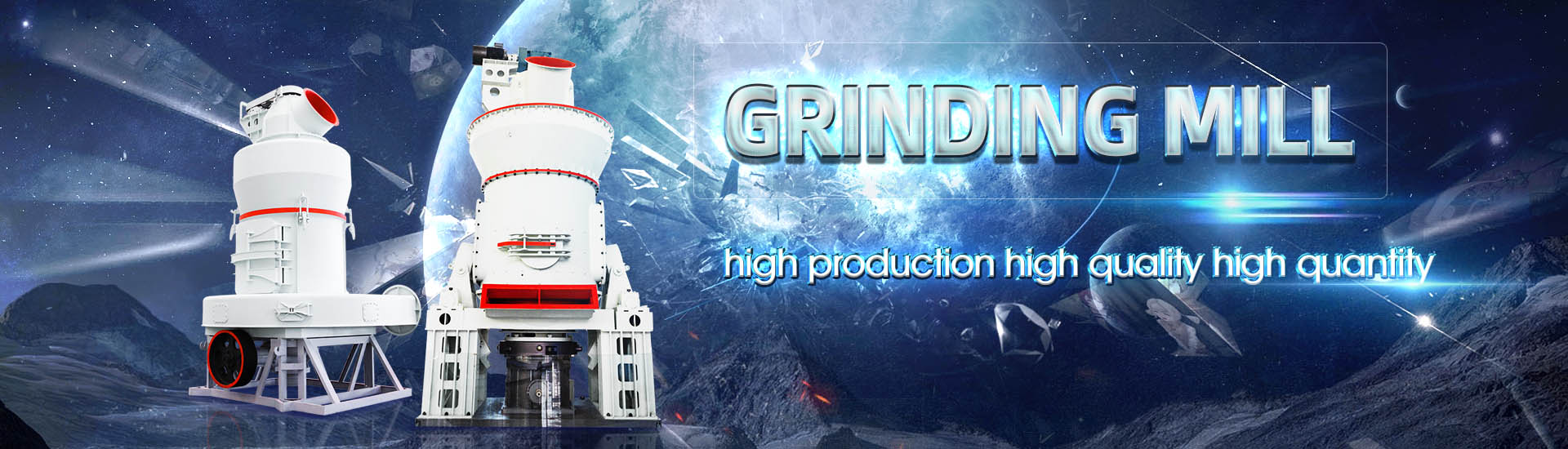
Ore mill for processing laterite mud
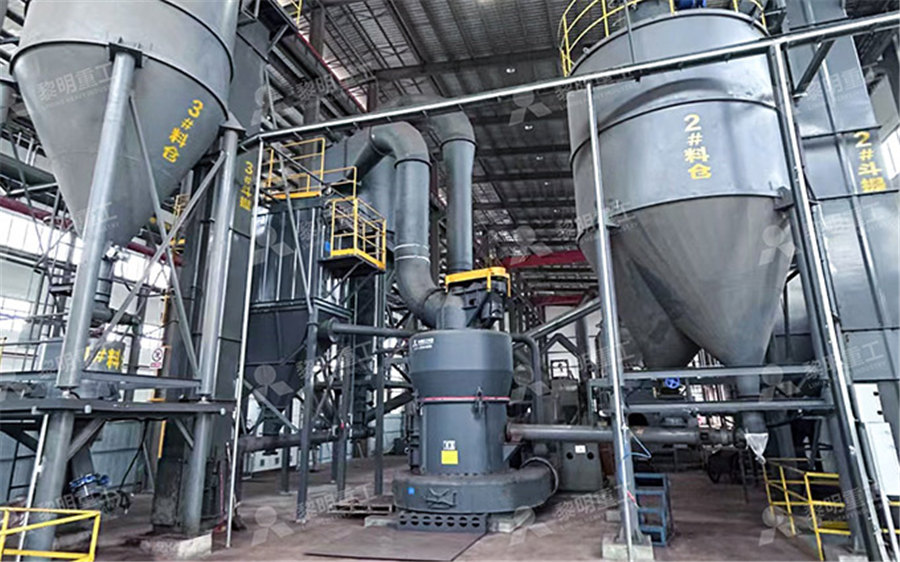
OPTIMIZATION OF LATERITE ORE GRINDING PROCESS
2022年12月31日 This study used a CCD (central composite design) of RSM to determine the dependence and interaction between several operating conditions that affect the grinding process using a ball mill, suchCaron technology is a comprehensive technology for processing lateritic nickel ores, including pyro and hydrometallurgical processes Laterite ores are mainly processed using this Review on hydrometallurgical processing technology of lateritic 2019年9月3日 Liu et al investigated a reduction roasting–magnetic separation process applied to lowgrade Yunnan laterite ore using MgCl 2 as the chlorination agent The ore was reported to contain 087% Ni, 204% MgO, and 322% SiO Nickel Laterite Smelting Processes and Some Examples Laterite ores are formed by the process of weathering and normally found in tropical regions where weathering extracts and deposits it in layers at varying depths below the ground Laterite Ore an overview ScienceDirect Topics
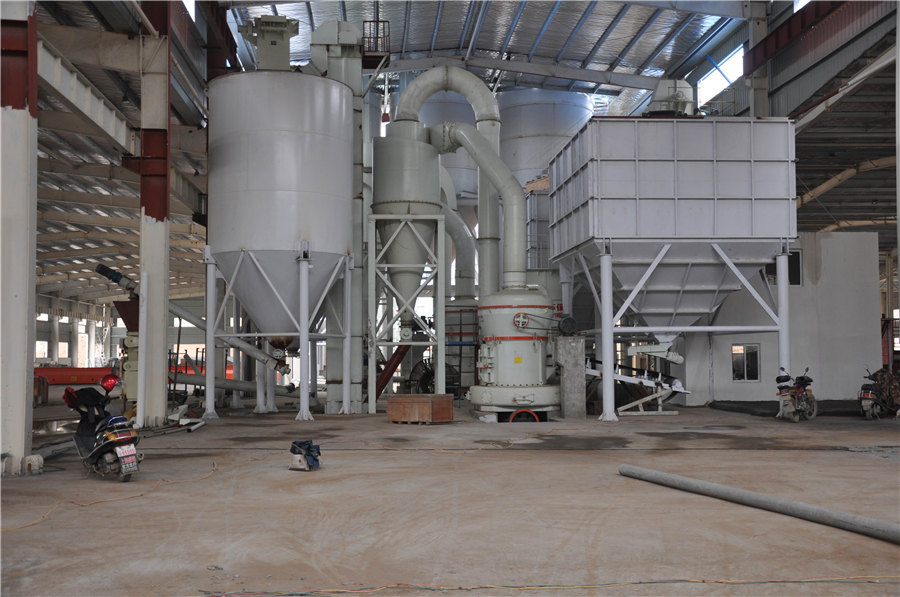
(PDF) Hydrometallurgical Processing of Nickel
2019年3月11日 Hydrometallurgical Processing of Nickel Laterites—A Brief Overview On The Use of Solvent Extraction and Nickel/Cobalt Project For The Separation and Purification of Nickel and Cobalt2024年11月12日 Despite its simple steps and reasonably efficient Ni extraction, not all nickel laterite ores are suitable for processing by the DRMS Future investigations should report A Review of Direct Reduction–Magnetic Separation Process for Liu et al [39] investigated a reduction roasting–magnetic separation process applied to lowgrade Yunnan laterite ore using MgCl2 as the chlorination agent The ore was reported to contain 087% Ni, 204% MgO, and 322% SiO2 as Nickel Laterite Smelting Processes and Some Examples 2018年5月29日 Results show that the red mud addition promoted the reduction of the saprolitic laterite ore and the iron ores in the red mud were coreduced and recovered By adding 35wt% Feasibility of coreduction roasting of a saprolitic laterite ore and
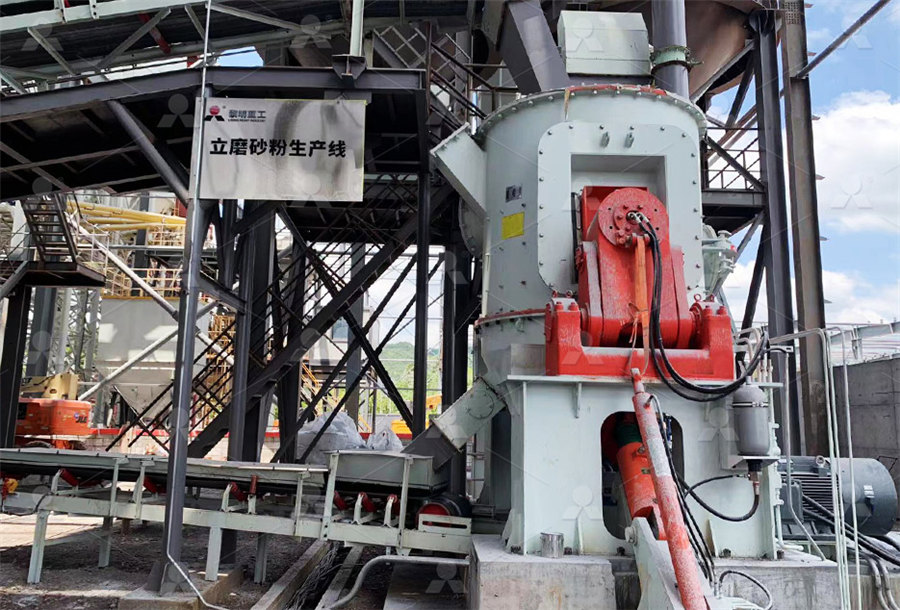
Effect of CoReduction Conditions of Nickel Laterite
2022年2月5日 Through the coreductionmagnetic separation process of nickel laterite ore and red mud, a ferronickel product with a nickel grade of 198%, iron grade of 8798%, nickel recovery of 9954% and iron recovery of 9559% was 2019年9月3日 New method of laterite ore processing: Smelting in twozone Vaniukov furnace to ferronickel In Proceedings of the Sustainable Industrial Processing Summit, Cancum, Mexico, 29 June–4(PDF) Nickel Laterite Smelting Processes and SomeR Elliott et al 321 saprolite The limonitic ore curs as the upper layer of the laterite deposit and is proc imarily composed of goethite, (FeOOH)Thermodynamics of the Reduction Roasting of Nickeliferous Laterite Ores2021年8月12日 Straw charcoal was used as a novel reductant in the coreduction roasting of laterite ore and red mud The influence of the reductant dosages, coreduction temperature, and coreduction time were investigated Results showed that a powdered ferronickel product of 181wt% nickel and 8140wt% iron was obtained under straw charcoal dosage of 15wt% and Study of Straw Charcoal as Reductant in Coreduction Roasting of
.jpg)
Development of laterite ore processing and its applications
2022年12月1日 SEM samples at a temperature of 1150 °C and the addition of 10 wt% Na2SO4 with various reduction times (a) 60 minutes, (b) 90 minutes, and (c) 120 minutes (Nurjaman, Sa'adah and Suharno, 2019)2021年10月24日 Nickel laterite ore is used to produce nickel metal, predominantly to manufacture stainless steel as well as nickel sulfate, a key ingredient in the batteries that drive electric vehiclesNickel Laterites—Mineralogical Monitoring for Grade Definition Laterite ore processing can be performed by pyro or hydrometallurgical mill, to reduce the particle size to 100% passing through a 10 m sieve Samples were discharged into PTFENickel and cobalt losses from laterite ore after the sulfation Red mud and nickel laterite ores are identified as the most interesting and promising scandium resources for future valorization Based on our findings during scandium recovery from red mud, the hydrometallurgical methods (acid leaching and solvent extraction) were effectiveScandium Recovery Methods from Mining, Metallurgical Extractive
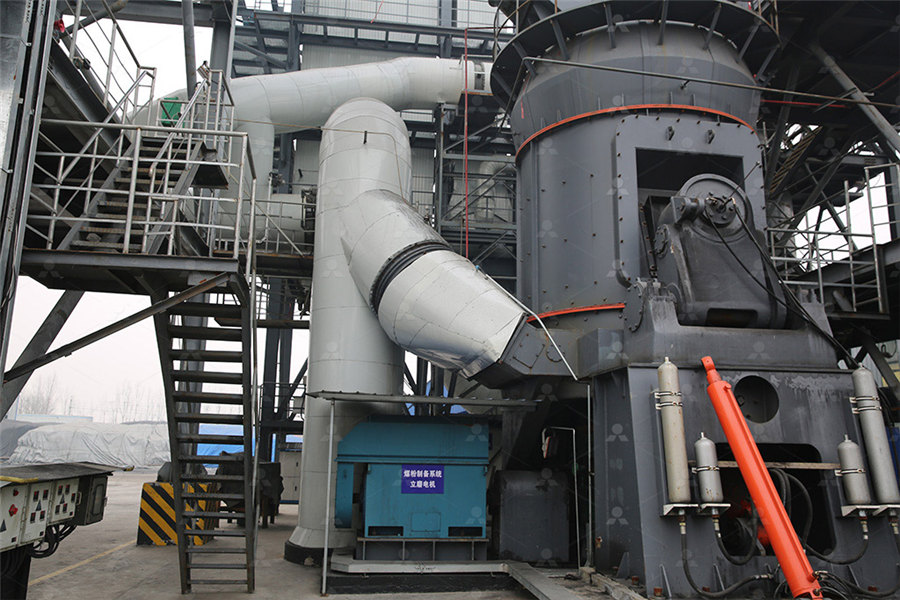
Flowsheet for processing refractory gold ore (sulphidic gold ores
Download scientific diagram Flowsheet for processing refractory gold ore (sulphidic gold ores) Modified after Asamoah, Zanin [13] from publication: Superabsorbent dewatering of refractory gold 2021年10月24日 Nickel laterite ore is used to produce nickel metal, predominantly to manufacture stainless steel as well as nickel sulfate, a key ingredient in the batteries that drive electric vehicles Nickel laterite production is on the rise and surpassing conventional sulfide deposits The efficiency of mining and processing nickel laterites is defined by their Nickel Laterites—Mineralogical Monitoring for Grade Definition 2024年8月21日 The acidleaching tailings of laterite nickel ore are a hazardous waste generated by the laterite nickel ore industry [1], [2], [3]As global demand for nickel continues to rise and nickel sulfide resources decrease, the extraction of nickel resources from laterite nickel ores the main development trend of the global nickel industry in the coming years [4]Magnetic separation for recovering iron resources from acid Nickel and Cobalt Production Michael S Moats, William G Davenport, in Treatise on Process Metallurgy: Industrial Processes, 2014 2231 Laterite Ore Upgrading Laterite ores are upgraded before smelting or leaching The upgrading entails gently crushing and/or grinding the ore and then separating the resulting small, soft, lowdensity Nirich laterized mineral particles from Laterite Ore an overview ScienceDirect Topics
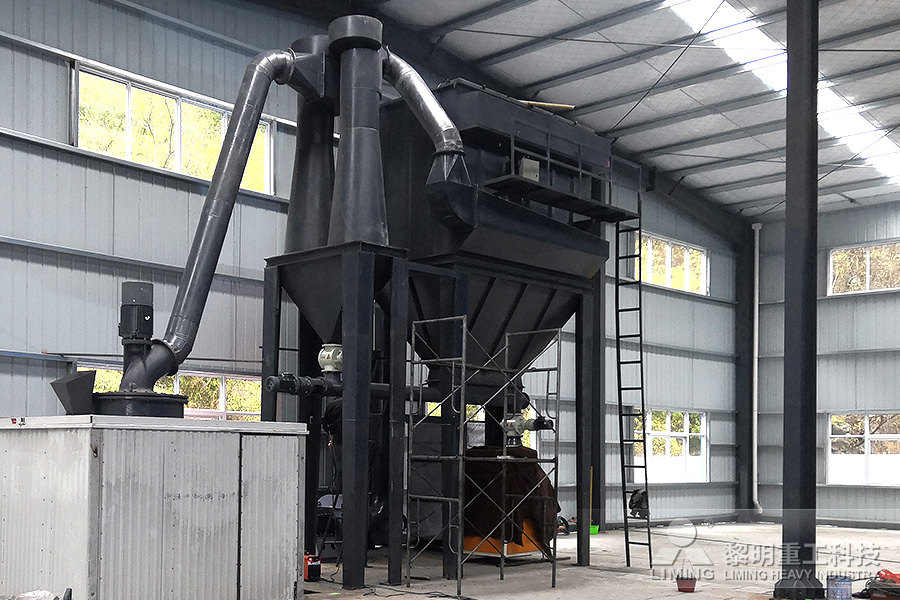
Petroleum coke as reductant in coreduction of lowgrade laterite ore
2022年1月27日 Petroleum coke is industrial solid wastes and its disposal and storage has been a great challenge to the environment In this study, petroleum coke was utilized as a novel coreduction reductant of lowgrade laterite ore and red mud A ferronickel product of 198wt% nickel and 8798wt% iron was obtained with 20wt% petroleum coke, when the roasting temperature 2022年12月31日 He, and Y Li, "Grinding kinetics of quartz and chlorite Optimization of Laterite Ore Grinding Process/ Gyan Prameswara 123 in wet ball milling," Powder Technology, vol 305, pp 418425, 2017OPTIMIZATION OF LATERITE ORE GRINDING Settling tests for the stirred mill products were conducted in 2 M NaCl to simulate expected process water quality where these laterite processes are located Primary dewatering of 10 wt% 20 wt%Preconcentration strategies in the processing of nickel laterite ores 2017年12月12日 The composition of the synthetic solution was determined according to the hydrometallurgical nickel laterite ore processing streams obtained from a HPAL (highpressure sulphuric acid leaching Concentration and Separation of Scandium from Ni Laterite Ore
.jpg)
Recommendation for lateritic Niore processing: garnierite
2021年11月1日 The objective of this study is to analyze the mineralogy and geochemistry of garnierite and its implication for Ni laterite processing Mineralogical analysis using optical microscopic and Xray 2015年4月7日 Despite the growth in nickel laterite processing, upgrading these ores remains a challenge This is mainly because of their complex and variable mineralogy and the lack of definite nickelbearing Preconcentration strategies in the processing of nickel laterite ores 2022年2月5日 The carbothermic coreduction of nickel laterite ore and red mud realized the simultaneous reduction The sinteringblast furnace sulfidation smelting method is suitable for processing laterite nickel ore with nickel content Grinding time was 10 min and grinding concentration was 667% treated by an RK/BM10 L rod millEffect of CoReduction Conditions of Nickel Laterite Ore and Red Mud 2020年1月1日 Laterite ores account for >60% of the world's nickel resources This ore contains considerable amount of scandium, a strategic material in increasingly high demand in various industriesHere, an innovative twostep process was developed in which scandium is first concentrated in a slag phase using carbothermic reduction and then is leached using NaOH An innovative process for extracting scandium from nickeliferous
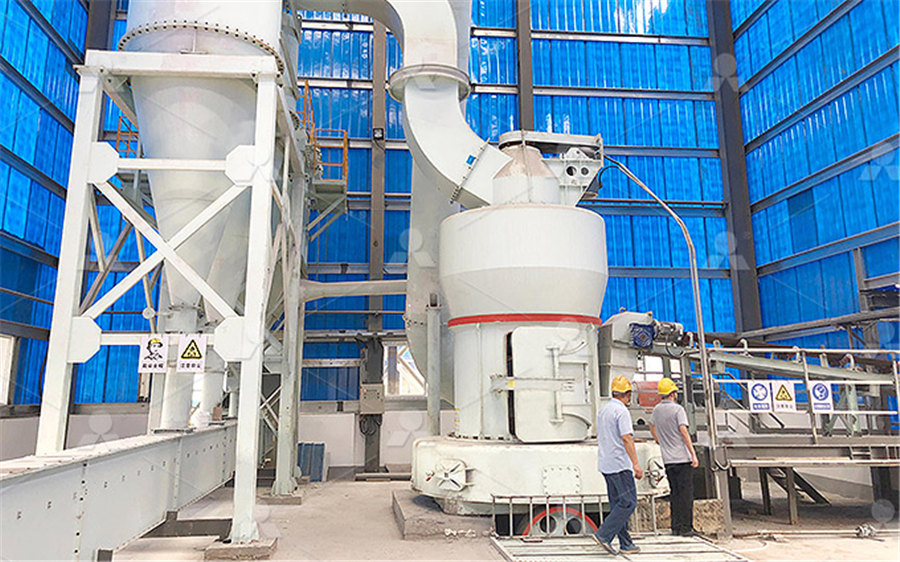
Nickel Recovery Optimization and Kinetic Study from Morowali Laterite Ore
2022年9月11日 Study of nickel leaching using sulfuric acid and phosphoric acid on the selectivity of lowgrade laterite nickel ore under atmospheric conditions has been successfully carried out2023年1月4日 Nickel plays a critical role in the mining industry However, the presence of nickel in the primary source of sulfide minerals is decreasing Focus has since turned to laterite ore, which contains up to 80% Ni metal The purpose of this study was to optimize nickel leaching using sulfuric acid and conduct a kinetic analysis to discover the mechanism that best controls Nickel Recovery Optimization and Kinetic Study of Morowali Laterite Ore2022年6月10日 Laterite nickel ore is a promising scandium resource with economically interesting concentrations and large amounts [1,2,3,4,5,6]It can be simply divided into two types, limonitic and saprolitic laterite [7, 8]Typical chemical composition and metallurgical process of two different types of laterite nickel ore is shown in Table 1 [1,2,3,4,5,6, 9, 10]Leaching Behavior of Scandium from Limonitic Laterite Ores for processing lateritic nickel ores, including pyro and hydrometallurgical processes Laterite ores are mainly processed using this technology The ore is roasted to selectively reduce Ni and Co to metallic forms These metals are then leached with a solution of ammonia or ammonium carbonate A small amount of iron is reducedReview on hydrometallurgical processing technology of lateritic
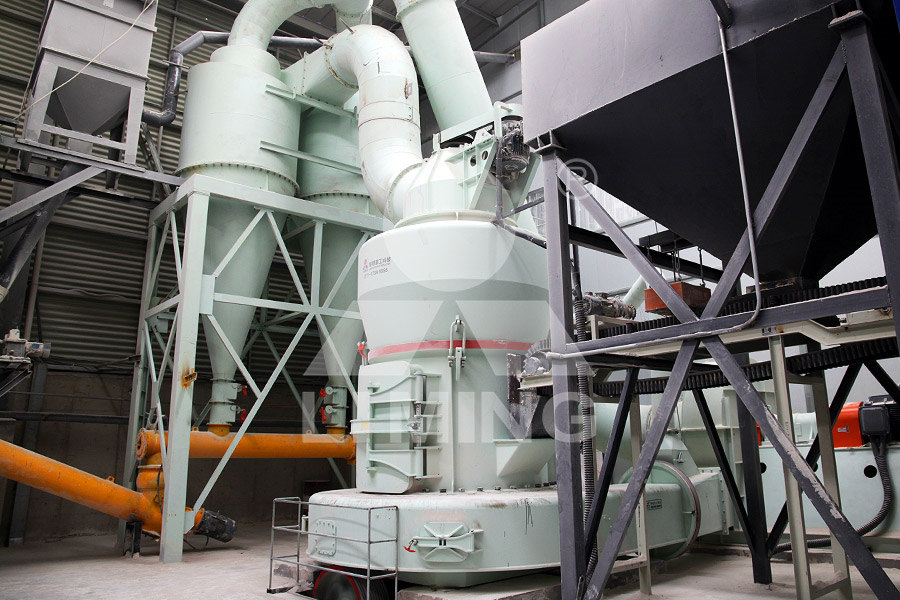
Innovative technology for processing saprolitic laterite ores by
2014年11月27日 An innovative technology for processing saprolitic laterite ores from the Philippines by The limonite ore were crushed to the size of less than 150 mesh using discmill, and then were 2017年2月10日 Laterite ore deposits are formed by nickeliferous olivines via prolonged weathering and leaching processes and are mainly distributed in tropical and subtropical regions near the equator (Dalvi et al, 2004)Moreover, the formation of a nickel laterite may be influenced by the composition, topography, structure, climate, and duration of the formation of the Mineralogical characterization and design of a treatment process 2017年8月15日 Elliot et al (2009) tested the leaching response of 50 aridregion Ni laterite ores from several deposits in Western Australia after they had been agglomerated using 20 kg sulphuric acid/t of ore in a rotating drum The wide variety of Ni laterite ores tested resulted in a wide variety of Ni and Co extractions (∼10–98%) as expectedPreconcentration strategies in the processing of nickel laterite ores 2016年4月1日 This study discuses a novel reductive roasting processing of a laterite ore and a red mud under microwave heat ing Both materials a re of great industria l significance ; laterite is the main nickelNovel applications of microwaves in the metallurgical processing
.jpg)
Preconcentration strategies in the processing of nickel laterite ores
2017年8月15日 In this study, segregation roasting and magnetic separation are used to extract nickel from a garnierite laterite ore The garnierite laterite ore containing 072% Ni, 0029% Co, 865% Fe, 2966% Processing process of laterite nickel ore: The process of direct reduction of granular iron in rotary kiln is also called Dajiangshan process The process flow is as follows: after drying, crushing and screening, raw ore is mixed with flux and reducing agent in proportion to form a pellet; after drying and hightemperature reduction roasting, the pellet generates nickel iron alloy; the mixture What equipment is used for processing laterite nickel ore 2022年5月31日 The processing methods of laterite nickel ore is mainly divided into two types: pyrometallurgy process and hydrometallurgy process According to the difference of nickel, cobalt content and ore type, and different working conditions, there are 7 kinds of methods to choose from This article will introduce you to these 7 laterite nickel ore processesHow to Extract Laterite Nickel Ore? 7 Processing MethodsDownstream processing of the first stage leach solution varies with the type of ore feed Typically, it includes pH adjustment, precipitation of nickelcobalt mixed sulphide (MSP) product with H 2 S, precipitation of aluminium, manganese and iron with magnesia, and evaporative crystallization of magnesium sulphate which is thermally decomposedDEVELOPMENTS IN HYDROMET PROCESSING OF NICKEL LATERITES
.jpg)
Recent Developments in the Chloride Processing of
2011年5月1日 Therefore, research in hydrometallurgical processing of laterite nickel ores has been vibrant, at least in the last three decades, resulting in many new technological development such as 2023年8月31日 An alternative laterite nickel ore processing using sulfuric acid as a leaching agent to produce class 1 nickel as a raw material for electric vehicle batteries produces natrojarosite residue as a (PDF) Valorization of Solid Residue from the Lateritic 2016年1月1日 Leaching of nickel laterite ore at atmospheric pressure is a leaching method that can be operated at >100⁰C temperatures in an atmospheric pressure, which is applicable to a lowgrade laterite oreHydrometallurgical processing of nickel lateritic ores2019年9月3日 According to a review published by Diaz et al, oxidetype nickel ores accounted for 64% of landbased nickel ores, but more than 60% of nickel production was based on the matte smelting of sulfide ores in 1988 []This picture has significantly changed over the past three decades because of the decrease in the reserves of highNi sulfide ores, which are mostly Nickel Laterite Smelting Processes and Some Examples of Recent
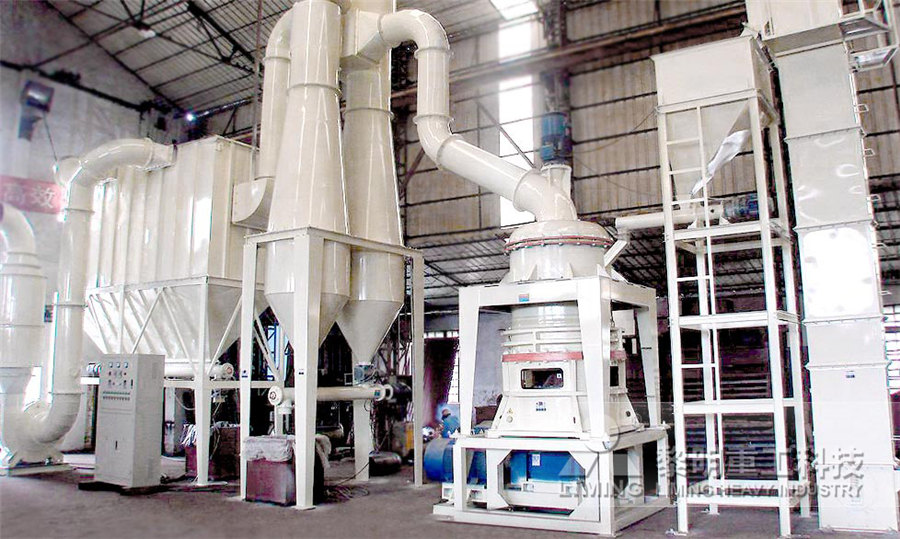
A novel process for extraction of iron from a refractory red mud
2020年9月7日 According to the XRD patterns of red mud and roasted ore (Fig 1, Fig 8(A)), comparing with the iron phase of the red mud , which changed from hematite (Fe 2 O 3 ) to a new iron phase dominated by2008年1月1日 The challenges in processing nickel laterite ores using flotation process were comprehensively reviewed Literature shows that flotation has not been successful to recover nickel from laterite oresBeneficiation of Nickel laterites for HPAL processing2018年5月29日 Results show that the red mud addition promoted the reduction of the saprolitic laterite ore and the iron ores in the red mud were coreduced and recovered By adding 35wt% red mud, the nickel grade and recovery were 490wt% and 9525wt%, and the corresponding iron grade and total recovery were 7100wt% and 9377wt%, respectivelyFeasibility of coreduction roasting of a saprolitic laterite ore and History of Development of Laterite Ore Processing Process and Its Application, Fathan Bahfie et al 91 magnesium (1015%) and low iron (1320%) Ferronickel smelting is the most widely appliedDEVELOPMENT OF LATERITE ORE PROCESSING AND ITS