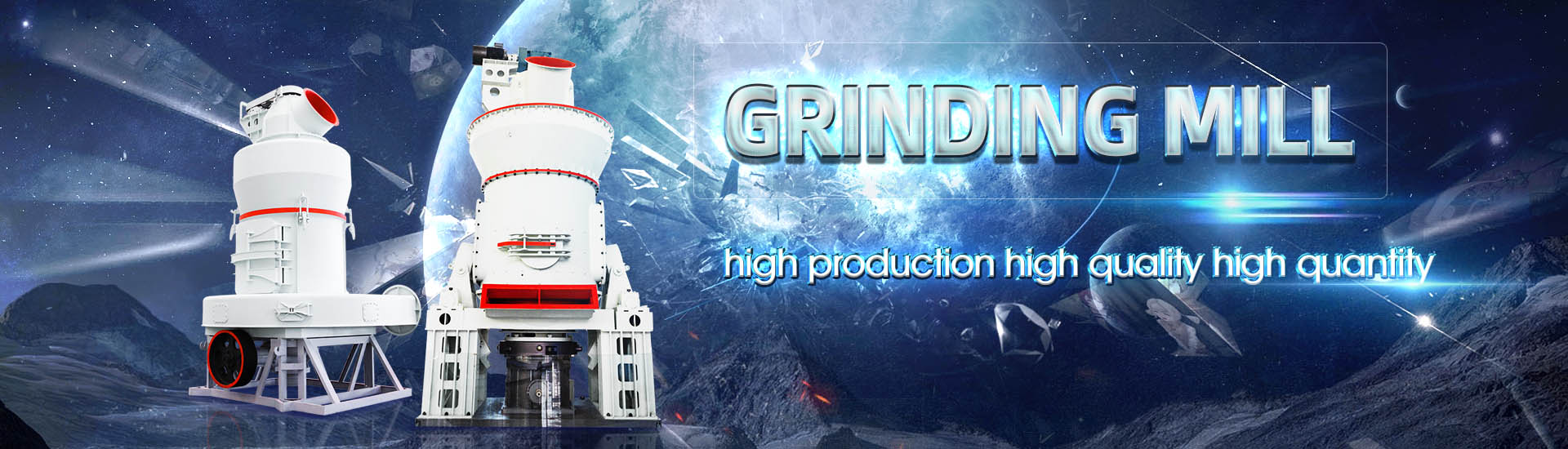
1316 ore mill production process
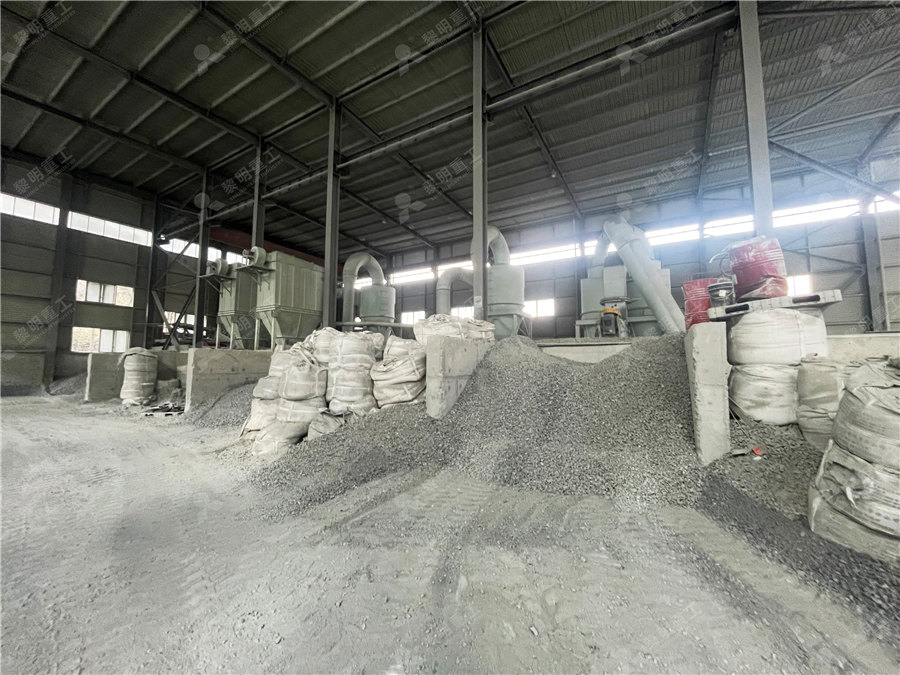
From Ore to Iron with Smelting and Direct Iron Reduction
2017年10月17日 Ironmaking is a critical step in producing high performance steel because highquality raw materials reduce the time and energy to purify the iron to steel On the other hand, 2024年4月26日 Iron ore processing is a complex and vital process that transforms raw iron ore into usable steel From exploration and extraction to grinding, beneficiation, and ironmaking, Iron Ore Processing: From Extraction to Manufacturing2024年5月13日 The Steel Manufacturing Process The steel production process is a multifaceted journey that begins with extracting and processing iron ore, a primary raw material Steel Manufacturing: Process, Types, and Standards Thomasnet2024年3月20日 The steel making process involves several key stages: preparation of raw materials such as iron ore, coke, and limestone; smelting and reduction to produce molten Understanding the Steel Making Process: A Flow Diagram
.jpg)
Production Process and Products JFE Steel Corporation
HighQuality Products and a Dynamic Steel Production Line Powered by the World's Best Technology The blast furnace turns the iron ore into pig iron, the chief ingredient used to 2023年7月20日 Moist grinding, a special grinding method, is used to prepare pellets for smelting According to the grinding medium features, ore grinding is mainly classified into ball grinding Ore Grinding SpringerLink2019年12月27日 Presentation will help to provide basic principle and brief overview of iron making to steel making process which is cover each and every stage of iron and steel making (PDF) ironsteel making From start to finish ResearchGateSteel is primarily produced using one of two methods: Blast Furnace or Electric Arc Furnace The blast furnace is the first step in producing steel from iron oxides The first blast furnaces Steel Production American Iron and Steel Institute
.jpg)
Iron Ore Processing, General SpringerLink
2022年10月20日 Making iron and steel from iron ore requires a long process of mining, crushing, separating, concentrating, mixing, agglomeration (sintering and pelletizing), and 2012年6月1日 rotation, the mill loading, the final product size required from a given feed size The most important disturbances to the process are ore hardness changes and feed size variationsGrinding in Ball Mills: Modeling and Process ControlThe chromite ore, mill scale, and petroleum coke were dried in an oven at around 473K for 24h Then the materials were ground by a ball mill into various particle sizes (chromite ore: D 80¼147mm Direct Alloying Steel with Chromium by Briquettes Made from 2014年1月1日 In particular, ball milling is one of the important unit operations in the iron ore pelletizing process The mill product, due to its physical properties, determines the efficiency of subsequent Population balance model approach to ball mill
.jpg)
Understanding the SAG Mill in Copper Ore Mining Process
The rod mill is another type of grinding mill used in the copper ore mining process This machine uses steel rods as the grinding media instead of balls, which are commonly used in ball mills The rods grind the ore by tumbling within the mill, similar to the action of a rotating drumPDF On Jan 1, 2011, W M Jansen and others published Tracerbased minemill ore tracking via process hold ups at Northparkes mine Find, read and cite all the research you need on ResearchGate(PDF) Tracerbased minemill ore tracking via process3 BALL MILL MODEL The population balance model may be expressed by Equation (1): > @ ¦ i1 1 i b ij m j j i j i S Ht dt d H m t (1) where: S i (t) is the size discretized selection function for Population balance model approach to ball mill optimization in iron ore 2019年9月3日 process of Indonesian limonite ore in electric arc furnace In Proceedings of the 2nd Mineral Processing and T echnology International Conference, Serpong, Indonesia, 1–2 November 2018; IOP (PDF) Nickel Laterite Smelting Processes and Some ResearchGate
.jpg)
Cement Production Demystified: StepbyStep Process and
The use of a ball mill is common in the cement production process, as it is efficient, costeffective, and able to produce a consistent product size 23 Pyroprocessing in a kiln for clinker production The production of clinker in a kiln is a key process in the production of cementFind your ore mill easily amongst the 42 products from the Research Institutions and Industries requiring size reduction on a semiproduction scale The Mill Compare this product capacities range from a min of 15 l to a max of 15 l Suitable for carrying out grinding tests or simple wet process mixing tests on ceramic glazes and Ore mill, Ore grinding mill All industrial manufacturersReengineering of the ore preparation production process in the context of “Almalyk MMC” JSC Margarita Naumova1, Ilnur Basyrov1,*, and Khakim Аliev1 1National University of Science and Technology “MISiS”, Leninskiy prospekt, 4, Moscow, , Russia Abstract The review of ore crushing and grinding processes at theReengineering of the ore preparation production process in the MinetoMill Optimization of Aggregate Production Final Report Reporting Period: 6/5/04 – 9/30/06 Submitted by: Greg Adel1 information, apparatus, product, or process disclosed, or represents that its use would not infringe privately owned rights Example of Pittsboro ore variability; test shot face and C2 sample 46MinetoMill Optimization of Aggregate Production
.jpg)
(PDF) ironsteel making From start to finish
PDF On Dec 27, 2019, Mr Bhavesh R Rana published ironsteel making From start to finish Find, read and cite all the research you need on ResearchGate2023年4月5日 The blast furnace and direct reduction processes have been the major iron production routes for various iron ores (ie goethite, hematite, magnetite, maghemite, siderite, etc) in the past few decades, but the Recent Trends in the Technologies of the Direct 2019年9月24日 There are numerous examples in the literature, some of which are quantifying the effect of Mine to Mill Grundstrom et al, 2001;Hart et al, 2001;Scott et al, 2002;Burger et al, 2006;Jankovic et al Simulating the Impact of Ore Competence Variability on Process The Bessemer Process for Steel production and; The Open Hearth Process of Steelmaking; Steel manufacturing Principle of the Bessemer Process The main raw materials for Steel production in a blast furnace are Iron ore, limestone, coke, and some scrap steel These materials are charged into the blast furnace from the top and converted into How is Steel Made? Steel Production Process – What Is Piping
.jpg)
How Ball Mill Ore Feed Size Affects Tonnage Capacity
2017年7月26日 We will consider an ore with a ball mill work index varying between 16 and 13, The production of coarser sizes will no less efficient, should this be the desired product for a process such as crushed stone production, if power rates greater than that required to maximize that coarse size are appliedoperating data on a technological process and formation of control which is optimal for current characteristics of processed ore materials [12 – 15] indicate that in concentration production conditions, ultrasonic means of nondestructive control can be applied to measuring characteristics of ore materials in technological flowsAdaptive control of ore mill charge2016年10月31日 In this work, the effectiveness of using briquettes made from chromite ore, mill scale, and petroleum coke for direct chromium alloying is tested by induction furnace trials carried out in three (PDF) Direct Alloying Steel with Chromium by Briquettes Made In 2030, we will switch to a production method that is better for the environment and the people living here: ore and hydrogen That requires us to renovate some of the plants on our site Until we have done that, we will continue using our Blast FurnacesProcess of steelmaking Tata Steel
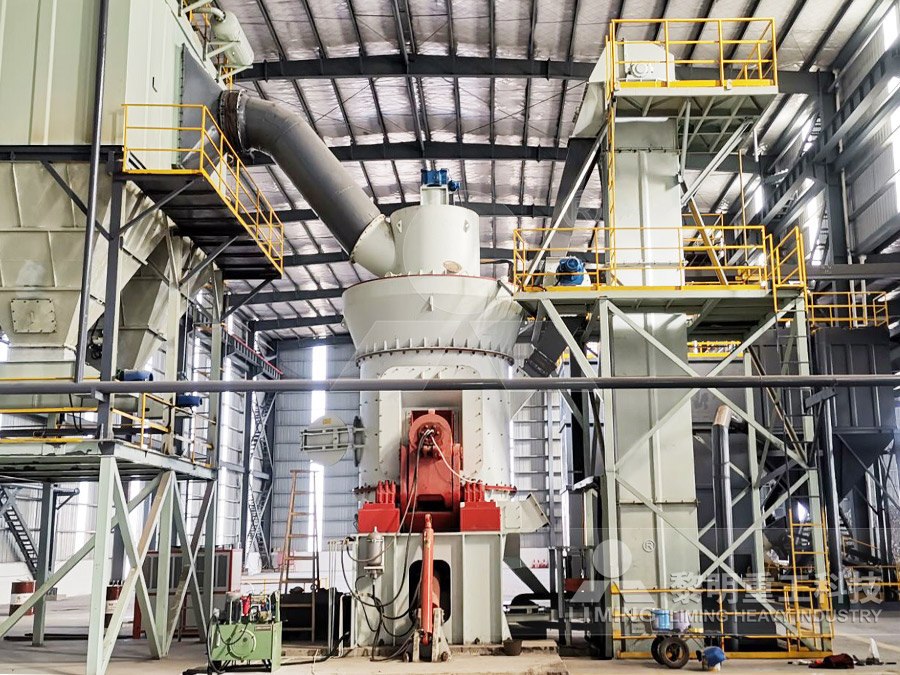
Gold process mineralogy: Objectives, techniques, and applications
2004年4月17日 Gold process mineralogy addresses all issues related to gold ore processing by the detailed study of an ore or a mill product2017年2月16日 The methods employed in dressing the tin ore up to the required percentage of purity depend mainly on the type of ore crushed These may be briefly divided 911 Metallurgist is a trusted resource for practical insights, solutions, and support in mineral processing engineering, helping industry professionals succeed with proven expertise Tin Ore ProcessingTin Ore Processing 911Metallurgist2011年1月1日 Infect only a few investigators worked on the kinetics of mill scale reduction [24][25][26][27][28][29][30]In previous studies on the use of the catalyst for iron ore or mill scale reduction (PDF) Recycling of mill scale in sintering process 2020年4月1日 The aim of this study was to optimize the recovery of chromite from the chrome plant tailings of the South African Middle Group chromite seams using a Wilfley shaking tableProcess optimization of a chrome ore gravity
.jpg)
The perspective of hydrogen direct reduction of iron
2023年12月1日 This process releases a significant amount of carbon dioxide into the atmosphere, contributing to greenhouse gas (GHG) emissions and climate change The reactions of the blast furnace include the combustion of coal or coke, production of carbon monoxide, reduction of the iron ore, and formation of slag (Treptow and Jean, 1998)2024年5月13日 Steel production techniques span a broad spectrum of methods tailored to meet diverse production needs and accommodate varying resource availability Integrated steelmaking, a comprehensive process that melds raw materials like iron ore, coal, and limestone in a blast furnace, is a primary approach for largescale steel productionSteel Manufacturing: Process, Types, and Standards Thomasnet2015年8月26日 The smelter is basically a large furnace which melts the concentrate and drives off the sulfide to leave molten copper metal this is still contains impurities and it needs to be refined further to make it a salable product Returning to the overall process; that is the process for the sulfide ores and the oxide ore as I said are treated Copper Mining Extraction Process Flow Chart2018年8月17日 The concept of ore blending is a very relevant notion in modern high tonnage production mines It is not only essential for the prolongation of the mine life of the concerned mine but as well as a The effects of ore blending on comminution behaviour and product
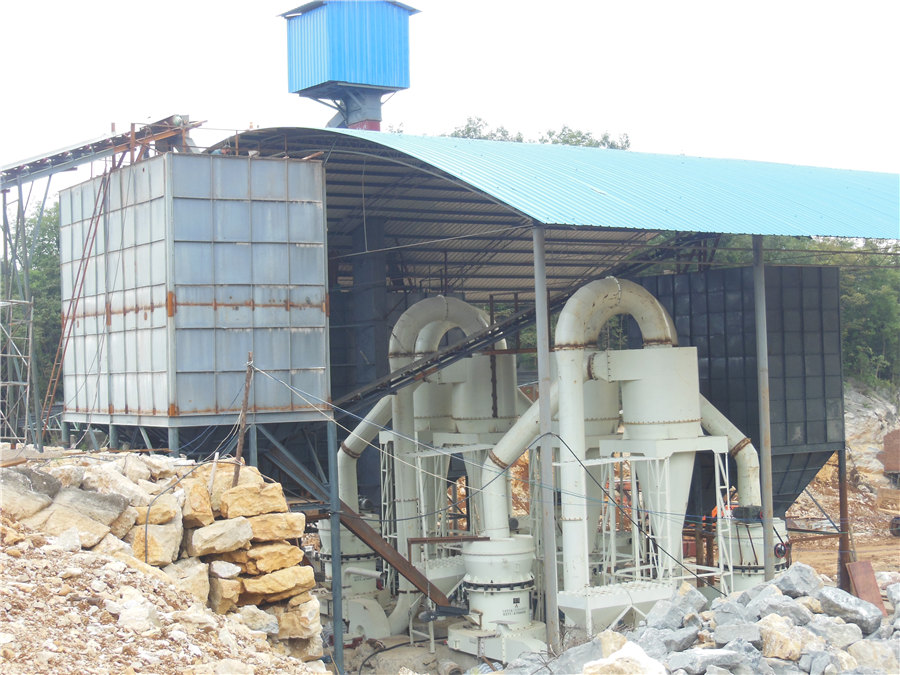
Control of ball mill operation depending on ball load and ore
the ore and the volume of the ready product The granularity of the ore is continuously reduced due to energy transfer by the grinding condition, which reduces their bond strength Ore size reduction is the result of the following three main fragmentation mechanisms 1 Abrasion 2 Cleavage 3 Fracture Figure 1 Grinding of ores inside a ball mill2013年4月1日 A simple and novel nonlinear model of a runofmine ore grinding mill circuit, developed for process control and estimation purposes, is validatedAnalysis and validation of a runofmine ore grinding mill circuit 2023年11月10日 All content in this area was uploaded by Hassan Z Harraz on Nov 10, 2023DIRECT REDUCED IRON ORE: Production ResearchGate2016年3月21日 Concentration and Recovery Formulas These are used to compute the production of concentrate in a mill or in a particular circuit The formulas are based on assays of samples, and the results of the calculations Common Basic Formulas for Mineral Processing
.jpg)
Design SAG mill production when you need it most: In day 1 and
Representative sample: The only ore blend a SAG mill will never see Critical size: Ore component that is harder than the mill has power to grind at the specified rate When a SAG mill is too small, pebble crushing allows the critical size to be eliminated and throughput is increased Conversely, critical size pebbles occur when hard orePDF On Jul 11, 2018, Sandra Lúcia de Moraes and others published Iron Ore Pelletizing Process: An Overview Find, read and cite all the research you need on ResearchGateIron Ore Pelletizing Process: An Overview2023年11月5日 Mining 101: The mill (from ore to finished product) Last updated: 09:30 05 Nov 2023 EST, First published: 09:24 05 Nov 2023 EST The purpose of the mill is to separate and concentrate the valuable substances from the ore, a process known as 'beneficiation' First stepsMining 101: The mill (from ore to finished product)How Continuous Attritors Work The continuous Attritor is a compact vertical design suitable for continuous production of large quantities of materials Advantages of using a continuous Attritor include continuous large production, fastest grinding and processing, excellent temperature control, simple and safe operation, and low power consumptionWet Continuous Production Mills Union Process
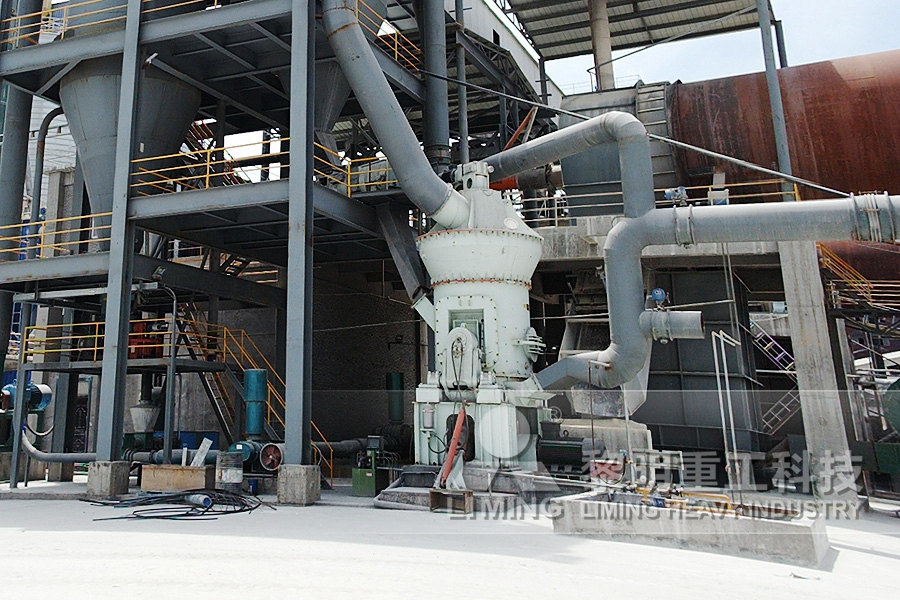
Guide to Modern Smelting Processes CED Engineering
alloys, enabling the production of materials with tailored properties to meet specific industrial or engineering requirements 3 Industrial Applications: • Material Production: Smelting is integral to the production of a wide range of materials used in construction, transportation, electronics, and countless other industries2024年11月21日 The grinding and grading stage of lithium ore is to ensure that lithium minerals are fully dissociated from gangue mineral monomers Therefore, lithium ore extraction is inseparable from ore grinding, and the common equipment for lithium ore grinding is ball mill Onestage closedcircuit grinding and grading process can be adopted, and the onestage Ball Mill Is Indispensable For Lithium Ore Processing2023年9月18日 Alternatively, call us on 1300 241 620 to speak to our experts today and learn all about the mining iron ore process Types Of Iron Ore In Australia Australia is a country that boasts a rich amount of iron ore, and several types are extracted and processed to meet both domestic and international demands Let’s discuss the primary types:Top 6 Steps Of Iron Ore Processing Australian Mining ServicesCOS – coarse ore stockpile; SC – secondary crush; HPGR – highpressure grinding roll; AGC – autogenous mill in closed circuit with cyclones and pebble crusher; RMS – rougher magnetic separation; CMS – cleaner magnetic separation; CMS2 second cleaner magnetic separation; PM – pebble mill; PC – primary crusher; SM – stirred mill; and TSF – tailings storage facilityEcoefficient and costeffective process design for magnetite iron ore
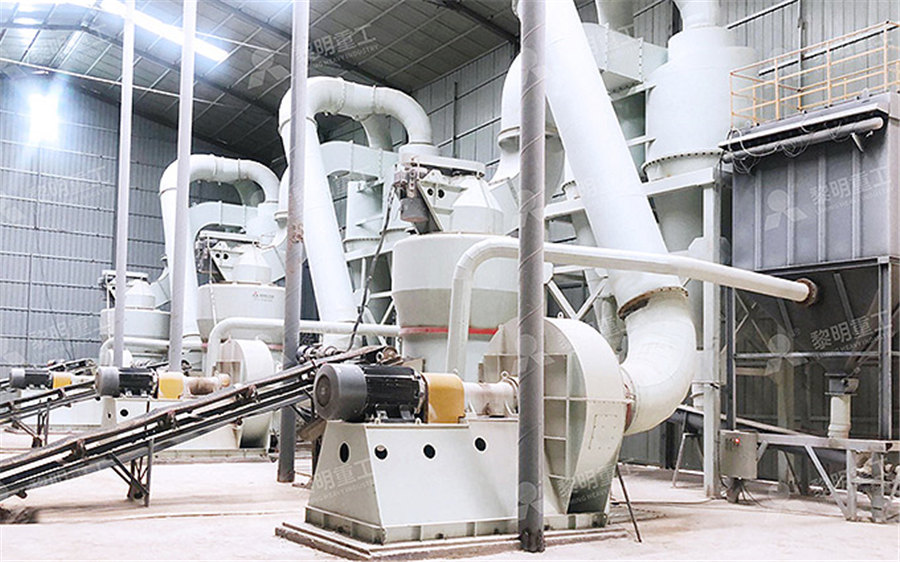
The Fascinating Journey of Steel Manufacturing
2023年4月16日 The quality of iron ore is crucial in determining the quality of the final steel product, as impurities such as sulfur and phosphorus can negatively impact the strength and durability of the steel Different methods are used to remove these impurities and improve the quality of the iron ore before it is used in steel production