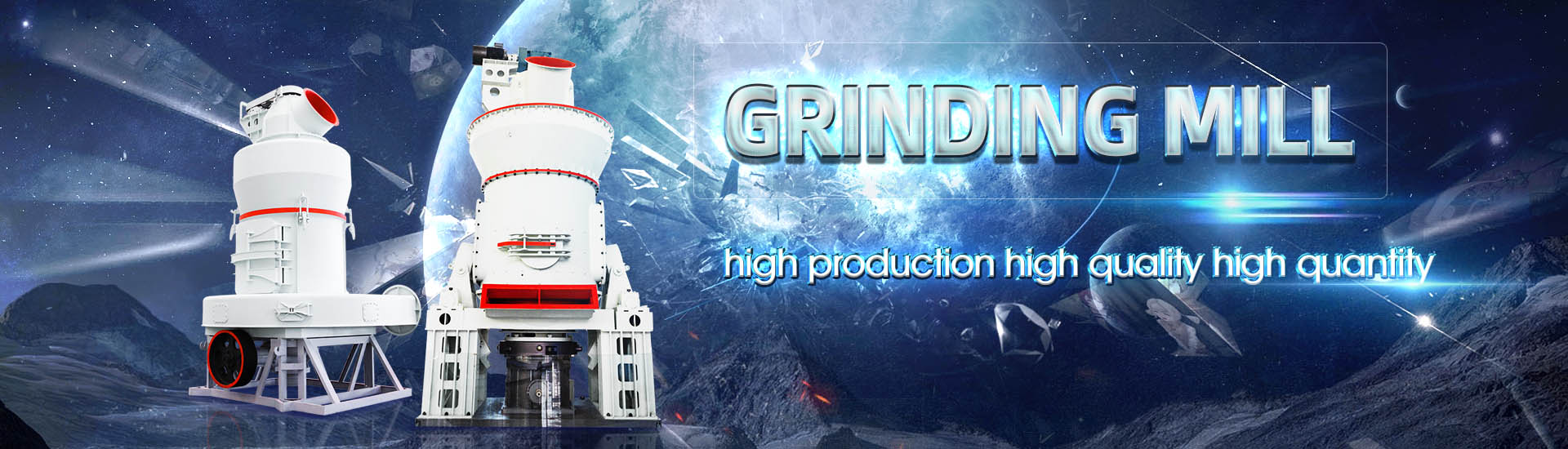
Coking open furnace
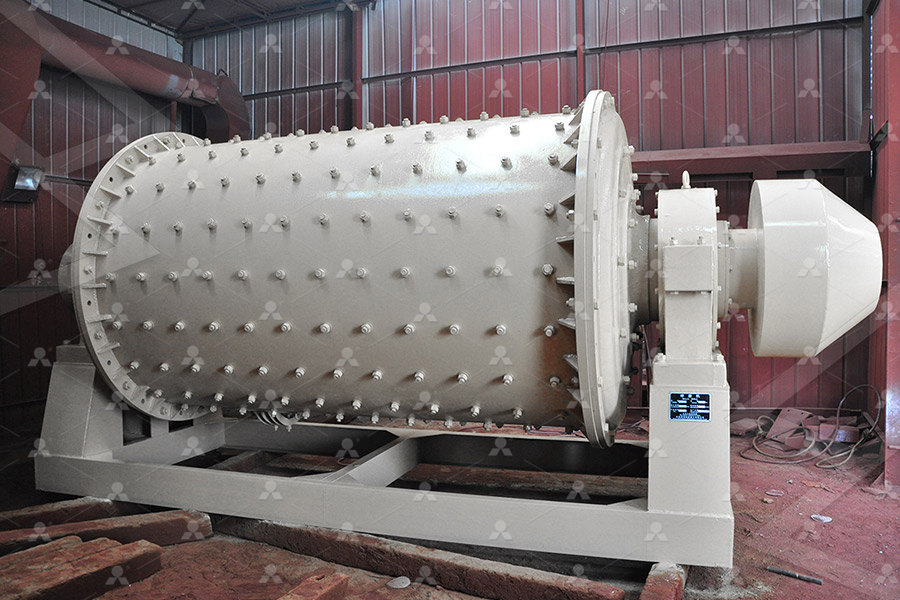
Coking IntechOpen
2022年8月5日 Coking is a process in which raw materials are thermally decomposed into products with lower boiling points Different types of coking processes include delayed coking, fluid coking, and flexicoking Delayed Old Short Fireboxes do not Accommodate New Longer Burner Flames without Impacting the Coker Heater Operation A Combined Review of the Process and the Heater Design is Coker Heater Design The Heart of the Coking Process Refining 2021年10月1日 This study provides a review on research for improving the properties and qualities of coking coal and metallurgical coke using preheating Factors such as coal type, Effect of preheating on coking coal and metallurgical coke 2018年4月1日 During heating of vacuum residue in coker furnace, coke is continuously deposited in furnace tubes which is removed at regular intervals by one of the three methods Effect of composition of coke deposited in delayed coker furnace
.jpg)
Composition, characteristics, and treatment technologies of
2024年4月12日 To study the total particulate matter (TPM) in flue gas emitted by coking plants, a sampling system that could be used to collect filterable particulate matter (FPM) and 2019年11月14日 Coke, the product of a coking process, is an important material in the metallurgical industry In a blast furnace that produces iron, it functions as the main supplier of Intelligent Optimization and Control of Coking ProcessTo isolate iron sulphide and reduce coke adhesion reactions that occur on the surface of a delayed coking furnace, a SiO2 coating was developed on Cr9Mo alloy by employing the Preparation and anticoking application of sol–gel SiO2 coating in 2024年7月23日 Among the features of coking, particular attention is paid to the poor thermal conductivity of the coal charge, which sets limits on the design Photographs of coke samples Physical Modeling of Heat and Mass Transfer in Laboratory Coking
.jpg)
Stateoftheart of Coke Formation during Steam Cracking: Anti
2018年10月24日 Coking tests demonstrate that a significant reduction in coke formation can be achieved using specialty coatings These advanced coatings are applied on the internal 2024年1月1日 Numerical study on oxyfuel combustion characteristics of industrial furnace firing coking dry gas Author links open overlay panel Gaofeng Fan a , Meijing Chen a , Chang’an Wang a , Qinqin Feng a , Yunlei Sun c , Jie Xu b , Yongbo Du a , Defu Che aNumerical study on oxyfuel combustion characteristics of 2022年7月22日 During the coking process in an ethylene furnace, the residue feed is converted to gas, light and medium distillates, and coke with no production of residual oil Reliably detecting excessive coking in the cracking tubes is critical to achieving optimal How to Improve Your Coke Monitoring and Decoking ProcessCoking is the process of heating coal in the absence of oxygen to a temperature above 600 °C (1,112 °F) to drive off the volatile components of the raw coal, leaving behind a hard, strong, porous material with a high carbon content Coking Wikipedia
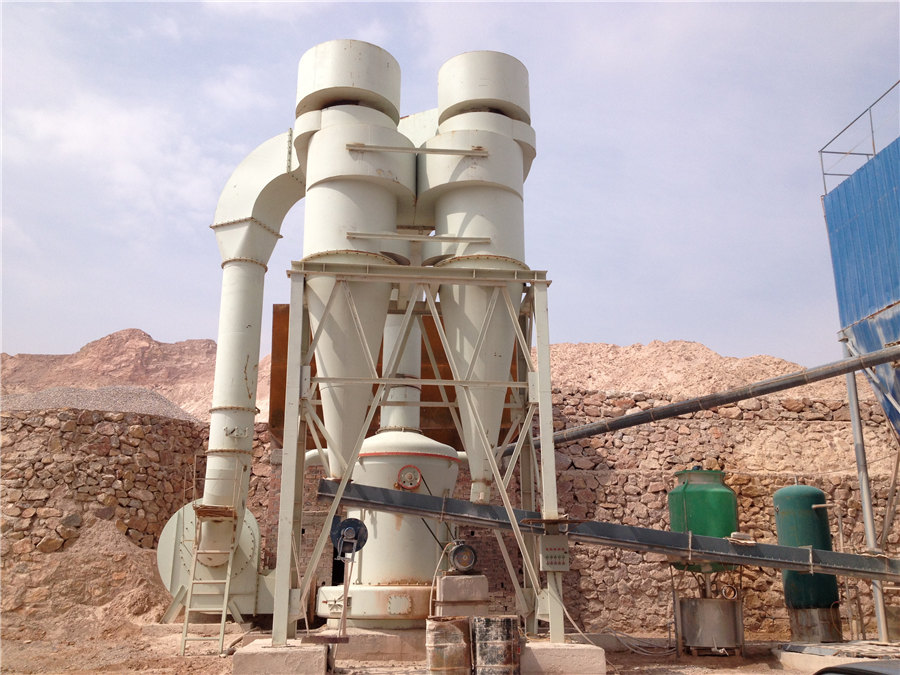
Effect of preheating on coking coal and metallurgical coke
2021年10月1日 In the coking process, the properties of coking coal, such as the CP and ash content, primarily control the coke quality [1, [7], [8], [9]] In coal blending, to ensure good coke quality, the proportion of highquality coking coal with a strong CP is significantly higher than that of slightly or noncaking coal, with 20% as the upper limit for the proportion of lowquality coal 2024年3月8日 Experimental results demonstrate that this method exhibits strong performance in the monitoring of industrial coking furnaces, The authors declare that they have no conflict of interest Open Research DATA AVAILABILITY STATEMENT The data that support the findings of this study are available from the corresponding author upon Enhanced process monitoring for industrial coking furnace using 2008年1月1日 An adaptive state feedback predictive control (SFPC) scheme and an expert control scheme are presented and applied to the temperature control of a 1200 kta −1 delayed coking furnace, which is the key equipment for the delayed coking process Adaptive SFPC is used to improve the performance of temperature control in normal operationAdaptive State Feedback Predictive Control and Expert Control 2023年9月1日 This Best Practice specifies the major requirements of ethylene furnace decoking provides guidelines on some issues Ethylene is produced by thermal cracking of hydrocarbons (Ethane/Propane/Butane BEST PRACTICE FOR ETHYLENE FURNACE DECOKING
.jpg)
Numerical study on oxyfuel combustion characteristics of
2024年1月1日 Hydrocarbylation offgas (HOG) and coking dry gas (CDG) were used for the present study According to the component content in CDG, each component is listed in order from the largest to the smallest, as shown in Table 2The N 2 content is 2063% in HOG, which hinders the possibility to obtain a high level of CO 2 in flue gas Hence, another type of 2024年6月1日 Machine learning approach with a posterioribased feature to predict service life of a thermal cracking furnace with coking deposition Author links open overlay panel Chanin Panjapornpon a, Chutithep Rochpuang a, Santi Bardeeniz a, Mohamed Azlan Hussain b Show more For all open access content, Machine learning approach with a posterioribased feature to 2024年4月12日 Sampling process Four stable coking furnaces—A, B, C, and D—of coking plants in North China were randomly selected The designed production capacity of coking furnaces A and B was 15 million Composition, characteristics, and treatment technologies of2023年5月2日 The main tasks of coking, sintering, and ironmaking processes at Severstal in 2017–2022 are specified The operation of the production complex until 2020 as part of “traditional” units of classical designs is described The assimilation of new facilities based on an essentially different technology in 2020 to 2022 is shown The results of blastfurnace Development of the Coking, Sintering, and BlastFurnace
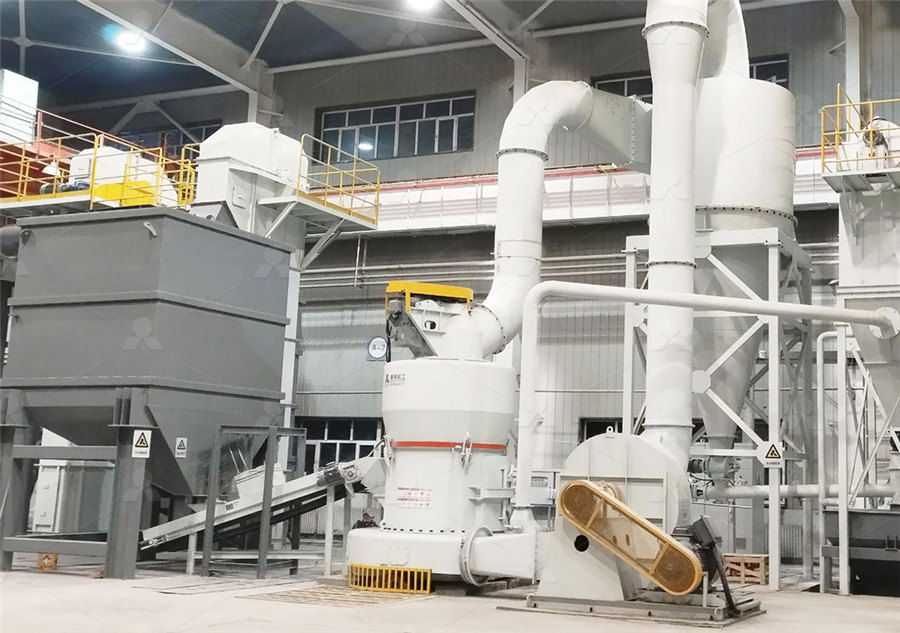
Improving Tube Furnaces for Delayed Coking Coke and Chemistry
2023年7月23日 The influence of the parameters of a tube furnace for delayed coking on the pressure drop, critical temperature, and salt content of the coil is investigated A mathematical model of the furnace is proposed Optimal coil parameters are determined The parameters of the furnace have a significant influence on the operational safety, the coke buildup within the 2022年1月1日 Superior quality coke with low CRI (Coke Reactivity Index) and high strength is indispensable for the safe and efficient operation of the blast furnaceThe hot tamping coking technology is comprehensively investigated when the coal samples undergo plastic stage to improve the coke quality and save the coking coal resource The influences of the tamping Coke characteristics and formation mechanism based on the hot 2015年12月27日 The introduction of DK coking additive to the coal batch improves the metallurgical properties of the coke produced The quality of coke produced exclusively from DK additive permits its effective use When introduced in the axial zone of the charge hole, it forms an axial ventilation region and thus the hearth may be packed with coke that is not susceptible to Innovations in blastfurnace coke Steel in Translation Springer2016年3月16日 5 MY: 301 Steel Making Processes Page 5 of 5 i) Fettling: The furnace lining gets eroded because of the action of the slag and/or metal, particularly at the slagmetal interface line It is repaired after every heat this is called fettling It is to be done to improve the furnace life Earlier it was done manually but now fettling machine do the job very efficiently Granular Steel Making: Lecture open hearth furnace PDF SlideShare
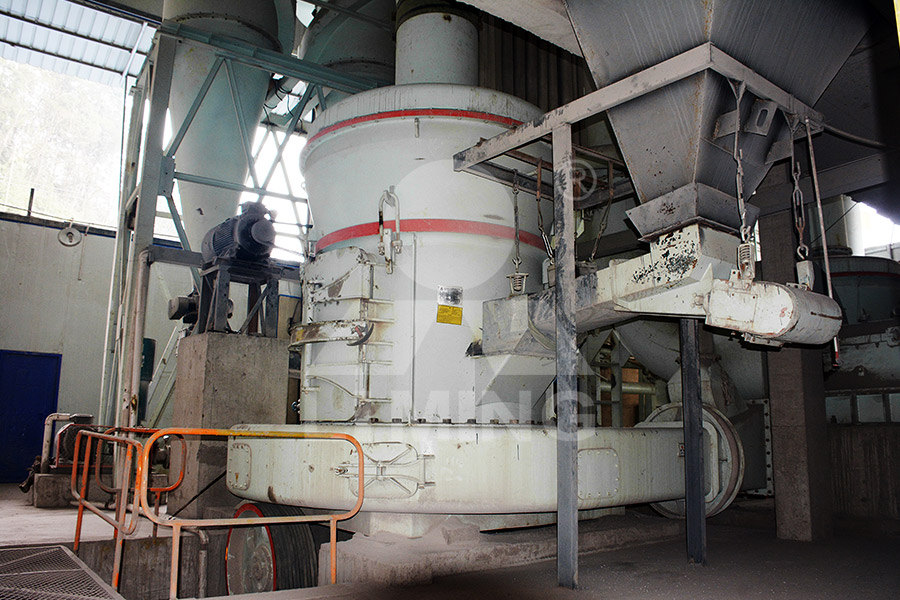
Preparation and anticoking application of sol–gel SiO2 coating in
2021年3月5日 To isolate iron sulphide and reduce coke adhesion reactions that occur on the surface of a delayed coking furnace, a SiO 2 coating was developed on Cr9Mo alloy by employing the sol–gel method The coating was characterised through Fourier transformation infrared spectroscopy, Xray diffraction, scanning electron microscopy, energy dispersive 2015年2月1日 The causes and characteristics of the massive failure of the radiant coil tubes in an ethylene cracking furnace, which failed during an emergency nonprogrammed stop, are investigated (see Fig 1) [1]This analysis leads to establish material, manufacturing and assembly quality on one hand, and to determine operative conditions that contributed to the failure, on Effect of coking in massive failure of tubes in an ethylene cracking Thermal processing is the most common refining technique for heavy residues Thermal processing techniques include delayed coking, fluid coking , flexicoking , and visbreaking ; of these, delayed coking is by far the most common method of thermal processing, with the ability to produce motor fuels from vacuum tower bottoms with a minimum of capital expenditureDelayed Coking SpringerLink2022年8月5日 PDF Currently, conventional oil is used as the main source for the petrochemical industry However, conventional oil’s capacity is declining, and that Find, read and cite all the research (PDF) Coking ResearchGate
.jpg)
ISCO Occupation Group 81313 Coking Furnace Operator
Definition Coking Furnace Operator: Coking furnace operators monitor the operation of a usually automatic industrial oven that takes in crushed, washed, and blended bituminous coal and heats it to temperatures between 1000 and 2000 °C without the presence of oxygen in order to obtain cokesThe finished cokes are then quenched with water or air and prepared for transport2019年11月14日 The process information contains the operating time of a single furnace, coking time, coaling time, and cokepushing time the scheduling of the coking operations is an open path because each coking chamber can only be pushed once To construct a closed loop, we introduce a virtual node that is both starting and ending nodesIntelligent Optimization and Control of Coking Process2017年10月1日 Ethylene cracking furnace is the key equipment in petrochemical industry Coking within coils in radiation section mainly affects the life span of ethylene cracking furnace During industrial production, engineers periodically measure the radiant coil surface temperature which reflects the degree of coking, in order to decide time for decokingStaff View: Coking Analysis Based on the Prediction of Coil Surface 2017年3月22日 In the petrochemical industry, an industrial pyrolysis furnace is a complicated piece of equipment that functions as both a reactor and highpressure steam generator During service, hard deposits of carbon (coke) Coke formation in pyrolysis furnaces in the
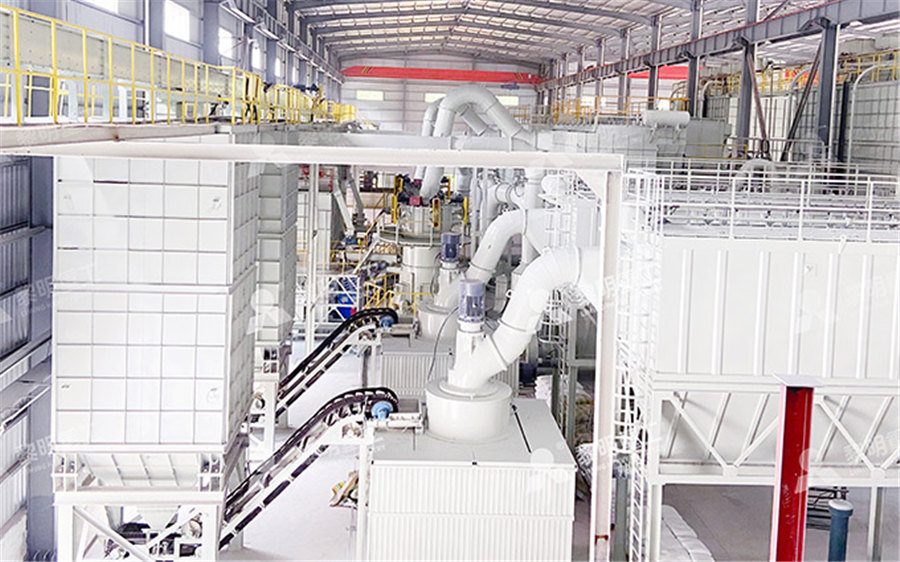
Computational fluid dynamics simulation on oxyfuel combustion
2024年9月1日 Computational fluid dynamics simulation on oxyfuel combustion performance of a multipleburner furnace firing coking dry gas Author links open overlay panel Tianlin Yuan a, Chang’an Wang a, Qinqin Feng Analysis of the effect of rigid vegetation patches on the hydraulics of an open channel flow with Realizable kε and 2015年2月1日 In this setup, specimens were placed in a tube furnace, exposed to Ethane (C 2 H 6) and Argon gases as the primary feedstocks, using optimized parameters Results of the coking test showed that the bare steel was largely covered with catalytic coke; while enhanced performance was observed for the gas phase aluminide coated steelsEffect of coking in massive failure of tubes in an ethylene cracking Keywords: Open top anode baking furnace; furnace reline; anode production; refractory design and installation; firing cycle 1 Introduction Anode Baking Furnaces (ABF) are one of the most critical equipments operated in an aluminium smelter and can generate high operational expenses In order to reduce smelter costs,Considerations for Selecting an Open Top Anode Baking Furnace 2019年12月3日 The carburizing and coking of ethylene cracking furnace tubes are the important factors that affect the energy efficiency of ethylene production To realize the diagnosis and prediction of the different coking degrees of cracking furnace tubes, and then take corresponding treatment measures, is of great significance for improving ethylene production and prolonging ABCANFISCTF: A Method for Diagnosis and Prediction of Coking
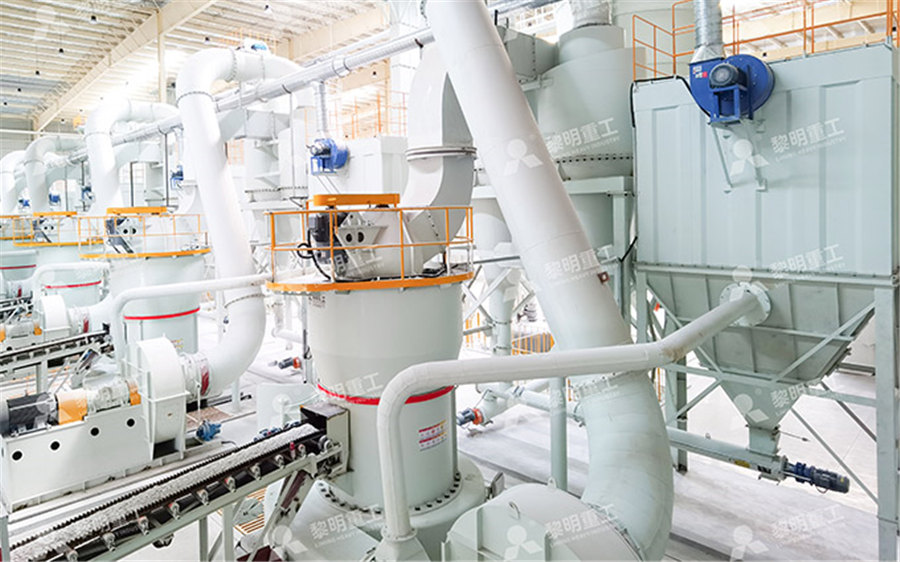
Coke Formation Model in Crude Oil Furnace for ScienceDirect
2018年1月1日 The crucial issue found in the furnace is carbon coking, which occurred at the innerside of the crude oil tube in the furnace during the preheating process The carbon coking and coating of the inner tube leads to the coke accumulating, the product quality deteriorating, the pressure drop increasing across the furnace, the energy consumption increasing, and the tube Avoid fired heater coking For many refiners, heater coking in Crude and Vacuum Distillation Units (CDU/VDUs) is a common occurrence Many units around the world are shut down every two years, every year, or even every six months to deal with chronic heater cokingAvoid fired heater coking DigitalRefining2023年12月15日 Endothermic hydrocarbon fuels are promising propellants in advanced aircraft due to their excellent energy density and cooling properties [1, 2]Active cooling technology utilizes the great endothermic ability of the fuel during supercritical thermal cracking to remove the waste heat, whereas, accompanying severe coking behavior hinders its application [3, 4]The dominant role of surface chemistry on coking resistance of 2024年1月1日 Coking chemistry is the subject of relative theories, technologies, processes, and equipment of process where main material coal in the condition of isolating air is researched, and coal is transformed into coke (or semicoke) and raw gas after physicochemical action like thermolysis and coking, and the raw gas is purified and separated to obtain coal tar and Coking Chemistry SpringerLink
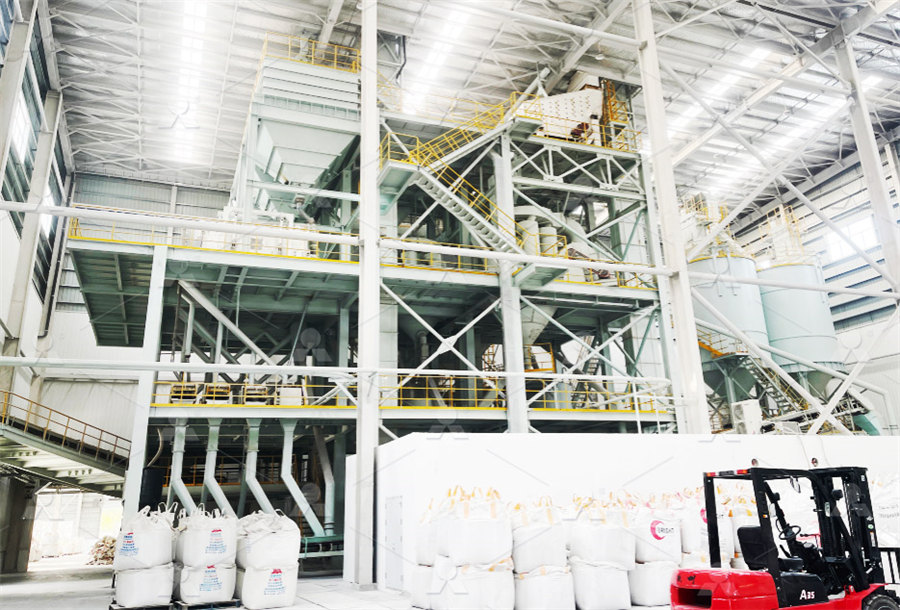
Career Guide: Coking Furnace Operator
Dive deep into the role of a Coking Furnace Operator! Uncover essential skills, career paths, and I am open to obtaining relevant certifications and furthering my education to enhance my skills as a Coking Furnace Operator Junior Coking Furnace Operator Career Stage: Typical Responsibilities 2022年1月1日 The properties of 1/3 coking coal used in the experiments are shown in Table 1 Firstly, 10 g crushed 1/3 coking coal with a particle size of less than 03 mm is charged into the cylindershaped crucible Then the crucible is placed into the furnace and heated to Coke characteristics and formation mechanism based on the 2018年10月24日 Over the 3 years, it was observed that the coking profile of the cracking furnace completely changed Only a small amount of HCG is required to gasify a significant amount of coke A sample taken from the coil after 14 months of service shows that the coating is in a similar condition as the “as produced” state, as shown in Figure 17Stateoftheart of Coke Formation during Steam Cracking: AntiCoking 2012年4月3日 Computer simulation of the coking process in coke furnaces provides information regarding the yield and quality of the coking products as a function of the temperature and the yield of volatiles from the batch The simulation includes calculation of the temperature in the heating channel from the nonsteady heatconduction equation of the coal bed in the furnace Simulation of coking in coke furnaces Coke and Chemistry
.jpg)
An Introduction to Fouling in Fired Heaters – Part 1 Interior
2021年9月15日 Solid particles like coke formed by the pyrolytic coking mechanism cover the catalytic sites and then takes over as the dominant mode of coke formation: It is used as ‘dilution steam’ in cracking furnaces to lower the hydrocarbon partial pressure and to reduce the residence time Typical steam to oil ratios are 02 So Furnace is not about Cooking the oponent, but rather, about using the Opponent as Fuel So sukuna chanting "Open" before using it is Sukuna opening the furnace to add more fuel usually Furnaces just work by themselves until you need to add more fuel, so Sukuna just "Opens it" when he needs to Fuel it to start burning stuff, or to refill it Sukuna's "Furnace"/"Stove" is not about cooking part Reddit2018年6月4日 An approach is proposed for assessing the coking properties and value of coal during prospecting, extraction, and deep processing, so as to objectively identify clinkering coal suitable for the production of blastfurnace coke As a trial, this approach is used in the assessment of clinkering and poorly clinkering coal of different maceral composition and Assessing the Coking Properties and Value of Coal for BlastFurnace A significant number of refineries experience accelerated fouling in their delayed coking unit (DCU) furnaces, in many cases from asphaltenic feedstocks Feeds to a DCU have traditionally come from the crude unit’s vacuum distillation tower bottoms, which contain a high concentration of asphaltenes High heat flux, feedstock quality (eg, asphaltenes), and increased throughput Coking » Avoiding DCU Furnace Fouling
.jpg)
Revamping a delayed coking unit Chemistry and Technology of Fuels
2010年11月16日 A delayed coking unit was revamped with separation of the streams from the onechamber, doubleflow coking furnace into two separate coking blocks A closed system for heating the coke chambers was implemented, eliminating harmful atmospheric emissions A set of measures was instituted that allowed reducing the yield of coke and heavy gasoil, increasing