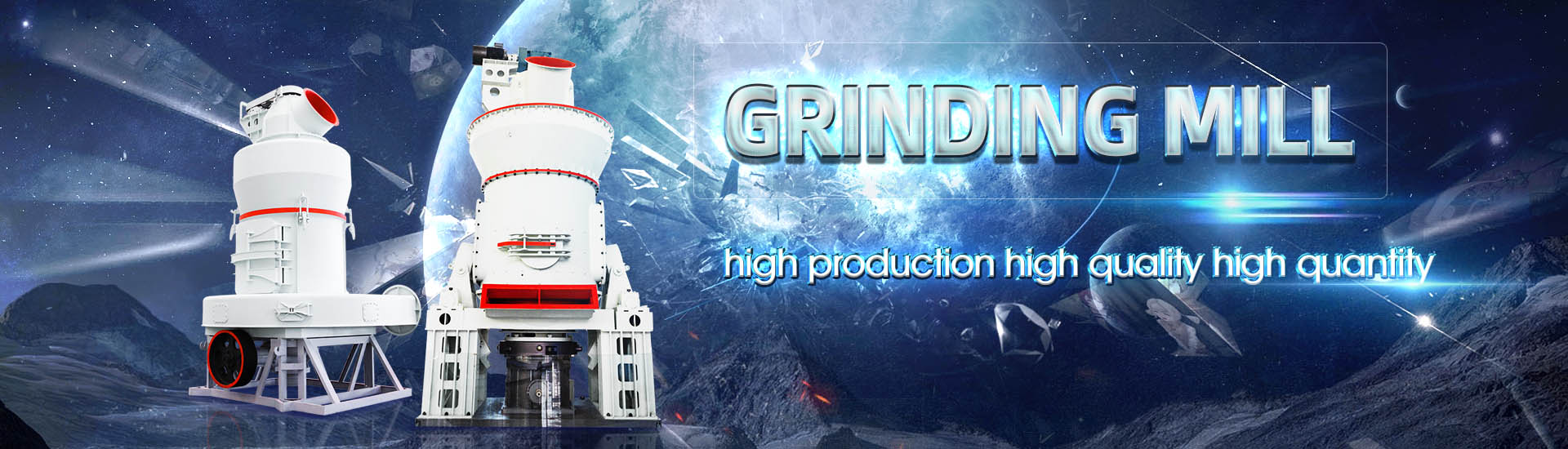
Sponge iron oxide powder grinding equipment
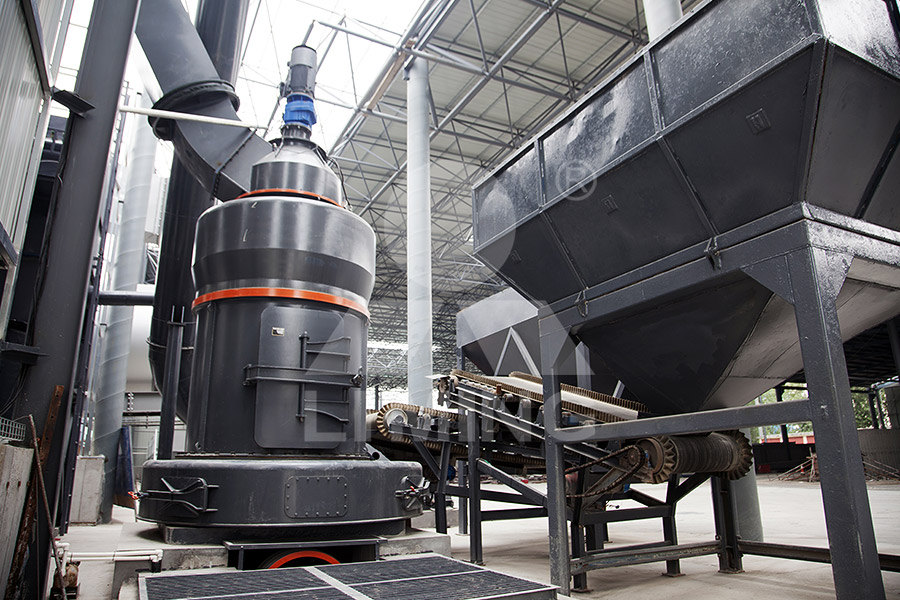
Sponge iron powder grinding machine
2024年10月16日 Find sponge iron powder grinding machine types and parts from wholesalers in China Shop for grinding equipment and parts at Alibaba and find a variety at competitive Micronization enhances color, texture, and surface area of iron oxides Jet Pulverizer has milled FeO2 for decades, for a variety of industries—our data can help you plan your next project Jet Iron Oxide Micronization : Jet Pulverizer2023年4月3日 In this work, a novel processing route was proposed for manufacturing iron particles using iron oxide powder as a raw material This iron oxide powder is a byproduct of Manufacturing and Properties of Spherical Iron Particles from a by Reduced Iron Powder is a spongelike ironbased product obtained by reducing iron oxide Various functions of 'DOWA Reduced Iron Powder' are used in many applications We have Reduced Iron Powder DOWA ELECTRONICS MATERIALS CO, LTD
.jpg)
Iron Manufacturing process related to the specified manufacture(s)
Sponge iron powder The Höganäs process is a direct reduction method for production of sponge iron powder using magnetite ore (Fe3O4) and carbon as raw materials The reduction process DRI, also known as sponge iron, is the product of reducing iron oxide in the form of iron ore and steel plant wastes into metallic iron, below the melting point of iron and typically in the range of Sponge Iron an overview ScienceDirect Topics2023年10月9日 Highly metallized direct reduction iron is produced through tunnel kiln direct reduction (vessel) process by using highgrade iron ore as raw material and coke powder as Direct Reduction Ironmaking SpringerLinkThe reduction of rolling mill scale to sponge iron powder is a new way to take advantage of a cheap byproduct of the steelmaking industry, yielding sponge iron that can be reused to the Production of sponge iron powder by reduction of rolling mill
.jpg)
SBM Ultrafine Powder Technology Industrial
Our main products include ultrafine vertical roller mill, ultrafine grinding mill, stone powder production equipment, Welcome to consult +17 [ protected] language >Shibang Industry Technology Group, Shanghai 2023年10月17日 Sponge iron is produced by lowtemperature reduction of iron ore in a rotary furnace, shaft furnace, or reactor Since the reduction temperature is lower than the melting temperature of the ore, the iron ore still maintains the shape of the ore after solidstate reduction, and has a porous and lowdensity spongelike structure, hence the name Sponge Iron SpringerLinkEquipment: Labcut 150 Variable Speed Precision Diamond Saw; Ideal for rough and fine grinding, including levigated aluminum oxide abrasive powders Recommended when fine polishing wrought aluminum alloys and magnesium Abrasive Powders Grinding Polishing Extec CorpProduction of sponge iron powder by reduction of rolling mill scale MI Martín*,1, FA López**, Mill scale contains both iron in elemental form and three types of iron oxides: wustite (FeO), hematite (αFe 2 O 3) and magnetite (Fe 3 O 4) greases from the equipment associated with rolling operations The oil content usuallyProduction of sponge iron powder by reduction of rolling mill
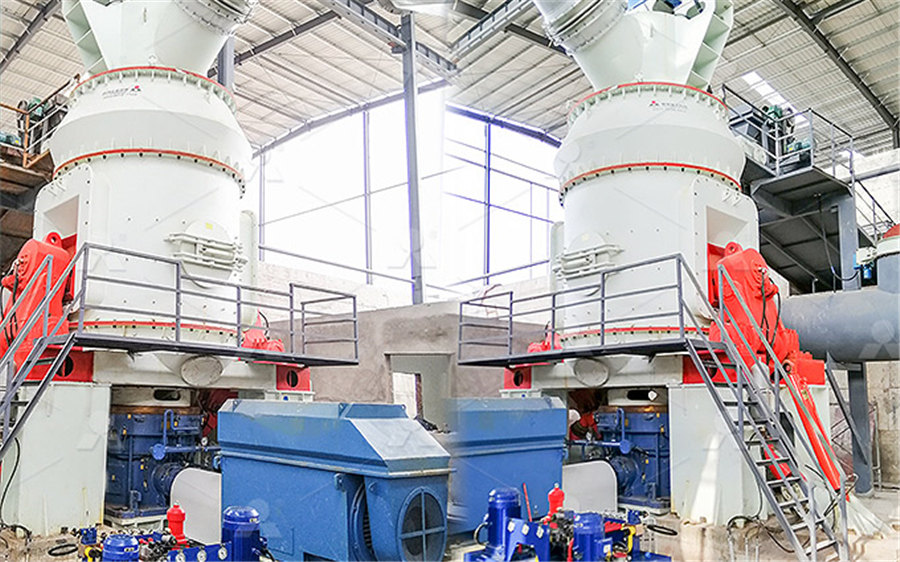
Grinding and Polishing Guide Buehler Metallography Equipment
2021年11月15日 Figure 31 SiC grit particle (arrow) embedded in a 6061T6 aluminum weldment (500X, aqueous 05% HF) The grinding abrasives commonly used in materials preparation are silicon carbide (SiC), aluminum oxide (Al2O3), emery (Al2O3 – Fe3O4), composite ceramics and diamondmaterial in the production of ironbase powder metallurgy parts Key Words: Powder production, Sponge iron, Solid byproduct 1 Introduction Mill scale is a steelmaking byproduct from the rolling mill in the steel hot rolling process Mill scale contains both iron in elemental form and three types of iron oxides: wustite (FeO), hematite (α Production of Sponge Iron Powder by Reduction of a By Get a complete guide to the metallographic preparation of powder metallurgy parts, including specific guidelines for fine grinding, diamond polishing and etching iron, copper and steel powders Expertise and insight from Struers, the world’s leading materialographic expertsMetallography of powder metallurgy parts Struers2020年3月3日 Sponge iron means porous iron produced by direct reduction processDirect reduction (DR) process is a solidstate reaction process (ie solid–solid or solid–gas reaction) by which removable oxygen is removed from the iron ore, using coal or reformed natural gas as reductants, below the melting and fusion point of the lump ore or agglomerates of fine ore []Sponge Iron SpringerLink
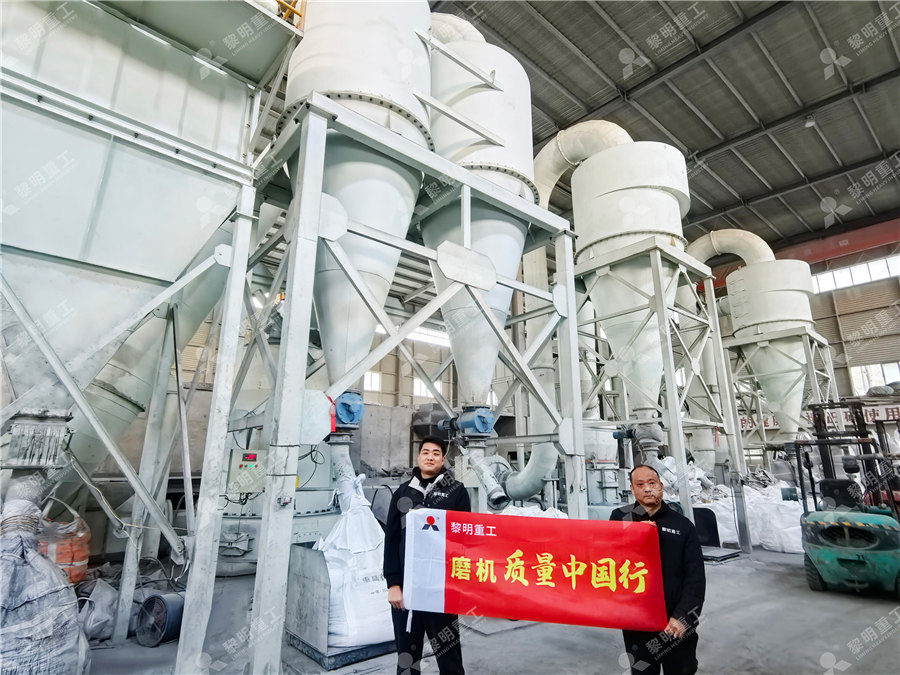
Process for batch production of sponge iron Google Patents
oxide material is not to be understood to refer only to ore, which has been crushed to a suitable grain size and possibly pelletized, but also to other metal oxide material in powder form such as calcined pyrites, crushed scale, red fume (ie, fume particles from oxygen blowing of iron or steel baths), cleaned grinding sludge and rill filings, etc, which waste products are agglomerated to 2021年1月4日 Until the late 19th century iron oxide pigments were obtained wholly from natural materials, generally with little alteration other than physical purification In some cases roasting or calcination was also carried out However, beginning in the first part of the 20th century, chemical methods were developed for synthetic production of commercial iron oxidesIron Oxide Pigments 911MetallurgistDirect reduction refers to solidstate processes which reduce iron oxides to metallic iron at temperatures below the melting point of iron Reduced iron derives its name from these processes, one example being heating iron ore in a Direct reduced iron WikipediaThanks to the experience obtained from the 1970's, to 2000’s in the hot briquetting of Waelz oxides (up to 650°C), phosphate (up to 1050°C) and sponge iron for Hot Compacting Iron process (up to 850°C), then SAHUTCONREURHot briquetting iron SAHUTCONREUR
.jpg)
sponge iron powder – Petroiron
About sponge iron powder Sponge iron powder is a finegrained, metallic powder produced by grinding and processing hot sponge iron (DRI) It is a versatile material with a wide range of applications, particularly in powder metallurgy and related industries Here’s a breakdown of the key features and characteristics of sponge iron powder:Sponge iron provides the base feedstock for all ironbased, selflubricating bearings and still accounts for around 30% of iron powder usage in PM structural parts Solid state reduction is also used for the production of refractory metal powders, using hydrogen as the reducing agent, and for the production of specialist iron powders by the reduction of mill scale (again using hydrogen)Powder production technologies Powder Metallurgy Review2020年10月1日 After some other processes, αFe 2 O 3 red powder particles byproduct of regeneration of spent pickling liquor in ARP in iron and steel industry should be ground up to pigment grade to convert it to a value added product, red iron oxide pigment In this study, grinding tests on αFe 2 O 3 red powder were performed using four different types of An investigation on optimum grinding system and conditions Myoc Iron Oxide Powder – 50 Gm (176 Oz), Iron Oxide Powder Cosmetic Grade, Iron Oxide Powder for Pigment, Iron Oxide Powder for Sunscreen, Iron Oxide Powder for Makeup, Pigment / Paint Pigment / Precious Metal Polish (Jeweler’s Rouge) / Pyrotechnics / Pewter Mold Release / Lens Grinding Abrasive / Lapidary / General NonToxic ColorantIron Oxide/Red 75 Micron Powder / 1 Ounce / 997% Pure
.jpg)
Elaboration of iron powder from mill scale ResearchGate
2010年1月1日 Iron oxide scale generally forms on lowcarbon steel surfaces during the hot rolling processes andproduces as solid waste more than 100 thousand tons per yearThe red iron oxide or ferric oxide glaze is one of those prevalent glazes that act as a much more common colorant for the glazing mixture With its easy availability, it offers a beautiful color to the glazing when fired inside the kiln Moreover, the potters use iron oxide wholeheartedly because during pottery glazing, the iron changes quite quickly in reduction firingEverything You Wanted to Know About Iron Oxide GlazeProduction of sponge iron powder by reduction of rolling mill scale M I Martı ´n*1,2,FALopez3 and J M Torralba4 Rolling mill scale is a solid byproduct of the steelmaking industry that Production of sponge iron powder by reduction of rolling mill scale2015年12月1日 In this study, production of sponge iron by direct reduction of oxides and the effect of reductant on metallization were investigated In the first stage of the study, scale formed during hot rolling of slabs was reduced in a rotating furnace using solid and gas reductants Coal was used as solid reductant and hydrogen released from the combustion reaction of LNG was Direct Reduction of Ferrous Oxides to form an IronRich
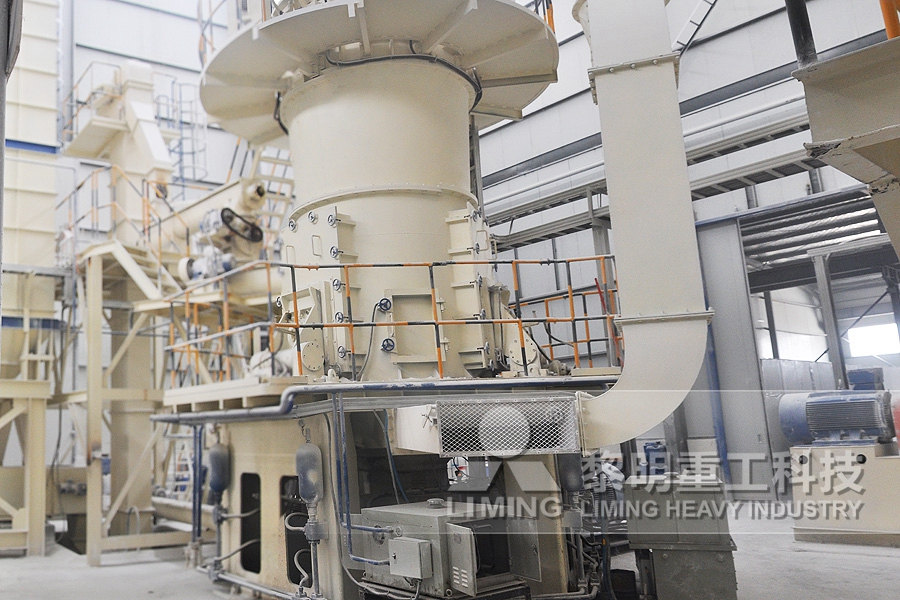
yield calculation of iron ore for sponge iron
Sponge iron is the metallic form of iron produced from reduction of iron oxide below the fusion temperature of iron ore (1535 oC) by utilizing hydrocarbon gases or carbonaceous fuels as coal The reduced product having high degree of metallisation exhibits a „honeycomb structure‟ due to which it is named as sponge iron2013年2月23日 Recrystallization of iron oxides is essentially a physical process in which smaller particles consolidate into larger ones with the loss of surface energy During the recrystallization of iron oxides, continued growth of iron Introduction to Iron ore Pellets and Pelletizing Keywords: Tunnel Kiln, Iron orecoal composite pellets, Sponge iron, Thermal efficiency, Carbon utilization efficiency, Percentage metallic iron 1 INTRODUCTION The tunnel kilns are mostly used by the ceramic industries for heating refractory and ceramic products [12] In the year 1908 use of tunnel kiln started for iron oxide reduction ThisSPONGE IRON PRODUCTION FROM ORE COAL COMPOSITE PELLETS IN TUNNEL KILNAluminium based powders Carbide powders Cobalt based powders Copper based powders Iron based powders Nickel based powders Oxide powders Titanium based powders Rhenium based powders Services Sponge iron powder NC10024 Data Sheet The green and edge strengths of the compacts are very high due to the spongy structure of the powder Iron powder for pressing sintering Höganäs
制粉项目-2023.11.17.jpg)
Aluminum Oxide Grit Manufacturers Suppliers in India
Long Lasting Shots And Equipments Sangariya Industrial Area Phase 2, Jodhpur D84, Extension1, Natural black iron oxide powder 200 mesh, packaging type: hd Natural Black Iron Oxide Powder 200 Mesh, Packaging Type: Grinding And Cutting Wheel Making Grade Standard 8 Mesh To 320 Mesh Brand VS Enterprise Packaging Type Bag1 A hard brittle layer of pure metal which is subsequently milled to obtain powder (eg iron powder) 2 A soft, spongy substance which is loosely adherent and easily removed by scrubbing 3 A direct powder deposit from the electrolyte that collects at the bottom of the cell Factors promoting powder deposits are, high current density, low metalPowder metallurgy – basics applications IIT Guwahati2023年10月9日 Comprehensive control of greenhouse gas emissions and response to climate change are concerns of countries around the world to protect living homes The steel industry is responsible for over 10% of global CO2 emissions, with approximately 80% of these emissions coming from the ironmaking process Great efforts have been made in both blast furnace (BF) Development and Problems of Fluidized Bed Ironmaking Process: In the blast furnace, iron is reduced and melted and the most common product is liquid iron called hot metal In direct reduction, iron remains in solid state and the product is the socalled direct reduced iron (DRI) Generically, the iron ore products Iron Ore Pelletizing Process: An Overview IntechOpen
.jpg)
Iron Ore Pelletizing Process: An Overview ResearchGate
2018年7月11日 Iron Ores and Iron Oxide Materials 50 Bentonite, an inorganic binder, has been the main binder used in the iron ore pelletizing process since the beginning of pellet production in the 1950s2023年10月9日 The product is direct reduction iron which is an ideal raw material for producing highquality steel and clean steel Direct reduction iron contains large number of fine pores and it looks like sponge when observed in a microscope, so it is also called sponge iron The sponge iron made of pellet is called metallized pelletDirect Reduction Ironmaking SpringerLinkUltrafine Mill To Solve Heavy Calcium Carbonate GrindingThere are many kinds of heavy calcium grinding and processing equipment in China They are combined with ultrafine grinding machine classifier to form an ultrafine Iron Powder, Metal powder, Reduce iron powder, 2023年9月15日 Iron powder is a powdered form of elemental iron It is commonly used in many industrial and manufacturing applications due to its unique properties and versatility This comprehensive guide will provide an overview of iron powder, its types, characteristics, applications, design considerations, suppliers, installation, operation and maintenanceIron Powder: Characteristics,types,Specifications Additive
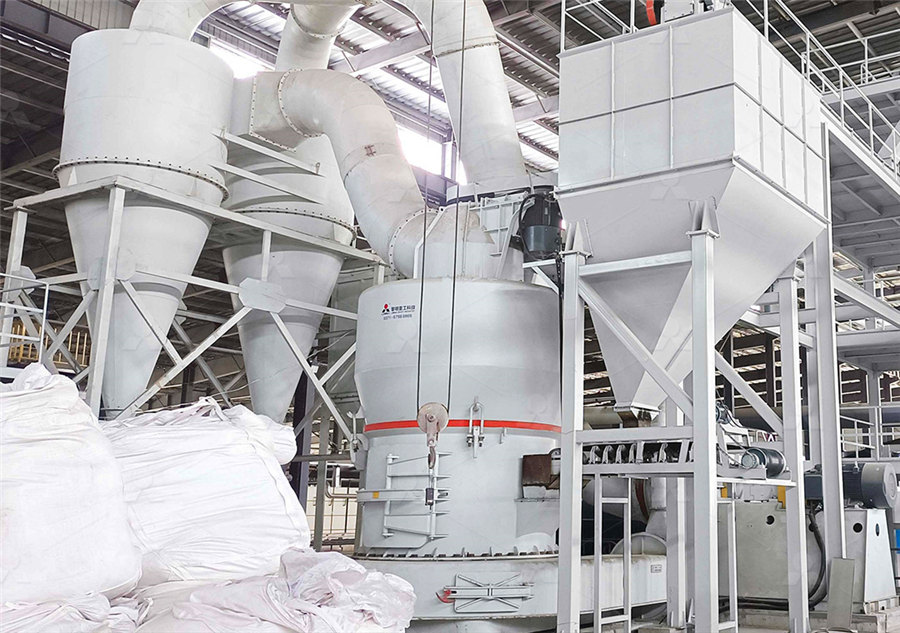
Iron Manufacturing process related to the specified manufacture
Sponge iron powder The Höganäs process is a direct reduction method for production of sponge iron powder using magnetite ore (Fe3O4) and carbon as raw materials The reduction process takes place in a gas fired tunnel kiln at around 1200°C for 60 hours producing a sponge iron cake that is crushed, milled and2016年3月30日 In book: Encyclopedia of Iron, Steel, and Their Alloys (pppp 10821108) Chapter: i) Direct Reduced Iron: Production; Publisher: CRC Press, Taylor and Francis Group, New York(PDF) i) Direct Reduced Iron: Production ResearchGatePart 3A: Iron Sponge Basics November 2017 One of the oldest technologies for the removal of hydrogen sulfide (H 2 S) from gas is the use of “Iron Sponge” A chemicalphysical process, originally developed to remove H 2 S from natural and coal gas streams, iron sponge has been in use for over 140 years and more recently to remove H 2HYDROGEN SULFIDE REMOVAL FROM BIOGAS Part 3A: Iron Sponge 2017年2月16日 PDF Sintering is a thermal agglomeration process that is applied to a mixture of iron ore fines, recycled ironmaking products, fluxes, slagforming Find, read and cite all the research you (PDF) Iron Ore Sintering: Process ResearchGate
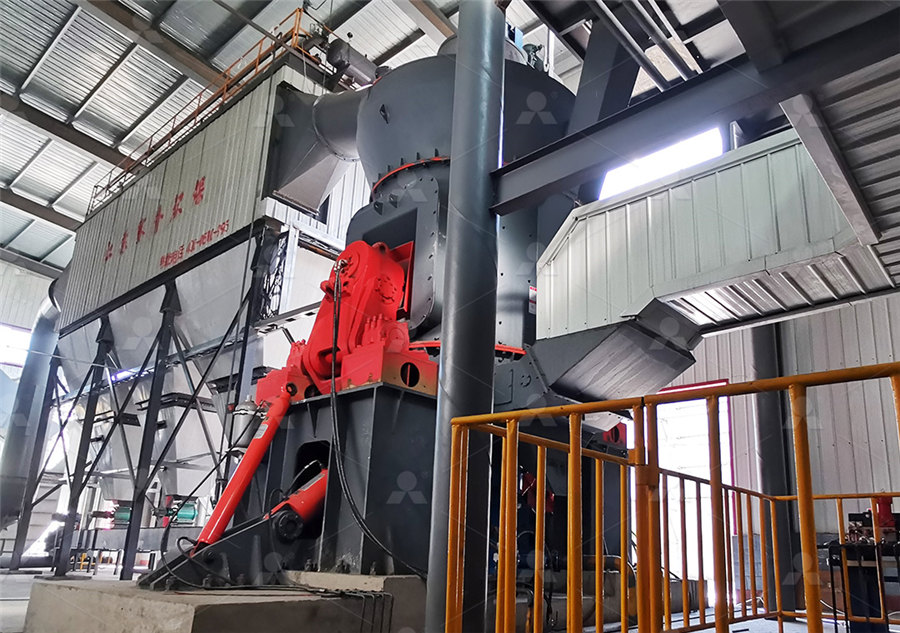
Powder Metallurgy: A Comprehensive Guide for Beginners
2023年9月5日 4 How to understand “Powder metallurgy technology is both ancient and young”? Powder metallurgy is an emerging field, yet it also has ancient roots Archaeological evidence suggests that as far back as 3000 BC, Egyptians used a type of bellows to reduce iron oxide to sponge iron with carbonReduced Iron Powder is a spongelike ironbased product obtained by reducing iron oxide Various functions of 'DOWA Reduced Iron Powder' are used in many applications Applications Powder metallurgy: Sintering machine components and bearing alloy;Reduced Iron Powder DOWA ELECTRONICS MATERIALS CO, LTDPart 3A: Iron Sponge Basics November 2017 One of the oldest technologies for the removal of hydrogen sulfide (H 2 S) from gas is the use of “Iron Sponge” A chemicalphysical process, originally developed to remove H 2 S from natural and coal gas streams, iron sponge has been in use for over 140 years and more recently to remove H 2HYDROGEN SULFIDE REMOVAL FROM BIOGAS Part 3A: Iron Sponge 51 SPONGE IRON PLANT There is a plan to install 4x100 TPD DRI kilns for production of 1,20,000 TPA sponge iron Manufacturing Process The proposed plant uses the coal based process in which iron oxide in pellet/iron ore will be reduced with non coking coal in a rotary kiln to make sponge ironProject Proponent M/s BRGD Sponge and Iron Pvt Ltd