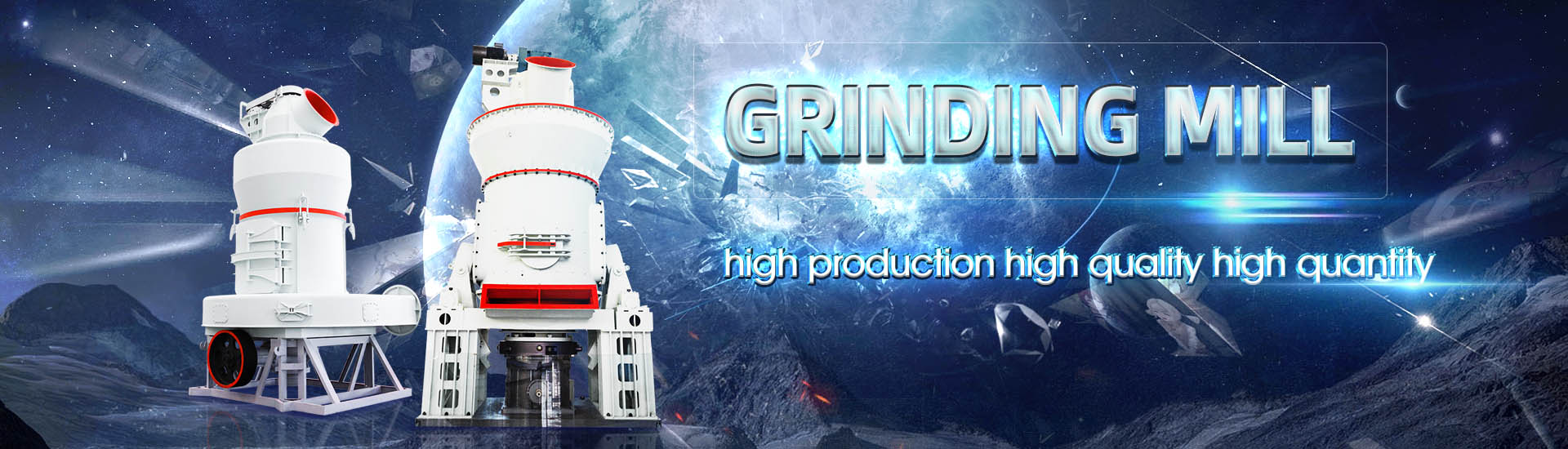
How to process silicon ore raw materials
.jpg)
Mining And Refining: Pure Silicon And The Incredible Effort
The raw material for most silicon production is the mineral quartzite Quartzite comes from ancient deposits of quartz sands that formed sedimentary deposits Over time and with heat and pressure, these quartz sandstones were transformed into the metamorphic rock quartzite, which is at least 80% quartz by volume 展开2024年9月7日 Silicon wafers are made through a process called Czochralski growth, where a silicon crystal is pulled from molten silicon and then sliced into thin wafers What are the key steps in silicon wafer fabrication?Silicon Wafer Manufacturing Process: Sand to SiliconRefining Raw Materials: From Ore to Pure Elements Once mined, the raw materials undergo refining processes to isolate the pure elements needed for semiconductor manufacturing Silicon, for instance, must be refined to a purity The Hidden Art of Mining and Refining Raw Materials Mineral quartz is 99 percent silicon, one of the most important raw materials of the 21st century Silicon is in every computer, mobile phone and, of course, in solar cells Trond BrendanVeisal is a geologistSilicon: mining and processing Britannica
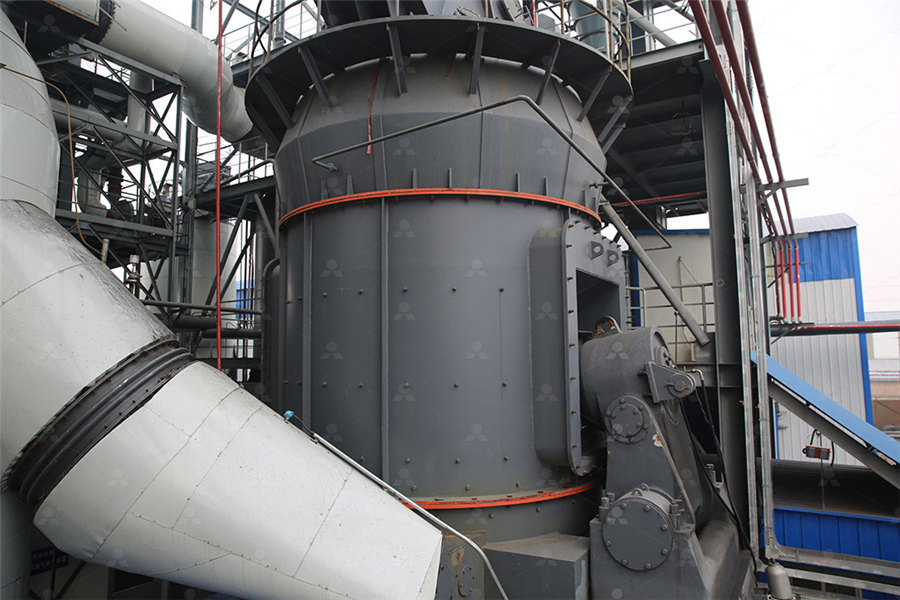
SILICON INGOT PRODUCTION PROCESS FOR WAFERS
As the basic raw material for the production of silicon wafers as substrates for microelectronic components, only monocrystalline silicon which is produced from polycrystalline silicon using 2018年9月21日 Any metal must be processed from its ore before employing it in various industrial applications; this is the similar case with Silicon (Si) as well Occurring in the form of Processing Methods of Silicon to its Ingot: a Review2019年6月1日 Any metal must be processed from its ore before employing it in various industrial applications; this is the similar case with Silicon (Si) as well Occurring in the form of silicates in theProcessing Methods of Silicon to its Ingot: a Review2023年3月21日 Silicon wafer processing refers to the manufacturing steps involved in producing highquality silicon wafers for use in semiconductor devices such as microprocessors, memory chips, and sensors The process involves Silicon Wafer Manufacturing: From Sand to Silicon
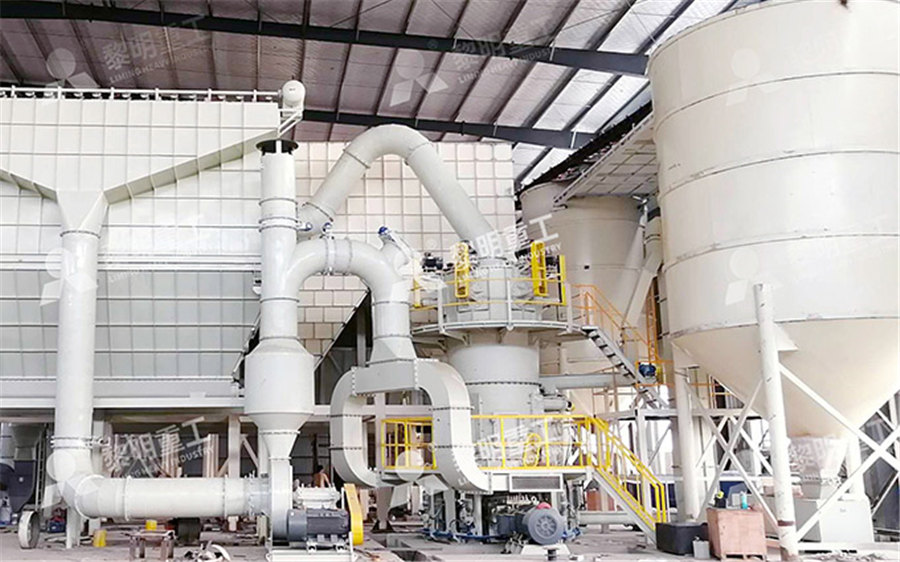
Refining Silicon PVEducation
While beach sand is also largely quartz, the most common raw material for electronic grade is high purity quartz rock Ideally the silica has low concentrations of iron, aluminum and other metals The silica is reduced 2022年10月7日 Through the Siemens process, highpurity polysilicon is obtained The next step is to use the Czochralski – CZ method to make monocrystalline (singlecrystal) silicon, which Manufacture of Silicon Wafer Wiley Online LibraryStage of Cement Manufacture There are six main stages of the cement manufacturing process Stage 1: Raw Material Extraction/Quarry The raw cement ingredients needed for cement production are limestone (calcium), sand and clay (silicon, aluminum, iron), shale, fly ash, mill scale, and bauxite The ore rocks are quarried and crushed into smaller pieces of about 6 inchesHow Cement is Made Cement Manufacturing Process2024年4月26日 The EAF process uses electricity to melt scrap steel and other raw materials, including iron ore, to produce steel 08 Conclusion Back Iron ore processing is a complex and vital process that transforms raw iron ore into Iron Ore Processing: From Extraction to Manufacturing

Towards sustainable extraction of technology materials through Nature
2021年9月21日 This section provides an overview of how technology materials get from a mine to being embedded in lowcarbon technology Production stages Moving elements from ore in the ground to the EV 2023年3月13日 The process of transforming raw materials into the sleek and durable stainless steel products we rely on is a fascinating journey we take you on a stepbystep guide through the manufacturing process, uncovering the secrets behind the creation of this versatile materialManufacturing Process From Ore To Stainless Steel: A Stepby 2024年11月4日 The raw materials: iron ore (hematite), coke (an impure form of carbon), and limestone are added into the top of the blast furnace Hot air is blown into the bottom Zone 1 Coke burns in the hot air forming carbon dioxide The reaction is exothermic so it gives off heat, heating the furnace carbon + oxygen → carbon dioxide Zone 2Extraction of iron IGCSE Chemistry Revision Notes Save My ExamsThe Tana quarry in Norway, near the North Cape here quartz is mined Mineral quartz is 99 percent silicon, one of the most important raw materials of the 21st century Silicon is in every computer, mobile phone and, of course, in solar cells Trond BrendanVeisal is a geologist He is searching for rock particularly free from impuritiesSilicon: mining and processing Britannica
.jpg)
How stainless steel is made material, manufacture, used,
To make stainless steel, the raw materials—iron ore, chromium, silicon, nickel, etc—are melted together in an electric furnace This step usually involves 8 to 12 hours of intense heat Next, the mixture is cast into one of several shapes, including blooms, billets, and slabsresources of silicon are virtually unlimited (although purity varies considerably) The main applications of silicon are as follows: deoxidation and alloying of steel and cast iron, alloying of aluminium, raw material in the chemical industry, and raw material in the semiconductor industry (electronic devices and photovoltaic cells)Silicon processing: from quartz to crystalline silicon solar cells2019年4月18日 Fortunately, there is no shortage of raw material Silicon is the second most common element in the earth’s crust, Purification starts by heating the sand with a reducing agent, carbon, to produce carbon monoxide and silicon The product of this process, known as metallurgical grade silicon (MGSi), may be as much as 99% pureFrom Sand To Wafers Semiconductor Engineering%PDF17 %âãÏÓ 1292 0 obj > endobj xref 1292 27 00000 n 00000 n 00000 n 00000 n 00000 n 00000 n 00000 n 00000 n 00000 n 00000 n 00000 n 00000 n 00000 n 00000 n Environmental impacts of extraction and processing of raw materials
.jpg)
Blast Furnace Process an overview ScienceDirect Topics
Blast furnace uses iron ore as the ironbearing raw materials, and coke and pulverized coal as reducing agents and heat source, lime, or limestone as the fluxing agents The main objective of blast furnace ironmaking is to produce hot metal with consistent quality for These sintering beds are used to compact the iron ore, limestone, and coke materials into a solid mass Loose materials are usually compacted into a solid mass as they are heated with burners The sintering process ensures that the iron ore, limestone, and coke materials are mixed evenlyLesson Explainer: Extracting Iron NagwaRaw Material: Gold Ore Gold ore serves as the vital raw material that forms the basis of the entire gold refinery process, leading to the production of pure gold Its significance lies in being the primary source from which gold is extracted and Gold Refinery Process: From Raw Material to Pure Gold2024年3月26日 Polycrystalline silicon, also known as polysilicon or multicrystalline silicon, is a vital raw material used in the solar photovoltaic and electronics industries As the demand for renewable energy and advanced electronic devices continues to grow, understanding the polysilicon manufacturing process is crucial for appreciating the properties, cost, and Understanding the Polycrystalline Silicon Manufacturing Process
.jpg)
How is Silicone Produced? A StepbyStep Guide to Silicone
2023年10月20日 Next, let’s take a look at how raw silicone is synthesized on an industrial scale Silicone Manufacturing Process There are two main ways silicone can be synthesized: Direct process; Polymerization process; Direct Process for Silicone Manufacturing The direct process reacts silicon with methyl chloride in the presence of a copper catalyst2020年1月31日 Raw Materials Stainless steel metal is formed when the raw materials of nickel, iron ore, chromium, silicon, molybdenum, and others, are melted together Stainless steel metal contains a variety of basic chemical elements that, when fused together, create a powerful alloyHow is Stainless Steel Made?Ferrosilicon is an alloy of iron and silicon, typically containing between 15% and 90% silicon It is produced by reducing iron oxide and silica in an electric arc furnace The process involves the following steps: 1 Raw materials preparation: Iron ore and silica are crushed and sized to a suitable size for use in the furnace 2Ferrosilicon Production ProcessRaw material: Contains: Function: Iron ore (haematite) Iron(III) oxide (Fe 2 O 3): A compound that the iron is extracted from: Coke: Carbon (C) Used as a fuel and reacts to form carbon monoxide Redox, extraction of iron and transition metals Extracting iron
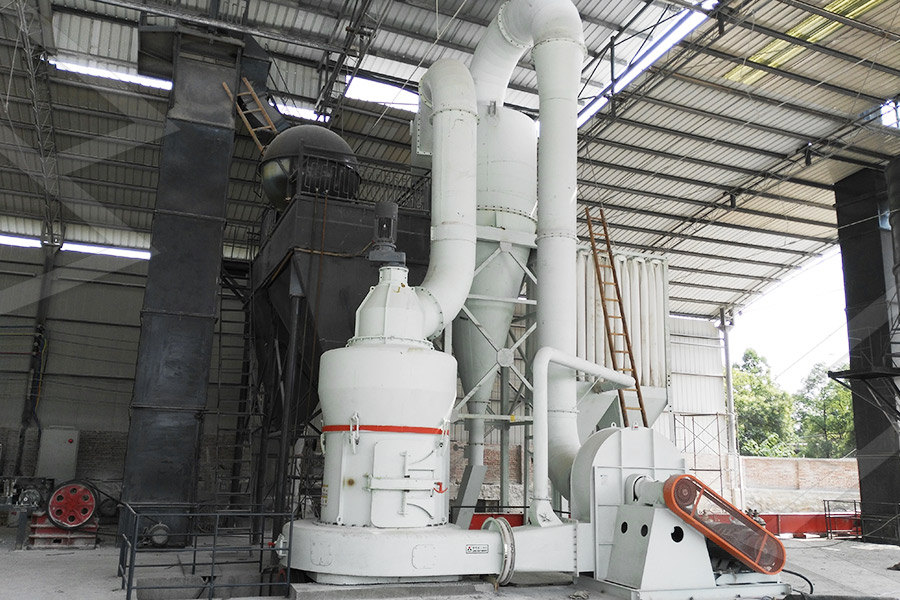
Pig Iron Manufacturing Process 911Metallurgist
2017年3月20日 In the latest report of the engineers at Trollhattan, it is stated that the power consumption per ton of pig iron varies in proportion to the iron content of the ore A poor ore and pig iron high in silicon and manganese require more power than a rich ore and pig iron low in silicon and manganese This was also found to be the case in California2022年6月15日 The production process of highpurity quartz requires ore deposit raw materials with high grade, which are usually pegmatite quartz and hydrothermal vein quartz (Platias et al, 2013, Zhang and Chen, 2010a)At present, the global distribution of highpurity quartz raw material deposits is extremely scarce (Larsen et al, 2000)In addition to China, 14 deposits Resource, characteristic, purification and application of quartz: a the relative amounts of manganese ores and HCFeMn slag in the raw material mix A process temperature of 1600 to 1650°C is necessary to obtain metal with sufficiently high content of Si and discard slag with low MnO FeMn slag has a relatively low melting temperature (about 1250°C) compared with MnoresSilicomanganese Production Process UnderstandingThe impurity levels in metallurgical grade silicon5 vary widely due to process variation and the source raw materials of silica and carbon Electronic Grade Silicon A small amount of the metallurgical grade silicon is further refined for Refining Silicon PVEducation
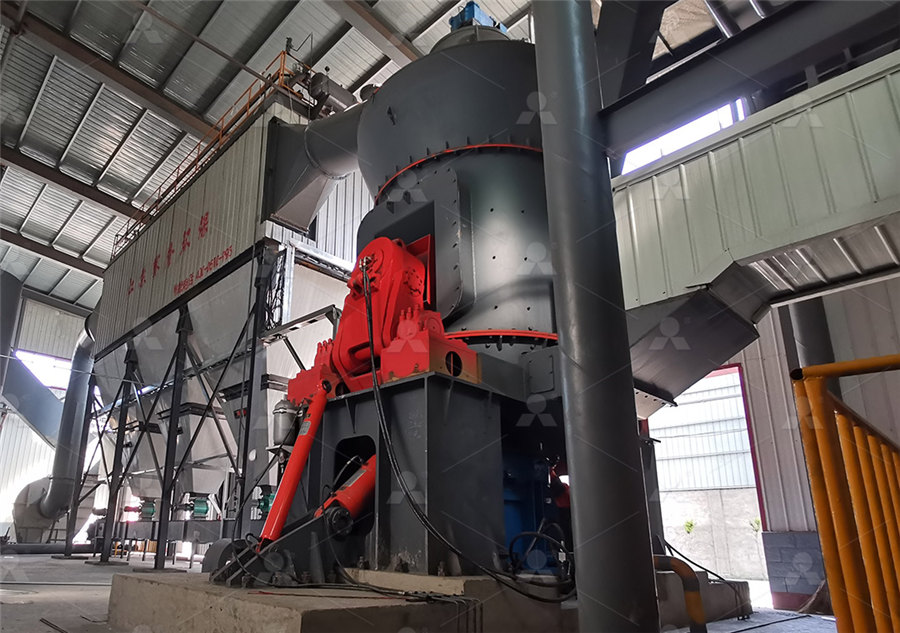
Production of FerroSilicon IspatGuru
2018年6月27日 Production of FerroSilicon satyendra; June 27, 2018; in the presence of iron ore, scrap iron, mill scale, or other source of iron The smelting of FeSi is a continuous process carried out in the electric submerged arc Manufacturing of Raw Silicon Manufacturing Process The first step is to remove oxygen from quartz because it reacts quickly with silicon, even at room temperature, and is present as silicon dioxide (SiO2) This is carried out in furnaces using carbon at temperatures just above silicon's melting point (1414 °C)How Is Raw Silicon Processed and Manufactured?2022年12月11日 Silicone is a highly versatile synthetic material used in a vast range of applications throughout multiple industriesSilicone can be found in the products we use in our daily lives, from the cars we drive, food preparation and storage products, baby bottles and pacifiers, and dental and other daily personal hygiene productsSilicone is also widely used in Silicone: A Guide to Production, Uses and Benefits SIMTECIron ore isn't pure iron oxide – it also contains an assortment of rocky material This wouldn't melt at the temperature of the furnace, and would eventually clog it up The limestone is added to convert this into slag which melts and runs to the bottom The heat of the furnace decomposes the limestone to give calcium oxideIron Extraction and Purification / Steel ChemKey
.jpg)
Iron Ore Sintering: Raw Materials and Granulation ResearchGate
2016年10月28日 Sintering is an agglomeration process that fuses iron ore fines, fluxes, recycled products, slagforming elements and coke The purpose of sintering is to obtain a product with suitable Extraction of raw materials (largely crude oil and natural gas, but also coal) – these are a complex mixture of thousands of compounds that then need to be processed 2 Refining process transforms crude oil into different petroleum products – these are converted to yield useful chemicals including “monomers” (a molecule that is the basic building blocks of polymers)How Is Plastic Made? A Simple StepByStep ExplanationThen, the ore is combined with coal or coke, which removes the impurities and other minerals, making the elementary Iron ready for steel production However, lately, recycled steel has been used more, contributing to sustainable practices by reducing the need for raw materials and energy The Blast Furnace Process ExplainedExploring the Steelmaking Process: From Ore to AlloySteelmaking process can generally be classified into four main different routes including blast furnace/basic oxygen furnace (BFBOF), direct reduction/electric arc furnace (DRIEAF), smelting reduction/basic oxygen furnace (SRBOF) and melting of scarp in electric arc furnace (EAF) Fig 1 shows the various steel production routes from the raw materials to the crude steel Steelmaking Process an overview ScienceDirect Topics
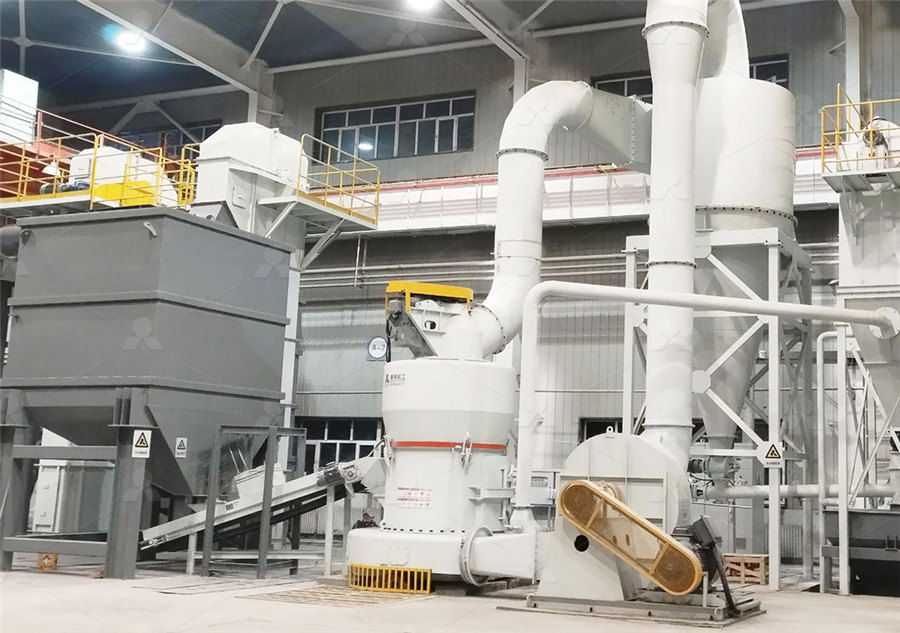
Critical raw materials act Consilium
2024年9月12日 1 Why the need for an EU critical raw materials act? The EU’s demand for base metals, battery materials, rare earths and more are set to increase exponentially as the EU divests from fossil fuels and turns to clean energy systems which necessitate more minerals The EU green transition will require the buildup of local production of batteries, solar panels, Raw Materials Titanium is obtained from various ores that occur naturally on the earth The primary ores used for titanium production include ilmenite, leucoxene, and rutile Other notable sources include anatase, perovskite, and sphene Ilmenite and leucoxene are titaniferous oresHow titanium is made material, manufacture, making, history, 2022年1月23日 Chemical Processing of Bauxite: Alumina and Silica Minerals—Chemistry, Kinetics and Reactor Design(PDF) Chemical Processing of Bauxite: Alumina and Silica Minerals manganese processing, preparation of the ore for use in various products Manganese (Mn) is a hard, silvery white metal with a melting point of 1,244 °C (2,271 °F) Ordinarily too brittle to be of structural value itself, it is an essential agent in steelmaking, in which it removes impurities such as sulfur and oxygen and adds important physical properties to the metalManganese processing Extraction, Uses Benefits Britannica
.jpg)
ferro silicon all you need to know about it
2023年11月23日 1 Selection Raw Materials Silica (Silicon Dioxide): Typically sourced from quartz or sand Iron Ore: Provides the iron component, often in the form of iron oxides like hematite or magnetite Carbon: typically in coke or coal form and acts as a reducing agent to remove oxygen from the iron ore 2 Preparation of Raw Materials The raw 2022年1月10日 The required pace of transition means that the availability of certain raw materials will need to be scaled up within a relatively short time scale—and, in certain cases, at volumes ten times or more than the current market size—to prevent shortages and keep newtechnology costs competitive (see sidebar “Rareearth metals”)The rawmaterials challenge: How the metals and mining sector Melted Silicon – scale: wafer level (~300mm / 12 inch) Silicon is purified in multiple steps to finally reach semiconductor manufacturing quality which is called Electronic Grade Silicon Electronic Grade Silicon may only have one alien atom every one billion Silicon atoms In this picture you can see how one big crystal is grown from theFrom Sand to Silicon IntelThe raw materials for the acid process are of a siliceous nature, but low in sulfur and phosphorus The maintenance of an acid slag prevents the elimination of these elements The pig iron and scrap are charged, and when melted the slag is rendered fluid and oxidized by ironore additions The carbon, silicon, How is Steel Made? Steel Production Process – What Is Piping
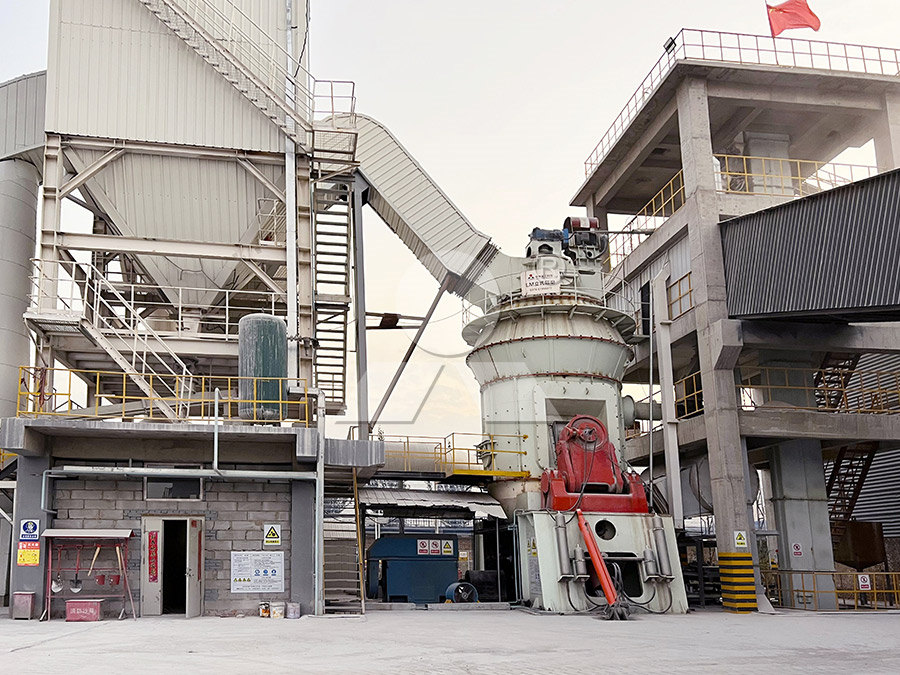
Using LateriteNickel Ore as Raw Material, Study on the Efficient
2023年12月11日 In this study, the laterite nickel ore was treated by basic hydrothermal method, and the product was dissolved directly in the form of sodium silicate Pure SiO2 was obtained by carbonizing sodium silicate solution The effects of various conditions on silicon extraction rate were studied by single factor experiment The optimum conditions of silicon leaching were as While each cement plant may differ in layout, equipment, and appearance, the general process of manufacturing portland cement is the same: crushed limestone and sand are mixed with ground clay, shale, iron ore, fly ash and alternative raw materials Some manufacturers grind the raw materials dry, while others use a wetgrinding process How Cement is Made Portland Cement Association