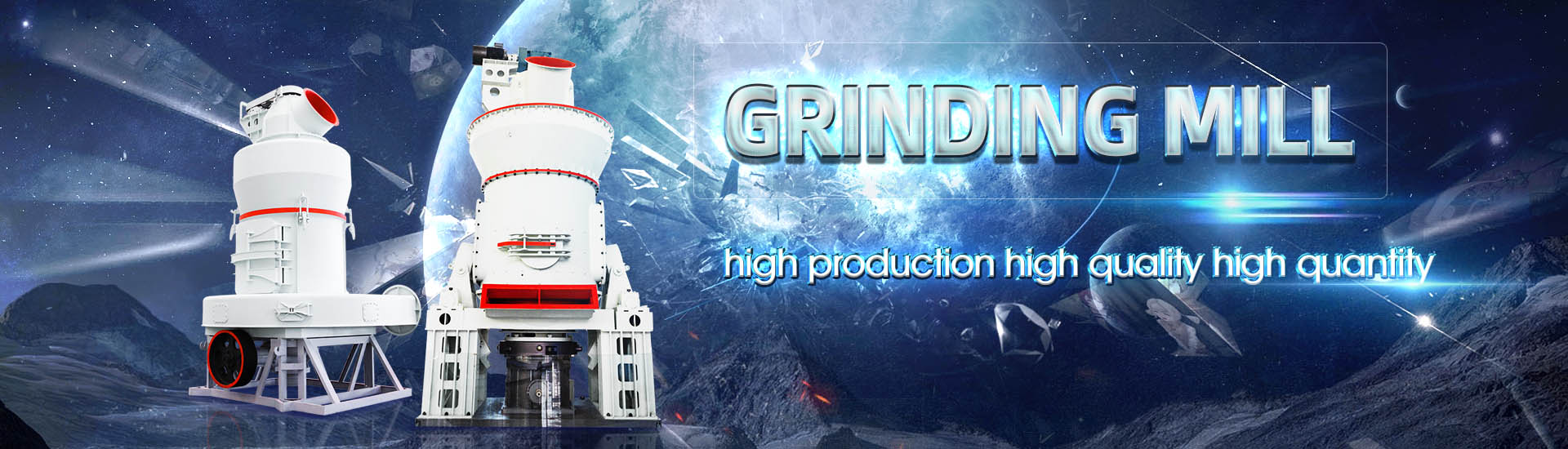
Ore crushing cost
.jpg)
Mining crushing grinding costs Thunder Said Energy
Mining crushinggrinding costs run at $10/ton of ore as a good rule of thumb, including $20/Tpa capex costs and 20kWh/ton of energy costs2016年1月11日 The approximate running costs for crushing plants of different capacities up to 4,000 tons per day on the basis of an eighthour crushing day Crusher Operating Costs: How to Optimize and ReduceDirect Costs The largest primary gyratory crushers cost US $2 million or more, while overall crushing plant costs can be as high as $18 million It’s necessary therefore to estimate crusher Crushing Plant Design and Layout Considerations 911 MetallurgistProduction costs are commonly provided as two headline metrics: Total Cash Cost (TCC) and Allin Sustaining Cost (AISC) Allin Sustaining Cost (AISC) includes cost items additional to Methodology: Production costs data set World Gold Council
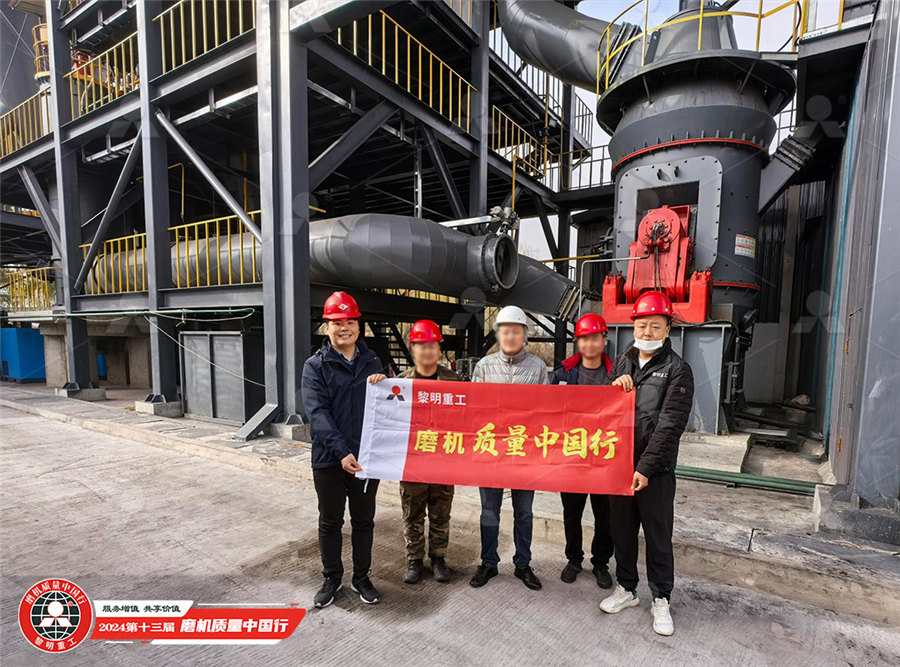
Drilling and blasting, loading and primary crushing
Therefore, the optimization of drilling and blasting is essential for controlling ore fragmentation and, consequently, the productivity and operating cost levels of the subsequent stagesThese 2 modular crushing and screening plants are unique, costefficient and productive, and designed to provide significant time and resource savings The Mining Crushing Stations are made up of 2 solutions: FIT™ Stations and Crushing Metso2018年12月12日 The particle size obtained through rock fragmentation affects loading, hauling and crushing performance Higher rock fragmentation means higher drilling and blasting costs A systemwide approach to minimize the operational cost of 2016年2月11日 Clean ore could be crushed and stockpiled without having to multihandle it, and prevented degradation of the finished product Minimal use of haul trucks with cost savings of about $4000 per day Maintenance and Reduction, control of operating costs in the mining

Development of ore sorting and its impact on mineral processing
2014年10月15日 The greatest operating cost for a typical ore sorter is the compressed air used to separate stones after they have passed through the sensor (Fig 2) The cost associated These costs mainly consist of fuel or electricity consumption, regular maintenance, spare parts, and consumables such as lubricants It is important to consider the type and capacity of the crusher, Iron ore crushing line; Aggregate crushing Calculation Of Owning And Operating Costs Of CrushersHistorically, ore transport was done by diesel trucks, Drilling and blasting, loading and primary crushing operating costs as functions of P80 for (a) CE and (b) JCDrilling and blasting, loading and primary crushing 2015年12月26日 The Compressive Strength of rocks is measured by crushing cylinder shaped (drill core) ore samples of 2″ x 2″ (51mm X 51mm) This techniques allows for a rocktorock relative comparison The Bond’ Crushing Crushing in Mineral Processing 911Metallurgist
.jpg)
Copper Ore Crushing, Grinding Flotation 911Metallurgist
2017年5月21日 They had the unique opportunity of processing the same ore both conventionally and in a semiautogenous circuit and were able to compare capital and operating costs The capital cost analysis at the time of the expansion showed 53,00000 per ton for the conventional plant and $2,00000 per ton for the SAG plantThe first step in the mining and processing of nearly any mineral ore is comminution Since the oil embargo of 1979, the mining companies have been striving to reduce energy consumption and costs The first serious step was the introduction of inpit crushing in the early 1980s With inpit crushing accepted as a standard design mode, the energy saving emphasis turned to Primary Crusher Optimisation for Improved ComminutionAdditionally, our Crushing Services are dedicated to optimizing mineral processing efficiency through the utilization of cuttingedge technology, which liberates minerals, reduces costs, and supports environmentally responsible mining practices Efficiency and Cost Savings: By optimising ore particle size, Crushing and Screening Services Ore sorting solutionsMetso is combining our legacy and expertise to introduce the Mining Crushing Stations These 2 modular crushing and screening plants are unique, costefficient and productive, and designed to provide significant time and resource savings The Mining Crushing Stations are made up of 2 solutions: FIT™ Stations and Foresight™ StationsCrushing Metso
.jpg)
Types of Crushers: Choosing the Right One for Each Stage
2024年7月17日 Crushers are widely used in ore crushing, aggregate production, construction waste recycling, and natural stone processing Understanding material characteristics and defining production needs can help you choose the right crushing method, saving costs throughout the production process Types of crushers2022年1月1日 Hematite and magnetite, the two predominant iron ores, require different processing routes Highgrade hematite direct shipping ores generally only require crushing and screening to meet the size requirements of lump (typically between 6 and 30 mm) and fines (typically less than 6 mm) minution and classification technologies of iron ore2024年10月17日 Clirik’s ore crusher integrates cuttingedge crushing technology, ensuring efficient processing of stone materials through a meticulously designed crushing chamber Compared to traditional equipment, it can increase crushing efficiency by more than 20% while reducing energy consumption, bringing higher output ratios and lower operating costs to What types of ore crusher are there and how much does one cost2014年10月15日 The energy costs required to refine metal values contained in ore to concentrates constitute the majority of the cost to produce metals On average across the mining industry, 44% of the total electricity consumption is dedicated to crushing and milling activities (Fig 1)Size reduction operations, nearly 150 × 10 9 kW h, are the largest single consumer of Development of ore sorting and its impact on mineral processing
.jpg)
Methodology: Production costs data set World Gold Council
1 Total Cash Cost (TCC) is a metric which includes all costs incurred at the mine site, such as open pit and underground mining, ore processing, (crushing, grinding, leaching etc) and onsite general administrative costs incurred in producing an intermediate goldbearing product such as a doré or sulphide concentrate%PDF16 %âãÏÓ 4215 0 obj > endobj 4235 0 obj >/Encrypt 4216 0 R/Filter/FlateDecode/ID[87C03FABF6FB2246BC4F9AB649B4B217>]/Index[4215 26]/Info 4214 0 R/Length 101 AusIMM – Leading the way for people in resourcesPrimary crushing followed by wet SAG or AG milling and ball or pebble milling Airswept AG milling (for coarse grind) Historically, the lowest operating cost for finegrained ores was achieved by multistage, fully autogenous grinding (Koivistoinen et al, 1989) with integrated magnetic separation steps between the stagesEcoefficient and costeffective process design for magnetite iron ore 2014年1月1日 The cost change in bottom (a) and top deck (b) 2 ORE CRUSHING PLANT The Cayeli mine is the first fully mechanized underground copper and zinc mine operating since 1994, Factors affecting the performance of crushing plant operations
.jpg)
Iron ore crushing and screening process SBM Ultrafine Powder
2022年8月3日 Iron ore crushing process: In the iron ore crushing process, the feeder, first crushing, secondary crushing, screening, Therefore, the processing cost of beneficiation is reduced It can be seen that the stage grindingstage separation process is more reasonable than the twostage continuous grinding 42016年3月11日 In the crushing section, the ore as it comes from the mine is broken down dry to a size suitable for the wet grinding machines ; these can, if necessary, be Metal costs in the form of crusher liners have not quite doubled in the last 20 years, Crushing Plant Flowsheet DesignLayout 911Metallurgist2023年11月20日 Transforming Iron Ore Processing in Nigeria: CostEfficient Crushing Plant Setup Nigeria, a nation endowed with vast mineral resources, is at the forefront of a transformative initiative in the iron ore crushing plant setup cost in nigeria LinkedInWhen ore is first processed (typically close to the mine) The remediation project has cost the mining company $70 million, and the mine was out of operation for 3 years (2014 to 2017) Mining involves blasting, breaking and crushing rock, and so dust is created82: Mining and Ore Processing Geosciences LibreTexts
.jpg)
Mineral processing Wikipedia
Crushing, a form of comminution, one of the unit operations of mineral processing Mineral processing is the process of separating commercially valuable minerals from their ores in the field of extractive metallurgy [1] Depending on the processes used in each instance, it is often referred to as ore dressing or ore milling Beneficiation is any process that improves (benefits) the Actual cost will vary depending of the process details and detailed equipment list and origin Copper, Zinc, Lead, etc, Ore PROCESS TAILINGS FILTRATION PLANT ORE CRUSHING GRINDING PLANT MERRILL CROWE IN LEACHING GOLD / SILVER PROCESSING CIL LEACHING FOR GOLD / SILVER CONCENTRATIONMineral Processing Plants Gold, Silver, Copper, Zinc, Lead, etc, Ore2003年1月1日 cost in crushing and grinding has been reduced by 30% No consideration is given here to crushing 40 million tons of ore per year, the savi ngs are $118 million per year(PDF) The Effects of Blasting on Crushing and Grinding 2016年5月10日 In the handling of wet, sticky ores such as encountered in tropical areas having distinct dry and rainy seasons, the crushing plant is a section of the mill which must be planned very carefully Unless this is done, crushing becomes a constant source of trouble resulting in lost production and high milling cost In some areas rainfall is high for prolonged periodsCrushing and Grinding Wet Sticky Ore 911Metallurgist
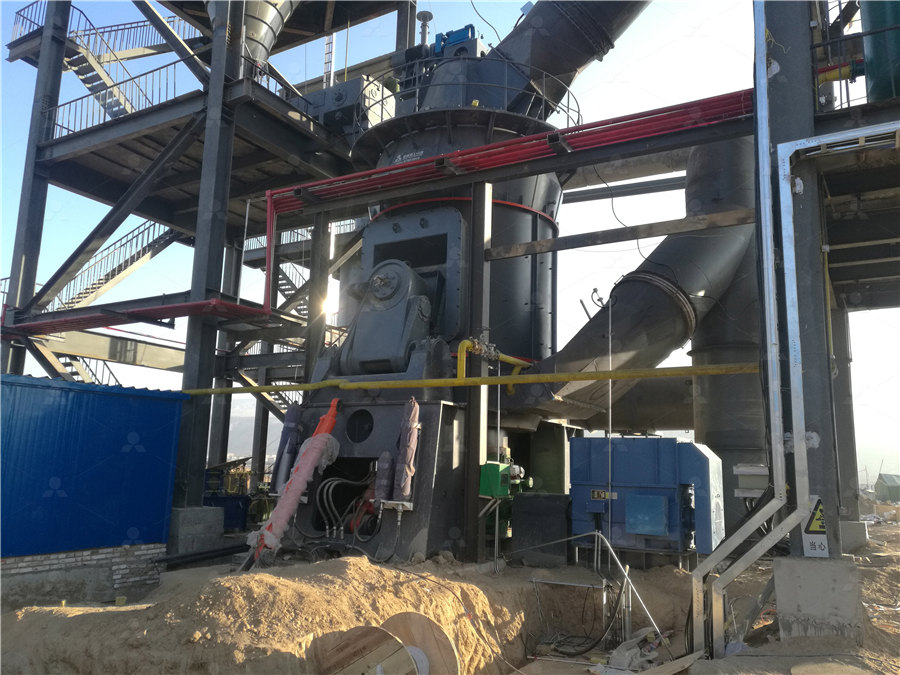
MeasurementControl for Crushing and Screening Process
2023年6月3日 It mainly includes crushing process control, crushing appliance fault diagnosis, and automatic distributing control Crushing Process Control To ensure the continuous, stable, and safe operation of the ore crushing production process, it is necessary to monitor the running state and parameters of key equipment (such as crusher and belt conveyor) in real time for 2016年3月19日 The cost data above referred to has been compiled from actual operating results and shows the cost of milling both for the old 50ton plant and the new 100 ton concentrator, as is now in use Note the reduction in milling costs through the use of the new flowsheet which includes an 8cell “SubA” Flotation MachineOperating Costs of Gold Processing Plant 911MetallurgistThe largest primary gyratory crushers cost US $2 million or more, while overall crushing plant costs can be as high as $18 million It’s necessary therefore to estimate crusher installation costs based on equipment costs plus the following direct costs, including construction contractor indirects: • Earthworks • MechanicalCrushing Plant Design and Layout Considerations MINE 2017年3月4日 Crushing of ore and minerals There are three stages in crushing as stage 1, The finer the ore, the higher the cost and finer grinding usually results in improved value recoverySIZE REDUCTION BY CRUSHING METHODS ResearchGate
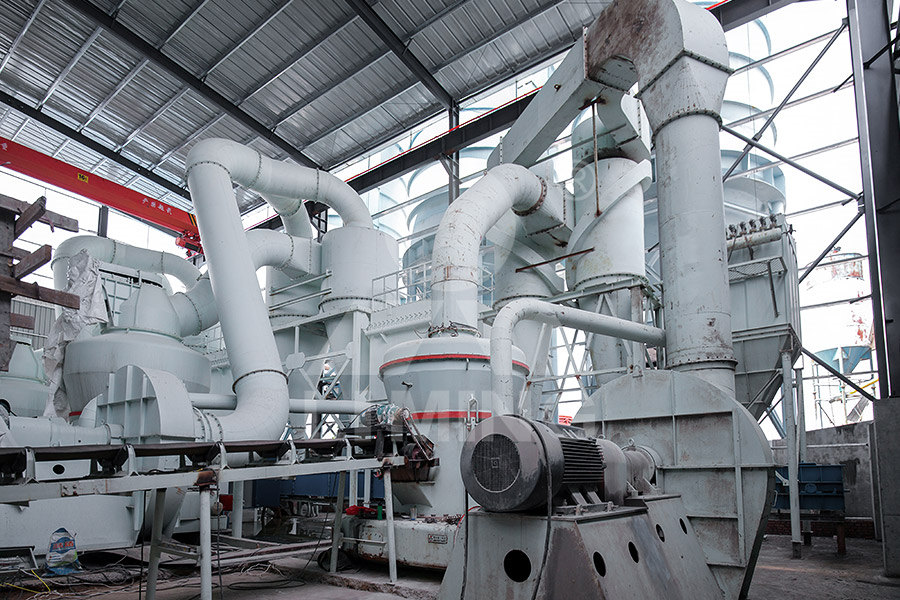
Gold Ore Processing Guide from Crushing to Cyanidation
2024年8月10日 01 Crushing and grinding for gold ore processing The cost of crushing and grinding in gold ore processing accounts for about 40%60% of the total cost of mineral processing Therefore, how to improve the efficiency of crushing and grinding and reduce energy consumption and production costs is the key to promoting the continuous development and 2016年2月29日 Some of the metallurgical relationships that must be considered from the testwork program as follows: ore grade relationship to gold recovery, crushing and grinding parameters and their relationship to the ore variability in the ore body, effect of other minerals on the process, minerals and/compounds that negatively impact processing cost such as oxidized Gold Extraction Recovery Processes 911MetallurgistReducing Grinding Energy and Cost Magnetite Iron Ore Design Case Study A Jankovic and W Valery Metso Process Technology Innovation, PO Box 1028, Eagle Farm Qld, 4009, AustraliaReducing Grinding Energy and Cost Magnetite Iron OreMetso ore sorting solutions combines our industry leading crushing and screening systems with ore sorting technology to deliver a more productive and energy efficient operation by removing unwanted waste including declining ore Bulk ore sorting solutions Metso
.jpg)
The Ore Grade and Depth Influence on Copper
2016年11月22日 The study evaluated implications of different ore grades and minedepth on the energy inputs to extract and process copper Based on a 191 value dataset from 28 copper mining operations, seven model equations 2014年4月3日 Fig 3 Types of processing ores The wet processing (Fig 4) is normally practiced for low / medium grade (60 % Fe to 63 % Fe) hematite iron ore The wet process consists of multistage crushing followed by different stages of washing in the form of scrubbing and / or screening, and classification etc, but the advantage is only partial removal of adhered alumina and free Beneficiation of Iron Ores IspatGuruSolution for Four years ago an orecrushing unit was installed at a mine which cost P81,000 Annual operating costs for this unit are P3,540 A unit that will handle the same quantity of ore and have the same operating costs as the one now in service can be installed for P75,000Answered: Four years ago an orecrushing unit was bartlebyThe study offers a detailed cost analysis of Iron Production via Ore Mining, Crushing, Concentrating, Extracting Using Blast Furnace In addition, the report incorporates the manufacturing process with detailed process and material flow, operating costs along with financial expenses and depreciation chargesIron Production Cost Analysis via Ore Mining, Crushing,
.jpg)
Particle ore sorting Metso
Metso sensorbased ore sorting, powered by TOMRA technology, will help you rise up to the challenges of the mining industry, including declining ore grades, high energy and production costs, water shortages, and stricter environmental regulations Increases lifeofmine in challenging environmentsReducing Grinding Energy and Cost Magnetite Iron Ore Design Case Study A Jankovic and W Valery Metso Process Technology Innovation, PO Box 1028, Eagle Farm Qld, 4009, The principles of particle breakage in crushing and grinding equipment remained mainly unchanged over the years with energy efficiency reducing as the product size (PDF) Reducing Grinding Energy and Cost Magnetite Iron Ore 2024年7月13日 A 120 TPH stone crushing production line typically consists of a vibrating feeder, It has a high reduction ratio and is capable of handling various types of rocks and ores Robust equipment design and reliable components minimize downtime and maintenance costs120 TPH stone crushing production lineDOI: 101080/X2016 Corpus ID: ; Cost analysis of material handling systems in open pit mining: Case study on an iron ore prefeasibility study @article{deWerk2017CostAO, title={Cost analysis of material handling systems in open pit mining: Case study on an iron ore prefeasibility study}, author={Marco de Werk and Burak Cost analysis of material handling systems in open pit mining: