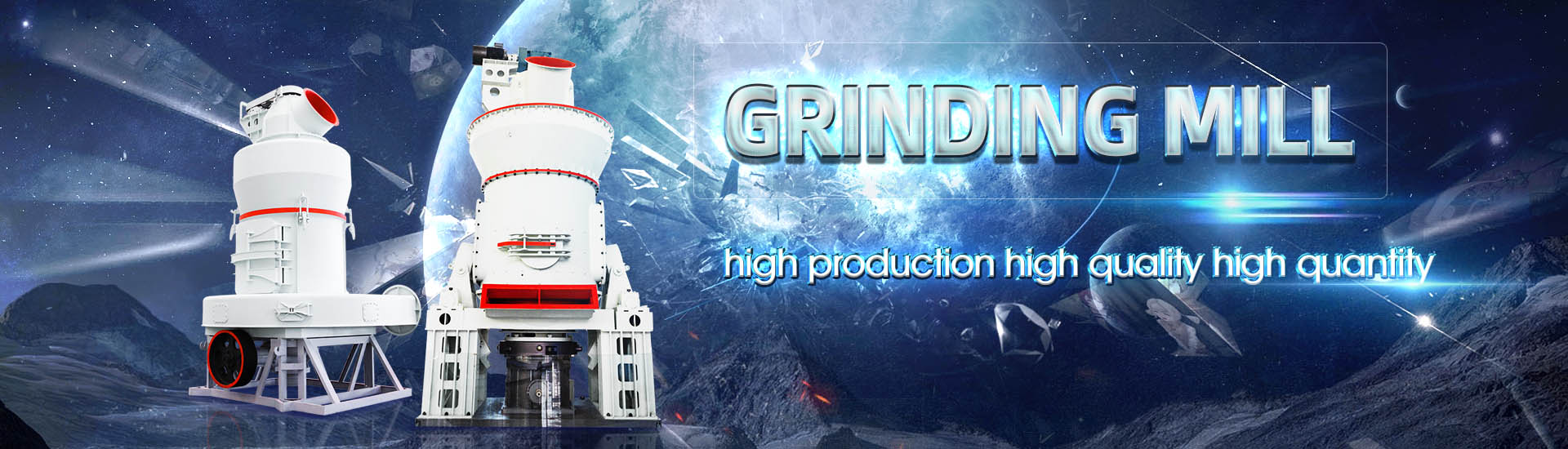
Lithium ore grinding in water slag

Processing of lithium ores: Industrial technologies and case studies
2021年5月1日 Water leaching of slag is accompanied by an exothermic reaction, which leads to the heating to 80–90 °C When the slag dissolves, the metallic lithium interacts with water 2023年1月1日 The process flow is to convert lithium in ore into lithium sulfate by mixing roasting lithium mineral and excessive potassium sulfate (or calcium sulfate or a mixture of both), leach Lithium extraction from hard rock lithium ores (spodumene, In this study, lithium was recovered from a simulated pyrometallurgical slag (pyroslag) via sodium roasting and water leaching The thermodynamic process for the reactions between slag and additives such as NaCl, NaNO 3 and Na 2 SO 4 Aqueous leaching of lithium from simulated 2024年11月2日 By 2003, the annual discharge of lithium slag in China surpassed 15 million tons, creating an urgent need for established largescale disposal technologies One of the Research Progress on the Activity Stimulation of Lithium Slag in
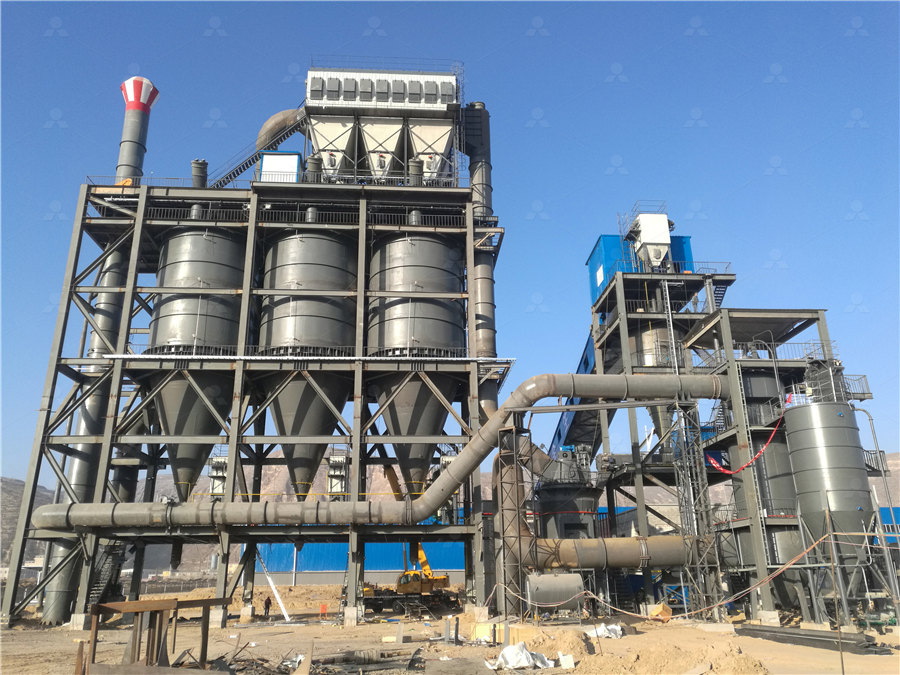
Chlorination Roasting of LiBearing Minerals and Slags: Combined
2023年8月24日 Li is extracted from three different Libearing minerals (kunzite, hiddenite, and lepidolite) and Licontaining slag, through the chlorination roasting process at 1100 °C under 2015年11月16日 Mixed grinding with Na 2 S followed by water leaching was performed to extract Li from lepidolite The leachability of Li increases dramatically in the ground mixture, regardless of the mixing ratio over the Extraction of Lithium from Lepidolite Using Mixed 2020年3月20日 In this study, lithium slag (LS), as the byproduct of lithium salts production, was treated by wet grinding process to prepare micro particles and used to expedite the early Preparation for microlithium slag via wet grinding and its 3 天之前 The composite sulfate roasting method is a highly effective technique for the extraction of lithium from lepidolite ore; however, the atomiclevel mechanism underlying the roasting Study on the Extraction of Lithium from Lepidolite Ore by
.jpg)
Processing of lithium ores: Industrial technologies and case studies
2021年2月1日 Request PDF Processing of lithium ores: Industrial technologies and case studies – A review Recently, there has been a steady increase in demand for lithium (Li) and its compounds 2022年10月31日 Ore preparations Spodumene ore samples (− 15 mm) were obtained from the Bald Hill Mine Eastern Goldfields, Western Australia Table 1 shows the mineralogy of the sample determined using XRD As Lithium deportment by size of a calcined spodumene ore2020年3月20日 Industrial wastes consumed by the preparation of building materials is a potential method to ensure the sustainable development In this study, lithium slag (LS), as the byproduct of lithium salts production, was treated by wet grinding process to prepare micro particles and used to expedite the early hydration of Portland cement (PC) The physicalchemical Preparation for microlithium slag via wet grinding and its 2024年2月16日 Lithium Slag (LS), also known as Delithiated Beta Spodumene (DBS), is a byproduct of lithium extraction from spodumene ore that contains active silicon dioxide and aluminium oxide making it a potential supplementary cementitious material (SCM) for concreteTransport properties of concrete containing lithium slag
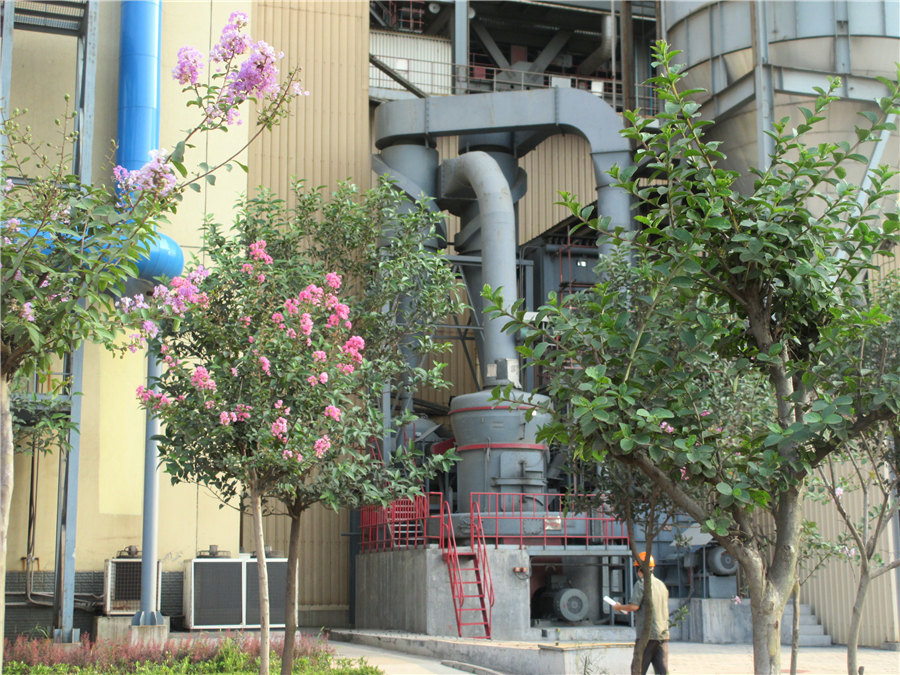
Research and exploration progress on lithium deposits in China
2020年3月1日 Rare metals are the critical mineral resources of strategic emerging industries (Wang RJ et al, 2015), which play an irreplaceable role both in the highend equipment manufacturing industry and in the field of new energy vehiclesBeing one of the most concerned minerals resources among the rare metals at present, the search for lithium ore has become a A kind of alkaline process handling process of lithium ore, is related to technical field of beneficiation, and the alkaline process handling process of the lithium ore is that lithium ore is baking mixed with alkali, and water quenching ore grinding is leached, and filters to obtain the first filtrate and filter residue;Lithium precipitating reagent is added in the first filtrate, the The alkaline process handling process of lithium ore2024年2月15日 Coalbased lithium ores: Thermal activation at 500 ℃ for 2 h: 8 M Oxalic acid, 5 mL/g, 60 min, 90 ℃ 8912 % of Li [25] Coal gangue: Thermal activation at 400 ℃ in N 2: 02 M (NH₄) 2 SO 4; (pH = 10), 30 mL/g, 180 min, 90 ℃ 5582 % of Li 467 % of Al, This work: Coal gangue: Grinding 90 min; thermal activation at 400 ℃ in N 2Study on modes of occurrence and selective leaching of lithium in 2024年10月1日 Recycling the high content of valuable metal elements contained in spent lithiumion batteries (SLIBs) has attracted significant interest By leveraging the concept of substitution of isomorphous replacement in earth minerals, this study proposes a novel approach for the selective extraction of Li and Mn from the artificial spodumenetype lithiumrich slag Selective extraction of Li and Mn from spent lithiumion battery
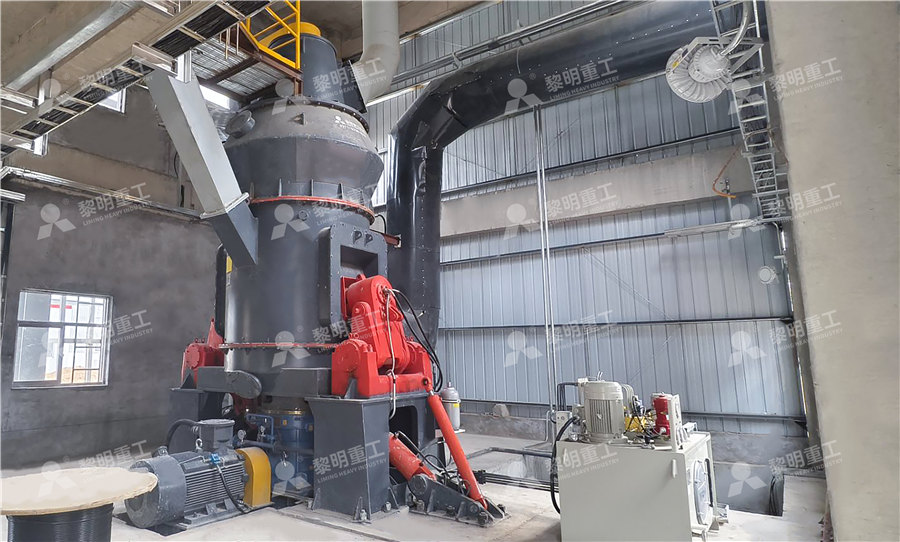
Lithium Ore Processing – an Overview of the Current and New
again to about 250°C to convert the spodumene into lithium sulfate and an aluminosilicate The mixture is water leached at about 50°C, dissolving about 98% of the lithium, and other impurities with the exception of the aluminosilicate The major ions present in the acidic solution are dependent upon2021年12月1日 In the third stage (July–November 2019), We first constructed a questionnaire (supplementary information) based on these indicators; then, we investigated the data from the 36 indicators from the following 16 orebased lithium extraction plants in China (Fig 2): Shehong Tianqi Lithium (ST), Huludao Hongjing Lithium (HH), Wudi Jinhaiwang Lithium (WJ), Pingxiang Sustainable production of lithium salts extraction from ores in 2018年12月20日 Lithium slag (LS) is a byproduct of lithium carbonate industry Based on sulfuric acid method, spodumene ore is firstly calcined at a high temperature of 1200 °C, and then processed with sulfuric acid method through roasting, leaching, washing and filtering processUtilization of lithium slag by wetgrinding process to improve 2019年10月15日 Lithium slag and fly ashbased binder for cemented fine Utilization of lithium slag by wetgrinding process to improve the early strength of Wang, 2014 WC Wang Effects of fly ash and lithium compounds on the watersoluble alkali and lithium content of cement specimens Constr Build Mater, 50 (2014), pp 727735 View Lithium slag and fly ashbased binder for cemented fine tailings
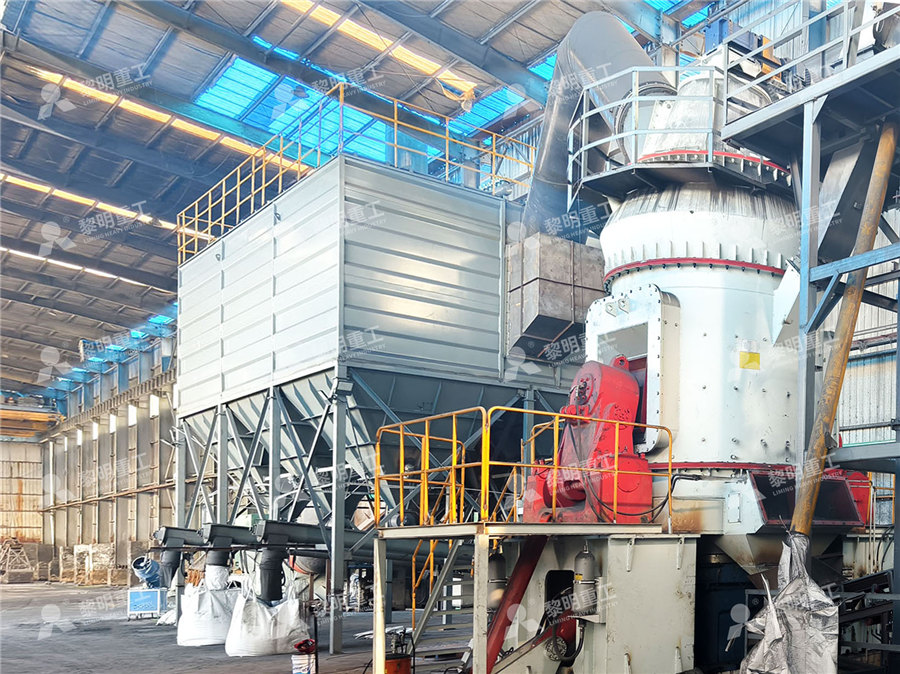
Preparation for microlithium slag via wet grinding and its
2019年12月1日 In this study, the fresh state and hydration properties of 0–60% lithium slag blended cement pastes were investigated at waterbinder ratio of 0472020年3月20日 Preparation for microlithium slag via wet grinding and its application as accelerator in Portland cement (spodumene ore) and the manufacturing process (Yiren et the speed of 400 rpm After separating the zirconia balls, microLS suspension was obtained It was noted that the water loss in grinding process was not Preparation for microlithium slag via wet grinding and its 2024年2月1日 The process flowsheet for the separation and recovery of lithium from overhaul slag via the H 2 SO 4 roastingwater leaching, which was shown in Fig 2 In this work, the roasting parameters studied includes roasting temperature, H 2 SO 4 dosage, and roasting time, to focus on the extraction of lithium, fluoride, and aluminumA novel approach for extracting lithium from overhaul slag by low 2023年12月27日 In step 1, to convert spodumene into lithium sulfate (Li 2 SO 4), the raw ore is crushed and separated both mechanically and via floatationNext, the concentrate undergoes energy and chemically intensive hot acidroasting This process (as shown in Figure 1 below) sees concentrated spodumene powder roasted at 1050°C, cooled, mixed with sulfuric acid, Hard Rock Spodumene Lithium Processing Saltworks Technologies
.jpg)
Aqueous leaching of lithium from simulated pyrometallurgical slag
In the pyrometallurgical treatment for spent lithiumion batteries (LIBs), lithium is generally present in slag with Al, Ca and Si and is hard to be further treated In this study, lithium was recovered from a simulated pyrometallurgical slag (pyroslag) via sodium roasting and water leaching The thermodynamic process2023年3月16日 When the content of lithium slag was 20 wt%, the softening coefficient of the specimen reached a maximum value, and the softening coefficients at 3, 7, and 14 days were 147, 191, and 151 times (PDF) Effect of MineralGenerated Lithium Slag on the Properties 2023年10月27日 The ball mill is a rotating cylindrical vessel with grinding media inside, which is responsible for breaking the ore particles Grinding media play an important role in the comminution of mineral ores in these mills This work reviews the application of balls in mineral processing as a function of the materials used to manufacture them and the mass loss, as A Review of the Grinding Media in Ball Mills for Mineral 2023年10月1日 In this study, lithium slag was utilised as a supplementary cementitious material (SCM) to develop pozzolanic activity and reduce CO 2 emissions related to cement production, with a focus on comprehensive chemical tests and microstructural assessments Lithium slag was primarily characterised through laser particle size analyser, Xray fluorescence, Xray Assessment of lithium slag as a supplementary cementitious
.jpg)
What is the Role of Water in Lithium Mining 911Metallurgist
2023年6月23日 Overexploitation of water for mining purposes can strain local ecosystems, deplete groundwater reserves, and threaten the livelihoods of communities dependent on agriculture and other waterintensive activities Sustainable Water Management in Lithium Mining: To mitigate the environmental impact of lithium mining and ensure the sustainable use 2024年9月15日 (4), (5), (6), lithium aluminate reacts with water to form lithium carbonate (Li 2 CO 3) and lithium aluminium carbonate hydroxide hydrate (Li 2 Al 4 (CO 3)(OH) 12 3H 2 O) Both recyclates can be identified by XRD analysis in all dissolved and subsequently recrystallized samples from the slag fine grinding tests (Fig 7)Fine grinding of pyrometallurgical battery slag and its influence Regarding reserves, the globally confirmed lithium resources have significantly increased, totaling approximately 98 million tons Bolivia boasts the highest reserves, accounting for 2157 % of the global total, followed closely by Argentina and Chile (Fig 1 d) [6]Among these, salt lake brine resources make up 723 % of the reserves, while ores account for 203 %, with nearly 50 % of Advances and promotion strategies of processes for extracting lithium 2024年6月13日 Sustainable harvesting of lithium is critical to the success of the entire battery industry Here, the authors report an electrochemical leaching method which can directly extract lithium from Direct extraction of lithium from ores by electrochemical leaching
.jpg)
Extraction of Lithium from Lepidolite Using Mixed Grinding with
2015年11月16日 Mixed grinding with Na2S followed by water leaching was performed to extract Li from lepidolite The leachability of Li increases dramatically in the ground mixture, regardless of the mixing ratio over the range of 1:1 to 3:1, while only 453% of Li was extracted in lepidolite ground without Na2S The leachability increased with an increase of the grinding time, and 2019年10月10日 Due to the increasing global demand of lithium, quartz and feldspar rich tailings ie quartzfeldspar sand (QFS) from lithium ore processing is likely to be more generated in near future For instance, Keliber Oy company is projecting to generate about 350 000 tons/year of quartz and feldspar rich tailings (QFS) in the near future [22]Recycling lithium mine tailings in the production of low The effective and lowtemperature extraction of lithium from the pyrometallurgical slag of spent lithiumion batteries (LIBs) remains a great challenge Herein, potassium carbonate/sodium carbonate (K2CO3/Na2CO3), which could form a eutectic molten salt system at 720°C, was used as a roasting agent to extract lithium from pyrometallurgical slag Lithium was successfully Extraction of lithium from the simulated pyrometallurgical slag of 2023年3月3日 Based on the pressure of environmental protection, more and more scientific researchers are trying to reuse aluminum–siliconrich industrial wastes In this study, activated lithiumslag and lead–zinc tailings were used as raw materials to prepare geopolymers at ratios of 3:7, 1:1, and 7:3 These geopolymers were initially cured for 12 h at 25 °C, 50 °C, 75 °C, and Solidification Experiment of LithiumSlag and FineTailings Based
.jpg)
Lithium processing technology Complete solutions that
Spodumene ores are typically consolidated from ore comprising 1–15% Li20 to a concentrate of about 6–65% Li20 To achieve this, the ore passes through a typical concentratortype plant, flowing from crushing and grinding, to gravity separation and DMS, to flotation, and then to the final dewatering of the concentrate2024年7月30日 Synergistic effects of the synthetic calcium silicate hydrates (CSH)/polycarboxylate (PCE) and Na2SO4 on hydration properties and microstructure of cementlithium slag (LS) composite binder were analyzed Results showed that CSHsPCE and Na2SO4 exhibited a synergistic effect on hydration acceleration of LScement binder Na2SO4 Impacts of CSHsPCE and Na2SO4 on hydration properties of lithium 2020年11月23日 A Combined Pyro and Hydrometallurgical Approach to Recycle Pyrolyzed LithiumIon Battery Black Mass Part 2: Lithium Recovery from Li Enriched Slag—Thermodynamic Study, Kinetic Study, and Dry (PDF) A Combined Pyro and Hydrometallurgical 2023年12月27日 This study critically reviews lithium slag (LS) as a supplementary cementitious material (SCM), thereby examining its physiochemical characteristics, mechanical properties, and durability within A Review on Cementitious and Geopolymer
.jpg)
Sustainable assessment and synergism of ceramic powder and steel slag
2024年2月14日 Solid waste management is a critical issue worldwide Effectively utilizing these solid waste resources presents a viable solution This study focuses on Iron ore tailings (IOTs), a solid waste generated during iron ore processing, which can be used as supplementary cementitious materials (SCMs) but have low reactivity, hindering their largescale application 2023年1月15日 Lithium production in China mainly depends on hard rock lithium ores, which has a defect in resources Extraction of lithium from lepidolite using chlorination roasting–water leaching process Transactions of Nonferrous Metals Society of China, 22(7), 1753–1759 doi: 101016/S10036326(11)613836 CrossRef Lithium extraction from hard rock lithium ores (spodumene, 2024年1月1日 Among them, the first two types of minerals are mainly composed of clay minerals, aluminous minerals, siliceous minerals, and a small amount of iron and titanium minerals The Jadar type lithium ore is composed of lithium and boron ore, and its components include Li 2 O, B 2 O 3, SiO 2 and Na 2 O(Benson et al, 2017; Brookfield et al, 2020)Efficient separation and extraction of lithium from lowgrade 2023年5月27日 The role of ball milling in lithium ore processing is to break down the lithiumcontaining minerals and release the lithium ions into the solution This is achieved through the mechanical grinding of the ore, which helps to increase the surface area of the material, making it easier for the leaching solution to penetrate and dissolve the lithium ionsBall Milling in Lithium Ore Processing: A Comprehensive Guide
.jpg)
Aqueous leaching of lithium from simulated pyrometallurgical slag
2019年8月1日 In the pyrometallurgical treatment for spent lithiumion batteries (LIBs), lithium is generally present in slag with Al, Ca and Si and is hard to be further treated In this study, lithium was recovered from a simulated pyrometallurgical slag (pyroslag) via sodium roasting and water leaching The thermodynamic pro Editors#39; Collection: Lithiumion batteries and beyond 2021年10月7日 In ores, the highest lithium concentrations are found in granitic pegmatites such as spodumene and petalite, with typical concentrations in the range of 12% Li 2(PDF) Lithium Mining, from Resource Exploration to Battery Grade 2023年3月28日 While lithiumion batteries are omnipresent, lithium recycling from endoflife batteries and production scrap remains costly and environmentally concerning Here, the authors report the Universal and efficient extraction of lithium for lithiumion 2024年10月28日 The escalating demand for lithium has intensified the need to process critical lithium ores into batterygrade materials efficiently This review paper overviews the transformation processes and cost of converting critical lithium ores, primarily spodumene and brine, into highpurity batterygrade precursors We systematically examine the study findings Transformations of Critical Lithium Ores to BatteryGrade MDPI