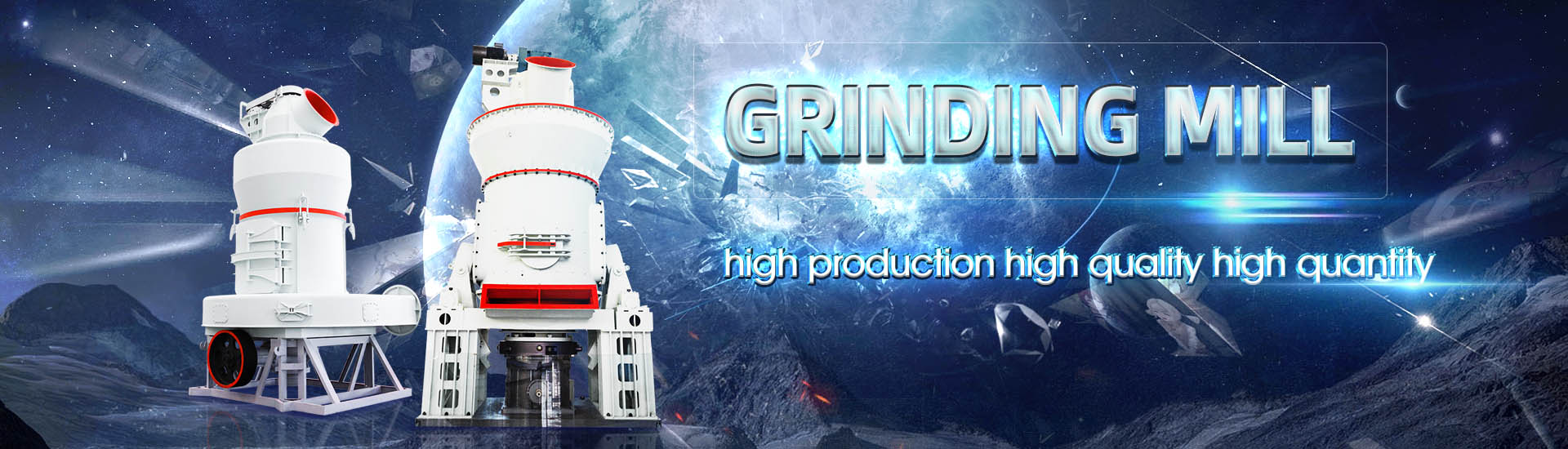
Φ35x13 cement mill Technical transformation

The digitization work of cement plant in China ScienceDirect
2023年11月1日 This article is to introduce the digitization work of smart cement plant in China To save power and promote the product quality, delicacy management in variety ways of In this paper, in view of the problems existing in the opencircuit production line of cement mill system, the original pulverizer is removed and replaced by a twoshaft and doublerotor high 水泥磨系统提产降耗技术改造Technical Transformation of With its unified, crossfunctional and enterprisewide approach to digital transformation – encompassing ABB Ability Knowledge Manager and ABB Ability Expert Optimizer among Digitalization and sustainability in cement Cement ABB Grouptransformation with its APC system, ABB Ability™ ExpertOptimizer, part of its dedicated digital portfolio of solutions for the cement industry Other systems include ABB Ability™ Building Main Head an intelligent cement plant ABB
.jpg)
Vertical Cement Mill Magotteaux
Magotteaux’s proprietary vertical cement mill technology has been developed through decades of innovation and expertise in grinding processes Our vertical cement mill wear parts are The polysius ® booster mill is an additional stage grinding solution, particularly efficient for finer grinding Therefore, it enables customer to produce ultrahigh performance cements or polysius® booster millThe comprehensive power consumption of cement grinding has been stabilized at around 22kWh/t, and the system output has been increased from 190t/h to 325~335t/h, providing an Optimization and Transformation of Production Process for2019年4月28日 Many opportunities exist to upgrade the older vertical mills with the latest technologies to improve efficiency Recently a southern California cement plant upgraded their A Cement Mill Upgrade Story Reboot IEEE Xplore
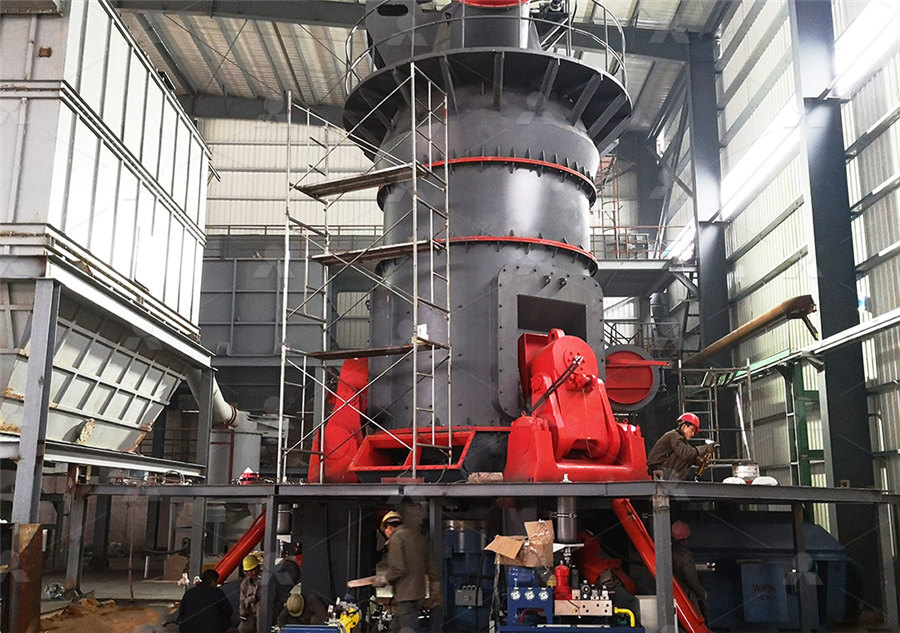
Grinding process optimization IEEE Xplore
2017年6月19日 The modular vertical roller mill for grinding cement raw material, cement clinker, and additives with an installed power of up to 12,000 kW was specifically designed to meet the As part of its green cement plant project, thyssenkrupp has expanded its product range with the polysius® booster mill While one cement manufacturer has already integrated the mill into his Let’s talk: polysius® booster mill – the ne xtClosedcircuit Grinding System Upgrade Cement Ball Mill Redetermine the chamber length and adjust the grinding media gradation and material flow rate according to the material characteristics are very important for adding a pre Ball Mill For Cement Grinding – Cement Ball Mill Ball Pa ge 1/ 17 Transfer and transformation of mercury in cement production Chongrui Yuan Chengdu University of Information Technology Yifan Wang Chengdu University of Information Technologyproduction Transfer and transformation of mercury in cement
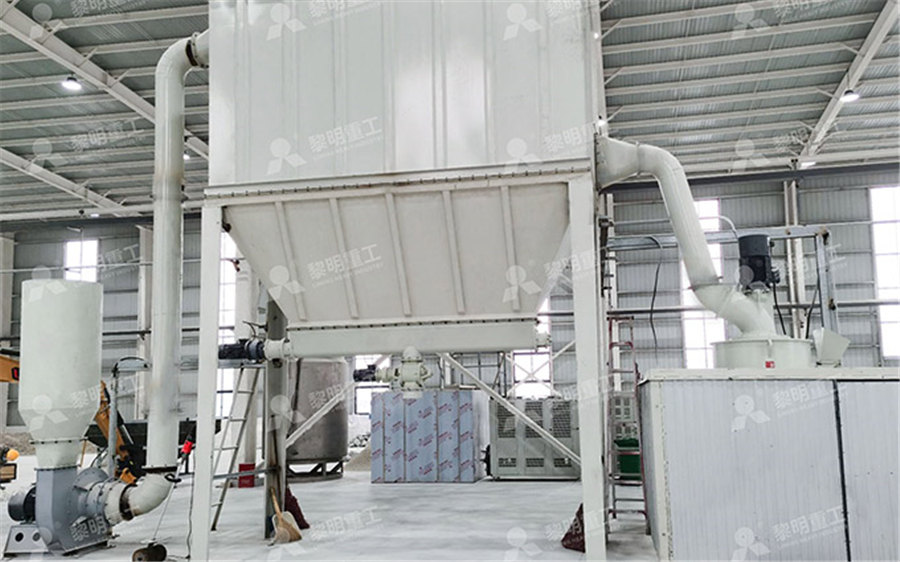
Cement Plant Upgrading Modernization AGICO
Cement mill open to close circuit The differences between the openflow system and close circuit system: compared with the openflow system, the close circular flow grinding system has less overgrinding in the cement mill, and the output With its unified, crossfunctional and enterprisewide approach to digital transformation – encompassing ABB Ability Knowledge Manager and ABB Ability Expert Optimizer among many other solutions – ABB is ideally placed to support the cement industry in this journey to Digitalization and sustainability in cement Cement ABB Group2020年8月13日 Calcium carbonate cements have been synthesized by mixing amorphous calcium carbonate and vaterite powders with water to form a cement paste and study how mechanical strength is created during the setting reaction Insitu Xray diffraction (XRD) was used to monitor the transformation of amorphous calcium carbonate (ACC) and vaterite Mechanisms of Phase Transformation and Creating Mechanical2022年4月19日 Another aspect of digital transformation is the horizontal integration where complete life cycle of the plant assets such as a Mill or a Kiln is managed by a digital databaseWHY HOW TO DO DIGITALIZATION IN CEMENT INDUSTRY?
.jpg)
The steel production transformation process in Europe: New slag
The main challenge of the steel industry for the next decade is the steel production transformation process, starting in Europe The CO 2 intensive blast furnace/basic oxygen furnace (BOF) route will be substituted by a combination of Direct Reduced Iron (DRI), based on natural gas, later on “green” hydrogen, with an Electric Arc Furnace (EAF) or a Submerged Arc Furnace (SAF), 2023年5月19日 Raw mill fan in cement industry carries gas and raw meal The pressure drop in raw mill fan is very high If a vertical roller mill is used for raw grinding in The practice has proved that the in Raw mill fan runs well after the technical transformation of VFD, Application of INVT GD5000 series VFD for Raw mill fan at Ambuja cement Four percentages of SCBA replacing partially Portland cement (0%, 15%, 30%, and 50%, in mass), two economicoriented Brazilian scenarios, and eleven life cycle impact categories related to the Mass balance of the cement mill system Download Table2019年6月1日 This article analyzes the problems of perfecting grinding equipment for largescale production – cement, ore, coal An improved design of a ball mill, equipped with internal energy Exchange Mechanics of the grinding media in ball mills with longitudinal and
.jpg)
Cement Separator Ball Mill Optimization PDF Mill
This document discusses optimizing cement separator and ball mill systems through periodic testing and evaluation It provides guidance on when and why to conduct optimization, including abnormal operations, poor performance, or 2021年3月3日 Cement is produced by a hightemperature (about 1500 °C) reaction in a rotary kiln of carefully proportioned and blended ratios of lime (CaO), silica (SiO 2), alumina (Al 2 O 3), and iron oxide (Fe 2 O 3)The production of cement is a chemical process requiring an accurate blend of the previously cited four key organic oxides and the limitation of several undesirable Cement SpringerLinkVertical roller mill manufacturers Vertical roller mill or VRM is a largescale grinding equipment designed for pulverizing cement raw meal, cement clinker, slag, coal, fly ash, limestone, and other hard grinding materialIt integrates grinding, drying, separation, and conveying in one machine The equipment is widely used in many industries such as cement, electric power, metallurgy VRM In Cement Plant Maximize Energy Saving CNBMSINOMAUnit82 Cement Mill Free download as Powerpoint Presentation (ppt / pptx), PDF File (pdf), Text File (txt) or view presentation slides online This document provides information on industrial drives used in cement manufacturing plants It discusses the different types of drives used including raw mill and cement mill drives, kiln drives, crusher drives, and waste gas fan drivesUnit82 Cement Mill PDF Mill (Grinding) Scribd
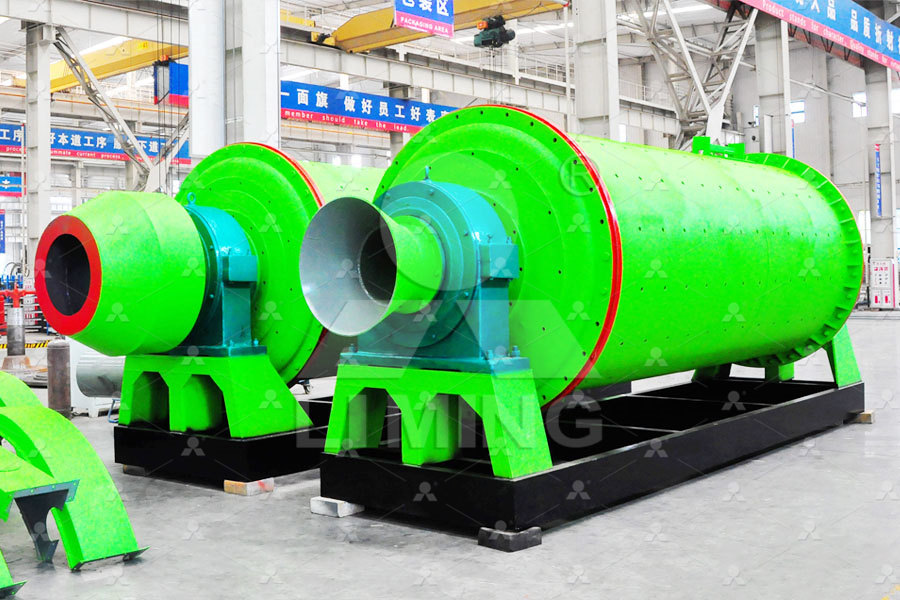
Technology trends in cement manufacturing
2018年3月31日 – Dr Anjan K Chattejee What have been the visible technological advancements in cement manufacturing during the last decade? The cement industry in the world has grown phenomenally in the last decade and the production level of all varieties of Portland cements taken together has crossed four billion tonnes, which is the largest volume amongst The Support that Our Team Will Provide During and After the Transformation Our team is available for any questions or support you may need during the cement plant technical transformation We can provide guidance on the best practices for technical implementation, assist with troubleshooting during implementation, and provide ongoing technical support to Technical Transformation Services for Cement PlantDiversified operating conditions, inputoutput constraints, and parametric variations in the Vertical Roller Mill (VRM) make it to have complicated dynamics and closedloop instabilityOperational experience from the United States' first vertical roller 2 Cement kiln rotation 3 Crushers and roller mill drives 4 Slip Power Recovery drives The ID fan induces kiln air fl ow, which must be continuously varied to match the process requirements Because cement making is a thermal and a chemical process, both air volume and mass fl ow must be controlled The processDrive Solutions for the Global Cement Industry
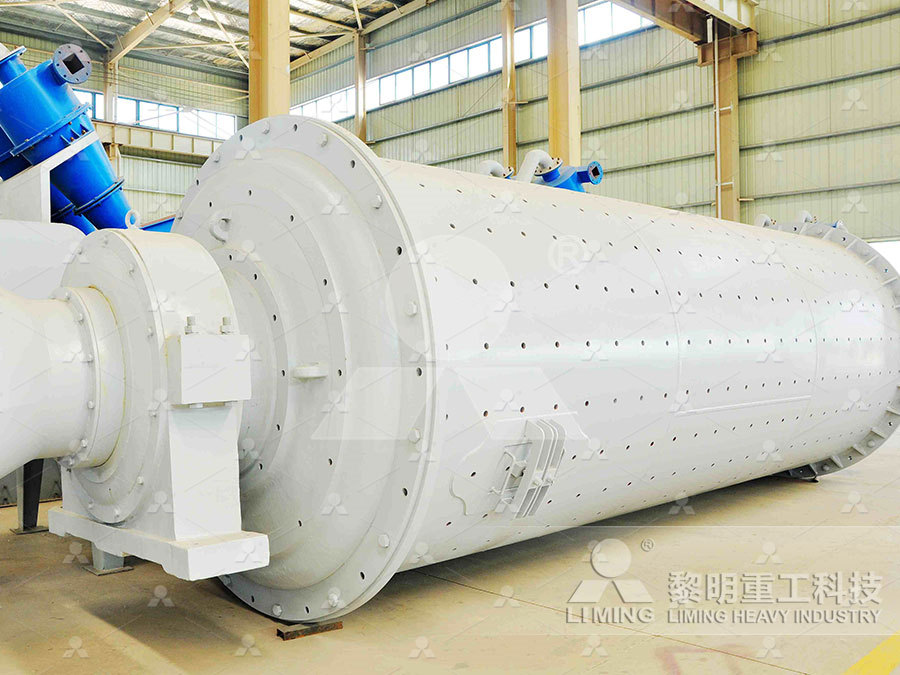
Modeling of energy consumption factors for an industrial cement
Description of variables Variables Min Max Mean STD The load of mill feed Feed rate (ton/h) 250 307 29716 711 The applied pressure for grinding by roller Working pressure (bar) 68 80 7276 192 The required hot gas for drying and transportation of raw material Input gas flow (m3/h) 60,000 890,000 600,559 90,434 The speed of classifiers rotor Classifier speed (rpm) 48 59 2021年11月1日 The standard Gb307602014 “Technical Specification for Collaborative Disposal of Solid Waste by Cement Kiln” indicates that the limit for Cr in clinker is 150 mg/kg The standard Gb318932015 “Limitation and determination of water soluble Cr(VI) in cement” indicates that the limit for water soluble Cr(VI) in cement products is 10 mg/kgThe migration and transformation of chromium during co Following the initial wear audit assessment by Welding Alloys’ technical team, they determined that the grinding components should be taken back to the profile template, using the Integra ™ mill wire products These products are Vertical roller mill Welding AlloysTechnical transformation of 5 000 tons per day cement production line 78 info@greatwallmachines Language English; Existing problems The company uses a combined grinding system composed of a roller press HFCG160140 and a tube mill Φ42 m×13 m to grind cementTechnical transformation of 5 000 tons per day cement
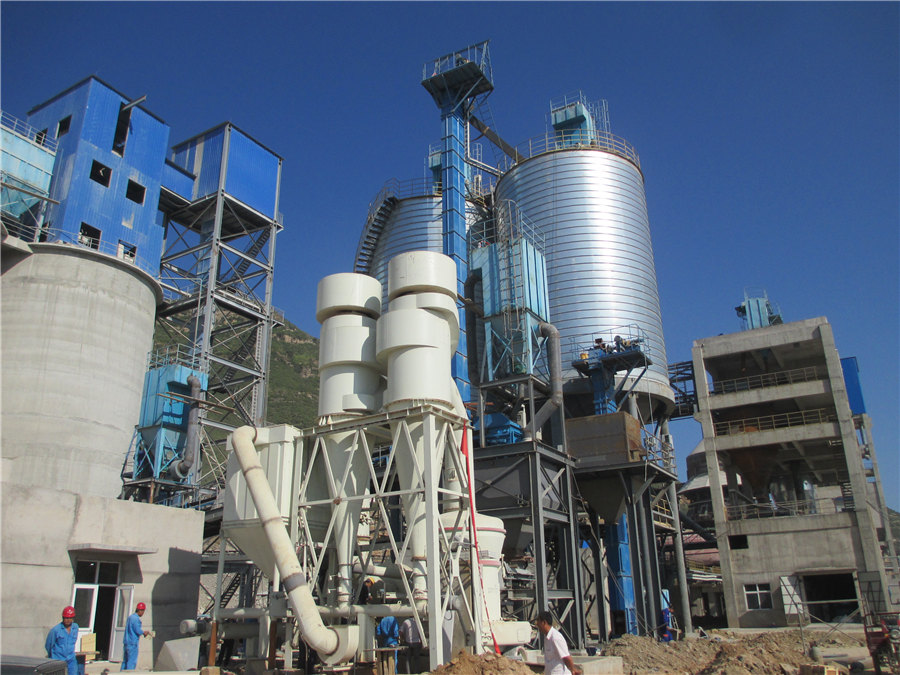
Transfer and transformation of mercury in cement
2022年8月22日 Acc ording to the Fig 20 to Fig 22, the main substances in cement mill are Ca(N O 3) 2 (about 6379%), and migration and transformation mechanism in cement pr oduction proc essMore over, 2021年12月31日 The cement industry is an industrial subsector with high energy intensity It represents nearly 15% of the total energy used by industries Many energysaving programs and strategies have been Investigation of Energy Saving Potential In A South African Cement 2011年9月15日 2010 USEPA cement facility mercury regulations will reduce emissions by 94% Highly variable mercury inputs confound facility assessment Emissions transience caused by an internal mercury loop complicates control design Current emissions models do not distinguish between mercury species Poor understanding of mercury species sorption and desorption Mercury regulation, fate, transport, transformation, and 2018年8月15日 The application of the Expert Optimizer (EO), an expert system from ABB, utilizing the RawMaterialProportioning (RMP) strategy is discussedDigitalization as a Catalyst for the Cement Industry
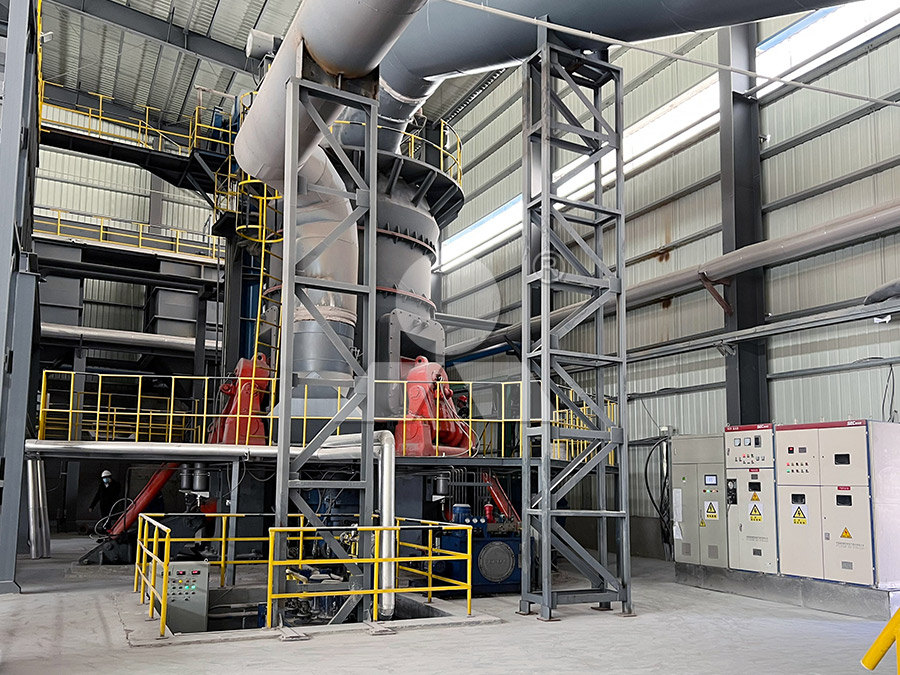
FLSmidth Ball Mill For Cement Grinding
The document summarizes the FLSmidth ball mill, which is designed for grinding clinker, gypsum, and dry or moist additives to produce any type of cement The mill can operate in open or closed circuits and with or without a pregrinder It has large throughflow areas to allow for low pressure drops The mill consists of standard modules that can be adapted for specific requirements It 2014年4月1日 Two mill systems are employed for most coal grinding applications in the cement industry These are, on the one hand, vertical roller mills (VRM) that have achieved a share of almost 90% and, on (PDF) The latest innovative technology for vertical roller mills CEMENT TECHNICAL DATA AND SPECIFICATIONS To aid you in fulfilling all of your specification and submittal needs, we have provided our certificates of compliance, monthly mill certificates, LEED letters, and safety data sheets for our cement products below If you need technical data that is not included here, please contact our technical teamMill certificates Argos USA Cement and Ready Mix Concrete Company2022年10月1日 PDF This study investigated a mathematical model for an industrialscale vertical roller mill(VRM) at the Ilam Cement Plant in Iran The model was (PDF) A cement Vertical Roller Mill modeling based on
.jpg)
About Us Dalmia Cement
With more than 47 years of experience in the cement industry, Mr Dalmia has served as the President of the Cement Manufacturers Association and is a respected figure in the cement industry Playing a pioneering role across the Deep decarbonisation of industry: The cement sector Cement sector overview Cement is the binding agent of concrete, the most widely used construction material in the world The cement sector is a major greenhouse gas emitter, responsible for about 7% of CO 2 emissions globally (1), and about 4% in the EUDeep decarbonisation of industry: The cement sector Europa2019年4月14日 Producing cement with appropriate quality and by spending the minimum cost, applying solutions including process optimization and use of grinding aid have been investigated before(PDF) Investigating and comparing the effect of 2024年10月14日 In today's construction industry, the demand for cement as a basic material continues to grow, and cement mills, as key equipment in the cement production process, play a vital role The production process of cement mills involves a variety of technical links, from the grinding of raw materials to the manufacture of finished cement, and each step affects the What Role Does Cement Mill Play In Production?
.jpg)
Technical Notebook CEMENT ADDITIVES FOR VERTICAL MILLS
page 03 12 cement additives division page 03 13 research development page 04 14 mapei technical services page 05 15 mapei cement academy – annual conference** page 05 2 vertical mills introduction page 07 3 principles of vertical grinding systems page 07 2023年8月23日 A cement mill is a fundamental component of the cement manufacturing process, playing a vital role in breaking down and grinding cement clinker into fine powder This finely ground powder, when mixed with other materials, produces the building material we commonly know as cement To achieve this crucial transformation, a cement mill comprises What Are the Parts of a Cement Mills? Cement Ball Mill It is known that the variable is strong coupling, nonlinear, multivariable and large timedelay dynamic characteristics in the raw cement vertical mill grinding process Against the problem which is difficult to establish accurate mathematical model, this paper establishes a production index prediction model of vertical mill raw meal grinding process by using echo state network Modelling of the vertical raw cement mill grinding process based 2018年9月10日 The simulator was used for the thermodynamic performance of a raw mill (RM) and raw materials preparation unit in a cement plant in Nigeria using actual operating data The raw mill has a capacity (PDF) Thermodynamic Analysis of Raw Mill in Cement
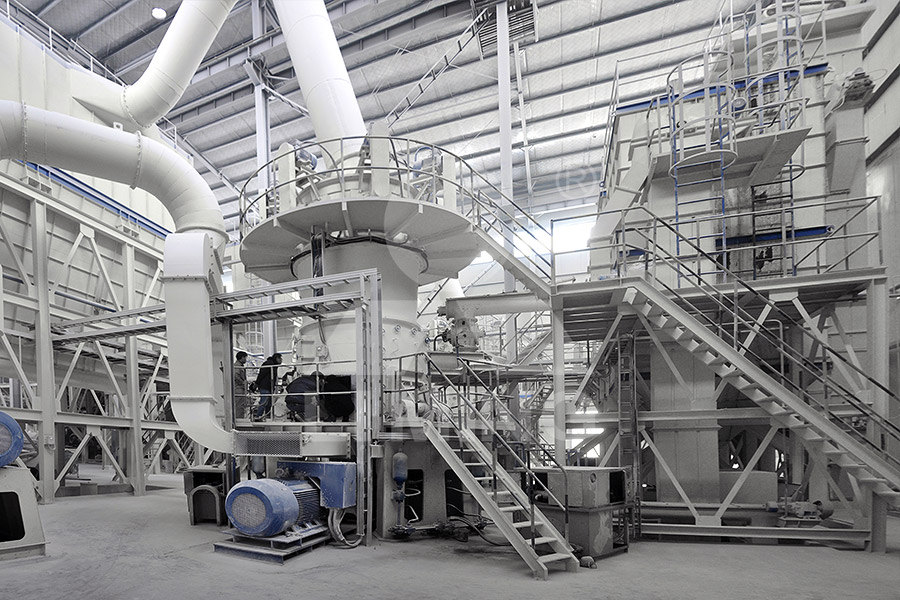
Cement Milll Separator Cyclone Air Separator in Cement Plant
Cement mill separator, or cement separator, is a type of equipment that was widely used in the cement grinding system and raw mill system of cement plantsThe function of the separator is to separate the finesized particles from the coarsesized particles, so as to avoid material condensation and over grinding in the mill, and improve the milling system’s grinding efficiency2021年2月7日 The migration and transformation of chromium during coprocessing of cement raw meal mixed with chromepolluted soil February 2021 DOI: 1021203/rs3rs/v1The migration and transformation of chromium during co