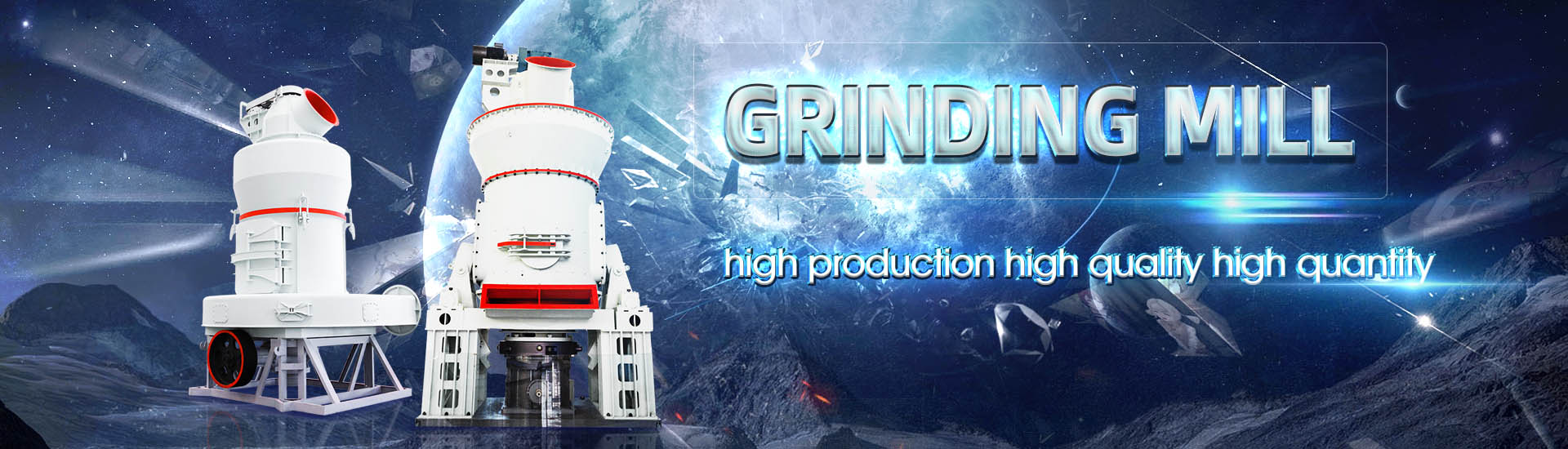
φ3x9 closedcircuit ball mill grinding slag production per unit
.jpg)
Analysis of the efficiency of the process in closed circuit ball mills
Ball mills for fine grinding cement clinker and additives are widely used around the world To improve the efficiency of a ball grinding the ball mills are transferred in closed circuit with air The relative capacity of a closed ball mill circuit as function of circulating load was calculated for three different classification arrangements: 1 cyclones with 38% of fine material reporting (by Closed circuit ball mill – Basics revisited AcademiaProduct Name: GGBS Production Line / Slag Mill Capacity: 3,6000 – 1,000,000 T/Y Grinding Systems: VRM system, Ball mill open circuit system, Ball mill closed circuit system, Roller press final grinding systemGGBS Production Line Slag Mill for Slag Powder There are three common types of processing for cement grinding stations: opencircuit grinding system, closedcircuit grinding system, and combined grinding system At present, most of clients use a combined grinding system, and its cement grinding Unit

Closed circuit ball mill – Basics revisited Request PDF
Request PDF On Apr 1, 2013, Alex Jankovic and others published Closed circuit ball mill – Basics revisited Find, read and cite all the research you need on ResearchGateAnalysis of the efficiency of the grinding process in closed circuit ball mills Valery I Telichenko1, Rashid R Sharapov1*, Svetlana YLozovaya2 and Vladimir ISkel1 1Moscow State University of Civil Engineering, Moscow, Russia 2Belgorod State Technological University named after VG Shukhov, Belgorod, Russia Abstract Ball mills for fine grinding cement clinker and additives areAnalysis of the efficiency of the grinding process in closed circuit 2016年1月1日 The purpose of the study is to assess the grinding and classification performance of a conventional Polysius® twocompartment ball mill and a Sepol® dynamic air classifier closed circuit process Analysis of the efficiency of the grinding process in closed circuit 2013年7月15日 The ball mill in closed circuit with cyclones is currently the most common grinding circuit in the mining industry, and has been so for over half a cen tury Due to its compact design, simple (PDF) Energy Efficient Ball Mill Circuit – Equipment Sizing
.jpg)
Grinding in Ball Mills: Modeling and Process Control
2012年6月1日 which is measured in tons of producti on per hour The production capacity depends 53 closedcircuit systems are shown in The process control in a ball mill grinding circuit faces In the manufacturing of Slag Grinding Unit Cement Plant, Clinker, Gypsum additives or slag are heaped into their respective yardsSubsequently these are carried to the respective jaw crushers with the help of belt conveyors Jaw crushers convert the big pieces of Clinkers, gypsum additives and slag into smaller pieces where from these pieces go to Bucket ElevatorsSlag Grinding Unit Manufacturers, Clinker Grinding Unit 1 Introduction Over the years, ball mill circuits closed with cyclones have become an industry standard, and since the early days, it has been recognised that classification efficiency and circulating load both have a major effect on the efficiency of closed circuit grinding (ie its capacity to produce the desired final product)(PDF) Closed circuit ball mill – Basics revisited AcademiaModeling And Simulation Of A Closed Loop Ball Mill Grinding Circuit Proceedings of IRF International Conference, Chennai, India, 20th April 2014, ISBN: 978938 10 II DYNAMICS OF THE BALL MILL GRINDING CIRCUIT product Blaine measured in cm²/g and the rejects Fig1 In a continuous ball mill grinding circuit, the ball millMODELING AND SIMULATION OF A CLOSED LOOP BALL MILL GRINDING CIRCUIT
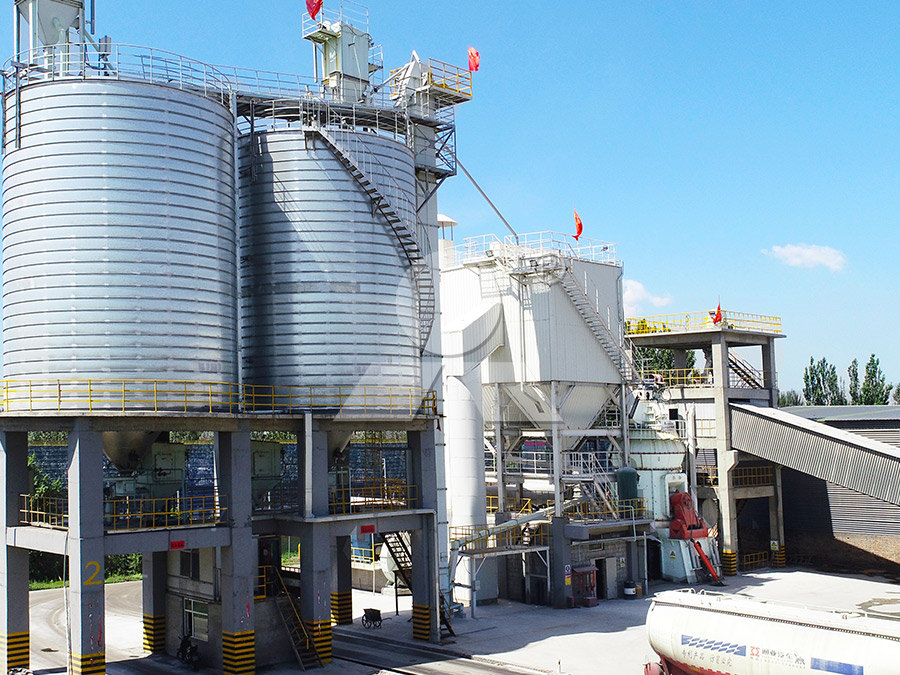
A closedloop SAG mill grinding circuit simulation
Fig 6 shows the closedloop grinding circuit of the SAG mill simulation In this closed grinding circuit simulation, a simple and crude PID control is imple mented to regulate the sump level to A ball mill is optimised for certain conditions – if these are changes, Pedro Leopoldo decreased from 11 litres to 7 litres per tonne of slag using oil As far as the HGG is concerned, For closed circuit mills grinding OPC as well as Everything you need to know about clinker/cement 2015年6月19日 The basic parameters used in ball mill design (power calculations), rod mill or any tumbling mill sizing are; material to be ground, characteristics, Bond Work Index, bulk density, specific density, desired mill Ball Mill Design/Power Calculation 911MetallurgistProduct Name: GGBS Production Line / Slag Mill Capacity: 36100 Million Tons Annually Grinding Systems: These include the VRM (Vertical Roller Mill) system, the Ball Mill open circuit system, the Ball Mill closed circuit system, and the Roller Press final grinding systemGGBS Production Line Slag Mill for Slag Powder Grinding
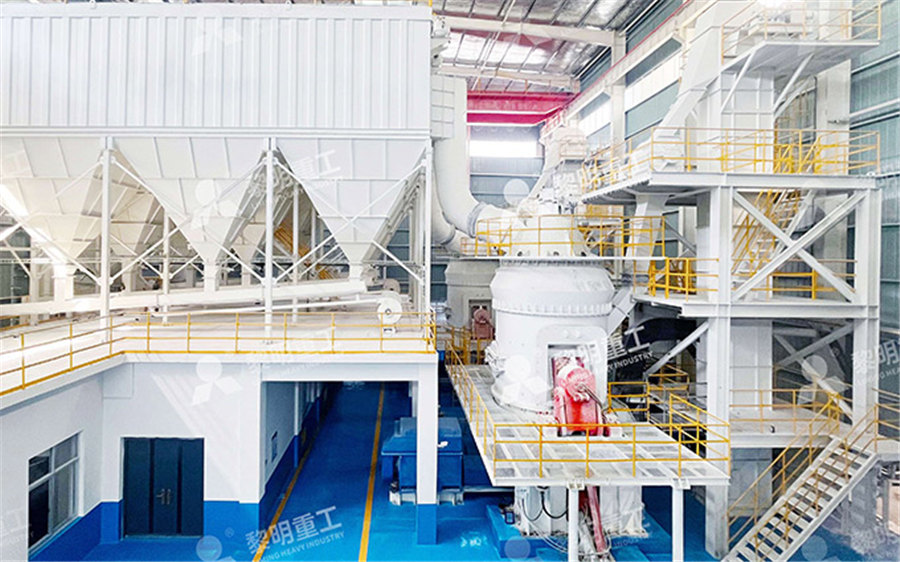
Grinding in closed circuit INFINITY FOR CEMENT EQUIPMENT
Pregrinding to a fineness of 2500 3000 Blaine is per formed in the coarse grinding mill In the open circuit fine grinding mill, fine particles of up to 6000 Blaine can be attained [143b] The onecompartment fine grinding mill is filled with 4 8 mm cylpebs grinding media; because of its small size, the grinding media are called minipebsThe cement ball mill can be used for opencircuit grinding, and also for closedcircuit circulation grinding which is composed of the powder concentrator and ball mill It has the characteristics of strong adaptability, continuous production, large crushing ratio and easy adjustment of Cement Grinding Unit Clinker Grinder AGICO CementOne of Russia's largest ball mill in size 4,6×14 m, with an power installation is 4250 kW [11] when the specific surface of the finished product in 3230 cm2pg reached capacity 126 tphAnalysis of the efficiency of the grinding process in closed circuit Slag grinding unit Processing material: slag produced in the ironmaking process in blast furnaces Final product: ground granulated blastfurnace slag (GGBS or GGBFS) Output: 3002,000 thousand tons/year Fineness: specific surface area of product≥420 m 2 /kgSlag Grinding Plant GGBS Plant One Stop Solution CNBM
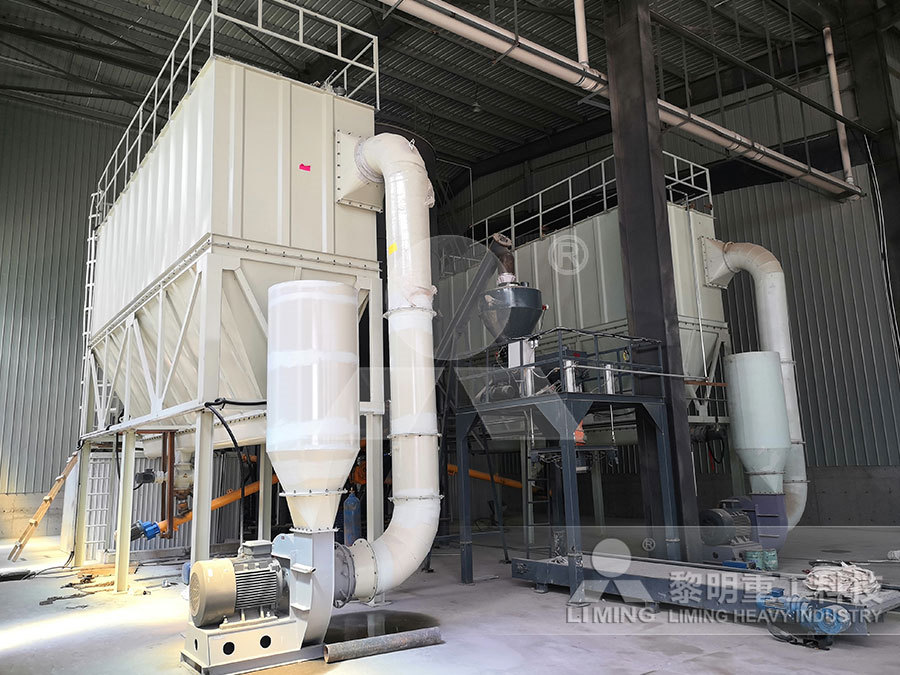
(PDF) Supplementary Relationship between Circulating Load and
2023年8月15日 The traditional model of closed circuit ball milling systems has been used for several decades, however, if the classifier of the closed circuit ball mill system performs the duties of both pre For example, from the point of view of saving electricity consumption per ton of cement and reducing operating costs, the closedcircuit vertical mill grinding system is certainly the most advanced However, in view of the fact that some of the equipment and the particle size of the grinding plant are not ideal, it is not suitableCement Grinding Plant Overview Cement Grinding Unit AGICO Between 1991 and 1996 the grinding circuit was operated on the principle of maximum throughput to minimise unit costs Power costs account for approximately 30 35 per cent of totalRecent Grinding Practice in the Copper Concentrator ofProcess flow of closecircuit cement grinding plant Closed circuit cement grinding plants are commonly used in the cement industry to produce different types of cement, including Portland cement, blended cements, and specialty cements, while meeting quality and environmental standardsThe closed circuit design helps in achieving consistent Close circuit Cement grinding plantSOLUTIONTongli Machinery
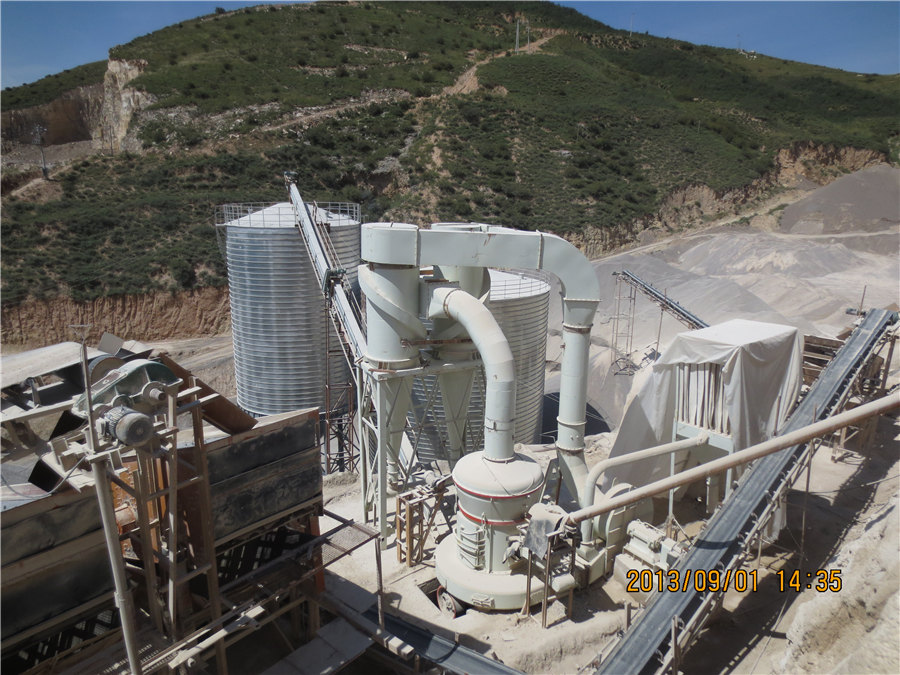
Cement Clinker Grinding Plant ball mills supplier
The cement grinding unit adopts a closed circuit grinding method The closed circuit grinding system has low power consumption per unit, the fineness of the finished cement is stable, and the clinker can be ground into different fines 2013年4月1日 Over the years, ball mill circuits closed with cyclones have become an industry standard, and since the early days, it has been recognised that classification efficiency and circulating load both have a major effect on the efficiency of closed circuit grinding (ie its capacity to produce the desired final product)Closed circuit ball mill – Basics revisited ScienceDirect2015年1月31日 From hubandspoke model to split grinding; from singlegrinding solution to a combination of system solutions; and from energyintensive traditional ball mill to upgraded versions and use of pregrinders, the cement industry is shifting towards more energyefficient grinding solutions ICR trains its spotlight on the current technology trends The cement Grinding Solutions Indian Cement ReviewOptimization of a Fully Airswept Dry Grinding Cement Raw Meal Ball Mill Closed Circuit Capacity With the Aid Free download as PDF File (pdf), Text File (txt) or read online for free This document discusses optimizing the production capacity of a fully airswept industrial scale twocompartment cement ball mill through simulation The mill has two compartments, with the first Optimization of A Fully AirSwept Dry Grinding Cement Raw Meal Ball
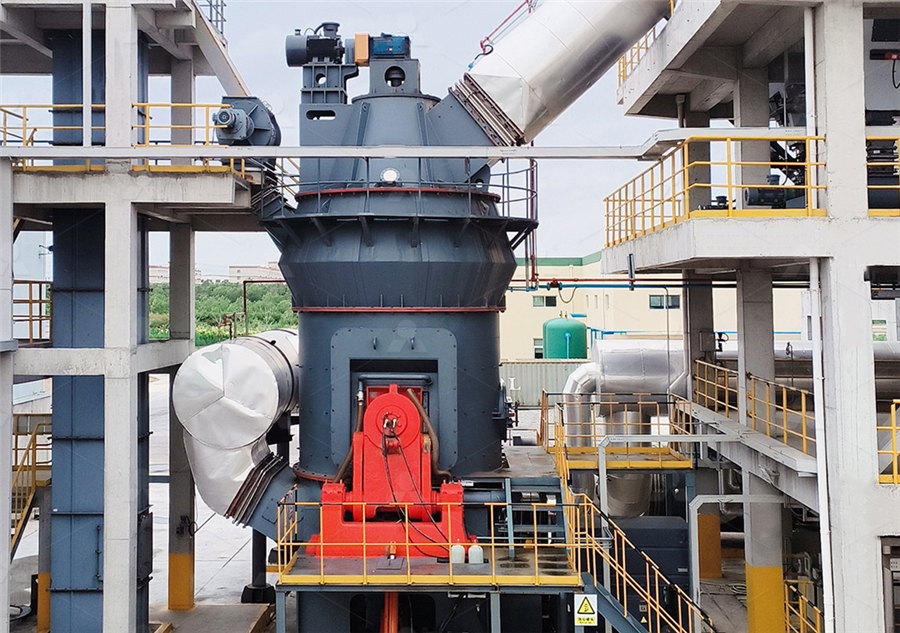
Closed Circuit Ball Mill PDF Mill (Grinding) Scribd
closedcircuitballmill Free download as PDF File (pdf), Text File (txt) or read online for free The document discusses NSI Equipments Pvt Ltd, a company that manufactures ball mills for industrial use It provides details about the company's vision, mission, quality policies, and the features and design of cylindrical and conical ball millsAutogenous Mill 10 45 6400 353 18 Ball Mill 5 64 2600 126 21 Regrind Ball Mill 32 48 740 39 19 Tower Mill 25 25 520 12 42 IsaMill 13 3 1120 3 280 3 3) 23/m) Ball Mill Tower Mill IsaMill (m Power Intensity Media Size No Balls / m Surface Area (kW/m (mm) 20 20 95,500 120 40 12 440,000 200 280 1 1,150,000,000 3600Fine Grinding as Enabling Technology – The IsaMillFigure 3f: Clinker grinding mill The output from the mill produces both the required fine cement and partially ground coarse particles A system incorporating an air separator through a bucket elevator and air slides separates the fine and coarse constituents The coarse product will be returned back into the mill for further grindingEVERYTHING YOU NEED TO KNOW ABOUT ESTABLISHING CEMENT GRINDING PLANT Closedcircuit Grinding System Upgrade Cement Ball Mill Redetermine the chamber length and adjust the grinding media gradation and material flow rate according to the material characteristics are very important for adding a pregrinding system and powder separator, as well as the internal transformation of cement ball millBall Mill For Cement Grinding – Cement Ball Mill Ball Mill

5 MATERIAL FLOW MODELS OF CLOSEDCIRCUIT GRINDING
5 MATERIAL FLOW MODELS OF CLOSEDCIRCUIT GRINDING The macrostructural models describing the material flows in closed circuit ball mill grinding include the rules of mass flow for steadystate, the nonlinear character of the mill, and the dead time relating to Mill Shell:The foundation of the Slag ball mill, the mill shell, is a cylindrical structure made of premiumgrade steelTongli heavy machinery is equipped with a large annealing furnace of 65x65x20m and a 65x65x20m large sandblasting room, which can conduct overall heat treatment and sandblasting on the ball mill to ensure the service life and appearance of the slag grinding ball mill Manufacturer Tongli Machinery2017年10月12日 This study aimed to develop a NNMPC for dry grinding in a closed circuit with a ball mill Artificial Neural Network represented the multiinputmultioutput system for the model to predict the (PDF) Predictive Control of a Closed Grinding Circuit 2016年10月21日 Advantages of closed circuit grinding 1 Power requirements per ton of finished material are lower 4 Less overgrinding or production of extreme fines You are operating an 8 feet diameter Ball Mill consuming 245 HP Comminution Theory Process Equipment 911Metallurgist
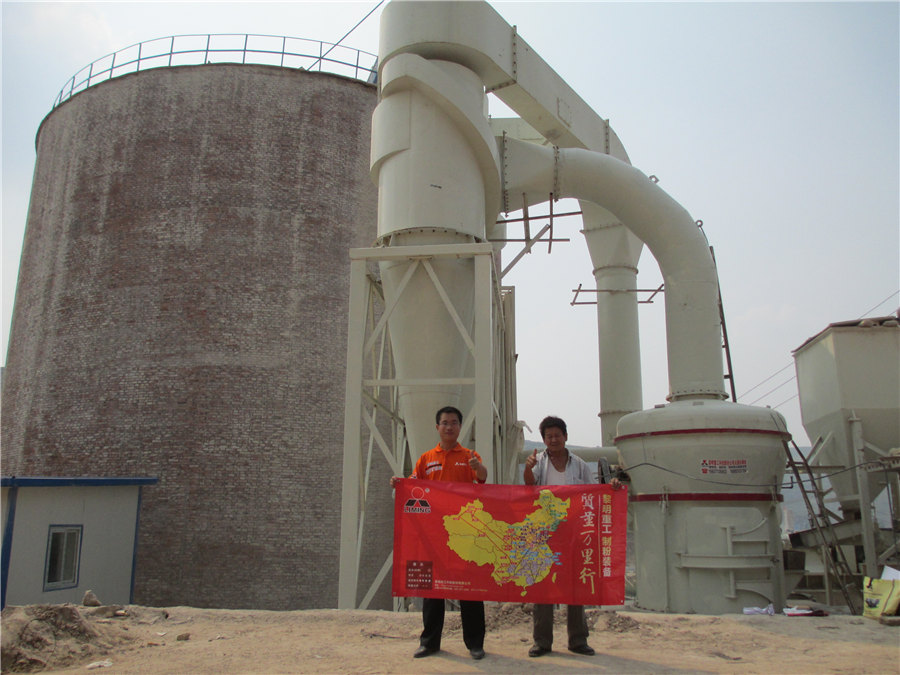
Operating experience with a vertical roller mill for grinding
2012年3月1日 Vertical roller mills are the mills traditionally used for processing granulated blastfurnace slag and for grinding composite cements From the energy aspect they are superior to grinding plant 2020年9月15日 diagram of cement ball mill grinding circuit is shown in Figure 2 The clinker, along with additives viz gypsum, slag, and / fly ash, called feed minerals, are introduced into the horizontally (PDF) Predictive Controller Design for a Cement Ball Mill Grinding Ball mill grinding efficiency 950% = (54 ÷ 64) Benchmark result A ball mill grinding efficiency above 80% is considered “good”; the measured efficiency of 95%Method of assessing ball mill health ResearchGate2020年12月30日 Part3 How to set up cement plant series Mini Clinker Grinding Unit 5 to 25 TPH Best option for start up at low costContact us: peegtechnical@gmailSetUp Mini Clinker Grinding Unit 5 to 25 TPH Ball Mill Close Circuit
.jpg)
ClosedCircuit Ball Mill Grinding Plant Scribd
Closedcircuit Ball Mill Grinding Plant Advantages Disadvantages Free download as PDF File (pdf), Text File (txt) or view presentation slides online Closedcircuit ball mill grinding plants have lower power consumption and allow for higher cement fineness than open circuit mills However, closedcircuit mills are more sophisticated, require more space, and have higher 2022年8月10日 Hybrid Grinding: a combination of Ball Mill with Roller press Horo Mill (HM): it is similar to the vertical mill but the roller arrangement differs from VRM In the ball mill, RP and Combined grinding system separation take place outside the grinding mill, whereas in the VRM separation and grinding take place in one systemEfficient grinding unit selection impacts profitability