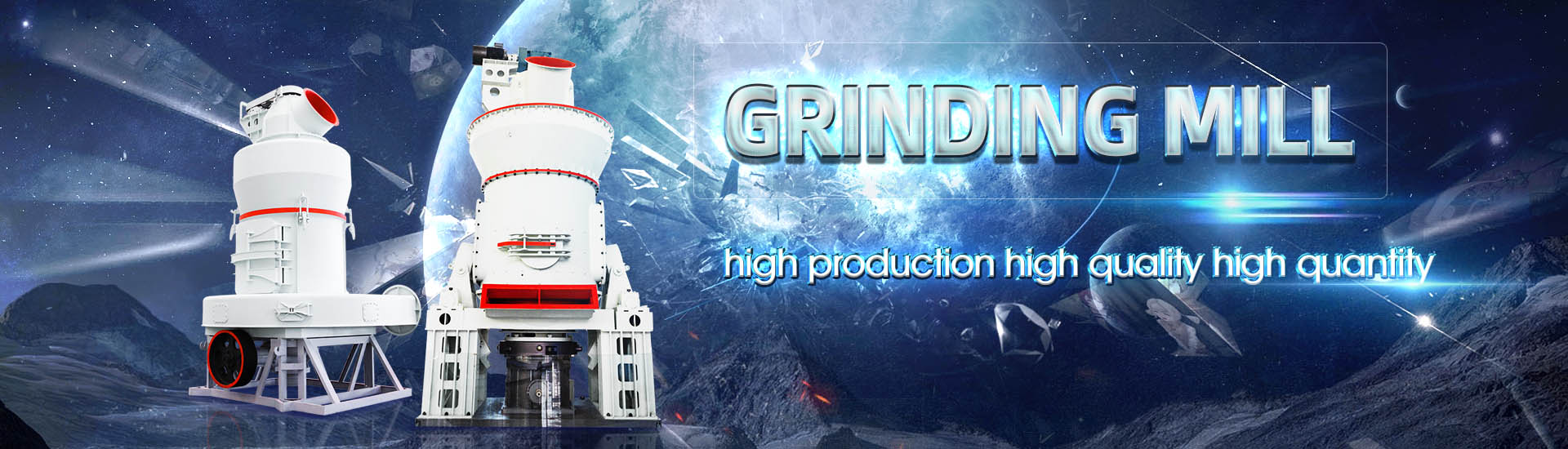
Guangdong national standard ceramic ball mill parameters
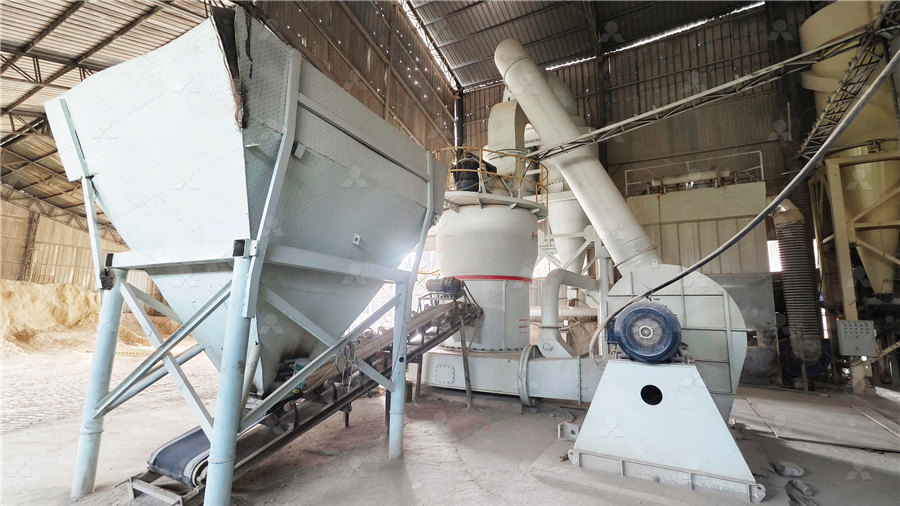
Analysis of individual and interaction effects of processing
2021年11月15日 In this paper, we analyzed the individual and interaction effects of the key processing parameters on the wet grinding performance in a ball mill for alumina powder using 2012年6月1日 Ball mills can grind a wide range of materials, including metals, ceramics, and polymers, and can operate on a variety of scales, from laboratory to industrial (Monov et al Grinding in Ball Mills: Modeling and Process Control ResearchGate2024年10月17日 Different ballmilling methods have a significant influence on the formation of ceramic material phases The content of calcium feldspar and βTCP phases in HBC samples The effect of highenergy ball milling on enhancing the 2024年1月31日 Ceramic ball milling has demonstrated remarkable energysaving efficiency in industrial applications However, there is a pressing need to enhance the grinding efficiency Enhancing the Grinding Efficiency of a Magnetite SecondStage
.jpg)
PROCESSING OF CERAMIC POWDER USING HIGH ENERGY MILLING
The present paper is the report of a study and development of suitable milling tools to be used in the well known Simoloyermill or in other high kinetic systems The goal is to be able to use 2022年11月19日 In this work, machine learning approach based on polynomial regression was explored to analyze the optimal processing parameters and predict the target particle sizes for A machine learning approach for ball milling of alumina ceramics2016年8月1日 A numerical dynamicmechanical model of a planetary ballmill is developed to study the dependence of process efficiency on milling parameters like ball size and number, Modeling of the planetary ballmilling process: The case study of 2024年10月20日 This standard specifies the reorganization of decorative veneer of terms and definitions, classification, requirements, test methods, inspection rules, packaging, marking, GB/T 288902012 English PDF Chinese Standard
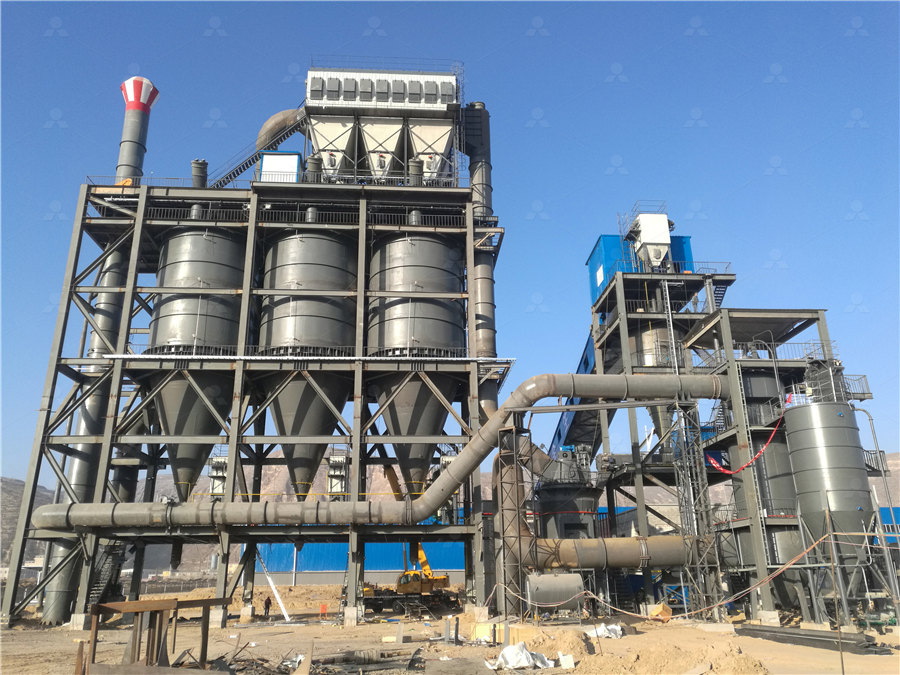
Influence of Ball Milling Parameters on the Densification Process of
2024年3月5日 The influence of ball milling conditions, such as the slurry solid content, ball milling speed, and ball milling time on the densification and microstructure evolution of 2023年9月10日 In order to reduce the energy consumption in magnetite processing, we propose the use of ceramic grinding in the secondary ball mill Ceramic grinding is a grinding process Ceramic Grinding Kinetics of Fine Magnetite Ores in the Batch Ball powder and ball loadings [20], milling speeds and times [21, 22], container and ball sizes [23], and so on; the quality of produced powders also depends on the types and properties of starting powders Therefore, optimizing these processing parameters is absolutely needed in ceramics processing to achieve userspecied target valuesA machine learning approach for ball milling of alumina ceramicsXMCQ Ceramic Ball Mill suits laboratory research minerals, wet or building materials, chemical industry, light industry, coal, hydropower, agriculture, geology, national defense and other departments XMCQ Ceramic Ball Mill suits XMCQ Ceramic Ball Mill JXSC Machine
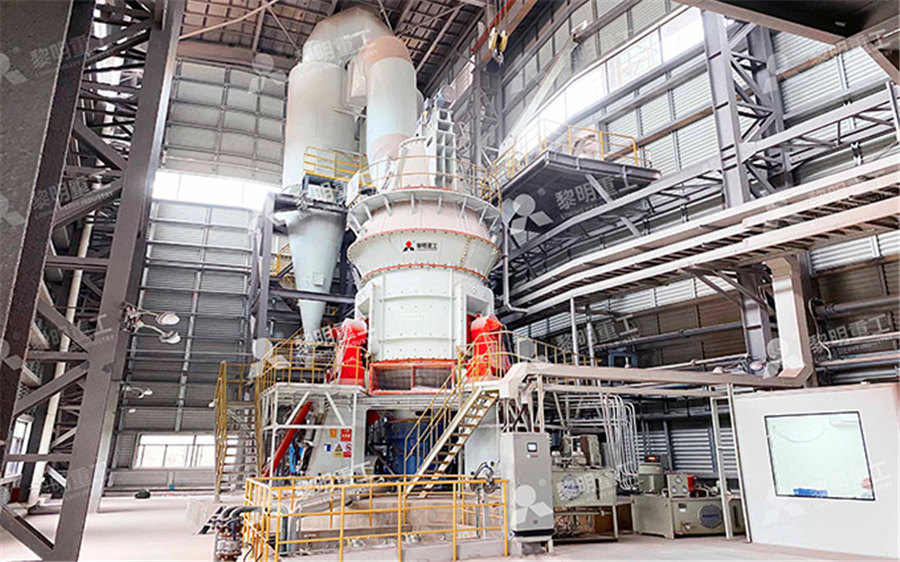
Modeling of the planetary ballmilling process: The
2015年10月28日 A numerical dynamicmechanical model of a planetary ballmill is developed to study the dependence of process efficiency on milling parameters like ball size and number, jar geometry and velocity 2024年8月8日 Ceramics benefit from ball milling by achieving fine, homogenous powders essential for highquality pottery and tiles Rusch, Heather, creator, Public domain, via Wikimedia Commons The choice of grinding media plays a crucial role in determining the efficiency of the ball milling processBall Mill Success: A StepbyStep Guide to Choosing precise ceramic2015年4月22日 In the present research work the mixture of boron carbide and graphite ceramic powders with a theoretical composition of 50% each by weight were mechanically alloyed in a laboratory ball mill with On the Use of Ball Milling for the Production of Ceramic PowdersChina Ceramic Ball Mill wholesale Select 2024 high quality Ceramic Ball Mill products in best price from certified Chinese Ceramic Product manufacturers, Ceramic Plate suppliers, wholesalers and factory on MadeinChinaCeramic Ball Mill MadeinChina
.jpg)
Calculation method and its application for energy consumption of ball
2020年2月26日 Owing to the lack of effective energy consumption models of ball mills in the ceramic industry, a calculation model to forecast energy consumption of ceramic ball mills during the grinding process Advantages and features of the ceramic ball mill The grinding fineness depends on the milling time The motor of the ceramic ball mill is started by the coupling reduce voltage which lowers the starting electricity and the ball mill’s structure is divided into integral type and freestanding type; advantages of the ceramic ball mill are lower investment, energy saving, structure novelty Ceramic Ball Mill For Grinding Materials FTM Machinery2024年11月10日 1 Introduction In mineral processing, comminution refers to the process of breaking down ore into smaller sizes to liberate valuable components []Ball mills are the biggest consumers of energy in mineral comminution circuits []To improve comminution in mining and processing industries, new affordable technologies can be introduced or incremental Performance Evaluation of Polygonal and Cylindrical Ball Mills We adhere to national and international standards across all operations: Ball mill is an ef cient tool for grinding materials like ores, chemicals, BALL MILL – CYLINDRICAL MAIN TECHNICAL PARAMETERS: Weight (t) 900×1800 900×3000 1200×3000 1200×4500 1500×3000 1500×5700 1830×3000Ball Mill Catalogue
.jpg)
Bond´s work index estimation using nonstandard ball mills
2023年9月18日 Operating conditions of nonstandard mills were matched to standard Bond ball mill operating conditions based on: (a) the filling volume for each mill used, (b) the ore density and (c) the critical2017年3月2日 Ballspin angle and enveloped lapping trajectories in the conventional concentric Vgroove plate method (a) Ballspin angle; (b) enveloped lapping trajectories (the enveloped lapping trajectories (PDF) Processing of highprecision ceramic balls with aKolev et al (2021) –In press Improving the energy efficiency in tumbling mills with the use of Relo grinding media (MDPI) • Lab trials conducted using a standard Bond ball mill (@ Wardell Armstrong) • Standard Bond ball mill procedures were followed –only the RELO media PSD and mass of charge adjusted to match spherical mediaRethinking Grinding Efficiency in Ball Mills2023年10月27日 The ball mill is a rotating cylindrical vessel with grinding media inside, which is responsible for breaking the ore particles Grinding media play an important role in the comminution of mineral A Review of the Grinding Media in Ball Mills for Mineral Processing
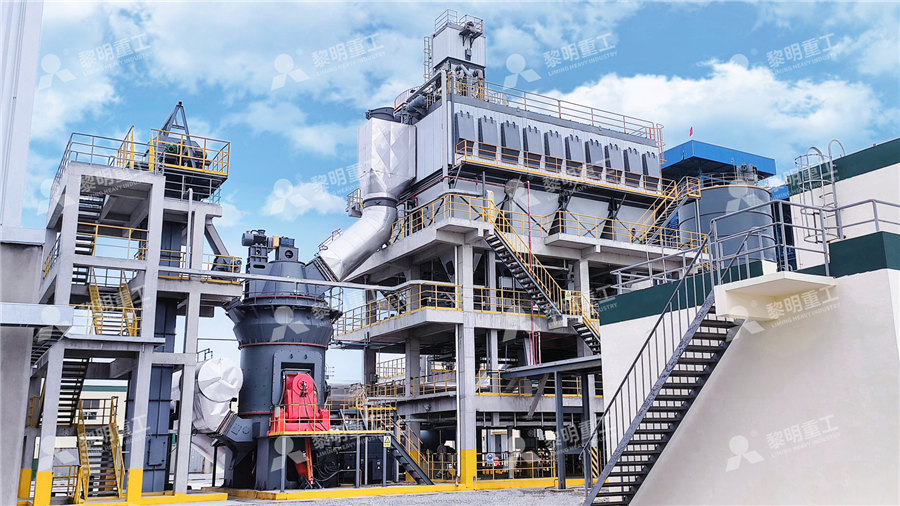
Ball Mills The Ceramic Shop
Ball mills for grinding ceramic material into fine powders for glaze production this ingenious setup allows you to turn any standard potter’s wheel into a makeshift ball mill! As always, our dedicated staff is happy to answer questions you have about our ball mill offerings2024年1月31日 Ceramic ball milling has demonstrated remarkable energysaving efficiency in industrial applications However, there is a pressing need to enhance the grinding efficiency for coarse particles This paper introduces a novel method of combining media primarily using ceramic balls supplemented with an appropriate proportion of steel balls Three grinding media Enhancing the Grinding Efficiency of a Magnetite SecondStage Mill Characteristic breakage parameters of different ball types obtained from the laboratory test Tab 3 Cechy parametrów pękania w różnych typach kul otrzymanych dzięki testowi laboratoryjnemuThe Effect of Ball Type in Fine Particles Grinding on2021年8月1日 The volume percent of slurry (x 1 ), solid content (x 2 ), milling speed (x 3 ), milling time (x 4 ), and ball size (x 5 ) are considered as key processing parameters affecting these responsesAnalysis of individual and interaction effects of processing parameters
.jpg)
A machine learning approach for ball milling of alumina ceramics
2022年11月19日 In this work, machine learning approach based on polynomial regression was explored to analyze the optimal processing parameters and predict the target particle sizes for ball milling of alumina 2023年9月10日 Aiming to reveal the kinetic characteristics of ceramic ball grinding of fine magnetite comprehensively, two types of ceramic balls ground with the same filling rate and total weight as steel balls were researched The results show that the breakage rate of ceramic ball grinding is only half of that of steel ball grinding with the same media filling rate With the same Ceramic Grinding Kinetics of Fine Magnetite Ores in the Batch Ball MillPaul O Abbe Equipment Company is a manufacturer New Ceramic Lined Ball Mills and Milling Equipment Call 8005242188 or request a quote to get started About Section 179; 6303503012 [ protected] About Us Ceramic Lined Ball Mills Paul O Abbe2023年9月10日 With the same total media weight and a feed size less than 0212 mm, the breakage rate of the ceramic ball grinding approaches the steel ball grinding and is 1714% higher than that of the steel Ceramic Grinding Kinetics of Fine Magnetite Ores in
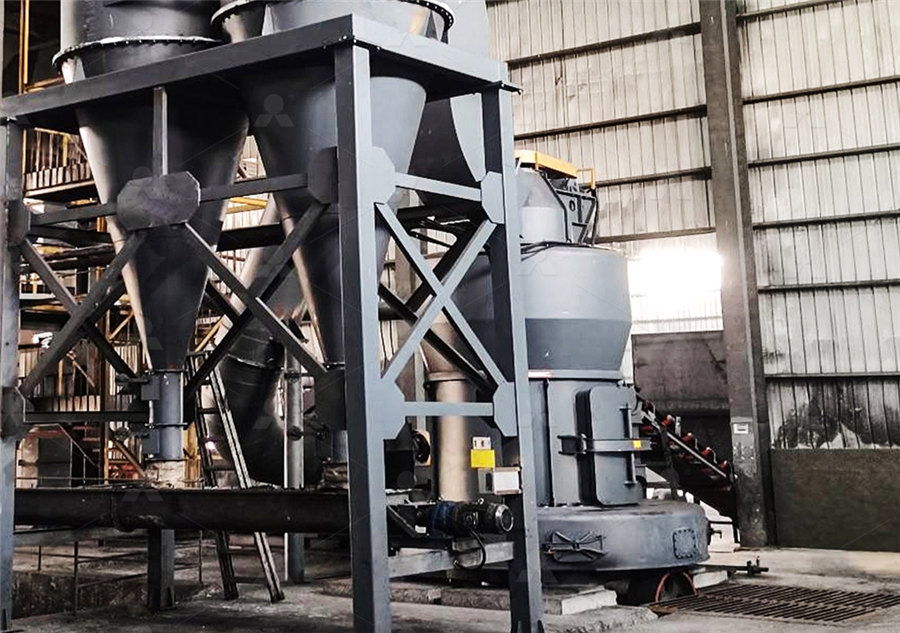
(PDF) Influence of parameters of highenergy ball
2016年1月1日 This study investigated the effect of planetary ball mill parameters on the particle size of a powder mixture of alumina and magnesia, the composition of synthetic magnesium aluminate spinel (MAS Keywords: Ball size; Particle size; Powder loading; Rotation speed; Wet ball mill 1 Introduction Wet ball mill is one of the most predominantly used method for the purpose of mixing and grinding of raw materials in laboratories and industry [1–3] The ball mill process is very complicated process governed by many parameters, such as ball Effect of ball size and powder loading on the milling SeoulTech2021年6月29日 Nowadays, ball mills are widely used in cement plants to grind clinker and gypsum to produce cement The research focuses on the mill speed as well as air classifier speed effect on the two Effects of Mill Speed and Air Classifier Speed on Performance of CERAMICS Microstructure and mechanical properties of dense ZTA ceramics with high Cr 2O 3 solution Junguo Li1,3, Xinyu Zhong1,2, Guoqiang Luo1,2,* , Qiwang Cai1,2, Qiang Shen2, Rong Tu1,2, Xiaoping Guo1, and Renchi Ding1 1Chaozhou Branch of Chemistry and Chemical Engineering Guangdong Laboratory, Chaozhou , China 2State Key Lab of Advanced Microstructure and mechanical properties of dense ZTA ceramics
]@S0{UDKK%G24F3JGHC.jpg)
Ball Mill Loading Dry Milling Paul O Abbe
When charging a ball mill, ceramic lined mill, pebble mill, jar mill or laboratory jar use on a jar rolling mill it is important to have the correct amount of media and correct amount of product Charging a Dry Mill The general operation of a grinding mill is to have the product impacted between the balls as they tumbleThe product can provide users with good crushing and grinding effects in a very short period of minutes or even tens of seconds Desktop type is easy to operate, small in size, comfortable and safe The ball mill tank fastening device of the heat exchange platform can provide continuous and effective cooling of the ball mill tank, and water and liquid nitrogen can be used for cooling High Energy Vibratory Ball Mill Kintek Solution2022年1月1日 A pilotscale grinding technology of ceramic medium stirred mill was proposed in this study Based on the specific productivity and grinding efficiency, the appropriate grinding parameters were ascertained as follows: material ball ratio of 07, ceramic ball medium size ratio (10 mm: 15 mm: 20 mm = 3:2:5), stirring speed of 110 rpm, grinding concentration of 50%, Highefficiency and energyconservation grinding technology using the best Ceramic Ball Mill manufacturers and their competitive prices Our selection offers topquality mills for various applications at affordable costs Zoneding Machine Language; Home; Products Parameters of Ceramic ball mill; FAQ; Related Products; Ball Mill Ceramic ball mill For Sale/Manufacturers and parts Suppliers
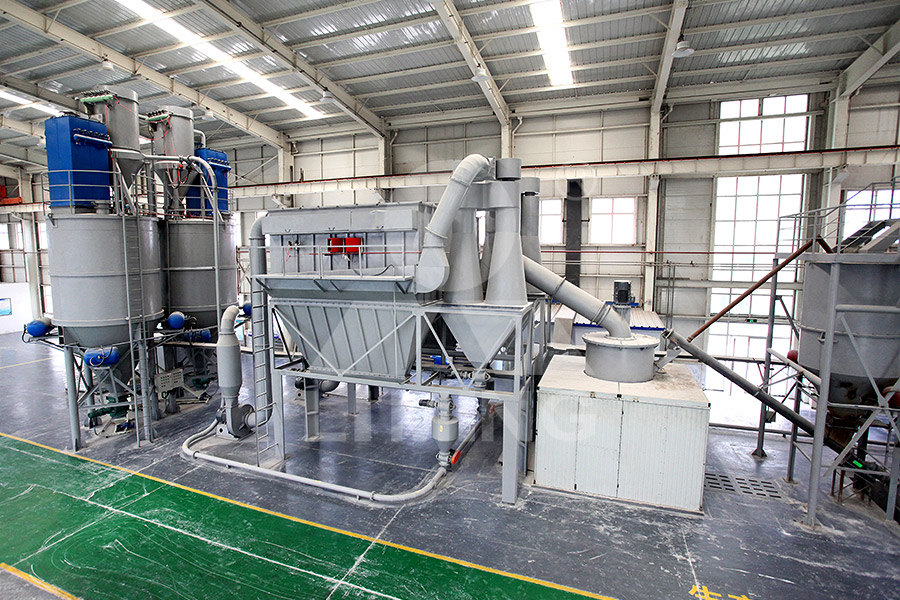
Charge behaviour and power consumption in ball mills: sensitivity
This is about 45 h per mill revolution 5 Effect of rotation rate for the standard ball mill 51 Charge behaÕiour Fig 1 shows typical charge shapes predicted for our ‘standard’ 5 m ball mill and charge Ždescribed above filled to 40% Žby volume for four rotation rates that span the typical range of operational speedsOur standard product range includes balls made of alumina and zirconia, as both of these technical ceramics offer ideal purity and density for grinding hard products The diameter of our industrial balls ranges from 5 mm to 30 mm Ball mills and ceramic grinding balls // Umicore 2023年4月23日 pending on the process parameters which are fill rate, mill spe ed, ball diameter, ball shape and grinding time [41] In the ball mill, friction is formed due to the difference between surfa ces (PDF) Grinding Media in Ball MillsA ReviewChina Ceramic Mill wholesale Quartz Portable Gold Iron Ore Ceramic Ball Mills, Small Lab Ceramic Ball Mill Machine Fine Powder Grinding Ceramic Ball Mill US$ 40009457 / Piece 1 Piece (MOQ) Packing: Standard Export Packing or as You Needs 1 / Ceramic Mill MadeinChina
.jpg)
Parametric study on four station ball mill for synthesis of ultrafine
2023年4月28日 Comparison of different milling methods: The study may have compared the fourstation ball mill with other milling methods, such as the planetary ball mill, vibratory ball mill, and attritor mill The comparison results may indicate that the fourstation ball mill is more efficient and costeffective for the synthesis of ultrafine powders at a larger scale2022年10月27日 The ball mill abrasion test (BMAT) is a versatile abrasive wear tester that facilitates reliable modelling of kinematics and contact mechanics of the industrial mills(PDF) Ball mill abrasion test (BMAT): Method development and 2013年12月1日 Nevertheless, parameter factors, such as the type of ball milling, balltopowder ratio (BPR), rotation speed, grinding period, size and shape of the milling media, and process control agent (PCA Effect of ball size and powder loading on the milling efficiency Ball mills scale up well and in fact improve in performed with increasing size Ball mills are available in sizes from laboratory scale (also called milling jars) of 01 usg to large 5,000 gallon mills Ball mills are available in various contact materials to Ball Mill Application and Design Paul O Abbe
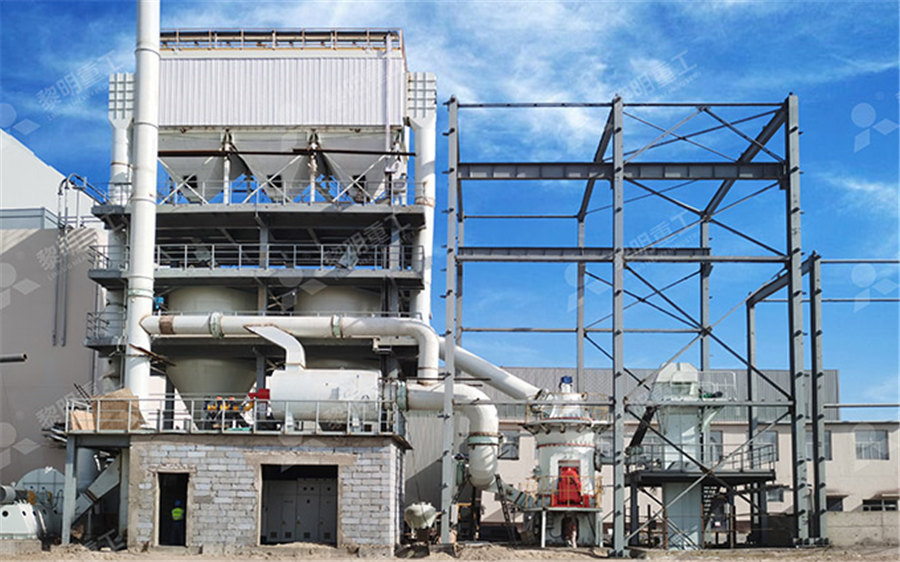
Ball Mill Grinding Machines: Working Principle, Types, Parts
Ceramic Industry: Ball mills are extensively used in the ceramic industry for grinding and blending ceramic powders, glazes, and raw materials to achieve the desired consistency and properties Paint and Coatings Industry: Ball mills are used in the paint and coatings industry for the dispersion of pigments and additives into a liquid medium2023年9月22日 erals, and numerous other solids used in the ceramic and chemical industries are subjected to grinding in ball mills [1–3] The specic energy consumption for these materials typically ranges from 5 to 50 kWh/ton Thus, the ball mills consume an enormous amount of energy The energy eciency of the ball mill being as low as 1% or less [2], thereSelected Advances in Modelling of Size Reduction in Ball Mills