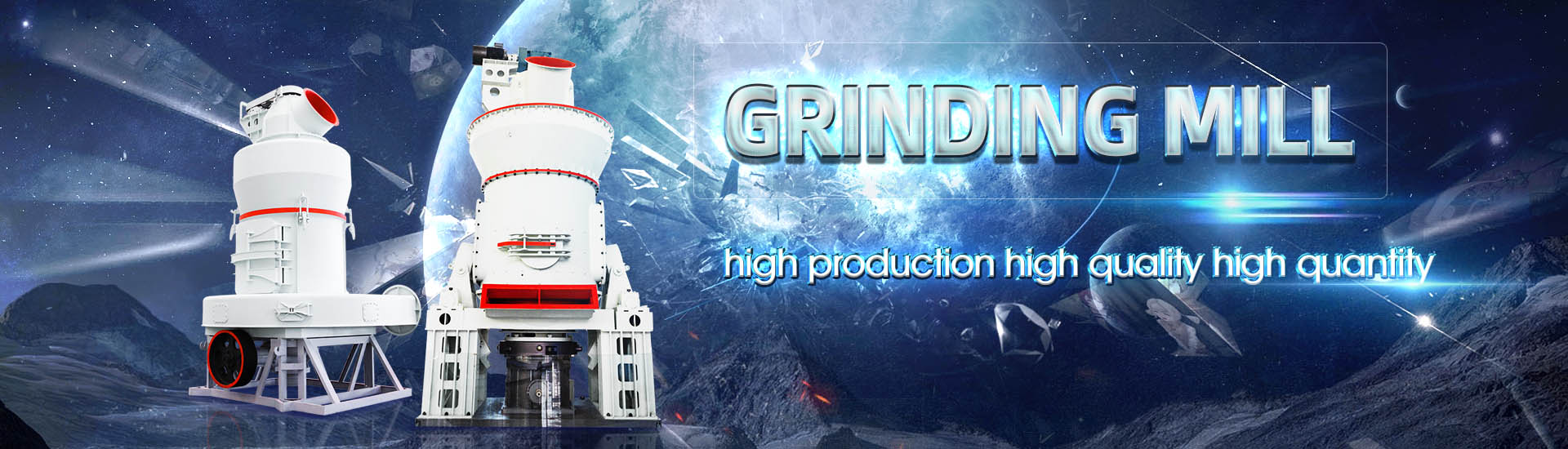
Reason for the coarse fineness of raw material vertical mill
.jpg)
Vertical roller mill for raw Application p rocess materials
Raw materials used to be ground to a rather finer level because the fineness of them affects the clinker burning efficiency Since the power consumption rate is high for the fine grinding of raw materials, great efforts were made to save energy by making raw materials coarse 2021年1月1日 For the past three decades the vertical roller mill has emerged to be the preferred choice for grinding raw materials With the grinding capacity of a vertical roller mill and the Review on vertical roller mill in cement industry its performance 2001年10月1日 LOESCHE vertical roller mills are widely used for the comminution of raw materials in the cement industry, for the comminution of clinker and blast furnace slag and for Loesche vertical roller mills for the comminution of ores and 2022年5月31日 As the rotation speed increases from 60 rpm to 100 rpm, the mass proportion of fines in the products decreases strongly, and that of coarse material increases significantly Analysis of vertical roller mill performance with changes in material
.jpg)
VERTICAL ROLLER MILLS A holistic VRM approach
The quadropol® vertical roller mill by thyssenkrupp Industrial Solutions takes a holistic approach to modern grinding systems in terms of its simple and compatible design Describing the key PROCESS TRAINING for operators of Vertical RAW Mills Heating of mill and grinding plant fineness of product, residue on 90)1 sieve[%] (product) and coarse material (grits) The grits are returned in the mill via the grit cone PROCESS TRAINING for operators of Vertical RAW Millsthat of a vertical roller mill (VRM) carrying out the same oper ations by a factor of between 15 and 2, depending on the degree of optimisation of the ball mill Fig 1 illustrates thisCEMENTS GROUND IN THE VERTICAL ROLLER MILL FULFIL THE 2017年9月11日 Due to the compact design and material transportation system of vertical roller mills (VRM), some important streams (total mill feed and discharge, dynamic separator feed and reject) remain in the Performance Evaluation of Vertical Roller Mill in
.jpg)
Rawmill Wikipedia
A raw mill is the equipment used to grind raw materials into "rawmix" during the manufacture of cement This was sliced up, discarding the coarse material at the bottom, and burned in the kiln Wet grinding is comparatively energyefficient, and so when good drygrinding equipment became available, For this reason, Vertical raw mill is important equipment widely used in the cement raw meal (cement raw materials) grinding section of the cement production process in cement plantBecause the vertical raw mill is the use of roller grinding principle to crush materials, its vertical raw mill operation is more efficient and energysaving, product output is more stable, so in cement industry, electric Vertical Raw Mill ball mills supplier2021年1月22日 In the whole process of cement production, the electricity consumption of a raw material mill accounts for about 24% of the total Based on the statistics of the electricity consumption of the raw A Survey and Analysis on Electricity Consumption of Raw Material Mill 2023年3月1日 On the other hand, no fineness soft sensing study in grinding circuits considers material analysis in the mill feed, therefore, a particular attention will be addressed to the right choice of parameters that impact raw meal fineness, including material quality characteristics, to build an accurate and reliable longterm modelEfficient machine learning model to predict fineness, in a vertical raw
.jpg)
Limestone Powder Ultrafine Vertical Roller Mill
Limestone Powder Ultrafine Vertical Roller Mill Modle : CLUM Series Finished Size: 4003000 mesh Processing Ability: 3 – 45t/h Max Feeding Size: 10 mm M 1 Set Price: $ Range Of Application: Limestone, Calcium Carbonate, Talc, Dry Grinding: Open circuit Ball mill, closed circuit Ball mill, vertical roller mill, Roll Press or Roll press in circuit with ball mill However, it would be seen that the most significant process and types used for raw material grinding operations in modern cement industry are: Process: Dry Closed circuit drygrinding Type of mill: Ball and Raw Material DryingGrinding Cement Plant Optimizationin combination with a ball mill for cement grinding applications and as finished product grinding units, as well as raw ingredient grinding equipment in mineral applications This paper will focus on the ball mill grinding process, its tools and optimisation possibilities (see Figure 1) The ball mill comminution process has a high electricalBALL MILLS Ball mill optimisation Holzinger ConsultingAfter the cement raw material is crushed, it will be sent into the raw mill for further grinding until a certain degree of fineness is reached, and then enter the clinker calcination process From the production experience of many cement plants, Raw Mill – Raw Mill In Cement Plant AGICO Cement
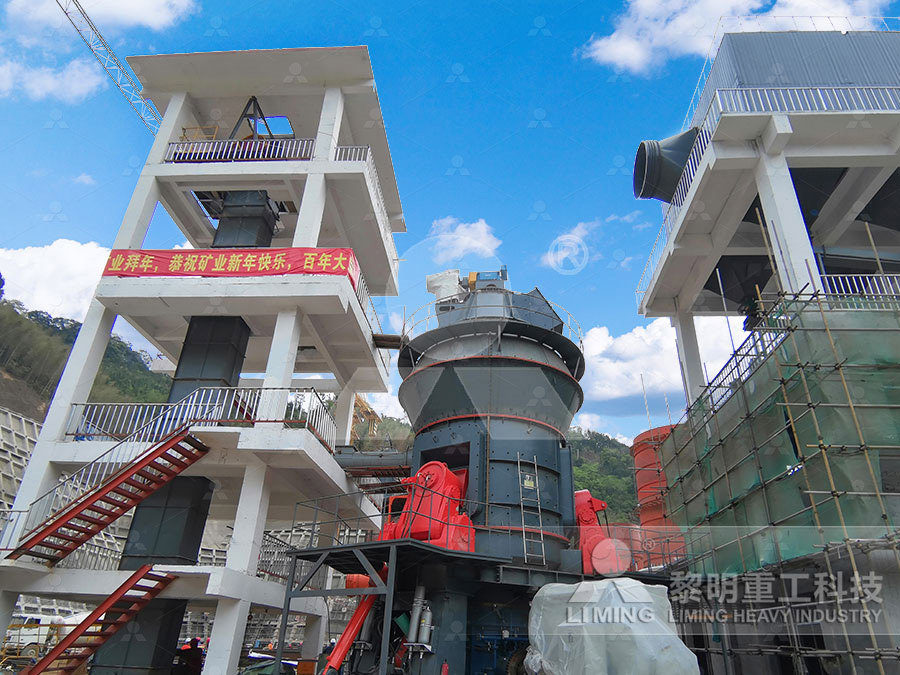
Operational parameters affecting the vertical roller mill
2016年9月1日 The results demonstrated that the VRM unit consumes around 81% (975 kWh/t of raw materials), and 36% (58 kWh/t of raw materials) more energy to grind raw material than the IBAT unit and domestic 2020年10月24日 Raw meal fineness is the percentage content of 80 µm sieving residue after the cement raw material is ground The accurate prediction of raw meal fineness in the vertical mill system is very Prediction of raw meal fineness in the grinding process of cement raw With the incensement of moisture of the raw material, the powder consumption will decrease obviously The vertical mill saves 30%40% of energy consumption compared to the ball mill Vertical mill has less noise than ball mill, about 2025dB Besides, vertical mill adopt enclosed system, and works under negative pressure, no dust, clean Vertical Cement MillIt is known that the variable is strong coupling, nonlinear, multivariable and large timedelay dynamic characteristics in the raw cement vertical mill grinding process Against the problem which is difficult to establish accurate mathematical model, this paper establishes a production index prediction model of vertical mill raw meal grinding process by using echo state network Modelling of the vertical raw cement mill grinding process based
.jpg)
Prediction of raw meal fineness in the grinding process of cement raw
2020年10月24日 The accurate prediction of raw meal fineness in the vertical mill system is very helpful for the operator to control the vertical mill However, due to the complexity of the industrial environment, the process variables have coupling, timevarying delay and nonlinear characteristics in the grinding process of cement raw materialThe LOESCHE scope of delivery includes a raw material mill with a capacity of 540 t/h of cement raw meal, a cement mill with an output of 350 t/h of clinker as well as a coal mill with an output of 45 t/h moisture and finenessCement Raw Material LoescheFig 1 Flowsheet of modular vertical roller mill 5000 R4 The required throughput rates were achieved in short time All fineness figures met the target values as well without anyGrinding Process Optimization Featuring Case Studies and If raw material fineness is too coarse, it will affect the firing of the clinker If the fineness exceeds the fine rules, the mill output will decrease and the power cent result of the raw material fineness per hour according to the laboratory The speed of the separator is such that the fineness is controlled within the range of R 008≤14~16%How to Improve Grinding Efficiency of Vertical Roller Mill
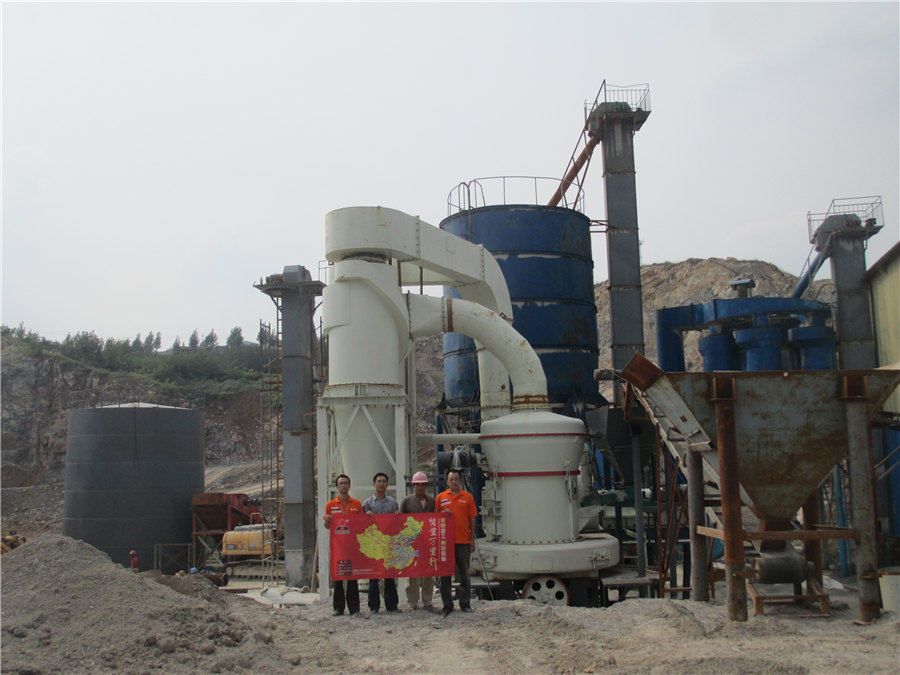
Increase productivity of vertical roller mill using seven QC tools
2021年1月29日 Vertical roller mills, VRMs, are widely used for grinding raw materials in factories engaged in the extraction and processing of minerals Any machine used for grinding or crushing consumes around Crushed material continues to move to mill edge, until being taken away by the wind ring in strong turbulence, and larger particles material again fell to the mill to continue to crush, the flow of materials through the upper part of the Raw mill Cement PlantThe vertical roller mill integrates crushing, drying, grinding, and conveying +17 Dolomite Ultrafine Vertical Roller Mill Discharge fineness: 1503000 meshes Feed size: 20 mm Output: 120 T/H Raw material grinding: Dolomite Ultrafine Vertical Roller MillThe ash hopper shell at the rotor’s base creates a space for the internal circulation of coarse particles, Generally, the retention time of raw materials in the vertical mill is 23 minutes, while in the ball mill, it can reach 1520 minutes fineness: Raw material moisture:Vertical roller mill DARKO
.jpg)
Polysius Roller Mills For grinding
for coarse material and an inlet chute designed to suit the mill feed material are integral parts of the grinding system Both the coarse feed valve and the chute can (if necessary) be indirectly heated in order to ensure reliable operation even in the case of high material moisture contents Wear protection Special materials, adapted to the abraVertical Roller SINOMALY produces cement raw material grinding mills in various specifications These machines are suitable for grinding mill production lines with an output of 2500t/d, 3200t/d, 4000t/d, 5000t/d, 6000t/d and 8000t/d The vertical grinding mill is utilized for the grinding of raw materials, mixed cement, and slag powderVertical Roller Mill for Cement Raw Material SINOMALYAll the foreign materials present in the raw material were removed Cleaned grains were then ground in a vertical hammer mill 32 Experimental plan 321 Experimental plan for the performance evaluation of porridge mill Proposed research work was carried out at the Food Processing Laboratory of Post Harvest Process and FoodPerformance evaluation of a Porridge (Hammer) Mill2016年6月1日 Raw meal fineness is the percentage content of 80 µm sieving residue after the cement raw material is ground The accurate prediction of raw meal fineness in the vertical mill system is very Modelling of the vertical raw cement mill grinding process based
2FD{P}PC]854]XQ.jpg)
Energysaving and Efficient Vertical Roller Mill Fote Machinery
A vertical roller mill is an energysaving mill that meets market demand while the coarse material is recirculated for further grinding 4 The finished product fineness The raw material moisture The finished product moisture Main motor power(kW) HLM1300K would be a length of 135 m and a diameter of 25 m, with a speed of approximately 20 revolutions per minute Such a mill would normally have a load of approximately 90 tons of grinding media, graduated from 90 mm to 60 mm in the first chamber, 50 mm to 15 mm in the second chamber and 15 mm down in the final chamberAn Introduction to Clinker Grinding and Cement StorageThe document discusses optimization and operation of vertical roller mills (VRMs) Key points include: 1) Continuously monitor and adjust process parameters to find the optimum operating conditions of highest capacity and lowest power consumption 2) Relevant process parameters to monitor include product rate, fineness, classifier speed, grinding force, power consumption, air Optimization of Vertical Raw Mill Operation PDFA new raw mill dassifier is now invariably of the ‘highefficiency’, rotating cagetype: the rotational speed controls product fineness at constant gas flow Raw milling can consume 10 30kWh/t; depending upon the materials and Raw milling and blending INFINITY FOR CEMENT
.jpg)
Best HLM Vertical Roller Mill Manufacturer and
As the vertical roller mill works, the motor drives the reducer to rotate the dial, the raw material are delivered to the center of the dial from the air lock rotary feeder The material moves to the edge of the dial due to the effect of centrifugal force 2022年11月23日 Raw meal fineness is the percentage content of 80 µm sieving residue after the cement raw material is ground The accurate prediction of raw meal fineness in the vertical mill system is very Research progress on control optimization of vertical roller mill 2020年10月24日 A twodimensional convolutional neural network method is proposed that is used to predict raw meal fineness during the grinding process of raw material and is proved to be very effective by comparing with the stateoftheart methods Raw meal fineness is the percentage content of 80 µm sieving residue after the cement raw material is ground The Prediction of raw meal fineness in the grinding process of cement raw MVR vertical roller mill from Gebr cement raw material, cement clinker or granulated blastfurnace slag – and how different their grindability and abrasiveness may be, Target fineness degrees: 1,500 – 6,000 cm 2 /g: Classifier: high efficiency classifier: Grinding table diameter:Cement mills and raw mills for high throughput rates Gebr Pfeiffer
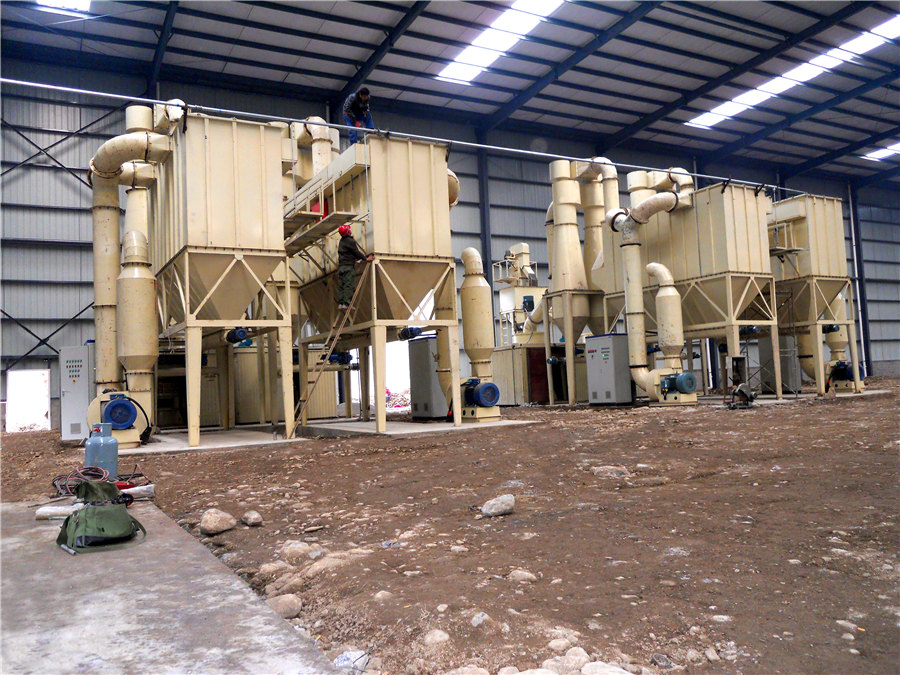
Vertical Roller Mills LNV TECHNOLOGY
Vertical Raw Mill: A vertical raw mill is mainly used in cement plants for raw material grinding Simple process flow, providing for drying, grinding and classifying all in one equipment; Minimum floor space requirement, compact layout and low investment in civil works; High grinding efficiency, low energy consumption and low wear on metal parts7 // Almost any plant for the grinding of cement raw material is a combination of machines specially adapted to the particular physical properties of the material to be ground As a result, our plants work efficiently without any trouble » Highly efficient grinding, drying, and separating in one unit » Outstanding production capacities exceeding 1,400 t/h in one single millPFEIFFER MILLS FOR THE CEMENT INDUSTRY2016年11月8日 The grinding process of vertical mill raw meal in cement industry features nonlinear, strong coupling and long timedelay, which is difficult to model precisely and implement stable control for Adaptive dynamic programming in raw meal fineness control of vertical Abstract: The grinding process of vertical mill raw meal in cement industry features nonlinear, strong coupling and long timedelay, which is difficult to model precisely and implement stable control for raw meal fineness Against the problem, a production index prediction model of vertical mill raw meal grindingAdaptive Dynamic Programming in Raw Meal Fineness Control of Vertical
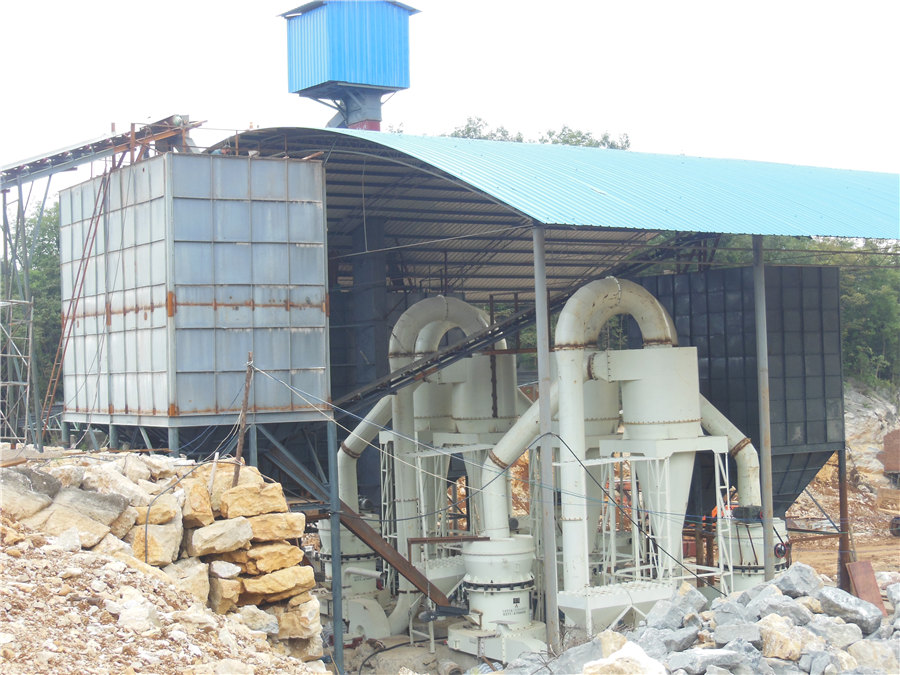
Raw Material Vertical Roller Mill
Raw Material Vertical Roller Mill xinxiang great wall machinery +09 Home; Products Vertical Roller Mill Cement greater than the specified size are separated and fall back to the plate, while meet the fineness demands are brought through the separator into the finished product warehouse Specifications Model