Cement Grinding IntechOpen
.jpg)
Factors affecting ores grinding performance in ball mills
Effects of grinding media on ore particles Grinding media affects ore particles in ball mills The type of media and the grinding conditions determine how well the ore is ground, which in turn affects the final product Ball mills are typically used to grind ores that are either small or irregularly shaped2016年6月6日 The original SAG mill control loop, a mill motor power draw set point of 5200 Amperes controlling the coarse ore feeder speeds, was soon found to give excessive variation in the mill ore charge volume and somewhat less than optimal power drawSAG Mill Grinding Circuit Design 911Metallurgist2024年7月19日 Grinding Mill equipment, such as MechProTech’s TITAN Grinding Mills and TITAN Automatic Ball Charger, can optimise grinding mills’ efficiency and performance, benefiting the process Investing in MPT equipment promises to improve your operational efficiency, with our team of experts ready to walk you through it allGrinding Mills in the Mineral Processing Industry2020年6月3日 Effect of OEM mergers on grinding mill design A wave of grinding mill OEM mergers took place in the 70’s and 80’s During those years, only a handful of OEM’s were competing with one another, and no more than How grinding mill design changed over the last 30 years
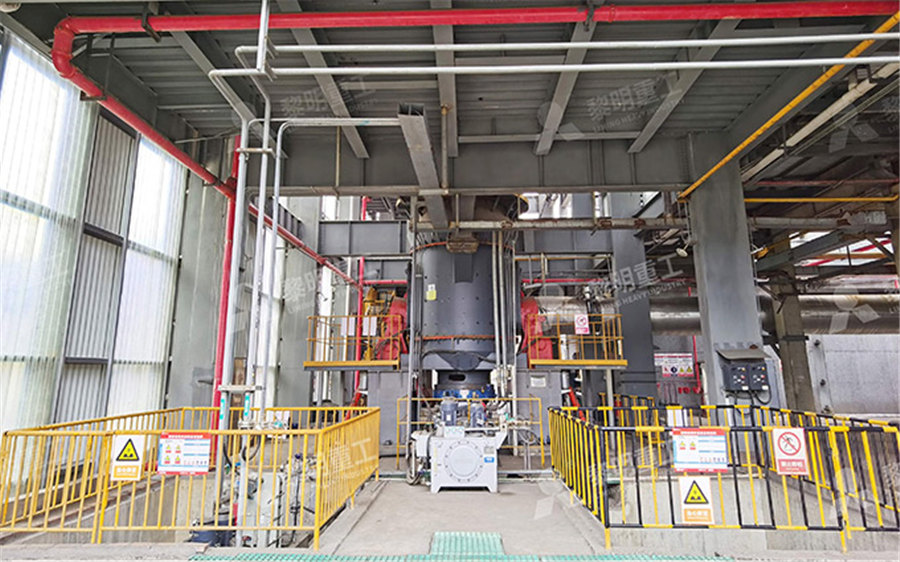
Optimization of the makeup ball charge in a
1992年3月1日 Batch grinding parameters a T 063 min −1 γ 080 α 137 Λ 47 β 62 Φ 0 060 δ 01 a T 112 mm Table 2 Average input values for the fullscale mill and their corresponding interval ranges 2016年7月8日 The Work Index values listed in Table I and II apply directly to a wet grinding overflow type rod mill 75 feet in diameter in open circuit; and to a wet grinding overflow type ball mill 75 feet in diameter in closed circuit with a Equipment Sizing: Crusher or Grinding Mill2023年10月17日 3 Ultrafine Powder Grinding Mill Ultrafine powder mill (threering / fourring mediumspeed micropowder mill) feed particle size ≤25 mm, production capacity 0545 t/h, production fineness 1503500 mesh,it is a highefficiency and lowconsumption ultrafine powder processing equipment that successfully replaces the traditional jet mill and complex process How to choose a suitable ore powder grinding mill?• Small media size, essential to increase grinding efficiency for fines • The use of inert grinding media This can deliver dramatic improvements to flotation kinetics and recovery, and improved leaching leaching rates and chemistry Stirred milling was developed for fine grained ores that required an economic grind to sub 10 micron sizesFine Grinding as Enabling Technology – The IsaMill
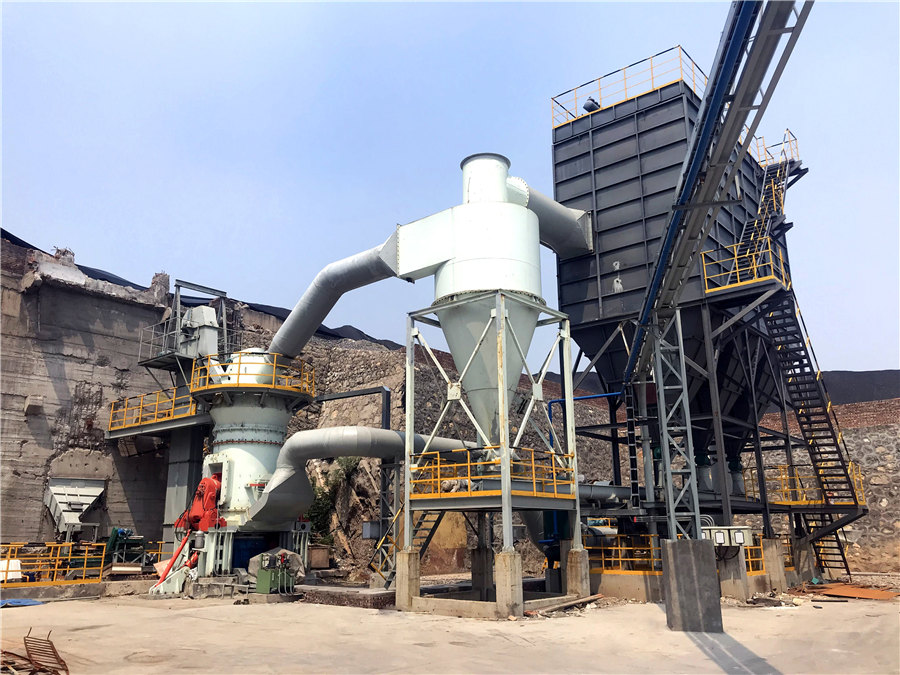
(PDF) Comminution in mineral processing ResearchGate
2018年11月19日 PDF The aim of mineral processing is to get the mineral from rock or Ore that has good economic value in the market Generally, the ability of Find, read and cite all the research you need 2024年5月17日 A SAG (SemiAutogenous Grinding) mill is a giant rotating cylinder filled with grinding media and the ore being reduced As the mill rotates, the grinding media lifts and the impact crushes the feed material SAG mill control refers to the practice of managing the mill load, which is the amount of material inside the mill at any given timeA guide to SAG Mill management2012年6月1日 As the cylinder starts to rotate, the grinding balls inside the cylinder crush and grind the feed material, generating mechanical energy that aids in breaking bonds, activating the catalyst, and Grinding in Ball Mills: Modeling and Process Control2021年1月1日 Mill filling has a dominant effect on grinding mill performance (Apelt, Asprey and Thornhill, 2001), and therefore, its accurate measurement is vital for modelling grinding mill performanceMeasuring filling is also necessary to estimate the composition of the load for mill modelling: rock and slurry for AG mills; rock, balls and slurry for SAG mills; or balls and slurry An improved method for grinding mill filling measurement and
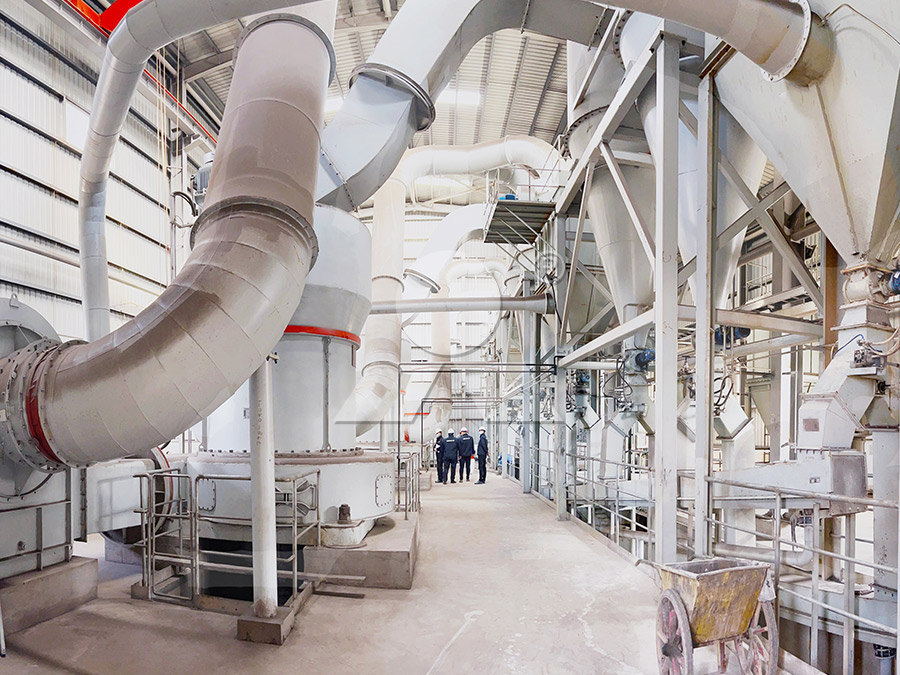
Grinding Mills — Types, Working Principle Applications
2018年8月17日 SemiAutogenous Mills/ SAG Mills (primary grinding mill) — these mills use grinding balls with forces of attrition, impact, and abrasion between grinding balls and ore particles that result in