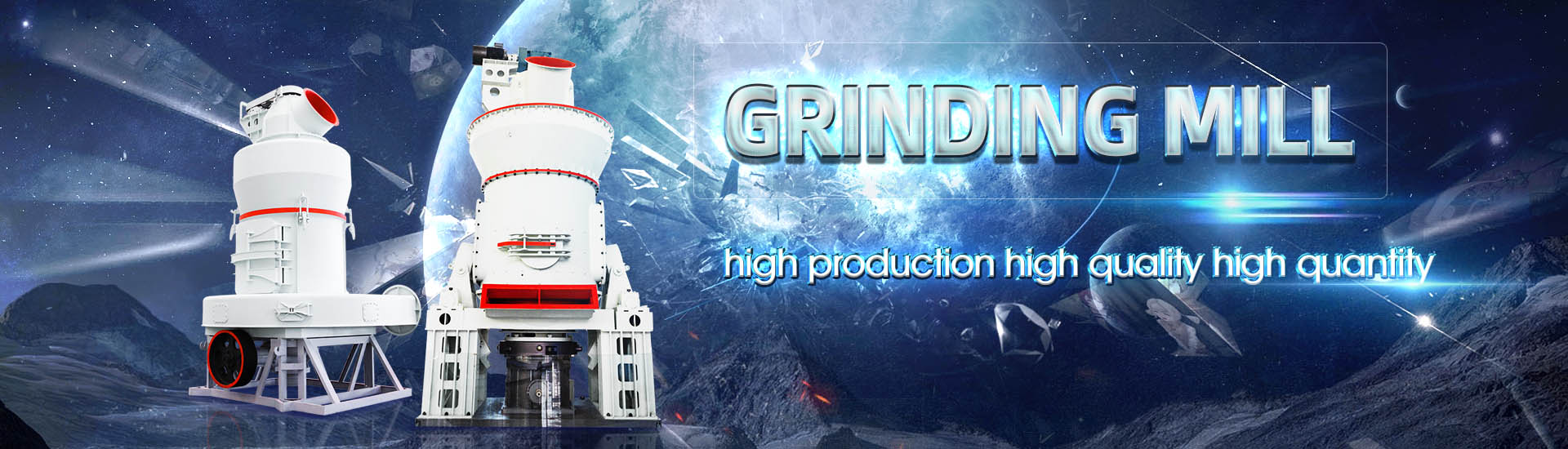
Director of Alkaline Furnace Lining Material Pulverizing Technology Mine in Shandong Province

Shandong Province Metallurgical Engineering Co, Ltd Shandong
At 00:32 on March 20, 2023, hot commissioning for the coal pulverizing system (medium speed mill with load) of the 1 # 1880m3 blast furnace PCI transformation project of Ironmaking Plant The Top Submerged Lance – TSL technology was invented in the early 1970s and permanently developed by Ausmelt to process a range of nonferrous, ferrous and waste materials Feed Lining Concepts for the Nonferrous Metal Industry RHI Magnesita2020年3月1日 In an attempt to generate a systematic approach to select FL ceramic materials, an evolutionary screening procedure (ESP) is proposed in this paper, where a multiobjective Materials selection of furnace linings with multicomponent 2021年5月15日 The study investigated the stabilization of gold mine tailings (GMTs) by applying an alkaline activation process and studying NaOH and KOH as activators in the presence of Alkaline Activation of Basic Oxygen Furnace Slag Modified Gold
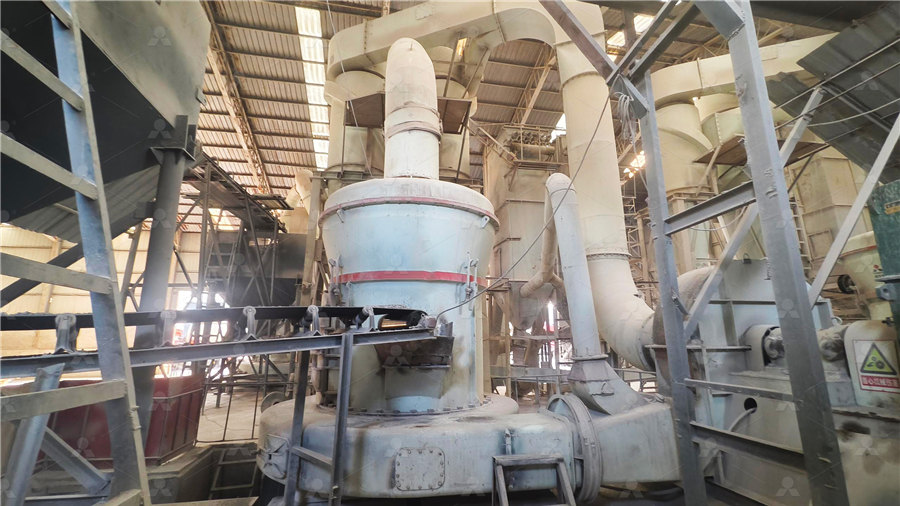
Innovative Refractory Technology for Coreless Induction Furnaces
This paper will discuss a completely new generation of refractories and address care of structural components, installation, sintering and optimal operation of coreless induction furnaces to 2017年3月14日 To do it right, here are five primary tips for maximum furnace lining efficiency: 1 Use IR thermography to inspect the existing lining — Ensuring lining quality is critical to Ensuring Furnace Lining Efficiency Foundry ManagementTokai COBEX is the leading carbon and graphite lining supplier for blast furnaces In the beginning of the 60’s, the refractory lining of the lower part up to the middle stack of blast Furnace Linings Tokai COBEX Group2019年8月13日 This paper investigates the effects of activator concentration, curing temperature and time on alkaliactivated materials based on lowalumina MTs from the Cu/Ni mine in Effects of Activator Properties and Curing Conditions on Alkali
.jpg)
Furnacing lining materials ELMON™ Elkem
Furnace lining materials are used to line and protect the hearth and side walls on the inside of submerged arc furnaces from damage during the smelting of ferroalloys Since the 1980s, 2020年2月20日 For this purpose, the paper presents a systematic review of tailings paste applications in mines for cleaner production First, the basic concepts and characteristics of A systematic review of paste technology in metal mines for cleaner 2004年1月1日 Since 1995, when "freeze lining" refractory systems were introduced to the ferroalloy industry, they have gained in popularity, due to the freeze lining?s reputation for reliability, safety, and the contribution it makes to profitability As with many popular and effective technologies, however, the freeze lining has spawned lowcost pretenders that claim the OneMine The Truths And Myths Of Freeze Lining Technology 2014年8月15日 Different types of BF refractories Different types of refractories which are used in blast furnace lining are described below Baked carbon blocks – Micro porous carbon block, semi graphitic carbon block, and micro porous Refractory lining of blast furnace – IspatGuru
.jpg)
Alkaline carbonates in blast furnace process ResearchGate
2014年10月1日 Alkalis (K and Na compounds, Kobayashi et al, 1979) enter in the blast furnace with the charge materials (should be limited to 2530 kg alkalis/ton pig iron, Kurunov et al, 2009 or 2585 kg Blast Furnace is the focus of any integrated steel plant Blast furnace is used to reduce the iron ore to iron The charge, which consists of iron ore, coke and limestone etc in the form of lumps and different ratios, is fed from the top Air heated in the blast furnace stoves, is applied from the bottom of the furnace TheBLAST FURNACE (BF) REFRACTORY LINING PATTERN IDCOnline2009年9月1日 The unwanted elements of the blastfurnace raw materials cause many technical problems in the sintering process as well as inthe blastfurnace ironmaking 1 It is widely known that alkali metals Analysis of the behavior of alkalis in a blast furnace2019年7月2日 Iron and steel making is one of the most intense energy consuming in the industrial sectors The intensive utilization of fossil carbon in the ironmaking blast furnace (BF) is related directly to Modern blast furnace ironmaking technology: potentials to
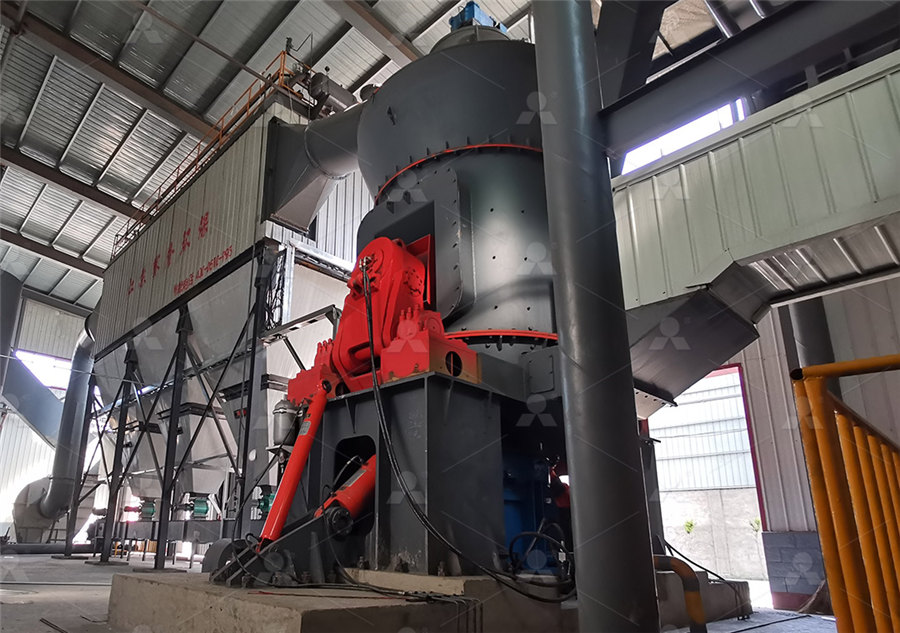
Mineral sequestration of CO2 using saprolite mine tailings in the
2018年7月1日 This study investigate the feasibility of sequestering CO 2 via mineral carbonation of calciumrich alkaline industrial wastes, such as steel slag (SS) and coal fly ash (FA) in acidic mine tailings Mine tailings are treated with SS and FA at various liquidtosolid ratios (15 and 30 ml/g) to extract metal components present in FA and SS to supplement the Ca 2+ and Mg 2+ Accepted Manuscript Mineral sequestration of CO2 using saprolite mine tailings in the presence of alkaline industrial wastes Amirali Ebrahimi, Morteza Saffari, Young Hong, Dia Milani, Alejandro Montoya, Marjorie Valix, Andrew Minett, Ali Abbas PII: S09596526(18)31059X DOI: 101016/jjclepro201804046 Reference: JCLP 12627 To appear in: Journal of Cleaner Mineral sequestration of CO 2 using saprolite mine tailings in the 2021年4月30日 111 Properties and Main Uses of Magnesium Metal Human beings discovered magnesium compounds as early as the seventeenth century Antoine Lavosier, a French scientist, theoretically inferred that an ore with unknown composition (ore containing alumina and magnesium oxide) contained a new metal element, but the magnesium could not be extracted Overview of Magnesium Metallurgy SpringerLink2021年8月9日 In the present paper, two types of magnesiabased refractory bricks for the wear lining of a steel ladle furnace are considered, with the aim of comparing their ecological performances The adopted methodology is the Life Cycle Assessment (LCA) approach from cradletogate of the two brick product systems, in accordance with the European and Possible ecological advantages from use of carbonless magnesia
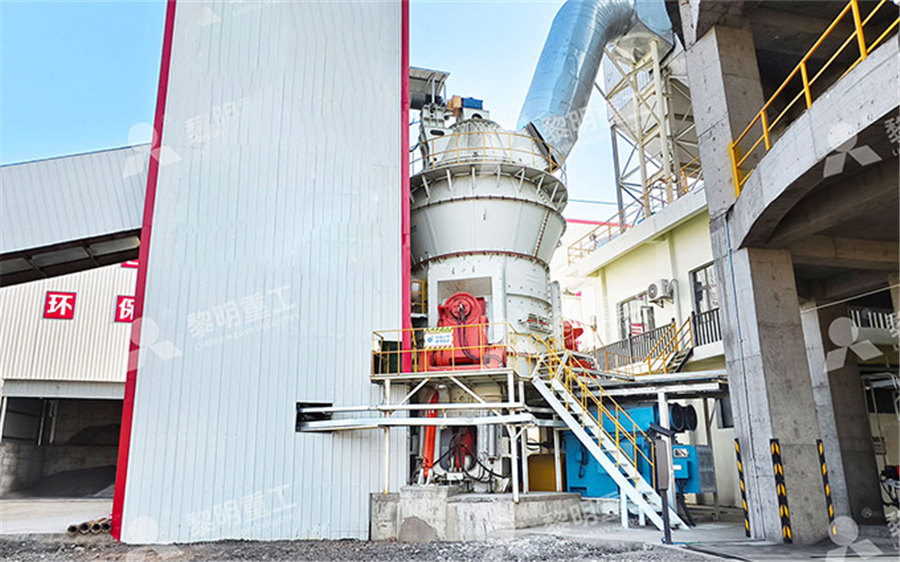
Understanding technology in mining and its effect on the work
2021年8月5日 This paper takes its starting point in the fact that many mines have managed to improve its work environment, with regards to, for example, accident occurrence, while at the same time having stopped seeing improvements in these areas even in the wake of technology interventions Technology projects in the mining industry continue to make claims on further 2005年11月30日 For graphite refractory, this dissolution is generally assumed to be mass transfer controlled [6,7] , ie, limited by the rate of [C] transport through the diffusion boundary layerWear mechanism for blast furnace hearth refractory lining2012年12月1日 The results showed that an alkaline environment was responsible for producing alkaline mine drainage due to the presence of limestone; this caused high pH (841) in the area’s groundwater resourcesThe impacts of alkaline mine drainage on Ba, Cr, Ni, 2024年3月4日 Blast furnace dust (BFD) is the solid powder and particulate matter produced by dust removal process in ironmaking industry The element composition of BFD is complex, and a direct return to sintering will lead to heavy metal enrichment and blast furnace lining corrosion In recent years, the application of BFD in wastewater treatment has attracted widespread Review in application of blast furnace dust in wastewater
.jpg)
Development and Status of the Treatment Technology for Acid Mine
2020年9月4日 Acid mine drainage (AMD) is difficult to treat due to its physicochemical characteristics, such as high pH and high heavy metal concentrations, so it causes great harm to the environment and human health If acid mine drainage is discharged arbitrarily without treatment, it will lead to a series of environmental problems and cause longterm 2023年7月5日 Coreless induction furnace is one of the most widely used equipment in the steelmaking sector, while the lining refractory are the key factors in determining the lifetime of the induction furnace The multiphysics field dominates the operating conditions of the lining refractory which can be wellstudied using numerical simulation techniques Based on the Effects of induction furnace conditions on lining refractory via of { A methodology for determining the erosion profile of the freeze lining Furnace lining repair material can be pumped in from the outside to fill a hot spot and cool a particular area An efficient furnace lining is essential for reducing overall maintenance costs and ensuring that facilities run smoothly, without unwarranted revenue loss due to downtime Follow these tips to keep your furnace running efficiently Achieving Furnace Lining Efficiency Foundry Management Technology
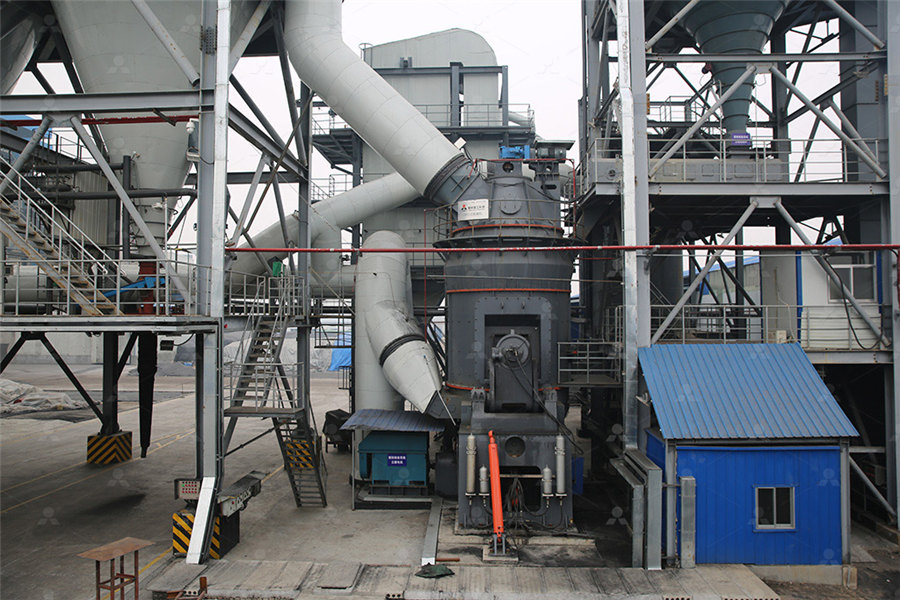
(PDF) Detection of Blast Furnace Hearth Lining Erosion by Multi
2021年7月26日 The blast furnace hearth refractories are exposed to complex chemical attack and thermal stress erosion, which will lead to the gradual failure of refractories2020年4月15日 Assuring that the furnace lining remains within the manufacturer specified limits requires careful usage of the lining during operation as well as inspection and monitoring procedures(PDF) Causes of the Quartzite Lining Destruction during Operation 2007年5月1日 The difference in dissolution behavior of MK in NaOH and KOH solutions was further investigated showing that the extent of dissolution is higher in NaOH rather than in KOH solutions with the same Dissolution of Aluminosilicate Minerals and byProducts in Alkaline 2016年5月15日 Overall the GM3 material had the worst wear behavior of the three 2) The hardest lining (GM30) exhibited mainly abrasive and fatigue wear, and its friction level seemed to reach a maximum at the intermediate speed within the applied range of 5–15 mm/s Further work over an extended range of sliding speeds should be useful 3)Comparison of the thermophysical properties, microstructures, and
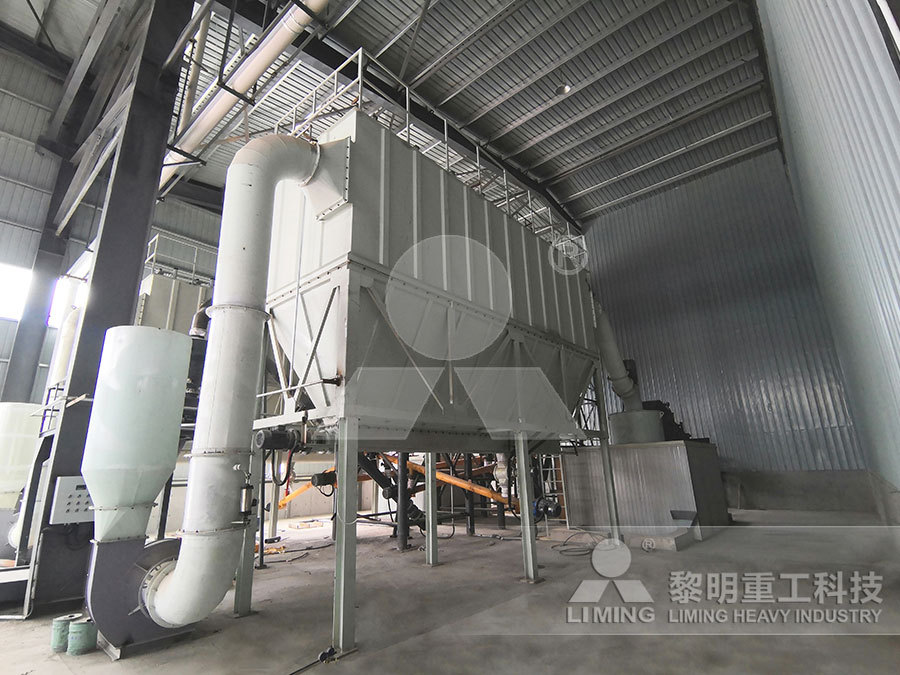
The geochemical characteristics and geological significance of alkaline
2013年12月1日 Alkaline complex in Chishan is closely related to the origin of rare earth elements REE deposits A systematic study on geochemical characteristics of the complex was conducted to reveal its 2011年12月1日 The suitability of some local clay deposits in Ekiti State, for lining the furnace to be used to degrade woody biomass to fuel and chemical products was investigated Four major sites in Ekiti State renowned for abundant clay deposits were selected, namely; Ikere Ekiti, Fagbohun Ekiti, Ishan Ekiti and Ara Ekiti The clay samples were crushed, milled (pulverised) Selection of appropriate clay for furnace lining in a pyrolysis 2023年7月11日 Results of studies on extending the time operation of gin and linter grates by hardening of the working area by highfrequency current are given in article(PDF) Investigation of heat exchange processes in the lining of 2017年5月30日 The final point to consider when lining a furnace is to ensure that the installation is completed correctly by a skilled professional for the task There are a number of products available for furnace lining, and all come with their own installation requirements Getting this wrong will cause inefficient lining as well as waste a lot of moneyEnsuring Effective Furnace Lining Efficiency Thermal Processing
.jpg)
Recovered soda residue as alkaline activator of furnace slag
2022年12月24日 Abstract The accumulation of soda residue (SR) poses a consequential threat to the environment because of the absence of effective methods for treating them on a large scale SR is composed of NaCl, CaSO405H2O, and Ca(OH)2 in addition to CaCO3, which can be potentially used to replace reagentgrade alkaline activators for activating furnace slag 2015年9月1日 In view of the everincreasing energy needs in the process industry, efficiency enhancements assume critical importance Refractory linings play a pivotal role in reducing the energy consumption of the process equipment along with ensuring safe and reliable operation of a plant Owing to the project complexities and installation schedules, refractorylined Investigation of Alkaline Hydrolysis in Refractory Linings of downtime Follow the five tips below to keep your furnace lining running efficiently Tip 1 – Evaluate the furnace liner by using infrared (IR) thermography inspection Infrared (IR) thermography scans are an essential step for evaluating the quality of the furnace lining Lining quality is critical to protecting the steelFive Tips for Achieving Furnace Lining Efficiency2020年9月9日 In an attempt to increase sustainability of construction materials, both ground granulated blastfurnace slag (GGBS) and, less popular, copper slag (CS) can be used in alkaliactivated compositesGeosynthesis of building and construction materials through alkaline
.jpg)
BLAST FURNACE TECHNOLOGY Paul Wurth
blast furnace technology 5 TECHNOLOG LEADERSHIP IN IRONMAKING – AVAILABLE HERE! blast furnace construction Modernisation 06 07 stockhouse charging systems 08 09 blast furnace top charging technology – the original 10 11 blast furnace Design: the blast furnace Proper, lining cooling 12 13 hot blast generation supply 14 年5月15日 Zinccoated scrap may affect induction furnace refractory lining negatively, Content Director Robert Brooks has been a businesstobusiness reporter, writer, including process technology, resource development, Understanding Zinc Penetration on Induction 2020年1月21日 The use of manganesecontaining materials as part of the blastfurnace charge in case of the BF3 furnace (EMZ) resulted in a decrease of lining temperature on the lower furnace levels (bottom levels of furnace stack, belly and bosh) on average by 100 °C, while stabilizing the temperature distribution along the circumference (Fig 3), which provided a Experience of Using ManganeseContaining Materials in BlastFurnace 2017年7月1日 A practice of cemented backfill technology with ultrafine tailings in a gold mine was comprehensively presented, and a series of tests were conducted in accordance with the peculiar properties of A practice of ultrafine tailings disposal as filling material in a
.jpg)
(PDF) Furnace lining analysis and design by mathematical and
2006年8月27日 Detail of the tuyere zone of a Pierce Smith converter where the FEM grid and the surface of the NWM nodes are shown The red dots represent the nodes of the NWM surface [11] 2021年12月1日 Copper is considered as an enabler to a greener future and, therefore, the environmental impact of its production is of high interest The world copper mine production was about 20 million tonnes in 2018 and the average growth rate has been 2% (ICSG, 2019)However, the mass adaptation of electric vehicles (EV) will create additional demand for copper (Nguyen Comparison of environmental performance of modern copper Download scientific diagram A lining characteristic of an electricarc furnace in ferromanganese production Initial corrosion profi les are for a monolithic magnesite sole from publication A lining characteristic of an electricarc furnace in 2014年11月1日 During the furnace campaign, the refractory lining suffers mechanical and chemical stress such as: oxidation, corrosion by alkalis, disintegration by CO, erosion and dissolution by intense flux of Monitoring the wear of the refractory lining in the blastfurnace
.jpg)
Design, fabrication and properties of lightweight wear lining
2022年3月1日 As shown in Fig 1, a conventional refractory lining structure has a wear lining, safety layer, and an insulation layer The wear lining resists erosion, wear, corrosion and thermomechanical loads of molten melts, while the insulation layer reduces the thermal transfer through refractory lining2020年8月15日 The mining industry produces billions of tons of mine tailings annually However, because of their lack of economic value, most of the tailings are discarded near the mining sites, typically under water The primary environmental concerns of mine tailings are related to their heavy metal and sulfidic mineral content Oxidation of sulfidic minerals can produce acid mine Mine tailings as a raw material in alkali activation: A review