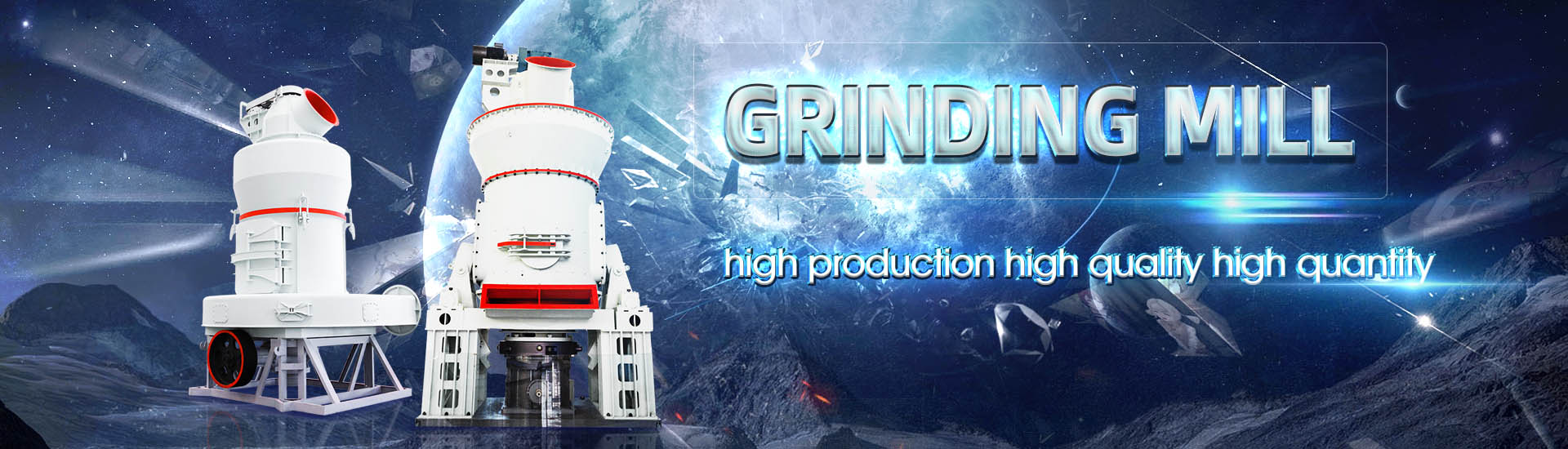
Rotary kiln filling amount
.jpg)
Mixing process for different filling degrees (n = 3 rpm)
The thermal efficiency of a rotary kiln is preponderantly influenced by the amount of lateral mixing of the material bed The dominant mechanism of the movement in the cross section is theDegree of filling is defined as the ratio of area/volume occupied by material to the area/volume empty Kiln filling % signifies the ease of heat transfer between flam and kiln walls to kiln feed In long kiln designs and SP kilns the kiln speed was Kiln Degree of Filling (% Filling) Cement Plant The rotary kiln is used in many solid processes, including drying, incineration, heating, cooling, humidification, calcination and reduction This widespread application can be attributed to Rotary kiln process: An overview of physical mechanisms, models Rotary kilns (Figure 1) are used for a range of mineral processing operations Kilns range in size from 2–6 m in diameter and can be 50–225 m long with an operating mass of up to 3000 t Modelling and optimization of a rotary kiln direct reduction process
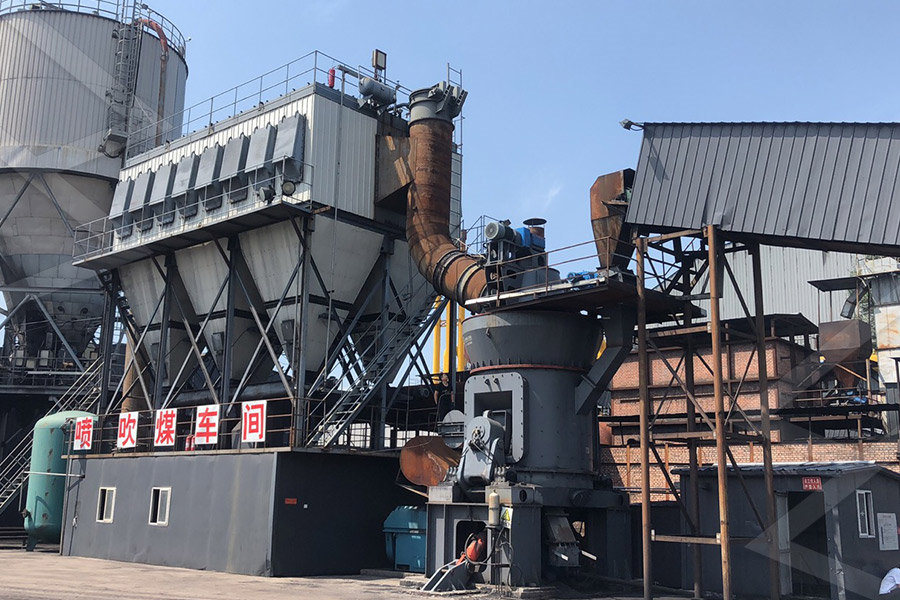
kiln filling %, kiln degree of filling, rotary kiln filling degree
From 40 to 11 L/D ratio in long wet kilns and modern two tire kilns, L/D has a special significance in cement plant Moreover, this dimensionless number is used commonly in engineering Previous Post Next Post Contents1 Useful formulas in Kiln Design Operation ( Updated Completed )11 Kiln effective cross section12 Kiln Effective Volume13 Kiln % filling14 Water consumption in GCT15 Kiln feed Retention Useful formulas in Kiln Design Operation ( Updated Rotary kilns are an advanced thermal processing tool used for processing solid materials at extremely high temperatures in order to cause a chemical reaction or physical change The FEECO Rotary Kiln HandbookKiln residence time and fill level affect the progress of chemical reactions, as well as the maximum throughput for a rotary kiln This is determined by (i) the maximum flow rate of the proposed Modelling and optimization of a rotary kiln direct reduction
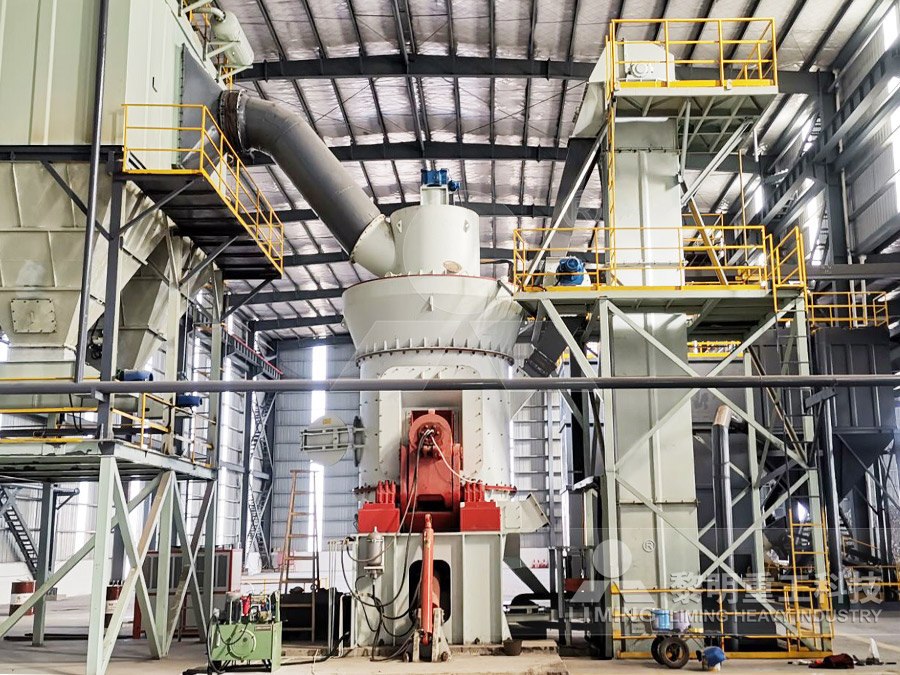
Rotary cement kiln calculations, kiln residence time, Burning zone
online calculators for cement plant, Rotary cement kiln calculations, kiln residence time, Burning zone loading, volumetric loading degree of filling,2020年7月3日 rotary kiln V k= 90m3, the t ilt Angle of rotary kiln incinerator S =175°, the speed of the rotary kiln v =12 r/min So, the inner diameter of rotary kiln D r k=2800 (mm), and the length (PDF) Parameter design of rotary kiln incinerator and 2002年1月1日 We also used the following simplifications: gas recirculation was neglected; gas temperature was constant throughout each segment and on the transversal section of the rotary kiln; the filling Mathematical models for the cement clinker burning process Part 1989年8月29日 Material Flow Studies in a Rotary Kiln PST SAI, GD SURENDER, AD DAMODARAN, V SURESH, ZG PHILIP, and K SANKARAN Experiments were conducted in a rotary kiln containing ilmenite particles to study the residence time distribution (RTD) of lowdensity particles, holdup, and bed depth profile The variablesResidence time distribution and material flow studies in a rotary kiln
.jpg)
Improving longterm operation performance of hazardous waste rotary
2024年2月15日 The stable operation and management of rotary kiln incineration facilities are very important, and they still face severe challenges For instance, the production capacity of current facilities is generally unsatisfactory, owing to factors such as unstable operating conditions, unskilled work operations, low level of equipment operation and maintenance, and The heat transfer mechanism in rotary kilns includes conduction, convection and radiation Figure 1 shows an indirectly heated rotary kiln As the rotary drum wall, which is usually made of steel or graphite, is heated externally with Q total, heat from the source is transported to the wall and then conducted through the wall Q WTHE CONTACT HEAT TRANSFER IN ROTARY KILNS AND THE For example, a rotary kiln with an inner diameter of less than 1 m has a suitable filling rate of 15%; and a rotary kiln with an inner diameter of 25 m allows a filling rate of only 6% If the filling rate is too large, the heating of the material is insufficient and uneven, which will affect the quality of the material calcinationHow Much Is The Filling Rate Suitable For Rotary Kiln?The length of each part of a rotary kiln is designed based on the inner diameter (D) of the kiln shell 1) The length of the kiln head overhanging section (l 1): l 1 = (12~15) D As the first section of a rotary kiln, l 1 is better not to be designed too long, or the length of the effective parts of the kiln will have to be shortened 2) The length of the preheating section (l 2): l 2 = (5 Cement Rotary Kiln Design
.jpg)
Rotary Kiln, a Unit on the Border of the Process and Energy
2022年10月26日 A rotary kiln is a unique facility with widespread applications not only in the process industry, such as buildingmaterial production, but also in the energy sector There is a lack of a more comprehensive review of this facility and its perspectives in the literature This paper gives a semisystematic review of current research Main trends and solutions close to Effectiveness factors for a rotary kiln with bed fill 52% The thick line shows the prediction of the passive layer model (Chapter 2) The value of the work lies in two aspects: firstly, the recognition of the contribution of the passive layer towards mass transfer, and secondly, theModelling of Rotary Kilns University of Twente Research 2005年7月1日 However, industrial rotary kilns are usually under continuous operation, in which the fill angle varies along the kiln length and is affected by many factors (such as inclination of the kiln Slumping–rolling transition of granular solids in rotary kilnsclones (P), Calciner (Ca), Rotary Kiln (K), and Cooler (Co) The production of clinker comprises several process equipment: a preheating tower (with a set of cyclones), a calciner, a rotary kiln, and a cooler, see Fig 1 As the formation of clinker takes place in the rotary kiln, this paper focuses on formulating a dynamical model for the A Dynamical Simulation Model of a Cement Clinker Rotary Kiln
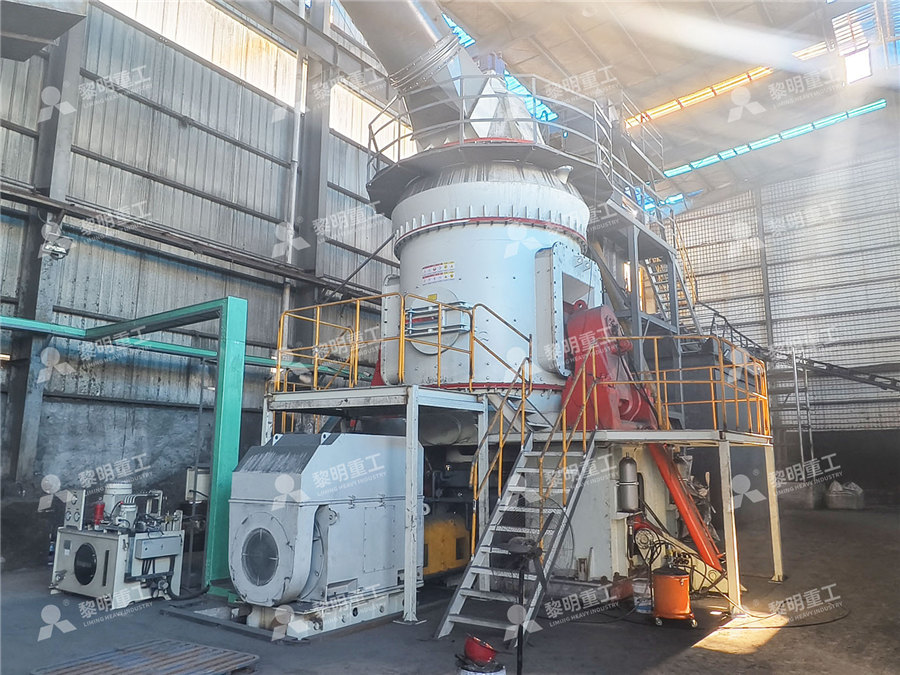
Rotary Kiln Tanabe Co, Ltd 株式会社タナベ
Batchtype rotary kiln is recommended for samples that require longtime firing (4 hours or more) As with the continuous rotary kiln, various atmosphere gases are inserted into the furnace and the raw material is fired while stirring View product details Small size batch type external heat rotary kiln (electric type)2021年7月25日 The reduction process inside the ore prereduction rotary kiln involves a series of physicochemical reactions, and indepth understanding of the reduction behavior is helpful to improve the product quality and productivity Numerical Analysis on Characteristics of Reduction 2020年9月5日 The cement plant is one of the most energyintensive industries, and the rotary kiln consumes significant share of this energy and the amount of consumed fuel has a direct effect on the finished product price (Radwan 2012)The cement plants consume high quantities of power which shape approximately 40% of the total production cost (Chatterjee and Sui 2019; Zanoli Improvement of a cement rotary kiln performance using artificial neural kiln, taking into account the geo metry of the kiln, it was divided into sections (Fig 2) The division was made according to the following principle: at the beginning and the end of the kiln, two small zones of 100 mm each Modeling parameter Parameters Values Measurement units Particle density 2460 kg/m3 Static particleparticle friction 01 –Effect of variation of internal diameter along the length of a rotary
.jpg)
Industrial Applications of Rotary Kiln in Various ResearchGate
Rotary kiln is used as waste incinerator, the cylinder is mounted at an angle of 12° and rotates at a speed of 02 to 03rpm, and diameter is 42m and 114m lengthPrevious Post Next Post Contents1 Kiln/Cooler Calculation Formulas11 Material Residence Time in Kiln12 Material Filling Degree in Kiln13 Clinker Cooler Exit Temperature14 Transport Efficiency of Grate Cooler15 Reference Kiln/Cooler Calculation Formulas Material Residence Time in Kiln The retention time of the material in a dry rotary kiln can be determined with the Kiln/Cooler Calculation Formulas INFINITY FOR CEMENT EQUIPMENT2023年3月3日 The cement industry includes energyintensive processes, eg, clinker rotary kilns and clinker grate coolers Clinker is obtained through chemical and physical reactions in a rotary kiln from raw meal; these reactions also involve combustion processes The grate cooler is located downstream of the clinker rotary kiln with the purpose of suitably cooling the clinker Advanced Process Control for Clinker Rotary Kiln and Grate Cooler2024年3月26日 Rotary kiln dryers are mostly in the use of the heavy metal industry for years and for sludge incinerations purposes As an alternative to the rotary kiln dryers for sludge drying, drum dryer or rotary dryer manufacturers are available on the market with having the knowledge of sludge treatment and processspecific solutionsSludge Drying by Belt, Disk, and Rotary Kiln Dryers
.jpg)
Modeling of Rotary Kiln in Cement Industry ResearchGate
2016年1月1日 PDF Cement production is a highly energyintensive process, and the rotary kiln is the most important part of the process • Average amount of coating conductivity 074 W/m 2 / ˚C was Download scientific diagram Clinker formation process in a modern plant rotary kiln from publication: the splash amount of 019 g at the furnace mouth is reduced to only 16%, Clinker formation process in a modern plant rotary kilnDownload scientific diagram Sections of the rotary kiln and nomenclature from publication: Numerical investigation of bed depth height, axial velocity and mean residence time of inert particles Sections of the rotary kiln and nomenclatureIn most kiln systems the required amount of excess air is slightly above the point where the flame temperature would be highest due to sulfur, maintain kiln filling degree constant and increase BET: 5: BZT: Low: The retention time of the Kiln Control and Operation INFINITY FOR CEMENT
.jpg)
Modelling and optimization of a rotary kiln direct reduction
Modelling and optimization of a rotary kiln direct reduction process Kiln residence time and fill level Kiln residence time and fill level affect the progress of chemical reactions, as well as the maximum throughput for a rotary kiln This is determined by (i) the maximum flow rate of the proposed burden through a kiln, and (ii) the residenceThe lime kiln is one of the main places for thermal energy consumption in Sarcheshmeh copper complex The gas consumption of this horizontal rotary kiln is approximately 17 tons per hour The amount of limestone entering the lime kiln is equal to 113 tons per hour, and the tonnage of the output product is equal to 61 tons per hour Investigating the potentials to improve the energy consumption of By default, the device is equipped with a filling connection and a level sensor for automatic filling Precise lubricant application despite the toughest conditions Until now, manual lubricant application into the riding ring gap of rotary kilns was a major challenge for maintenance staffSafe riding ring lubrication for rotary kilns Ring StarPrevious Post Next Post Contents1 Useful formulas in Kiln Design Operation ( Updated Completed )11 Kiln effective cross section12 Kiln Effective Volume13 Kiln % filling14 Water consumption in GCT15 Kiln feed Retention Time16 Cooler performance Useful formulas in Kiln Design Operation ( Updated Completed ) Kiln effective cross section Useful formulas in Kiln Design Operation ( Updated
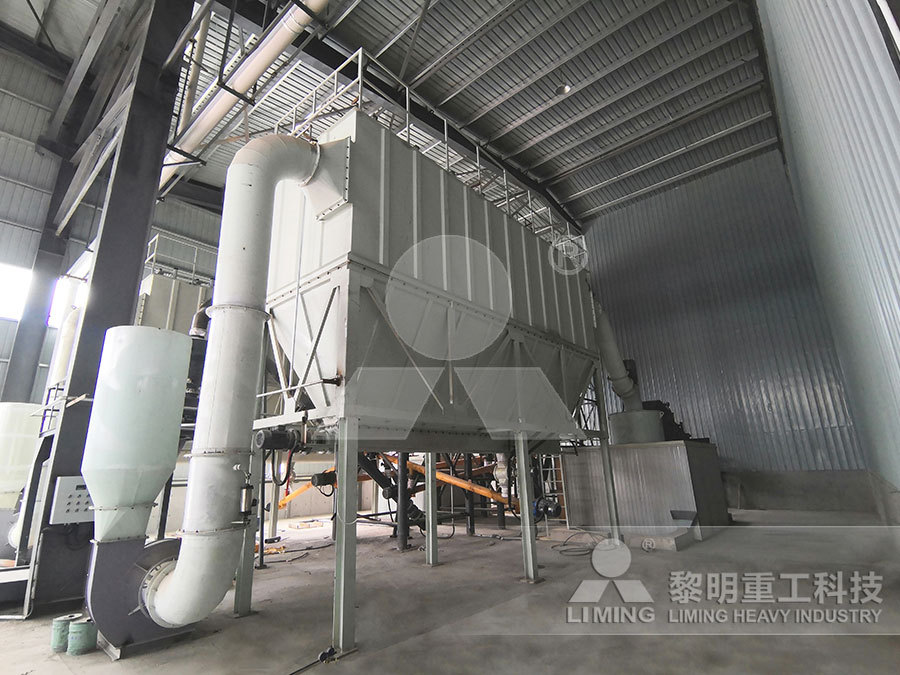
Rotary Kilns Heat Systems Carbon Regeneration Kilns Australia
An indirect fired horizontal rotary kiln is the most cost effective carbon regeneration kiln both in capital expenditure and ongoing spares For all enquiries: +61 3 9357 7393 ectiveness factors for a rotary kiln with bed fill 52% The thick line shows the prediction of the passive layer model (Chapter 2) The value of the work lies in two aspects: firstly, the recognition of the contribution of the passive layer towards mass transfer, and secondly, theModelling of Rotary Kilns utwentecirculation of thermal oil in the walls of the rotary kiln to predict its temperature gradients, the heating rate, the influence of the rotation, temperature and mass flow of the system oil and homogenization of its bed 2 Mathematical modeling In this section, the physical problem (rotary kiln) description will be presented, involving theDYNAMIC MODELING OF THE HEAT TRANSFER PROCESS IN ROTARY 2014年1月1日 A Rotary kiln is a cylinder which rotates around its cylindrical axis and acts as a device to exchange the heat The construction, position and alignment of kiln is a essential factor for the Industrial Applications of Rotary Kiln in Various
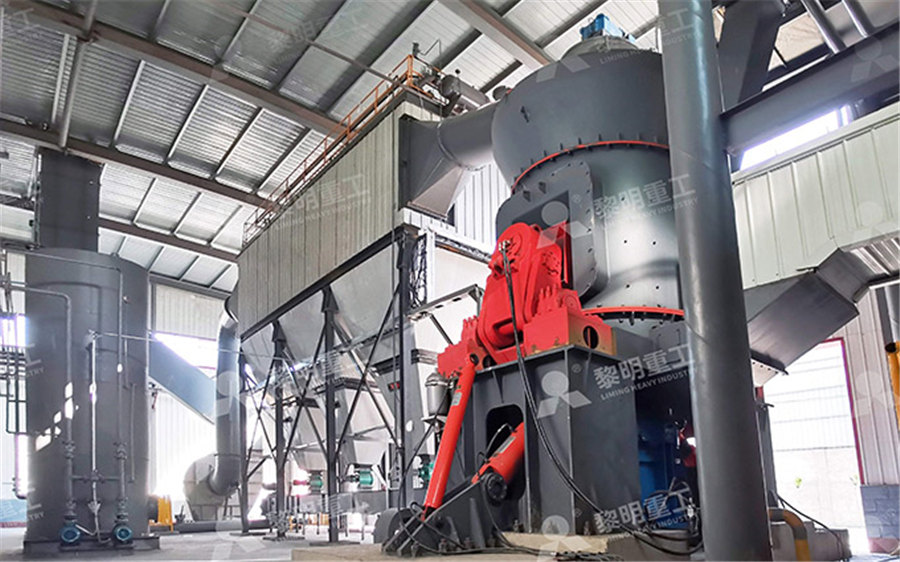
GEOMETRICAL CHARACTERISTICS OF THE SOLID BED IN A ROTARY KILN
diameter of the rotary kiln, its rotation speed, the filling degree of the drum with material, the dynamic angle of its repose and the particles diameter are proposed Keywords: rotary kiln, rolling motion, active layer Received 30 July 2013 Accepted 25 November 2013 INTRODUCTION Rotary kilns serve for a hightemperature heat treat 2016年1月6日 Large amount of Sugar – Ash materials are produced as a byproduct in the sugar industry These materials can be re – external 03cycled with the scrap per hour but filling capacity is 8T per hour Rotary kiln is also used in the production of sarooj with 200kg/hrA Review on Design and Thermal Analysis of Rotary Kiln for Lime 2010年7月22日 Degree Of Kiln filling Kiln Cross Sectional loading: % of Filling or Area of this segment (A1) = Kilns Degree Area of cross section of Kiln (A) Theta Centric Angle Theta % of Kiln (Degree) filling 110 1565 105 1375 100 121 Segment 95 107 r = radius inside lining 90 909 85 775 r^2 A1 = O – Sin O 80 652 2 75 542 70 45 A = II r^2Formulas kiln PPT Free Download SlideShare2019年4月18日 Hazardous waste output in the world is increasing every year To achieve higher efficiency and lower pollution, the incineration technology for hazardous waste needs to be studied further This study mainly reviews the research progress in incineration, slagging, and pollutant emission in the rotary kiln in China and abroad in the last 10 years, and conducts a Hazardous waste incineration in a rotary kiln: a review
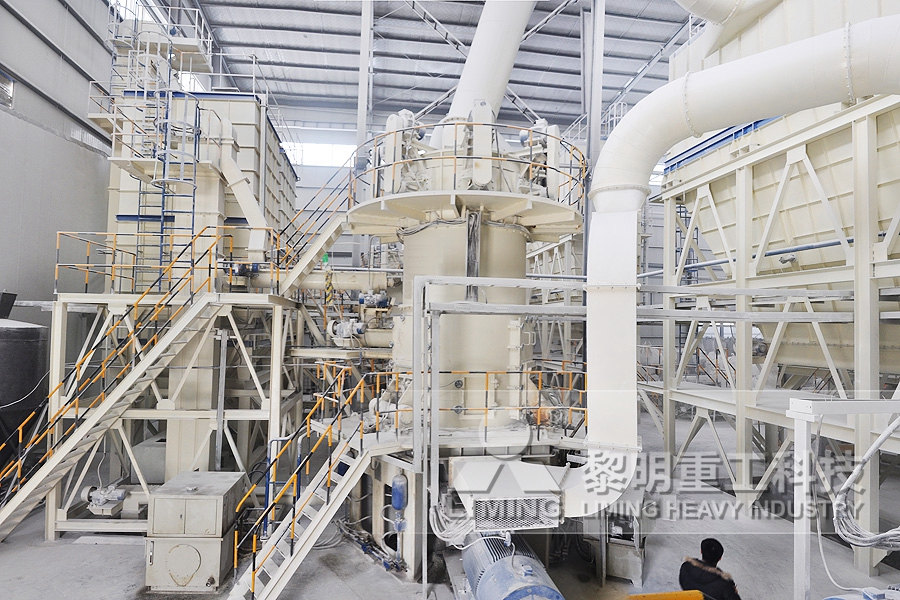
Longitudinal and transverse mixing in rotary kilns: A discrete
2005年8月1日 The focus is on the effect of the main operating conditions, ie, the filling degree and the rotational speed of the rotary kiln, on quantitative measures of longitudinal and transverse mixingrotation and the amount of bed fill For faster processes the upper surface of the rotary kiln (the active layer) becomes important for modelling the rate of reaction or drying This rate depends on the same parameters as the slower rates and the ratio of the particle diameter to the diameter of the rotary kiln This helps to unravel the mysterySLOWLY UNFURLING THE MYSTERY OF ROTARY KILNSROTARY KILN CONSTRUCTION While FEECO rotary kilns are custom designed around the material to be processed, in general, there are some standard components that serve as the basic design of a rotary kiln The diagram shown on page 8 illustrates some of the common standard components found on a basic directired kiln A diagram of anThe FEECO Rotary Kiln Handbook FEECO International Inc2011年3月30日 The axial discharging velocity of the particles was experimentally investigated at the discharge end of two rotary kilns with 400 and 250 mm internal diameter, respectively Sand, glass beads and clinker were used as experimental materials A physical method without using imaging technology was developed to measure the axial discharging velocity based on the Experimental investigation of the axial discharging velocity of
.jpg)
polysius graphite seal: Sealing every rotary kiln effectively and
2 Graphite seal at a rotary kiln on the kiln outlet side Sealing off a rotary kiln process from false or inleaked air is vital to maximizing process reliability and availability Although standard sealing solutions are preinstalled in most kiln systems, maintenance work and the replacement of wornout parts are expensive operations