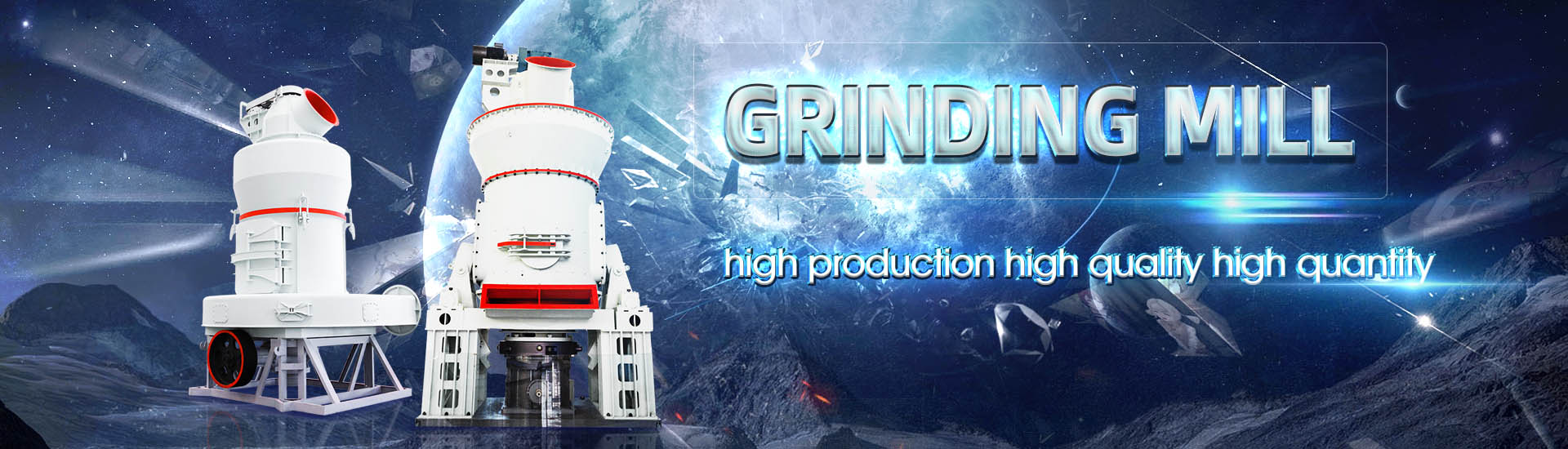
Cement grinding station process flow diagram
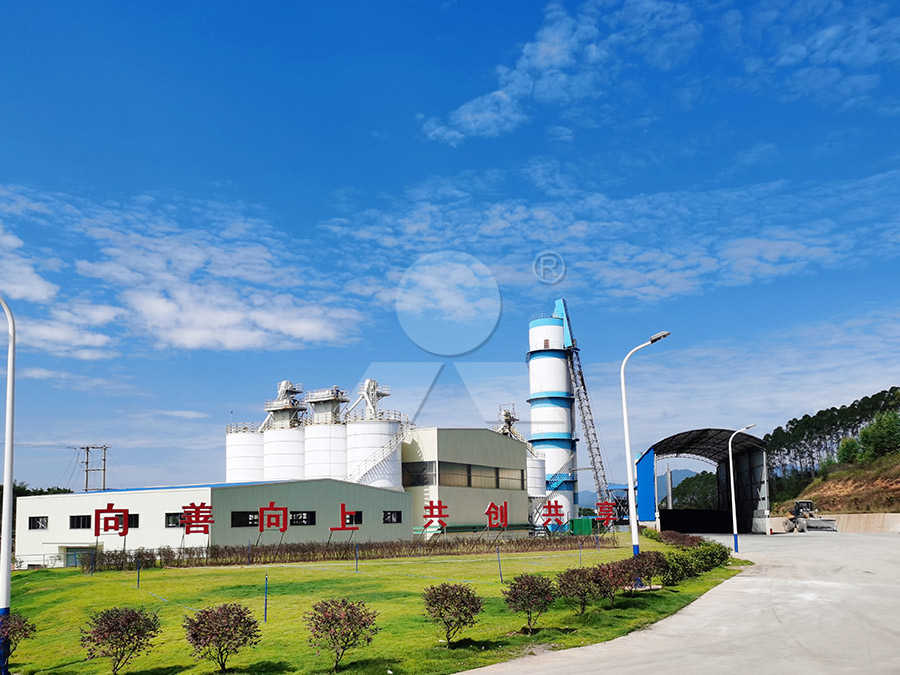
Typical cement manufacturing process flow diagram
The purpose of this study is to examine the production process, its economic support, raw material availability, demand, process modification, optimization steps to implement the production According to [39], Figure 4 provides a process flow diagram of the general cement production process and the associated inputs, during various steps of the production processProcess flow diagram for the cement manufacturing Explore Amrit Cement's stateoftheart cement grinding unit Learn about our cement grinding process and plant stages for high quality cementCement Grinding Unit Process High Quality Cement Figure 1 shows the detailed process flow diagram of the cement plant The consistency of the measured data is proved much better, and the balance shows clearly where the heat isProcess Flow Diagram of the Cement Plant
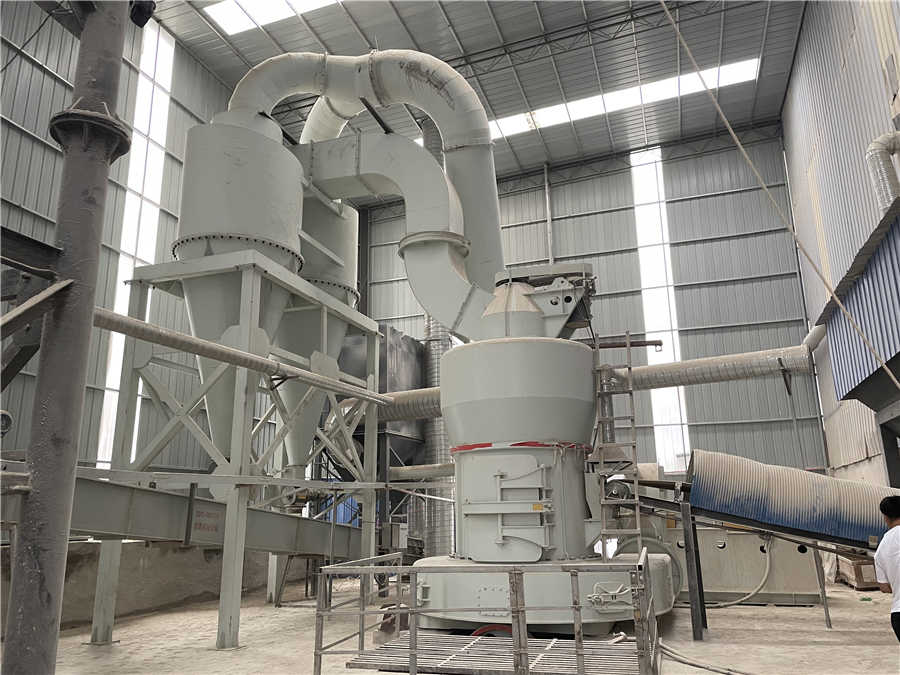
116 Portland Cement Manufacturing US Environmental
Five different processes are used in the portland cement industry to accomplish the pyroprocessing step: the wet process, the dry process (long dry process), the semidry The Cement Plant Operations Handbook is a concise, practical guide to cement manufacturing and is the standard reference used by plant operations personnel worldwide Providing a The Cement Plant Operations Handbook International Cement An evaluation of the grinding system and operation includes meaningful and critical inspection of all equipment, components and the process parameters by experts PEC Consulting can help OPTIMIZATION OF CEMENT GRINDING OPERATION IN BALL MILLS1971年8月17日 A diagram of the process, which encompasses production of both portland and masonry cement, is shown in Figure 1161 As shown in the figure, the process can be 116 Portland Cement Manufacturing US EPA
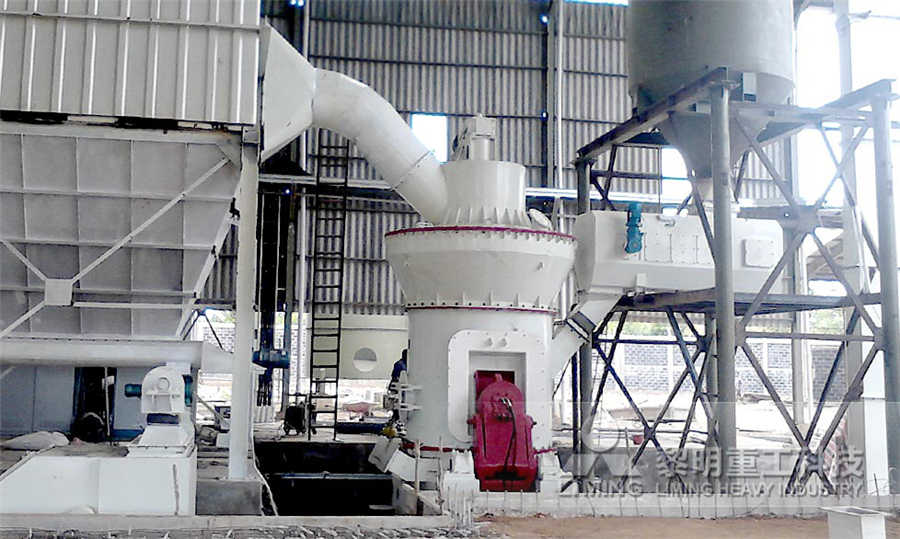
How Cement is Made Cement Manufacturing Process
Stage 2: Grinding, Proportioning, and Blending The crushed raw ingredients are made ready for the cementmaking process in the kiln by combining them with additives and grinding them to ensure a fine homogenous mixture The composition of cement is proportioned here depending on the desired properties of the cement Generally, limestone is 80%, and the remaining 20% In this study the process flow diagram for the cement production was simulated using Aspen HYSYS 88 software to achieve high energy optimization and optimum cement flow rate by varying the flow The cement raw material blending process and its control system2014年6月10日 Evolution of the cement Process • Wet process easiest to control chemistry better for moist raw materials • Wet process high fuel requirements fuel needed to evaporate 30+% slurry water • Dry process Cement manufacturing process PPT Free Download9 Cement Grinding A closed circuit grinding system is applied The main equipment consists of a 46x12m double compartment tube mill and a sepax separator This mill at this time produces two types of cement namely Ordinary Portland Cement (OPC) and Pozzolana Portland Cement (PPC) OPC comprises 90%clinker, 5%additive (limestone) and 5 %( gypsum)Manufacturing process flow 1 Quarrying and Crushing Messebo Cement
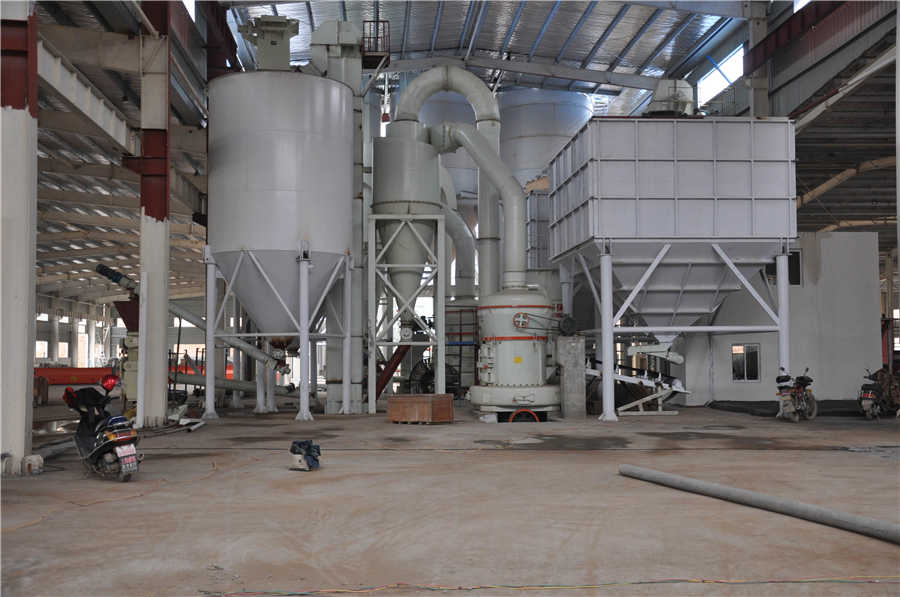
CEMENT GRINDING SYSTEMS INFINITY FOR CEMENT EQUIPMENT
The final manufacturing stage at a cement plant is the grinding of cement clinker from the kiln, mixed with 45% gypsum and possible additives, into the final product, cement In a modern cement plant the total consumption of electrical energy is about 100 kWh/t The cement grinding process accounts for approx 40% if this energy consumption2019年11月30日 Significant advancements have been made in raw material grinding, preheating, controlled clinker cooling, cement grinding, and packing technologies with advanced process control and instrumentation system in recent yearsManufacture Of Portland Cement Process Flow chart civil Download scientific diagram Process Flow Diagram of the Cement Plant from publication: Energy audit of thermal utilities in a cement plant Energy Audit and Thermal ResearchGate, the Process Flow Diagram of the Cement Plant ResearchGateThe flow diagram of a typical cement manufacturing process is shown in Fig 1 [3] Finally produced cement is transported in bags (packages) or as a bulk powder Table 1 shows the cement Cement manufacturing process flow diagram [3] ResearchGate
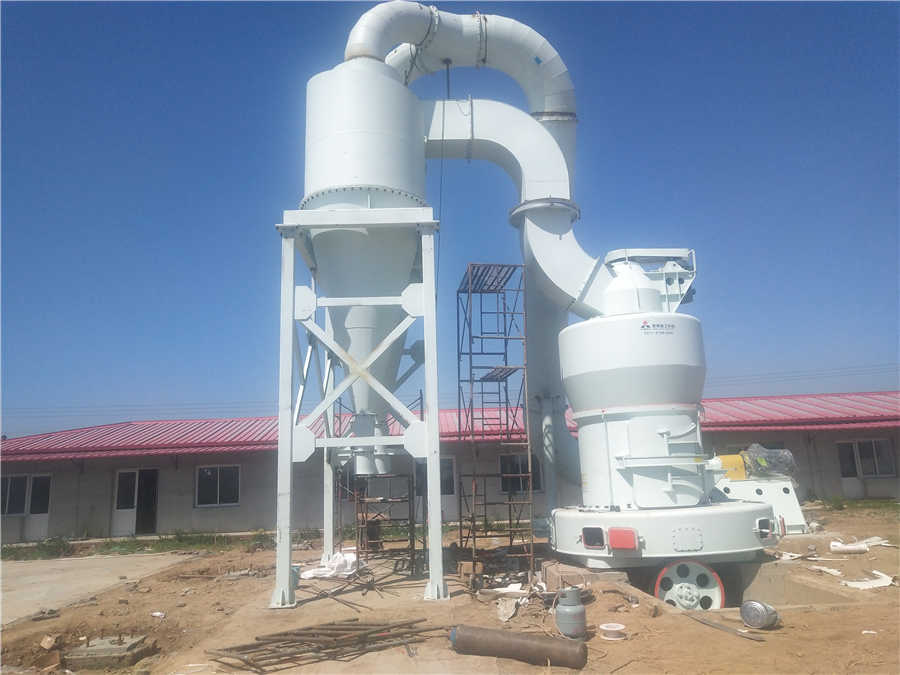
Simulation and Optimization of an Integrated Process Flow Sheet
2021年3月9日 In this study the process flow diagram for the cement production was simulated using Aspen HYSYS 88 software to achieve high energy optimization and optimum cement flow rate by varying the flow rate of calcium oxide and silica in the clinker feed Central composite Design (CCD) of Response Surface Methodology was used to design the ten experiments for Condition in one of the grinding chambers of the mill Results of Optimization The graphical analysis presented in Figure 2 represents progress of grinding along the length of the mill after optimizing the grinding process rogress of grinding is clearly visible in Desired p the graphs Figure 2: Analysis of longitudinal samplesOPTIMIZATION OF CEMENT GRINDING OPERATION IN BALL MILLS2021年3月9日 In this study the process flow diagram for the cement production was simulated using Aspen HYSYS 88 software to achieve high energy optimization and optimum cement flow rate by varying the flow Simulation and Optimization of an Integrated Process Flow Sheet Download scientific diagram Flow chart of the grinding and blending process from publication: Effective Optimization of the Control System for the Cement Raw Meal Mixing Process: I PID Tuning Flow chart of the grinding and blending process
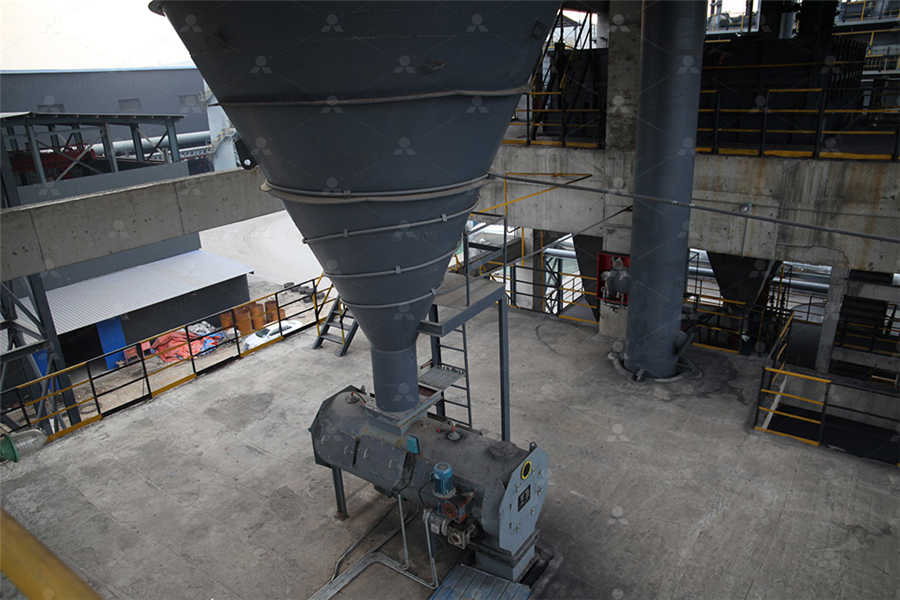
Wet Process Of Cement Manufacturing With Flow
As the perflow diagram of the wet process of cement manufacturing, the rotary kiln is an essential and important component of a cement manufacturing factory 6 It is made of a thick steel cylinder of diameter anything from 3 meters to 8 Cement grinding process The whole workflow of the cement grinding plant is as follows: the cement clinker, gypsum, and mixture in the cement silo are mixed by the belt conveyor in a certain proportion and transported to the cement roller press, cement mill or group of them for grindingCement Grinding Plant Overview Cement Grinding Unit AGICO CementEarly hydraulic cements, such as those of James Parker, James Frost and Joseph Aspdin were relatively soft and readily ground by the primitive technology of the day, using flat millstonesThe emergence of Portland cement in the 1840s made grinding considerably more difficult, because the clinker produced by the kiln is often as hard as the millstone materialCement mill Wikipediaprocess engineering for the cement lime industries mechanical engineering (plant design, piping, process gas handling, environmental controls, nuisance dust collection and materials handling, crushing and grinding systems) in engineering, we offer key disciplines for process calculations and flow diagrams process selection and equipment PROCESS ENGINEERING FOR THE CEMENT LIME INDUSTRIES

Clinker Grinding Techniques in Cement Manufacturing JM
2023年10月19日 Therefore, efficient grinding techniques and technologies are employed to minimize energy use and reduce production costs, contributing to the sustainability of the cement industry Types of Clinker Grinding Techniques used in cement manufacturing process Clinker grinders are an important part of the cement manufacturing process2013年8月30日 After 1982 all the cement manufacturing plants in India are equipped with the technologies of Dry process, since this is more energy efficient and environment friendly method of cement manufacturing In this post I am sharing with you the flow diagram of the wet process of the mixing because it is in the syllabus of the many Diploma coursesWet process Cement manufacturing Flow Diagram2020年8月25日 A full cement production process includes the cement crushing process, raw mill process, clinker process, and cement grinding process, cement packing process, and related process Find more! Skip to content +86 s about blog contact EN ES Menu Menu Home;Cement Production Process Cement Manufacturing Process AGICO CEMENTwith essential process calculations Contents Section A – Process summaries 1 Introduction 10 1 The basics of cement manufacture – 2 History of cement manufacture – 3 Portland cement in today’s world 2 Raw materials management system – 22 Concrete problems 16 1 Raw materials – 2 Raw mix – 3 Reserves – 4 Crushing – 5 The Cement Plant Operations Handbook International Cement

Cement Grinding Cement Plant Optimization
Cement grinding operation may be performed in one of the following mill setups (ThyssenKrupp) A simplified process flow these separators is as follows Material is fed onto a rotating dispersion plate via air slide, whence it is dispersed off into the classifying air stream2020年10月5日 12 Working In case of continuously operated ball mill, the material to be ground is fed from the left through a 60° cone and the product is discharged through a 30° cone to the right As the shell rotates, the balls are Cement industry : grinding process of ball mill PPTThe cement manufacturing process starts from the mining of raw materials that are used in cement manufacturing, mainly limestone and clays A limestone quarry is inside the plant area and a clays quarry is as far from the plant area Manufacturing process LafargeDownload scientific diagram Stages in cement production flow chart [43] from publication: A review on kiln system modeling The purpose of this study is to evaluate performance cement of Stages in cement production flow chart [43] ResearchGate
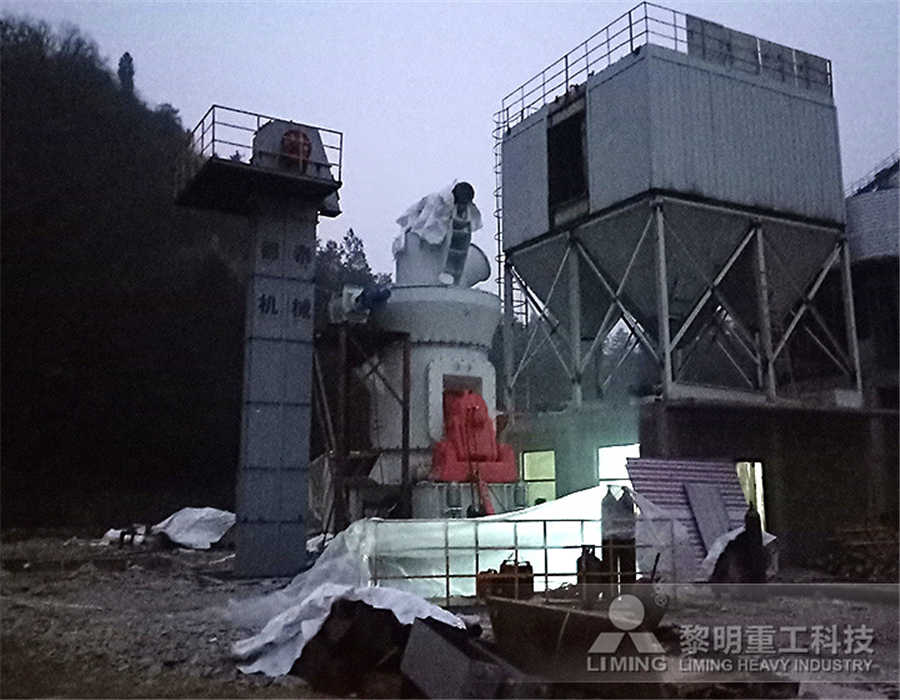
(PDF) Process Automation of Cement Plant ResearchGate
2012年4月30日 grinding, blending, pyroprocessing, Plant Process Flow Diagram 2 There are three main categorized that generate air pollutants in the production process of cement manufacture: It is possible to have a diagram in your IELTS writing task 1 academic paper A diagram is also known as a process The diagram shown below is from IELTS Cambridge Book 8, Test 3 IELTS Diagrams IELTS Diagrams come in two types: Type 1: Diagram about a Cycle This could be about a nature cycle or a life cycle Type 2: Diagram about a processIELTS Diagram: Model Answer Band Score 9 with TipsFig 1018 shows a flow diagram of a grinding plant with an F L Smidth cement cooler The F L Smidth cement cooler is manufactured for capacities up to 100 t/h; for this cooler size the con sumption of the cooling water is 65 m3/h, and the power input is 90 kWFinish grinding INFINITY FOR CEMENT EQUIPMENTManufacture Process of Cement The powdered limestone and water washed clay are sent to flow in the channels and transfer to grinding mills where they are completely mixed and the paste is formed, ie, known as slurry The grinding process can be done in ball or tube mill or even bothManufacture of Cement Materials and Manufacturing Process of
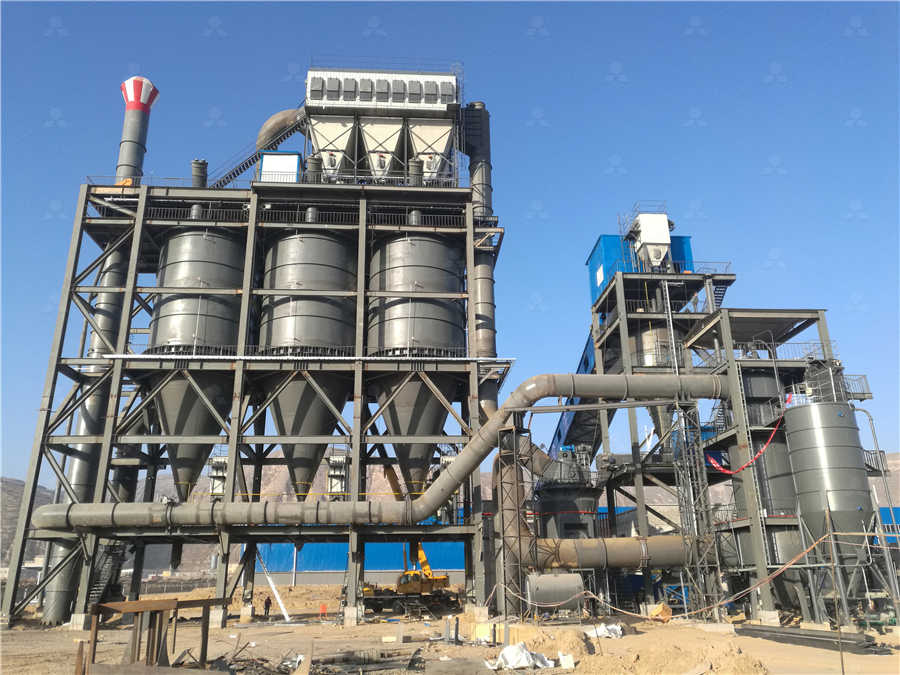
Everything you need to know about clinker/cement Grinding
Everything you need to know about clinker/cement Grinding if You read and understand this article , you will be ready to be a cement grinding area manager FEED AND FEED SYSTEM Feed Temperature Plants with satellite coolers have high clinker temperatures: eg Cumarebo, Oujda Exit satellite cooler 200250°C Exit grate cooler 100150°C2015年8月1日 The results show that approximately 248t, 469t, and 341t of materials are required to produce a ton of the product in raw material preparation, clinker production, and cement grinding stages Analysis of material flow and consumption in cement production processmills for drygrinding the abovementioned grinding stock Loesche has developed and built the largest and most efficient grinding plants for its customers Loesche plants are specifically planned for the required process steps and equipped with the associated techno logy This technology comprises: • Processing plants and material storagePROCESS OPTIMISATION FOR LOESCHE GRINDING PLANTSThe flow diagram of a typical cement manufacturing process is shown in Fig 1 [3] Finally produced cement is transported in bags (packages) or as a bulk powder Table 1 shows the cement Cement manufacturing process flow diagram [3]
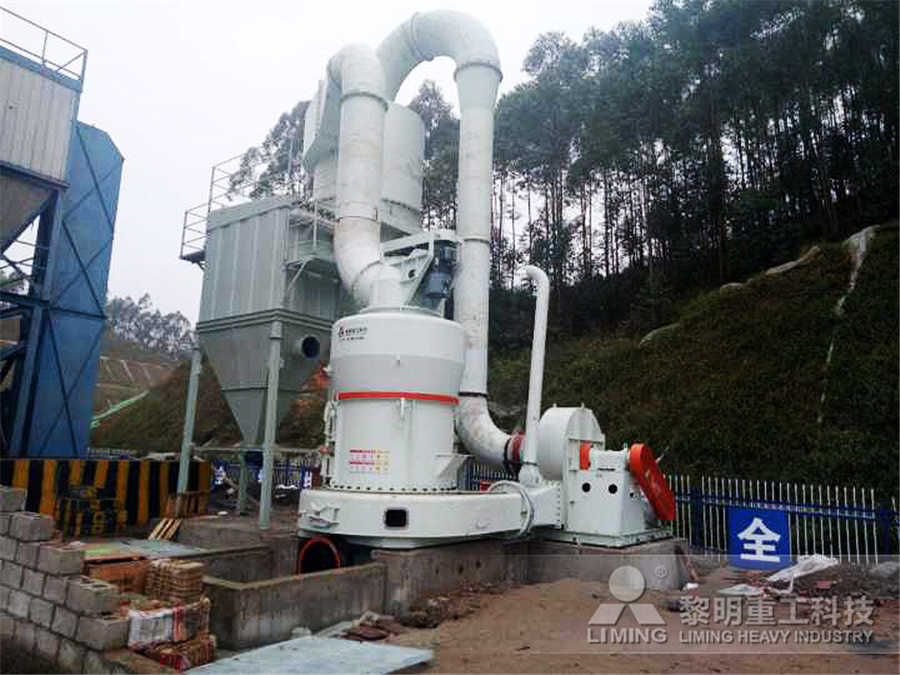
Cement Grinding Unit Cement Grinding Plant
AGICO Cement is a cement equipment manufacturer supplies EPC projects for cement grinding station with a simple process, easy operation, low investment Get a FREE quote now! Skip to content +86 info@cement Grinding Unit Nearest Railway station : Athipattu ,23 km from the plant Nearest Airport : Cement grinding, Wagon Tippler storage Wagon Tippler Operation Cement Mill Operation Packer Operation Truck/Bulk loading Operation CGU –PROCESS FLOW DIAGRAM ` 6 CGU –Sep 2023 Ramesh babu SP INDIA Z U A R I C E M E N T L I M I T E D “24th National Award for Excellence in Green Business Centre2016年1月20日 In the surveyed cement plant, three balances are established between input and output material in the raw mill, clinker production, and cement grinding system 248 t, 469 t, and 341 t of materials are required to produce a ton of the product in raw material preparation, clinker production, and cement grinding stages; waste gases account for the largest proportion of the Analysis of material flow and consumption in cement production process Chemical process industries are running under severe constraints, and it is essential to maintain the endproduct quality under disturbances Maintaining the product quality in the cement grinding process in the presence of clinker heterogeneity is a challenging task The model predictive controller (MPC) poses a viable solution to handle the variability This paper addresses the Predictive Controller Design for a Cement Ball Mill Grinding Process
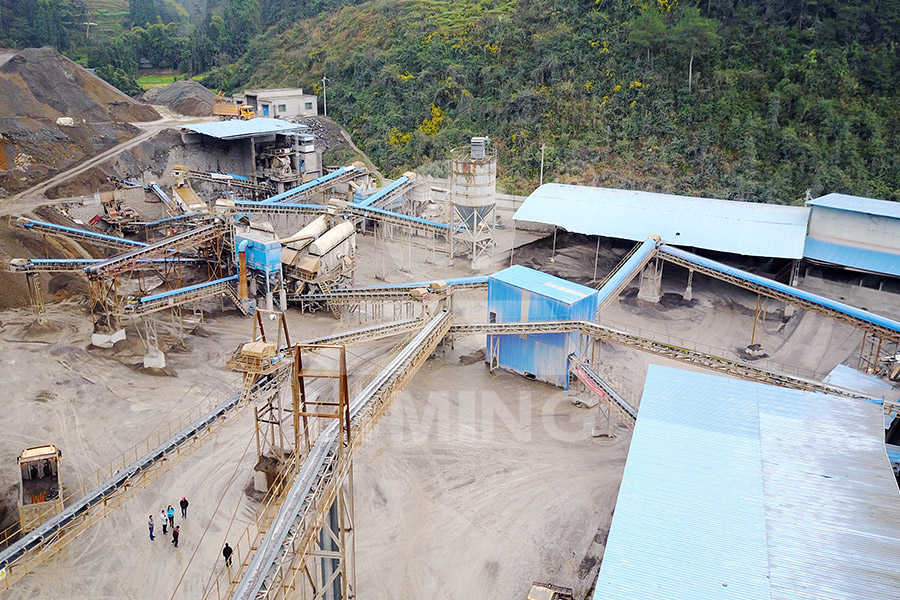
Manufacturing of Cement By Dry and Wet Process Expert Civil
Burning: In this operation, the slurry is directly fed into a long inclined steel cylinder called a Rotary kilnIn this kiln there are 3 different zones shown in fig below Cement Manufacturing Process Flow Chart (i) Drying Zones: In the wet process, the drying zone is comparatively larger than the dry process It is because the raw material in slurry form is directly fed into the kiln 2017年8月15日 To produce powdered cement, the nodules of clinker are ground to the consistency of powder Grinding of clinker, together with additions of approximately 5 percent gypsum to control the setting properties of the cement can be done in ball mills, ball mills in combination with roller presses, roller mills, or roller pressesThe Cement Manufacturing ProcessThe power ingesting of a grinding process is 5060% in the cement production power consumption The Vertical Roller Mill (VRM) reduces the power consumption for cement grinding approximately 3040% associated with other grinding mills The process variables in cement grinding process using VRM are strongly nonlinear and having large timePROCESS CONTROL FOR CEMENT GRINDING IN VERTICAL 2024年9月10日 Steps of Cement Manufacturing The steps involved in cement manufacturing are as follows: Quarrying: Raw materials such as limestone and clay are extracted from quarries or mines; Crushing and Grinding: The extracted raw materials are crushed and ground into a fine powder; Blending: The crushed and ground raw materials are blended in specific proportions Cement Manufacturing Process: Know Extraction, Processing