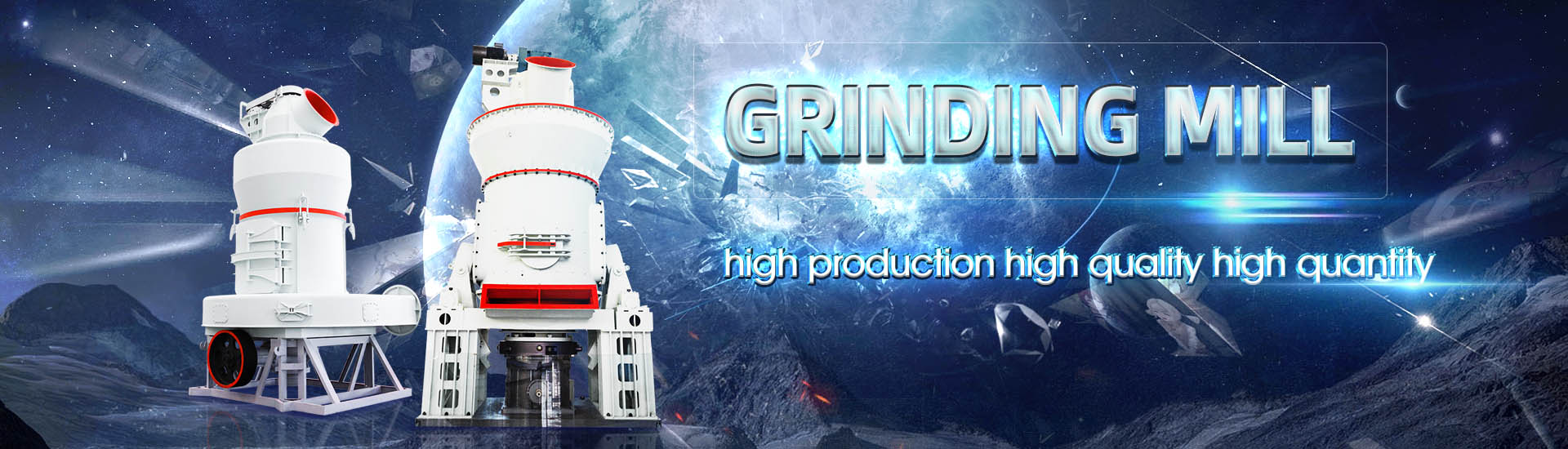
Electrolytic aluminum waste slag mill Calcium carbonate station
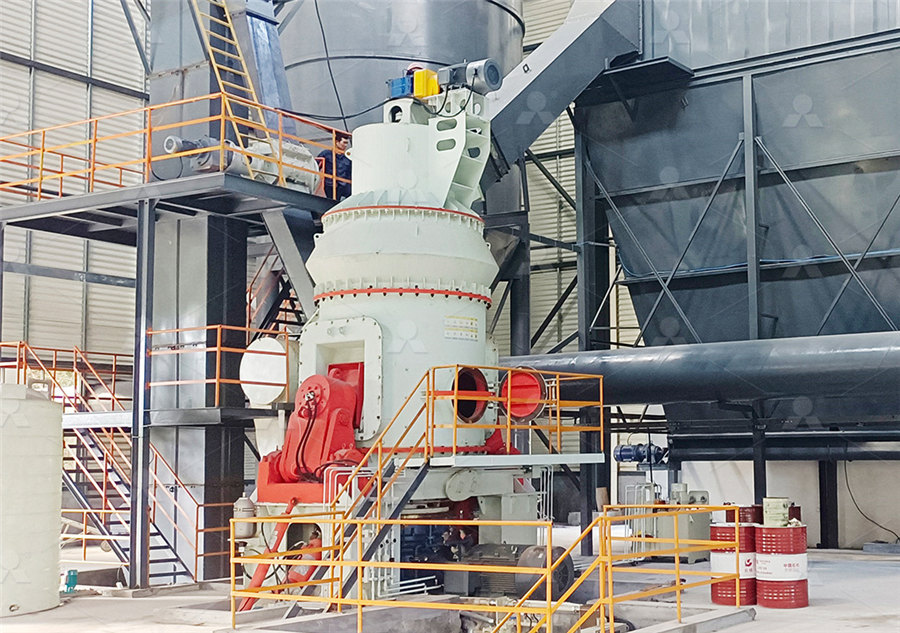
The recycling of carbonrich solid wastes from aluminum
2024年5月23日 Here, we review carbonrich solid wastes with focus on sources and hazards, detoxification, separation, recovery, recycling and disposal Treatment techniques include 2023年9月1日 本研究采用湿法冶金工艺,使用碳酸钠溶液作为浸出剂,从含锂铝电解渣中选择性浸出锂。 锂的浸出效率高达 9912%,而钙 (Ca) 和铝 (Al) 等其他元素的浸出率极低。 此外, 从废弃含锂铝电解渣中选择性回收碳酸锂的清洁工艺 2023年5月20日 Spent carbon anode (SCA) discharged from the aluminum electrolysis industry is an unavoidable solid waste with an estimated production of 700 kilotons in 2021, which has Regeneration of raw materials for aluminum electrolysis from 2024年2月1日 Aluminum metal was produced using the cryolitealumina molten salt electrolysis method (Ishak et al, 2017)A large amount electrolytic aluminum slag (EAS) is generated during the electrolysis process, as the falling of carbon particles on the anode into the electrolysis cells and the accumulation of lithium fluorine result in energy consumption and electrolyte scrapping Efficient lithium recovery from electrolytic aluminum slag via an
.jpg)
Research on the Coprocessing of Mixed Electrolytic Aluminum Waste
Research on the Coprocessing of Mixed Electrolytic Aluminum Waste in Circulating Fluidized Bed Boiler Lei Shi1, grinding the materials with an electric mill, 50 grams of electrolytic aluminum waste samples were sieved to 0075 mm Blending ratio Calcium carbonate/g Condition 1 5:5 0 Condition 2 7:3 0 Condition 3 :7 02022年12月12日 Based on the research on bulk solid waste contact molding technology by our team [49], the comprehensive performance of pressed bricks with different ratios of aluminum ash and calcium carbide slag was investigated, the ratios of aluminum ash and calcium carbide slag are 9:1 ∼ 1:9 and pure aluminum ash and calcium carbide slag, the pressing pressure is 300 Comprehensive performance study of aluminum ash and calcium Research on the Coprocessing of Mixed Electrolytic Aluminum Waste in Circulating Fluidized Bed Boiler Lei Shi1, grinding the materials with an electric mill, 50 grams of electrolytic aluminum waste samples were sieved to 0075 mm Blending ratio Calcium carbonate/g Condition 1 5:5 0 Condition 2 7:3 0 Condition 3 :7 0Research on the Coprocessing of Mixed Electrolytic Aluminum Waste 2022年2月19日 Recycling waste containing rare earth has always been a research hotspot The molten salt electrolysis process of rareearth metals and alloys generates a large amount of waste slag, which contains high rareearth content and, thus, has very considerable recovery value However, the high content of fluorine in rareearth molten salt slag brings challenges to the Recovery of RareEarth Elements from Molten Salt Electrolytic Slag
.jpg)
A novel approach for lithium recovery from waste lithium
2021年10月1日 Aluminum electrolysis of China, solid waste, such as waste aluminum electrolyte, has been largely idled and caused serious environmental pollution In this paper, a novel approach is developed for achieving the separation/recovery of lithium from spent lithiumcontaining aluminum electrolyte by a sodium carbonate roasting–acid leaching process2020年12月1日 The rapid development of the electrolytic aluminum industry in China and the increasing demand for aluminum products have led to the development of many lowgrade bauxite mines with an average Li 2 O content of at least 058% (Wang et al, 2013)Due to the use of this lowgrade bauxite in the electrolytic aluminum process, the content of lithium in the Novel process for the extraction of lithium carbonate from spent 2022年5月1日 Most widely used acidic agents could react with these carbonates and release CO2 before they were recarbonated After the leaching step, alkaline reagents (eg, NH4OH, NaOH) are introduced to Preparation of calcium carbonate nanoparticles from waste carbide slag 2023年9月1日 Lithium (Li)bearing aluminum electrolyte slag is an inevitable byproduct of the aluminum industry, and improper disposal or stacking it may lead to potential environmental hazards This study employed hydrometallurgical processes to selectively leach lithium from Licontaining aluminum electrolyte slag, using sodium carbonate solution as the leaching agent Clean Process for Selective Recovery of Lithium Carbonate from Waste
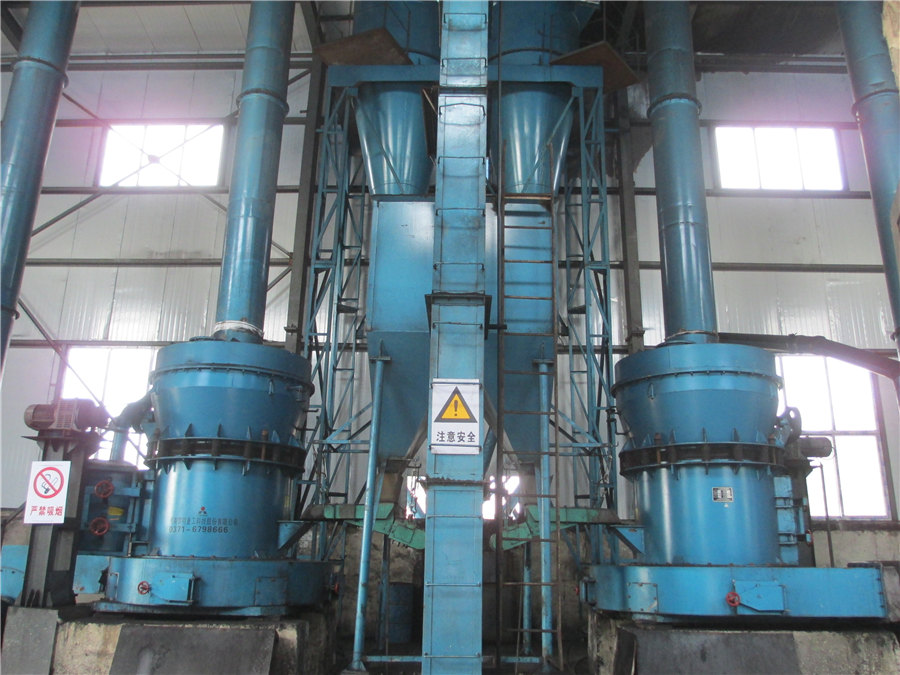
Recovery of carbon and cryolite from spent carbon anode slag of
2022年10月10日 One of the main electrolytic aluminum production costs is the consumption of carbon anodes, and carbon anode slag is a common hazardous waste in the aluminum industry2024年5月26日 Mineral carbonation is one of the known methods for carbon capture, utilization, and storage (CCUS) Slag from the steel industry is studied as a common source of CaCO3 via mineral carbonation owing to its high Ca content Despite numerous preliminary studies, the optimal factors governing the mineral carbonation of steelmaking slag, such as extraction and Experimental study on indirect mineral carbonation using five calcium aluminate hydrate, calcium carbonate and hydroxide Mailar et al [20] tried to replace some sintering raw materials with secondary aluminum dross to make refractoryResearch on the Preparation Parameters and Basic Properties of 2023年10月1日 The main components of waste aluminum cryolite electrolyte are cryolite (Na 3 AlF 6), potassium cryolite (K 2 NaAlF 6), lithium cryolite (Na 2 LiAlF 6), fluorite (CaF 2), and approximately 2% carbon black (Wang et al, 2019)The main treatment methods of waste aluminum cryolite electrolyte can be divided into two categories: combined thermalwet Efficient extraction and recovery of lithium from waste aluminum
.jpg)
Efficient lithium recovery from electrolytic aluminum slag via an
2024年2月1日 The electrolytic aluminum industry generates a large amount lithium (Li)containing electrolytic aluminum slag (EAS) annually, and this can result in severe environmental pollution and wasting of Li resources This paper proposes a method for recovering Li from the slag using AlCl 3 as the leaching agent The effects of the leaching temperature, AlCl 3 2022年2月19日 Recycling waste containing rare earth has always been a research hotspot The molten salt electrolysis process of rareearth metals and alloys generates a large amount of waste slag, which Recovery of RareEarth Elements from Molten Salt Electrolytic Slag 2021年10月6日 Secondary aluminum dross is a byproduct of the electrolytic aluminum industry, whose main components are Al2O3, AlN and Na3AlF6 Secondary aluminum dross is a type of hazardous waste, with a Research on the Preparation Parameters and Basic Properties of 2024年6月29日 Aluminum electrolyte is a necessity for aluminum reduction cells; however, its stock is rising every year due to several factors, resulting in the accumulation of solid waste Currently, it has become a favorable material for the resources of lithium, potassium, and fluoride In this study, the calcification roasting–twostage leaching process was introduced to extract Stepwise extraction of lithium and potassium and recovery of
.jpg)
Study on Harmless and Resources Recovery Treatment Technology of Waste
2012年12月31日 The main mineral components of waste cathode carbon include sodium fluoride, cryolite, calcium fluoride, silicate minerals and so on, therein the fluorine content is about 986%, and the content 2021年11月1日 Sodium carbonate (Na2CO3) has the potential to become an efficient solid activator for preparing onepart alkaliactivated ground granulated blast furnace slag cementsCalcium carbide residue as auxiliary activator for onepart sodium 2020年12月1日 The rapid development of the electrolytic aluminum industry in China and the increasing demand for aluminum products have led to the development of many lowgrade bauxite mines with an average Li 2 O content of at least 058% (Wang et al, 2013) Due to the use of this lowgrade bauxite in the electrolytic aluminum process, the content of lithium in the Novel process for the extraction of lithium carbonate from spent 2024年6月1日 Calcinating the slag with calcium oxide and aluminum sulfate at 1173 K achieved fluorine fixation to form rare earth oxides by 69, 70 recovery of waste sulfur slag, 71, 72 recovery of aluminum electrolytic waste residue, 73 Rare earth recovery from fluoride moltensalt electrolytic slag by sodium carbonate roasting REEs recovery from molten salt electrolytic slag: Challenges and
.jpg)
(PDF) Synthesis and Performance Evaluation of Nano
2023年12月13日 Synthesis and Performance Evaluation of NanoCalcium CarbonateModified Geopolymers Incorporating Fly Ash and Manganese Slag: A Comprehensive Investigative Study December 2023 Processes 11(12):年6月9日 The production of precipitated calcium carbonate (PCC) from steel slag has been proposed as a potential method of simultaneously reducing the CO2 emissions from the steelmaking process and turning Production of papermaking grade calcium carbonate 2017年10月24日 Aluminum production is accompanied by production of fluorinecontaining solid waste Every year in the Bratsk Aluminum Plant 40000 tons of this waste is produced with a high fluorine and carbon content Technology for producing calcium fluoride is developed in order to regenerate fluorine Optimum conditions are studied and determined for leaching fluorine from Technology for Preparing Calcium Fluoride from Aluminum Production WasteAluminum ash is a large amount of industrial solid waste produced by the electrolytic aluminum industry, and calcium carbide slag is an alkaline industrial solid waste produced by the energy industry Both of them will cause serious pollution risks to the environment Its harmless and resourcebased treatment has become one of the main research prehensive performance study of aluminum ash and calcium
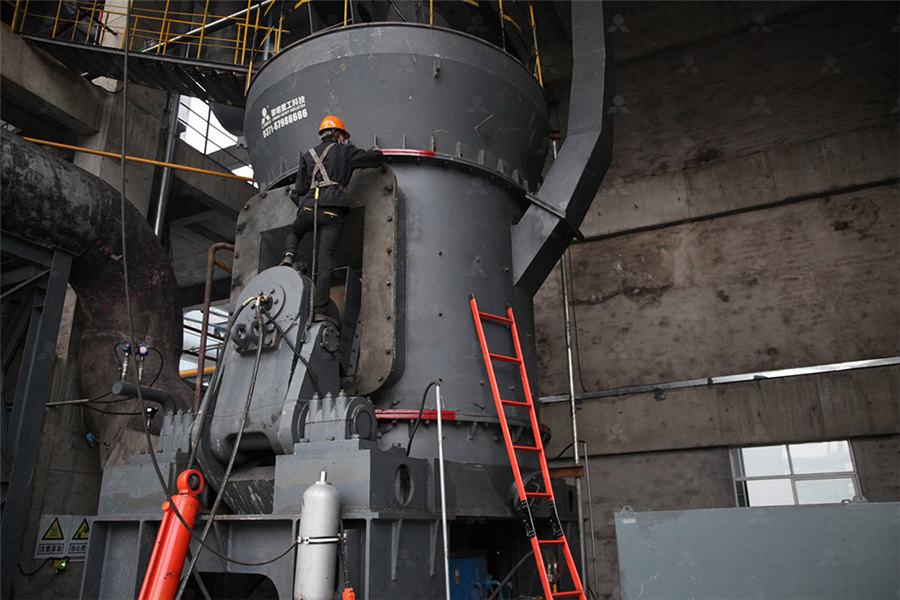
Kinetic and thermodynamic analysis on preparation of belitecalcium
2023年8月10日 Kinetic and thermodynamic analysis on preparation of belitecalcium sulphoaluminate cement using electrolytic manganese residue and barium slag by TGADOI: 101016/jjclepro2024 Corpus ID: ; Efficient lithium recovery from electrolytic aluminum slag via an environmentally friendly process: Leaching behavior and mechanismEfficient lithium recovery from electrolytic aluminum slag via an 2017年2月21日 Twoway Valorization of Blast Furnace Slag: Synthesis of Precipitated Calcium Carbonate and Zeolitic Heavy Metal Adsorbent(PDF) Twoway Valorization of Blast Furnace Slag: Synthesis of Recovery of carbon and cryolite from spent carbon anode slag of electrolytic aluminum by flotation based on the evaluation of selectivity index Yemin Wang1, Xuexia Wang1* and Muhammad Bilal2 Recovery of carbon and cryolite from spent carbon anode slag of
.jpg)
How to extract lithium from electrolytic aluminum waste residue?
Both methods have their own advantages and disadvantages, and the specific choice depends on the composition and characteristics of the waste residue Both acid leaching and alkali leaching methods require pretreatment of electrolytic aluminum waste by grinding Firstly, dry the waste residue to reduce its moisture content to below 5%Request PDF On Dec 1, 2013, Arshe Said and others published Production of precipitated calcium carbonate (PCC) from steelmaking slag for fixation of CO2 Find, read and cite all the research Production of precipitated calcium carbonate (PCC) from steelmaking 2008年9月1日 As discussed in Chapters 8 to 14 and of this tome, since industrial residues, such as, fly ash (Chapter 8), slags (Chapter 9), carbide lime (Chapter 10), cementbased construction waste (Chapter Fixation of CO2 by carbonating calcium derived from blast furnace slag 2007年7月24日 Calcium carbonate is used in large amounts in the pulp and paper industry as a paper filler When it is manufactured, the calcium carbonate waste is purged from the process Here we demonstrate that, due to the elevated calcium concentration of 1685 g kg−1 dry weight (dw), alkaline pH of 126 and neutralizing (liming) effect value of 424% expressed as Ca Calcium carbonate waste from an integrated pulp and paper mill
.jpg)
Rare earth recovery from fluoride moltensalt electrolytic slag by
2023年8月1日 When the mass ratio of sodium carbonate to fluorinated rare earth moltensalt electrolytic slag was increased from 02 to 06, the recovery of rare earth improved from 801% to 979% and there was almost no change in the leaching efficiency of rare earth when the mass ratio of sodium carbonate to the fluorinated rare earth moltensalt electrolytic slag continued to 2024年2月1日 Overhaul slag, as one of the main hazardous solid wastes generated in the electrolytic aluminum, has high research value [12]The electrolytic cell lining is eroded by continuous chemical corrosion of hightemperature molten metal and salt, resulting in expansion and peeling off, leading to low production efficiency and degradation of performance [13]A novel approach for extracting lithium from overhaul slag by low The aluminum electrolyte waste used in this work was sourced from an electrolytic aluminum plant in Sichuan, China The quantitative analysis and characterization were carried out for the aluminum electrolyte sample before the experiments The result of XRD (see Fig 1a) indicates that the aluminum electrolyte consisted mainly of cryolite Na(3 Stepwise extraction of lithium and potassium and recovery of 2013年12月1日 Calcination of the limestone is energy intensive as it requires high temperatures (∼1000 °C) the objective of this study is to evaluate the feasibility of production of precipitated calcium carbonate from steel converter slag Calcium was extracted selectively from the slag with an aqueous solution of ammonium salt (NH 4 NO 3, CH 3 COONH 4 Production of precipitated calcium carbonate (PCC) from steelmaking
.jpg)
Clean Process for Selective Recovery of Lithium Carbonate from Waste
This study employed hydrometallurgical processes to selectively leach lithium from Licontaining aluminum electrolyte slag, using sodium carbonate solution as the leaching agent A notable leaching efficiency of 9912% is yielded for lithium, with minimal leaching observed for other elements such as calcium (Ca) and aluminum (Al)2023年12月1日 Tong et al (2023) mixed aluminum sulfate and calcium oxide to treat the rare earth molten salt electrolytic slag and achieved the expected effect, indicating that the reaction with fluoride in rare earth molten salt electrolytic slag after mixed roasting is feasible, which is consistent with the thermodynamic calculation results of the reaction of coroasting aluminum Review of efficient recycling and resource utilization for rare earth 2023年12月1日 Based on these considerations, the idea of using vegetable waste through natural fermentation to produce organic acids as a substitute for traditional industrial acids, and using them to soak and treat blast furnace slag, is proposed by our team, while the generated WCS would be employed as the Ca source for the synthesis of valueadded amorphous Producing amorphous calcium carbonate using waste Carich