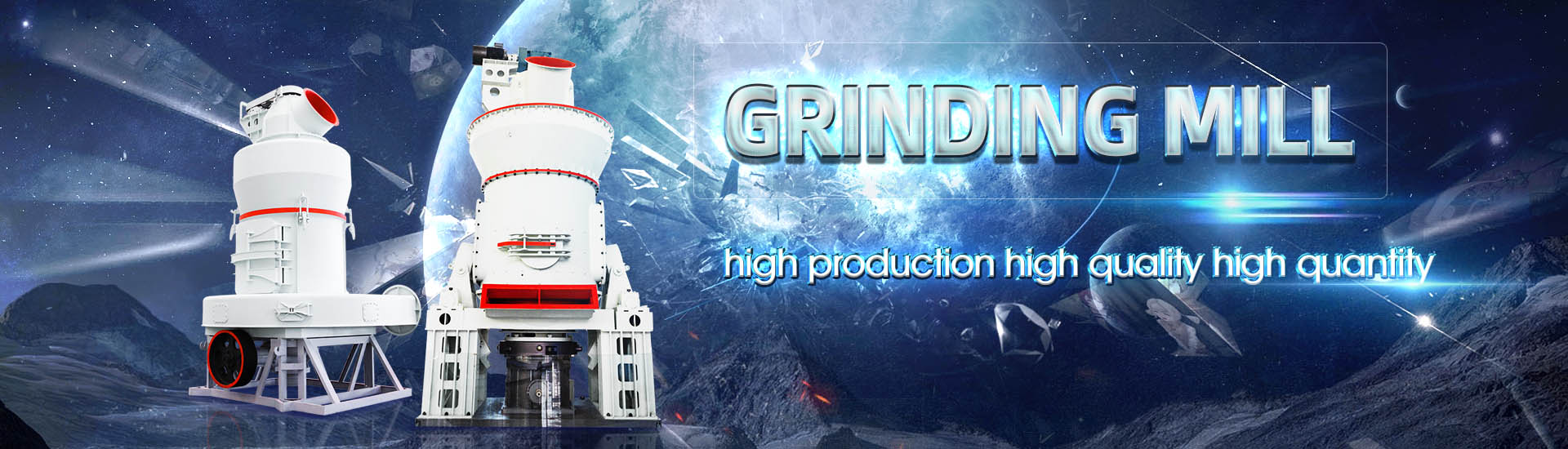
GZ4200 mesh pulverized coal mill quotation
.jpg)
Industrial Bowl Mills Bowl Mill Pulverizer for Sale Wabash Power
Bowl mills supplied by Wabash Power are capable of grinding harder coal with higher percentage moisture content and can reduce the product fineness in excess of 90% passing a 200 mesh screen at a reduced output capacity The feed size of the coal to the mill should be pre Pulverization of coal is currently the favored method of preparing coal for burning Mechanically pulverizing coal into a fine powder enables it to be burned like a gas, thus allowing more Coal Pulverizer – Power Plant Pall Corporation1800 rpm primary air fan, and four mill outlets supplying pulverized coal to one of the three horizontal rows of (4) dualfuel burners When operating at boiler MCR, each mill had a coal throughput of approximately 53,000 #ffir Specified product fineness was 70% thru 200 mesh and 98% thru 50 mesh Diminishing supply of the original Kansas coalWorldProven Coal Pulverizer Technology Debuts in the USCollecting coal samples using an isokinetic probe provides the best data describing actual operating conditions inside the coal pipe Source: Storm Technologies Inc The isokinetic coal sampling method, although more difficult, is the best option for determining the true mill coal fineness produced and to calculate pulverizer performancePulverized Coal Pipe Testing and Balancing Storm Technologies,
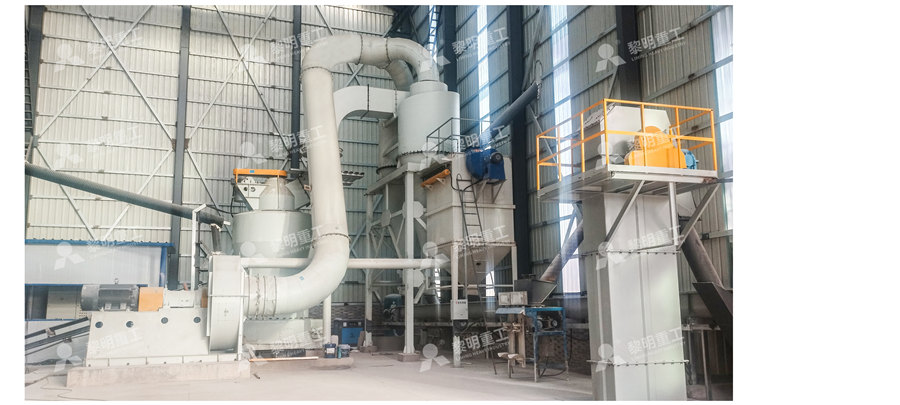
Boiler Mill and Coal Pulverizer Performance GE Steam
Can GE service my boiler mills? YES Our boiler mills and coal pulverizers span the globe and are built in a variety of sizes and capacitiesWe provide customized maintenance solutions, and offer a full spectrum of highquality solutions for 2022年2月24日 Production of clean pulverized coal for boiler combustion heating and power supply Fineness: 200 mesh, D8090, according to the needs of backend combustion Suitable coal types: bituminous coal, anthracite, blue carbon, etc The production of clean pulverized coal is used for boiler combustion heating and power supply to improve the operating efficiency of How is pulverized coal processed? SBM Ultrafine Powder 2011年10月1日 A sample set of results from a vertical air swept pulverizer with a static classifier might be 9925% passing 50 mesh (297 µm), 8738% passing 100 mesh (149 µm), 7212% passing 140 mesh (105 µm Improved Coal Fineness Improves Performance, Reduces EmissionsSection of coal bowl mill Table 1 Guaranteed coal conditions for mill performance evaluation Coal Moisture % 20 Coal HGI 55 Mill Outlet Temperarure °C 80 Mill Air Flow T/hr 102 Coal Fineness (% passing trough 200 mesh) 70% passing through 200 mesh and 90% passing through 50 mesh Differental Pressure 300 mmwc Coal Output from Mill 609 t/hrA Study on 500 MW Coal Fired Boiler Unit’s Bowl Mill
.jpg)
Vertical Grinding Mill (Coal Pulverizer) Explained saVRee
Introduction This article concerns itself with vertical grinding mills used for coal pulverization only (coal pulverizers), although vertical grinding mills can and are used for other purposes The 3D model in the saVRee database represents a vertical grinding bowl millOther grinding mill types include the ball tube mill, hammer mill, ball and race mill, and , roll and ring mill2023年11月20日 HGM series ultrafine grinding mill is used by customers to grind pulverized coal, with an output of 5tph, and a finished powder fineness of 200 mesh It is +17 [ 200 mesh coal pulverizer grinding mill delivery site 20/11/2023 admin HGM series ultrafine grinding mill is used by customers to grind pulverized 200 mesh coal pulverizer grinding mill delivery siteMill connection: the circulating fan is connected to the explosionproof bag dust collector and the inert gas supplement pipe: the inert gas supplement pipe is connected to a heat source system that supplements the low oxygen content heat source gas to the pulverized coal vertical mill to control the low oxygen in the extracorporeal circulation system The limiting oxygen content What is the process flow of vertical mill to produce pulverized coal?This article delves into the properties, benefits, and risks associated with pulverized coal, and outlines essential safety measures to mitigate these risks Properties and Uses of Pulverized Coal Pulverized coal is created by grinding coal into a fine powder, which increases its surface area and enhances its combustion efficiencyUnderstanding Pulverized Coal: Benefits, Risks, and Safety
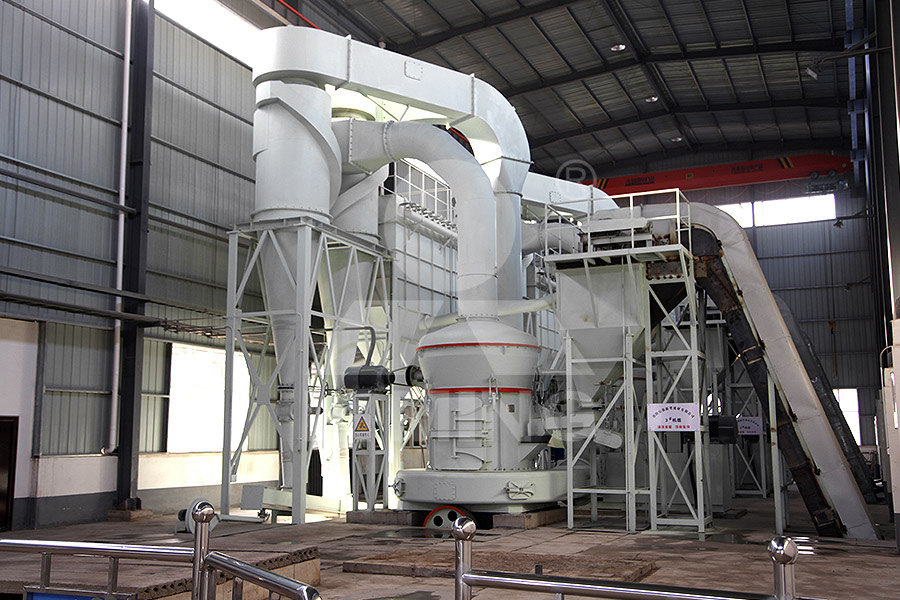
Numerical Study of the Erosion Process and Transport
2022年1月26日 Numerical mesh and geometrical model for pulverized coal ducts for mill 1, mesh for individual ducts and for 4 mills The mesh was refined using the mesh adaptation optionThe BTM is a lowspeed mill that primarily grinds coal by impact and attrition The VRM is a medium speed mill that grinds coal by compression and, because of the low coal inventory in the mill and flat grinding surfaces, develops shearing action as well For both mills a constant centrifugal force is maintained The speedA Comparison of Three Types of Coal Pulverizers Babcock Powerof 10 percentage points passing through 200 mesh and over 1 percentage point improvement passing through 50 mesh cool air comes in contact with the pulverized coal Easy Access for Maintenance Created Date: 11/29/2018 11:18:41 AM RILEY POWER’S ATRITA COAL PULVERIZERS RELIABLE COSTEFFECTIVE Pulverization of coal is currently the favored method of preparing coal for burning Mechanically pulverizing coal into a fine powder enables it to be burned like a gas, thus allowing more efficient combustion Transported by an air or an air/gas mixture, pulverized coal can be introduced directly into the boiler for combustionCoal Pulverizer – Power Plant Pall Corporation
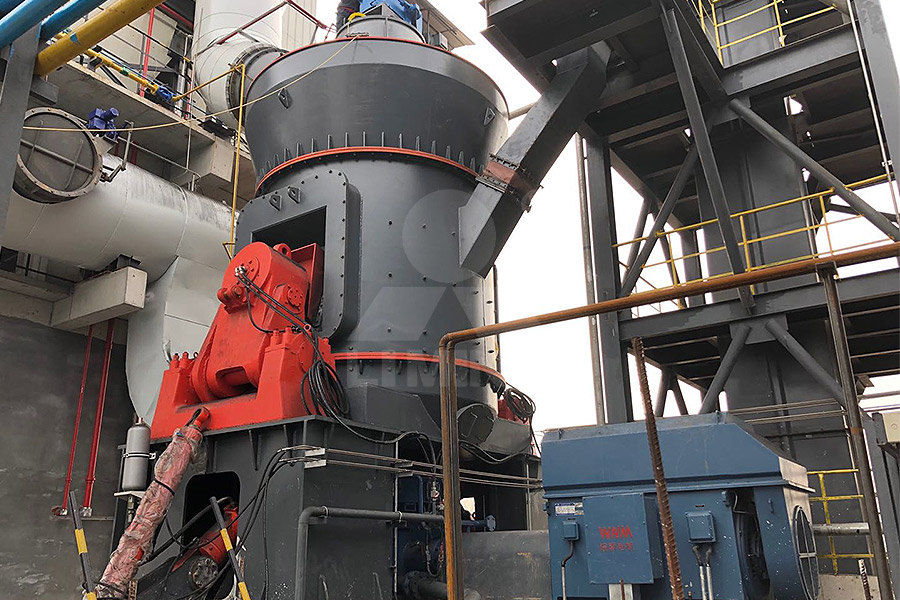
Pulverized Coal Preparation Pulverized Coal Grinding Plant Coal
★ Pulverized Coal Preparation System 1 The raw coal from storage and conveying system come into air swept coal mill for grinding The coal powder mass and heat transfer with 200℃~350℃ hot air The moisture enter into flue gas from coal Coal powder is dried by hot air Then coal powder come to powder separator with airflow for ONLINE COAL FLOW MEASURING AND BALANCING (CONTROL) AND ONLINE COAL FINENESS MEASURING SYSTEM FOR COMBUSTION OPTIMISATION IN A THERMAL BOILER Suresh G Chandwani1, Dr Francesco Turoni2, Reinhardt Kock2, Dr Michael Haug2, Dr Michael Schreiber2 1NSGuzder Company Pty Ltd, Neville House, Currimbhoy Road, CPRI Online Coal Flow Balancing and Fineness AdjustmentFuel preparation for a pc boiler occurs in a mill, where coal is typically reduced to 70% through a 200mesh (74μm) screen Figure 2 shows a particlesize distribution from a bowlmill grinder typically used in power plants A typical utility specification for particle size distribution of the coal is that 70% of the mass should pass through a 200mesh screen, which is equivalent to 70% Pulverized Coal Boiler an overview ScienceDirect TopicsElectric Power Company who introduced pulverized coal firing in power stations Pulverized coal is the most efficient way of using coal in a steam generator The coal is ground so that about 70 % will pass through 200 mesh (0075 mm) and 99 % will pass through 50 mesh (0300 mm) A pulverized coal boiler can be easily adapted for other fuels Coal Pulverising in Boilers
.jpg)
Pulverised Coal Combustion an overview ScienceDirect Topics
161 Pulverized coal combustion In pulverized coal combustion (PCC), dust burners are used to feed coal into the combustion chamber, where flame core zones of the combustion chamber having a temperature range between 1450°C and 1600°C are present To attain the required efficiency, pulverized coal is given a swirling motion around the flame 2024年1月11日 With a vertical roller mill (VRM) VRMs consist of a rotating table or bowl and rollers 1 To grind the coal, feed raw or initially crushed coal into the mill which is then ground between the rotating components; 2 Finally, hot air How to Process Coal into Pulverized Coal in 5 Steps?A coal mill is also called a coal pulverizer or coal grinder It is a mechanical device used to grind raw coal into pulverized coal powders The most used coal mills in cement plants are airswept ball mills and vertical roller mills At present, most Coal Mill in Cement PlantNomenclatureBowl Mills 583 XRS / 803 XRP Bowl mills 58,80 stands for bowl diameter in inches If the number is even then its shallow bowl mill If the number is odd then its deep bowl mill 3 number of rollers three nos X frequency of power supply 50 cyclesIn USA ’x’ means 60 cycles R Raymond, name of the inventorPulverizer Plant OM Aspects
.jpg)
Coal and Mill PDF Mill (Grinding) Mechanical Engineering
Coal and mill Free download as PDF File (pdf), Text File (txt) or view presentation slides online The document discusses pulverized coal mills used in power plants It describes different types of mills including tube mills, ball mills, and bowl mills Tube mills are low speed while bowl mills are medium speed The document explains the construction, operation, and maintenance of bowl Pulverization of coal is currently the favored method of preparing coal for burning Mechanically pulverizing coal into a fine powder enables it to be burned like a gas, thus allowing more efficient combustion Transported by an air or an air/gas mixture, pulverized coal can be introduced directly into the boiler for combustionCoal Pulverizer – Power Plant Pall Corporationin the mining or coal processing operations Fig3 Mill fuel piping connections to furnace II COAL MILL SPECIFICATIONS PERFORMANCE ANALYSIS Typical Coal Pulveriser Mill Details in 660 MW SuperCritical [3] Unit is as given in table Table No 1 Table1 Coal mill Type Bowl Type Mediumspeed Coal mill Number of Mills 6set/ boilerPulveriser Mill Performance Analysis Optimisation in SuperA simple energy balance model of the coal mill is derived in (Odgaard and Mataji 2006), this model is based on a more detailed model found in (Rees and Fan 2003)In this model the coal mill is seen as one body with the mass m mThe following variables are defined: T(t) is the temperature in the coal dust flow in the mill, ṁ PA (t) is the primary air mass flow, T PA (t) is Coal Mill an overview ScienceDirect Topics
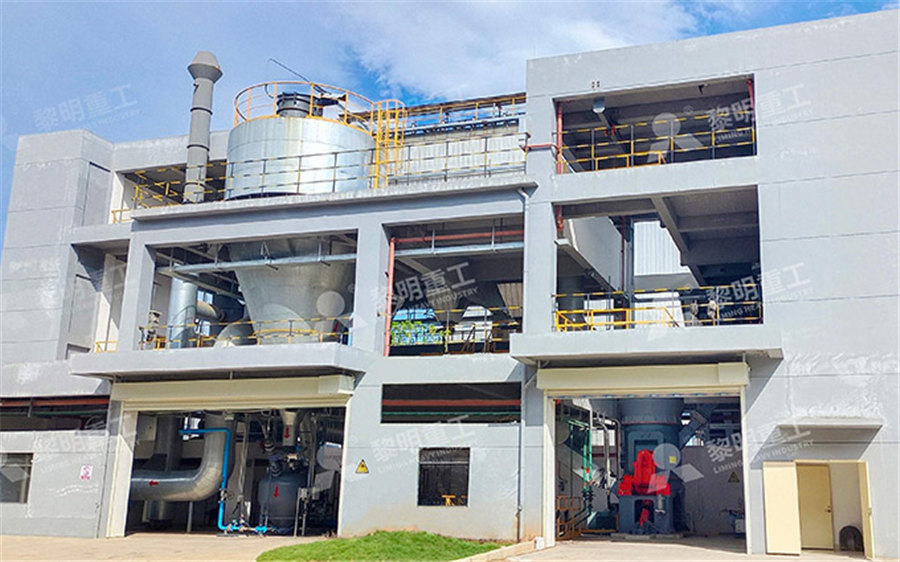
Pulverised Coal an overview ScienceDirect Topics
With a PCfired unit, the coal is first pulverized in a mill to the consistency of talcum powder, which means that at least 70% of the particles will pass through a 200mesh sieve The pulverized coal is generally entrained in the primary combustion air before being blown through the burners into the combustion chamber, where it is fired in in the mining or coal processing operations Fig3 Mill fuel piping connections to furnace II COAL MILL SPECIFICATIONS PERFORMANCE ANALYSIS Typical Coal Pulveriser Mill Details in 660 MW SuperCritical [3] Unit is as given in table Table No 1 Table1 Coal mill Type Bowl Type Mediumspeed Coal mill Number of Mills 6set/ boilerPulveriser Mill Performance Analysis Optimisation in Super Technical Cement Forum / Coal Mill Pulverized Coal 200 Mesh The forum in now closed, please join us on the International Cement Review Linkedin Group eric 13/07/2010 17:39:26 Coal Mill Pulverized Coal 200 Mesh Coal Michael Clark 14/07/2010 15:30:20 Coal Mill Pulverized Coal 200 Mesh International Cement Review2024年8月23日 Hourly production of 3120 tons of coal mill, 200 mesh pulverized coal processing equipmentHourly production of 3120 tons of coal mill, 200 mesh pulverized coal
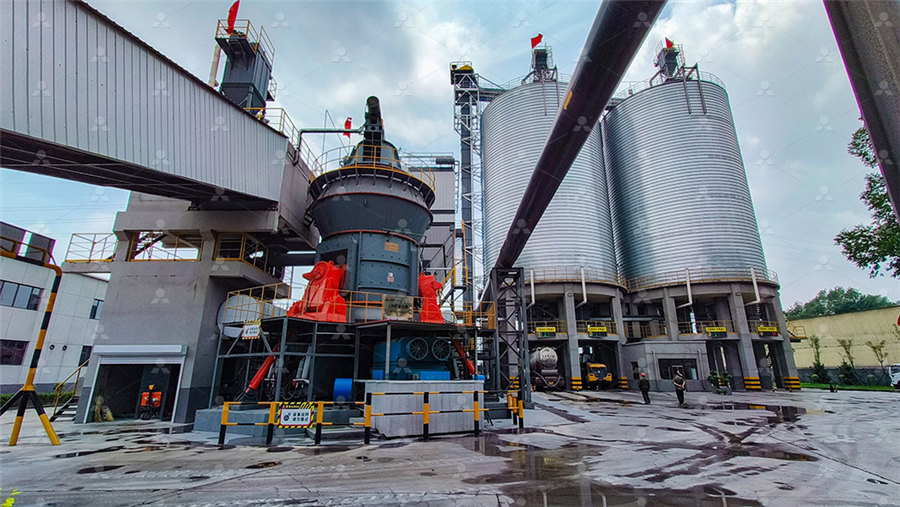
Understanding Pulverized Coal Injection in Blast Furnace
2018年10月21日 Fig 1 Pulverized coal combustion and gas composition in raceway The extent of combustion (combustion efficiency), and hence the amount of unburnt material transported out of the raceway, depends on several parameters which include (i) properties of the coal, such as the VM content, particle size and density, and (ii) operating conditions, for example, blast gas The design “capacity” of the same pulverizer will grind 135,000 pounds per hour with fuel that is 55 HGI (Hardgrove Grindability Index) coal, ¾” raw coal top size, 7% moisture and produces pulverized coal that is 70% passing 200 mesh fineness (red line) This is pretty standardThe Storm Approach to Coal Pulverizer Optimization2019年2月14日 The aim of present paper is to review various aspects of pulverized coal combustion such as oxyfuel combustion, cocombustion of coal and biomass, emissions from pulverized coal furnaces, ash formation and deposition, and carbon capture and sequestration (CCS) technologies to outline the progress made in these aspectsA complete review based on various aspects of pulverized coal 2019年5月10日 Monitoring Coal mill Performance 55% Capacity to grind 70% thro 200 mesh – Lb/hr Case – 2 HGI Index – 50% Capacity to grind 70% thro 200 mesh – Lb/hr Case – 3 HGI Index At lower PA flows the pulverized coal is in danger of falling out of suspension and laying out in the coal conduits, Monitoring Coal mill Performance PPT SlideShare
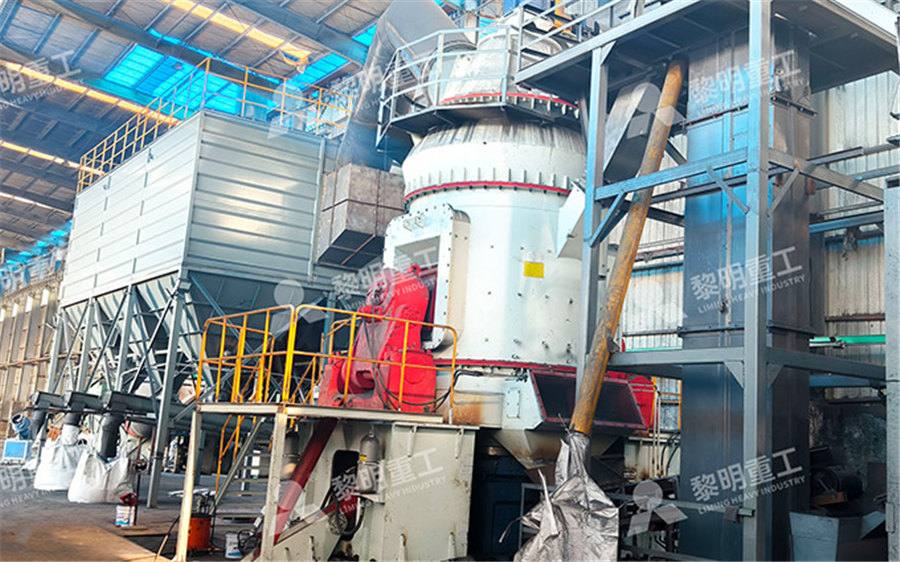
Coal Pulverizers an overview ScienceDirect Topics
Gas turbine combined cycle Shigehiro Shiozaki, Akira Yamada, in Advances in Power Boilers, 2021 637 Gasifier facilities 6371 Coal pulverizing and feeding system The purpose of the coal drying system is drying and grinding the raw coal for stable transportation of pulverized coal to gasifier and stable/highefficiency gasification at the gasifierEffective pulverized coal storage is vital for the safe and efficient operation of coalfired industrial processes utilizing coal By understanding the storage methods, safety considerations, and technological advancements, industries can mitigate risks, improve efficiency, and minimize environmental impactPulverized Coal Storage: Essential Practices and Considerations Coal IN COAL PULVERIZER MILL Name : Agustin Kurniastuti NRP : 2112 204 808 Advisor : Prof Ir Sutardi, M Eng, PhD ABSTRACT In coal fired power plant, the capacity of coal pulverizer mill to supply pulverized coal (PF) are play an important role to achive efficient combustion inside furnace Grinding, drying and classifying which occur inside coal STUDI NUMERIK PENGARUH TEMPERATUR UDARA PRIMER After the primary air powder is sent into the plasma ignition pulverized coal burner, the dense phase pulverized coal enters the central area of the plasma torch and catches fire quickly within about 01s, and provides a high temperature heat source for the light phase pulverized coal, so that the light phase pulverized coal also catches fire quickly, and finally forms a stable Pulverized Coal Burner Pulverized Coal Burner For Rotary Kiln