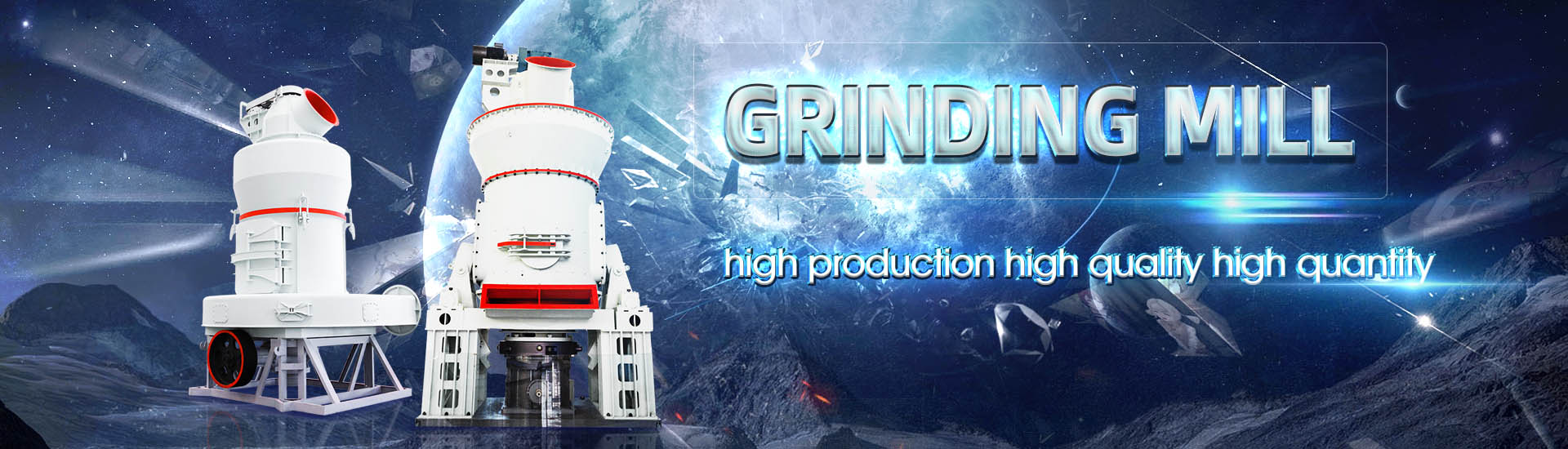
Limestone desulfurization dosage price, end of the year
.jpg)
FLUE GAS DESULPHURIZATION Centre for Science and
A 500 MW plant will require about 32,000–40,000 tonnes of limestone annually, costing around three to four crore rupees with an impact of less than one paisa per unit of electricity2021年5月21日 At present, finegrained limestone sorbents, often called limestone flour, with grain size under 100/120 μm are used in the Polish power industry as a sorbent for flue gas desulphurisation in the wet limestone Limestone Sorbents Market for Flue Gas For circulating fluidized bed technology, desulfurization by adding limestone to the furnace is a lowcost and simple strategy, and its efficiency is almost comparable to that of traditional Recent advances in process and materials for dry desulfurization of 2021年7月15日 Comparison of the production volume of synthetic gypsum and consumption of limestone sorbents applied in flue gas desulphurisation in wet method (surveyed gypsum (PDF) Limestone Sorbents Market for Flue Gas ResearchGate
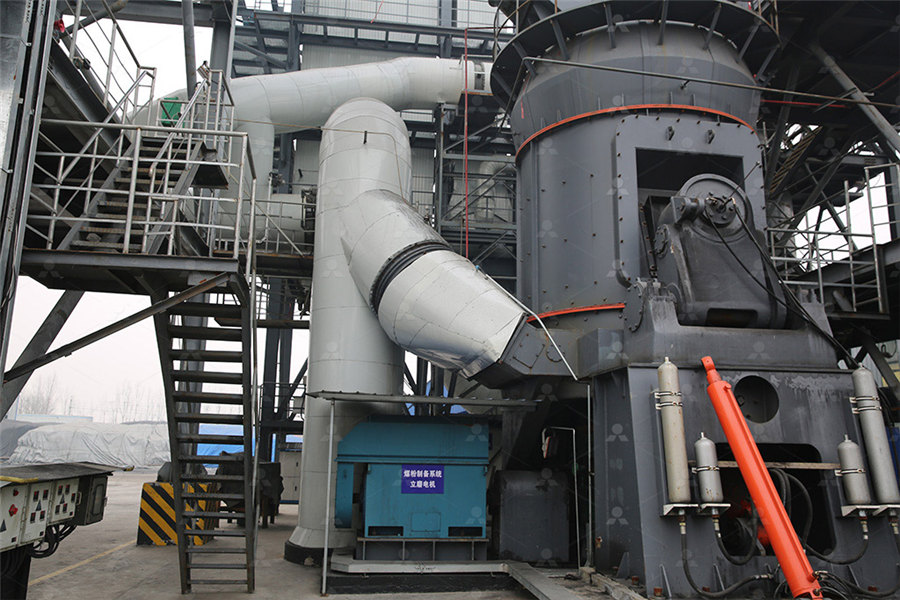
Model of the Wet Limestone Flue Gas Desulfurization Process for
2001年5月19日 A detailed process model of the wet limestone flue gas desulfurization system has been presented This model can be used to calculate indispensable parameters for 2001年5月19日 A detailed process model of the wet limestone flue gas desulfurization system has been presented This model can be used to calculate indispensable parameters for Model of the Wet Limestone Flue Gas Desulfurization Process for 2015年3月15日 According to the chemistry of the wet limestone desulphurisation process, in wet limestone FGD system with forced oxidation (Fig 1), limestone slurry is prepared in a closed Status of Flue Gas Desulphurisation (FGD) systems from coalfired In most developed countries, wet scrubber (fluegas desulfurization; FGD) technology is a wellestablished process for removing SO2 Also, costs have been reduced significantly from 150 Wet Flue Gas Desulfurization (FGD) ARCOR Epoxy
.jpg)
Lime / Limestone Wet Scrubbing System for Flue Gas Desulfurization
Wet scrubbers are used in utilities, paper mills, and chemical plants to remove sulfur dioxide (SO 2) and other pollutants from gas streams Undesirable pollutants are removed by contacting 2020年8月15日 The representativeness and completeness scores of the dosage and desulfurization cost were 1 and 2, respectively, because the overall scale of each enterprise Comprehensive evaluation of flue gas desulfurization and Currently, desulfurization technologies can be categorized into three main types: wet flue gas desulfurization (FGD) [11], [12], [13], semidry desulfurization [14] and dry desulfurization [15]Wet flue gas desulfurization is widely employed in largescale desulfurization processes due to its high efficiency and low energy consumption [16]However, it poses a significant environmental Recent advances in process and materials for dry desulfurization 2022年12月1日 As limestone desulfurization can release CO2, when limestone desulfurization was replaced with steel slag of equal desulfurization ratio, CO2 emissions could be reduced by 2796 kg and limestone Desulfurization characteristics of limestone slurry with
.jpg)
Applications of Ultrafine Limestone Sorbents for the Desulfurization
2019年10月29日 Presently, the most widely used technology for flue gas desulfurization is the limestone/limegypsum wet desulfurization process, which accounts for more than 90% of the thermal power market (Liu 2000年10月1日 As limestone desulfurization can release CO2, when limestone desulfurization was replaced with steel slag of equal desulfurization ratio, CO2 emissions could be reduced by 2796 kg and limestone Use of Limestone for SO2 Removal from Flue Gas in the Semi Analysis of limestone for flue gas desulfurization in a power plant ARL OPTIM’X SimultaneousSequential Wavelength Dispersive Xray Fluorescence Spectrometer Xray fluorescence aircooled Rh end window tube with thin Be window (0075 mm) and has a Analysis of limestone for flue gas desulfurization in a power plantLimestone Market Size and Share: The global limestone market size was valued at USD 856 Billion in 2024Looking forward, IMARC Group estimates the market to reach USD 1207 Billion by 2033, exhibiting a CAGR of 374% during 20252033Asia Pacific currently dominates the market, holding a significant market share of over 560% in 2024Limestone Market Size, Share, Price and Industry Outlook 2033
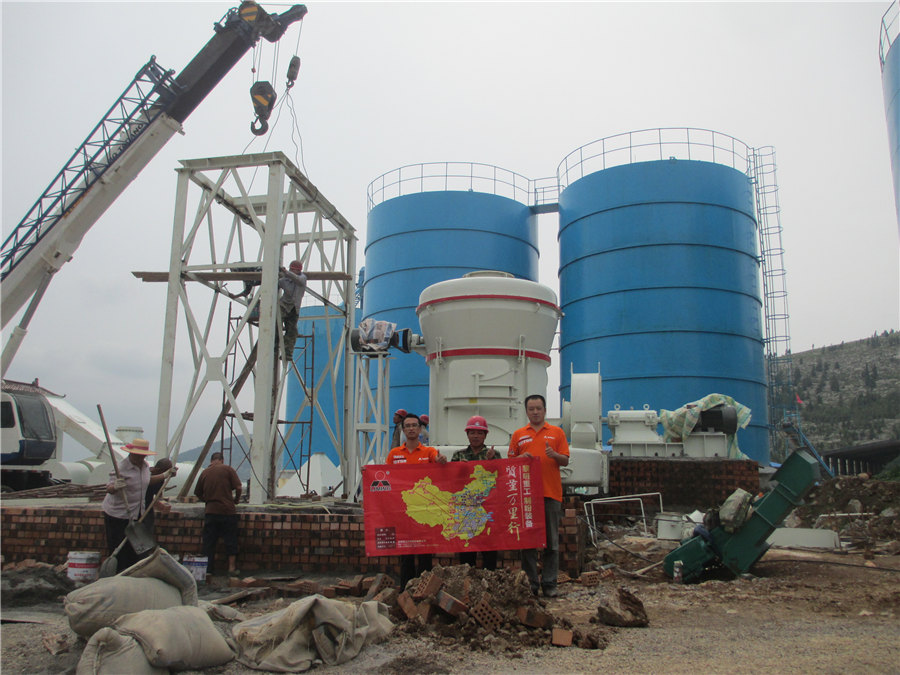
(PDF) Enrichment of Limestone Used in the ResearchGate
2021年11月30日 Laboratory research of the reactivity of limestone used for desulfurization of coal fluidized bed boilers have shown that reactivity of CaO after limestone calcination process in boiler is 2014年8月1日 The oxidation of calcium sulfite in the citric acidenhanced limestone flue gas desulfurization was studied in the bubbling reactor The oxidation rate of calcium sulfite is restrained by citric acidFeatures of Use of Limestone and Lime in Wet ResearchGateKnowing that approximately 87% of anthropogenic atmospheric sulfur oxides (SO 2 and sulfur trioxideSO 3 ) are emitted from fossil fuelfired plants [7], these emissions are the main targetFlow diagram of the limestone scrubbing methodKeywords: Desulfurization, Flue gas, Limestone, Process optimization Received: October 13, 2006; revised: December 4, 2006; accepted:December 6, 2006 DOI: 101002/ceat 1 Introduction and Scope The wet limestone (calcite) flue gas desulfurization (FGD) process for stationary sources represents over 90 % of installed desulfurization capacities in the world and Technology Optimization of Wet Flue Gas Desulfurization Process
.jpg)
Optimum Values of Process Parameters of the “Wet Limestone
2002年4月1日 In this article the method of cost optimization of the “Wet Limestone Flue Gas Desulfurization System” is presented The optimization calculations include process and cost models2020年8月1日 Incineration of sludge can be an effective method to minimise waste whilst producing useful heat However, incineration can cause secondary pollution issues due to the emission of SO 2, therefore a set of experiments of sludge incineration in a bubble bed furnace were conducted with limestone addition to study desulfurization of sludge incineration flue gasDesulfurization using limestone during sludge incineration in This article discusses the analysis of limestone for flue gas desulfurization in a power plant using an EDXRF spectrometer It is equipped with an aircooled Rh endwindow tube with a slender Be window (005 mm) 5 EVIDENT Determination of Flue Gas Desulfurization by Various flue gas desulfurization processes—physicochemical, biological, and chemobiological—for the reduction of emission of SO 2 with recovery of an economic byproduct have been reviewedSchematics of limestoneforced oxidation process (LSFO)
.jpg)
Application and Development Trend of Flue Gas Desulfurization
Typical FGD Technologies in China Desulfurization process Sodium sulphite process Phosphorous ammonia fertilizer process Basic aluminium sulfate process Managanses dioxide process Phosphate ore desulfurization process Venturi desulfurization process Rotary spray drying process Limestone injection into the furnace and activation of calcium process 2022年7月14日 The carbide slag has the advantages of wide sources, low price, and similar active ingredients with limestone, so that the carbide slag can be used for replacing the traditional limestone desulfurization to reduce the desulfurization cost and solve the problem of a large amount of carbide slag stacking; and meanwhile, the carbide slag can also capture CO 2 Desulphurization mechanism and engineering practice of carbide 2001年5月19日 Wet Flue Gas Desulfurization (WFGD) unit based upon spray scrubber has been widely employed to control SO2 emissions from flue gas in coalfired power plantModel of the Wet Limestone Flue Gas Desulfurization2015年3月15日 Depending on the SO 2 concentrations and the excess air in the flue gas, as well as on the pH of limestone slurry, some systems may be operated in the natural oxidation mode However, for most applications it is beneficial to control oxidation [10]In natural oxidation mode, the main product is a mixture 50–60% of CaSO 3 ⋅½ H 2 O and CaSO 4 ⋅2H 2 O in a Status of Flue Gas Desulphurisation (FGD) systems from coal
.jpg)
Model Predictive Control of a Wet Limestone Flue Gas Desulfurization
2009年5月27日 In order to meet the emission standard and reduce the cost of WFGD system, there are some works devote to improve the performance of WFGD by technology optimization (Carletti et al 2017;Hrastel Evaluation of Limestone Impurities in the Desulfurization Process of Coal Combustion Gas 265 Brazilian Journal of Chemical Engineering Vol 34, No 01, pp 263 272, January March, 2017EVALUATION OF LIMESTONE IMPURITIES IN THE DESULFURIZATION 2021年12月1日 From the analysis above, it can be deduced that the desulfurization process by using lowgrade limestone as SO 2 absorbent is divided into three stages: (1) SO 2 dissolves into LGL slurry firstly followed by the formation of SO 3 2−, HSO 3 − and H 2 SO 3 species [21]; (2) continuous dissolution of Cabased compound including CaCO 3 and CaMg Insights into the desulfurization mechanism of lowgrade limestone 2010年5月11日 Request PDF Limestone dissolution in flue gas desulfurization Experimental and numerical study BACKGROUND: Wet FGD technologies account for around 87% of such systems worldwide, particularly Limestone dissolution in flue gas desulfurization ResearchGate
.jpg)
Desulphurization mechanism and engineering practice of carbide
The commonly used wet desulfurizer is limestone, which is expensive (Xu et al 2019) The carbide slag has the advantages of wide sources, low price, and similar active ingredients with limestone, so that the carbide slag can be used for replacing the traditional limestone desulfurization to reduce2015年3月1日 Wet fluegas desulfurization (WFGD), which involves the limestoneand ammoniascrubbing methods, has been extensively used in the industry because of its high SO 2 removal efficiency and Status of Flue Gas Desulphurisation (FGD) systems fromThe Limestone Emission Control (LEC) process is the basis for computer simu lation and optimization considered in this study The process is shown in Figure 101 and described in detail by Prudich et al [1] The process uses coarse wet limestone particles (approximately oneeighth inch in diameter) as the sorbent inSIMULATION AND OPTIMIZATION OF A GRANULAR LIMESTONE 2017年1月11日 In the first channel (1 m long), 26 kg of limestone (granulometry 510 mm) were used at two different flow rates: 25 ml/min and 50 ml/min At the end of each of the drains caps fitted with (PDF) THE EFFICIENCY OF LIMESTONE IN NEUTRALIZING ACID MINE
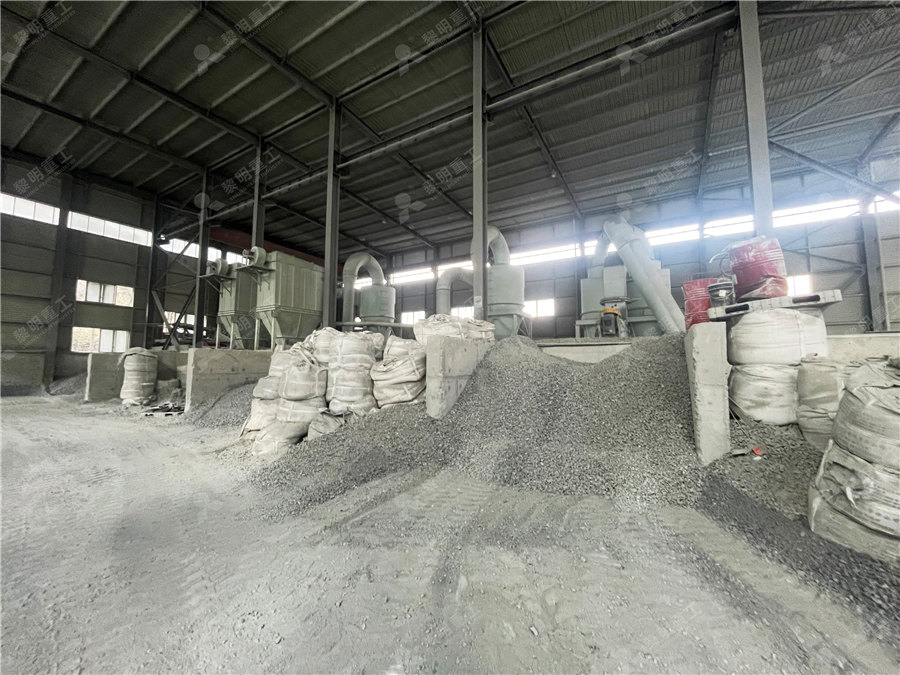
(PDF) Improving the desulfurization performance of CaCO 3
2018年2月1日 Wet fluegas desulfurization (WFGD), which involves the limestoneand ammoniascrubbing methods, has been extensively used in the industry because of its high SO 2 removal efficiency and 2019年6月1日 The paper presents data concerning the influence of ammonia on wet flue gas desulfurization (WFGD) absorber Paper presents preliminary results of an industrial scale study on WFGD absorber, that collects flue gases from four boilers with total flue gas flow capacity of the WFGD equal to 1 500 000 Nm3/h Each boiler is equipped with selective noncatalytic [PDF] Influence of ammonia on wetlimestone flue gas desulfurization prepared by first crushing the limestone into a fine powder using a ball mill and then mixing the powder with water in the slurry preparation tank Particle size of the limestone impacts the efficiency of SO2 removal In the typical wet limestone FGD system, the limestone is ground to an average size of 5 to 20 μm The sorbent slurryA review wet flue gas desulfurization by the use of limestone2017年1月17日 ABSTRACT In this article, the influence of temperature, stirring speed, limestone type, particle size, and desulfurization additives on the limestone dissolution rate was investigated The dissolution reaction was modeled by shrinkingcore model As the temperature increases, the dissolution reaction rate increased rapidly, and the activation energy was 2576 Effect of additives on limestone reactivity in flue gas desulfurization
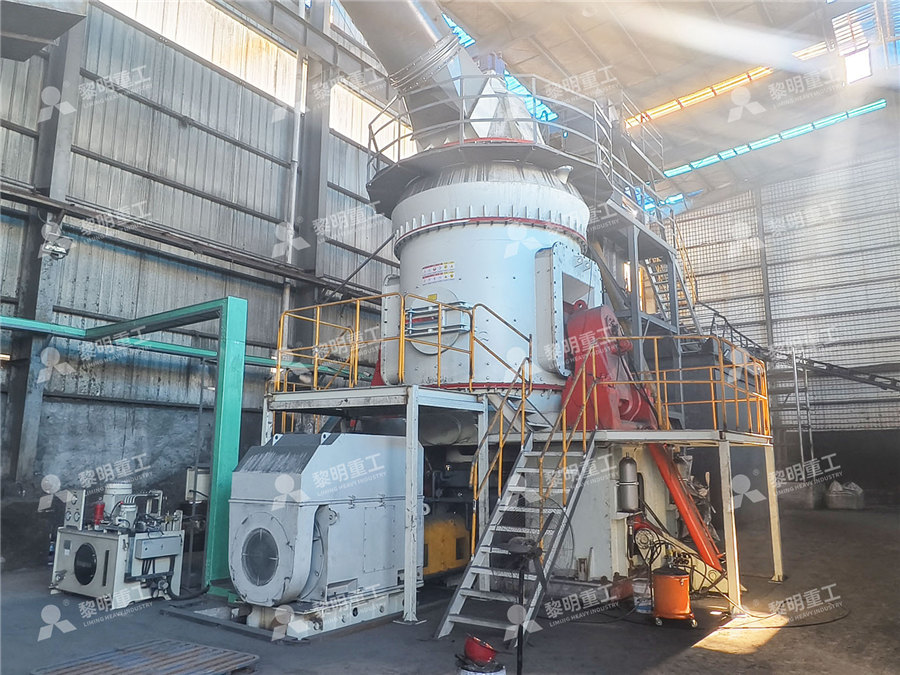
Experimental Study and Mechanism Analysis of Modified Limestone
2012年1月1日 In 2009, China’s coal consumption was 302 billion tons, in which over 50% was consumed for power generation By the end of 2009, total installed capacity of coalfired power units was 601,320 MWe, As can be seen in Fig 4, red mud can improve the limestone’s desulfurization performance in the whole temperature range should be optimized with enhanced endofpipe control technologies to achieve deep reduction of air pollutants Keywords Fine particulate matter (PM 25) Watersoluble ions Flue gas Desulfurization Denitrification Technology evaluation Uncertainanalysis Introduction Since the “Eleventh FiveYear Plan” period, the constructionComprehensive evaluation of flue gas desulfurization and 2021年2月1日 After one year of operation, the technology is reliable and stable The removal rate of suspended matter, COD, fluoride, the effluent quality of the system is better than the discharge requirements of "Discharge standard of wastewater from limestonegypsum flue gas desulfurization system in fossil fuel power plants" (DL/T9972006)LimestoneGypsum Wet Flue Gas Desulfurization Wastewater 2016年1月20日 Ma et al (2016) used O 3 combined with limestonegypsum washing system for desulfurization and denitration in industrial carbon black furnace (100,000 ton/year)Characteristics of O3 Oxidation for Simultaneous Desulfurization
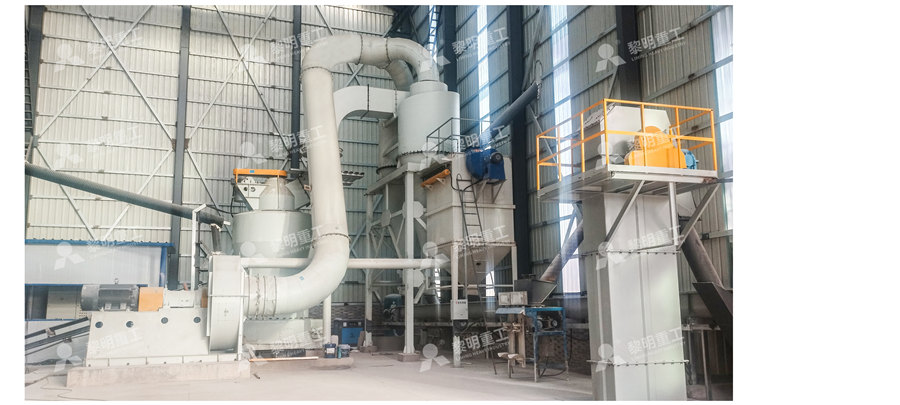
Production and resource utilization of flue gas ResearchGate
2021年7月1日 FGD (FlueGas Desulfurization) gypsum waste is a industrial waste of the process of reducing SOx discharged in the combustion chamber of a coalfired power plant by a lime mixture or limestone powderWet FGD system using limestone as the sorbent Most wet FGD systems use a limestone sorbent that is prepared by first crushing the limestone into a fine powder using a ball mill and then mixing the powder with water in the slurry preparation tank Particle size of the limestone impacts the efficiency of SO2 removal In theA review wet flue gas desulfurization by the use of limestone2013年10月1日 Limestone slurries are widely utilized in wet flue gas desulfurization (WFGD) processes The evaluation of the reagent's reactivity is fundamental for process design and plant operationModeling Limestone Reactivity and Sizing the Dissolution 2021年12月1日 Utilization of lowgrade limestone (LGL) in wet flue gas desulfurization (WFGD) has been considered as a promising technology due to the decrease in lInsights into the desulfurization mechanism of lowgrade limestone
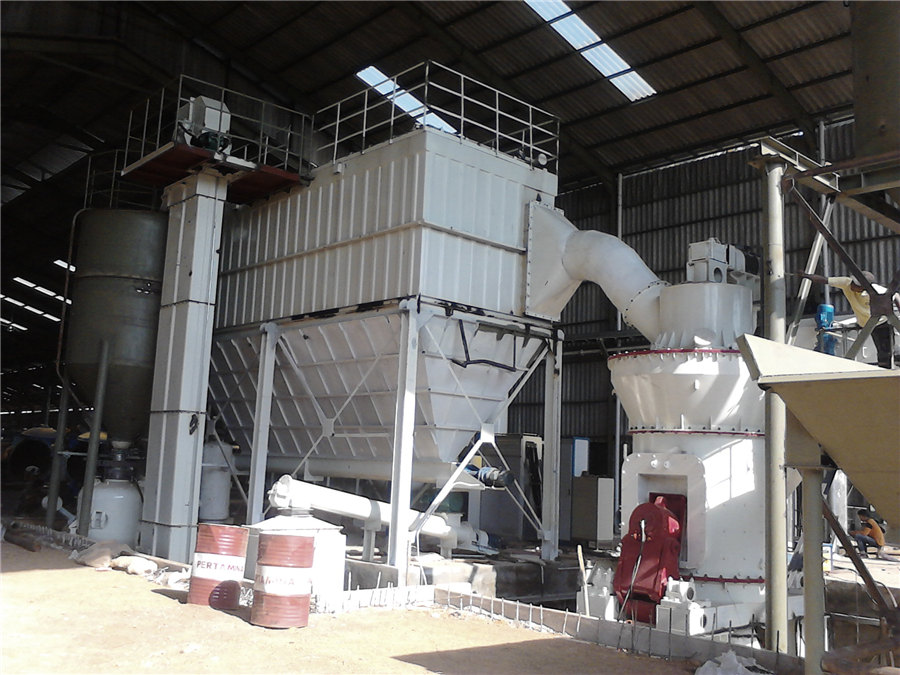
Insights to the oxidative desulfurization process of fossil fuels
According to the environmental constraints and stringent environmental regulations, the high efficiency sulfur removal processes have been considered in oil refinery industries (Babich and Moulijn 2003; Ismagilov et al 2011; Song 2003; Wang and Yang 2018)Desulfurization processes can be classified into two main groups “hydrodesulfurization based” and “nonhydrogen 2002年1月1日 Flue Gas Desulfurization: The State of the Art [J] January 2002; 51(12):167688; and specifically wet limestone FGD, have been predominantly selected over the FGD technologiesFlue Gas Desulfurization: The State of the Art [J] ResearchGate