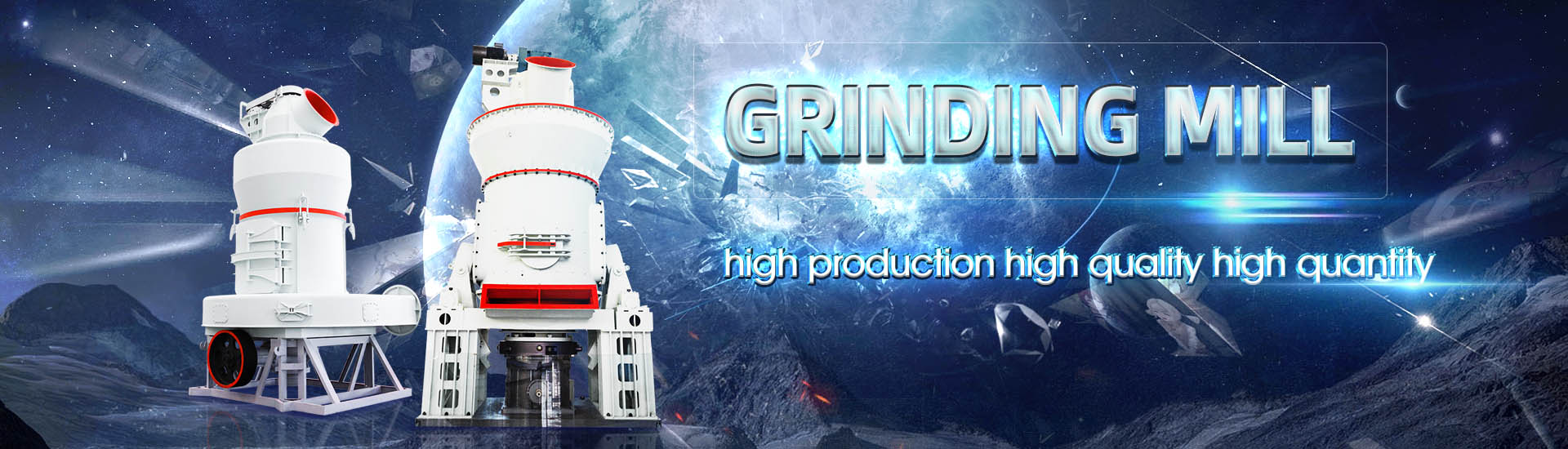
Residual Pole Ore Grinding Mill
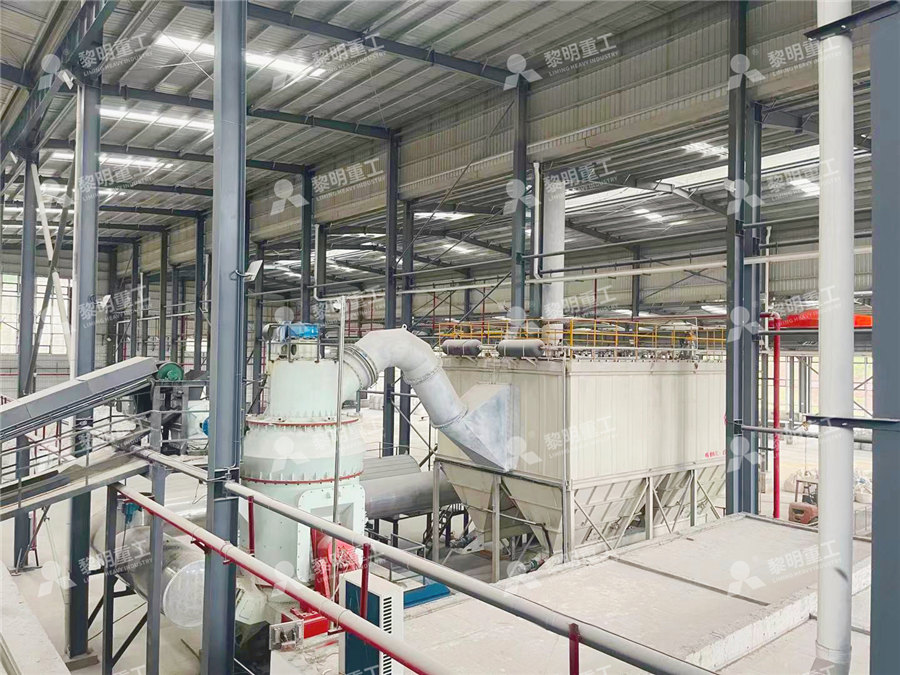
Ore Grinding SpringerLink
2023年7月20日 According to the material transmission methods, ore grinding is divided into dry grinding, wet grinding, and moist grinding Dry grinding relies on pneumatic conveying, in which the classification system and gas supply system of grinding products are complex and thus are 2023年10月27日 Grinding media play an important role in the comminution of mineral ores in these mills This work reviews the application of balls in mineral processing as a function of the A Review of the Grinding Media in Ball Mills for Mineral Processing Grinding media can be the ore itself (autogenous grinding primary and secondary), natural or manufactured nonmetallic media (pebble milling) or manufactured metallic media steel Selection Of Rod Mills, Ball Mills, Pebble Mills And Regrind MillsCustomized grinding mill parts including heads, shells, trunnions and liners, main bearings, gears and pinions, and more! Metallic, PolyMet™, Megaliner™, Rubber and Orebed™ mill liners for all mill types Whether old or new, we can Grinding mills for mining and minerals processing
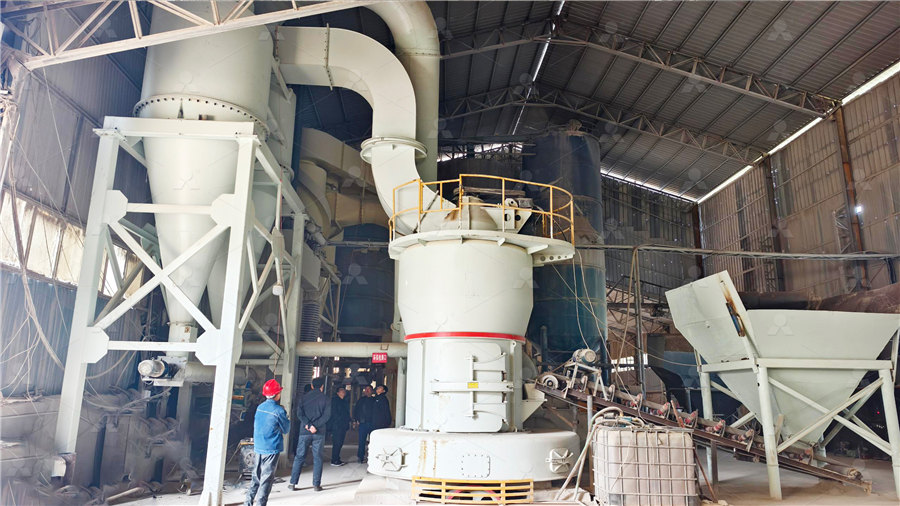
Chapter 7 Grinding Mills Wills' Mineral Processing Technology,
It is performed in cylindrical steel vessels that contain a charge of loose crushing bodies—the grinding medium—which is free to move inside the mill, thus comminuting the ore particles 2023年5月3日 The rod mill grinds the ore by the pressure and peeling force of the grinding media The bar first breaks up the coarse particles and then grinds the smaller ones The rod Rod Mill SpringerLink2023年7月27日 Rod grinding process is an ore grinding method which uses a long round metal rod as the grinding medium in a mill to smash the ore In the rod grinding process, when the Rod Grinding Process SpringerLinkIt is performed in cylindrical steel vessels that contain a charge of loose crushing bodies—the grinding medium—which is free to move inside the mill, thus comminuting the ore particles Grinding Mill an overview ScienceDirect Topics
.jpg)
Fine grinding: How mill type affects particle shape characteristics
2017年9月1日 The objective of this work is to assess the influence of fine grinding in ball mills and stirred mills on valuable mineral liberation and particle shape characteristics of UG2 ore, a 2015年4月9日 The mill is normally used for grinding of ores Lining of the cylinder plays very important role It protects the mill from abrasions and at the same time it helps in lifting of the material from the bottom of cylinder The Grinding Mills and Their Types IspatGuru2021年8月2日 CLIRIK barite grinding mill is a new generation of milling equipment improved on the basis of the traditional Raymond mill It is the most commonly used industrial mill +29Barite Ore Grinding MillCLIRIK Machinery2019年1月30日 The weight of mill and charge (ore and grinding media) is 3,452 tons The substructure method is used for dynamic analysis of the ball mill foundation, that is, the structure and soil are DYNAMIC DESIGN FOR GRINDING MILL
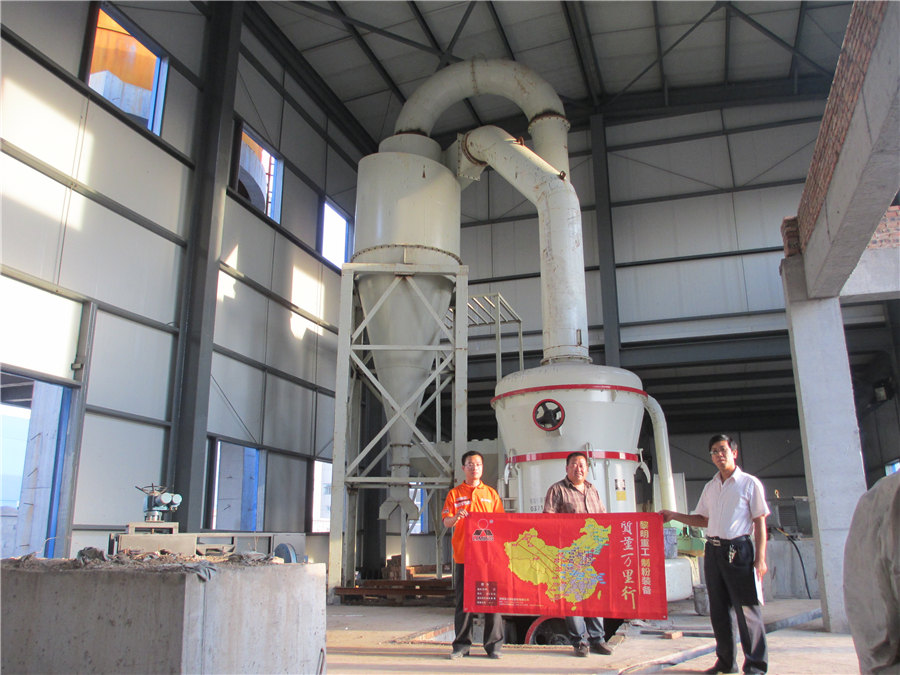
Research of iron ore grinding in a verticalrollermill
Request PDF On Mar 15, 2015, Mathis Reichert and others published Research of iron ore grinding in a verticalrollermill Find, read and cite all the research you need on ResearchGate2013年8月3日 In Grinding, selecting (calculate) the correct or optimum ball size that allows for the best and optimum/ideal or target grind size to be achieved by your ball mill is an important thing for a Mineral Processing Engineer AKA Metallurgist to do Often, the ball used in ball mills is oversize “just in case” Well, this safety factor can cost you much in recovery and/or mill liner Calculate and Select Ball Mill Ball Size for Optimum Grinding2023年7月20日 Therefore, the rod mill is mostly used for coarse grinding of the previous period of ball mill, or grinding of brittle materials and materials against overcrushing, such as tungsten and tin ore before gravity separation; and (3) autogenous mill – it refers to the materials which themselves are collided and ground mutually to be crushed when the grinding mill rotates, and Ore Grinding SpringerLink2023年11月21日 In the present incident, one of the rollers of grinding mill in cement plant failed during operation, exhibiting longitudinal cracking over inner surface Deposition welding was carried out just before the incident to match the wornout profile of the roller Investigation revealed that the subsurface of the cracked region contained discontinuities like blow holes Operational Failure of Vertical Roller Attached to a Grinding Mill
.jpg)
Grinding in Ball Mills: Modeling and Process Control
2012年6月1日 As the cylinder starts to rotate, the grinding balls inside the cylinder crush and grind the feed material, generating mechanical energy that aids in breaking bonds, activating the catalyst, and 2018年8月17日 The concept of ore blending is a very relevant notion in modern high tonnage production mines It is not only essential for the prolongation of the mine life of the concerned mine but as well as a The effects of ore blending on comminution behaviour and 2021年1月1日 Mill filling has a dominant effect on grinding mill performance (Apelt, Asprey and Thornhill, 2001), and therefore, its accurate measurement is vital for modelling grinding mill performanceMeasuring filling is also necessary to estimate the composition of the load for mill modelling: rock and slurry for AG mills; rock, balls and slurry for SAG mills; or balls and slurry An improved method for grinding mill filling measurement and Savona Equipment is your source for mill components and accessories for large primary ore process concentrating through secondary and tertiary fine material as well as complete ore processing facilities All our reconditioned mill components will be supplied ready for service We can supply SAG mill parts and Ball mill wearparts including ball mill liners and shell liners Our Grinding Mill Parts for Sale Ball Mill Parts SAG Mill Parts
.jpg)
Electric Drives for Large Ore Grinding Mills 911Metallurgist
2019年4月19日 Ore grinding mills are really just slowly rotating barrels, or some 60% of the 200 megawatts supplied to a large iron ore concentrator, are for grinding Mill Power Transmission Arrangements Note the absence of salient pole pulsationsvariable speed operation the grinding process can be optimized for ores with varying grinding properties This leads to significant optimization potential for the plant design as well as for its operation Furthermore, energy and cost savings due to optimized operation, high system efficiency and high system availability are shown IntroductionTECHNICAL AND COMMERCIAL BENEFITS OF GEARLESS MILL DRIVES FOR GRINDING Francisco M Pole 3,4 and Luis Balance of the Size Class Distribution of the Grinding Circuit Minimizing Residual Errors Size distribution of the ore particles of the fresh feed to the millUse of the Swebrec Function to Model Particle Size Distribution in 2016年1月1日 In wet grinding practice, highstress abrasion occurs over a small region when ore particles are trapped between the grinding balls and the mill liner, and the load is sufficient to fracture A comparison of wear rates of ball mill grinding media
.jpg)
Making remote mines and low ore grades economical and shifting
A milling circuit is a complex, multivariable interacting system Dynamically changing ore conditions and wear parameters pose particular problems for grinding controllers By integrating data, the automation system optimizes grinding controls, avoiding the 2019年4月1日 This study addressed the enhancement of cerium dissolution from weathered residual rare earth ore by mechanochemical activation by planetary ball millingMechanism and kinetics of enhancement of cerium dissolution 2019年4月1日 The effect of grinding by a planetary ball mill on the extent and rate of cerium dissolution from weathered residual rare earth ore and its mechanism were investigated Quantitative cerium dissolution from the weathered residual rare earth ore was achieved by planetary ball milling for 720 min; cerium dissolution from the without grinding ore was 200%Mechanism and kinetics of enhancement of cerium dissolution 2014年8月20日 The weight of mill and charge (ore and grinding media) is 3,452 tons The substructure method is used for dynamic analysis of the ball mill foundation, that is, the structure and soil are DYNAMIC DESIGN FOR GRINDING MILL FOUNDATIONS
.jpg)
Operational Failure of Vertical Roller Attached to a Grinding Mill
The schematic of grinding mill and isolated vertical roller assembly is shown in Fig 1 During operation of grinding mill, normal load was maintained below * 70 bar depending on the characteristics of feed material The grinding mill consisted of a table with diameter * 2500 mm and grinding track of * 1600 mm diameter1 Grindability: The grindability of the ore affects the efficiency of the grinding mill Harder ores require more energy and longer grinding times, which can impact the mill's performance and operational costs 2 Media andliner Wear: The condition of the grinding media and liners affects the mill's efficiencyUnderstanding the operation of grinding mills in the mining and 2012年12月1日 Optimization of inmill ball loading and slurry solids concentration in grinding of UG2 ores: A statistical experimental design approach December 2012 Minerals Engineering 39:149155(PDF) Optimization of inmill ball loading and slurry solids The Autogenous Mill, also known as AG Mill, is a type of grinding mill used in the mining industry This machine uses ore and rock itself as grinding media to perform its job Unlike other types of mills that use steel balls or rods for Understanding the SAG Mill in Copper Ore Mining
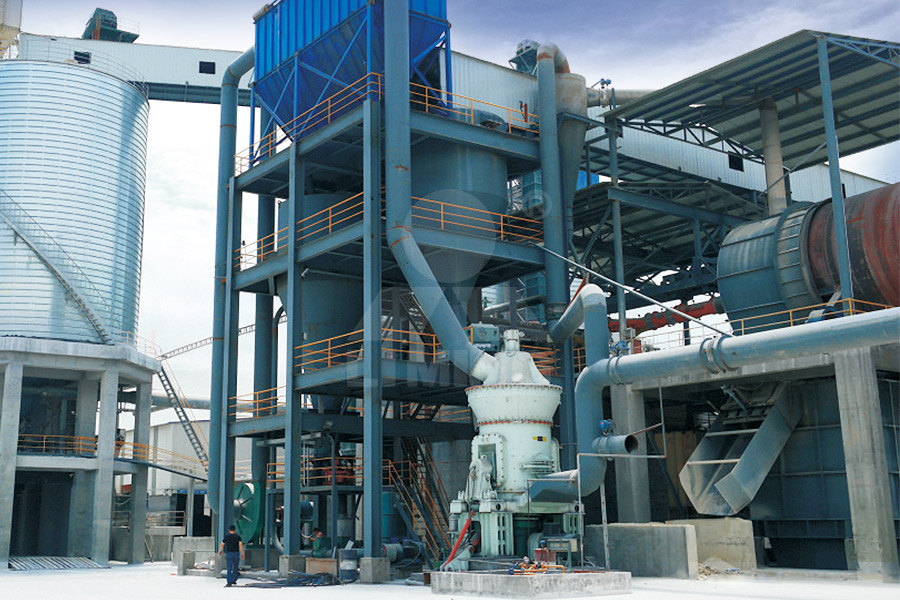
High pressure grinding rolls HPGR for iron ore, cement MAXTON
5 天之前 In comparison to conventional crushing and grinding methods are reached through increase of capacity in combination with – potential benefits to the separation kinetics of downstream processes such as floatation and leaching as consequence of residual microcracks generation in the crushed product of low energy requirements, increase of valuable product 2015年12月1日 Öksüzoglu and Uçurum [27] studied the ultrafine grinding of gypsum ore in a dry ball mill In their grinding tests, the mill speed was varied from 50 to 90% of the critical speed for gypsum oreAn experimental study on the ultrafine grinding of gypsum ore An autogenous mill of ID 67 m and an effective grinding length of 21 m was fed with ore of SG 38 to 20% of its volume The mill was operated continuously 24 hours per day at 1200 t per day and 75% of the critical speed The solids in the mill charge were at 80% solids Estimate:1Semi Autogenous Grinding Mill ScienceDirect TopicsSBM ultrafine powder technology co,ltd Is China's excellent ore mill supplier Our main products include ultrafine vertical roller mill, ultrafine ultrafine grinding mill, stone powder production equipment, Welcome to consult +17 [ protected] language >Shibang Industry Technology Group, Shanghai Ultrafine Powder Tech SBM Ultrafine Powder Technology Industrial Grinding Mill,
.jpg)
Optimization and Experimental Study of Iron Ore Grinding
2024年9月26日 Energy savings and consumption reduction of ball mills are crucial for industrial production The grinding medium is an important component of a ball mill In theory, using higherdensity grinding media can yield better grinding results However, for materials with varying grindability, employing grinding media of different densities can reduce energy consumption 2014年10月1日 In a test performed in the Loesche test center in Germany, copper slag grinding saved 229% energy in an airswept model and 344% energy in an overflow model [13,14]Copper Ore Grinding in a Mobile Vertical Roller Mill Pilot PlantOne reason is the dry inbed grinding principle Results of extensive test works with two types of magnetite iron ores in a Loesche VRM are presented here Within these test works, mill parameters like grinding pressure, separator speed and dam ring height were varied, following a factorial design of the experimentsResearch of iron ore grinding in a verticalrollermillA crushing plant delivered ore to a wet grinding mill for further size reduction The size of crushed ore (F 80) was 40 mm and the SG 28 t/m 3 The work index of the ore was determined as 122 kWh/t A wet ball mill 1 m × 1 m was chosen to grind the ore down to 200 micronsGrinding Mill an overview ScienceDirect Topics
.jpg)
Population balance model approach to ball mill
2014年1月1日 An analysis of the kinetics of dolomite grinding in a dry ball mill reveals that the following approximations apply for the parameters of the batch grinding model: the size discretized selection 2018年8月8日 The paper presents a study on the effectiveness of the grinding process in an electromagnetic mill devoted to ultrafine grinding, and the influence of processing parameters on the mill’s performance The research was Grinding Kinetics Adjustment of Copper Ore Grinding Analysis of the sulfuric acid leachate were 074 (without grinding of the ore), 087 (for ore that had been ground for 10 min), 083 (20 min grinding), The chemical composition of the weathered residual rare earth ore, 080 (60 min grinding), 079 (360 min grinding), and 068 (720 min obtained from the Republic of South Africa, was measured by xray grinding)Mechanism and kinetics of enhancement of cerium dissolution 2020年10月18日 An iron ore concentrate sample was ground separately in a pilotscale HPGR mill in multiple passes and a dry opencircuit ball mill to increase the specific surface area of particlesThe effects of iron ore concentrate grinding methods (HPGR and
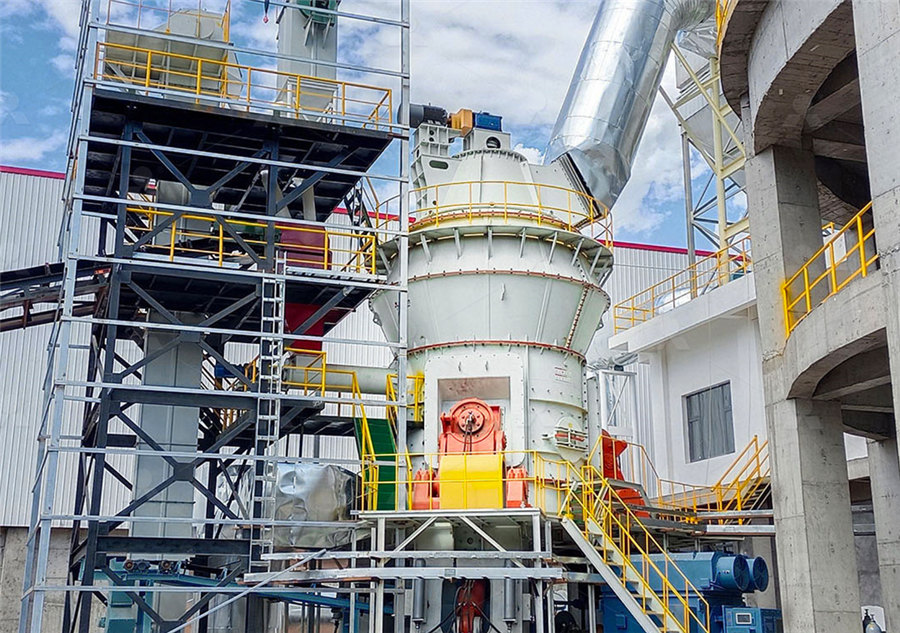
Ore Pretreatment Methods for Grinding: Journey and Prospects
2018年6月18日 Ore pretreatment methods for grinding: journey and prospects, Mineral Processing and Extractive Metallurgy Review, DOI: 101080/2018 To link to this article: https://doior g/10 2024年2月21日 This paper proposes the ball mill load recognition algorithm (MRUFWD) based on multiresidual unit fusion (MRUF) and Wasserstein distance transfer learning to address the problem of accurately judging the working state parameters during ball mill grinding operations The proposed algorithm can significantly enhance the processing capability of underlabeled Multiresidual unit fusion and Wasserstein distancebased2020年3月28日 Based on batch grinding method and normalization idea, a conical ball mill is used and a quantitative separation method of grinding characteristics of multicomponent complex ore is proposedDevelopment of a Novel Grinding Process to Iron Ore Pelletizing 2017年10月3日 Imagine (Marty says “wait, see the diagram below!”) a cylindrical steel vessel with an ore and a grinding medium moving inside the mill, the rotating drum lifting this material and finally breaking the ore into a specified product Further, the grinding mills can be categorized into three major types – rod mills, ball mills, and SAG millsGrinding Mill Types, Working Principle Applications
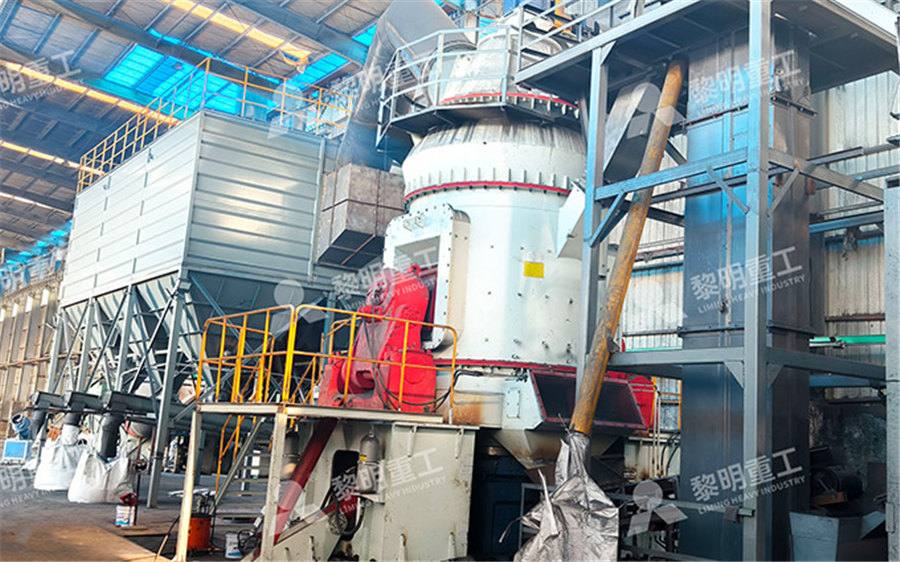
Analysis and Optimization of Grinding Performance of Vertical
2022年1月23日 Residual 4950 × 10 − 6 7 7071 × 10 Aydogan, N Copper ore grinding in a mobile vertical r oller mill pilot plant Int J Miner Pr ocess Productivity increase of the vertical