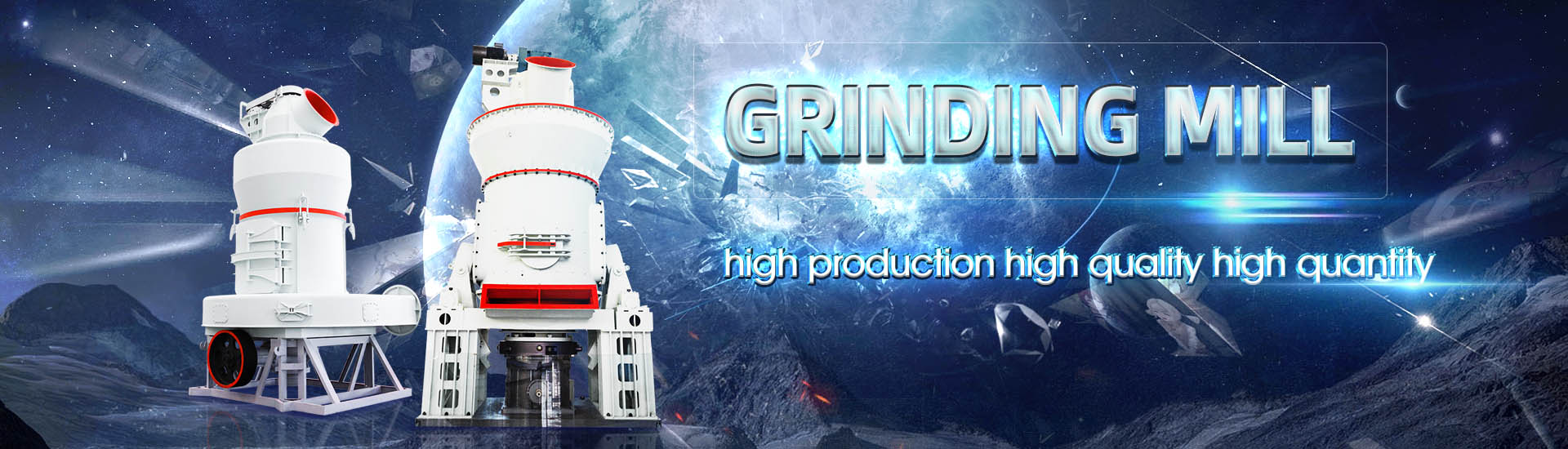
Iron oxide black grinding equipment process flow
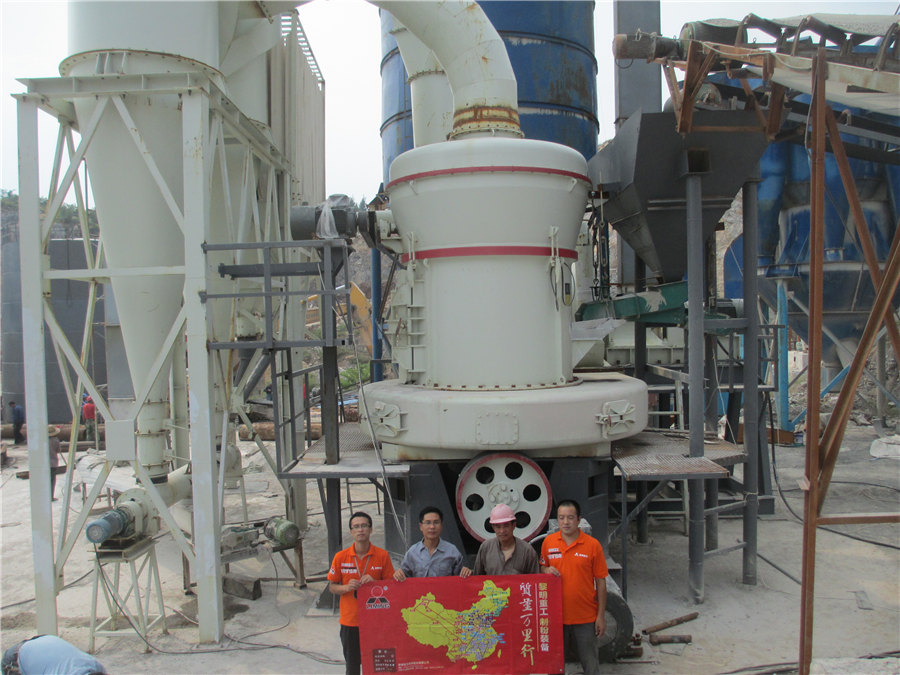
Iron Oxide Grinding Production Line With HGM80 Ultrafine Mill
4 天之前 Process Flow: 1 Raw Material Preparation Input Material: Iron oxide Initial Size: ≤20 mm Moisture Content: ≤6% (predrying required if higher) 2 Grinding Process Core 2022年1月1日 Through discussion of industrial flow sheets for iron ore beneficiation, including three flow sheets for upgrading magnetite ores and seven flow sheets for beneficiating Physical separation of iron ore: magnetic separation ScienceDirect2024年4月26日 Iron ore processing is a complex and vital process that transforms raw iron ore into usable steel From exploration and extraction to grinding, beneficiation, and ironmaking, each stage plays a crucial role in Iron Ore Processing: From Extraction to Manufacturing2024年1月1日 Ironmaking is the process of refining iron oxides in iron ores into metallic iron The earth’s crust is rich in iron, accounting for 42% of the total elements, ranking fourth With no Ironmaking SpringerLink
.jpg)
An investigation on optimum grinding system and conditions for
2020年10月1日 This study aims to characterize and then determine the method which allows for a high efficiency and quality for grinding the αFe 2 O 3 red powder into red iron oxide pigment 2022年1月1日 Firstly the most commonly used crushing and screening technologies, are discussed, including some typical flowsheets and a short review of new trends This is Comminution and classification technologies of iron ore2021年5月18日 Iron oxides nanoparticles with magnetic properties are good candidates for biomedical applications as they improve the quality of magnetic resonance imaging (MRI), cell Synthesis, Properties, and Applications of Iron Oxides: Versatility 2009年1月1日 The results of a theoretical option study for high capacity processing of a hard, finegrained silicarich magnetite ore is presented in this paper, with the emphasis on comminution circuitProcessing of Magnetite Iron Ores–Comparing

Iron Ore Processing, General SpringerLink
2022年10月20日 Making iron and steel from iron ore requires a long process of mining, crushing, separating, concentrating, mixing, agglomeration (sintering and pelletizing), and Download scientific diagram Process flow sheet for Pelletization using wet grinding process from publication: Iron Ore Pelletization Technology and its Environmental Impact Assessment in Eastern Process flow sheet for Pelletization using wet 2020年10月1日 After some other processes, αFe 2 O 3 red powder particles byproduct of regeneration of spent pickling liquor in ARP in iron and steel industry should be ground up to pigment grade to convert it to a value added product, red iron oxide pigment In this study, grinding tests on αFe 2 O 3 red powder were performed using four different types of An investigation on optimum grinding system and conditions 2024年8月17日 Defect name: features: Main causes: Stoma : There are smooth holes of different sizes inside or on the surface of the casting ① The furnace charge is not dry or contains many oxides and impurities; ② Pouring tools or Casting Production: Process Flow, Equipment,
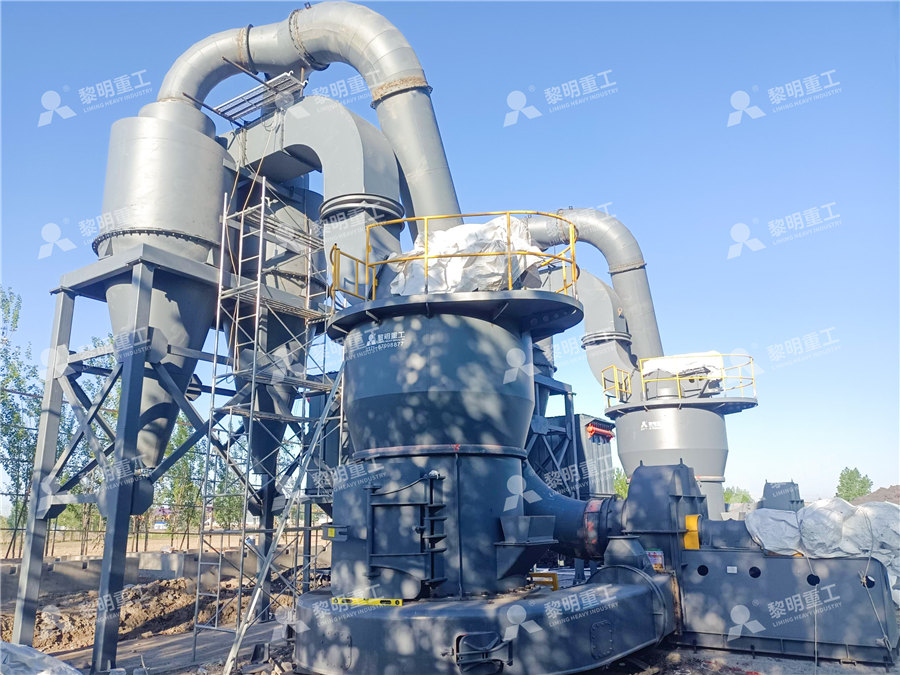
Physical separation of iron ore: magnetic separation ScienceDirect
2022年1月1日 Spiral separators can therefore be used to take out the coarser iron oxide grains in the primary grinding circuit to save grinding energy and help achieve a higher iron recovery Fig 914 presents a typical flow sheet for processing an oxidized ore containing about 30% Fe using a combination of spiral and SLon magnetite separators as well as reverse flotation2019年8月23日 Strong magnetic separation Manganese mineral is a weak magnetic mineral ( the specifical magnetization coefficient x=10×106~600×106cm3/g ), and it can be recovered in a strong magnetic field magnetic separator with a magnetic field strength Ho=800~1600kA/m (10000~20000oe), the manganese grade is increased by 4% to 10%Manganese Processing Equipment, Process Flow, Cases JXSC2019年9月25日 Black, brownish black, reddish brown, red, yellow, gray, white; rarely colorless However, tin ore is often accompanied by iron oxide minerals such as magnetite and hematite, therefore, the tin ores process generally adopts a twofour stage grinding circuit As for the tin process flow, Tin Processing Equipment, Process Flow, Cases JXSC Machine2019年8月23日 Zinc alloys well with other metals resulting in stronger, harder metals Brass, for example, is a mixture of copper and 20%45% zinc Adequate amounts of zinc are essential to a healthy life in all humans and animalsZinc Processing Equipment, Process Flow, Cases JXSC Machine

The six main steps of iron ore processing Multotec
When iron ore is extracted from a mine, it must undergo several processing stages Six steps to process iron ore 1 Screening We recommend that you begin by screening the iron ore to separate fine particles below the crusher’s CSS before the crushing stage A static screen is used to divert the fine particles for crushing2022年8月17日 (2) Grinding process Most iron ore grinding processes use twostage grinding processes, and most small and mediumsized concentrators use onestage grinding processes In recent years, some concentrators have changed the twostage grinding to threestage grinding due to the adoption of the new finescreen regrinding processIron ore crushing equipment and process flow2009年1月1日 The design outcome is a process flowsheet that specifies the required equipment and their arrangements in the beneficiation plant The iron ore beneficiation plants normally include a series Processing of Magnetite Iron Ores–Comparing Grinding Options2023年11月26日 The stepbystep guide provided in this article highlights the equipment, chemical reactions, and methodologies employed in each stage of the chrome plant process flow By grasping the intricacies of the chrome plant StepbyStep Guide: Chrome Plant Process Flow
.jpg)
(PDF) Diversity of Iron Oxides: Mechanisms of
2023年4月27日 Static magnetic properties of various samples of silicairon oxide systems: (a)Hysteresis loop and backfield demagnetization curve of a sample containing εFe 2 O 3 1 A process for the production of iron oxide black pigments by reaction or aromatic nitro compounds with metallic iron, optionally with addition of control chemicals, to form finely divided pigments consisting predominantly of Fe3 O4 , characterized in that the finely divided pigments thus produced are subjected to a heat treatment at 200 to 800 degrees C in a nonoxidizing EPB1 Manufacturing process for black iron oxide 2024年3月17日 A carefully calculated mixture of iron ore, coke, and limestone is fed into this furnace Here, temperatures soar above 2000 degrees Celsius, creating the perfect conditions for a chemical transformation The coke reacts with the blast of air, producing carbon monoxide gas which strips away oxygen atoms from iron oxide, reducing it to liquid ironA Visual Guide: Steel Making Process Chart Cabaro Group2022年4月30日 Iron oxide nanoparticles have been of great interest due to their physical and chemical properties, and the coprecipitation method is among the main ways to produce them Despite being the cheapest and most straightforward method, its main disadvantage during the scaleup process is the increase in the nanoparticle’s polydispersity and the reactor’s Automation of a lowcost device for flow synthesis of iron oxide
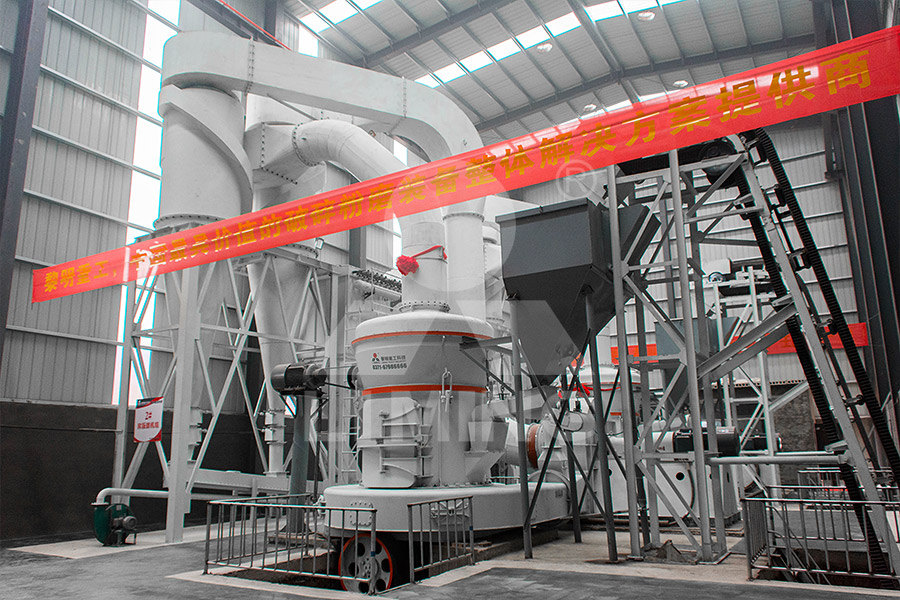
(PDF) CoPrecipitation Synthesis of Stable Iron Oxide
2020年6月1日 Coprecipitation is by far the most common synthesis for magnetic iron oxide nanoparticles (IONPs), as cheap and environmentally friendly precursors and simple experimental procedures facilitate 2018年4月15日 Iron chromium grinding waste (ICGW) is an iron‑chromium solid waste, resulting from grinding processes of chromium steel In China, >10 million tons of ICGW are produced each year The solid waste is a mixture of small metal particles, lubricants, resin adhesive and residuals from grinding media, such as abrasive belts or stone wheels [ 23 ]Preparation and formation mechanism of monodisperse micaceous iron June 2022; ARCHIVE Proceedings of the Institution of Mechanical Engineers Part C Journal of Mechanical Engineering Science 19891996 (vols 203210) 236(2):1107(PDF) A comprehensive review on the grinding process: Home Black Oxide: All You Need to Know The process of black oxide treatment has been a trendy yet underappreciated metal finishing technique used to protect and add aesthetic value to various components, parts, and devices In this post, we will discuss the basics of black oxide, focusing on itsBlack Oxide: All You Need to Know okdor

Introduction to Iron ore Pellets and Pelletizing processes
2013年2月23日 Fig 2 Flowsheet of straight travelling grate process Grate kiln process The grate kiln process was developed by former Allis Chalmer and the first plant on this technology was constructed in 1960 In the grate kiln process (Fig 3) the traveling grate is used to dry and preheat the pellets2010年3月1日 Each of the three black oxide processes has different heat and chemical requirements that must be considered when designing a blackening system Low Temperature, High Quality For today’s conscientious manufacturer the inhouse black oxide process itself must be safe to operate, nonpolluting, and produce the highest quality finishesBlack Oxide Finishing for Gears Gear Solutions Magazine Your 2016年2月29日 Small miners employ this process due to alluvial deposits contain free gold, the process is fast and efficient, the final product has a high gold grade and recoveries are between 80 to 95%, commercialization is fast Gold Extraction Recovery Processes2019年3月8日 Electrolytic inprocess dressing (ELID) is a grinding technique used to generate highquality surfaces on hard and brittle material Oxide layer formed on grinding wheel during ELID grinding heavily influences the surface roughness of the workpiece To study the microscopic structure of the oxide layer and model the thickness of it, we conducted a Microscopic characterization and modeling of oxide layer for
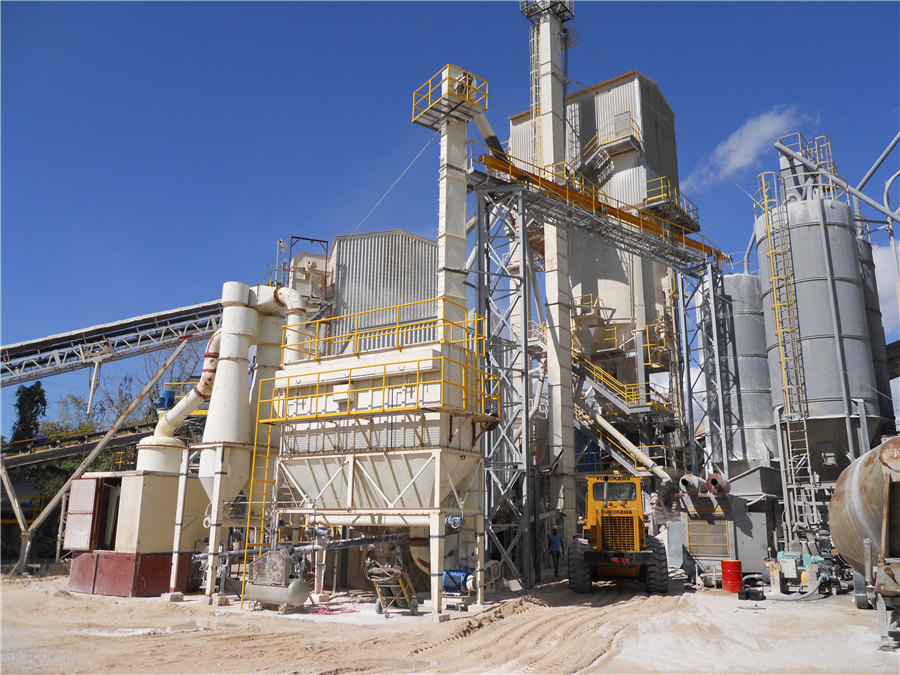
Hot Dip Galvanizing Properties and Process Guide
Issue 1 Hot Dip Galvanizing Properties and Process Guide June 2021 The galvanized coating The galvanizing process produces a durable, abrasionresistant coating of metallic zinc and zinciron alloy layers bonded metallurgically to the steel base and completely covering the work piece No other coating for steel matches2015年12月31日 Black Iron ore 4,520 18,469 22,989 Grate Kiln technology with wet grinding technology Typical flow sheets for the pelletization pu rchased from local market using wet grinding processIron Ore Pelletization Technology and its Environmental Impact 2024年1月12日 Key Definitions: Crucible: the thermit chemical reaction takes place in a vessel called a crucible; Mixture: A mixture of finely divided aluminum, metal oxide with the addition of any required alloying metals; Mold: This is a mold that is formed around parts that need to be weldedThe mode receives the molten metal Reaction: The chemical reaction between Thermit Welding Guide: Process Equipment Weld GuruDownload scientific diagram Process flow sheet for Pelletization using dry grinding process from publication: Iron Ore Pelletization Technology and its Environmental Impact Assessment in Eastern Process flow sheet for Pelletization using dry grinding process
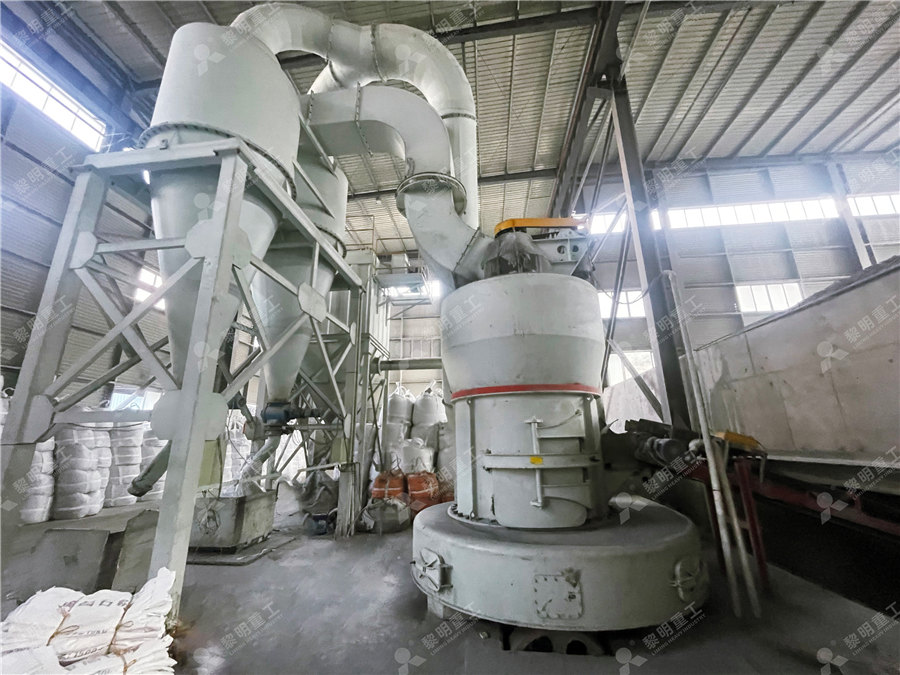
Process Mineralogical Assessment of the Grinding Products of
Process Mineralogical Assessment of the Grinding Products of the Per Geijer Iron OxideApatite Deposits Patrick Krolop a, Kari Niiranen , Sabine Gilbrichtb, and Thomas Seifertb aProcess and Product Development, LuossavaaraKiirunavaara AB (Publ), Kiruna, Sweden; bInstitute of Mineralogy, TU Bergakademie Freiberg, 2021年9月1日 For example, the black oxide coating process transforms the exterior of metal alloys such as steel, stainless steel, copper, zinc, and other ferrous metals It improves their corrosion resistance and ultimately blackens their surfaces In this article, we will break down the black oxide process, the different types, and their applicationsBlack Oxide Finish: An Extensive Guide for Precision Machined Parts2023年4月3日 Cold blackoxide finish is done at room temperature, whereas hot blackoxide finish involves a higher temperature process (around 285°F or 140°C) Cold blackoxide finish is generally easier and more costeffective to apply but may not provide the same level of corrosion resistance and wear protection as hot blackoxide finishProtect Metal Parts with BlackOxide Finish: Process & Benefits2017年2月16日 PDF Sintering is a thermal agglomeration process that is applied to a mixture of iron ore fines, recycled ironmaking products, fluxes, slagforming Find, read and cite all the research you (PDF) Iron Ore Sintering: Process ResearchGate
.jpg)
Synthesis, Properties, and Applications of Iron Oxides: Versatility
2021年5月18日 21 Iron (III) Oxides Iron (III) oxide is, of course, a compound that exhibits four different crystalline polymorphs: αFe 2 O 3, βFe 2 O 3, γFe 2 O 3, and εFe 2 O 3Hematite and maghemite usually appear in nature, while beta and epsilon structures are generally synthetic oxides [10, 11]In general, the iron (III) oxides anions arrange in closepacked structures, 2024年8月5日 The transition to green steel production is pivotal for reducing global carbon emissions This study presents a comprehensive technoeconomic analysis of various green steel production methods, including hydrogen reduction and three different electrolysis techniques: aqueous hydroxide electrolysis (AHE), molten salt electrolysis, and molten oxide electrolysis Economics of Electrowinning Iron from Ore for Green Steel 2019年8月23日 The wet process includes three stages of ore preparation, ore beneficiation processing and product processing The beneficiation stage may include hydraulic grading, flotation, selective flocculation, magnetic separation, chemical treatment (bleaching), etc to remove different impurities The prepared slurry pulp is first desanded by the rake type Kaolinite Processing Equipment, Process Flow, Cases JXSC reduction process to achieve 80% passing 0150 mm size The 45% hematite and 418% quartz particles fall under the size category below 75µm Thus, the ground product of the gravity separation process and fine material obtained from the original feed (classifier O/F) were mixed and subjected to a grinding process to obtain 80% passing 75 µmSPECIAL IRON ORE PROCESSING ISSUE Development of a process
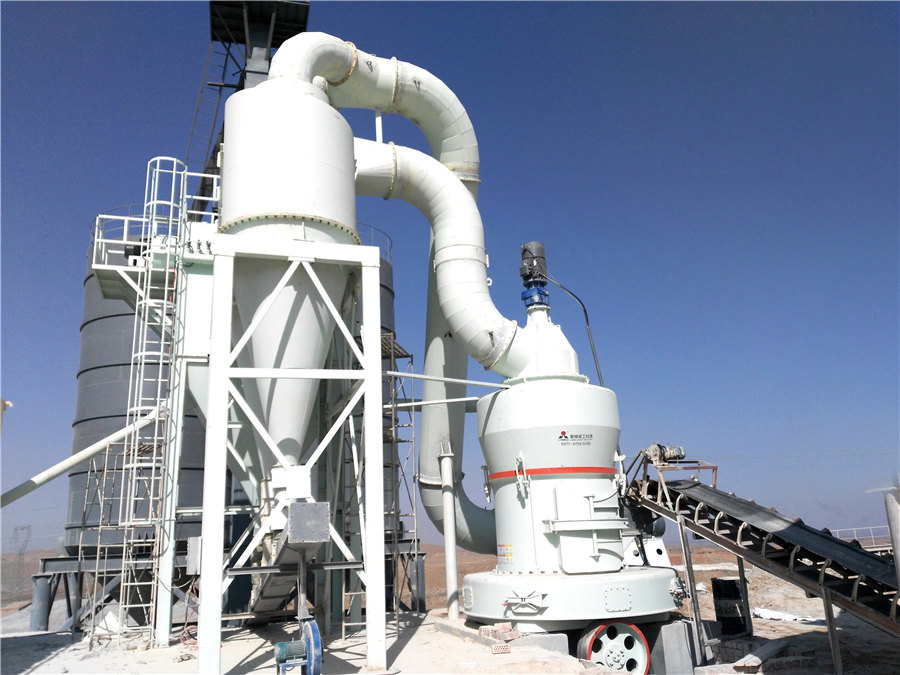
Process for preparing transparent iron oxide pigment dispersions
This invention relates to a process for preparing transparent iron oxide pigment dispersions The dispersions are prepared by milling a mixture of iron oxide pigment and a liquid vehicle in a bead mill containing glass beads as the grinding media The pigment dispersions can be used in the preparation of paints and coatings which exhibit transparent quality and absorb ultraviolet 2023年8月26日 Hot Black Oxide: In this process, the material is immersed in hot baths containing sodium hydroxide (NaOH), nitrates (such as sodium nitrate – NaNO3), and/or nitrites (such as sodium nitrite – NaNO2) at a temperature of 141 °C (286 °F)The surface of the material is converted into magnetite (Fe3O4), which is a black oxide Water is periodically added to the Black Oxide Coating Process Explained Heat Treatment Masters2023年3月13日 As for the grinding and floating process, it is more advantageous to adopt the stage grinding and floating process for refractory copper ore, such as the regrinding and reseparation of coarse concentrate, regrinding and reseparation of bulk concentrate, and separate treatment of medium ore 2 Beneficiation methods of copper oxide oreHow to Process Copper Ore: Beneficiation Methods and Equipment2022年10月21日 Beneficiation Method and Process Flow of High Purity Quartz Sand Luna Wang,whatsapp+94 Report this article Shandong Xinhai Mining Technology Equipment IncBeneficiation Method and Process Flow of High Purity Quartz
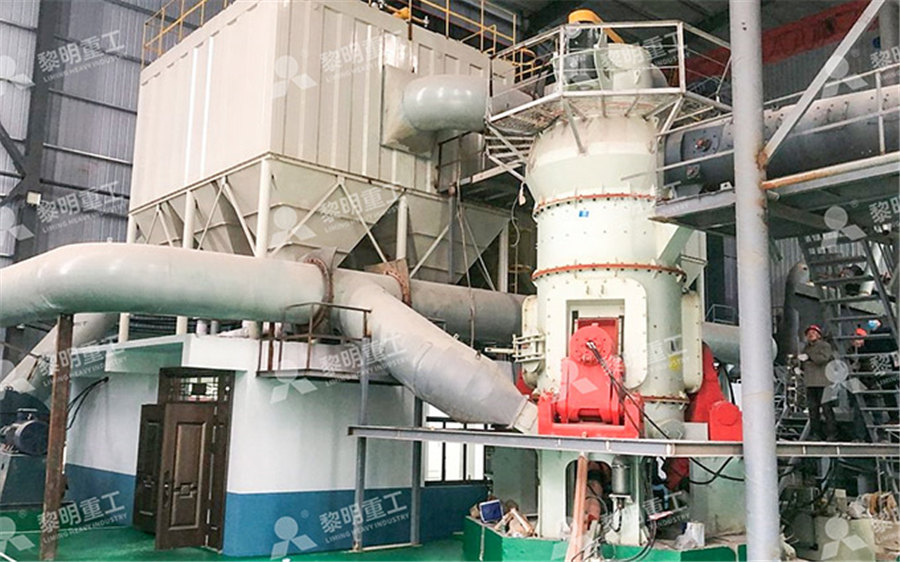
Iron Ore Pelletization: A Critical Review of Processes and
2024年4月16日 Iron ore pelletization is a critical aspect of the steel manufacturing process, providing a method to utilize fine iron ore particles and beneficiate lower grade ores, which enhances the overall output and efficiency of steel production processes Pelletization involves converting iron ore fines into compact pellets, which are then used in blast furnaces or direct