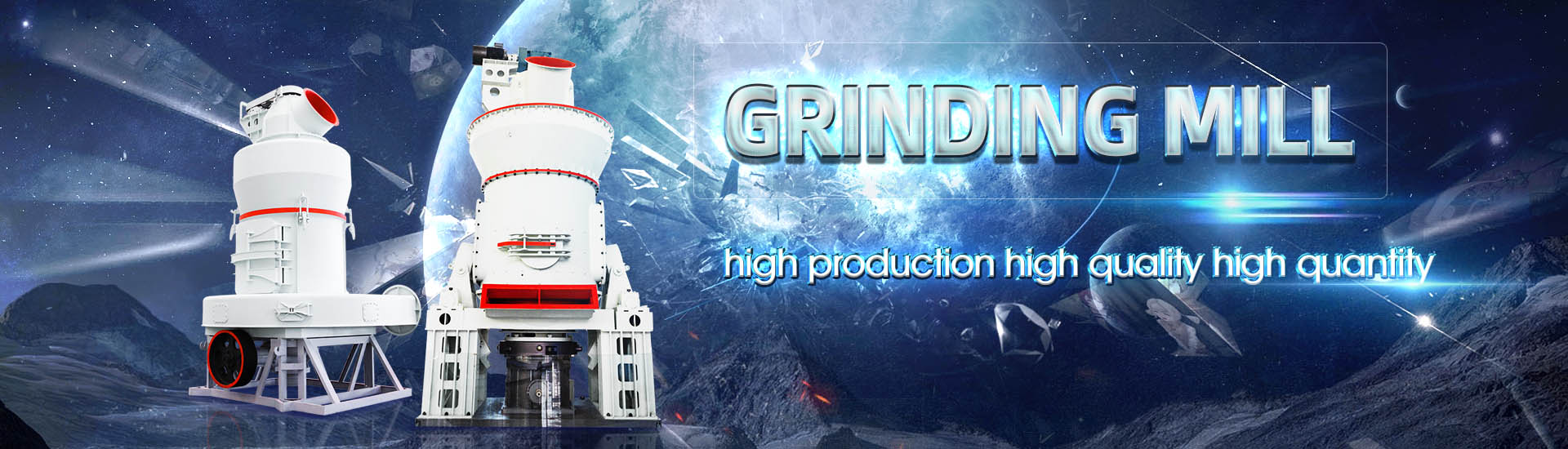
Twolayer ore mill
.jpg)
Intelligent optimal control system for ball mill grinding process
In this paper, an intelligent optimal control method with twolayer hierarchical construction is presented Based on fuzzy and rulebased reasoning (RBR) algorithms, the intelligent optimal 2023年10月27日 Grinding media play an important role in the comminution of mineral ores in these mills This work reviews the application of balls in mineral processing as a function of the A Review of the Grinding Media in Ball Mills for Mineral Processing Roller mill is a type of grinding equipment for crushing materials by pressure between two or more rolling surfaces or between rolling grinding bodies (balls, rollers) and a track (plane, ring, and Roller Mill Springer2022年4月1日 Milling makes use of a combination of impact, attrition, and shear mechanisms to further reduce the size of ore particles down to micron sized particles There is a combination Review on advances in mineral processing technologies suitable

New Automated System for Optimisation of Ore Grinding Process
1998年9月1日 As a result of the recent scientific and experimental studies new microprocessor devices have been developed of the ore grinding process control system The brief description 2019年4月16日 This paper brings together two separate studies, in which the vertical roller mill was used to grind two different precious metal ores, an epithermal gold deposit hosted in quartz vein from(PDF) LEARNING FROM OTHER INDUSTRIES; WHY THE The dry milling of ore in LOESCHE vertical roller mills has shown significant process advantages, as well as economic and ecological benefits To demonstrate these a mobile oregrinding plant the OGPmobile has been Mills for minerals and ores Loesche2023年11月24日 Factors that influence the grinding efficiency include mill design, liner design, mill speed, mineralogical composition of the ore, charge ratio, and grinding media properties Grinding Media in Ball Mills for Mineral Processing
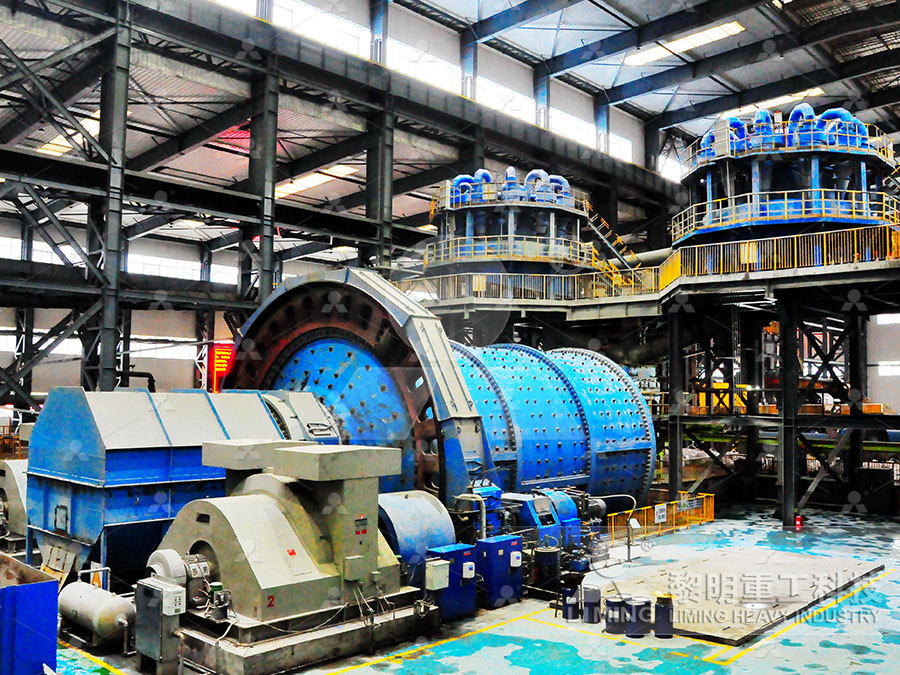
Ball Mill an overview ScienceDirect Topics
where Ω E is the energycorrected ball wear rate, g per kWh, d R is the diameter of the largest balls in the mill (the recharge size), mm, K d E is the linear wear rate of balls, µm per kWh t −1, Ai is the Bond abrasion index determined in a laboratory test (unitless), F 80 is the feed 80% passing size of the ore, µm, and pH is the water acid/base measurement of the mill pulp2017年5月1日 Twostage reduction for the preparation of ferronickel alloy from nickel laterite ore with low Co and high MgO contents May 2017 International Journal of Minerals Metallurgy and Materials 24(5 Twostage reduction for the preparation of Find your ore mill easily amongst the 42 products from the leading brands (Fritsch GmbH, Retsch, Eriez, ) on DirectIndustry, chemical industry, etc, it has two ore grinding Compare this product Remove from comparison tool ball grinding mill horizontal for ore ball grinding mill Final grain size: 74 µm 400 µmOre mill, Ore grinding mill All industrial manufacturers2015年6月19日 The basic parameters used in ball mill design (power calculations), rod mill or any tumbling mill sizing are; material to be ground, characteristics, Bond Work Index, bulk density, specific density, desired mill tonnage capacity DTPH, operating % solids or pulp density, feed size as F80 and maximum ‘chunk size’, product size as P80 and maximum and finally the type of Ball Mill Design/Power Calculation 911Metallurgist
.jpg)
The Ultimate Guide to Ball Mills Miningpedia
2019年8月14日 • Central discharge ball mill: the inlet of medium unloading ball mill is at both ends, and the outlet is in the middle of the ball mill 4 According to the ore discharge of ball mill: • Overflow ball mill: Discharge the ore through hollow shaft • Grid ball mill: Discharge the ore through the plaid plate2020年1月1日 In this work complex investigations of the abrasing wear of lining of selfgrinding mills (semiautogenous grinding mills) are carried out with the obtaining of mathematical models of wearabrasing The study of the lining layer abrasing wear in the semiautogenous 2017年2月16日 The ore is conveyed to the mill over a distance of seven miles by a 2foot On the completion of the charge—about twothirds water and onethird concentrate—the shaft and the lightest The uppermost layer is skimmed off till the tin shows sufficiently clean for bagging These skimmings are then treated in a small Tin Ore Processing 911MetallurgistR Roller Mill Xiao Xiao1, Huang Lilong2 and Xu Kuangdi3 1Changsha Research Institute of Mining and Metallurgy, Changsha, China 2Changsha Research Institute of Mining and Metallurgy, Changsha, China 3Chinese Academy of Engineering, Beijing, China Roller mill is a type of grinding equipment for crushing materials by pressure between two orRoller Mill Springer
.jpg)
Three Stage Flow Sheet with Two Stage HPGR and Ball Mill Fine
Comparative grinding tests of twostage closed HPGR with 7 mm and 1 mm screens and a final mill grind, and twostage closed HPGR with a 7 mm screen and an air classifier cutting for final product 2013年2月1日 Mesoacidophilic bacterial leaching of ball mill spillage (containing chalcopyrite >80%) was carried out in an innovative twostep bioleaching method The major drawback of mesoacidophilic bioleaching limiting industrial application is the passivation phenomenon over the ore surfaces in iron–sulfur rich environmentsTwo step mesoacidophilic bioleaching of chalcopyrite containing 2000年1月1日 Download Citation Cropping of twolayer chilled mill rollers Production of chilled cast iron rollers has been organized This rollers are used at the rolling mills Worn roller should be Cropping of twolayer chilled mill rollers ResearchGate2023年6月12日 The most valuable ores of gold are quartz gold ore, silver gold ore, copper gold ore, gold sulfide ore, etc 1 Grind bulk silverrich gold ore to a finer size by using a ball mill 2 Leach the flotation tailings the covalent radii 8 Types of Gold Ore Properties and Ways to Process
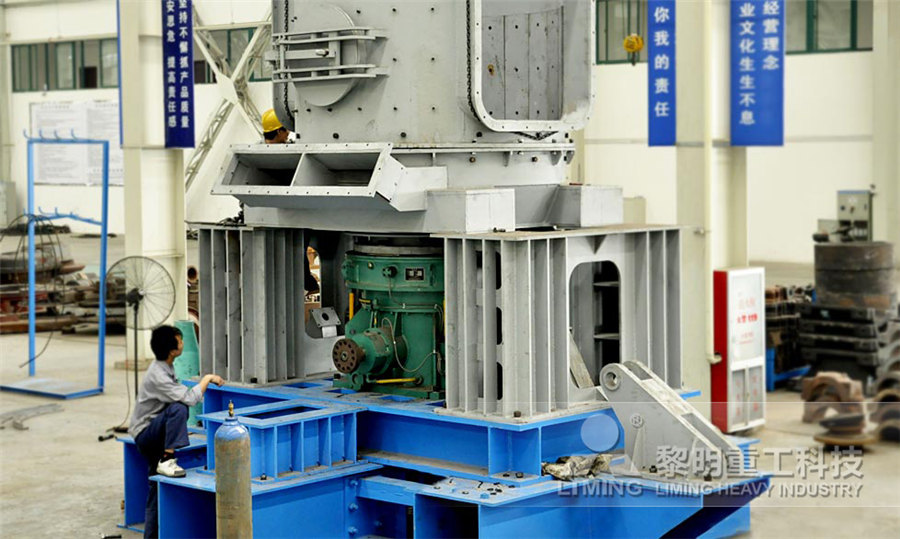
Recycling of steel plant mill scale via iron ore sintering plant
2012年4月1日 Request PDF Recycling of steel plant mill scale via iron ore sintering plant During the processing of steel in steel mills, iron oxides will form on the surface of the metal These oxides 2023年4月23日 Comminution is a very important and resultdetermining step in mineral processing This is because further downstream processes in the beneficiation chain depend entirely on it(PDF) Grinding Media in Ball MillsA Review ResearchGate2021年10月8日 Abstract The authors study the engineering geological characteristics and material constitution of loparite ore mill tailings in the active disposal area and in the dump decommissioned more than 30 years ago The material constitutions and the contents of valuable components are nonunform in the test tailings The content of light rare earth elements in fine Studies of Properties and Composition of Loparite Ore Mill In the mill, the mixture of medium, ore, and water, known as the mill charge, is intimately mixed, the medium comminuting the particles by any of the above methods Apart from laboratory testing, grinding in mineral processing is a continuous process, material being fed at a controlled rate into one end of the mill and discharging at the other end after a suitable dwell (residence) timeGrinding Mill an overview ScienceDirect Topics
.jpg)
Population balance model approach to ball mill optimization in iron ore
3 BALL MILL MODEL The population balance model may be expressed by Equation (1): > @ ¦ i1 1 i b ij m j j i j i S Ht dt d H m t (1) where: S i (t) is the size discretized selection function for 2024年10月30日 Ore is a deposit in Earth’s crust of one or more valuable mineralsThe most valuable ore deposits contain metals crucial to industry and trade, like copper, gold, and iron Copper ore is mined for a variety of industrial uses Copper, an excellent conductor of electricity, is used as electrical wire Copper is also used in constructionOre Education National Geographic Society2024年4月26日 The final stage in iron ore processing is ironmaking, where the iron ore is transformed into molten iron through a process called reduction The most common method of ironmaking is the blast furnace route In a blast furnace, iron ore, coke (carbon), and fluxes (limestone or dolomite) are loaded into the furnace from the topIron Ore Processing: From Extraction to ManufacturingMILL OPTIMIZATION IN IRON ORE GRINDING* Patrícia Mundim Campos Faria1 Luís Marcelo Tavares 2 Raj K Rajamani 3 other two mills were used in this investigation: a pilotscale ball mill (0416 in a layer loading manner that is, alternating layers of ball, feed and water, POPULATION BALANCE MODEL APPROACH TO BALL MILL OPTIMIZATION IN IRON ORE
.jpg)
Towards waterless operations from mine to mill ScienceDirect
2022年9月1日 Waste rocks occupy space from ore in the grinding mill, thus lowering the mill’s ore grinding capacity and mineral concentrator’s concentrate production Moreover, in most cases, waste rock is harder and, consequently, more difficult to grind than the ore which is often found in the weaker areas of the rock2023年11月16日 Therefore, the filtered tailings used herein are termed 80/20 and were generated with moisture content values ranging from 12 to 18% The grain size distribution of the 80/20 tailings used is highlighted in Fig 1Table 1 summarizes the main physical characteristics of the iron ore tailings According to the Unified Soil Classification System (ASTM 2017a), 80/20 Dry Stacking of Filtered Iron Ore Tailings: Comparing OnField For the flow around a circular cylinder Zdravkovich [10] showed that the boundary layer at the cylinder is laminar for Reynolds numbers up to about 105 Changes in the holdup, ie in solids loading and particle size distribution, (PDF) Grinding in an air classifier mill Academia2018年4月16日 Request PDF Comparing Vertical Roller Mill Performance on Two Different Precious Metal Ores The vertical roller mill (VRM) is a comminution device in which crushing, grinding and Comparing Vertical Roller Mill Performance on Two Different Precious
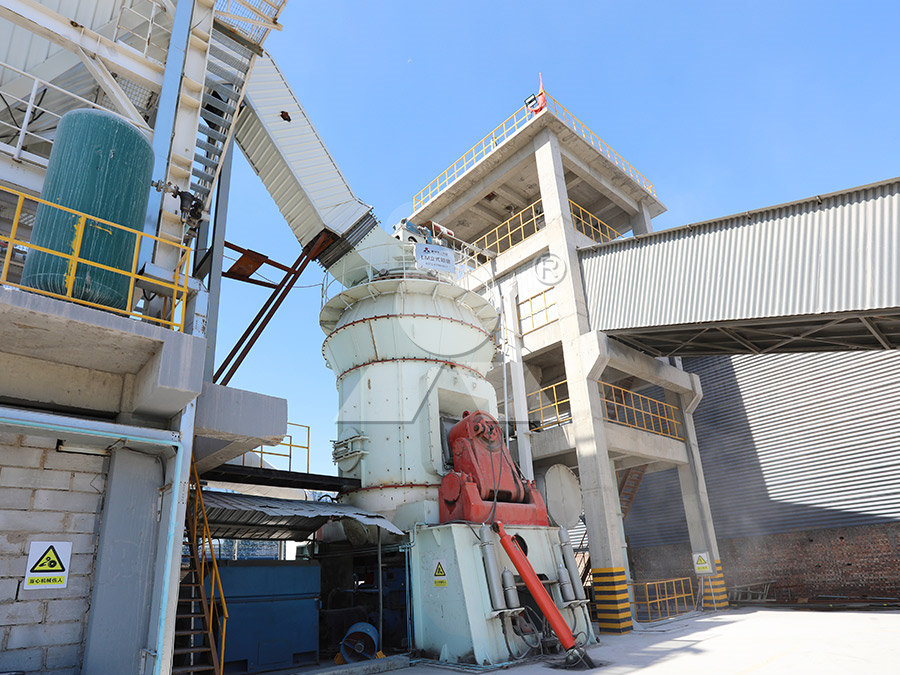
Iron Ore Agglomeration Technologies IntechOpen
2017年12月20日 Until the 1950s of the last century, the oxidized iron ores that were loaded into the blast furnace had granulometries within 10 and 120 mm However, the depletion of highgrade iron ore sources has made necessary the utilization of concentration processes with the purpose of enriching the iron ore Because of these processes, a fine granulometry is produced, and 2016年7月14日 HPGR test results published by Grier (1992) on gold ores from the Mt Todd project showed significant energy savings for a HPGR/Ball Mill circuit as compared to a SAG/Ball Mill plant By adding a Polycom highpressure grinding roll, the throughput of existing plants can be increased by as much as 150% while simultaneously reducing the power consumption by HPGR 911MetallurgistTo prevent ore from wearing out grinding mill drums, replaceable liners are inserted ABB and Bern University of Applied Science have developed a liner wear monitoring system based on accelerometers and machine learning that identifies the best time to change the liner and thus reduce downtime costsMachine learning solves grinding mill liner monitoring ABBOre T ype Mill Circuits Classification Device Bond Work Index @300 two basic problems; South African ores contain an average of around 34 g of platinum group elements per ton of The extractive metallurgy of South Africa's platinum ores

What Ore Testing is Required For Mill Selection
2015年4月15日 Discharge from each mill Feed to each classification stage Oversize from each classification stage Fines from each classification stage, k Power drawn by each mill (motor input) Motor and drive efficiency of each mill, Size of and type of grinding media used in each mill Speed in RPM for each mill Liner design and condition in each mill2020年10月18日 An iron ore concentrate sample was ground separately in a pilotscale HPGR mill in multiple passes and a dry opencircuit ball mill to increase the specific surface area of particlesThe effects of iron ore concentrate grinding methods (HPGR and 2016年2月1日 The purpose of this study is to understand how ore loss and dilution affect the mine call factor, with the aim of subsequently improving the quality of ore mined and fed to the millMonitoring ore loss and dilution for minetomill 2013年2月1日 Two step mesoacidophilic bioleaching of chalcopyrite containing ball mill spillage and removal of the surface passivation layer Author links open overlay panel S Panda a d FESEMEDS studies indicated severe corrosion effects of the wash solution on the passivation layer Two step bioleaching of the ore sample yielded 326% Two step mesoacidophilic bioleaching of chalcopyrite containing ball
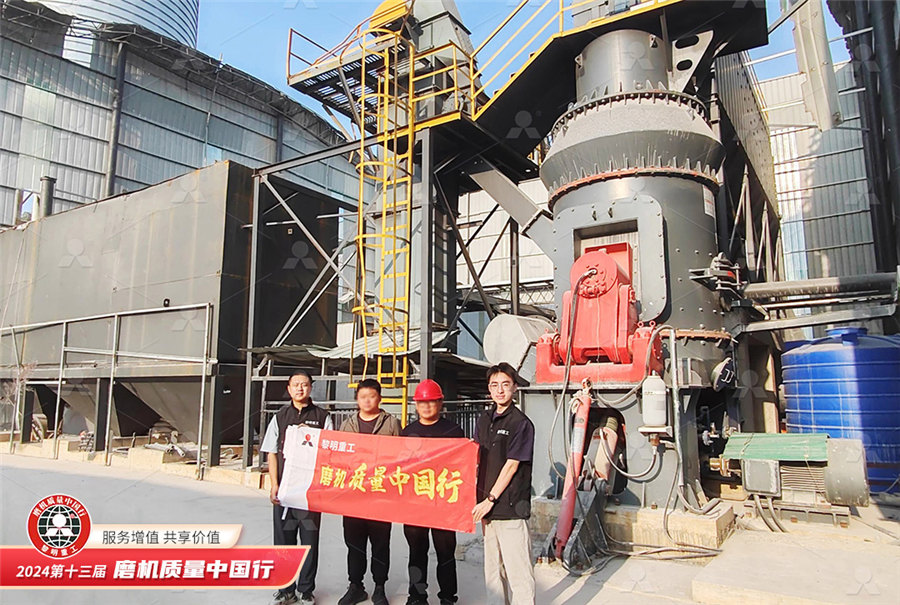
Population balance model approach to ball mill
2014年1月1日 The mill product, due to its physical properties, determines the efficiency of subsequent stages of classification, filtration and pelletizing, thus impacting the quality of iron ore pellets2016年10月31日 According to Gruessner, at the Hannan’s Star Mill, Kalgoorlie, the ore from two No 5 dry ball mills was treated wet in a tube mill 16 feet 5 inches long and 3 feet 11 inches in diameter The ball mills crushed 78 tons per day and, after classification, the coarser part of this, amounting to 38 tons, was ground to about 250 mesh in the tube millTube Mills 911Metallurgist2020年9月22日 Grinding machine has been widely used in gold mines in South Africa since 1905 At that time, the grinding machine used river pebble as the grinding medium, which was essentially a gravel mill Later, in order to improve the production capacity of the mill, cast iron balls were used as the medium, so normal gravel mills were evolved into ball mills and rod millsGrinding Machines: Types and Selection Principles Miningpedia2019年10月19日 Ball mills are extensively used in the size reduction process of different ores and minerals The fill level inside a ball mill is a crucial parameter which needs to be monitored regularly for optimal operation of the ball mill In this paper, a vibration monitoringbased method is proposed and tested for estimating the fill level inside a laboratoryscale ball mill A vibration Monitoring the fill level of a ball mill using vibration sensing and
.jpg)
Crushing Plant Flowsheet DesignLayout 911Metallurgist
2016年3月11日 It was felt by some that crushing to this fine size is only possible if the ore is friable and is relatively soft in comparison to the harder ores Our results show that some of the copper ores are as hard as taconite and are crushed to ball mill feed all passing 13MM (½”)2020年6月1日 PDF Mill scale, often shortened to a two or singlelayer iron scale is formed So, with less heating, the wustite layer is thin there are manganese ores in Uzbekistan, STUDY OF IRON EXTRACTION FROM MILL SCALE ResearchGateHowever, ore below the pay limit adds variation to the mill grade as increased mill throughput will be required to make up for the loss of gold, and that impacts on the recovery in the plant It is against these perspectives and findings of this study that the MCF should be seen as a method that identify the real problems underground and when these are addressed, the profitability of Monitoring ore loss and dilution for minetomill integration in • Metallic mill linings • Skega™ PolyMet™ mill linings • Skega™ rubber mill linings • Orebed™ mill linings • Megaliner™ Liners for all types of mills Our stateoftheart linings are available for mills of virtually all types, sizes and brands • Semiautogenous mills • Fully autogenous mills • Ball mills • Rod millsMill lining solutions for horizontal Mill