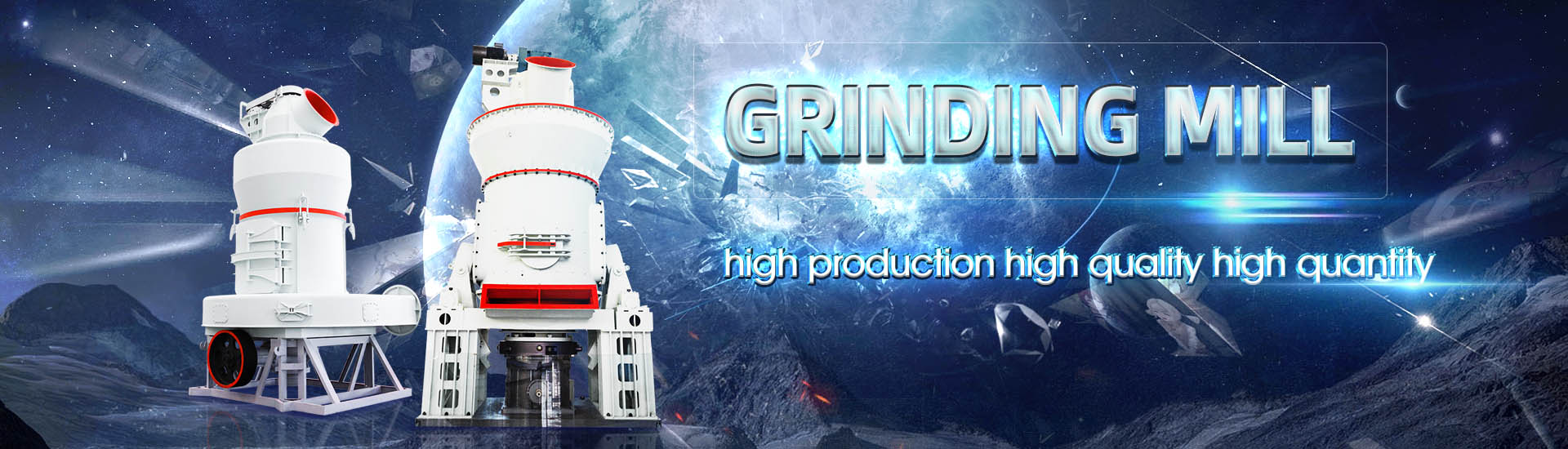
Ceramic pellet powder making process
43.jpg)
Case Study 2: Ceramic Powder Processing
This case study has been focused on the intensification of the freeflowing powder preparation process involved in the very beginning of the ceramic tile manufacturing process Nowadays, the most widely used ceramic tile shaping method is uniaxial pressing of spraydried powder in Fundamentals of Ceramic Powder Processing and Synthesis presents examples of these modern methods as they apply to ceramic powders The book is organized to describe the natural and Fundamentals of Ceramic Powder Processing and Synthesis2015年2月1日 Pelletization is a method of agglomeration that permits the particlesize enlargement, in which ceramic powders are processed into pellets or granules of dimensions Pelletization Technology: Methods and ApplicationsA ReviewOne distinguishes between a buildup granulation process with the aid of pelletizing tables or pelletizing drums and press pelletizing, eg by briquetting using briquetting rolls, the socalled Chapter 14 Pelletizing by Extrusion
.jpg)
Foundations of Ceramic Synthesis: Processes, Principles, and
1 天前 415 Chemical and Process Industries a Ceramics are utilized to line industrial furnaces and kilns to endure high temperatures and provide protection against both thermal and Dry compaction is one of the most popular shape forming processes, since it involves a relatively simple technology while allowing high production rates However, our understanding of this Dry pressing of ceramic powders SpringerLinkUsually this is done by a sintering process which is a consolidation and densification step of the granular compact through the action of heat During this stage, the microstructure of the Ceramics: Sintering and Microstructure EPFLThis article explains how ceramic powders are made It begins by briefly describing the raw materials used in structural clay products, whitewares, refractories, and advanced ceramics It Processing and Characterization of Ceramic Powders
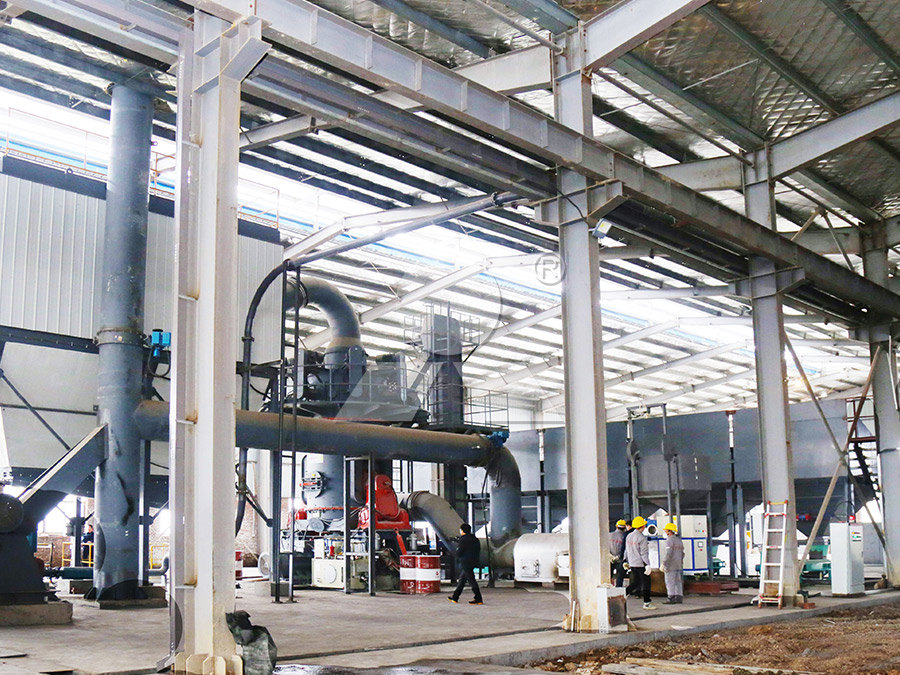
The preparation process of ceramic pellet ResearchGate
Based on the design from the view of the Goldschmidt tolerance factor, Ba0955La003TiO3doped Zr ferroelectric ceramics were prepared by solidstate reaction method The experimental results2020年5月1日 To conduct the process, we directly sandwich a pressed green pellet (Fig 1B) of ceramic precursor powders between two Jouleheating carbon strips that rapidly heat the pellet through radiation and conduction to form a A general method to synthesize and sinter bulk In the firing process, raw materials that are compressionmolded (volumetric filling rate: approx 60%) are heated at temperatures below their melting points to sinter powder and create density Ceramic powder particles induce mass transfer at Fine Ceramics Production Process Introduction to The pelleting process starts with a bin (Figure 1, Item 1) in which the mixture of mash is stored From there, the mash will flow by gravity into the pellet mill (Figure 1, Item 2) This machine is usually located on the ground or main work floor level The hot, extruded mash (pellets) flows by gravity into a cooler (FigureThe Pelleting Process CPM
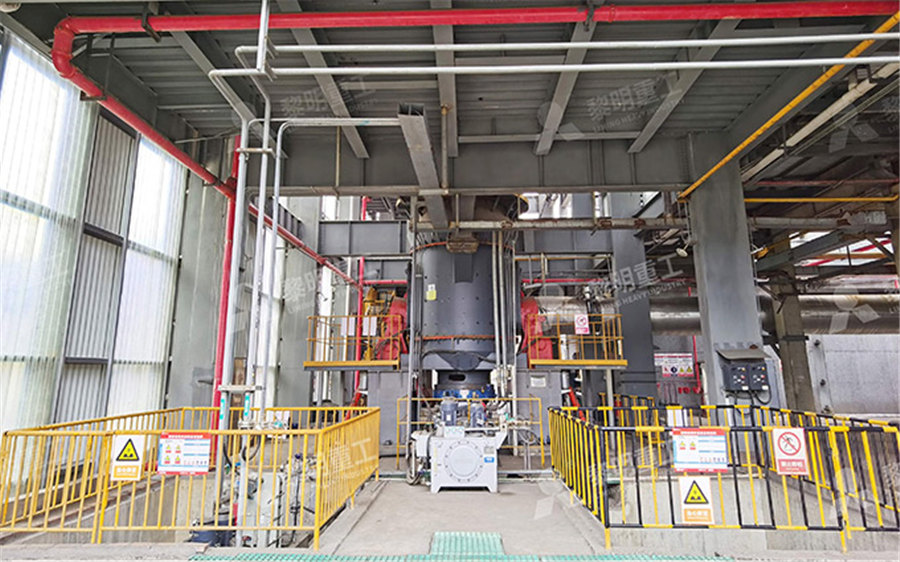
Chapter 13: Applications and Processing of Ceramics
• Thin sheets of green ceramic cast as flexible tape from “slip” • Used for integrated circuits and capacitors and other flat components • Slip = suspended ceramic particles + liquid carrier (contains binders, plasticizers) Fig 1318, Callister Rethwisch 8e Particulate forming #3: Tape casting: Ceramic Fabrication Methods (ii)the ceramic process because of the highly homogeneous final composition of the powder obtained by system and then the resulting pellets are grinded to obtain a powder with the desired particle size distribution The main difference between the two evaluated technologies is that after granulation, freeflowingCase Study 2: Ceramic Powder ProcessingHowever, our understanding of this process is still empirical Most industrial problems in this area are solved Bortzmeyer, D (1992) Modelling ceramic powder compaction Powder Technol, 70(2), 131–139 Article CAS Google Scholar Dry pressing of ceramic powders SpringerLink17 小时之前 In general, you can make ceramics by burning certain clays at high temperatures The process of making ceramics involves four phases Here I have elaborated on the whole process of making ceramics Collection of Clays Manufacturers collect the clay to make ceramics by excavating the earth Ceramics, on the other hand, cannot be made with just How Are Ceramics Made? (Step By Step Process) Techiescientist
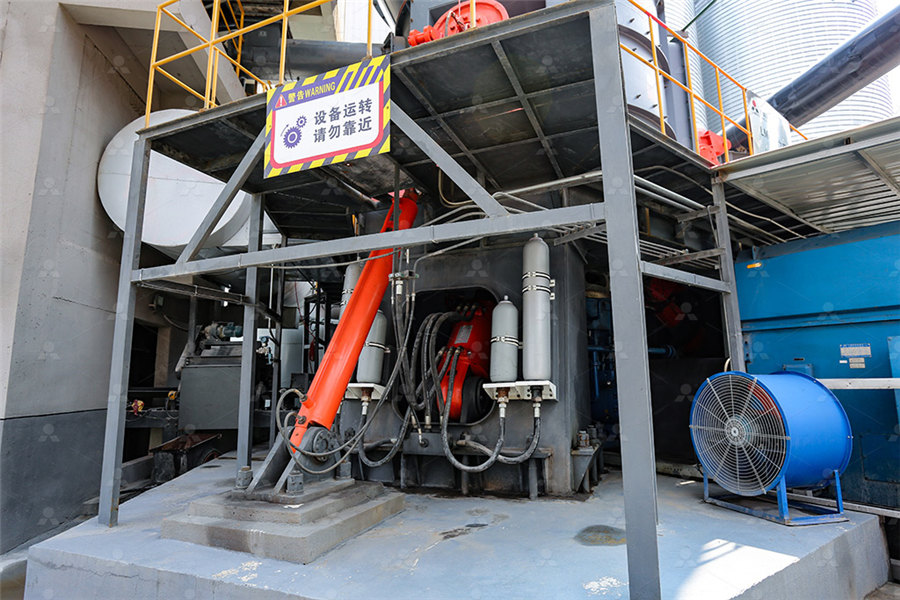
Advances in Sintering and Pellet Technology
2023年5月31日 Pellet making is also a type of agglomeration process that converts fine powders into a solid shape material—mostly small, rounded, spherical, or cylindrical body units A wide range of fine powder materials, like chemicals, medicines, iron ore, minerals, animal compound feed, plastic and more can be converted to pellet with strong physical and chemical propertiesKBr Particle Production Process Preparation before making pellets Before starting the process of making KBr pellets for XRF analysis, there are a few key considerations that need to be taken into account These include: Temperature uniformity requirements: The temperature uniformity plays a crucial role in the pelletising processAn InDepth Guide on Laboratory Presses and KBr Pellets The slip casting process is illustrated below in Figure 1 Figure 1: Schematic showing the steps used in slip casting First the slip is prepared by mixing the ceramic powder with a liquid Next the slip is poured into the mold which absorbs the liquid out of the slip leaving a thin wall of powder along the mold wallCeramic Processing: Slip Casting American Ceramic SocietyBalling process: the green pellet is the rolled pellet without any thermal process It is obtained under strict control of moisture and has a spherical shape and diameter of 8–16 mm; Induration process: the green pellets are hardened in a high temperature processing at controlled heating rates, and aiming to achieve the physical and metallurgical requirements for handling, Iron Ore Pelletizing Process: An Overview IntechOpen
.jpg)
The Practice of Pellet Making SpringerLink
2019年7月31日 This chapter discusses the important issues and problems of pellet making in practice The individual working steps of pellet production such as material handling, chipping , drying , conditioning , pressing technologies, posttreatment and packing are introduced The general layout of pellet making technologies is also treatedMaking Metal Powder The first step in the overall powder metallurgy (PM) process is making metal powders There are four main processes used in powder production: solidstate reduction, atomization, electrolysis, and chemicalMaking Metal Powder MPIF2024年5月20日 Also, the stability of the BaTiO 3 ceramic was analysed through XRD patterns (shown in Figure S1 of Supplementary Information) and it was found that as sintered BaTiO 3 ceramic pellet and fast cooled BaTiO 3 ceramic pellet (after 3rd cycle) were in accordance to JCPDS No:05–0626 revealing that BaTiO 3 ceramic pellet was stable after piezocatalysis Facilitating flexoelectric effect in BaTiO3 ceramic for pollutant We are the experts in converting powder into pellets With product lines for creating pellets through both low pressure extrusion and high pressure pelletization, our team of process experts can deliver the right solution to form the exact product characteristics you require Pelletizing your materials provides a number of benefits, including:Pelleting Chemical Powders LCI Corp
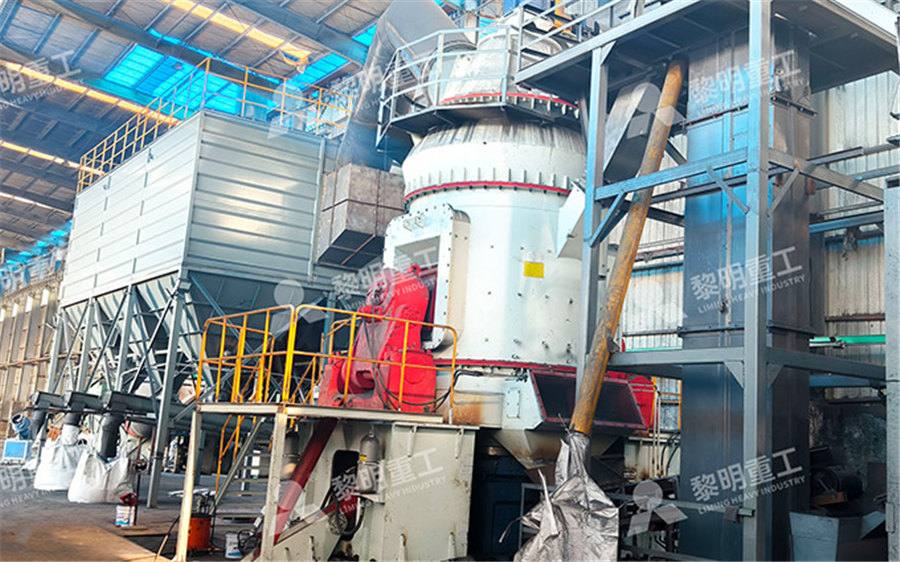
Your guide to pelleting Borregaard
Formulate a recipeThis is usually done by a nutritionist to ensure the target animal will get the nutrients it needs Weigh out the ingredients according to the recipeYou need several different size scales: large scales for macroingredients that make up more than 10% of the formulation, and small scales/manual handweighing to add microingredients which make up less than 1% 2014年1月1日 In contrast, wet forming is the predominant powderforming process with ceramics With the mix is granulated into the form of pellets with a nominal size of 1–5 mm and fed USA, came up with a new slurrybased manufacturing process for making ceramic components in which conventional wet processing techniques were Powder Processing of Bulk Components in ManufacturingDownload scientific diagram The preparation process of ceramic pellet from publication: Oxygen defect related high temperature dielectric relaxation behavior in (Ba,La)(Zr,Sn,Ti)O3 ceramics The preparation process of ceramic pellet ResearchGate2008年4月2日 Sol–gel process provides an alternate route for fabrication of ceramic nuclear fuel The sol–gel process provides several advantages over the conventional powder pellet fabrication process by eliminating handling of radioactive powders The sol–gel process uses only fluids or fluid like materials, thus become amenable to remote handling The sol–gel process Status of sol–gel process for nuclear fuels Journal of SolGel
.jpg)
Powder agglomeration processes of bulk materials – A state of
2024年1月1日 Granulation is a process that is wellknown and widely used in various industries This is primarily used when bulk material in the form of a fine powder is considered difficult to treat and process [1]The process is designed to convert fine powders into granular materials with controlled physical properties, ie a specific shape (granule size) and a specific bulk densityOther articles where powderpellet process is discussed: nuclear ceramics: Nuclear fuel: fuels traditionally follows a standard powderpellet process This involves comminution, granulation, pressing, and sintering at 1,700° C (3,100° F) in a reducing atmosphere The resulting microstructure consists of large, equiaxed grains (that is, with dimensions similar along all Powderpellet process technology Britannica2015年7月16日 Due to the different characteristics of various raw materials, the pellet quality is unequal To improve the pellet quality or maximize production capacity, you can add binder to help the ligninlacked material to compress Binders and other additives – crucial for pellet makingThis automatic powder pellet press is mainly used for samples that require high pressure for shaping, making operation more userfriendly Equipped with limit protection switch, Producing metal powder compacts for sintering Automatic Powder Pellet Press ZYLAB
.jpg)
Does anyone know how much pressure is needed for a
I am making PZT (Pb(Zr,Ti)O3) pellets I loaded 07ton/cm2 on the pellet for several times today (using hydraulic press), but, it still shows the crack at the edge/body of pelletModern methods of powder shape forming, such as isostatic pressing, slipcasting, extruding, tapecasting, and 3D printing, have been developed for making green bodies of ceramics and metals The green body is then heated through a sintering process, reducing porosity and increasing densityIsostatic Pressing of Ceramics: Process and PrecisionThe ceramic media I personally use and recommend is these ceramic pellets from Polly Plastics (link to Amazon) I’d recommend getting 3 pounds worth because I often find that one 15 pound bag isn’t quite enough These pellets are all the same size which works just fine, but some people prefer the version with mixed sizes of pelletsRock Tumbling Media: How Much and What Kind to UseMost ceramic products are claybased and are made from a single clay or one or more clays mixed with mineral modifiers such as quartz and feldspar The types of commercial clays used for ceramics are primarily kaolin and ball clay 1172 Process Description1,35 Figure 1171 presents a general process flow diagram for ceramic products AP42, CH 117: Ceramic Products Manufacturing US EPA

Microspheres and pellets of UO2 prepared via ADU by
2020年9月10日 Sol–gel process provides an alternate route for fabrication of ceramic nuclear fuel The sol–gel process provides several advantages over the conventional powder pellet fabrication process by 2018年9月30日 PRESSING: Pressing is accomplished by placing the powder * into a die and applying pressure to achieve compaction * premixed with suitable binder and lubricant and preconsolidated so that it is freeflowing Free flowing can be achieved by granulation or spray drying BINDERS PLASTICIZERS – they coat the powder and provide lubrication during pressing Different Production Techniques Ceramic Ninja2019年1月1日 Fig 1 Powder processing and sintering for making ceramic components Fig 2 Constrained sintering and cosintering [8] 2 Continuum mechanics of sintering 21 Isotropic constitutive equation The sintering is a densification process, where the volume of a powder compact decreases with time First, we assume the case of isotropic microstructureSintering mechanics of ceramics: a short review ScienceDirectCompaction of ceramic powders is a forming technique for ceramics in which granular ceramic materials are made cohesive through mechanical densification, either by hot or cold pressing The resulting green part must later be sintered in a kiln The compaction process permits an efficient production of parts to close tolerances with low drying paction of ceramic powders Wikipedia
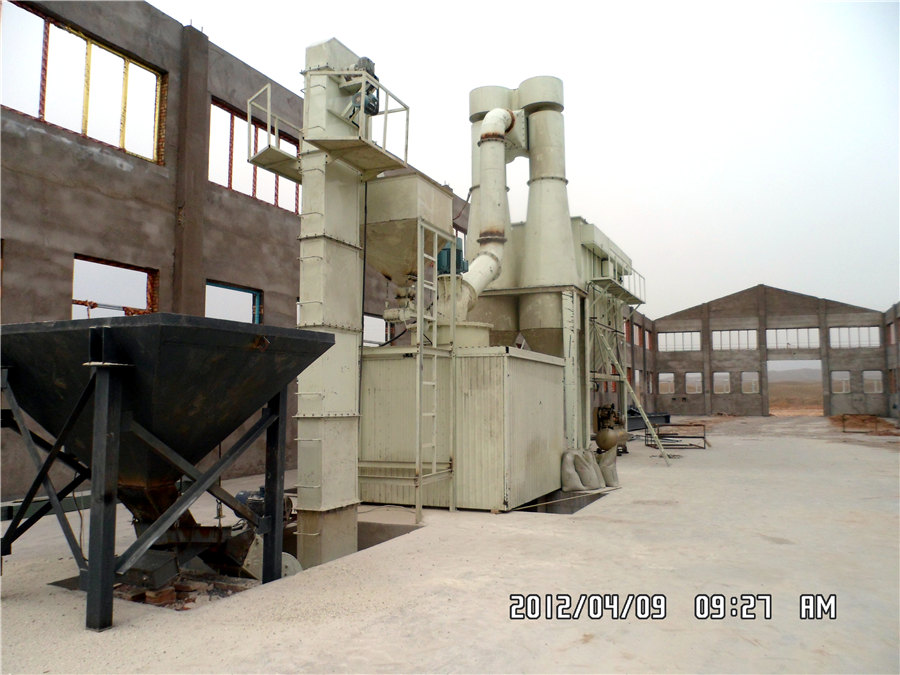
Iron Ore Pelletizing Process: An Overview
2018年7月11日 Balling process: the gre en pelle t is the roll ed pellet wi thout a ny thermal process It is ob tained under stri ct control of moi sture and has a sphe rical sha pe and diameter of 8 – 16 mm;Ceramic dry pressing is to put ceramic powder (5% to 8% moisture content) into a metal mold, compress it under the action of force (usually unidirectional pressure), and partially discharge the gas in the void in the blank, and the ceramicThe particles are displaced, gradually approached, and tightly meshed with each other, finally forming a blank with the same crosssection as that Ceramic Dry Pressing2009年9月25日 Different UO2 ceramic pellets types originated from AUC and ADU industrial routes are compared based This residue is reincorporated into the production process in the form of U3O8 powder (PDF) A comparative study of UO2 ceramic pellets for nuclear 2023年12月1日 For glassceramic and ceramic materials, the most straightforward bulkforming method involves preparing a pellet by cold pressing [96] However, pressing powder in a die is typically suitable only at a laboratory scale and is insufficient for producing the thin samples required for mass productionOpen Ceramics
.jpg)
Powder Process an overview ScienceDirect Topics
Methods for Synthesis of Nanoparticles and Fabrication of Nanocomposites Ajay Vasudeo Rane, Sabu Thomas, in Synthesis of Inorganic Nanomaterials, 2018 5331 Powder Process The powder process is one of the techniques used in the manufacture of ceramic nanocomposites, in which compression, rolling, and extrusion are used as the processing method In a simple The Lay Ceramic pellets, developed by engineer Kai Parthy, are part of the Lay Filaments brand, known for its specialized and functional 3D printing materialsThese pellets come in the format of very fine sinterable powder that consists of a polymeric binder combined with modified clay powderDue to their tiny particle size distribution ranging from 005 to 15 mm the Lay Ceramic Lay Ceramic pellets (in powder) Kai ParthyDownload scientific diagram A model explaining the sintering process from publication: Calcia Stabilized Ceria Doped Zirconia Nanocrystalline Ceramic Calciastabilized cerium doped cubic A model explaining the sintering process ResearchGate2013年2月23日 Tab 2 Comparison between straight travelling grate process and grate kiln process : Sl No Straight travelling grate process: Grate kiln process: 1: Drying , preheating, induration, and cooling cycle is carried out in a single unit: Drying , preheating, induration, and cooling cycle is carried out in different units: 2Introduction to Iron ore Pellets and Pelletizing processes