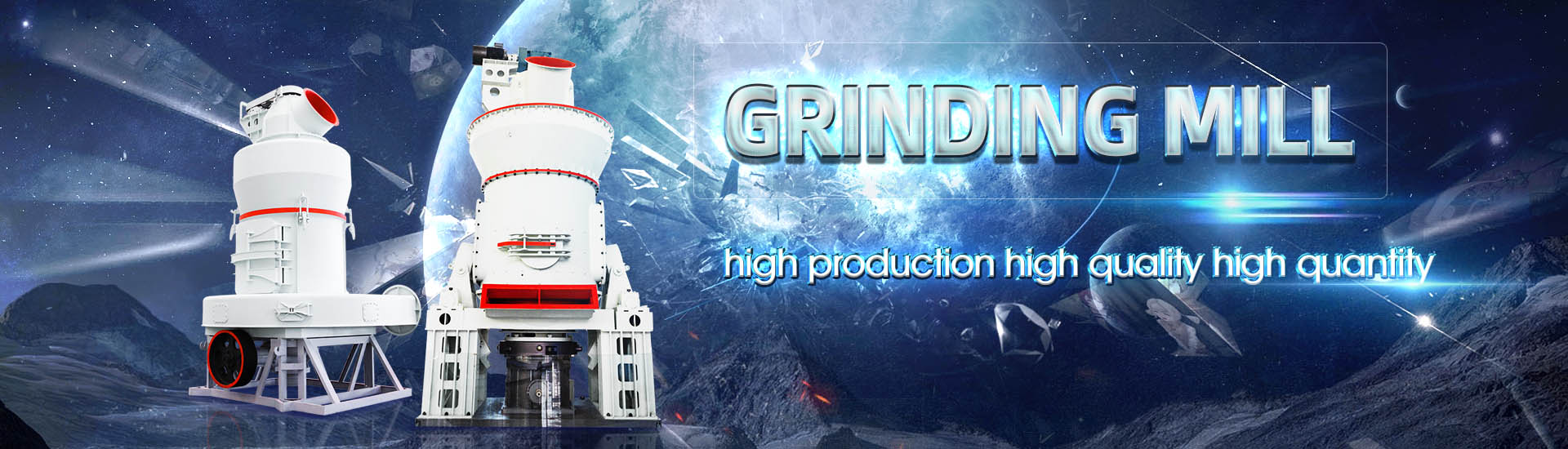
Ball mill single chamber ball mill single chamber ball mill single chamber

Ball Mill an overview ScienceDirect Topics
A ball mill is a type of grinder used to grind and blend materials, and the ball milling method can be applied in mineral dressing, paints, ceramics etc The ball milling owns the strengths of Ball and Rod Mills JeanPaul Duroudier, in Size Reduction of Divided Solids, 2016 Rod Mill2024年8月15日 By reproducing four classic and distinct reaction types drawn from literature, our study underscores the significance of thorough documentation of all used equipment With our Navigating Ball Mill Specifications for TheorytoPractice ball mill chamber generally requires – depending on the desired size reduction – bigger media at the chamber inlet and smaller sizes towards the mill outlet To fulfil this requirement, the industry has developed socalled classifying liners in a variety of shapes and designsBALL MILLS Ball mill optimisation Holzinger Consulting
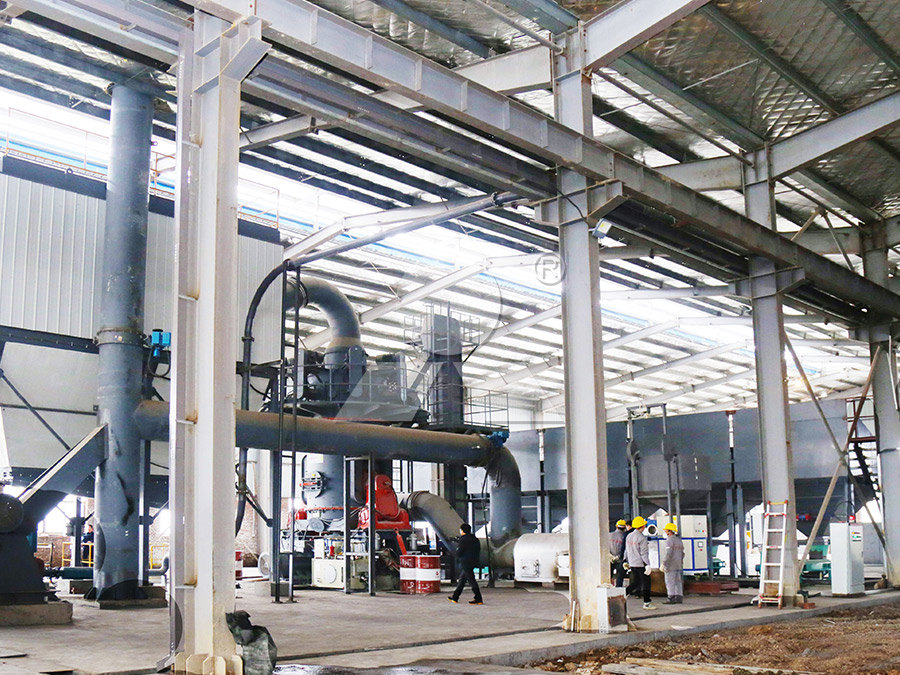
Ball Mill an overview ScienceDirect Topics
Another type of ball mill is used to an increasing extent, where the mill is vibrated instead of being rotated, and the rate of passage of material is controlled by the slope of the mill The ball mill is used for the grinding of a wide range of materials, including coal, pigments, and felspar for pottery, and it copes with feed up to about 50 mm in size2015年6月19日 The basic parameters used in ball mill design (power calculations), rod mill or any tumbling mill sizing are; material to be ground, characteristics, Bond Work Index, bulk density, specific density, desired mill Ball Mill Design/Power Calculation 911MetallurgistThis document provides guidance on ball mill grinding processes It covers topics such as ball mill design including length to diameter ratios, percent loading, critical speed, and internals evaluation Methods for assessing ball charge, wear rates, and liner management are described Empirical relationships for power draw and grinding laws are presented The document also discusses Ball Mill Grinding Process HandbookSmaller balls are used here to grind the product material finer In this paper we analyse the charge motion, short term ball segregation processes and energy utilisation in a 4 m diameter two chamber cement ball mill using DEM The first chamber is 43 m Ball motion, axial segregation and power consumption in a full
.jpg)
Grinding in Ball Mills: Modeling and Process Control
2012年6月1日 Such a structure may consist of several singleinput singleoutput control efficiency of the ball mill and the economic assessment of the process control R e f e r e n c e s 1 A j a a l, 2009年8月1日 The internal shell diameter of the first chamber is 385 m and it is 43 longIt has a wave liner fitted consisting of 36 liner plates around the circumference Fig 1 shows the internal structure of the first chamber of the cement mill Fig 2 shows a close up of the lifter plates whose profile consists of a gradual rise to a high point followed by an abrupt drop back to the shellBall motion, axial segregation and power consumption in a full The Planetary Ball Mill PM 100 is a powerful benchtop model with a single grinding station and an easytouse counterweight which compensates masses up to 8 kg Automatic grinding chamber ventilation ; 10 SOPs can be stored, In the Ball Mill PM 100 this counterweight can be adjusted on an inclined guide railPlanetary Ball Mill PM 100 RETSCH highest fineness2024年8月15日 As illustrated for a planetary ball mill in Figure 1, the point impact energy of a single collision between the ball and the molecules, must exceed the threshold energy (activation energy of a single molecule) as shown in Equation 1, in order to overcome the energy barrier of a single molecular eventNavigating Ball Mill Specifications for TheorytoPractice
.jpg)
Cement ball mill process calculation pdf PPT SlideShare
2024年1月5日 3 Ball mill for dry grinding (eg cement) Coarse grinding chamber 33 % of total grinding path length Lifter plate lining 100 mm – 60 mm balls Fine grinding chamber 67 % of total grinding path length Classifying plate lining 50 mm 15 mm balls Intermediate diaphragm Discharge diaphragmSmaller plants tend to add extra crushing stages in order to operate a single grinding stage only If a ball mill uses little or no water during grinding, it is a ‘dry’ mill If a ball mill uses water during grinding, it is a ‘wet’ mill A typical ball mill Ball Mill (Ball Mills Explained) saVRee saVReeLength of ball mill Shaft diameter Length of shaft Speed of ball mill Media size and shape Since the optimum number of revolutions per minute (rpm) for a ball mill is directly related to the ball mill radius, these two factors are grouped together to study Consider for a moment the path travel by a typical ball in a halffull ball millDesign and Analysis of Ball Mill For Paint Industries IJSRDOperation and Elements of a ClosedCircuit Ball Mill System Cement ball mills typically have two grinding chambers The first chamber is filled with larger diameter grinding media andlined with lifting liners The first chamber coarsegrinds the feed material and prepares it for the second chamber The second chamber is the fine grinding OPTIMIZATION OF CEMENT GRINDING OPERATION IN BALL MILLS
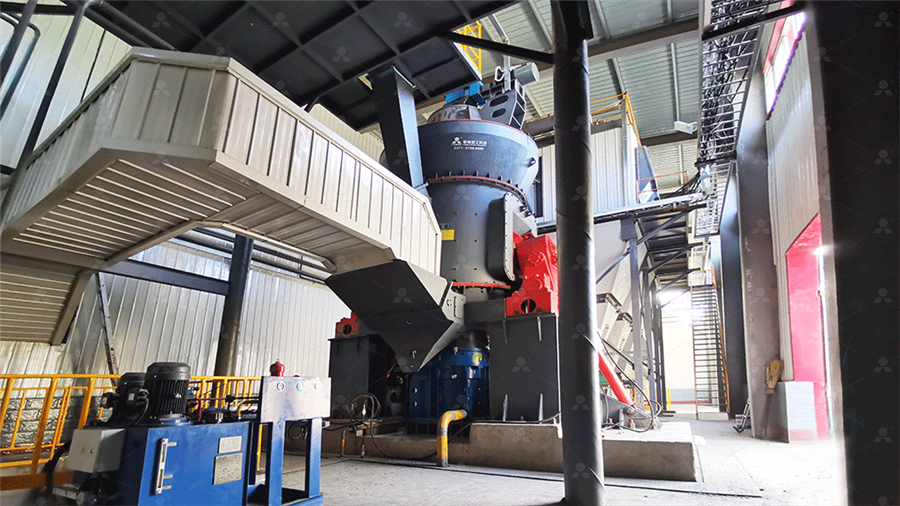
Planetary Mono Mill PULVERISETTE 6 classic line / Description
High performance in minimum space The Planetary Mono Mill PULVERISETTE 6 classic line is a highperformance Planetary Ball Mill with a single grinding bowl mount and practical, easily adjustable imbalance compensation Your advantage: Particularly easy use and highenergy effect of up to 650 rpm2016年10月10日 At the short ball mill grinding is a more rough and for grinding fineness a lot of material has to be returned from classifier to the mill, it leads to mill overload In long ball mills the grinding occurs only at the front and the rest of the balls in the drum only increases power consumption Drum mills have one grinding chamber (short and How ball mill works? Energosteel Grinding Media Ball 2020年7月2日 A comprehensive investigation was conducted to delineate the effect of ball size distribution, mill speed, and their interactions on power draw, charge motion, and balls segregation in a (PDF) Effects of Ball Size Distribution and Mill Speed and Their 2017年7月1日 To determine simulation parameters, first a single ball (2 or 25 cm) Keywords: tumbling mill, chamber filling degree, fill selfoscillation, specific power intensity in grindingThe effect of ball size distribution on power draw, charge motion
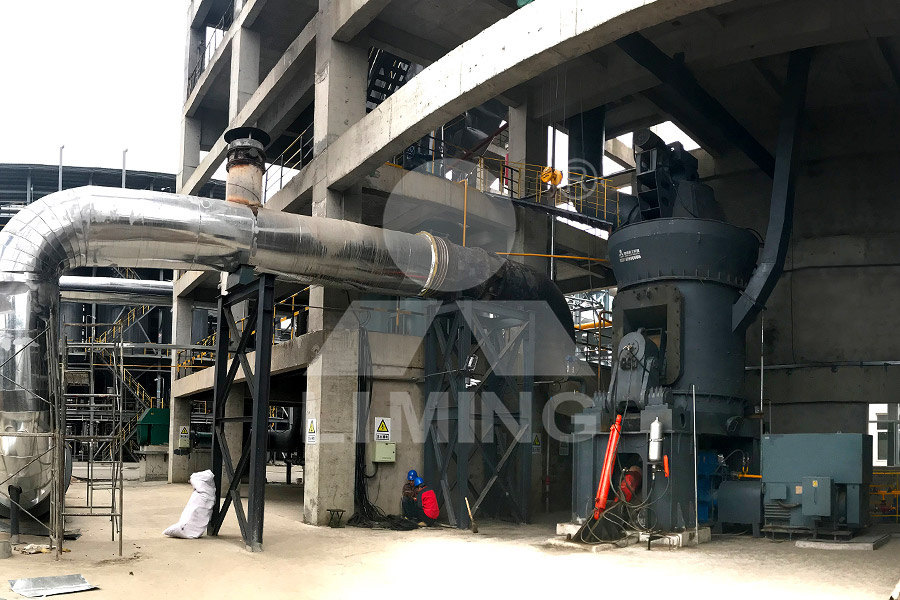
Continuous Ball Mill, Manufacturer, India
Rollers are fixed on the support The ball mill rotates on its axis Mill rotates on four rollers and two tiers It is provided with girth gear along with gearbox and motor Features of Continuous Ball Mill:Low installation cost; Low power consumption; Perforated grinding plates are provided for the final product size Dustproof chamber Our ball mill housing is completely made up of mild steel powder coated The rotating jar cover is designed completely from thick Stainless steel 304 grade Our Ball mill balls are made up of chromeplated mild steel to give vigorous crushing of samples We offer standardsized lab ball mills ranging from 2 kg to 10 kg and tailormade ball Lab Ball Mills 2kg to 100Kg Manufacturer Supplier India Yatherm2015年4月9日 Ball mills Ball mill (Fig 1) is same kind of mill as rod mill, except that it is filled with balls instead of rods Because of balls have greater ratio of surface area than rods they are more suitable for fine grinding Balls are also lighter, so the kinetic energy of a single dropping ball is smaller than a rodGrinding Mills and Their Types – IspatGuru2014年3月1日 Analysis of ball mill grinding operation experimental modeling at a chamber filling degree of 045 were carried out using a monosize ball charge and a single size fraction of the (PDF) Analysis of ball mill grinding operation using mill power

Ball Mill Working Principle Ball Mill Types MC
This design makes the short cylinder ball mill exhibit high efficiency in operation In addition, short cylinder ball mills are usually single chamber structures, which is also an important factor in achieving efficient operation 2 Medium Long Ball Planetary Ball Mill PM 400 for size reduction with the highest degree of fineness powerful short grinding times reproducible results Learn more Automatic grinding chamber ventilation ; 10 SOPs can be stored, Adapter for single Planetary Ball Mill PM 400 RETSCH powerful and Download scientific diagram Internal view of a twochamber ball mill from publication: Radiotracer Investigation of Clinker Grinding Mills for Cement Production at Ghacem Radiotracer Internal view of a twochamber ball mill ResearchGate2013年8月3日 In Grinding, selecting (calculate) the correct or optimum ball size that allows for the best and optimum/ideal or target grind size to be achieved by your ball mill is an important thing for a Mineral Processing Engineer AKA Metallurgist to do Often, the ball used in ball mills is oversize “just in case” Well, this safety factor can cost you much in recovery and/or mill liner Calculate and Select Ball Mill Ball Size for Optimum Grinding
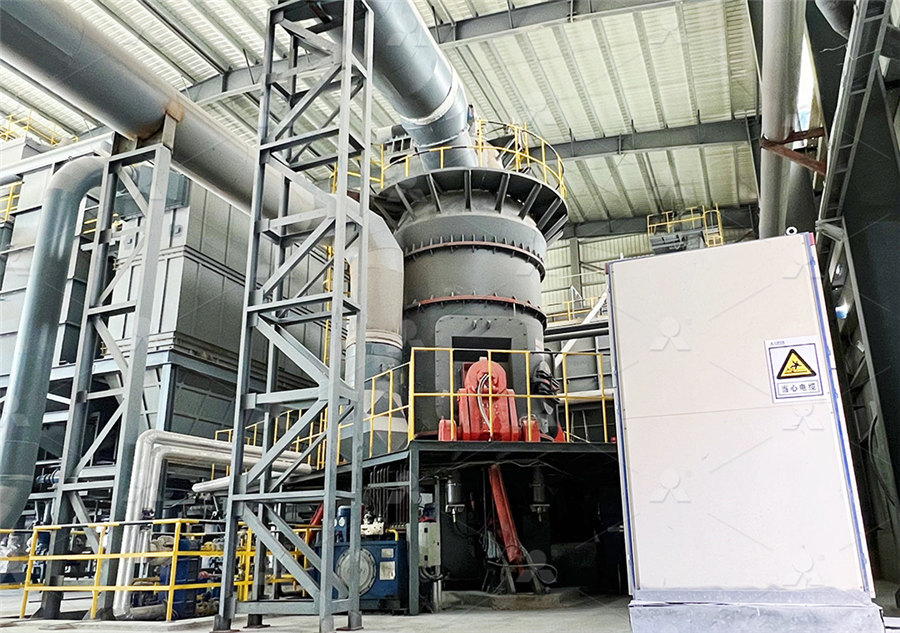
Optimization of Cement Grinding Operation in Ball Mills PEC
The first chamber is filled with larger diameter grinding media and lined with lifting liners The first chamber coarsegrinds the feed material and prepares it for the second chamber The second chamber is the fine grinding chamber It is lined with classifyingtype mill shell liners and provided with finer ball chargeWhen the ball mill is operating, the clinker is fed into the first chamber in the cylinder body through the hollow shaft at the feeding end of the mill When the cylinder rotates, the grinding balls, under the action of inertia, centrifugal force, and friction force, clings to the lining plate inside the cylinder and rotates with itCement Mill for Sale Buy Cement Ball Mill Vertical Roller Mill 2017年2月20日 All Grinding Mill Ball Mill Manufacturers understand the object of the grinding process is a mechanical Ball mills and autogenous mills with metal lining also can be provided with single or double waved plates for the discharge chamber At a bulk weight for balls of 46 kg/dm³ and a charge volume of 40 per cent for Grinding Mill Design Ball Mill Manufacturer 911Metallurgist2015年9月1日 Overflow ball mill grinding chamber with extended discharge head lifter bars single panel and oriented diagonally across the pan el The dam ring at the trommel disc harge end has slo ts Simulation of overflow ball mill discharge and trommel flow using
.jpg)
Ball mill for cement grinding
An inefficient ball mill is a major expense and could even cost you product quality The best ball mills enable you to achieve the desired fineness quickly and efficiently, with minimum energy expenditure and low maintenance With more than 4000 references worldwide, the FLSmidth ball mill is proven to do just thatSmaller plants tend to add extra crushing stages in order to operate a single grinding stage only If a ball mill uses little or no water during grinding, it is a 'dry' mill If a ball mill uses water during grinding, it is a 'wet' mill A typical ball mill China Ball Mill Manufacturers Suppliers FactoryIn the wet grinding of paints and varnishes, the classic ball mill has been completely replaced by the agitatorballmill, The VOLLRATH singlechamber beadmill type VMSM 1/B is ideal for “ReCircular grinding” The optimally BeadMills Vollrath GmbH2021年6月29日 Nowadays, ball mills are widely used in cement plants to grind clinker and gypsum to produce cement The research focuses on the mill speed as well as air classifier speed effect on the two Effects of Mill Speed and Air Classifier Speed on Performance of
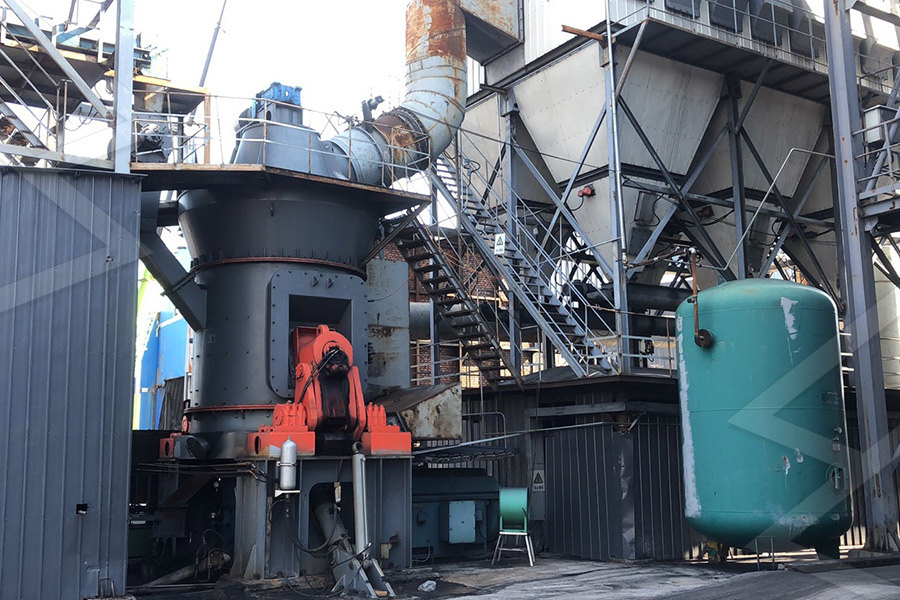
Ball Mill Basket Mill Machine Manufacturer from Thane
Manufacturer of Ball Mill Basket Mill Machine, Premixing, dispersion, compounding and dilution are all accomplished in a single unit that requires less space, less time and less energy to achieve bigger results Technique Milling chamber design eliminates by Fine Grinding and Mill Cooling PROBLEM Insufficient mill cooling lead to material agglomeration on balls and liners The grinding is not any more done by balls against material but by material against material SOLUTION Adapted mill cooling, playing with:Clinker temperatureMill ventilationWater injectionEVERY COMPONENT OF BALL MILL DETAILED EXPLAINED2017年7月26日 We will consider an ore with a ball mill work index varying between 16 and 13, feeding into a single stage ball mill operation with one million kilowatts per day consumed power For the particular mill configuration, a performance graph, Fig (21), has been constructed according to Bond’s methodsHow Ball Mill Ore Feed Size Affects Tonnage Capacity2018年8月7日 In this work, three modelling approaches to DEM implementation to charge motion modelling are compared these being single ball trajectories, system of individual balls describing the mill charge DEM Investigation of Mill Speed and Lifter Face Angle on
.jpg)
Ball Mill SBM Ultrafine Powder Technology
Ball Mill Discharge fineness: 007504 mm Feed size: The working principle of ball mill The material enters the first chamber of the mill evenly and spirally from the feeding device through the feeding hollow shaft it enters the second bin through the singlelayer partition board2013年2月7日 Scheme of a ball motion pattern in a single pot of a planetary ball mill – (a) cascading, (b) cataracting, (c) rolling nfluence of varied frictional coefficients on simulated ball motion Process Engineering with Planetary Ball Mills ResearchGate