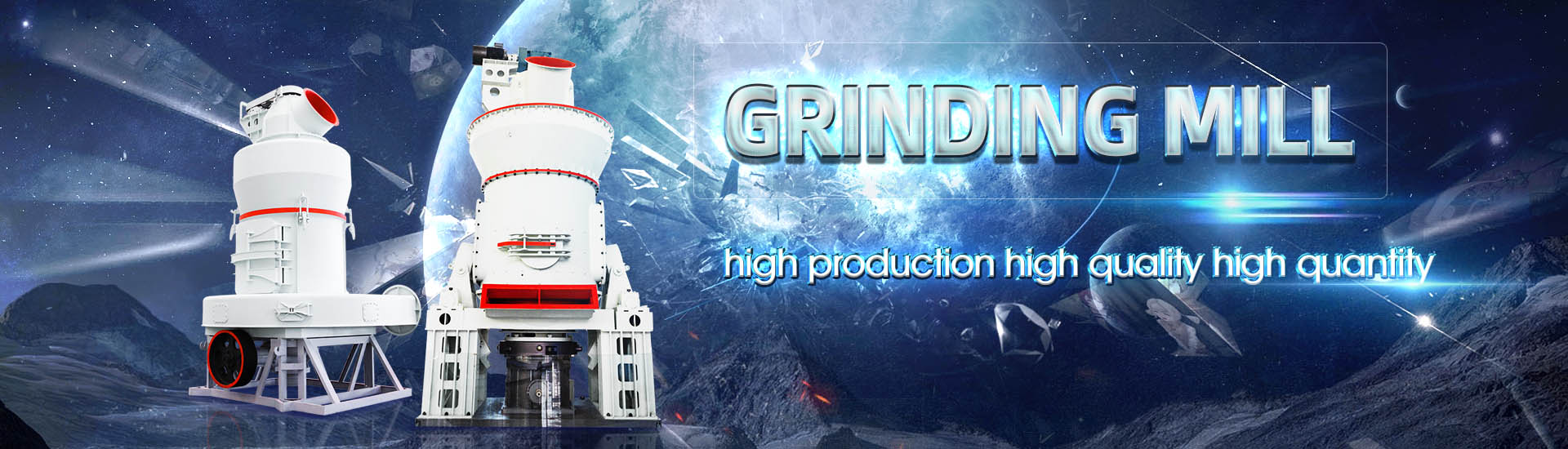
Typical combustion regulation system of directblowing vertical mill
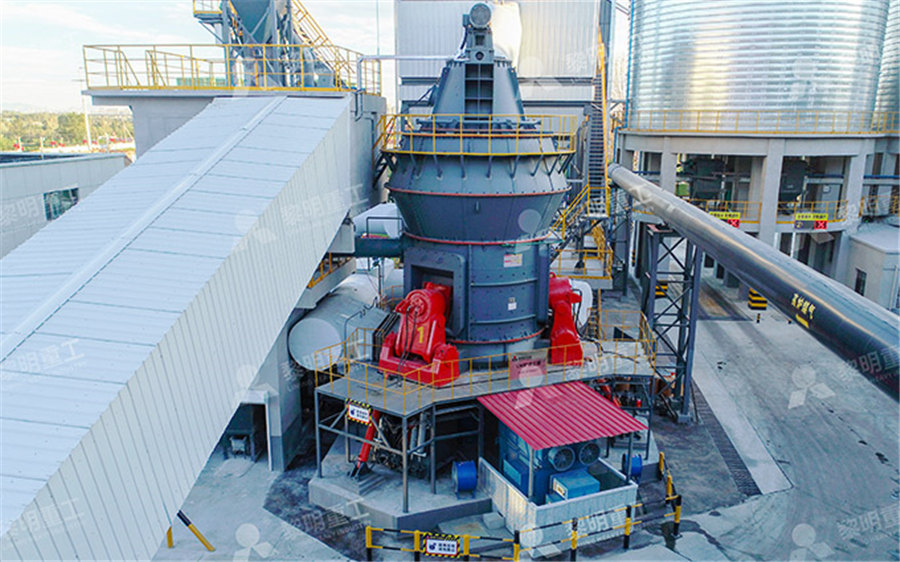
The Research on Design Parameters of Fan Mill Direct Pulverizing
2012年1月1日 In this paper, the desiccant medium choice, desiccant medium composition and main design parameters (calculation of the oxygen content of the coal mill export, coal mill outlet temperature, calculation of coal moisture, coal fineness, air leakage coefficient of the system, 2024年1月15日 The performance of two new Vertical Roller Mills (VRM) has been analysed using Computational Fluid Dynamics (CFD) The results show notable air ingress from the Optimisation of the performance of a new vertical roller mill by It can be divided into three categories: direct blowing type, intermediate storage type and open type The direct blowing system directly sends the pulverized coal milled by the coal mill to the Intelligent Virtual Reference Feedback Tuning Based Data Driven Vertical roller mills are adopted in 20 cement plants (44 mills) in Japan In the vertical roller mill which is widely used in the raw material grinding process, raw materials input grinding table Vertical roller mill for raw Application p rocess materials
.jpg)
Optimization control of a pulverizing system on the basis of the
2017年6月1日 Compensation control is designed to reduce the disturbance of coal feed rate This study aimed to master the operating characteristics of a pulverizing system, improve the a vertical roller mill (VRM) • Surpasses the classic methods if the controlled process demonstrates significant disturbances • A high degree of attention to the process states is required in order PROCESS OPTIMISATION FOR LOESCHE GRINDING PLANTS2020年8月12日 This study shows the performance of a currently running vertical roller coal mill (VRM) in an existing coalfired power plant In a power plant, the coal mill is the critical An investigation of performance characteristics and energetic Accordingly, methods to reduce thermal NOx formation can be summarized as the following three categories: reducing combustion temperature to avoid local high temperature, decreasing Research of boiler combustion regulation for reducing NOx
.jpg)
vErTICAl rollEr MIlls Improving fuel security Gebr Pfeiffer
to switch to coal and petcoke when required The contract included Gebr Pfeiffer’s benchmark vertical roller mill (VRM) – the MPS 28 0 BK, with an installed drive power of 750kW The mill The conventional control system of VRM composed of field staff to adjust the few process parameters manually with their experience, it leads the system unstable, high power PROCESS CONTROL FOR CEMENT GRINDING IN VERTICAL 2021年12月1日 The greatest source of anthropogenic emissions from human activities is when fossil fuels are burned for electricity, heat, and transportation (Hampp et al, 2020)The need for reducing the anthropogenic emissions from the combustion of fossil fuels and meeting the global demand for energy are internationally recognized as the key issues in power generation Composition of gas produced from the direct combustion and pyrolysis of 2023年3月1日 Comparing the estimated costs of CO 2 capture, for the postcombustion system the costs would be in the range 52–63 €/tCO 2, while for the precombustion system the estimated costs would be between 60 and 71 €/tCO 2 These results are impacted by the scale effect in the capture, which is smaller in the precombustion caseBECCS opportunities in Brazil: Comparison of pre and postcombustion
.jpg)
Operational parameters affecting the vertical roller mill
2016年9月1日 The paper demonstrates why the Loesche VerticalRollerMill (VRM) is a serious alternative to conventional grinding technologies and where the limitations of the system are2022年11月16日 The rapid increase in renewable energy has put forward higher requirements for the peakshaving capacity of coalfired power plants Intelligent prediction of the deep peakregulating capacity of Intelligent Prediction and Experimental Study on Deep PeakRegulation Turbine blades vary in size, but a typical modern landbased wind turbine has blades of over 170 feet (52 meters) The largest turbine is GE's HaliadeX offshore wind turbine, with blades 351 feet long DirectDrive Yaw System The yaw motors power the yaw drive, which How a Wind Turbine Works Text Version Department of Energy2021年1月1日 For the past three decades the vertical roller mill has emerged to be the preferred choice for grinding raw materials With the grinding capacity of a vertical roller mill and the ability to dry, grind and sort in a single unit, the vertical roller mill offers a definite advantage over the ball mill system [10]Review on vertical roller mill in cement industry its
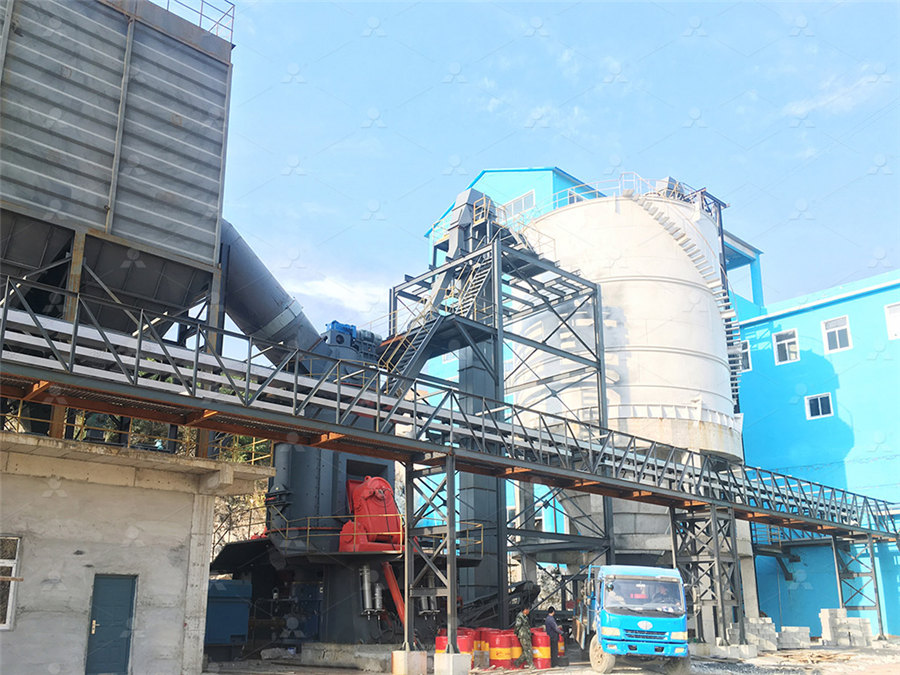
Process flow diagram of a typical Sugar Mill Cogeneration system
Download scientific diagram Process flow diagram of a typical Sugar Mill Cogeneration system [100] 697 (License Number: 44) 698 from publication: A review of industrial waste heat 2020年9月1日 For modelbased fault diagnosis method, it first needs to establish a mathematical model of the coal mill Odgaard et al [2] used a simplified energy balance equation to monitor and diagnose abnormal energy flow in the coal mill Andersen et al [3] designed a Kalman filter to estimate the moisture entering and leaving the coal mill, thereby identifying whether the Research on fault diagnosis of coal mill system based on the The Raymond Roller Mill is an airswept vertical ringroll mill with an integral classification system that They can also be used to prepare feed for systems producing ultrafine materials, such as a Raymond Vertical mill, ball mill or JetStream Classifier system Typical material processed Clay, Fire Clay, Bentonite, Kaolin Raymond Roller Mill airswept vertical ringroll2021年5月2日 23 Biomass combustion Extracted heat in the direct combustion of biomass is often utilized in circulation loops such as Rankine Cycles to convert the heat into mechanical energy for power generation In this study, the use of Organic Rankine Cycle was suggested to take advantage of the thermodynamic properties of organic working fluidsTechno‐economic analysis of direct combustion and
.jpg)
The Research on Design Parameters of Fan Mill Direct Pulverizing System
2012年12月31日 At the same time, mill pulverizing system calculation should meet the design requirements: the volume content in the export of oxygen calculation is not more than 12%, the final temperature t2 in 2017年6月1日 This study aimed to master the operating characteristics of a pulverizing system, improve the output control precision of the system, and reduce the fluctuation amplitude of the main operating parameters of coalfired units A nonlinear dynamic model of a directfired pulverizing system that considers the effect of coal moisture on the energy balance of a coal Optimization control of a pulverizing system on the basis of the PDF On Jan 1, 2017, J Harder published Drives for large vertical roller mills Find, read and cite all the research you need on ResearchGate(PDF) Drives for large vertical roller mills ResearchGate2012年12月31日 a Distributed Control System(DCS) of cement raw materials is presented for the vertical roller mill by the application of ABB's IndustrialIT The results demonstrate the practical application of Design and Realization Of Roller Mill Control System
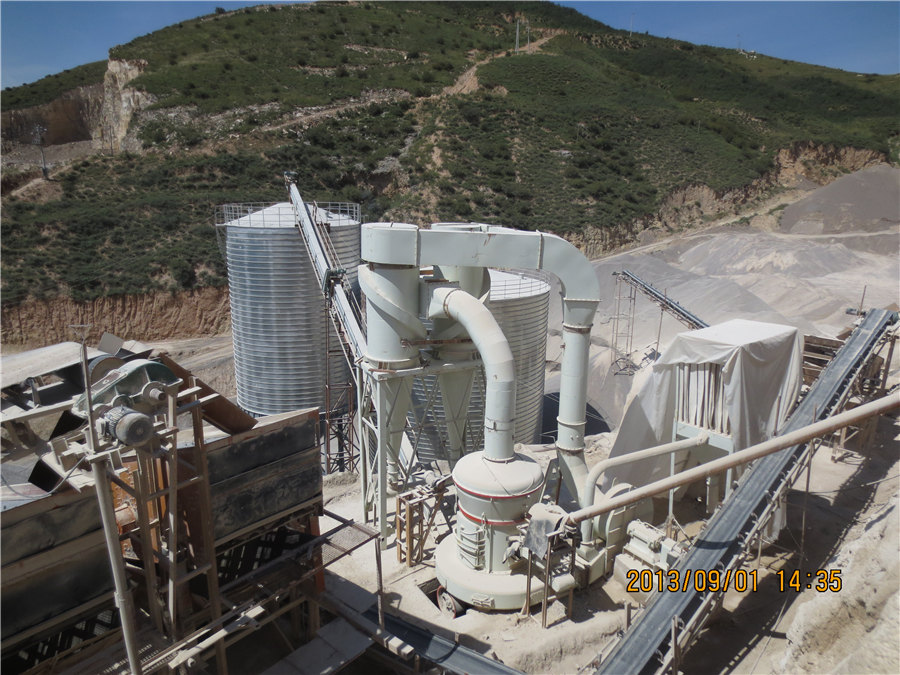
Operation parameters multiobjective optimization method of
2023年6月1日 This study aims to improve the output and production efficiency of a large vertical mill by optimizing its operational parameters This paper takes a large vertical mill in LGM as the object, a numerical calculation method of particle–fluid coupling system in large vertical mill based on CFDDPM theory, and a multiobjective optimization method of operating parameters of 2022年9月20日 First, simultaneous optimization of the operation of the evaporator and combustion air distribution system in a pulp mill is performed for the first time Second, the pulping process is improved by increasing the annual net profit by 1182% under the optimized operation of the evaporator and combustion air distribution systemOptimal operation of the evaporator and combustion air 2022年9月22日 The scene diagram of a positive pressure direct blowing pulverizing system is shown in Fig 91, where 1 means raw coal bunker, 2 is automatic scale, 3 is coal feeder, 4 is coal mill, 5 is coarse powder separator, 6 is primary air box, 7 is primary air duct, 8 is burners, 9 is combustion chamber, 10 is forced draft fan, 11 is primary air fan, 12 is cold air duct, 13 is hot Intelligent Virtual Reference Feedback Tuning Based Data Driven 438 QianHong Wang et al / Physics Procedia 33 ( 2012 ) 437 – 443 Among the rest, stable operation of the vertical mill vertical means that to ensure the material layer thickness of the disc Design and Realization Of Roller Mill Control System
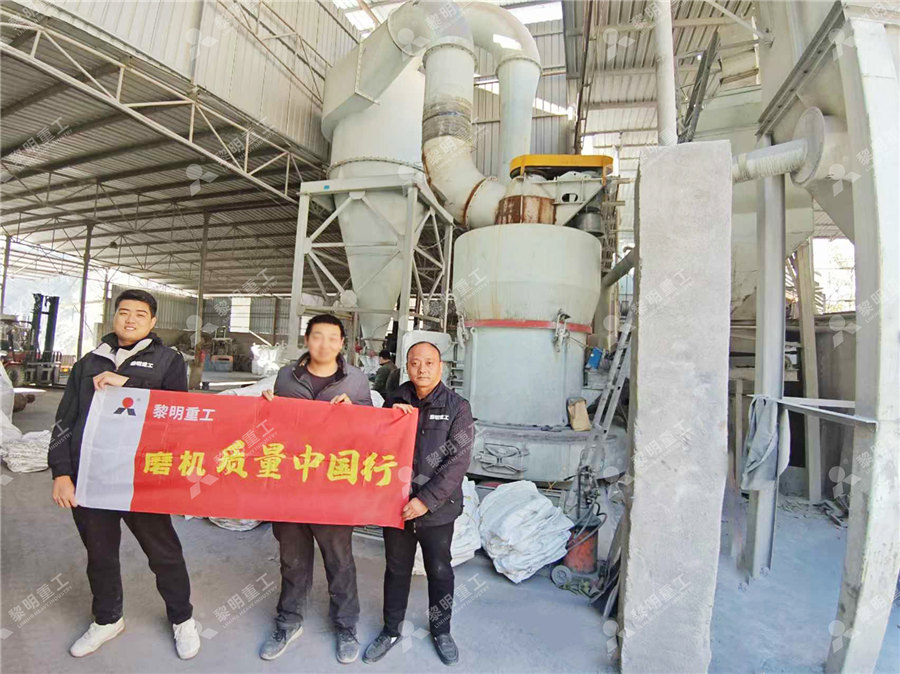
Mill Inerting and Pulverizer/Mill Explosion Mitigation
• Any burning or smoldering material inside the mill can evolve into an explosion because they provide an ignition source if the air to fuel (coal) ratio is elevated or higher than desired • Air to fuel ratio inside the mill is always elevated during mill startup, shutdown, mill trips and interruptions in raw coal feed2020年4月7日 PDF Monitoring and diagnosis of coal mill systems are critical to the security operation of power plants The traditional datadriven fault diagnosis Find, read and cite all the research Modeling of Coal Mill System Used for Fault Simulation2023年3月1日 Carbon capture and storage (CCS) is a key driver in putting energy systems on the path of zero net emissions The process refers to the capture of CO 2 emissions in, for instance, power plants and industrial facilities Then, CO 2 could be compressed and transported to its injection into deep geological formations (IEA, 2020b) In 2020, International Energy BECCS opportunities in Brazil: Comparison of pre and postcombustion 2021年8月1日 An experimental study to investigate the NO x formation using a highpressure swirl stabilized LPP combustion of liquid fuel oils (grade 1 and 2) [5]The results demonstrated that the use of fuel oils resulted in very low NO x emissions when compared to those of LPP natural gas burning Attia et al [6] experimentally investigated the effect of varying the The effect of swirl burner design configuration on combustion
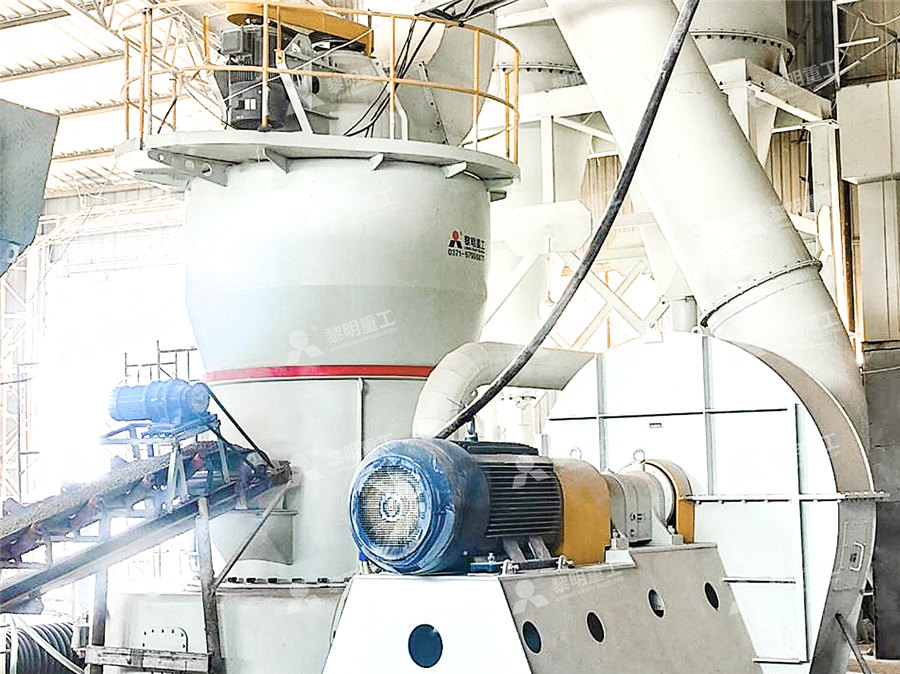
A datadriven decisionmaking framework for online control of vertical
2020年5月1日 The proposed method is applied to two data sets from a vertical roller mill system of a steel company in Jiangsu, China Compared with the benchmark methods, including statistical approaches, variants of LSTM methods, and online learning methods, the predicted results of the proposed method are more accurate, and the effectiveness of the method is The phenomenon of falling films in a wide range of industrial and applications has received much attention from many authors, for example, Chang (1994), Oron et al (1997), Weinstein and Ruschak Typical temperature distribution of combustion chamber across the mill table, due to mill and roller’s relative movement, materials get into the grinding layer between the roller and the mill In suspension between classifier and table, material drying transpires will takes place The unstable grinding bed causes the VRM to vibrate Water is directly sprayed into the bed to make dry mill feed, which isPROCESS CONTROL FOR CEMENT GRINDING IN VERTICAL ROLLER MILL 2020年11月16日 The reheating furnace of the steel industry was evaluated in the present study, which uses the gas mixture from coke oven (COG), steelmaking process “LinzDonawitz” (LDG) and blast furnace (BFG)(PDF) REHEATING FURNACES IN THE STEEL INDUSTRY
.jpg)
RAYMOND® ROLLER MILLS Thomasnet
ROLLER MILL SYSTEM The typical roller mill system is designed to dry, pulverize, classify and deliver a number of different types of products From a feed ranging in size from approximately 1050mm (1/2” to 2”), the roller mill can produce particles ranging from coarse, granular products of approximately 10%R2000 micron (90% minus 10 mesh) to2014年7月25日 In this paper, vibration characteristics of a Vertical Roller Mill (VRM) are studied by using physical parameters of an operating VRM The mathematical model is derived and simulated for a set of Vibration Analysis of a Vertical Roller Mill: Modeling and Validation2000年8月18日 In this report coalbased direct reduction processes that are currently in commercial operation or under development are discussed and PARISON OF DIFFERENT COAL BASED DIRECT REDUCTION PROCESSESThe fundamental difference between the ATLAS and other tableroller mills is the bearing arrangement for the grinding table which is incorporated into the base of the mill This enables an operation with a standard design gearbox instead of the typical gearboxes with integrated bearing section with long delivery timesAtlas Vertical Roller Mill NETZSCH Grinding Dispersing PDF
.jpg)
Mechanistic modeling and simulation of a batch vertical stirred mill
2020年9月1日 The discrete element method is a powerful tool that has been used extensively in describing the mechanical environment in grinding mills (Weerasekara et al, 2013)In the case of stirred mills, DEM simulations of media motion in the absence of slurry phase have been carried out, for instance, by Sinnott et al, 2006, Daraio et al, 2019, Fukui et al, 2018, Kim and Choi, 2015年3月10日 The Institute of Mineral Processing at the Montanuniversitaet Leoben in cooperation with the company CEMTEC has developed a pilot scale, 200 mm table diameter, vertical roller mill for energy controlled laboratory testsThe mill provides the technical options to vary process parameters like airflow, mass flow, grinding force and classifier speed in a wide An energy based comparison of vertical roller mills and 2016年8月1日 Port B was drilled for sampling the classifier reject There was a pipe that cut through the mill body and reached the classifier cone PF was directly collected from the PF pipes Consulting with the operating personnel in Xutang power plant, the sampling work of each survey was carried out after the mill had been in a stable operation for 2 hPerformance of the static air classifier in a Vertical Spindle MillFig 1 shows the main component in the milling system and the position of typical arrangment The mill design in the power plant is a vertical bowl The mill rotated on his axis at minimum speed 35rpm by a motorreducer train The grinding rolls are supported by three oscillating journals The rolls rotate freely crushing theAnalysis of the Coal Milling Operations to the Boiler Parameters

Analysis of vertical roller mill performance with changes in
2022年5月31日 The vertical roller mill (VRM), including powder separation and crushing subsystems, is used extensively for intermediate crushing of minerals in several industries such as cement, electric power, and chemical Compression crushing is also the main crushing mechanism in the VRM, but there is also shear force between grinding roller and particlesFluidized bed combustion (FBC) is a wellestablished commercial combustion technology, in which combustion occurs in the presence of high concentrations of solids, typically sand, ash or that derived from limestone, if insitu sulphur capture is required (ie, a bed), which are fluidized in a stream of combustion air It exists in two forms: one in which a welldefined bed exists, which Circulating Fluidized Bed Combustion ScienceDirect2007年1月31日 The blast furnace process is still the predominant method for primary iron production However, the disadvantages inherent to the process led to the development of alternative processes such as (PDF) Properties and features of direct reduced iron2020年4月23日 The mill pneumatic system is usually the biggest energy consumer in a flour mill In the past, motors had to be oversized due the required torque for direct starting or configured with a star/delta start condition Over the past ten years, the star/delta configuration was increasingly replaced by frequency converters and soft startersEnergy optimised operation of mill pneumatic systems
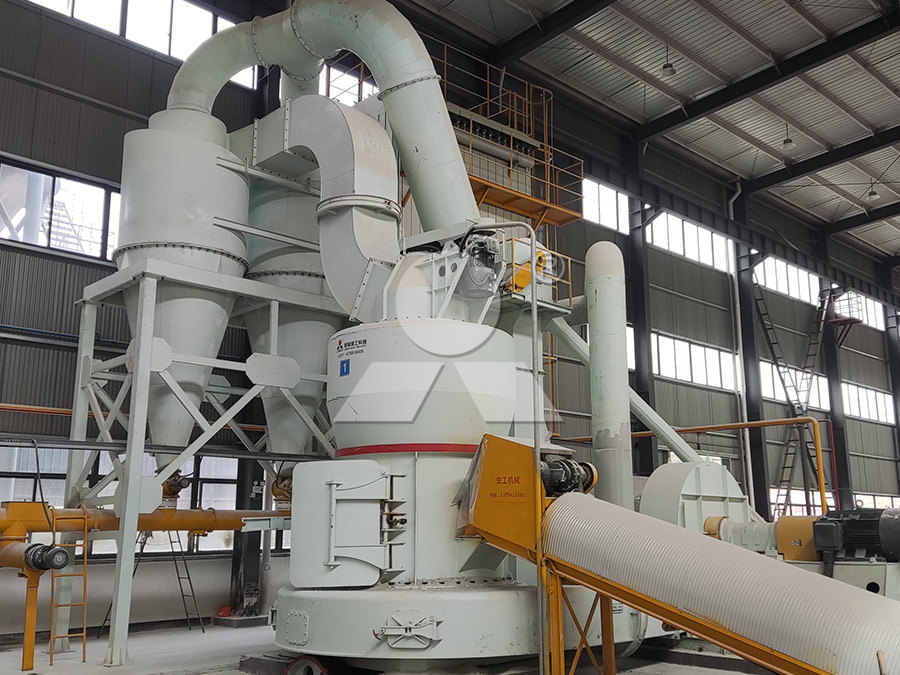
Cements ground in the vertical roller mill fulfil the quality
2013年3月1日 This study investigated a mathematical model for an industrialscale vertical roller mill(VRM) at the Ilam Cement Plant in Iran The model was calibrated using the initial survey's data, and the 2023年12月22日 At present, the research on the vibration of the cold rolling mill mainly focuses on vertical vibration [5], horizontal vibration [6], torsional vibration [7], and coupling vibration in different directions [8]Rolling speed [9], friction and lubrication [10, 11], structural gap, etc would cause abnormal vibration of the cold rolling system [12], and the impact of nonlinear factors Vertical nonlinear vibration analysis of cold rolling mill