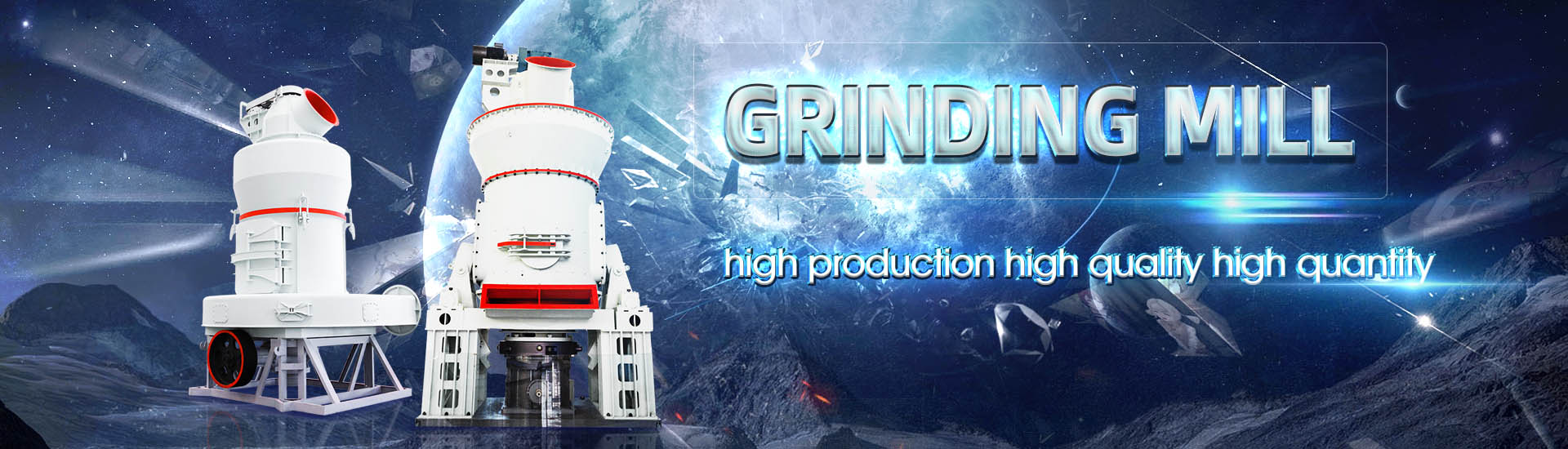
Diagram of raw material grinding in cement plant
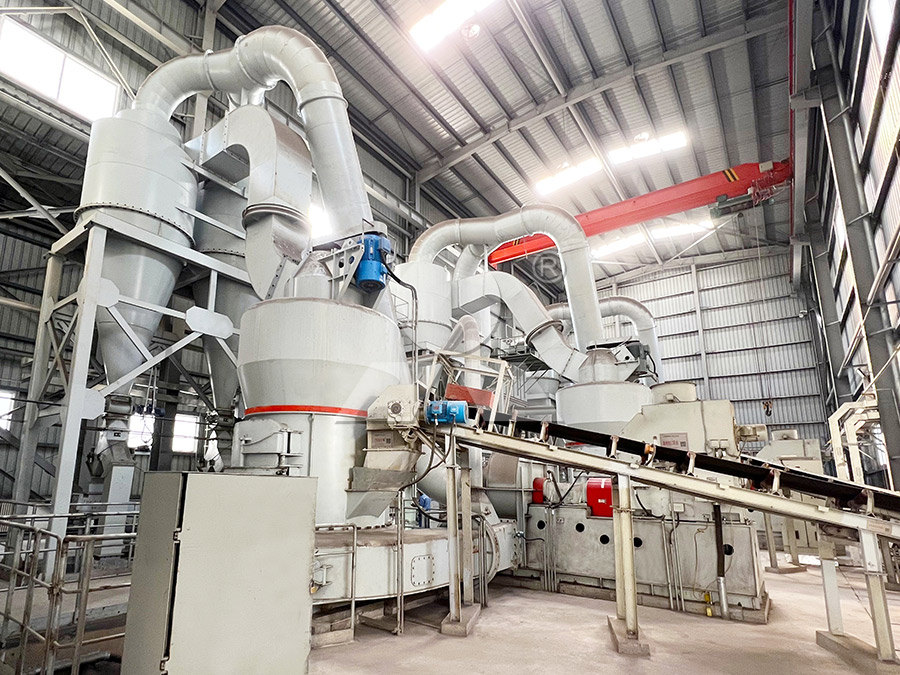
Raw Material DryingGrinding Cement Plant Optimization
Closed circuit ball mill with two compartments for coarse and fine grinding and a drying compartment with lifters are generally found in cement plants for raw material grinding 1971年8月17日 The initial production step in portland cement manufacturing is raw materials acquisition Calcium, the element of highest concentration in portland cement, is obtained from 116 Portland Cement Manufacturing US EPAand Iron ore are proportioned and sent to Raw mill Unit for grinding The proportioning ratio is done/adjusted every hour by the communication of weigh feeders beneath each bins and the CEMENT PRODUCTION AND QUALITY CONTROLIn this study, a flue gas emission from a cement manufacturing process 40% of the CO 2 comes from fossil fuel combustion in the kiln process, about 50% is due to decarbonation ofTypical cement manufacturing process flow diagram
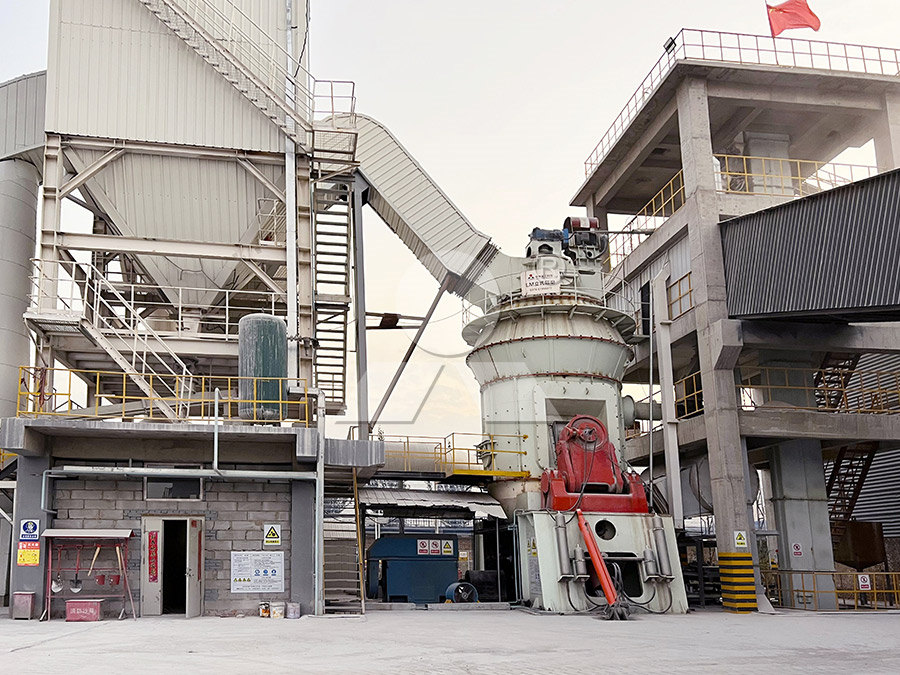
How Cement is Made Cement Manufacturing Process
There are six main stages of the cement manufacturing process The raw cement ingredients needed for cement production are limestone (calcium), sand and clay (silicon, aluminum, iron), produced in portland cement manufacturing plants A diagram of the process, which encompasses production of both portland and masonry cement, is shown in Figure 1161 As 116 Portland Cement Manufacturing US Environmental Rawmix is then fed to a cement kiln, which transforms it into clinker, which is then ground to make cement in the cement mill The raw milling stage of the process effectively defines the Rawmill Wikipediaraw materials, burning, grinding and quality control are supported by a range of chapters addressing critial topics such as maintenance and plant reporting, alongside a detailed The Cement Plant Operations Handbook International Cement
.jpg)
Cement Grinding Unit Process High Quality Cement
In raw grinding, a ball mill with a high efficiency separator is used to achieve uniform particle size in raw mix for the next stages of the manufacturing process At the Cement Grinding Stage, 90 – 95% of the clinker is mixed with gypsum Stage 2: Grinding, Proportioning, and Blending The crushed raw ingredients are made ready for the cementmaking process in the kiln by combining them with additives and grinding them to ensure a fine homogenous mixture The composition of cement is proportioned here depending on the desired properties of the cement Generally, limestone is 80%, and the remaining 20% How Cement is Made Cement Manufacturing Process2012年8月30日 Cooling and Final Grinding; Packing Shipping; Cement Manufacturing Process Phase 1: Raw Material Extraction Cement uses raw materials that cover calcium, silicon, iron and aluminum Such raw materials Cement Manufacturing Process Engineering IntroCrushing the raw materials Homogenizing the mixture Proportioning the raw materials accurately Grinding the materials into a fine powder Storing and blending the materials to ensure consistency How can I start a cement StepbyStep Guide to the Manufacturing of Cement
.jpg)
The Cement Plant Operations Handbook International Cement
cement manufacture – 3 Portland cement in today’s world 2 Raw materials management system – 22 Concrete problems 16 1 Raw materials – 2 Raw mix – 3 Reserves – 4 Crushing – 5 Drying – 6 Preblending – 7 Storage and handling 3 Raw milling and blending 3 Computerised Maintenance Management Systems 30 1 Raw milling 1971年8月17日 materials are produced in portland cement manufacturing plants A diagram of the process, which encompasses production of both portland and masonry cement, is shown in Figure 1161 As shown in the figure, the process can be divided into the following primary components: raw materials acquisition and handling, kiln feed preparation 116 Portland Cement Manufacturing US EPA2018年8月28日 Extraction of raw material and crushing of material Generally cement plants are fixed where the quarry of limestone is near bye This saves the extra fuel cost and makes cement somehow economical Raw materials are extracted from the quarry and by means of conveyor belt material is transported to the cement plant There are also various other Cement Manufacturing Process The Engineering CommunityRaw mill is generally called cement raw mill, raw mill in cement plant, it refers to a common type of cement equipment in the cement plantIn the cement manufacturing process, raw mill in cement plant grind cement raw materials into the raw mix, and the raw mix is sent to the cement kiln to make cement clinker, next, clinker and other admixtures will be ground into finished cement by Raw mill Cement Plant
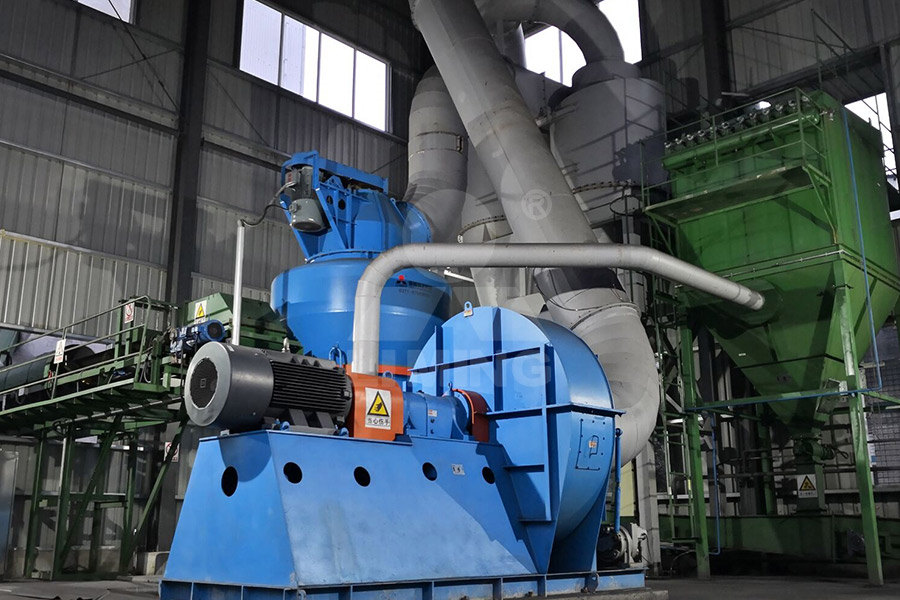
Cement Extraction, Processing, Manufacturing Britannica
2024年11月23日 Soft materials are broken down by vigorous stirring with water in wash mills, producing a fine slurry, which is passed through screens to remove oversize particles Blending A first approximation of the chemical composition required for a particular cement is obtained by selective quarrying and control of the raw material fed to the crushing and grinding plantAGICO Cement Vertical Mill AGICO Cement Ball Mill Cement Vertical Mill Grinding System Cement vertical mill, also called roller mill, is another raw mill commonly used in cement pared with the cement ball mill, it has a great difference in structure, grinding principle, process layout, automatic control, and energy consumption, which play an important role in the Raw Mill – Raw Mill In Cement Plant AGICO Cement Raw MillEVERYTHING YOU NEED TO KNOW ABOUT ESTABLISHING CEMENT GRINDING PLANT 1MTY These will include loading and unloading of raw materials and cement into trucks/tippers, handling during storage, Ref Appendix C on page 96 for electrical details in single line diagramEVERYTHING YOU NEED TO KNOW ABOUT ESTABLISHING CEMENT GRINDING PLANT Such a plant dries raw material with a moisture content of 68 % The wear of grinding media when grinding cement raw materials is approx 2050 grams/t of mill throughput Fig 423 shows a capacity diagram of FLSdryerpul Drying of raw materials INFINITY FOR CEMENT
.jpg)
Cement Raw Meal Homogenization Process in The
Raw meal homogenization is the most important process link of the four, accounting for 40% of the homogenization task It is an important factor to support the balanced and stable working performance of preheaters and kilns, and 2016年1月20日 In the surveyed cement plant, three balances are established between input and output material in the raw mill, clinker production, and cement grinding system 248 t, 469 t, and 341 t of materials are required to produce a ton of the product in raw material preparation, clinker production, and cement grinding stages; waste gases account for the largest proportion of the Analysis of material flow and consumption in cement production Cement is typically made from limestone and clay or shale These raw materials are extracted from the quarry crushed to a very fine powder and then blended in the correct proportions This blended raw material is called the 'raw feed' or 'kiln feed' and is heated in a rotary kiln where it reaches a temperature of about 1400 C to 1500 CCement manufacturing components of a cement plant Understanding Cementvertical roller grinding mills for grinding: • Coal • Cement raw material • Clinker / granulated slag • Industrial minerals, and • Ores The core elements of these plants are the Loesche vertical mills for drygrinding the abovementioned grinding stock Loesche has PROCESS OPTIMISATION FOR LOESCHE GRINDING PLANTS
.jpg)
From raw materials to cement
Drying and raw grinding Burning The burning of the raw meal at approx 1,450°C is carried out in Lepol or preheater kilns that work by varying methods, the The crushed material is transported into the raw material storage of the cement plant by conveyorbelts, cableways or railways and also in exceptional cases with trucks1 Mixing of raw material The major raw materials used in the manufacture of cement are Calcium, Silicon, Iron and Aluminum These minerals are used in different form as per the availability of the minerals Table shows the raw materials for Portland cement manufacture The mixing procedure of the manufacture of cement is done in 2 methods, Dry Manufacture of Cement Materials and Manufacturing Process of 2016年10月5日 In this chapter an introduction of widely applied energyefficient grinding technologies in cement grinding and description of the operating principles of the related equipments and comparisons over each other in terms of grinding efficiency, specific energy consumption, production capacity and cement quality are given A case study performed on a EnergyEfficient Technologies in Cement Grinding IntechOpenHowever, new cement kilns are of the 'dry process' type Dry process kilns In a modern works, the blended raw material enters the kiln via the preheater tower Here, hot gases from the kiln, and probably the cooled clinker at the far end of the kiln, are used to heat the raw meal As a result, the raw meal is already hot before it enters the Manufacturing the cement kiln Understanding Cement
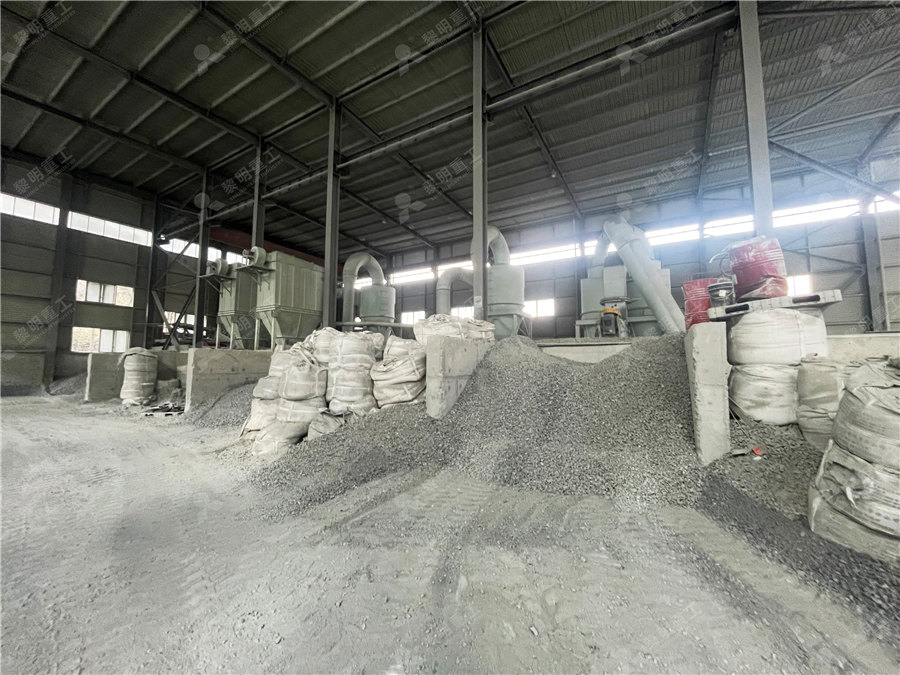
Everything you need to know about Crushers in Cement industry
An intermediary storage of the raw material is necessary since the material flow has to be divided up after the primary crusher and the secondary crushers should be loaded The jaw crusher should be mentioned as alternative to the primary gyratory crusher However, its use for cement raw materials is advantageous only under very special conditionsIn recent years, the tube mill has gradually been replaced by roller mill and other equipment, became the main equipment of cement grinding in cement cement manufacturing plant While in raw meal grinding, with the mature use of Raw Material Preparation in Cement Manufacturing 2021年3月3日 In this chapter, the term cement is used in its classical meaning: a crystalline compound of calcium silicates and other calcium compounds having hydraulic properties Cement is therefore a hydraulic binder, that is, a material that chemically reacts with water by converting the waterbinder system into a solid matrix with the capacity to agglomerate other solid materialsCement SpringerLinkCorrect blending and concentrating on the quality of raw materials are the two key factors that decide the superiority of the cement Raw material blending is in fact one of the most important processes in cement manufacturing since it has a Raw Mill in Cement Plant Cement Manufacturing
.jpg)
Cement Production Process Cement Manufacturing Process AGICO CEMENT
2020年8月25日 Feeding raw meal into cement kiln to make clinker, the clinker, and some mixed materials will be ground together by cement grinding plant, the finished cement will be done Cement raw material preparation: Limestone is main raw materials for cement manufacturing, and most cement plants are located next to the quarry to reduce the transportation 2023年12月20日 Cement manufacturing is a complex process that begins with mining and then grinding raw materials that include limestone and clay, to a fine powder, called raw meal, which is then heated to a sintering temperature as high as 1450 °C in a cement kilnThe Cement Manufacturing Process Thermo Fisher ScientificThe entire manufacturing process in a modern plant is now controlled through a microprocessor based programmable logic control system to maintain a consistently uniform quality of cement and a high rate of production The entire operation of the plant is controlled centrally in a single control room and the plant employs minimum of manpower as compared to previous plants Cement Manufacturing Process: How the Cement is Made?2024年9月5日 2 Raw material grinding After crushing, the raw materials are carried to a grinding mill and made into a fine powder This is done using equipment such as ball mills or vertical roller mills The grinding process ensures the correct particle size of raw material and its homogeneous constitution, which is so critical for product quality 3 A Comprehensive Guide to the Cement Manufacturing Process
.jpg)
Stages in cement production flow chart [43] ResearchGate
Download scientific diagram Stages in cement production flow chart [43] from publication: A review on kiln system modeling The purpose of this study is to evaluate performance cement of 2017年9月11日 The cement industry is the main supplier of raw materials for the production of concrete and reinforced concrete For grinding cement, two types of mills are used ball and rollerPerformance Evaluation of Vertical Roller Mill in Cement GrindingCement Grinding Plant Hot Sale; Modular Grinding Plant; Concrete Batching Plant; Small Concrete Batching Plant; Mobile Concrete Batching Plant; Generally, the proportion of components in cement raw materials is 6775% limestone, 10 How Is Cement Produced in Cement Plants Cement Making With the continuous development of cement production technology, the production limit of cement plants is also increasing Nowadays, cement plants with a clinker capacity of more than 5000 tons per day are gradually becoming Large Cement Plant Design Principles AGICO
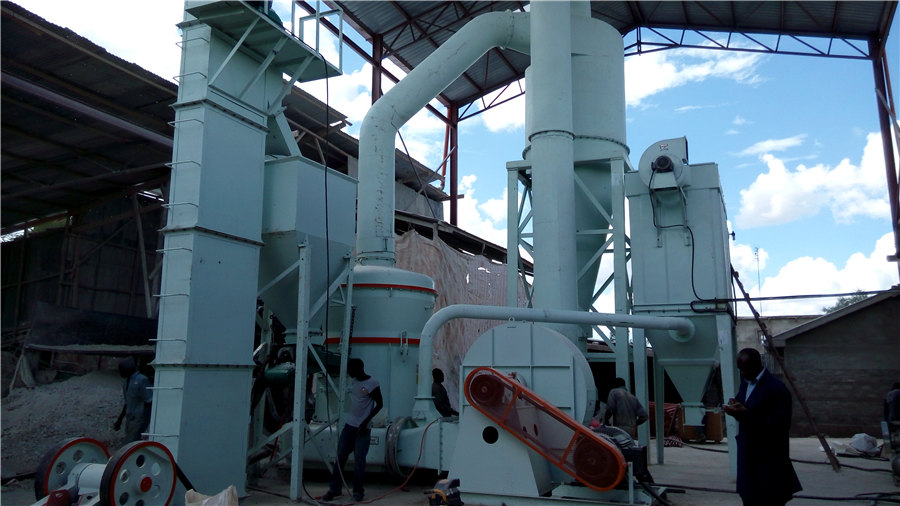
OPTIMIZATION OF CEMENT GRINDING OPERATION IN BALL MILLS
grinding progresses, which is not the case in the above graph Compare this with the milling progress as presented in Figure 2 after optimization The following picture shows the condition of the grinding media and the material in one of the grinding chambers of the mill observationThese s provide a clear idea of internal conditions While each cement plant may differ in layout, equipment, and appearance, the general process of manufacturing portland cement is the same: crushed limestone and sand are mixed with ground clay, shale, iron ore, fly ash and How Cement is Made Portland Cement AssociationOperationally, roller mills are quite sensitive to changes in parameters Abrasive raw materials such as sand can cause quite rapid wear of grinding surfaces Material is retained on the table using a dam ring at its circumference As the table wears, the depth of material on the tab(e increases and mill power consumption increasesRaw milling and blending INFINITY FOR CEMENT EQUIPMENTAfter been crushed, proportioned and ground into appropriate granularity, most of the raw materials will be fed into cement kiln for calcining clinker, and then we usually add an appropriate amount of gypsum (sometimes mixed with other materials or additives) in the cement grinding process, finally obtaining the cement products with a qualified finenessAll about the Wet Process of Cement Manufacturing
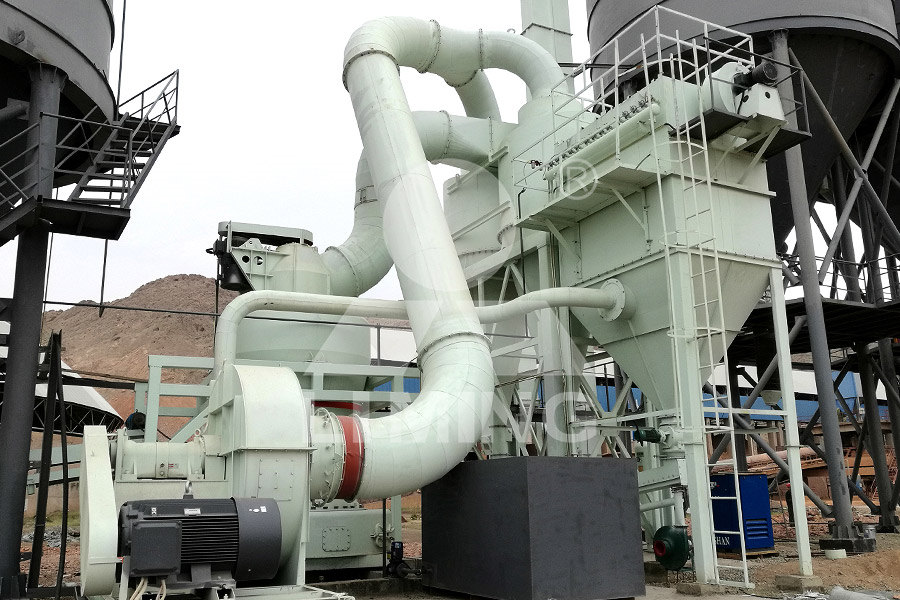
Cement Manufacturing Process and Its Environmental Impact
2023年7月10日 The cement manufacturing process involves the extraction and processing of raw materials, such as limestone, clay, and shale, which are then heated in a kiln at high temperatures to form clinkerCement conveyor refers to a belt conveyor in cement plant, which is necessary accessory equipment in the cement production line A belt conveyor is a kind of material handling equipment with strong adaptability, applied for conveying bulk density less than 167t / m³, it is mostly used for powder, granular, small lump materials, and bagged materials, such as sand, ore, coal, Cement Conveyor Belt Conveyor In Cement Plant AGICO2019年1月3日 Clinker grinding technology is the most energyintensive process in cement manufacturing Traditionally, it was treated as "low on technology" and "high on energy" as grinding circuits use more than 60 per cent of total energy consumed and account for most of the manufacturing cost Since the increasing energy cost started burning the benefits significantly, Clinker grinding technology in cement manufacturingDownload scientific diagram The cement raw material blending process and its control system from publication: Modeling and Optimization of Cement Raw Materials Blending Process This paper The cement raw material blending process and its control system
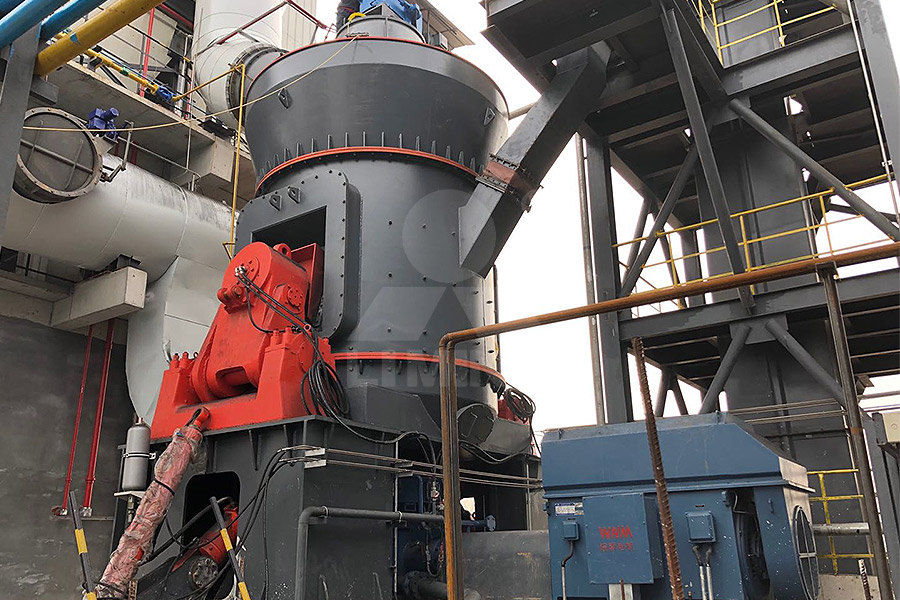
Optimizing Material Flow with Belt Conveyor in Cement Plant
2024年5月23日 In cement plants, belt conveyors are used to move raw materials such as limestone, clay, and other additives from the quarry to the processing plant They are also employed in the transportation of intermediate products like clinker and finished goods like cement to storage or shipping areas