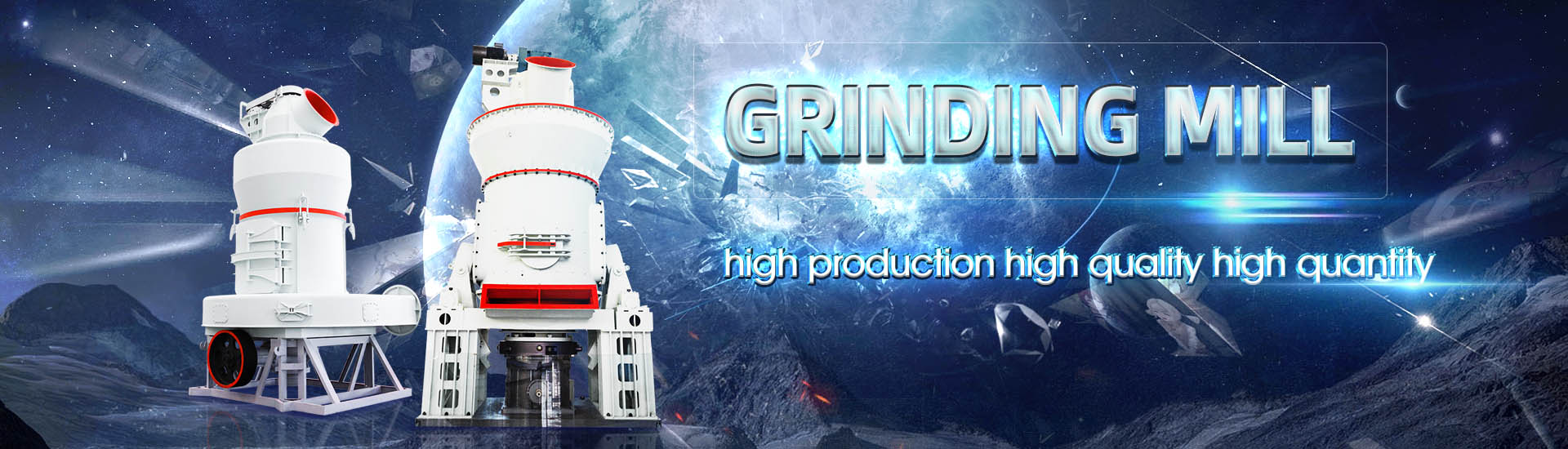
Therefore when grinding roller
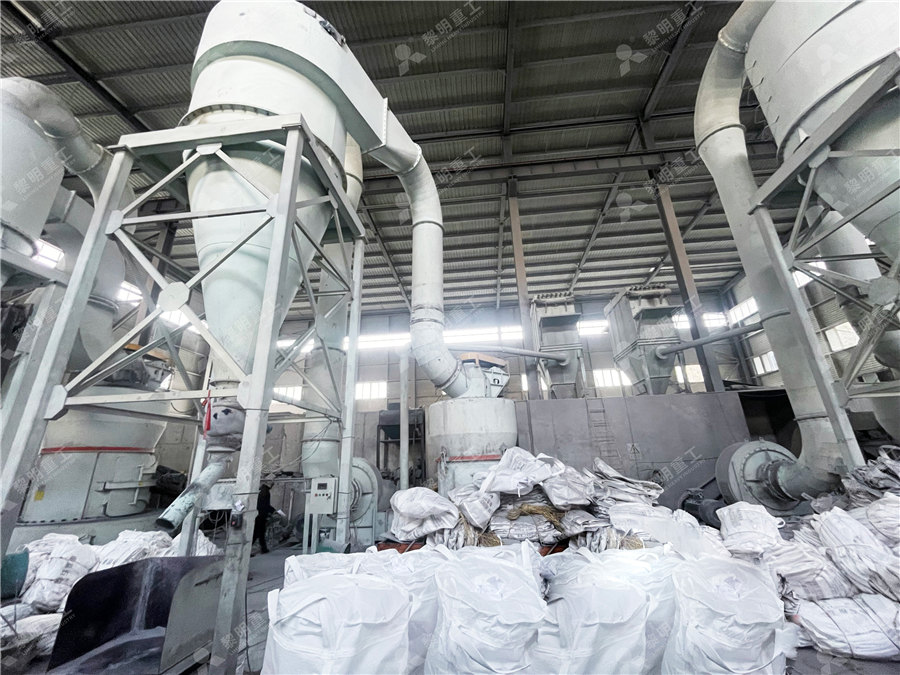
Analysis of vertical roller mill performance with changes in
2022年5月31日 The vertical roller mill (VRM), including powder separation and crushing subsystems, is used extensively for intermediate crushing of minerals in several industries such as cement, electric power, and chemical Compression crushing is also the main crushing Roller mill is a type of grinding equipment for crushing materials by pressure between two or more rolling surfaces or between rolling grinding bodies (balls, rollers) and a track (plane, ring, and Roller Mill Springer2007年1月1日 This chapter describes how the flour milling process interacts with the wheat kernel structure to separate it into its functional components The chapter traces the historical Chapter 7 Roller Milling of Wheat ScienceDirect2009年1月1日 Based on screening analysis, laser size analysis, grindability and rigidity tests of samples collected on line from a cement and a power plant, a simulation of the grinding Grinding process within vertical roller mills: experiment and
.jpg)
Vertical roller mill for raw Application p rocess materials
Grinding raw materials needs lots of energy Tube mills had been used for grinding, but the energy efficiency level was lower Therefore, the introduction of highly efficient grinding The roller mill’s ability to reduce materials to a uniform particle size provides more control of product characteristics and minimizes waste, as shown in Figure 1 The mill’s controlled Roller mills: Precisely reducing particle size with greater efficiency2020年6月17日 In this article, the critical enabling roller grinding technology is introduced toward higher stability, efficiency, accuracy, and intelligence, including: (1) the grinding machine Advances in grinding technology in China with application in steel 2020年3月27日 During the grinding process, the material particles, abrasives and some impact loads will cause wear on the roller surface, which will affect the technical performance and service life UsingVertical Roller Mill Wear Mechanisms and Preventive
.jpg)
Surface roughness in grinding outer ring inner raceway of tapered
2023年6月20日 The results show that when the workpiece speed is 300 rpm and the grinding depth is 03 μm, the surface roughness decreases from 0259 to 0208 μm as the grinding 2022年9月21日 Infeed centreless grinding can produce rollers with roundness control of 01 µm The surface roughness Ra can be 004 µm Wu et al and Xu and Wu performed systematic Advances in ultraprecision machining of bearing rolling elementsSimply put, the roller press is the most energyefficient grinding machine on the market Since its commercial introduction into the cement industry by KHD in the 1980s, hundreds of them have been installed in the cement and minerals Roller Press KHD Humboldt Wedag2017年12月6日 In addition, the influence of the process parameters on the surface roughness and the material removal rate when external grinding SAE 8620 steel was reported in [16]An experimental study of the effects of dressing parameters on the
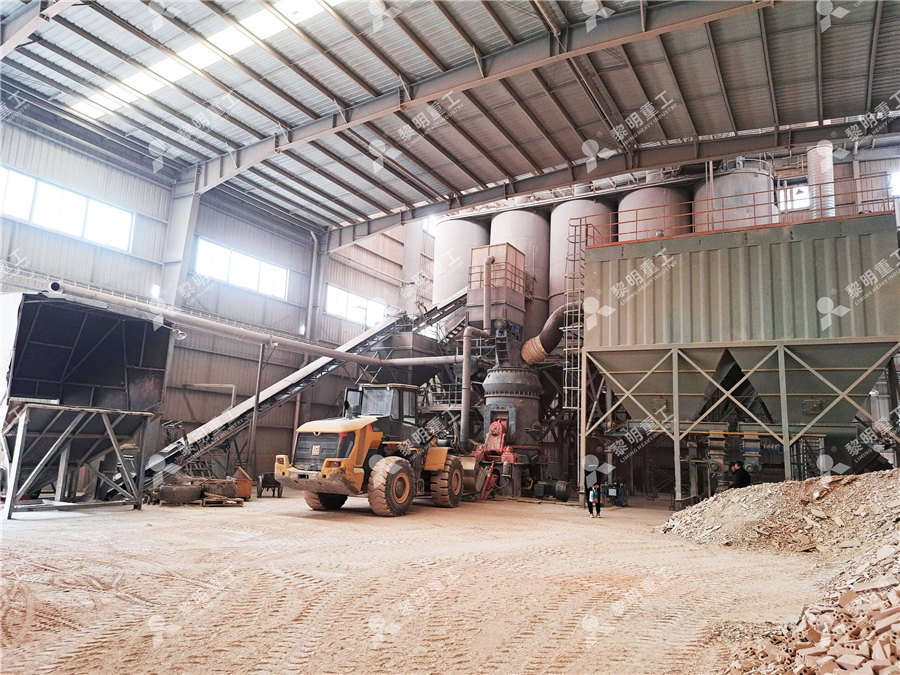
Polysius Roller Mills For grinding
4 Advantages of Polysius roller mills at a glance: xHigh operating reliability and availability, as well as easy system handling, due to the fact that grinding, drying and separation all take place in a single compact unit xConsistently high product quality with minimum energy requirement, due to the integrated highefficiencyTherefore, the chemical composition and fineness of vertical mill products can be quickly determined and corrected 6 Low wear and high utilization rate Because there is no direct metal contact between the grinding roller and the grinding disc in the operation of the limestone powder ultrafine vertical roller mill, Limestone Powder Ultrafine Vertical Roller Mill Clirik Grinding 2020年3月27日 34 Ensure the leakproofness of the grinding roller The leakproofness of the grinding roller has a great influence on the bearing Be sure to use a specific rotating oil for sealing, this can Vertical Roller Mill Wear Mechanisms and Preventive MeasuresPrevious Post Next Post Contents1 KILN ALIGNMENT ROLLER GRINDING2 1 Hot kiln alignment using electronic devices21 11 Advantages of this Technique22 12 Tools and Instruments Used23 13 Measurement Procedures Using Total Station24 14 General Notes3 2 Grinding of rollers tyres31 21 Grinding Method32 22 Grinding Machine33 23 KILN ALIGNMENT ROLLER GRINDING INFINITY FOR CEMENT EQUIPMENT
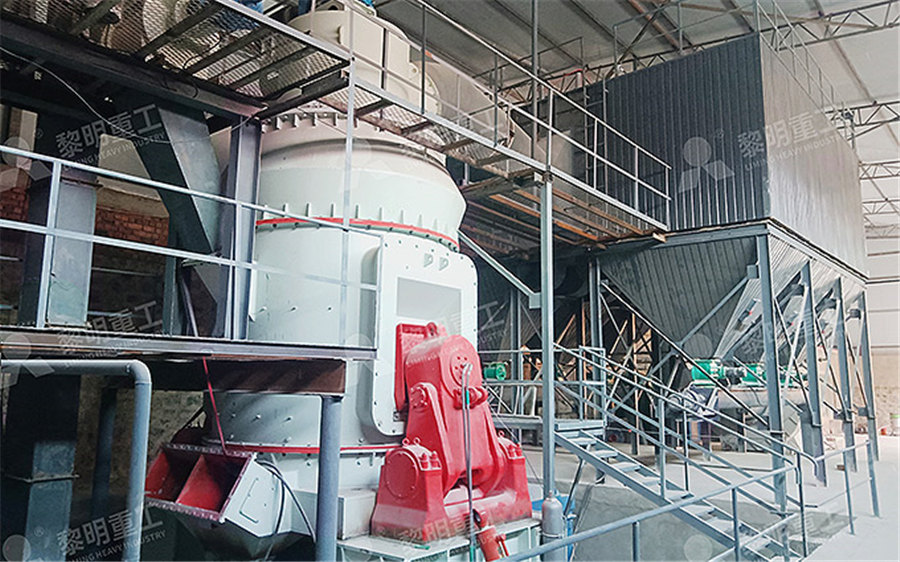
Advances in grinding technology in China with application in
2020年6月17日 Compared with transverse cylindrical grinding, roller grinding requires highprecision multiaxis motion In addition, with the insite machine vision for gloss defect, and intelligent process parameter optimization strategy Therefore, this article will shed light on the development trend of the enabling technology toward 2007年2月1日 First Polysius slag roller mill in China The first Polysius roller mill for slag grinding in China is in operation since 2002 in Anshan in the province of Liaoning The grinding plant of the Angang Group Slag Development Company is exactly the same size as the one which has been in operation since 1995 just a few hundred kilometres away in KoreaSlag grinding with the Polysius Roller Mill in ChinaTherefore, the cracks and damage on the cot surface must have to be removed, the common way to Top roller cot grinding The diameter of top roller rubber cot reduced after each grinding cycle was by 03mm The semiautomatic grinding machine was used for grinding the cotsAn Investigation on the Effect of Top Roller Cot Grinding and2023年7月4日 The basic structure of the roller mill includes the grinding roller, the grinding body, the force generation and transmission mechanism, airflow, and the device for easy replacement It can be divided into vertical roller mill, horizontal cylinder roller mill, high pressure roller mill, Raymond mill, and column millRoller Mill SpringerLink
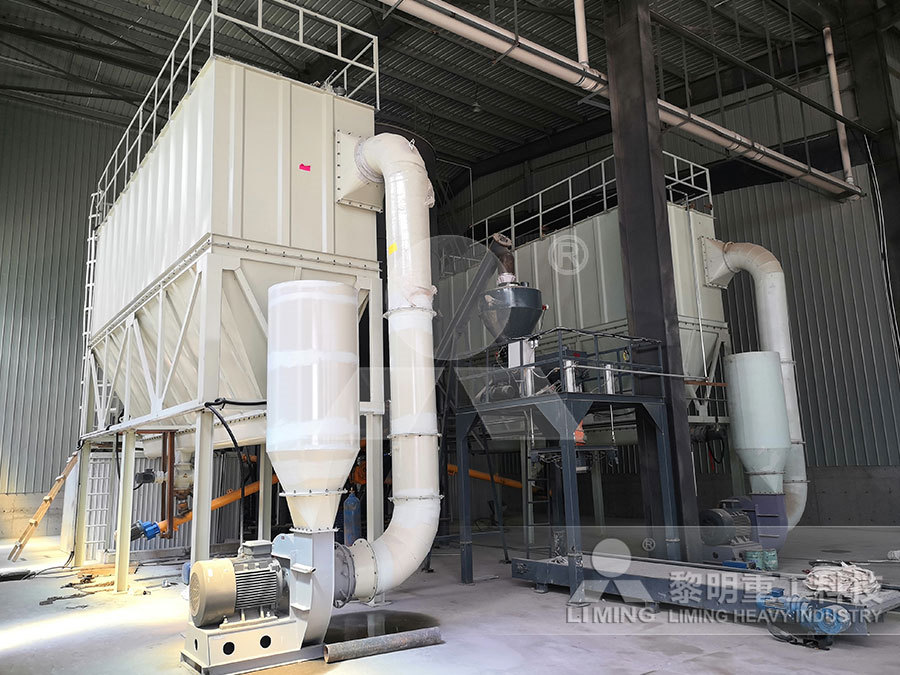
Grinding considerations when pelleting livestock feeds
roller mill during its normal expected life will be 10 to 20 times more expensive than the machine cost alone It is therefore very important to make sure the equipment selected is carefully matched to the specific grinding task to ensure most efficient operation For hammermills, the diameter (tip2020年3月1日 Grain milling might be the oldest manufacturing process in the world Archaeologists have found drawings, dating back to 2600 BC, of the basic process of rubbing or grinding using two stones on the walls of Egyptian tombs (Walker Eustace, 2016)Grinding (milling) of cereal grains is the fundamental operation currently used to produce flour, which is Stone milling versus roller milling: A systematic review of the R Roller Mill Xiao Xiao1, Huang Lilong2 and Xu Kuangdi3 1Changsha Research Institute of Mining and Metallurgy, Changsha, China 2Changsha Research Institute of Mining and Metallurgy, Changsha, China 3Chinese Academy of Engineering, Beijing, China Roller mill is a type of grinding equipment for crushing materials by pressure between two orRoller Mill Springerroller mill during its normal expected life will be 10 to 20 times more expensive than the machine cost alone It is therefore very important to make sure the equipment selected is carefully matched to the specific grinding task to ensure most efficient operation For hammermills, the diameter (tipGrinding considerations when pelleting livestock feeds
.jpg)
Cement grinding Vertical roller mills versus ball mills
With respect to forming a stable grinding bed the OK mill’s patented roller and grinding table designs proved to be a major breakthrough Figure 1: As shown in track will thus become coarser and therefore less prone to fluidisation Industrial experience has proven that due to the design of grinding parts and the high efficiency 2012年3月1日 Operating experience with a vertical roller mill for grinding granulated blastfurnace slag and composite cements the LM 352+2 vertical roller mill therefore had to be resurOperating experience with a vertical roller mill for grinding 2021年10月2日 The present study is directed to the temperature and residual stress fields in the hardfacing remanufacturing for a largescale grinding roller with damage For this purpose, a numerical procedure for the hardfacing process based on the thermal cycle curve method was established, and the effectiveness of the proposed procedure was verified by the Numerical simulation of hardfacing remanufacturing for large 2009年1月1日 Keywords: vertical roller mill; grinding; simulation 1 Introduction Grinding is a highly energy consuming process Considerable coal, cement raw materials and clinkers, Therefore, optimizing grinding process parameters is a very important field of study related to energysaving and the reduction of power consumption in ChinaGrinding process within vertical roller mills: experiment and
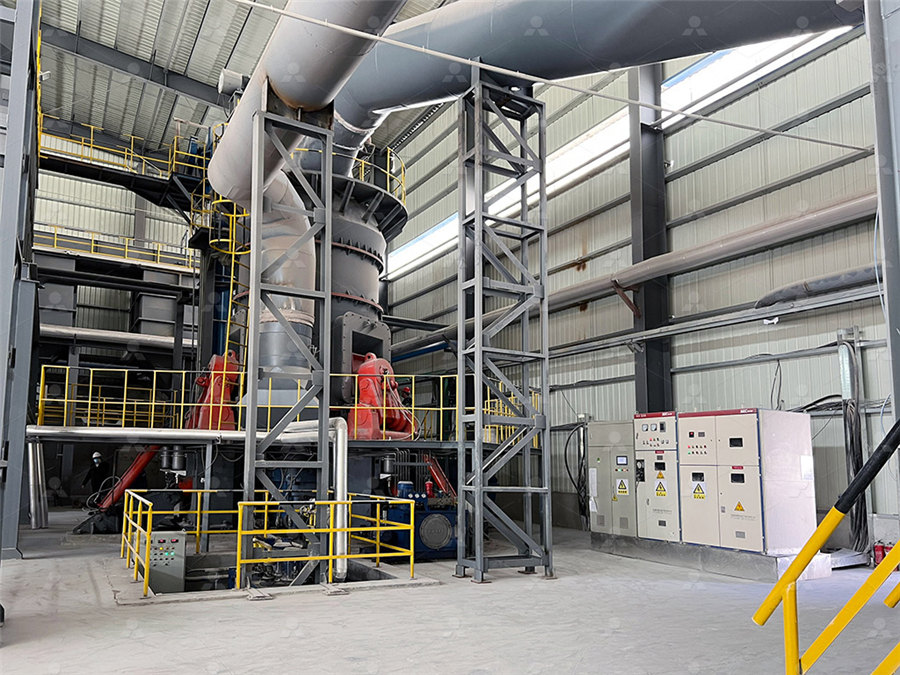
The mechanism investigation of ultrasonic roller dressing vitrified
2022年9月1日 The dressing object is the VCBN grinding wheel (Henan Moao Superabrasive Co, LTD), the diamond roller is made of powder metallurgy, the wheelbase is 45 steel, the parameters of the grinding wheel and roller are provided in Table 1, and the workpiece is bearing rings (φ 60 mm × 20 mm), whose material is 100Cr62023年2月6日 To improve the wear resistance and mineral crushing performance of grinding rollers in cement, mining, and other engineering fields, a striped groove morphology was designed on the normal grinding roller surface in this study The wear resistance of grinding rollers with different striped groove parameters and the crushing performance of quartz sand were tested Effect of the Bionic Transverse Stripe on Wear Resistance and2018年1月1日 Roller dressers consist of a cylindrical body with a single layer of diamond particles impregnated in a metal matrix Dressing rolls can also be made to specific forms which will then be generated in the surface of the abrasive wheel, therefore enabling the grinding of complex features onto the workpiece [4]This leads to a much faster dressing process and An experimental study of the effects of dressing parameters on the large vertical roller mills for grinding cement raw material Redundancy und interchangeability – große VertikalRollenmühlen für die Rohmehlerzeugung 4DiplIng M Keyssner, Loesche GmbH, Düsseldorf, Germany Reprint from / Sonderdruck aus: Cement International – Redundancy and interchangeability – large vertical roller mills
.jpg)
Investigation of Waveforms of Roller Bearing’s Working Surfaces
2020年6月5日 When grinding the roller bearings of the roller bearings, it is necessary to ensure rapid removal of the allowance and processing performance [1,2,3], the final macro and micro geometric accuracy of the machined surface []It is known that the magnitude of the cut layer during grinding is proportional to the normal grinding force [5, 6], and the formation of the 2024年3月1日 Introduction As the core tool in grinding processes, grinding wheels directly affect processing quality, efficiency, and costs Therefore, when selecting grinding wheels, it is necessary to comprehensively consider multiple factors, including the characteristics of the workpiece, the performance of grinding wheel abrasives, and other important factorsGrinding Wheel Selection Guide: Comprehensive Considerations grinding using standard bond grinding calculations based on population balance models is successfully applied [4, 38] Various grinding laws, energy relationships, control factors and controller design for cement grinding are discussed in [37] Figure1 Vertical roller mill for cement grinding [13] VRM shown in Figure1 uses hydraulically hardPROCESS CONTROL FOR CEMENT GRINDING IN VERTICAL ROLLER 2022年1月23日 Roy, GR Increasing cement grinding capacity with vertical roller mill technology In Proceedings of the IEEE Cement Industry T echnical Conference, Jacksonville, FL, USA, 5–9 May 2002Analysis and Optimization of Grinding Performance of Vertical Roller
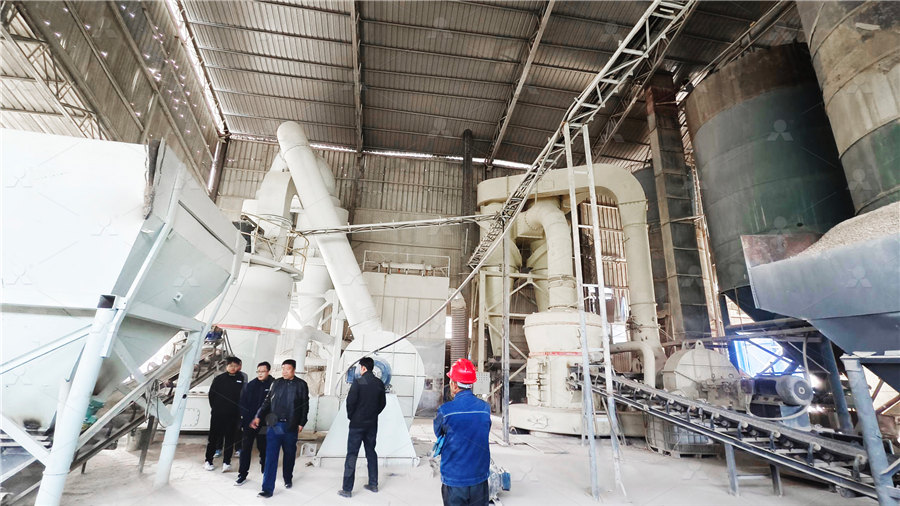
Triple Roller Mill|Grinding Of High Viscosity Materials
Generally, they can be easily ground To meet the grinding requirements, the final processing fineness of the triple roller mill can generally reach about 118µm (measured with a fineness scraper), but it is not suitable to grind raw materials with acid and alkali components or enough to cause roller corrosionVertical Roller Mill Parts Manufacturing Service AGICO CEMENT not only designs and manufactures vertical roller mills suitable for raw meal grinding, cement grinding, and pulverized coal grinding, but also supplies cast steel parts for various parts of vertical roller mills Our factory is equipped with the most advanced vertical mill production line in China, which can process Vertical Roller Mill Parts AGICO Cement PlantSM18 SERIES HORIZONTAL EMERY ROLLER Rice milling is a processing process in which the rice grains are forced to collide, rub and roll with each other with the help of the rotating milling roller, and the rice grains are partially or completely removed by the grinding and friction, so that the rice grains can meet the predetermined quality requirementsSM18 SERIES HORIZONTAL EMERY ROLLERFANGFANG RICE Therefore, roll crowning is one common method of reducing the nip variation caused by roller deflection The other benefit of crowning a roll is that it will yield improved product quality And more importantly Banding – Roller Wear, Grinding Dynamic Nip Impression 1 2 a a The Basic Theory of Crowning Industrial Rollers Thomasnet
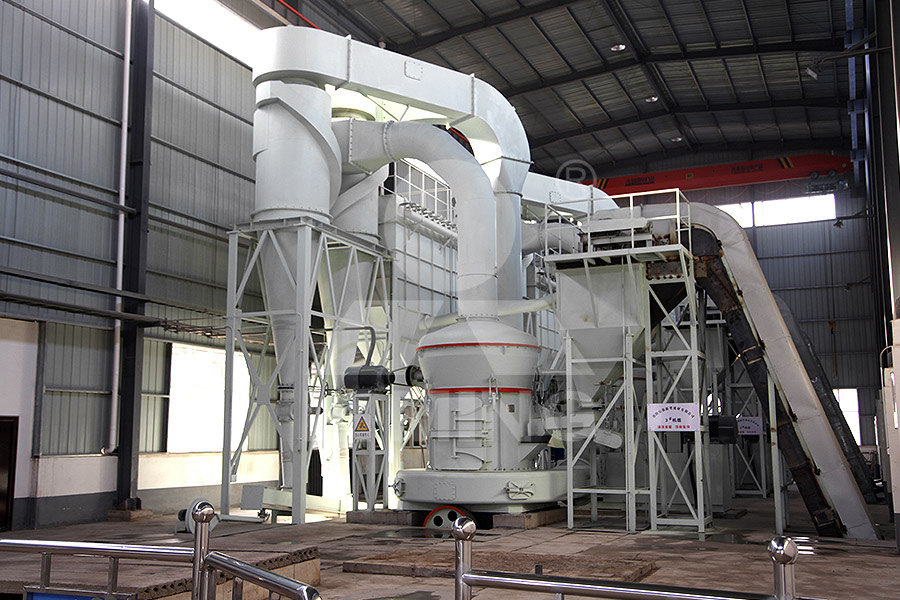
ultrahard abrasives grinding wheel dressing solutionsdiamond roller
2022年12月29日 Diamond roller dressing method: a method of cutting the grinding wheel to be dressed by using a rotary tool inlaid or covered with many small particles of diamond on the working surfaceDiamond dressing rollers are widely used in profile grinding (cored and coreless), internal circular profiles, threaded profiles, flat profiles, guide plates, multikey shafts and gears Highpressure comminution of ores with High Pressure Grinding Roller Presses (HPGRs) is predominantly achieved through compression flotation or other separation processes Grinding with HPGRs therefore helps to optimize the energy requirements and performance of such downstream processes In order to achieve proper interparticle HighPressure Grinding Roller Presses for Minerals Processing2021年2月26日 The present study is directed to the temperature and residual stresses fields in the hardfacing remanufacturing for a largescale grinding roller with damage(PDF) Numerical Simulation of Hardfacing Remanufacturing for 2023年11月21日 In the present incident, one of the rollers of grinding mill in cement plant failed during operation, exhibiting longitudinal cracking over inner surface Deposition welding was carried out just before the incident to match the wornout profile of the roller Investigation revealed that the subsurface of the cracked region contained discontinuities like blow holes Operational Failure of Vertical Roller Attached to a Grinding Mill
.jpg)
Design and Dynamic Performance Study on Hydrostatic Lubrication System
sion Roller Grinding head To develop the hydraulic lubrication system, it is necessary to analyze the lubrication requirement of the highspeed roller grinder Therefore, the structure principle of highspeed roller grinding head was analyzed firstly The structure of the highspeed precision roller grinding head is as shown in Fig 1A particular challenge when using the double disc surface grinding process is the avoidance of thermal surface damage (grinding burn), as a sufficient amount of coolant cannot always be transported to the grinding zone through the very narrow grinding gap Therefore, resinbonded grinding wheels with grit sizes between 36 and 220 and extremely Double disc surface grinding ATLANTICKeywords Grinding wheels Safety Mechanical design Analysis 31 Introduction To achieve a high performance from a grinding wheel it must stay sharp, and must have the ability to absorb a high volume of metal chips Therefore, the grinding wheel must be porous and must be able to withstand high grinding loads that areChapter 3 Grinding Wheel Safety and Design56 CEMENT INTERNATIONAL 4 2/2012 4 VOL 10 ZUSAMMENFASSUNG Vertical roller mills are the mills traditionally used for processing granulated blastfurnace slag and for grinding compositeOperating experience with a vertical roller mill for grinding
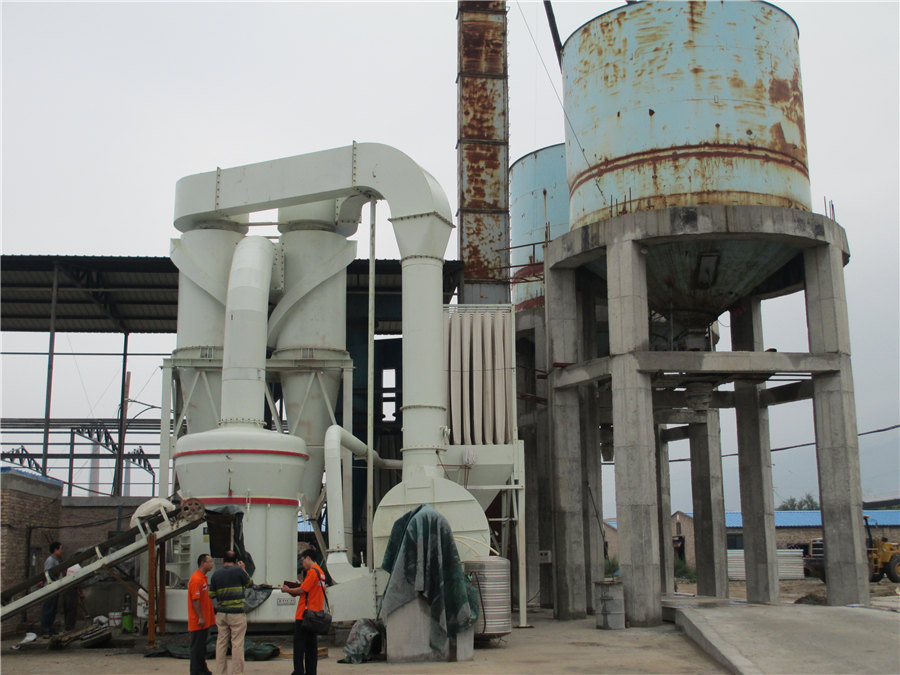
Material Use Roller Mill Maintenance: What You Need to Know
2023年7月25日 Products You Can Grind in a Roller Mill “You can grind multiple products in a roller mill,” says Josh Tracy of RMS’s Research Development Department “Our automated machines have what’s called ‘recipes’, in which you can set and name them based on the material you’re grinding2015年3月10日 Vertical roller mills (VRM) have been used extensively for comminuting both cement raw materials and minerals like limestone, clinker, phosphate, manganese, magnesite, feldspar and titanium These mills combine crushing, grinding, classification and drying operations in one unit and have advantages over conventional machines and literature reports that 15% Copper ore grinding in a mobile vertical roller mill pilot plant