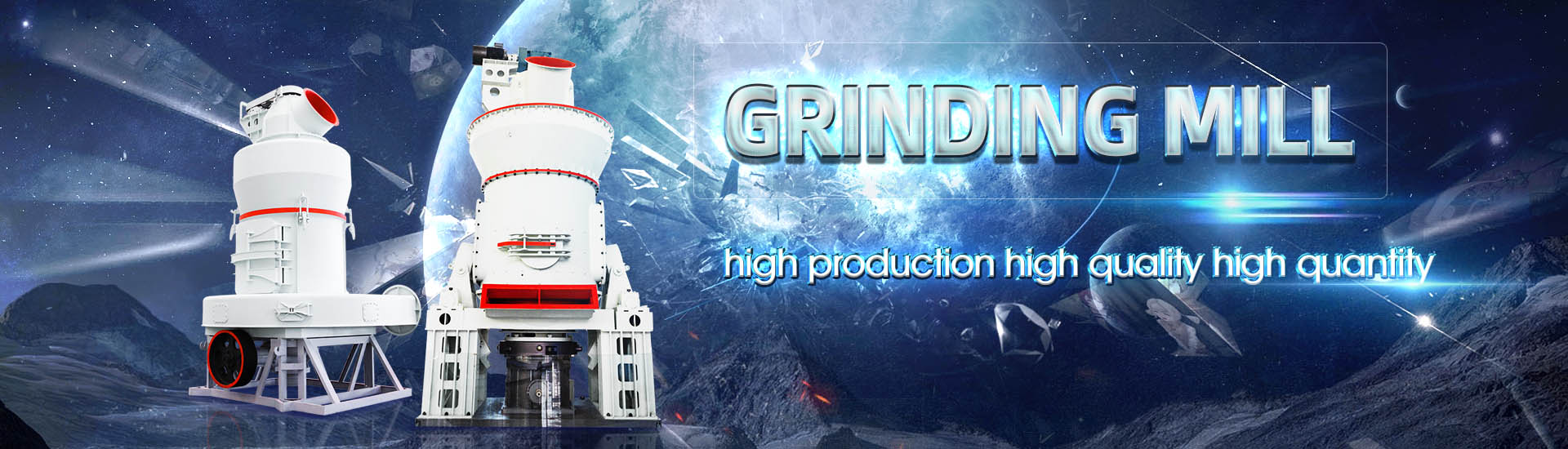
Mill coal drop pipe function
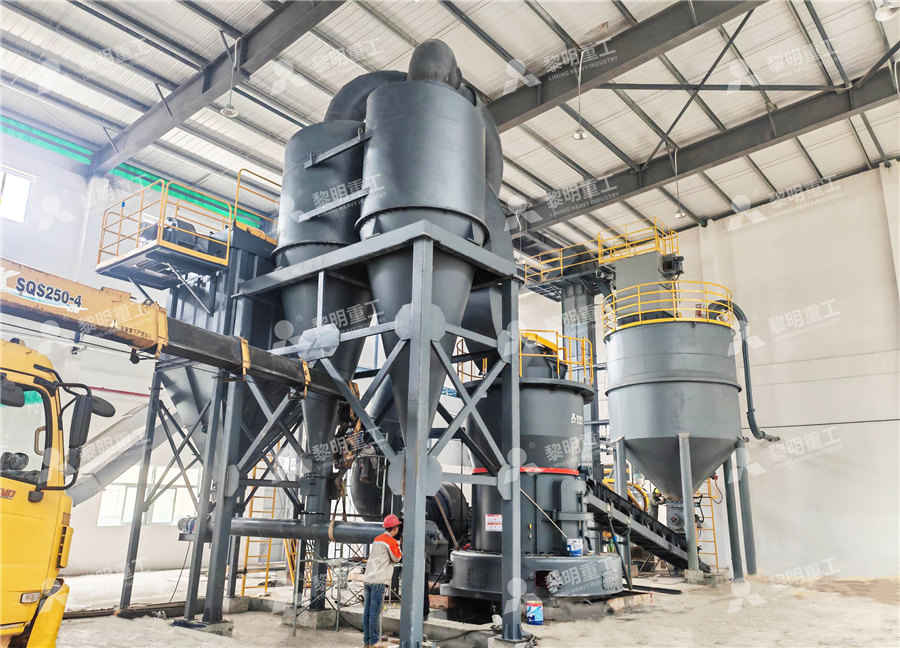
Analysis of the Coal Milling Operations to the Boiler Parameters
Milling system in coal power plant purposely to process the raw coal to become as pulverise fuel before enter to the boiler furnace Pulverise fuel enter to the boiler furnace through pulverise 2011年1月1日 Debris into the coal handling system can make the belt vertical cut through, coal drop pipe, coal bunker and other clogging phenomenon The coal crusher and other Operation and Maintenance of Coal Handling System in Thermal This paper presents a newlydeveloped technology for correcting coal flow in individual coal pipes from a pulverizer classifier without changing PA flow distribution balance Performance is13045 Coal Distributor Paper:Layout 1 Babcock Power2024年5月1日 To avoid abnormal operating conditions of coal mills in time and effectively, a dual fault warning method for coal mill is proposed Three typical faults of coal mill plugging, coal Dual fault warning method for coal mill based on ScienceDirect
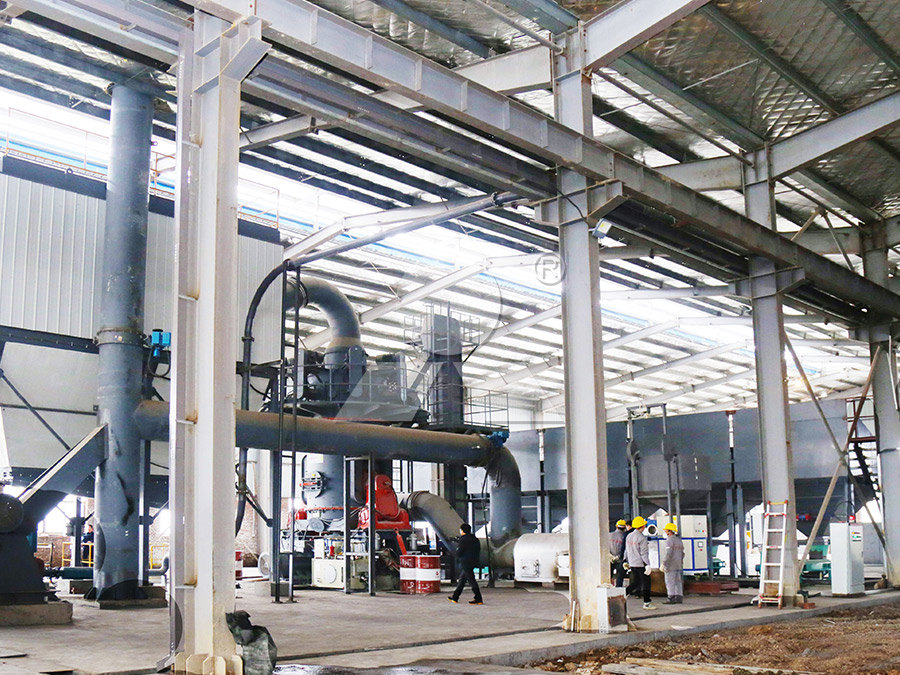
CFD Modeling of MPS Coal Mill for Improved
2009年1月1日 It was shown that uniform velocity at the throat improves the air and coal flow distribution at the outlet pipes A newly developed coal mill model provides a valuable tool that can be usedCoal Pulveriser Mill Function and Operation details Pulverizer as shown in fig1 is used in power plant to reduce the size of the incoming raw coal to a fineness thatPulveriser Mill Performance Analysis Optimisation in Super2020年4月2日 Pulverise fuel enter to the boiler furnace through pulverise coal pipe (PC) which attached to the boiler The different mill has different PC pipe corners, and with different length andAnalysis of the Coal Milling Operations to the Boiler Evaluate rifflers and burner lines Perform unit performance and emissions baselining Measure coal and PA flow imbalances Check measurement or collection location Review sample CoalCONTROL™ – EMISSIONS REDUCTION THROUGH BURNER
.jpg)
Double inlet outlet ball mill Geckointech
Coal feeder sends coal into drop pipe Coal falls down to screw conveyor and gets pushed into cylinder of ball mill Inside, steel balls will grind coal into fine particles Hot primary air enters cylinder through hollow pipe at two ends of 2024年5月1日 The working process of this coal mill is as follows: the raw coal is conveyed by the coal feeder and enters into the grinding disk through the coal drop pipe The raw coal from the coal feeder is ground under the friction with the grinding parts and the rest of the coal, and is gradually ground into fine coalDual fault warning method for coal mill based on ScienceDirectCoal Mills are used to pulverize and dry to coal before it is blown into the power plant furnace Operation The coal is feed into the coal mill through a central inlet pipe where gravity is used to lead the coal to the bottom of the mill, where the grinding table and some heavy rollers pulverizes the coal to particlesCoal Mills SolidsWikiPulveriser function is to crush/grinding the raw coal into a predetermined size in order to increase the surface area of the coal Hot air through the mill besides removing coal moisture, picks up the lighter particles and takes them through Pulveriser in Thermal Power Plant Bowl Mill Ball Mill

Operation Manual: HRM1700M Vertical Roller Coal Mill PDF Pipe
The document provides installation and operation instructions for the HRM1700M Vertical Roller Coal Mill It describes the mill's technical parameters, components, structure, working principles, and installation process Key aspects include grinding rollers that can be removed for maintenance, a hydraulic system that controls grinding pressure, and a separator that 2009年5月1日 The function of a modern pulverizer system is to dry and grind the power station’s coal supply and distribute it to the burners In a bowlmill coal pulverizer, raw coal, which is fed through a central coal pipe at the top of coal pulverizer, falls by gravity to a rotating grinding table where it is pulverized between grinding rollersCFD analysis: bowling for pulverized coalMill Training Manual Alstom Free download as PDF File (pdf), Text File (txt) or read online for freeMill Training Manual Alstom PDF Coal Mill (Grinding)classifier cone and drop back into the mill table for further processing 3 MODELING EQUATIONS The modelling equations proposed by Pietr Niemczyk et al (2012) is used to develop the coal mill model The following assumptions are made to develop the coal mill model: (1) Coal in the mill is either pulverised or unpulverised, ieModeling and Control of Coal Mill
.jpg)
Design of Improving Coal Chute in Thermal Power Plant Based on
2021年9月1日 function from paddy field to our plant is a traditional 900mm× 900mm square straightthrough coal drop Meng, WJ, (2014) Discrete element analysis of materials transferred by drop pipe 2007年4月1日 The traditional way to measure this important property is to collect samples from the coal pipe, In a case study aimed at optimizing mill function on a 600 MW lignitefired unit in central Measuring Coal Particles in the Pipe Power Engineering2009年9月20日 table through the coal feed pipe This paper describes the experimental measurement of coalmill transfer functions at a 380 Mw steam turbine generator of TransAlta Utilities in CanadaModeling and Parameter Identification of Coal MillCoal Pipe Balancing Methodology Airflow Sciences Corporation has performed a detailed analysis and design to balance the flow within the coal pipes for numerous plants across North America The methodology is as follows: 1 Utilize the Advanced Coal Flow Measurement (ACFM) equipment to accurately measure both air flow and coal flow rate in each Coal Pipe Balancing Airflow Sciences
.jpg)
Coal Mills SolidsWiki
The coal is feed into the coal mill through a central inlet pipe where gravity is used to lead the coal to the bottom of the mill, If the the particles are too heavy they will drop to the bottom of the mill and will be pulverized once more The coal Coal pipe F9 on pulverizer B was the only pipe that met the original plant fuel specification guarantee of 70% passing 200 mesh, which is far short of the 75% minimum we use Even so, fuel fineness and fuelPulverized Coal Pipe Testing and Balancing Storm Technologies, From the coal yard, the coal is transfer to the mill bunkers through conveyor belt The bunkers are sized for an effective capacity of twelve (12) hours at BMCR with design coal Each mill bunker has one hopper, connected to the feeders Mills operate when the bunker coal gate valves are opened, coal is allowed to flow to the gravimetric feedersAnalysis of the Coal Milling Operations to the Boiler Parameters2009年11月1日 The velocity data is that of the moving coal particles (See Figure 3) Air velocity in these pipes ranges from 110 to 120 fps The difference between the air and coal velocities is the coal slipBalancing Coal Pipes Power Engineering
46.jpg)
Detection of Malfunctions and Abnormal Working Conditions of a Coal Mill
2018年5月2日 Coal mill malfunctions are some of the most common causes of failing to keep the power plant crucial operating parameters or even unplanned power plant shutdowns Therefore, an algorithm has been developed that enable online detection of abnormal conditions and malfunctions of an operating mill Based on calculated diagnostic signals and defined 2022年1月26日 The highest erosive wear occurred for the M3 mill dust ducts for the case coal 1 and amounted to 456 mm/5200 h On the other hand, the lowest erosive wear occurred for the M2 mill dust ducts Numerical Study of the Erosion Process and Transport of Pulverized Coal ASME Coal Fineness Sampling Test Procedure Rev 3/2010 Page 1 2367 LAKESIDE DRIVE, SUITE A1 BIRMINGHAM, AL 35244 PHONE (205) 4530236 FACSIMILE (205) 4530239 Pipe Wall Drilled with 45/64 Drill (703) Notes: 1 The 11/4” NPT Connections must fit Microsoft Word ASME Coal Sampling Test Procedureclassifier cone and drop back into the mill table for further processing 3 MODELING EQUATIONS The modelling equations proposed by Pietr Niemczyk et al (2012) is used to develop the coal mill model The following assumptions are made to develop the coal mill model: (1) Coal in the mill is either pulverised or unpulverised, ieModeling and Control of Coal Mill
.jpg)
MRHS Mill Reject Handling System in Thermal Power Plant
The function of Mill Reject Handling system Mill Rejects from coal mill will drop into the Pyrite Hopper through the grid Oversize material will be retained on the grid Compressed air from dense phase conveying airline will then be injected to convey the accumulated mill reject to the storage silo via pipe work2023年4月12日 At the inlet pipe 250 with a pressure drop of 436261 Pa, a head loss of 65582 m, and an efficiency of 39% Best results on pipe inlet 200 Cyclone merupakan alat untuk memisahkan partikulat dari aliran fluida tanpa filter Cyclone dalam hal ini untuk memisahkan partikulat dari aliran udara supaya tidak masuk ke coal millAnalysis of Fluid Flow in Pipeline and Cyclone Systems for The direct cost of coal grinding is a function of the wear and tear of the powdered coal mill , which in turn is influenced by the expected particle size spectrum of the coal dust and thus of the mill settings, eg hopper load, mill speed and separator adjustment Therefore, a costOnline measurement of coal fineness and airfuel ratio inside the coal pipeCNU CN06U CN0U CNU CN U CN U CN U CN 0 U CN0 U CN 0U CN U CN U CN U Authority CN China Prior art keywords coal pipe handling frame breakage pipe coal breakage Prior art date CNU Coal mill coal drop pipe blockage cleaning
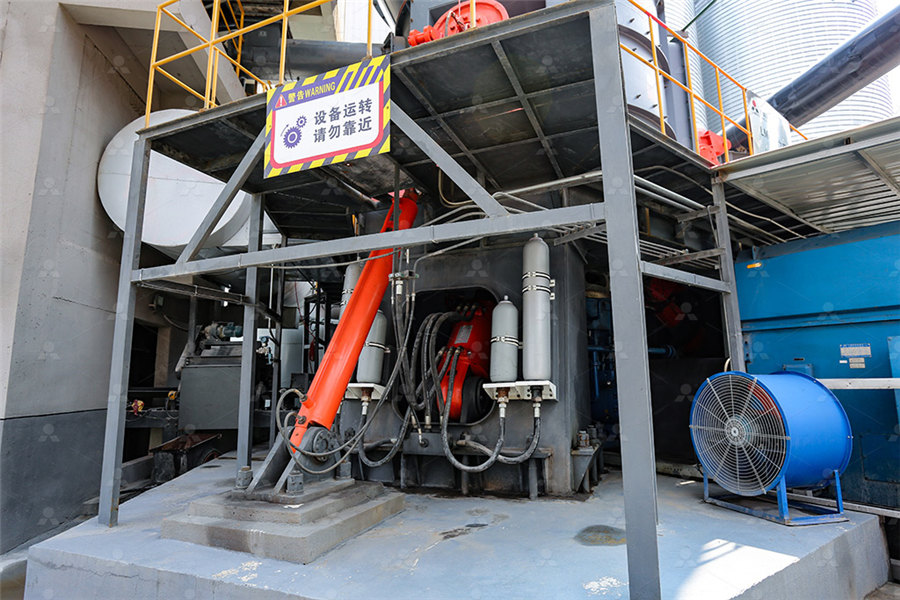
CFD Modeling of MPS Coal Mill for Improved Performance and Safety
2009年1月1日 The main functions of a Moistu re evaporation causes a drop in air and coal flow distribution at the outlet pipes A newly developed coal mill model provides a valuable tool that can be Ceramic Liner pipe is a high technology production technologyselffuel high temperature clutch synthesis method 1) High Abrasion Resistant: Vickers hardness of the corundum lining is HV1100 to1500, as high as that of tungstencobalt hard alloys, and the abrasion resistance is 20 times as carbon steel pipesThe ceramic lined elbow throughout the power, metallurgy, coal The mill motor supplies energy to the mill by rotating the mill table and thus crushing the raw coal between the grinding elements Furthermore there is a seal air fan which suppliesASS FLOW AND PARTICLE SIZE MONITORING OF PULVERISED 2022年1月26日 One of the main causes of damage to the elements of coalfired boilers installations, leading to breakdowns and, consequently, a shutdown of the block, are erosive processes Unfortunately, there is not much research conducted on dust erosion of the dust ducts supplying the air–dust mixture to the burners The problem of erosion of the dust ducts Numerical Study of the Erosion Process and Transport of Pulverized Coal
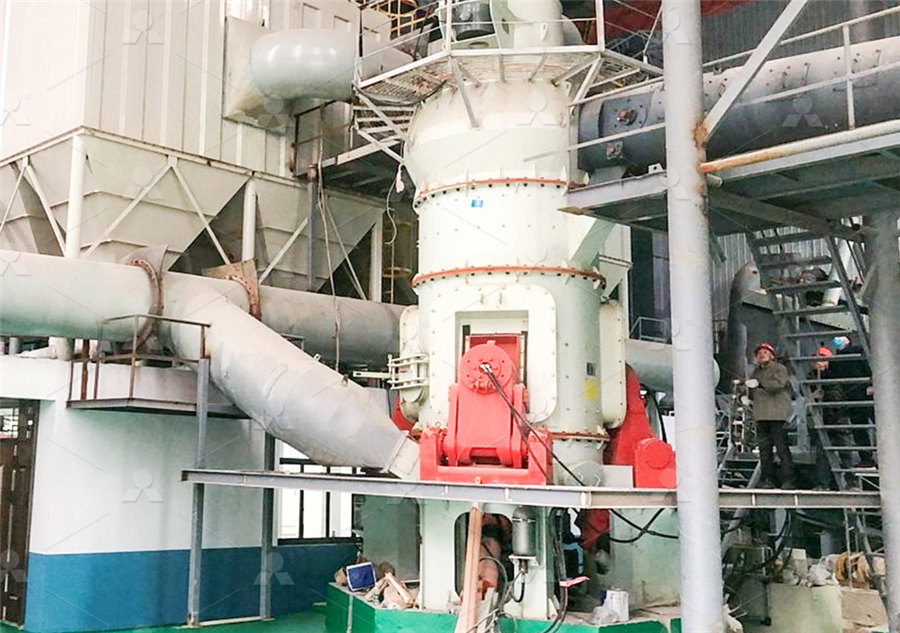
A unified thermomechanical model for coal mill operation
2015年11月1日 As presented by Andersen et al (2009) and Odgaard, Stoustrup, and Mataji (2007), coal moisture imposes limit on the maximum load at which a coal mill can be operated and the load gradient (how fast the mill may change its operating point), if it is desired that the pulverized coal entering the furnace has moisture content less than or equal to a certain value Coal pipe F9 on pulverizer B was the only pipe that met the original plant fuel specification guarantee of 70% passing 200 mesh, which is far short of the 75% minimum we use Even so, fuel fineness and fuelPulverized Coal Pipe Testing and Balancing2011年1月1日 An investigation has been carried out into the deposits generated on cooled probes and the gas compositions produced from cofiring miscanthus mixed with Daw Mill coalDeposit formation and emissions from cofiring miscanthus with Daw Mill 2020年8月12日 This study shows the performance of a currently running vertical roller coal mill (VRM) in an existing coalfired power plant In a power plant, the coal mill is the critical equipment, whose An investigation of performance characteristics and
.jpg)
Coal Mill PDF Combustion Chemistry
Coal Mill PPT Free download as Powerpoint Presentation (ppt / pptx), PDF File (pdf), Text File (txt) or view presentation slides online The document provides an overview of coal mill operation, protections, and interlocks It discusses coal mill Raw coal is moved from the storage to the mill by conveyor mechanism The type of coal mill envisaged for our model is bowl mill which is shown in Fig1 Raw coal is introduced near the centre of the grinding table through the coal feed pipe The coal moves outward on the rotating table and it is ground under the rollerPulverised Coal Flow measurement in Thermal Power PlantCoal and mill Free download as PDF File (pdf), Text File (txt) or view presentation slides online The document discusses pulverized coal mills used in power plants It describes different types of mills including tube mills, ball mills, and bowl mills Tube mills are low speed while bowl mills are medium speed The document explains the construction, operation, and maintenance of bowl Coal and Mill PDF Mill (Grinding) Mechanical EngineeringFrequently our pulveriser used to be stopped and directly it caused loss of power generation and also affected the economical figure of our power house In this paper our objective is to measure the temperature of the coal pipe to prevent the de choking of the coal flow pipe A Coal mill model using Evolutionary computation technique reported (PDF) Measurement and Control of Coal Pipe Temperature of Coal
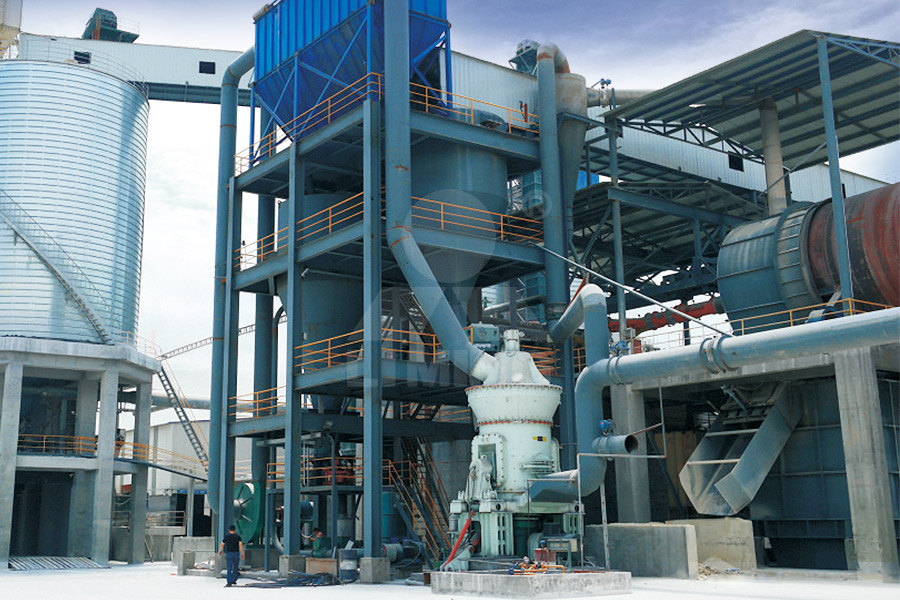
Modeling and Parameter Identification of Coal Mill
2 Modeling of Coal Mill The function of a coal mill is to supply the dry and the pulverized coal to the boiler burner Fig 1 shows a sectional view of MBF coal mill considered in the study Raw coal is introduced near the center of the grinding table The transfer functions of coal mill are experimentally measured in [5, 6] table through the coal feed pipe The coal moves outward on the rotating table and it is ground under the rollerModeling and Parameter Identification of Coal Mill ResearchGateThis document discusses coal pulverizers/mills which are critical components that convert the stored energy in coal into electricity There are various types of pulverizers that primarily utilize grinding, drying, classification and circulation processes Key aspects covered include the different principles of grinding, types of pulverizers, performance criteria such as fineness and Coal Mill in Thermal Power Plant2022年7月26日 learning machine; coal mill; fault diagnosis 1 Introduction Coal mills are important equipment of the coal pulverizing system The structure of the MPS mediumspeed coal mill is shown in Figure1[1] As can be seen from Figure1, the raw coal entering the coal mill through the coal falling pipe is squeezed and ground byFault Diagnosis of Coal Mill Based on Kernel Extreme Learning
.jpg)
Flow measurement of five seal air pipes at a coal mill using the
2023年5月11日 Flow measurement of five seal air pipes at a coal mill using the heater method at a coal fired power plant and numerical analysis of one of the pipes with curvature