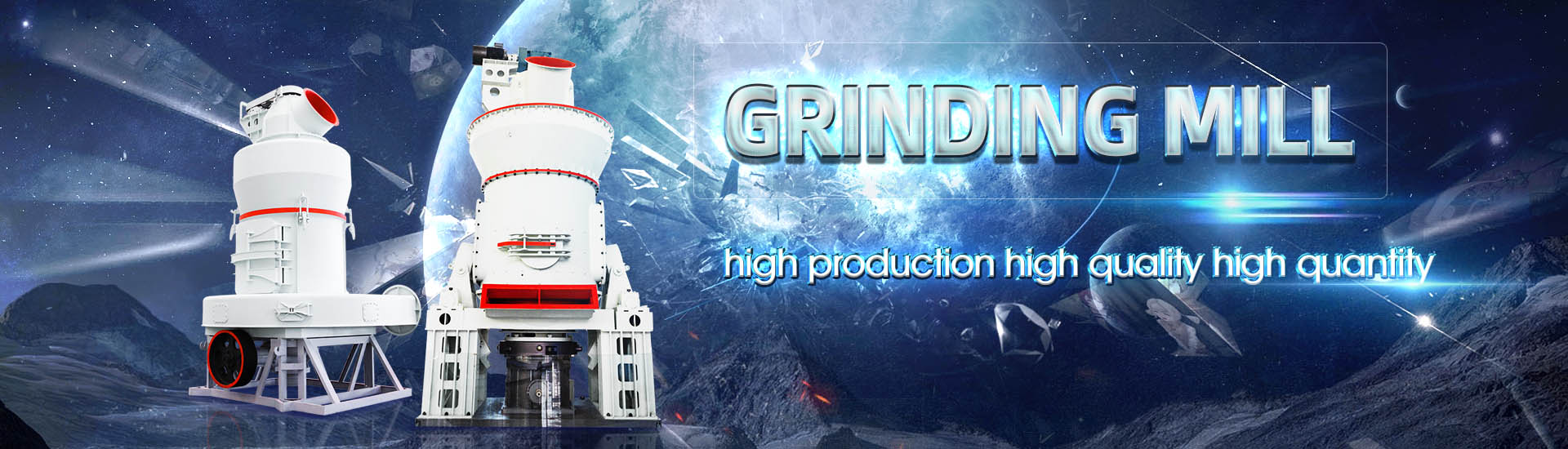
Two methods of pyrometallurgical lead smelting
.jpg)
(PDF) Pyrometallurgy ResearchGate
2016年1月1日 Pyrometallurgical methods are commonly used to process highgra de ores, such as iron ore, while hydrometallurgical and electrometallurgical met hods are often used in combination to extractTo remove and recover remaining impurities from lead bullion, either pyrometallurgical or electrolytic refining is used; the choice between the two methods is dictated by the amount of bismuth that must be eliminated from the Lead processing Refining, Smelting, Alloying Britannica2023年10月27日 Two basic pyrometallurgical processes are used to obtain lead from lead (II) sulphide or mixed concentrates of lead sulphide and zinc sulphide: sintering/smelting (Imperial Smelting Process, ISP) or direct smelting These Zinc and Lead Metallurgical Slags as a Potential Source 2018年1月19日 This review presents and compares the different technologies available for pyrometallurgical processing of secondary lead materials Smelting is most often achieved in Pyrometallurgical Processing of Secondary Lead Material: An
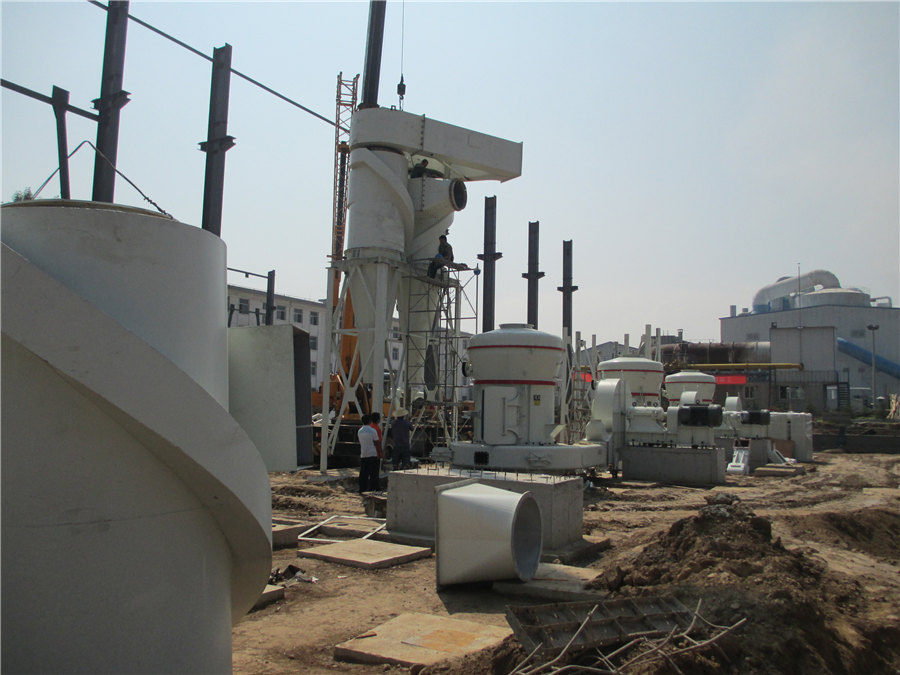
Metals Special Issue : Fundamentals of Advanced
2022年12月31日 Some examples include HIsmelt in ironmaking, oxide metallurgy in steelmaking and oxygen bottom blowing in copper and lead industry These new technologies have enabled complex primary and 2018年3月11日 This review presents and compares the different technologies available for pyrometallurgical processing of secondary lead materials Smelting is most often achieved in Pyrometallurgical Processing of Secondary Lead Material: An 2 Lead Smelting Almost all lead concentrates are processed pyrometallurgically Most primary lead is smelted through the sintering–blast furnace route Direct smelting processes an Lead Smelting an overview ScienceDirect Topics2021年1月26日 Though there are many variations, there are two basic and widely accepted smelting methods: flash smelting and bath smelting Flash smelting involves using oxygenated A Review of Recent Advances in Pyrometallurgical Process
.jpg)
Modified pyrometallurgical technology for recovery of impurities
The pyrometallurgical purification process start when that leads bullion melts in a 20 tons kettle capacity for refining process from remaining slag and alloying elements by pyrometallurgical 2023年1月22日 This chapter reviews the waste leadacid battery (LAB) recycling technologies LAB structure, components and use areas are given Pyrometallurgical, hydrometallurgical or combined LAB recycling methods and flowsheets are covered in detail along with possible chemical reactionsWaste LeadAcid Battery Recycling Technologies SpringerLinkThe oldest, and still the most common smelting process for oxide ores involves heating them in the presence of carbon Originally, charcoal was used, but industrialscale smelting uses coke, a crude form of carbon prepared by 232: Principles of Extractive Metallurgy Chemistry 2014年6月6日 Antimonial dust is a byproduct of lead smelting and an important material for extracting antimony A new pyrometallurgical process for producing antimony white from the antimonial dust is reported The process mainly consists of three steps, which are reduction smelting, alkaline refining, and blowing oxidation First, the reduction smelting of antimonial A New Pyrometallurgical Process for Producing Antimony
.jpg)
A New Pyrometallurgical Process for Producing Antimony White
A New Pyrometallurgical Process for Producing Antimony White from ByProduct of Lead Smelting WEIFENG LIU,1 TIANZU YANG,1,3 DUCHAO ZHANG,1 LIN CHEN,1 and YUNFENG LIU2 1—School of Metallurgy and Environment, Central South University, Changsha , China 2—Henan Yuguang Gold Lead Stock Co, Ltd, Jiyuan , China 3—email Pyrometallurgy is a branch of extractive metallurgyIt consists of the thermal treatment of minerals and metallurgical ores and concentrates to bring about physical and chemical transformations in the materials to enable recovery of valuable metals [1] Pyrometallurgical treatment may produce products able to be sold such as pure metals, or intermediate compounds or alloys, suitable as Pyrometallurgy Wikipedia2017年7月10日 Pyrometallurgical processes are a primary method to recover PGMs from spent catalyst3 In general, they can be divided into three groups: smelting, chlorination, and sintering processes Smelting Process The smelting process is the mostly commonly employed approach for concentrating PGMs in many companies with advanced metallurgical and refining Pyrometallurgical Recovery of Platinum Group Metals from Spent 2023年10月27日 Currently, two methods are used to obtain zinc and lead, the pyrometallurgical method and the hydrometallurgical method This article discusses in detail the slags formed in the pyrometallurgical Imperial Smelting Process (ISP), the target Zinc and Lead Metallurgical Slags as a Potential Source of Metal
.jpg)
Characterization of Two Sludges from a Pyrometallurgical
2020年8月13日 Abstract Gas scrubbing sludge (SS) and fine dust of converters (SC) are wastes generated in the offgas cleaning system of smelting and converting processes Both wastes are considered hazardous materials due to their high metal contents and leaching characteristics The main purpose of this study was to gain essential knowledge on the recovery of valuable 2018年5月16日 While these values will be different than those for recycled (secondary) lead, two processes are present in each manufacturing source: smelting and refining Smelting has a GWP of approximately 055 kg CO 2 (kg Pb) −1 compared to refining which has a GWP of approximately 012 kg CO 2 (kg Pb) −1, highlighting the impact of lead smelting Lead acid battery recycling for the twentyfirst century2014年6月6日 Antimonial dust is a byproduct of lead smelting and an important material for extracting antimony A new pyrometallurgical process for producing antimony white from the antimonial dust is reported The process mainly consists of three steps, which are reduction smelting, alkaline refining, and blowing oxidation First, the reduction smelting of antimonial A New Pyrometallurgical Process for Producing Semantic Thermodynamic analysis and process modeling can aid concept development and parameter selection Our recent pyrometallurgical experience includes: Indium recovery from lead smelter dusts; Chloride drossing of Pyrometallurgy Hazen Research
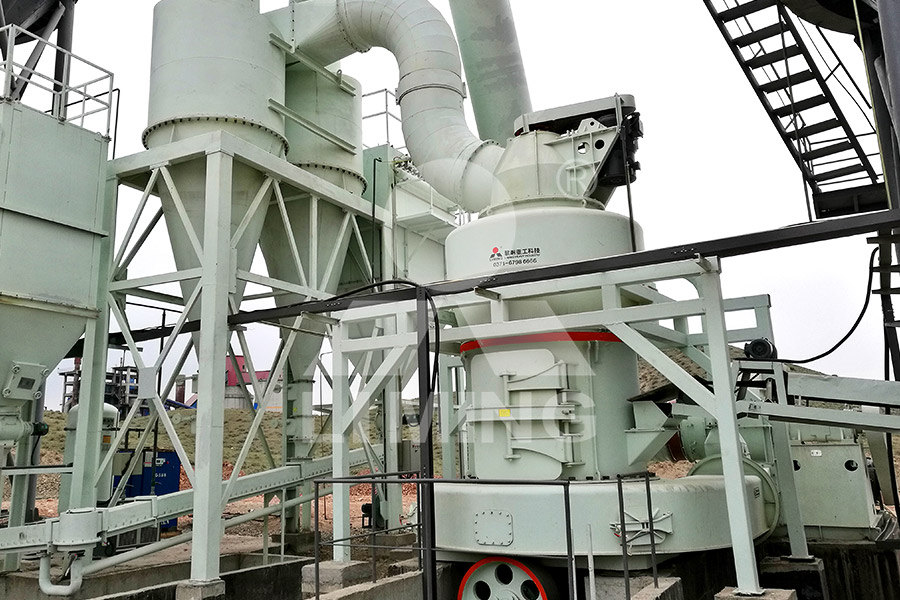
Pyrometallurgy: Process, Advantages, Disadvantages
2023年8月3日 Pyrometallurgy is the extraction and purification of metals by heatbased methods It as smelting and calcining in that those two involve a chemical change to the raw material, whereas in refining, the end material is There are two methods of smelting zinc: the pyrometallurgical process and the electrolysis process [2] Both methods are still used [2] [4] Both of these processes share the same first step: roastingThe top path is the pyrometallurgical process of smelting zinc and the bottom path is the electrolytic processZinc smelting Wikipedia2022年8月12日 Antimony is classified as a critical/strategic metal Its primary production is predominated by China via pyrometallurgical routes such as volatilization roasting—reduction smelting or direct reduction smelting The performance of most of the pyroprocesses is very sensitive to concentrate type and grade Therefore, technology selection for a greenfield plant A Review on Pyrometallurgical Extraction of Antimony from2020年11月16日 This paper reviews the PGMs recovery from waste catalysts using a metals smeltingcollection process, which belongs to the main pyrometallurgical process, in the presence of various metal collectors, such as lead, copper, iron, matte, print circuit board (PCB) or reactive metals of calcium and magnesiumMetals smeltingcollection method for recycling of platinum

A New Pyrometallurgical Process for Producing Antimony
2014年9月1日 Antimonial dust is a byproduct of lead smelting and an important material for extracting antimony A new pyrometallurgical process for producing antimony white from the antimonial dust is reported2017年7月10日 Recovering PGM from the spent automotive catalysts can be realized by two methods: the pyrometallurgical and hydrometallurgical methods The pyrometallurgical methods use high temperature (over Pyrometallurgical Recovery of Platinum Group Metals from Zinc smelting is the process of converting zinc concentrates (ores that contain zinc) into pure zinc The most common zinc concentrate processed is zinc sulfide, which is obtained by concentrating sphalerite using the froth flotation methodThere are two methods of smelting zinc: the pyrometallurgical process and the hydrometallurgical process (over 90% of hydrometallurgical Zinc: smelting, producing and classificationMetalpediaDespite its success, there are still a number of drawbacks of the pyrometallurgical Pb recycling process, primarily related to operational and environmental concerns []Smelting has a high energy demand due to the high operating temperatures, while the use of carbon as a fuel leads to the generation of CO 2The high energy demand in conjunction with the production of CO 2 Lead acid battery recycling for the twentyfirst century

Feasible Time for Extraction of Lead from Spent Paste by
2018年12月28日 Most lead and zinc secondaries are recycled via pyrometallurgical smelting processes Many of the problems historically encountered in secondary smelters have been solved by the addition of 2017年1月1日 The aim of this study is to investigate the possibility of pyrometallurgical recovery of lead and bismuth from preliminary desulfated copper converter flue dust into a metal phase, by carbothermal Hydro pyrometallurgical treatment of copper lead, two processes are present in each manufacturing source: smelting and refining Smelting has a GWP of approximately 055kg CO2 (kgPb)−1 compared to refining which has a GWP of approximately 012kg CO2 (kgPb)−1, highlighting the impact of Lead acid battery recycling for the twentyfirst century2022年12月31日 Pyrometallurgical technologies have the advantages of Leadrich slag as a green feedstock can be used in a blast furnace or smelting reduction furnace to produce lead In this study, the original data of a BF are Metals Special Issue : Fundamentals of Advanced
.jpg)
Pyrometallurgical options for recycling spent lithiumion
2021年4月15日 These pyrometallurgical recycling techniques have gained extensive applications at the industrial scale, eg, Ultrahightemperature smeltingtechnology (UHT) of Umicore, Belgium [32], Roasting−smelting process of Glencore (Xstrata), Switzerland [32], High temperature melting recovery (HTMR) process of Inmetco, USA, Calcination process of Sony 2019年7月1日 Lead slag is a byproduct of lead production process, mainly from two ways: lead ore smelting and waste leadacid battery recovery At present, nearly 95% of the recovery plants for spent lead acid batteries are based on pyrometallurgical A review on lead slag generation, characteristics, and utilizationCurrently, two methods are used to obtain zinc and lead, the pyrometallurgical method and the hydrometallurgical method This article discusses in detail the slags formed in the pyrometallurgical Imperial Smelting Process (ISP), the target Zinc and Lead Metallurgical Slags as a Potential Source of Metal PDF On Jan 1, 2020, Wenzhao Cui and others published Pyrometallurgical Recovery of Valuable Metals from Flue Dusts of Copper Smelter Through Lead Alloy Find, read and cite all the research you Pyrometallurgical Recovery of Valuable Metals from Flue Dusts
.jpg)
Advancements in the separation, purification, and smelting
Addressing the issues in traditional pyrometallurgical processes such as inefficient silver and lead removal from bismuth using zinc and the problematic aspects of chlorinebased lead removal methods—low separation efficiency, high energy consumption, severe environmental pollution, and health hazards2009年12月1日 Slags from the Pb/Ag medieval (14th century) smelting plant located at Bohutin, Přibram district, Czech Republic, were studied from the mineralogical and geochemical points of view Two types of slags were distinguished: (i) quenched slags formed mainly by Pbrich glass and unmelted residual grains of SiO2 and feldspars, and (ii) crystallized slags mainly MINERALOGY OF MEDIEVAL SLAGS FROM LEAD AND SILVER SMELTING 2023年9月1日 This paper is structured as follows: Section 2 gives a brief overview of materials and methods After explaining the two pyrometallurgical recycling processes selected here as examples, possible process variations are presented in a morphological box Furthermore, the total cost of ownership (TCO) method used for the economic analysis is describedPyrometallurgical recycling of different lithiumion battery cell 211 Primary lead production There are two pyrometallurgical processes available for the production of lead from lead sulphide or mixed lead and zinc sulphide concentrates: sintering/smelting in a blast furnace or Imperial Smelting Furnace (ISF); direct smeltingEMEP/EEA air pollutant emission inventory guidebook 2019
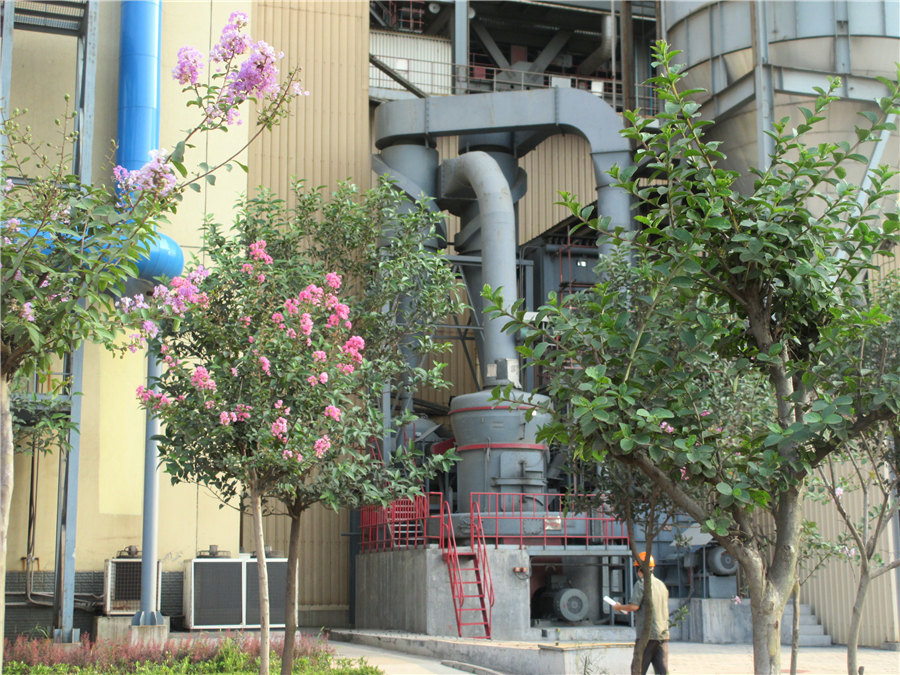
Environmental Impacts of Energy‐Efficient
2015年11月23日 Two of these technologies dominate Cu production methods used in the world, the OUTOKUMPU flash furnace (more than 30% of production) and smelting Cu matte in flame furnaces (approximately 25% of production), 2016年8月1日 This article reviews recent studies on the recycling of spent lead paste and describes novel technologies Although the pyrometallurgical process has been dominant in the secondary lead recycling processes, there has been growing pressure to achieve sustainable greener recycling methods to address the environmental pollution issues caused by emissions A critical review on secondary lead recycling technology and its • Metal Extraction: Smelting is the primary method for extracting metals from their ores It allows for the separation of valuable metals from the host rock or mineral matrix in which they are naturally found Commonly extracted metals include iron, copper, aluminum, lead, zinc, nickel, and precious metals like gold and silverGuide to Modern Smelting Processes CED Engineering2021年11月26日 This chapter describes pyrometallurgical processes to recover metals from WEEE, such as waste printed circuit boards Furthermore, it discusses their advantages, limitations, and associated challenges Further details on the copper and leadsmelting strategies used to recycle ewastes are also presentedPyrometallurgical Processes for Recycling Waste Electrical and
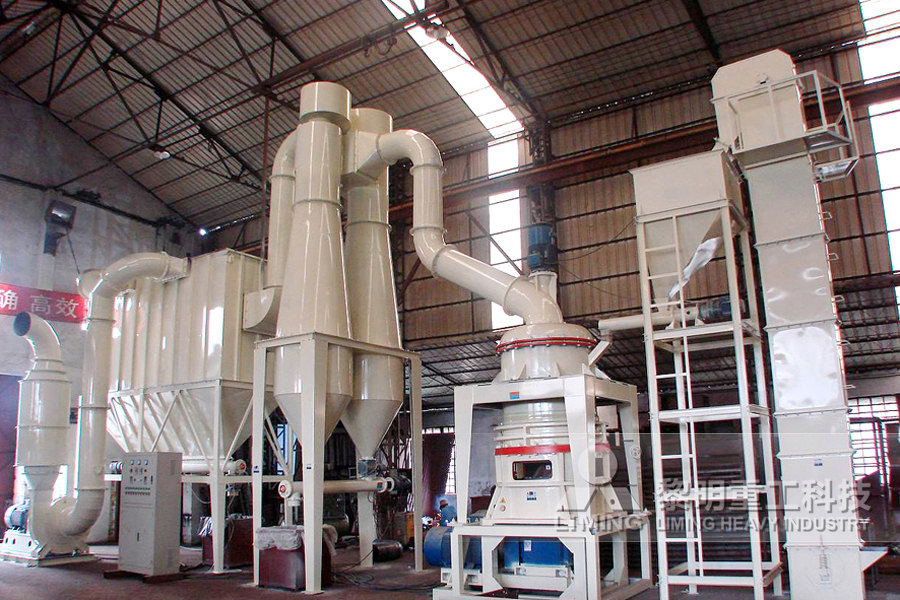
Pyrometallurgical Process an overview ScienceDirect Topics
A critical review of the preprocessing and metals recovery methods from ewastes Rima Kumari, Sukha Ranjan Samadder, in Journal of Environmental Management, 2022 41 Pyrometallurgical process Pyrometallurgical process is a traditional approach of metal recovery where, different thermal treatments such as incineration, roasting, sintering, and smelting are carried out under 2016年12月31日 Pyrometallurgical methods, such as smelting, combustion, pyrolysis, and molten salt processes, can alternatively be implemented on this metalrich fraction (Ebin and Isik 2016)Pyrometallurgical Processes for the Recovery of Metals from 2023年11月23日 Currently, two methods are used to obtain zinc and lead, the pyrometallurgical method and the hydrometallurgical method This article discusses in detail the slags formed in theZinc and Lead Metallurgical Slags as a Potential Source of Metal 2020年4月29日 The treatment of spent lead paste is essential for the recycling of spent leadacid batteries In this study, we propose a facile route for the recovery of lead from spent lead paste by predesulfurization followed by lowtemperature reduction smelting The effects of two desulfurization methods, ie, highpressure and normalpressure processes, on the Recovery of Lead from Spent Lead Paste by Pre Springer
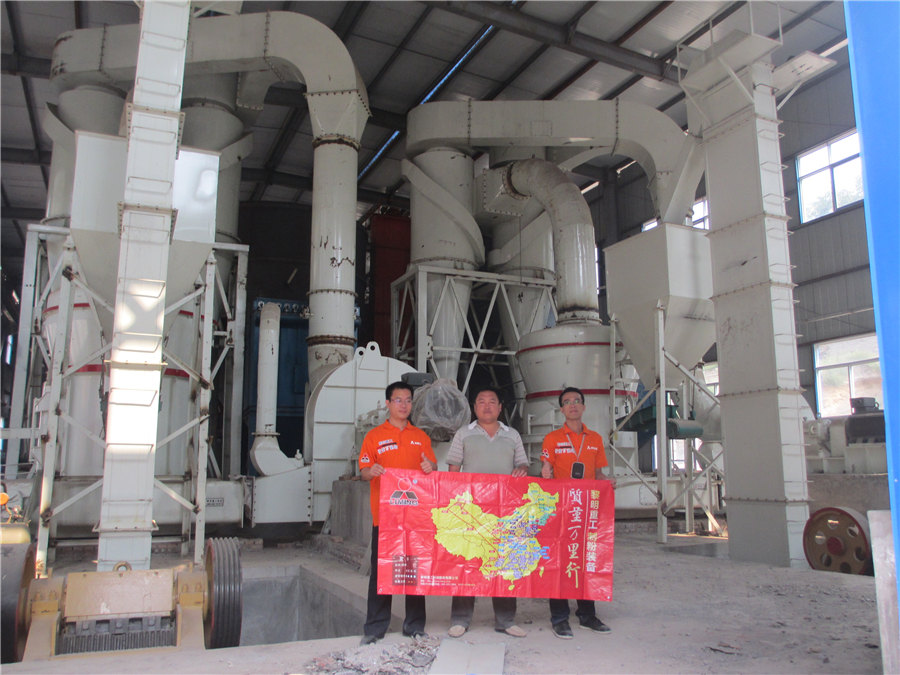
Pyrometallurgical Recovery of Valuable Metals from Flue Dusts
2020年1月25日 Lead sulfide from the copper concentrates is converted to oxide and sulphate in the dusts collected during smelting and converting processes and they are difficult to be leached and filtered The pyrometallurgical approach has been confirmed to be the only way to efficiently treat the highPb dusts