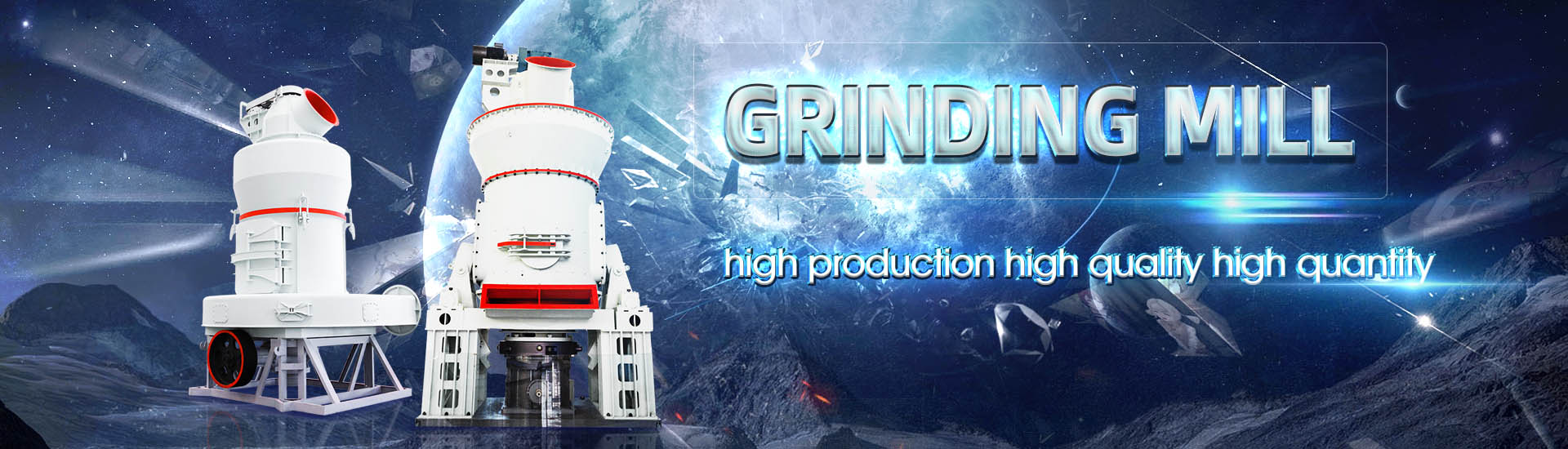
How to calculate the operating cost of large lepidolite ore grinding mill
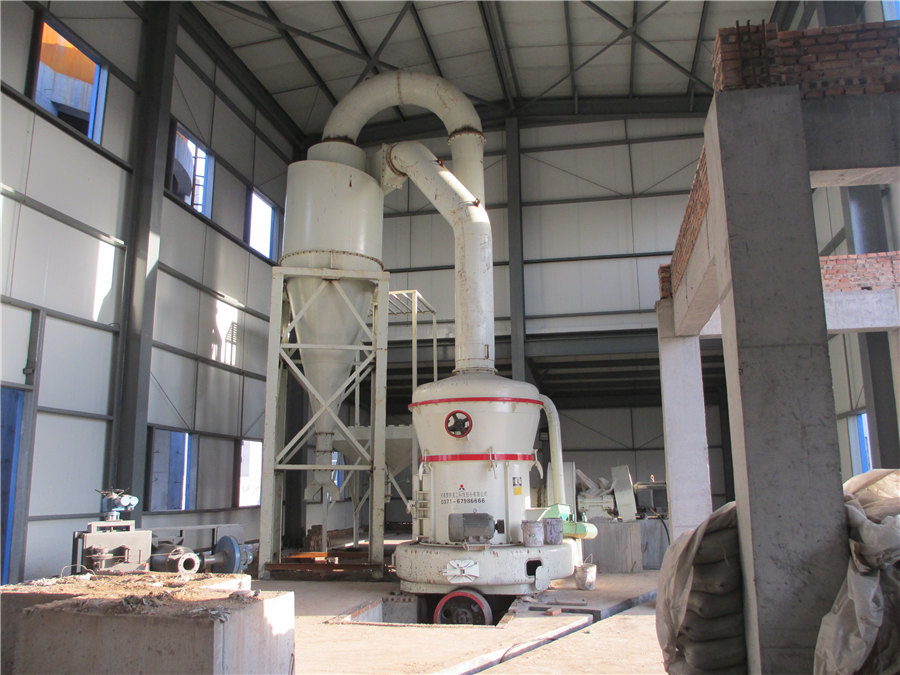
COSTS AND COST ESTIMATION Chapter NUBE MINERA
Accurate operating costs are estimated from the quantities and unit costs of all components of supplies and labor, as deter mined by accurate knowledge of the ore body, the mine planning,2023年1月1日 When the price of lepidolite concentrate is 227–303 $/t, the production cost of lithium carbonate is about 1061 k$/t (Hu Z, 2019) The above research shows that the Lithium extraction from hard rock lithium ores (spodumene, 2014年2月1日 This paper provides a breakdown of operating costs in 63 mines by dividing them into three main categories: mining, milling, and general and administrative (G A) costs The Mine operating costs and the potential impacts of energy and 2022年9月1日 The main findings obtained by adopting different mineralprocessing strategies for lepidoliteore upgrading are presented in this work, including preconcentration at coarse sizes Separation of lepidolite from hardrock pegmatite ore via dry

Treatment of an Indigenous Lepidolite Ore for Sustainable Energy
2022年2月10日 Consequently, the treatment of a Lepidolite ore was investigated for lithium extraction and purification through a combination of sodium carbonate roasting and water 2015年7月28日 In open pit mine planning, many factors affect total fixed and operating costs, such as haulage costs, particularly when the mine goes deeper, geomechanical features of the (PDF) Determination of Optimum Production Capacity and Mine Capital intensity and operating costs are more competitive than for production of lithium carbonate: Elimination of sodium sulphate circuit; significant capital equipment and byproduct Developing High Purity Lithium Chemicals from LepidoliteConsequently, the present study treated an indigenous Nigerian sourced lepidolite ore by moderate carbonate roasting and water leaching to obtain a product that could be used as a Treatment of an Indigenous Lepidolite Ore for Sustainable Energy
.jpg)
Lithium extraction from hard rock lithium ores (spodumene,
2023年1月15日 The processing cost of lithium extraction from lepidolite by sulfate roasting method is higher than that from spodumene by sulfuric acid due to the consumption of high This paper focuses on the research progress of extracting lithium from spodumene, lepidolite, petalite, and zinnwaldite by acid, alkali, salt roasting, and chlorination methods, and analyzes Technology, resources, environment and cost2017年1月17日 Grinding mills are infamous for their extremely low energy efficiency It is generally accepted that the energy required to produce new mineral surfaces is less than 1% of the electricity consumed Breaking down energy consumption in industrial 2016年3月19日 To aid in arriving at approximate operating costs, we are giving four charts with curves showing operating costs for the different standard methods of treating ores These charts show the costs compiled from actual Operating Costs of Gold Processing Plant
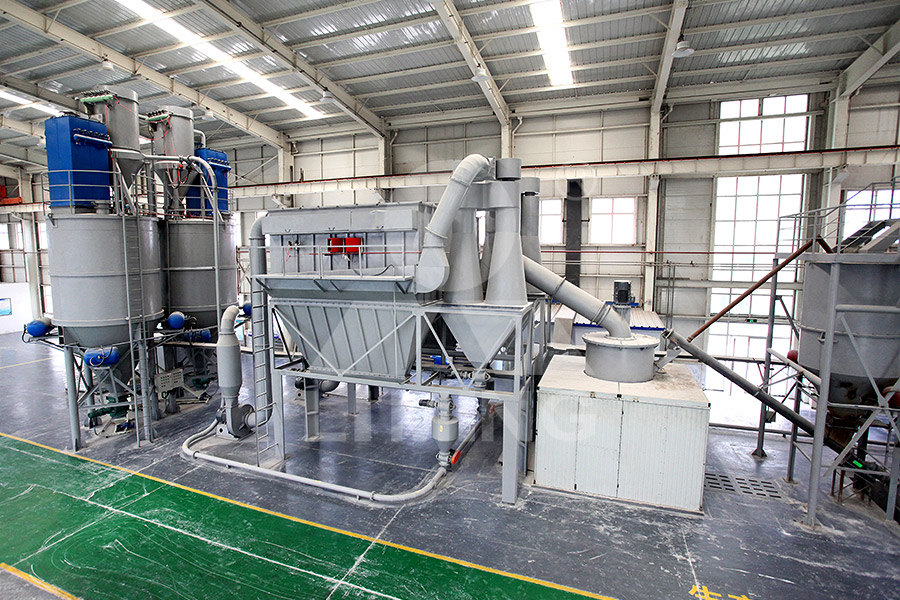
The economics of large scale ore sorting
2014年1月1日 The challenge for large lowgrade ore bodies is to crush and sort at coarser rock size in order to minimise specific energy consumption in comminution and to reduce waste disposal costs For large 2022年9月1日 For example, the dry processing of micas offers two benefits: (i) The reduction of the negative impact of coarse micas on the grinding process; thus, improving the efficiency of the comminution stage, and (ii) reduction of the operating costs (less ore sent to the fine grinding process and no drying stage for the products obtained by electrostatic separation)Separation of lepidolite from hardrock pegmatite ore via dry The costs of extracting the metal from the ore and other operating expenses are not deducted from the mineral deposit value As a result, a major or midtier mining company that wants to replace their mined reserves might pay only a small percentage of this metal value for the deposit (eg, 5% to 10%)Mineral Deposit Value How to Calculate the Potential Value 2016年9月1日 Plot showing relationship between the daily capacity of straight cyanide plants and the overall cost per ton of ore treated The figures are based on an average of a number of Canadian producers The operating costs for straight cyanide plants show a greater uniformity than is the case for plants employing combinations of cyanidation and flotationMineral Processing Operating Cost Estimate of Ore Treatment
.jpg)
Common Basic Formulas for Mineral Processing Calculations
2016年3月21日 Pulp Densities Pulp densities indicate by means of a tabulation the percentages of solids (or liquidtosolid ratio) in a sample of pulp This figure is valuable in two ways—directly, because for each unit process and operation in milling the optimum pulp density must be established and maintained, and indirectly, because certain important tonnage calculations are Ball mill optimisation As grinding accounts for a sizeable share in a cement plant’s power consumption, optimisation of grinding equipment such as ball mills can provide significant cost and CO 2 emission benefits to the cement producer of large grains These cannot be ground by an unadjusted ball charge andBALL MILLS Ball mill optimisation Holzinger Consultingcosts and operating costs The contingency allowance expresses the probability of capital costs and operating costs being higher than anticipated when it is difficult to determine the precise characteristics of an aspect of the mine or plant Because accurate cost estimation requires tailoring of mineCOSTS AND COST ESTIMATION Chapter NUBE MINERAN Vieceli et al, Kinetic approach to the study of froth flotation applied to a lepidolite ore 733 dustriais, SA (MOTA® Ceramic Solutions) Samples for flotation tests were prepared through successive stages of screening and fine crushing in a roll crusher (Sturtevant)Kinetic approach to the study of froth flotation applied to a IPG
.jpg)
Calculating the value of iron ores in ironmaking
2011年1月1日 At present we are witnessing large investments in the iron ore industry, fuelled by demand from Asia At the same time, there is a changing landscape in pricing of iron ores, with the recent 2022年1月1日 Lithium extraction from hard rock lithium ores (Spodumene, Lepidolite, Zinnwaldite, Petalite): Technology, resources, environment(PDF) Lithium extraction from hard rock lithium ores: technology 2024年6月28日 In addition, large but extraneous costs are not represented, which may also show a company with a negative net profit having a positive operating profit Operating Profit: NonOperating Income and Operating Profit: How to Calculate, What It Tells You, The required power consumption of a grinding mill based on the calculations shown above can be estimated thanks to this free Excel calculator : Calculation Tool Grinding Mill Power Calculation Warning : this calculator is provided to illustrate the concepts mentioned in this webpage, it is not intended for detail design Grinding power : step by step calculation PowderProcess
.jpg)
Equipment Sizing: Crusher or Grinding Mill 911Metallurgist
2016年7月8日 UNTIL THE THIRD THEORY OF COMMINUTION of “Work Index” method of determining crushing and grinding mill size was introduced, there was no way of accurately figuring the most applicable, most economical size of crushing and grinding mill Naturally, with little or no factual operating data correlated in useful form, it was easy enough, even for the 2021年2月1日 Recently, there has been a steady increase in demand for lithium (Li) and its compounds, accounting for 10% over the past decade The level of production and industrial use of lithium currently Processing of lithium ores: Industrial technologies and case studies 2023年1月1日 When the price of lepidolite concentrate is 227–303 $/t, the production cost of lithium carbonate is about 1061 k$/t (Hu Z, 2019) The above research shows that the production cost of extracting lithium from ores is closely related to the price of lithium concentrate, which is much higher than that of extracting lithium from brineLithium extraction from hard rock lithium ores (spodumene, lepidolite 2016年12月28日 Regarding the optimization of cost for internal and external grinding processes, several previous researches presented the cost function based on the grinding parameters [11][12][13][14][15]Cost Optimization of Surface Grinding Process ResearchGate
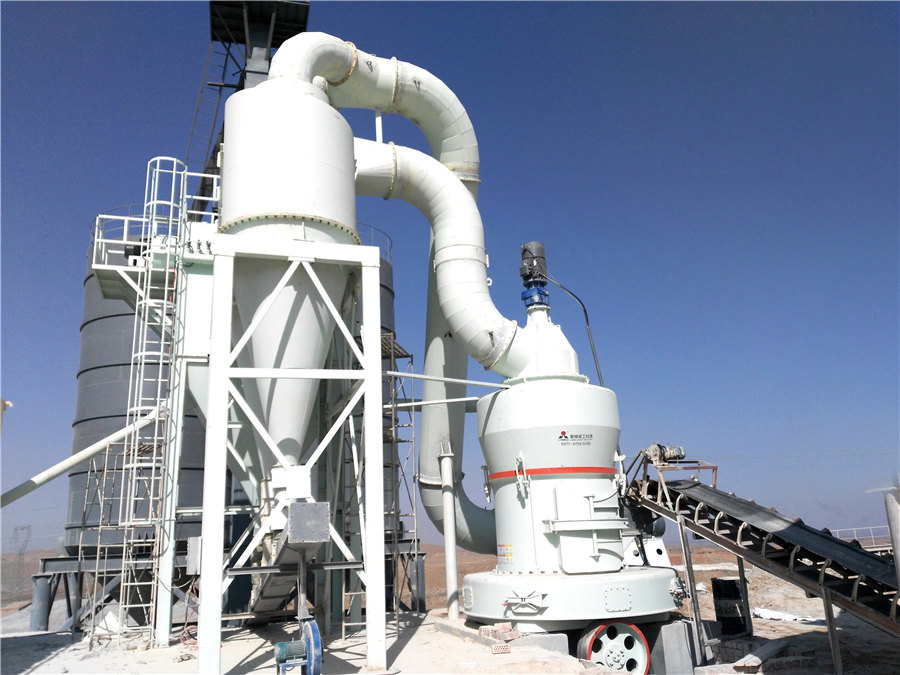
CNC Machining Costs: Tips and Strategies For CostSaving
2023年12月7日 To understand the cost of CNC machining, it’s essential to delve deeper into the process itself CNC, or Computer Numerical Control machining, is a manufacturing technique that uses automated, highspeed cutting tools to form shapes from metals and plasticsStandard CNC machines, such as lathes, routers, and milling machines with 3, 4, and 5 axes, are employed 2017年2月13日 In all ore dressing and milling Operations, including flotation, cyanidation, gravity concentration, and amalgamation, the Working Principle is to crush and grind, often with rod mill or ball mill, the ore in order to liberate the minerals In the chemical and process industries, grinding is an important step in preparing raw materials for subsequent treatmentBall Mills 911Metallurgist2021年10月7日 The paper discusses the process of lithium mining, from resource exploration to the production of batterygrade lithium salts(PDF) Lithium Mining, from Resource Exploration to 2009年1月1日 Traditionally, the lowest operating cost was achieved by multistage, fully autogenous grinding since this eliminated the steel grinding media costs which may represent up to 50% of the grinding costProcessing of Magnetite Iron Ores–Comparing
.jpg)
Hard Rock Lithium Processing SGS
efficient crushing and grinding circuits using both power and modelbased methods We can design bankable circuits and provide operating advice to maximize milling efficiency, considering both steel and power consumption Our practical experience also ensures that we recommend effective circuit configurations that offer ease of operation2024年6月28日 Economies of scale can allow large companies to sell the same goods as smaller companies for lower prices We calculate operating costs as $213 billion + $439 billionOperating Costs Definition: Formula, Types, and RealWorld 2016年1月1日 The wear of balls used during a grinding process is considered one of the losses that cause an increase in the operating cost allocated to the ball mill [21] Ball wear occurs due to abrasion A comparison of wear rates of ball mill grinding mediaAssuming a typical large openpit mining cost of £125 t −1 of ore, a milling cost of £2 t −1 and indirect costs of £2 t −1, the mine will lose £203 for every ton of ore treated The breakdown of costs and revenues, following the example for tin ( Figure 117 ), is given in Figure 119 Milling Cost an overview ScienceDirect Topics
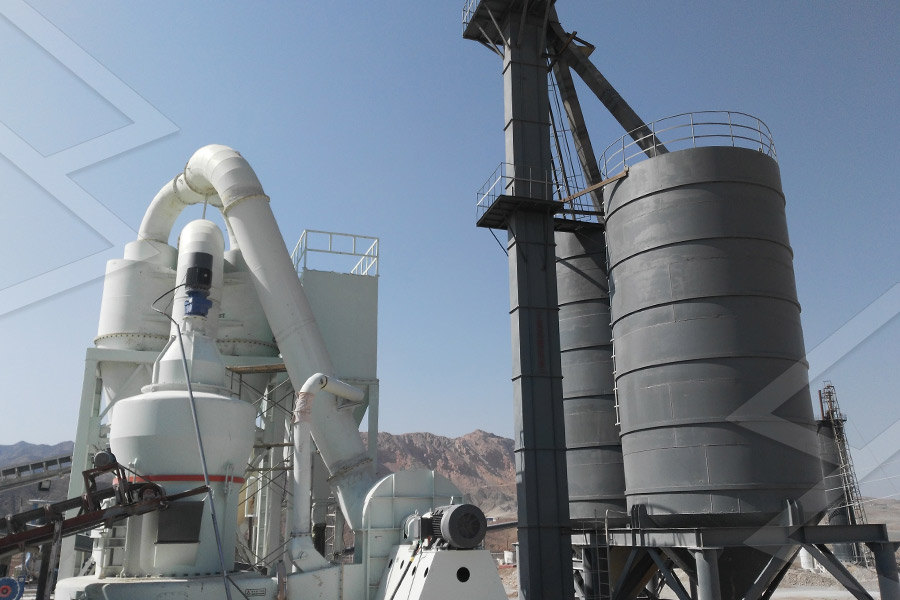
Operating Costs: Definition, Formula, and Example QuickBooks
Operating Cost Formula To determine your business' operating costs, you'll need to go through your income statement for the specific accounting perio d, then use the following formula: Operating Cost = Cost of Goods Sold + Operating Expenses (OPEX)COGS includes all expenses that are directly associated with the production of goods or services, including the following This type of mill has been widely used in mineral processing plants for decades due to its high efficiency and low operating cost Moreover, it can grind large quantities of ores at once without needing any The rod mill is another type of grinding mill used in the copper ore mining process This machine uses steel rods as the grinding Understanding the SAG Mill in Copper Ore Mining ProcessThe head assay of a copper ore is 08% Cu The expected overall copper recovery from the ore is 88% Calculate the maximum stripping ratio if the total cost of production (excluding overburden removal) is $590per ton ofore andoverburden removal costs are$03per ton ofwasteAssume copper valuesof$100,Chapter Open Pit Miningmodel earlier developed by Heyman and Lindström in order to calculate the cost per metric ton within the world of crushing and screening By implementing the cost calculation in Microsoft excel it would be more user friendly and applicable when calculating the cost in crushing and screeningCost Analysis for Crushing and Screening – Part II
.jpg)
Froth flotation separation of lepidolite ore using a new Gemini
2021年6月1日 They found that the synergy effects of the carboxyl group and amino groups can enhance the selectivity of CEA to fluorite and calcite [8] Huang et al, indicated that the Gemini surfactant of 2019年1月15日 There are two economic sources of lithium; brines and hard rock ores The majority of the global lithium production, greater than 60%, is produced from brines while lithium ores accounted for the remaining production (Ebensperger et al, 2005)Table 1 summarises the world’s major lithium producers from ores and brines, and the total reservesThe beneficiation of lithium minerals from hard rock ores: A 2022年1月1日 Application of more efficient grinding technologies developed in the last 30 years, including high pressure grinding rolls (HPGR) for fine crushing and stirred milling for fine grinding, has provided opportunities to further reduce the operating costs associated with minution and classification technologies of iron ore2023年1月15日 Lithium production in China mainly depends on hard rock lithium ores, which has a defect in resources, environment, and economy compared with extracting lithium from brine This paper focuses on the research progress of extracting lithium from spodumene, lepidolite, petalite, and zinnwaldite by acid, alkali, salt roasting, and chlorination methods, and analyzes Lithium extraction from hard rock lithium ores (spodumene, lepidolite
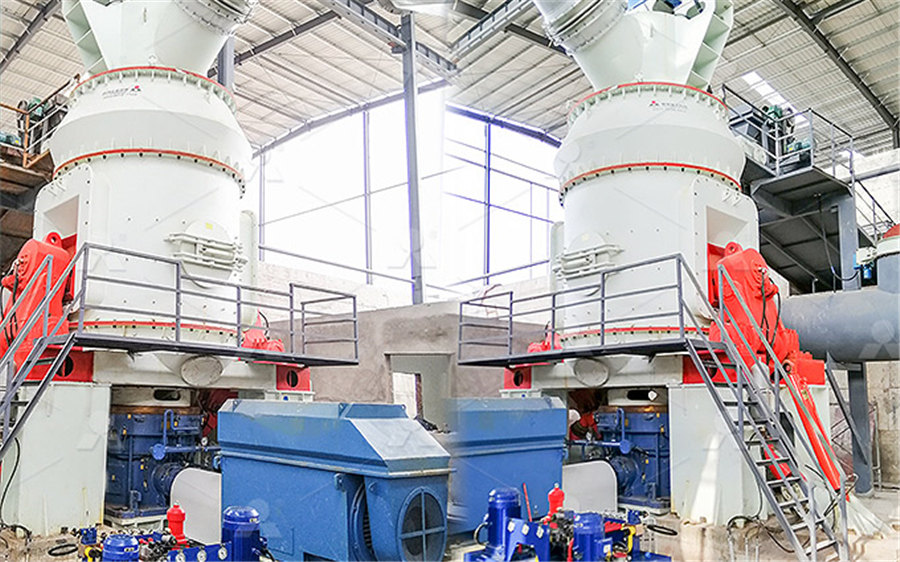
SAG Mill Optimization using Model Predictive Control Andritz
exhibits many of these aspects Maintaining the SAG mill weight at the optimum value is critical for achieving maximum grind rate efficiency and mill production (Powell, MS, van der Westhuizen, AP, Mainza, AN 2009) However, SAG mill weight is difficult to control as the dynamic response changes as the mill approaches maximum capacity2018年4月20日 The first two Grinding Efficiency Measurement examples are given to show how to calculate Wio and Wioc for single stage ball mills Figure 1 The first example is a comparison of two parallel mills from a daily operating report Mill How to Measure Grinding Efficiency 911Metallurgistlithium ore • Fast detection of impurities or offspec ore mineralogy • BT XRD in laboratories or containers or an automated environment 46 Title of the presentation 21 October 2020 Mineralogical monitoring of lithium ores and brines Fast decision making and counteractions on changing conditions, reduced operational costsAccurate mineralogical analysis for lithium ore processing Analyse Understanding Mine to Mill is presented in five parts Part A – Setting the Scene provides some definitions of Mine to Mill (M2M) and the historical background A chronology of Mine to Mill developments is followed by brief descriptions of the very wide range of Mine to Mill applications which have been implemented over the last 15 yearsUNDErsTaNDINg MINE TO MILL 911 Metallurgist
.jpg)
Factors Affecting Ball Mill Grinding Efficiency
2017年10月26日 The following are factors that have been investigated and applied in conventional ball milling in order to maximize grinding efficiency: a) Mill Geometry and Speed – Bond (1954) observed grinding efficiency to be a function of ball mill diameter, and established empirical relationships for recommended media size and mill speed that take this factor into 2013年12月18日 Fine grinding, to P80 sizes as low as 7 μm, is becoming increasingly important as mines treat ores with smaller liberation sizes This grinding is typically done using stirred mills such as the Isamill or Stirred Media Detritor While fine grinding consumes less energy than primary grinding, it can still account for a substantial part of a mill’s energy budget Overall Energy Use of Fine Grinding in Mineral Processing