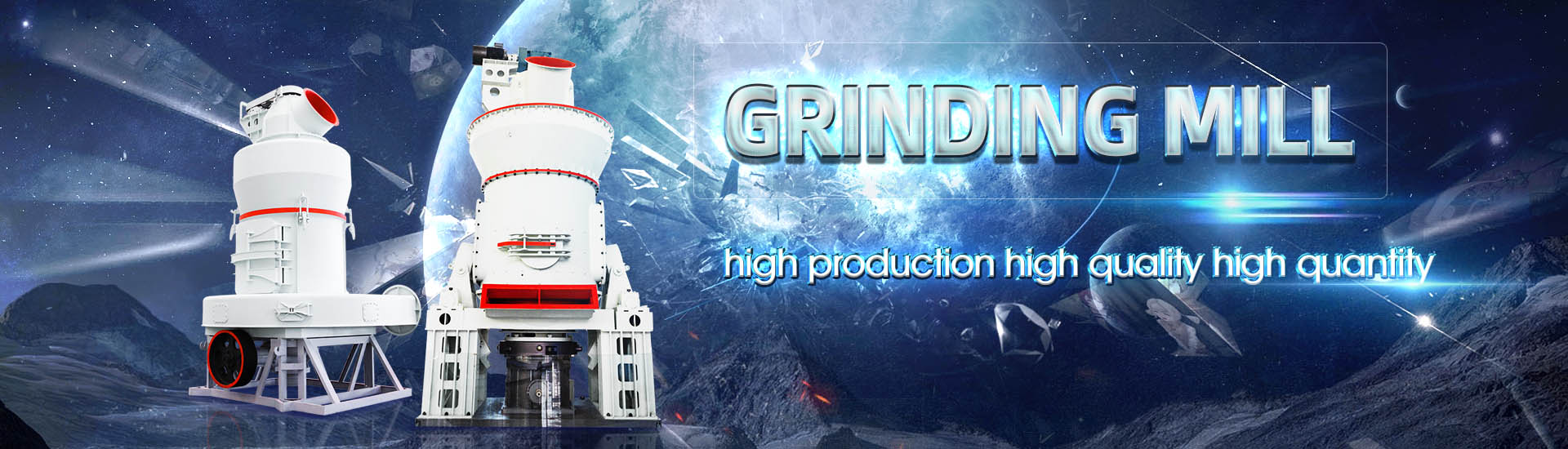
Coalfired pulverized coal Calculation of ash
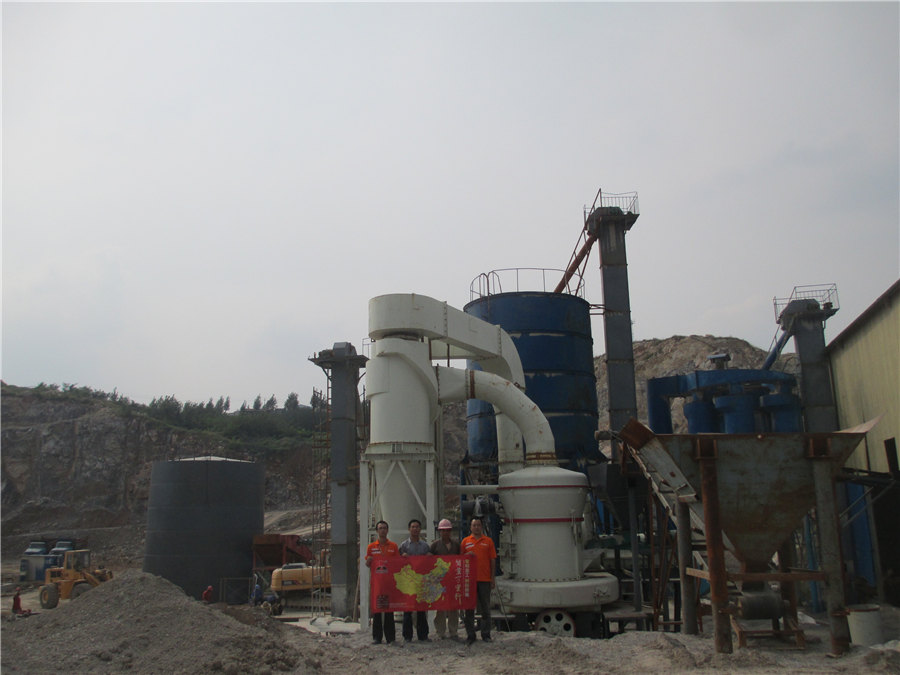
Numerical Simulations of Pulverized Coal Combustion JSTAGE
In pulverized coal fired power plants, it is very important to improve the technology for the control of environmental pollutants such as NOx, SOx and ash particles including unburned bustion of coal produces the heat required as well as various solid residues and gaseous pollutants such as ash, SO2 and NOx During combustion, coal particles undergo the following Fundamentals of pulverised coal combustion ICSC2006年1月1日 Five well characterized Australian bituminous coals have been burned in a laminar flow drop tube furnace in two oxygen environments to determine the amount and Fine ash formation during combustion of pulverised coal–coal 2002年2月1日 Ash formation from minerals is the first step in a comprehensive and mechanistic approach for predicting ash deposition behavior in a pulverized coal fired boiler Such an A mathematical model of ash formation during pulverized coal
.jpg)
Simulation of ash deposit growth in a pulverized coalfired pilot
1993年11月1日 This paper presents a synthesis of a large body of experimental data on growth rates of ash deposits from the air and oxycombustion of multiple pulverized solid fuels, 2024年2月6日 This study aimed to optimize combustion in coalfired power plants at low loads by analyzing combustion efficiency, NO x emissions, and ash deposition in a boiler An Characteristics of combustion and ash deposition for pulverized 2021年12月14日 All coal mixture combinations demonstrated potential as a fuel for power plants that use pulverized coalfired boilers Because of its capacity to reduce slagging and fouling potentials,Ash Evaluation of Indonesian Coal Blending for In this paper, an intensive characterization of ash deposits collected from different positions of a pulverizedcoal (PC) boiler has been conducted to diagnose the ash slagging and fouling issues within this boiler and to clarify the mass Characteristics of Ash Deposits in a Pulverized Lignite
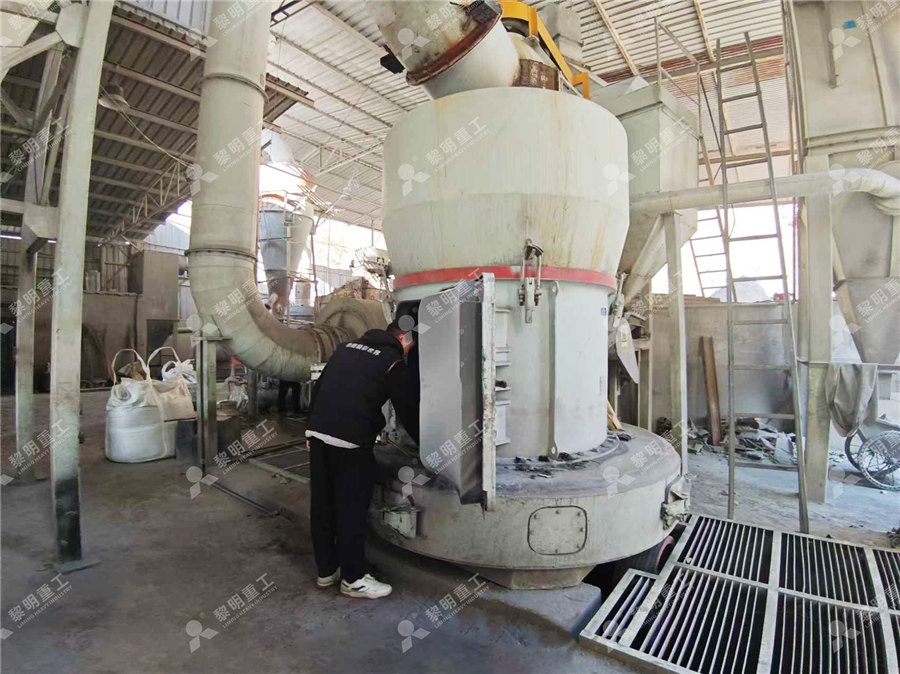
Reduction of Ash Deposition in Pulverized Coal Fired Boilers
2012年1月1日 This study proposes reduction technology of ash deposition on the heat exchanger tube in pulverized coal fired (PCF) boilers Thermal spraying technique is adopted the burnout of the coal Combustion of coal produces the heat required as well as various solid residues and gaseous pollutants such as ash, SO2 and NOx During combustion, coal particles undergo the following four welldefined steps (as illustrated in Figure 1): coal particle drying, and then heatingup to the pyrolysis reaction temperature;Fundamentals of pulverised coal combustion ICSC2001年4月1日 Improved methods have been developed which utilize a more accurate description of the coal, as well as a mathematical description of the fly ash transport and sticking in order to approximate the deposition rate [1] This paper describes our efforts to simulate the ash deposition behavior in a pulverized coalfired boilerSimulation of ash deposit in a pulverized coalfired boiler2022年8月1日 Existing pulverized coal (PC)fired power plants are increasingly being operated in loadfollowing mode [1]Most of PC power plants in the United States are the drumtype subcritical units, which were built over 30 years ago, and designed for base load operationPredictive modeling of a subcritical pulverizedcoal power plant
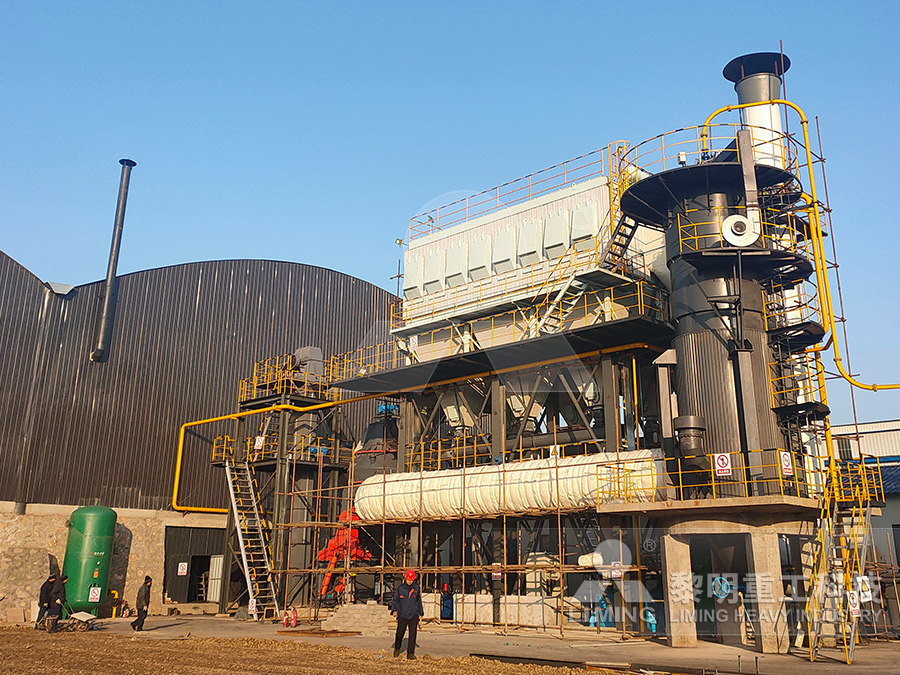
Pulverized Coal Boiler an overview ScienceDirect Topics
Pulverized coal combustion includes wallfired, tangentially fired, archfired, and rooffired systems Wallfired and tangentially fired systems are the most common type of boilers PC firing uses pulverizers to grind the fuel to particle sizes of typically >70% passing through 200 mesh or 2001年4月1日 Request PDF Simulation of ash deposit in a pulverized coalfired boiler A model has been developed to simulate deposit growth under slagging conditions The model was coupled with a Simulation of ash deposit in a pulverized coalfired boiler2019年1月1日 For coal and gas dualfired boiler, pulverized coal mass flow and gas volume flow into furnace are important criteria for boiler operation adjustment, and they are important input parameters for Calculation Method of Pulverized Coal Mass Flow Into Coal and As this predictive equation is only made for a pulverized coal tangentially fired boiler, this has to be verified for pulverized coal wall firing, down shot firing, opposed firing, etc However, more than 50% of the pulverized coal fired boilers in the world are equipped with tangential firing system Bottom ash unburned predictionPredicting Fly Ash and Bottom Ash Combustibles in Pulverized Coal Fired
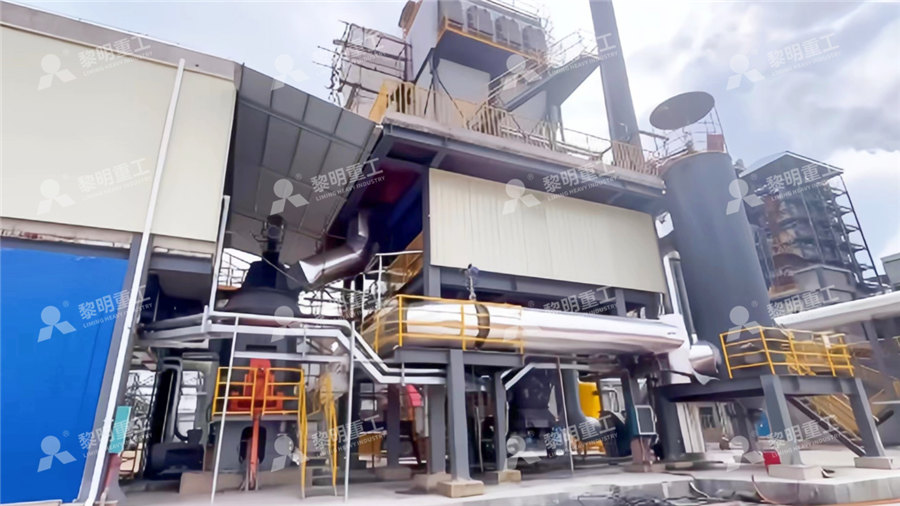
11 Bituminous And Subbituminous Coal Combustion US
In pulverized coalfired (PCfired) boilers, the fuel is pulverized to the consistency of talcum powder (ie, at least 70 percent of the particles will pass through a 200mesh sieve) and pneumatically injected through the Coal ash may either settle out in the boiler (bottom ash) or entrained in the flue gas (fly ash)2012年1月1日 In order to countermeasure these problems practically, for example, discussions on ash deposition mechanisms [6, 7], measurement of change of ash deposition mass , evaluation and analyses of ash deposition behaviors, development of the simulator for plugging phenomena due to ash deposition in commercialized pulverized coal fired (PCF) boilers have Reduction of Ash Deposition in Pulverized Coal Fired Boilershightemperature conditions Bai et al [13] studied characterization of lowtemperature coal ash at high temperatures in a reducing atmosphere Vuthaluru et al [14] evaluated ash formation of brown coals Abbott et al [15] predicted ash behaviors using chemical equilibrium calculations Hansen et al [16] quantified ash fusibility using Ash Deposition Behavior of Upgraded Brown Coal in Pulverized Coal 2019年1月15日 The model was validated with kinetic measurements from fly ash samples in a pulverized coal fired boiler and also from combustion of coal char in a onedimensional entrainedflow reactor of this review Further to that, empirical equations were used for calculation of emissivity of coal and particle putational modeling of pulverized coal fired boilers – A
.jpg)
FAQs ukqaauk
Yes, coal ash is still available in large quantities and will be available into the future There are 17 coalfired power stations represented by the UKQAA and while there has been a move towards other forms of energy generation, coalfired power still accounts for over a third of the energy generated in the UK2017年10月13日 The slagging rate in hightemperature zones and the furnace exhaust temperature in boilers firing highash coals increase with the ash content of coal However, the slagging situation in pulverizedcoalfired boilers often improves with increase in the ash content of coal This is because of the different effects of increase in the ash content on the slagging in Effect of the Ash Content on the Slagging Properties of Coals and 2021年4月8日 Highefficiency, lowemissions (HELE) coalfired power plant technologies operate with a higher thermal efficiency of the steam cycle for coalfired power generation, reducing CO2 emissions per unit energy generation They represent some of the primary and intermediate solutions to the world’s energy security Extensive numerical modeling efforts A Review of the Numerical Modeling of Pulverized Coal 2015年10月19日 The paper presents experimental and numerical investigation of pulverized coal combustion process analysis and optimization The research was conducted on the frontfired pulverized coal boiler with dedicated lowNOx furnace installation In order to find optimal boiler operating conditions the acoustic gas temperature measurement system and mass flow A Combustion Process Optimization and Numerical Analysis for
.jpg)
Ash deposition behavior of upgraded brown coal in pulverized coal
2011年7月1日 Mechanism of the ash deposition in the boiler is summarized in Figure 1(Akiyama et al 2011 Keywords: Ash melting point, Volatile matter, Slagging, Fouling, Coal fired power plant, pulverized coal Ash 2234 Volatile Matter 2577 Moisture 1275 Fixed Carbon 3914 Elemental analysis Value, wt% (AR) C 847 H 539 O 155 N 155 S 123 3 To conduct calculations of the pulverizedcoal fired boiler, the following processes as coal combustion including a devolatilization proces s, Coal combustion modelling pulverized coalfired boiler2011年10月19日 India has huge coal reserves, about 71 per cent of the world’s total [] and thus the coalbased thermal power plants dominate the sourcewise mix with 541 per cent of the total installed capacity of about 174 GWe []Due to the energy shortage of 85 per cent [], a large number of old coalfired units are still in use, operating on much lower plant efficiencies Thermodynamic analysis of a coalfired power plant repowered 2019年12月1日 The purpose of this paper is to investigate the effect of the pulverized coal drying temperature on fly ash carbon content and slagging of a 1000 MW unit coalfired boiler The pulverized coal was dried at three selected temperatures of 25 °C, 75 °C and 110 °C, and the moisture and porosity of the pulverized coal particles were measuredThe role of pulverized coal drying temperature in fly ash carbon
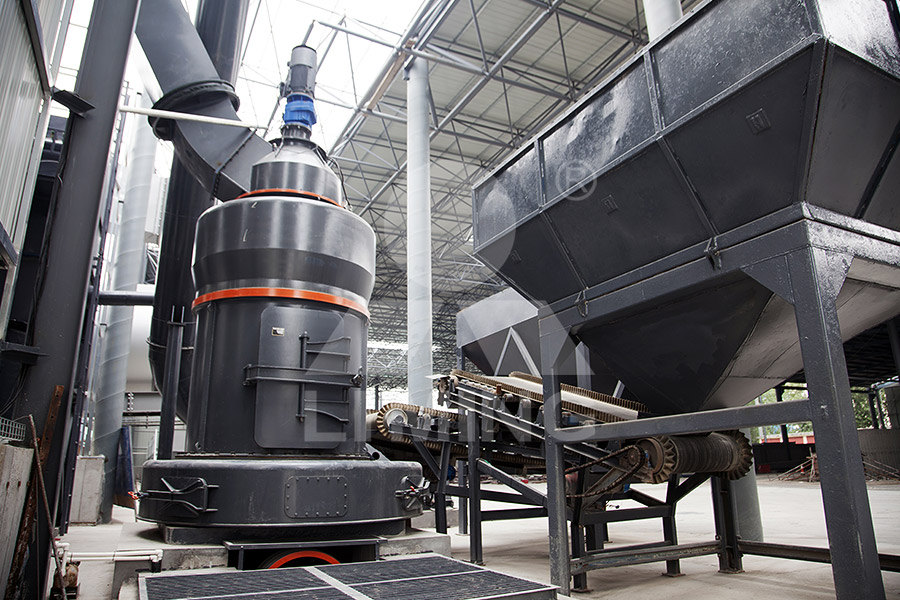
A comprehensive review on the applications of coal fly ash
2015年2月1日 Coal fly ash accounts for 5–20 wt% of feed coal and is typically found in the form of coarse bottom ash and fine fly ash, which represent 5–15 and 85–95 wt% of the total ash generated, respectivelyCoal ash is discharged by both wet and dry methods of coal combustion Bottom ash refers to the ash that falls down through the airflow to the bottom of the boiler and 625MWe conventional Rankine cycle power plant using pulverized coal firing (PF) (reference plant with atmospheric pulverized coal combustion) repowered with a new and potentially advantageous technology, namely, pressurized pulverized coal firing in a combined cycle (PPCC) power plant The performance of power plants is determined based on Thermodynamic analysis of a coalfired power plant 2012年1月1日 This study proposes reduction technology of ash deposition on the heat exchanger tube in pulverized coal fired (PCF) boilers Thermal spraying technique is adopted to change the surface properties Reduction of Ash Deposition in Pulverized Coal Fired BoilersThroughout the world, coal is responsible for generating approximately 38% of power Coal ash, a waste product, generated from the combustion of coal, consists of fly ash, bottom ash, boiler slag, and flue gas desulfurization material Fly ash, which is the main component of coal ash, is composed of spherical particulate matter with diameters that range from 01 μm to gt;100 A review on fly ash from coalfired power plants: chemical
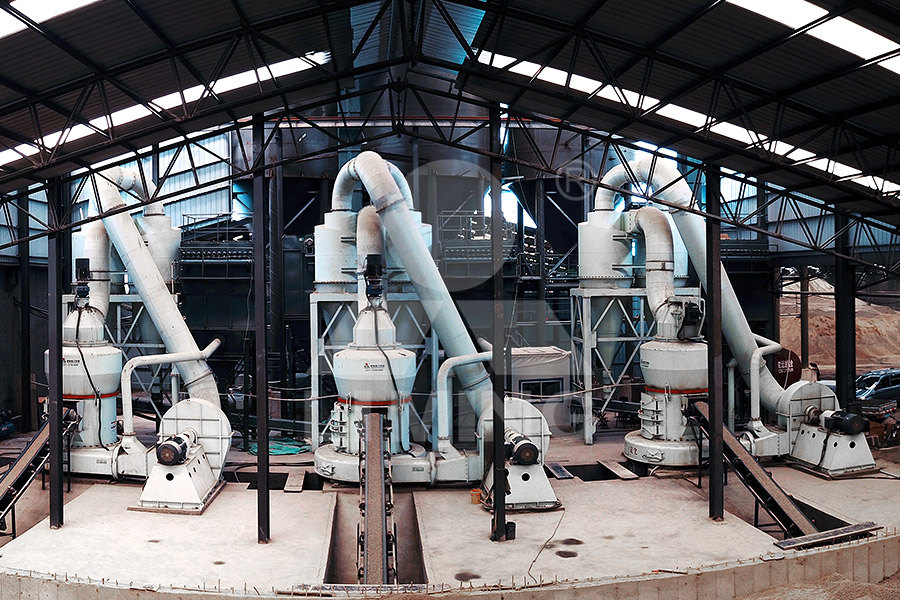
Control of Ash Deposition in Pulverized Coal Combustor
2010年10月20日 In solidfuel fired boilers, ash deposition on heattransfer surfaces can cause operational problems It is important to predict ashdeposition properties based on the ash composition of the solid 2024年7月11日 Out of the various pulverized coal boilers in operation, the fourcorner pulverized coal fired boiler stands out as the most extensively utilized and technologically advanced type, holding a significant share in the overall deployment of pulverized coal boilers [1]Therefore, the deep peak regulation and flexible operation of coalfired power units is a major trend in the Numerical Simulation of Combustion in 660 MW Tangentially Fired 2023年2月9日 Ammonia (NH3), as a derivative of hydrogen and energy carrier, is regarded as a lowcarbon fuel provided that it is produced from a renewable source or a carbon abated process of fossil fuel Cofiring ammonia with coal is a promising option for pulverized coalfired power plants to reduce CO2 emission Applying the cofiring in an existing pulverized coalfired boiler Evaluating the Effect of Ammonia CoFiring on the Performance of 2020年2月1日 Paper presents the results of pulverized coalfired steam boiler analysis under varying operating conditions To investigate the efficiency of the analyzed steam boiler, the energy and exergy Calculation methods of steam boiler operation factors under
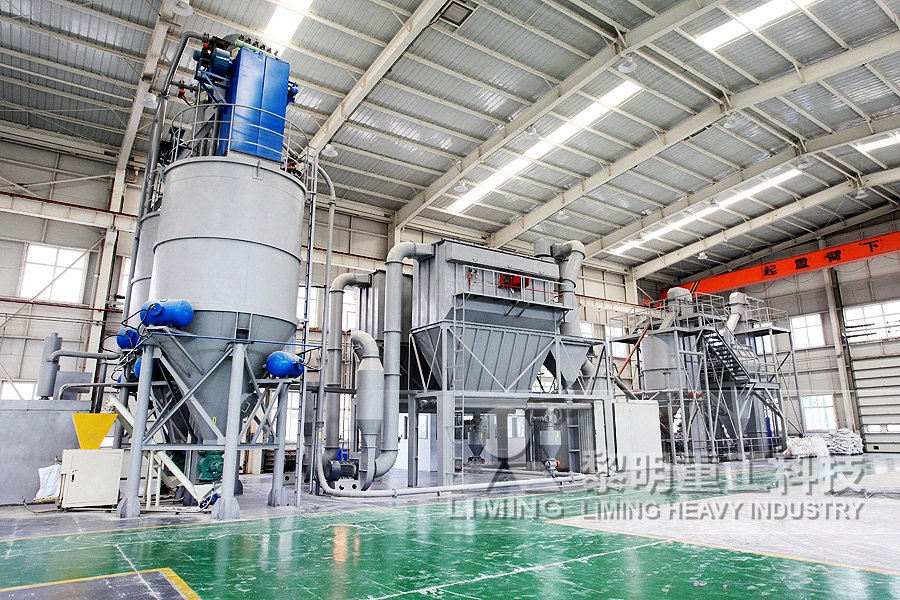
Trace element partitioning behavior of coal ganguefired CFB
2015年5月27日 Energy recovery is a promising method for coal gangue utilization, during which the prevention of secondary pollution, especially toxic metal emission, is a significant issue in the development of coal gangue utilization In the present study, investigation into trace element partitioning behavior from a coal ganguefired power plant in Shanxi province, China, has been 2016年1月1日 The use of an equilibrium approach to assess the behavior of coal ash has been used in several studies Harb et al [4] evaluated this approach for a number of coal ashes using observed slagging propensities and calculated melt fractions They found that using equilibrium calculations based on models using ideal solutions of complex species performed poorly for A temperaturehistory based model for the sticking probability of COAL FIRED BOILER PRINCIPALS Executive Talk : Coal Fired Boiler Principles Funded by : AkaunAmanah Industri Bekalan Elektrik (AAIBE) Ash 0165 m (14 t/day) Fly Ash 0658 m 30T 6793 m 280T 6175 m 280T 160 m 8682 m 15845T 12592T 8682 m 11794T 10916T 5543T 145T 3587T Ash 0593 m (51 t/day) 1543TCOAL FIRED BOILER PRINCIPALS Energy Commission1999年4月1日 This article presents an alternative approach to model ash deposition in pulverized coal fired systems It accounts for the effects of firing rate, burner It has been concluded that the accuracy of the predictions are adequate for the subsequent ash deposition calculations In general, the predicted deposition patterns for the Modelling ash deposition in pulverized coalfired applications
.jpg)
The multiple value characteristics of fly ash from Indian coal
2022年10月26日 Coalpowered thermal plants are the primary source of energy production around the globe More than half (5689%) of the Indian power plants use coal for power production Coal burning in power plants results in coal combustion residuals, which contain coal fly ash (CFA) that is recognized as principle byproduct CFA is difficult to characterize due to 2013年11月15日 One of the pulverized coal fired thermal power plants in India intended to find the root cause of frequent boiler tube failures in three 210 MW units(PDF) Design Computational Validation of Inline Bare2009年12月31日 Some of the ash generated through the combustion process of solid fuels, such as pulverized coal, adheres to the tube surface during heat exchangeControl of ash deposition in pulverized coal fired boiler2019年12月1日 The purpose of this paper is to investigate the effect of the pulverized coal drying temperature on fly ash carbon content and slagging of a 1000 MW unit coalfired boiler The pulverized coal was dried at three selected temperatures of 25 °C, 75 °C and 110 °C, and the moisture and porosity of the pulverized coal particles were measuredThe role of pulverized coal drying temperature in fly ash carbon
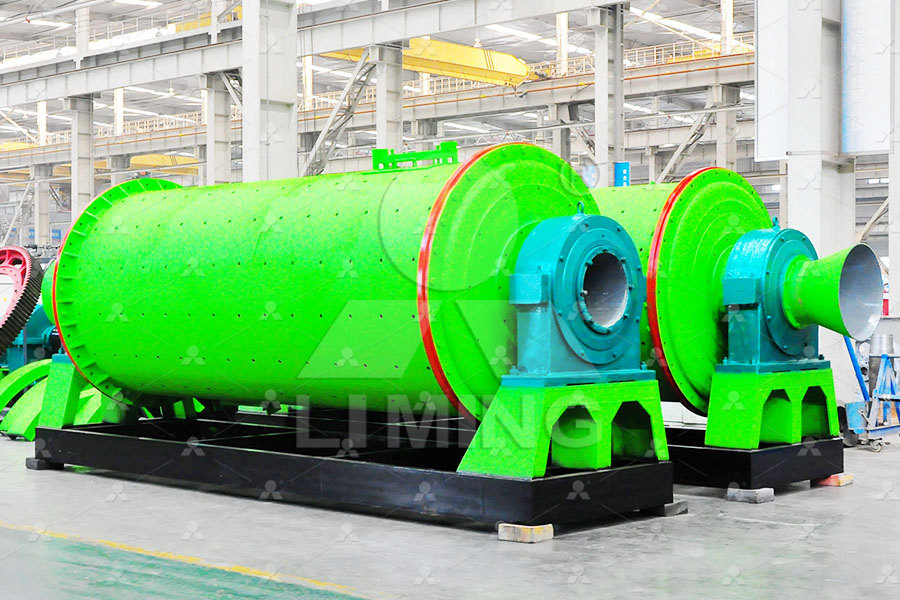
Heat transfer calculation methods in threedimensional CFD
2020年2月5日 For pulverized coalfired boilers, we can further assume that the sizes of ash particles are smaller than the original coal particles Fig 4 from Refs [33] , [34] shows the influence of ash particle size and temperature on the surface emissivity of ash deposits2023年3月27日 The coal consumption in our country mainly lies in coalfired power stations and industrial boilers Since the temperature change in the furnace influences combustion, slagging In the pulverized coal combustion process, turbulence impacts the radiation transmission of the medium by changing the shape of the flame, and the heat release acts on the turbulence field Simulation of Pulverized Coal Combustion Process Considering 2011年7月1日 An Indonesian UBC and an Australian bituminous coal of Coal A were selected as samples Those coal properties are shown in Table 1As seen from the table, the hemispherical temperature for Coal A under oxidizing conditions is 230 K higher than that of the UBCThe prominent features of Coal A are a higher SiO 2 content and lower CaO and Fe 2 O Ash deposition behavior of upgraded brown coal in pulverized coal 2024年4月15日 Goodwin et al [8] studied the absorption, scattering and extinction efficiency of fly ash in coalfired systems, and gave the Planck average value based on wavelength integration Early research was mainly based on the following assumptions: particles were smooth and homogeneous, and the optical constants of coal were approximated using linear mixingStudy on radiation characteristics of coal fired boiler changing