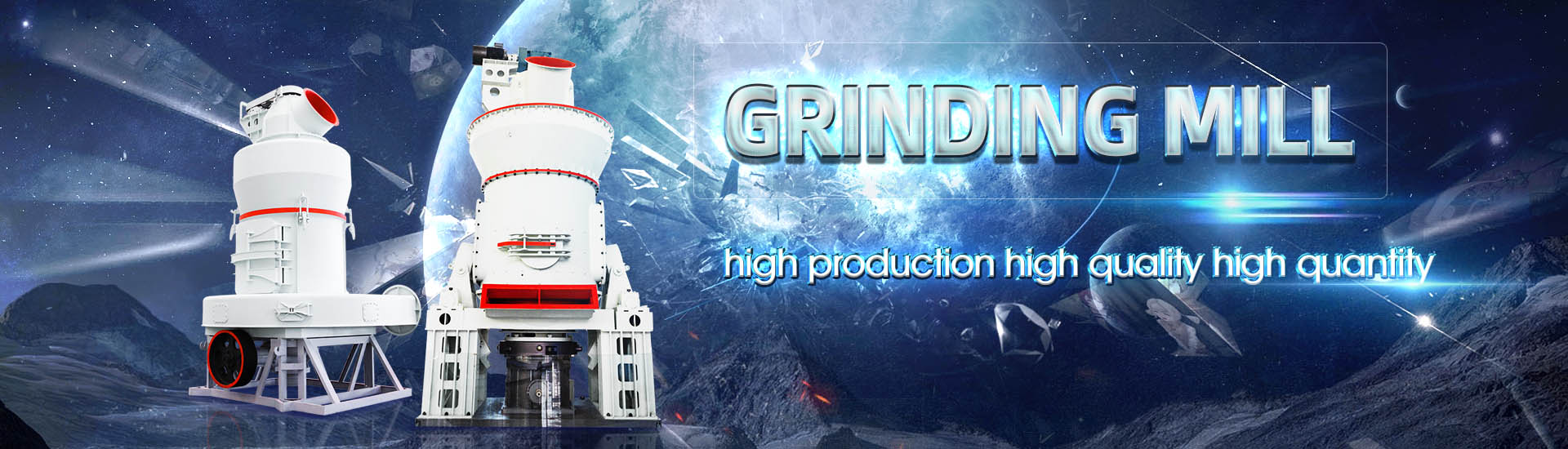
Cement production line parameters
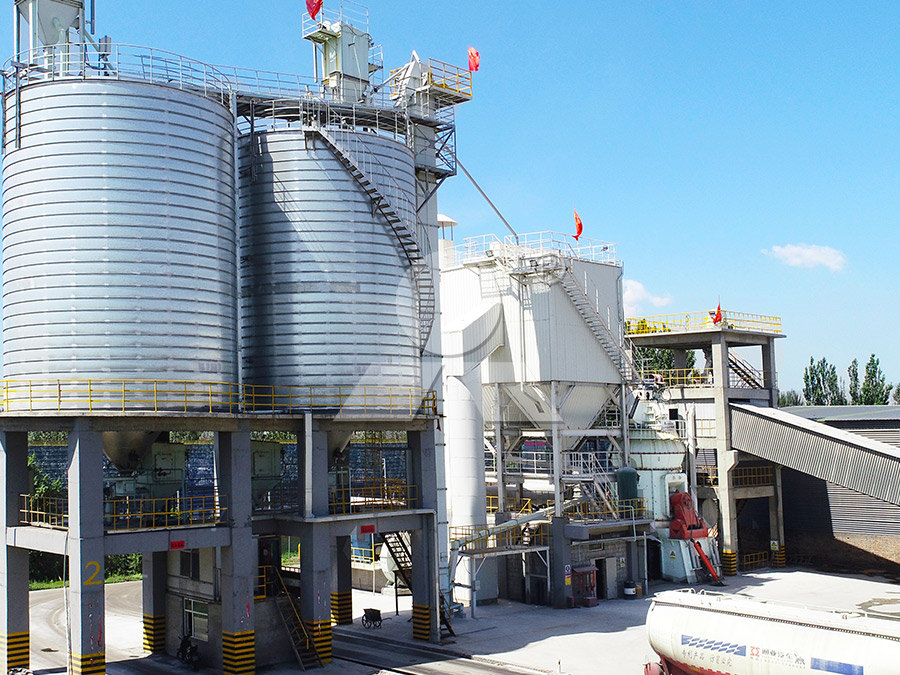
The Cement Plant Operations Handbook International Cement
The Cement Plant Operations Handbook is a concise, practical guide to cement manufacturing and is the standard reference used by plant operations personnel worldwide Providing a 2020年2月15日 There are several process parameters in a cement rotary kiln system, which should be studied in order to observe trends that may indicate problems and provide Parametric Studies of Cement Production Processes John 2020 • A reference cement clinker production line • Specs for standard process units • Utilities description, cost and climate impact • Extent of capture and CO 2 specs • Economic Process characteristics of clinker and cement production SINTEF2024年9月15日 Operating parameters of a cement plant were optimized by BP neural network and GA Feeding quantity of raw meal, coal at kiln inlet and outlet were the main objects The Operation optimization of cement clinker production line based
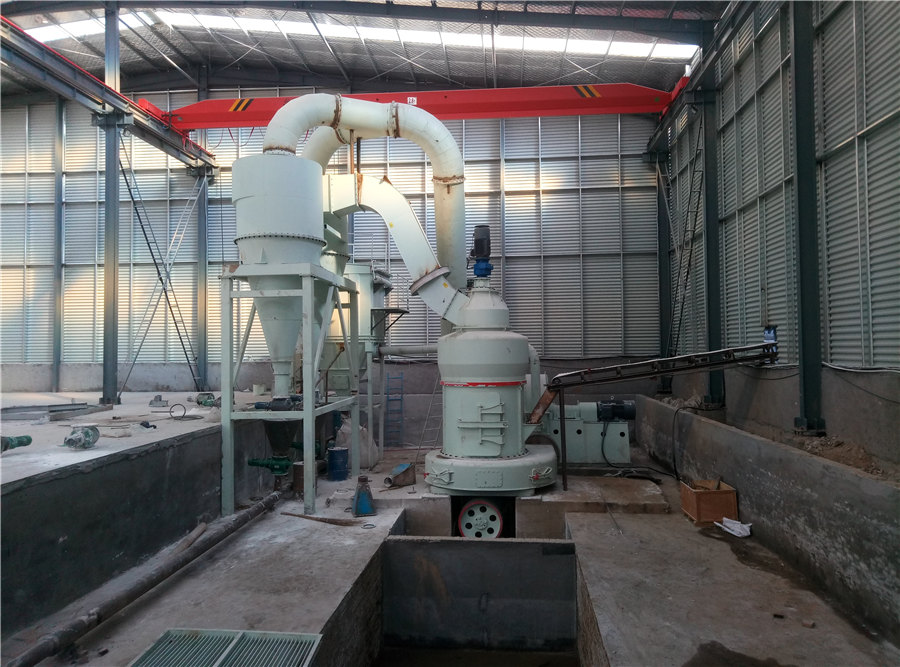
Energy and thermodynamic analysis of a typical cement
2022年10月1日 In this paper, a mass and thermal balance experiment of a 5000 t/d cement plant in China is performed to obtain the operating parameters and energy distribution The 2024年3月1日 By using these tools to guide the selection of raw materials, process parameters, and production pathways, it is possible to produce sustainable clinkers that meet highquality Cement and Concrete Composites ScienceDirectThe physical parameters are temperature, pressure, air velocity, abrasion, mechanical stress, content of liquid phase generated at the operating temperature, liquid viscosity, surface Chapter 4 Cement Manufacturing and Process Control2019年8月27日 The measured values of those parameters that are the most important for kiln operation are herein called the control parameters To keep the control parameters close to a Cement Manufacturing and Process Control SpringerLink
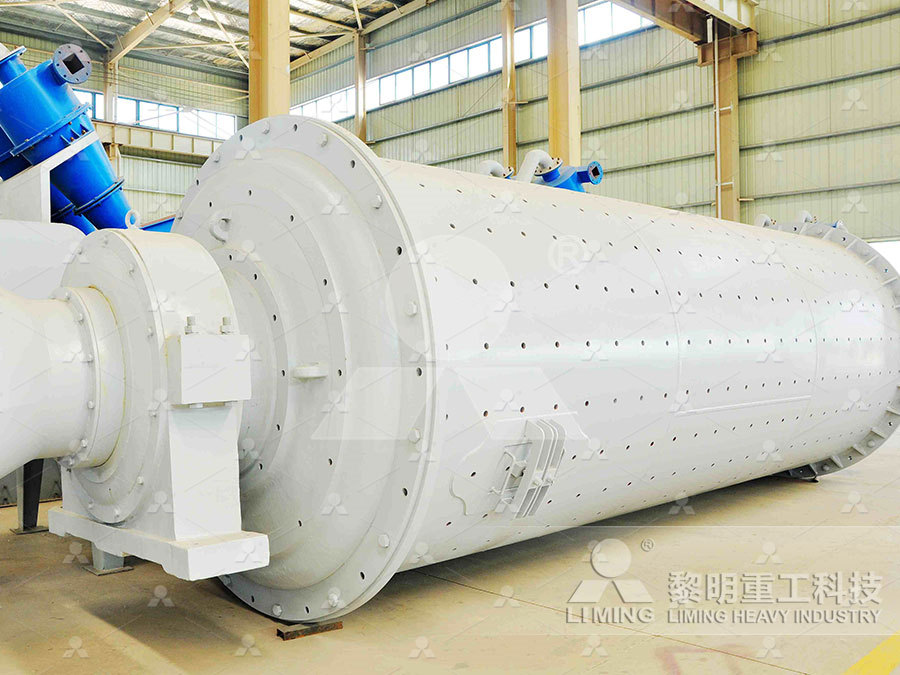
A practical guide to improving cement manufacturing processes
There are 4 stages of cement production that help maintain consistent raw material quality with minimal chemistry deviation, from quarry to silo to customer The Quarry: The cement AGICO dry process cement production line comprehensively adopts the IT technology, multifunction grinding system, newtype wearresisting and heatresisting materials, mechanical powder conveying device, and some other Cement Production Line Cement Manufacturing 2024年1月29日 Recent advances in artificial intelligence (AI) technologies such as deep learning open up new opportunities for various industries, such as cement manufacturing, to transition from traditional humanaided manually Quality Control of Cement Clinker through Operating 2024年9月15日 Operation optimization of cement clinker production line based on neural network and genetic algorithm Author links open overlay panel Lisheng Pan a, Yuan according to a series of actual operation data tested during a whole year in a Chinese cement clinker production line The three operation parameters such as the raw meal Operation optimization of cement clinker production line based
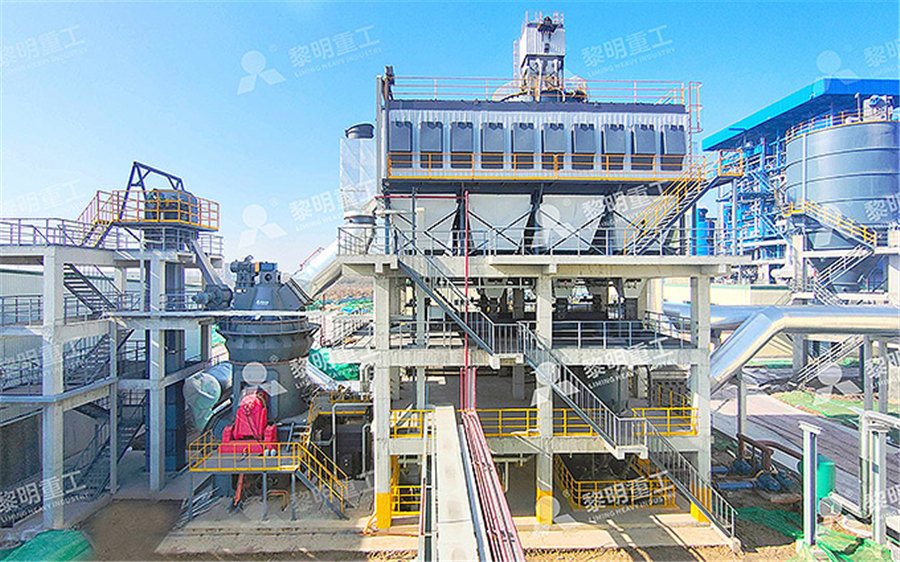
Cement Manufacturing and Process Control SpringerLink
2019年8月27日 The major raw materials used as a source of CaO for cement manufacturing are limestone, chalk, marl, etc These raw materials by virtue of their natural occurrence contains other mineral impurities eg, MgO, SiO 2, Al 2 O 3, Fe 2 O 3, alkali compounds, and sulfidesThese impurities play an important role to influence the cement manufacturing 2023年12月26日 As we all know, the dryprocess cement production line is commonly used in the cement industry The new type of dryprocess cement production process includes four main sections: Prehomogenization of raw materials, homogenization of raw materials, clinker firing, cement grinding, etc Raw material conveying system The raw material, including limestone, 6 Cement Equipment For Dryprocess Cement Production LineThe cement production process 1 The Quarry: The cement production process begins with the extraction of limestone and clay from the quarry 2 Crusher and PreBlending: The material is then crushed to reduce particle sizes and blended to reduce variability in composition 3 Raw Mill and Kiln: Raw materials and additives areA practical guide to improving cement manufacturing processes The 2500t / d cement clinker production line adopts a new dry process, with an annual output of 775,000 tons of cement clinker and a total cement output of 105 million tons / year Tel:+86513 Email: 2500TPD new type dry process cement clinker production line
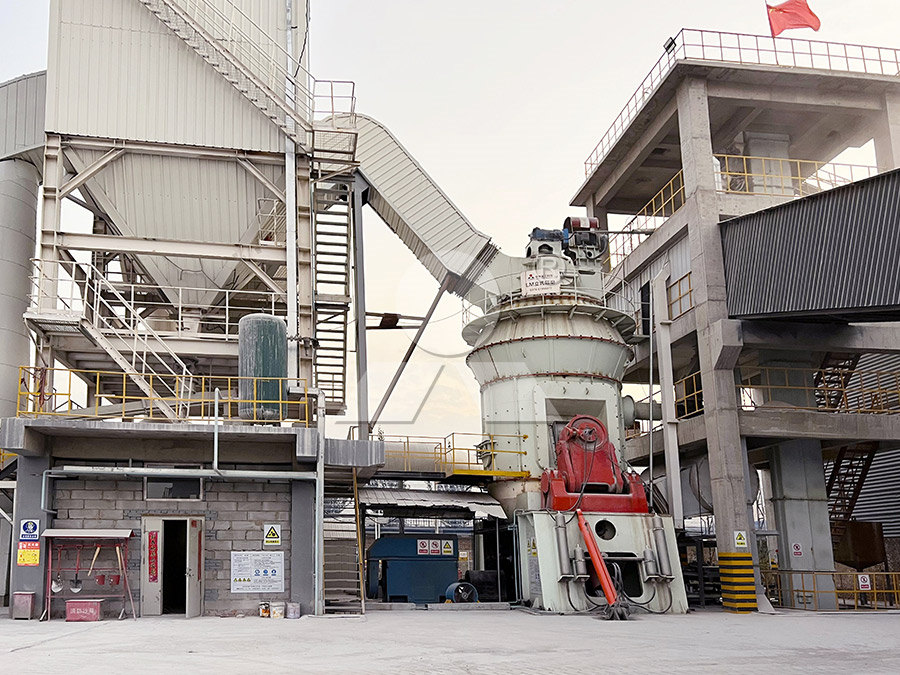
Cement Production Line Zoomjo Group
Large Cement Plant / Cement Factory Cost Capacity: 2,500 – 7,000 TPD For largesized cement enterprises, mini cement plant with lower output cannot support the higher market requirement, so sometimes people would like to build one largescale cement plant with greater production Free Scheme and Estimate Cost can be sent to you now 12024年9月15日 The above three operation parameters were further optimized to achieve the lowest specific standard coal consumption by genetic algorithm The schematic diagram of cement clinker production process is shown in Fig 1, and the main parameters mentioned above can be found in the system diagramOperation optimization of cement clinker production line based 2024年3月1日 We’ve found that our cement production articles are some of the highest viewed content on our blog site So, we’ve put together a list of our blog articles related to the cement production process and analysis Here are the top 15 of our most read cement articles, in no particular order:Everything about Cement Production Thermo Fisher Scientific2024年6月1日 Cement production accounts for approximately 7–8 % of global CO 2 emissions, Reference clinker burning line with CAP CO 2 capture [107] This involves the implementation of advanced control systems to monitor and regulate kiln parameters such as temperature, airflow and fueltoair ratiosDecarbonising cement and concrete production: Strategies,
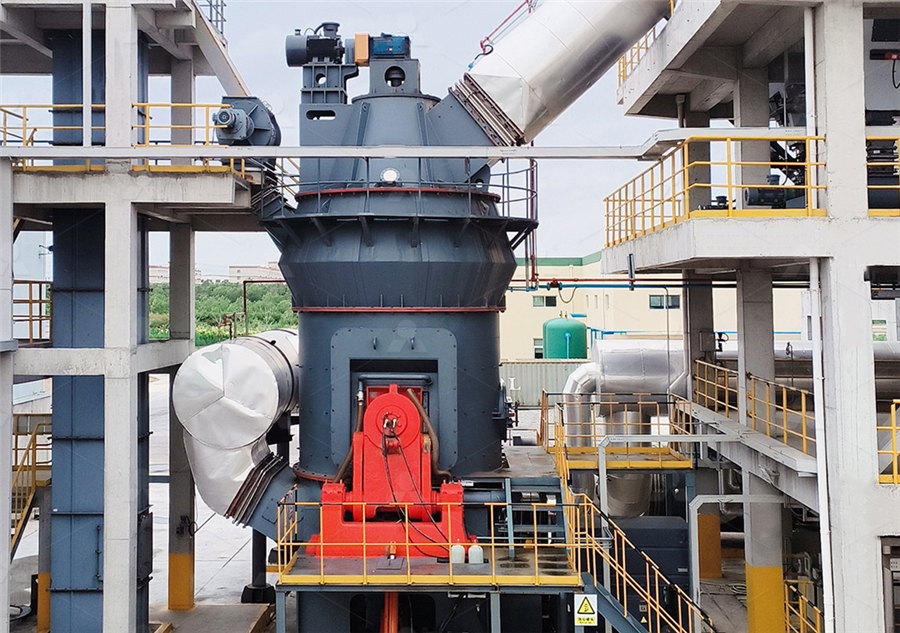
Predictive Model for Cement Clinker Quality
2016年1月1日 this study is foc used on the d evelopment o f a regressionbased model for on line estimation of clinker quali ty clinker quality parameters for cement production can be achieved 22023年12月11日 Countryspecific parameters on cement production, energy intensity, emission factor, which we obtained from the National Cement Production Line Atlas 2019 published by CCEMENTProjecting future carbon emissions from cement production in CEMENT PRODUCTION AND QUALITY CONTROL A Cement manufacturing Process Source:civilengineeringforumme The whole process of cement manufacturing in Messebo Cement plant which consists of two separate Cement Production lines can be summarized into the following processes ;as can be seen in the process and Quality flow diagram below; 1CEMENT PRODUCTION AND QUALITY CONTROLCement production line is a production line construction project composed of a series of supporting equipment for cement production It is mainly composed of crushing equipment, homogenizing equipment, raw meal preparation equipment, drying equipment, preheating and decomposition equipment, clinker burning equipment, cooling equipment, grinding equipment, Cement production lineNanjing BOSIHAN International Trade
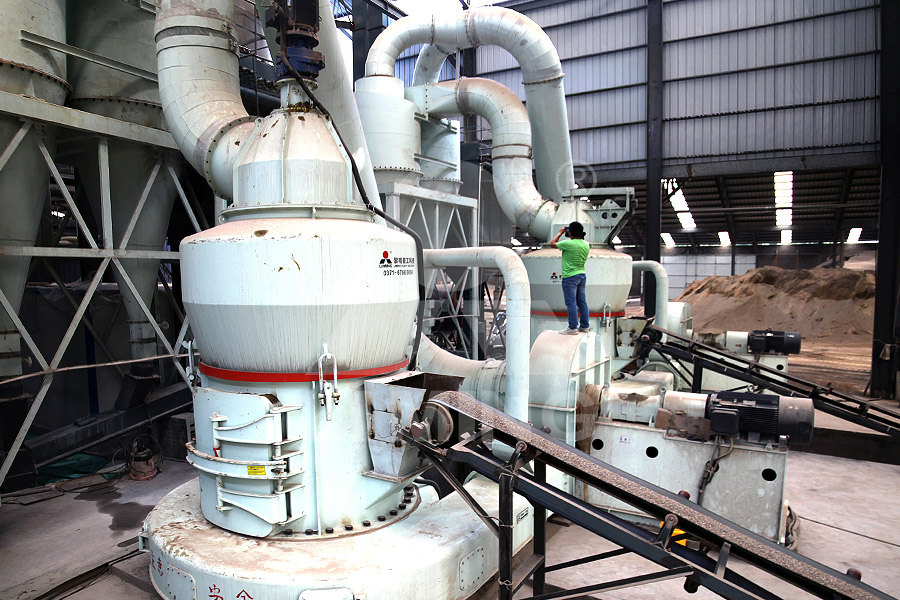
(PDF) Modeling operational cement rotary kiln variables with
2022年10月20日 Cement production plants are one of the extremest CO2 emissions, and the rotary kiln is a cement plant’s most energyconsuming and energywasting unit Thus, enhancing its operation assessments For a more detailed account of the cement production process, see the Understanding Cement book View of a cement kiln (the long nearlyhorizontal cylinder) and preheater tower (Picture courtesy Castle Cement) Summary of production process Cement is typically made from limestone and clay or shaleCement manufacturing components of a cement plant Understanding Cement2015年8月1日 Cement production, which is highly dependent on the availability of natural resources, will face severe resource constraints in the future This is especially true for the cement industry in China(PDF) Analysis of material flow and consumption in cement production 300 t/d Cement Production Line 300t/d cement production line designed by Great Wall machinery, fully learns from the lessons and experiences of more than 20 years of NSP production line design, advanced vertical roller mill grinding system and DCS automatic control system; 3000 t/d Cement Production Line Xinxiang Great Wall Machinery provides turnkey basis service Cement Production Line
.jpg)
Everything you need to know about Kiln Burning Systems
An additional 5% to 10% production in a year will impact spectacularly on the profit line given the large proportion of fixed costs at a cement plant The cement kiln requires a particular heat transfer regime for best fuel economy, optimum product quality and maximum productionNote that the Cement CO 2 and Energy Protocol and the Protocol Spreadsheet have a specific line number index (see Column B in the Excel® file) These line numbers are used throughout all documents of the Protocol They differ from the Excel® row numbers In the Internet Manual, the index of line numbers consists of the word “line” and the line number with three digitsLinebyLine Cement CO2 ProtocolHeshmat et al (2017) studied an actual standing cement production line and identified the bottlenecks encountered with the production line The observed bottlenecks were resolved using simulationSchematic diagram of the cement production line 2022年10月1日 Cement production is one of the energyintensive industries, which consumes nearly 5% of the global industrial energy [1, 2]In cement production, energy cost accounts for 30%–40% of the total production cost [3]In particular, China's cement production accounts for 55–60% of the world's cement production [4]The new dry process cement production Energy and thermodynamic analysis of a typical cement production

(PDF) Control Charts and Models Predicting Cement
2012年7月1日 The present study aims to describe control charts techniques daily applied in the quality control of cement production and at the same time to develop mathematical models predicting the cement In the cement production line, producing 1 ton of Cement need grind at least 3 tons of materials (including raw materials, fuel, clinker, mixed materials, gypsum)Grinding operation consumes about 60% of total power in cement plants, raw material grinding more than 30%, while coal mill used in cement plant consumes 3%, cement grinding about 40%Cement Production Line2020年8月25日 As we all know, there are two elements to affect the quality and efficiency of the cement production line: cement production process and cement equipment Cement equipment refers to all equipment in the cement plant, such as cement mill, cement crusher, cement kiln, cement silo, cement preheater, etcCement Production Process Cement Manufacturing Process AGICO CEMENT2021年8月30日 The cement manufacturing industry has played a fundamental role in global economic development, but its production is a major facilitator to anthropogenic CO2 release and solid waste generationHealth Risk and Environmental Assessment of Cement Production
.jpg)
Online Material Analysis for Cement Production FAQs
With the use of realtime analysis results from the online analyzer and the optimization parameters in the software, the standard deviation of modulus in raw meal production was decreased by 70% for LSF, 50% for SM, and 33% for AM With the production of more homogeneous and stable raw meal, the clinker quality was also increased2017年10月20日 1 Introduction Nowadays, cement manufacturing is an energyintensive industry The energy costs of cement industry are about 40% of the product cost that indicates that this sector is one of the biggest CO 2 emitter The global anthropogenic CO 2 emission of cement industry is approximately 5% []The International Energy Agency reported in 2011 that Heat Integration in a Cement Production IntechOpenallow production of cements with minimum 28 day strengths as low as 25 MPa This means that cement is often produced with strength averages ranging from 30 to more than 60 MPa at 28 days, along with correspondingly variable CO 2 emi ssions However, comparing the trueProduct Quality and Sustainability in the Cement IndustryThe grate cooler is a quenching type cement cooler applied for the cement manufacturing plant According to the movement mode of the grate, the grate cooler can be divided into three types, rotary type, vibrating type, and push Grate cooler Cement Plant
.jpg)
1000t/d cement production lineChina Pengfei Group Co,Ltd
During the process of cement production,it needs grinding three tons materials for product one tone portland cement (including all kinds of raw materials、fuels、clinkers、compound material、gypsum)According to the statistics,the cement dry process production line grinding operation needs to consume 60% power of the the whole plant, among it the raw material grinding elemental analysis of cement D on’t estimate, measure R ealtime elemental analysis from quarry to kiln Figure 2: PGNAA and PFTNA capabilities in cement production For cement manufacturers, neutron activation analysis is a particularly compelling technique because of its ability to: • Directly measure key compounds of interest, includingCostefficient strategies for sustainable cement productionSustainable cement production; Alternative fuels in cement kilns; Cement kiln safety; Energy efficiency in cement kilns; Future of cement kilns TO Download this post and all the books and excel sheets and my personal notes and presentations I collected about cement industry in the last 30 years click the below paypal linkComprehensive Guide to Cement Kilns: Processes, Types, Cement conveyor refers to a belt conveyor in cement plant, which is necessary accessory equipment in the cement production line A belt conveyor is a kind of material handling equipment with strong adaptability, applied for conveying bulk density less than 167t / m³, it is mostly used for powder, granular, small lump materials, and bagged materials, such as sand, ore, coal, Cement Conveyor Belt Conveyor In Cement Plant AGICO
.jpg)
Cement production line
Cement production line Mainly by crushing and pre homogenization, preparation of raw meal homogenization, preheating and decomposing, Thereby, it is greatly significant to select appropriate grinding mill and production process, optimize technological parameters, 2015年12月1日 The reason for the very limited additional potential savings of thermal energy is the necessary heat for the clinker production process Fig 1 shows the heat flows, the thermal input, the use for clinkering and drying, and the remaining waste heat flows that might be utilised However, the remaining waste heat is already used to a high degree, indicated by the already Process technology for efficient and sustainable cement production2024年3月1日 This study quantified emissions' impacts from a cement production system in terms of emergy using the approach framework proposed by Zhang et al, in 2009 [44] because cement production has similar emission characteristics to steel production; however, the specific parameters should be adjusted according to characteristics of systems in studyImpacts of energysaving and emissionreduction on sustainability OWNING AND READING MOST IMPORTANT BOOKS IN CEMENT INDUSTRY + MANUALS AND NOTES AND SHEETS FROM THE MOST SUCCESSFUL PLAYERS IN CEMENT INDUSTRY WILL CHANGE YOUR CAREER AND WILL MAKE YOU REACH MANAGERIAL POSITIONS FASTER , Control Parameters The most important control parameters in any Kiln Control and Operation INFINITY FOR CEMENT EQUIPMENT
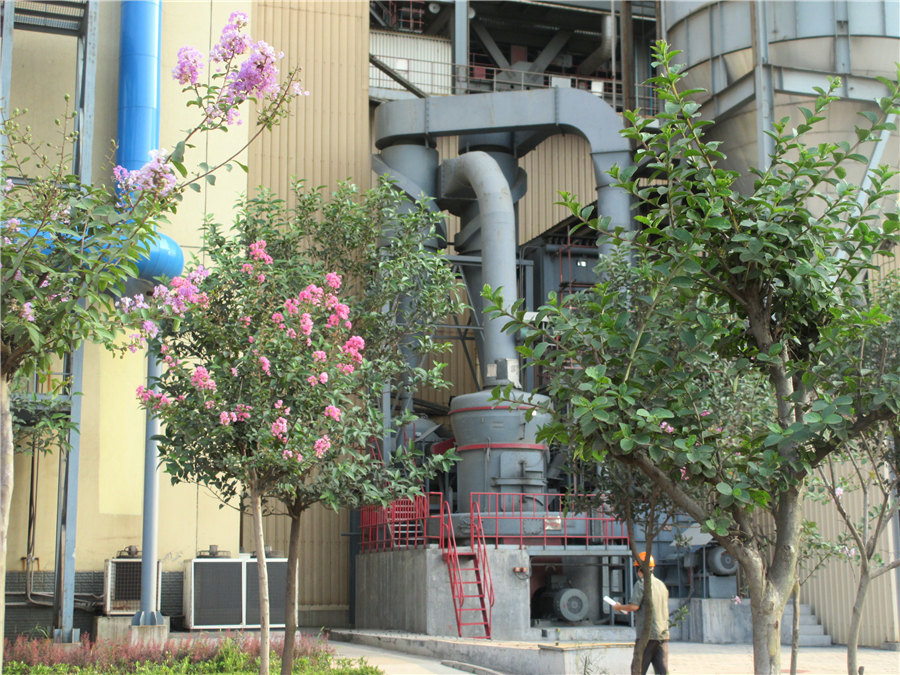
Preconditions for achieving carbon neutrality in cement production
2023年11月1日 However, the potential of CCUS to help reach climateneutral cement production depends on the specific operational parameters under which the cement plants are operated In addition, the postcapture downstream activities, such as transport, storage, and conversion, are geographically and contextdependent