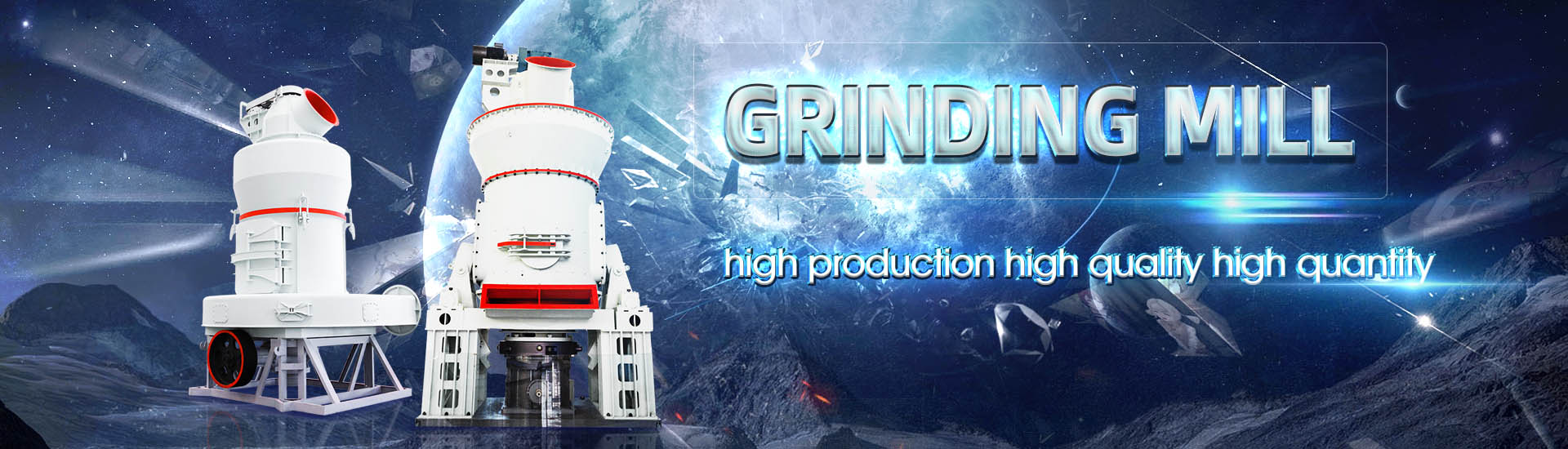
Rationalization suggestions for cement grinding, for the purpose
.jpg)
OPTIMIZATION OF CEMENT GRINDING OPERATION IN BALL MILLS
The purpose of the diaphragm is to retain the grinding media in their central respective chambers, provide adequate opening for the airflow and, in some special types, regulate the feed to the second compartmentGrinding aids are organic compounds that are added to the mill during cement grinding Their main purpose is to reduce the energy required to grind the clinker into a given fineness In Grinding aids for high performance cements CADD MapeiThomas Holzinger, Holzinger Consulting, discusses cement grinding system optimisation Introduction The cement industry uses a wide range of different systems in raw material, coal, Thomas Holzinger, Holzinger Consulting, grinding system There is potential to optimise conventional cement clinker grinding circuits and in the last decade significant progress has been achieved The increasing demand for “finer cement” products, (PDF) Cement grinding optimisation Alex Jankovic Academia
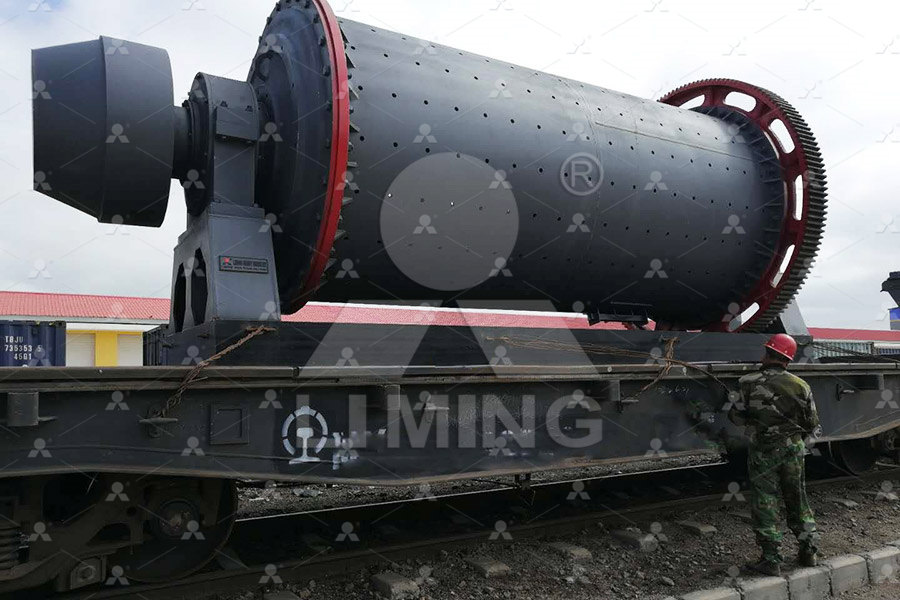
DOUDCGAN: Optimization of cement grinding operational
Targeting the problems of multiple equivalent optimal solutions and easy to fall into local optimal solutions in Paretobased optimization algorithms, this paper proposes a new optimization 2004年11月1日 To optimise cement grinding, standard Bond grinding calculations can be used as well as modelling and simulation techniques based on population balance model (PBM) Cement grinding optimisation ScienceDirectOptimization addresses the grinding process, maintenance and product quality The objective is to achieve a more efficient operation and increase the production rate as well as improve the run Optimization of Cement Grinding Operation in Ball Mills PEC 2018年7月1日 This study aimed at optimizing both the energy efficiency and the quality of the end product by modifying the existing flowsheet of the cement grinding circuit As a general Energy and cement quality optimization of a cement grinding circuit
.jpg)
(PDF) Cement grinding optimisation ResearchGate
2004年11月1日 green house gas emissions, reinforces the need for grinding optimisation This paper describes the tools available for the analysis and optimisation of cement grinding common solution to grind raw materials and cement Roller presses are used mainly in combination with a ball mill for cement grinding applications and as finished product grinding BALL MILLS Ball mill optimisation Holzinger ConsultingDOI: 102991/ssmi18201913 Corpus ID: ; Research on the Path of Rationalization Suggestion to Enhance Project Value under EPC Mode @article{Qian2019ResearchOT, title={Research on the Path of Rationalization Suggestion to Enhance Project Value under EPC Mode}, author={Cheng Qian}, journal={Proceedings of the 2018 International Symposium on [PDF] Research on the Path of Rationalization Suggestion to 2023年10月19日 Role of Clinker Grinding in Cement Production Clinker grinding is a vital and integral process in cement production, playing a crucial role in transforming clinker into the final cement product Here’s an exploration of Clinker Grinding Techniques in Cement
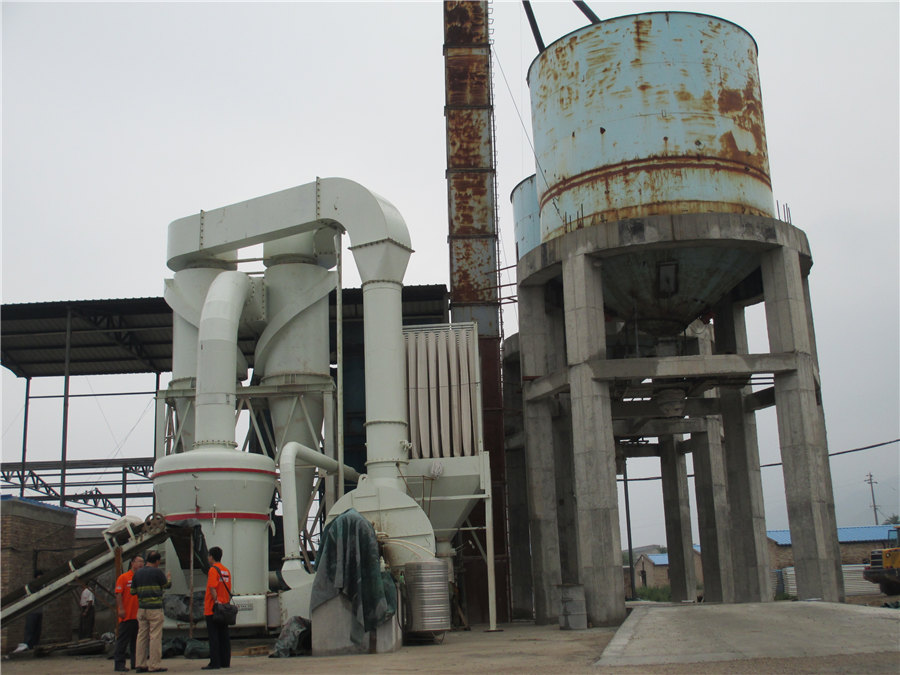
Improvements in New Existing Cement Grinding
o Finished grinding may consume 25 – 50 kWh/t cement, depending on the feed material grindability, additives used, plant design especially the required cement fineness Cement grinding is the single biggest consumer of electricity 2019年1月3日 Clinker grinding technology is the most energyintensive process in cement manufacturing Traditionally, it was treated as "low on technology" and "high on energy" as grinding circuits use more than 60 per cent of total energy consumed and account for most of the manufacturing cost Since the increasing energy cost started burning the benefits significantly, Clinker grinding technology in cement manufacturing2021年10月31日 Portland Cement is manufactured by adding 3% gypsum to clinker which is produced by grinding, pulverizing, mixing, and then burning a raw mix of silica, and calcium carbonate(PDF) Designing Raw Mix for Manufacturing Portland Cement Condition in one of the grinding chambers of the mill Results of Optimization The graphical analysis presented in Figure 2 represents progress of grinding along the length of the mill after optimizing the grinding process rogress of grinding is clearly visible in Desired p the graphs Figure 2: Analysis of longitudinal samplesOPTIMIZATION OF CEMENT GRINDING OPERATION IN BALL MILLS
.jpg)
The Use of Limestone in Portland Cement: A StateoftheArt
2003年6月5日 Required water:cement ratio to achieve a slump of 60 to 70 mm in concretes made with different cements Cement E contained a limestone not conforming to the EN 1971 criteria2017年5月19日 Grinding is an essential operation in cement production given that it permits to obtain fine powder which reacts quickly with water, sets in few hours and hardens over a period of weeks i Overview of cement grinding: fundamentals, additives, technologiesCEMENT GRINDING OPTIMISATION Dr Alex Jankovic, Metso Minerals Process Technology AsiaPacific, Brisbane , Australia email: alexjankovic@metso Dr Walter Valery, Metso Minerals Process Technology AsiaPacific, Brisbane, Australia Eugene Davis, Metso Minerals AsiaPacific, Perth, Australia ABSTRACT The current world consumption of cement is about (PDF) Cement grinding optimisation Alex JankovicSurvey of compound and closed circuit mills Virtually all the cement produced in the United States is ground in closed circuit grinding mills; ie finished cement grinding mills with a yearly produc tion capacity in 1982 of approximately 104 million short tons – not to take for real cement production are closed circuit separator grinding millsGrinding in closed circuit INFINITY FOR CEMENT EQUIPMENT
.jpg)
(PDF) EFFECTS OF VARIOUS GRINDING AIDS DOSAGE
2023年1月1日 In this study, the effects of four grinding aids with three different levels on the three important characteristics of the cement, namely the specific surface area, the compressive strength of the 2013年11月1日 The purpose of the study is to promote Portlandlimestone cement in countries where these cements are not usually used Materials characterization showed that the grinding quality of the seven The Effects of grinding on the properties of Portland Previous Post Next Post Contents1 KILN ALIGNMENT ROLLER GRINDING2 1 Hot kiln alignment using electronic devices21 11 Advantages of this Technique22 12 Tools and Instruments Used23 13 Measurement Procedures Using Total Station24 14 General Notes3 2 Grinding of rollers tyres31 21 Grinding Method32 22 Grinding Machine33 23 KILN ALIGNMENT ROLLER GRINDING INFINITY FOR CEMENT EQUIPMENTpurpose of testing MAGA/VM 10, one of the newly developed cement grinding additives for vertical rollers mill The present industrial test has been performed with the objective of enhancing the compressive strengths of a blended cement with a high slag content All the main cement characteristics are reported as follows:Improvement of cement performances through the use of grinding
.jpg)
Maintenance Performance Optimization for Critical Subsystems in Cement
2023年9月26日 case study, in this case, a cement grinding plant The study provides a pragmatic reference model framework to practitioners that enhances maintenance decisionmaking by identifying2021年2月1日 The purpose of the present investigation is to develop 100% cementfree Alkali Activated Slag Mortar (AASM) with binders Ground Granulated Blast Furnace Slag (GGBS) and Silica Fume (SF), with an (PDF) Optimization of Gypsum Composition Against Setting Time 2022年1月14日 The influence of grinding aids (pure triethanolamine and ethylene glycol) on the properties of cements, their compatibility with an acrylatebased superplasticizer and the rheological parameters The Effect of Various Grinding Aids on the Properties of Cement Ball race mill (Petersmill of the Claudius Peters Joint Stock Company, Hamburg, Germany) The cement industry employs the Petersmill (pre viously called FullerPetersmill) mostly for coal grinding It is a few years now that the shockproof construction (shock resistance – 35 bar) of the Petersmill was designed for coal grindingRoller mills INFINITY FOR CEMENT EQUIPMENT
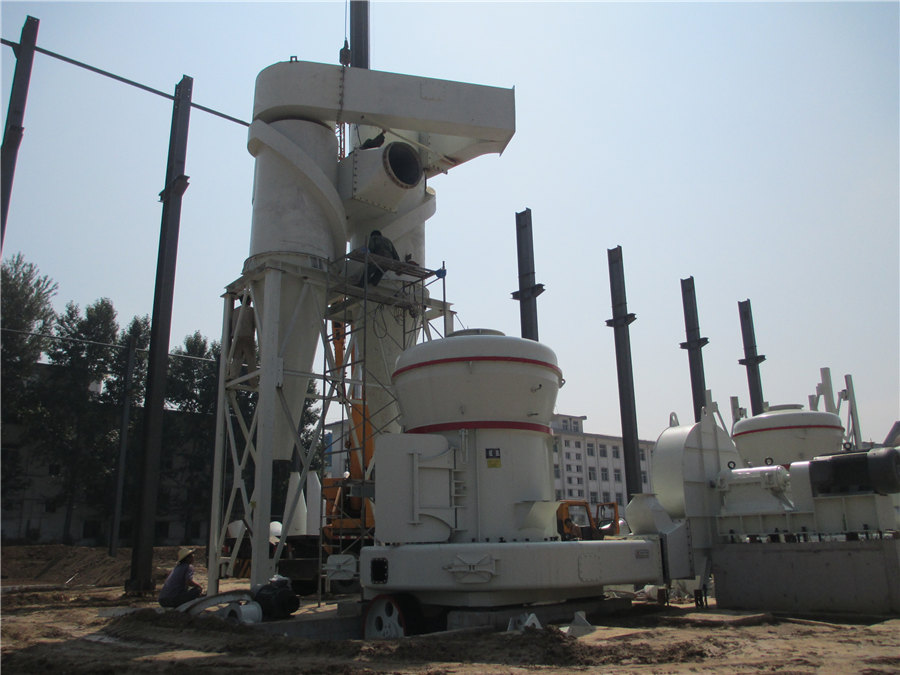
Diagnostic Study For Cement Mill Optimization PDF Mill (Grinding
Diagnostic Study for Cement Mill Optimization Free download as PDF File (pdf), Text File (txt) or read online for free The document discusses a case study of diagnostic studies conducted to optimize cement mill performance at a cement plant in India Key findings from the study include uneven grinding media distribution in the mill, high clinker fines and temperature being fed to 2016年10月23日 Exact proportioning is dependent upon their chemical properties before and after calcining to cement clinker For good kiln practice the grind required is 8892% – 200 mesh for standard cement, 99%200 mesh for high early Uniform kiln feed size helps reduce tendency to form kiln rings WET VS DRY Grinding of Cement Wet grinding is generally Cement Grinding 911Metallurgist2024年5月18日 Different geopolymer inputs have different physical and chemical characteristics depending on source or process from which they are made [2, 4, 8]High physical and chemical quality variability of materials even from the same source were noticed due to variations within raw material sources [1, 3]Different grindability of materials means different particle sizes for Application of Dry Grinding as an Optimisation Tool for the Intensifying the cement grinding process Mas’uda Mukhamedbaeva1, Abdugoffor Khurmamatov1*, and Abduvali Mukhamedbaev2 1Institute of General and Inorganic Chemistry of the Academy of Sciences of the Republic of Uzbekistan, Tashkent, Uzbekistan 2”ANTENNBRANCH” LLC, Tashkent, Uzbekistan Abstract This article deals with the intensification of the Intensifying the cement grinding process e3sconferences
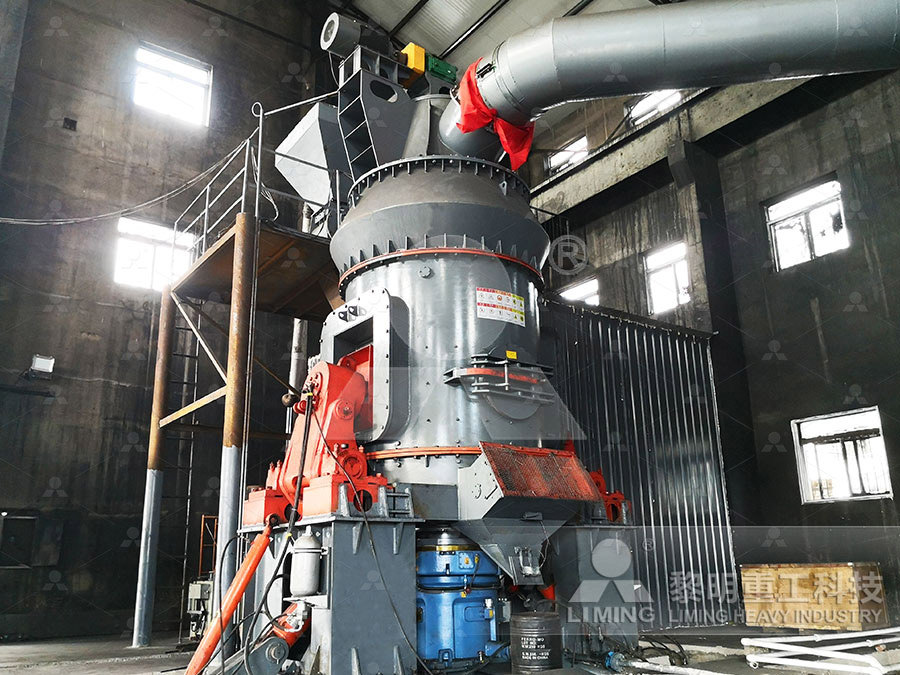
Coal Grinding Cement Plant Optimization
Most commonly used mills for coal grinding in cement plants are closed circuit air swept (Single chamber) ball mills and vertical mills Ball Mill: Single chamber ball mills (with classifying liners and dam ring) with drying chamber and static or dynamic separator are commonly existing for coal grinding in cement plant for one or more kilns as per capacityTAVERO® TAVERO® Grinding Aids are engineered to enhance the efficiency of the cement grinding process by reducing agglomeration and improving material flowabilityBy using TAVERO® Grinding Aids, manufacturers can increase mill output without incurring additional costs, while simultaneously reducing energy consumption and improving the particle size TAVERO® Grinding Aids for Cement Chryso North AmericaAGICO Cement is a cement equipment manufacturer supplies EPC projects for cement grinding station with a simple process, easy operation, low investment Get a FREE quote now! Skip to content +86 s greatly improve the grinding efficiency, and achieve the purpose of high output and low energy consumption cement grinding Unit2020年8月14日 In the cement crushing plant, there are 4 common types of cement crusher to process raw materials into requires sizes, such as jaw crusher, cone crusher, impact crusher, and hammer crusher These 4 cement crusher has its own advantages to be suitable for various section of cement crushing plant6 Tips For Cement Plant Manufacturer Turnkey Cement Plant
.jpg)
Low Cost Grinding Aids for Cement
The main function of grinding aids is to partially neutralise the charges present on the surface of cement particles, which develop during milling, reducing the surface free energy of the material being ground For this purpose, the additive molecules are adsorpted over the surface of the cement particles by weak electrostatic2023年8月21日 ICR looks at the inner workings of grinding mills in the cement industry to understand the technological advancements that are reshaping the landscape against the foreground of sustainability Innovations to enhance the grinding processes are aimed at minimising their environmental footprint while increasing efficiency and performance In CuttingEdge Grinding Solutions Indian Cement ReviewA portland cement clinker, a natural pozzolan, and a granulated blast furnace slag (GBFS) were used to obtain blended cements that contain 25% mineral additives Two of the cements produced were obtained by intergrinding and the other two were obtained by separate grinding and then blending All of the blended cements and the control cement without any additive had the Comparison of Intergrinding and Separate Grinding For The2020年12月15日 For grinding cement, two types of mills are used ball and roller Recent decades have proven the great effectiveness of a vertical roller mill for grinding raw materialsCapacity of roller mill for cement grinding ResearchGate
.jpg)
Concrete Grinder 101: The Insider's Guide to Concrete Grinding
2023年4月3日 Wet grinding involves using water to cool the grinding segments and aid in the surface being ground The water helps to cut the grinding process and reduces the amount of dust created Note: When it comes to choosing between dry grinding and wet grinding for your concrete surface, it's essential to consider both advantages and disadvantages of each For several decades the cement industry has successfully utilized vertical roller mills (VRM) for grinding of raw materials and solid fuels Most recently, this technology has been employed for Operational experience from the United States' first vertical roller Grinding aids for high performance cements Grinding aids are organic compounds that are added to the mill during cement grinding Their main purpose is to reduce the energy required to grind the clinker into a given fineness In addition, some products (usually referred to as performance enhancers) provide positive effect on cement hydration Grinding aids for high performance cements CADD Mapei2022年12月23日 PDF Even if cement is a wellconsolidated material, the chemistry of cement the energetic viewpoint, the grinding process consumes ca 60% of the total electrical en(PDF) An Insight into the Chemistry of Cement—A Review
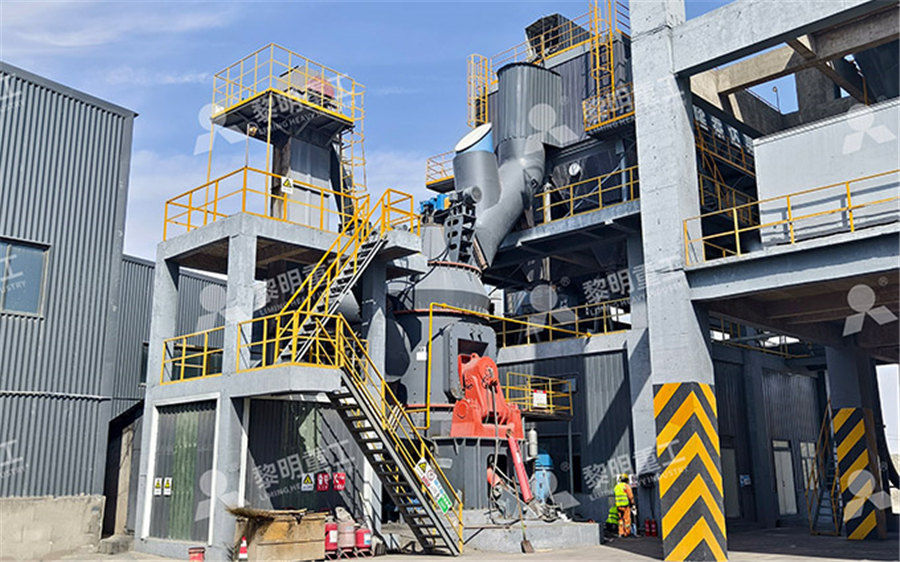
(PDF) Investigation of the effect of polymer‐based novel grinding
2021年11月20日 Grinding aids, primarily amine group chemicals, are used to reduce agglomeration and increase concrete strength in order to ensure an efficient comminution process in the modern cement industryrationalization suggestion There is rationalization, which is that when you do something or think something bad you rationalize it and you give it a more socially acceptable explanation还有合理化,是指当你做坏事或有不良想法时,你会将行为合理化, rationalization 百度百科2024年1月9日 Cement production contributes significantly to anthropogenic greenhouse gas emissions (GHG), a major contributor to global carbon emissions The environmental impacts of cement production have grown in recent years and it is urgent to reduce its carbon footprint Systems dynamics (SD) is a simulation method used to understand the nonlinear behavior of Carbon emissions mitigation methods for cement industry using 2020年9月14日 From there the clinker is conveyed to ball mills or roller presses, in which it is ground down to very fine cement, with the addition of gypsum and anhydrite, as well as other additives, depending on the use to which the cement is to be put Step #6 The finished cement is stored in separate silos, depending on type and strength classThe essentials of electrical systems in cement plants EEP
.jpg)
IMPROVING THERMAL AND ELECTRIC ENERGY EFFICIENCY AT CEMENT
2019年3月8日 44 Special Purpose V ehicle final cement grinding and mixing operation at the site Others ship some or all of their clinker production to standalone cementVertical roller mills and ball mills represent two clearly distinct technologies However, with proper adjustments to the operational parameters of the vertical roller mill almost identical cement properties can be achieved by the two mills that satisfy the cement user’s demandsNevertheless, the two types of mills have their distinctive meritsCement grinding Vertical roller mills VS ball mills