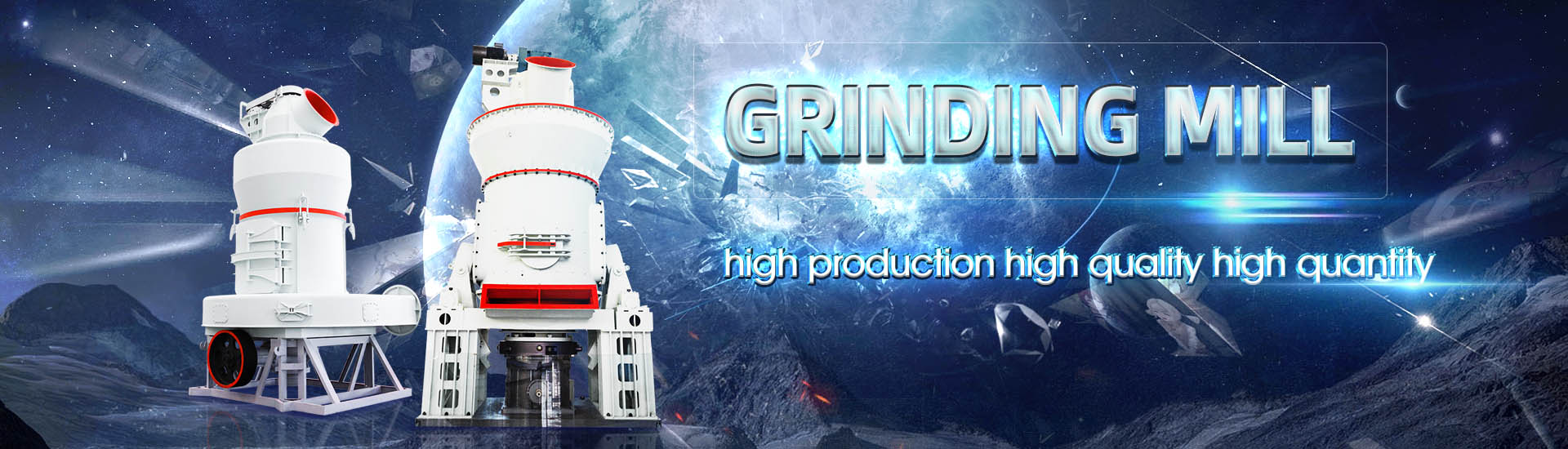
Jigging quicklime coal process, vertical mill
.jpg)
Coal mill, gypsum mill, clay mill, etc Pfeiffer MPS mills
MPS vertical mill from Pfeiffer is the ideal allrounder Grinding of coal, petcoke, clay, limestone, quicklime, gypsum, and many other materialsGebr Pfeiffer SE; Barbarossastr 5054: Phone: +49 (0)631 4161 0: 67655 ReferencesThe core elements of these plants are the Loesche vertical mills for drygrinding the abovementioned grinding stock Loesche has developed and built the largest and most efficient PROCESS OPTIMISATION FOR LOESCHE GRINDING PLANTSVertical roller mills are not only used for grinding cement raw materials but also find an application in grinding a wide variety of coal types in cement and power plants Gebr Pfeiffer SE (GPSE) COAL GRINDING IMPS: more than meets the eye Gebr Pfeiffer
.jpg)
PASSION FOR GRINDING
Processing of all quicklime qualities with the most different feed sizes, producing nonexpanding hydrates with guaranteed residual moisture rates of less than 1%coal grinding 1979 First vertical mill for cement grinding Gebr Pfeiffer Process Technology 7 Determination of all important parameters at the test station Characterization of products at the lab SOLUTION PROVIDER Quicklime Clay Talcum Pozzolana Kaolin and many others 14 16PASSION FOR GRINDINGVertical Coal Mill (VCM) is equipment for grinding and pulverizing coal into micron size Rotary kilns then use the powders as fuel burners The VCM has a housing section equipped with a lining The layout of the coal mill with a rotary classifier2007年1月1日 Jigging has been known for centuries as an ore concentration process [10] Hydraulic jigs of different types are widely used in several applications, covering every density range from less than 1 Advances in dry jigging improves coal quality ResearchGate
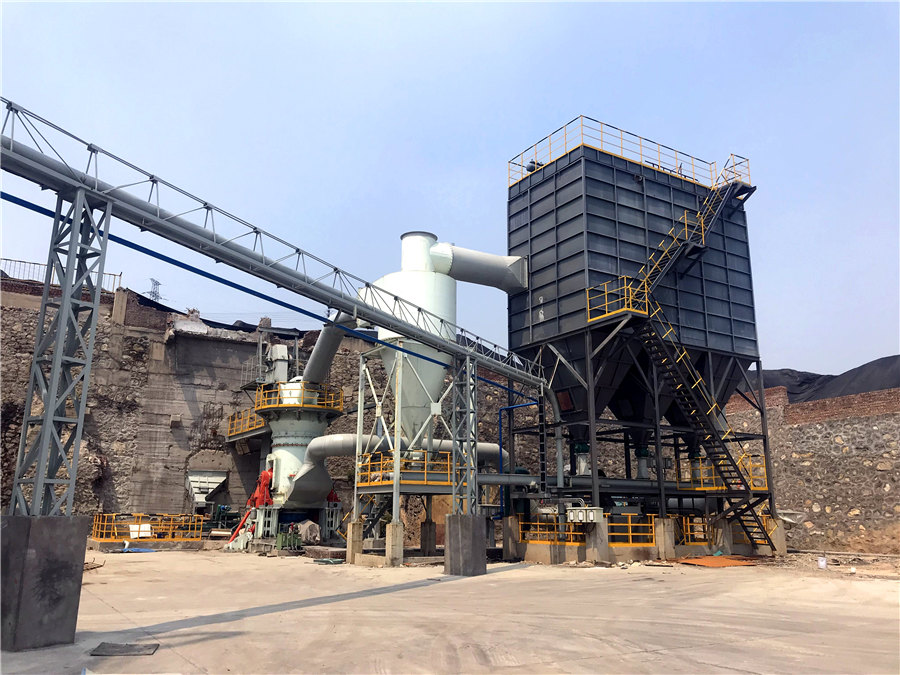
Operation Manual: HRM1700M Vertical Roller Coal Mill
HRM1700MVRM Free download as PDF File (pdf), Text File (txt) or read online for free The document provides installation and operation instructions for the HRM1700M Vertical Roller Coal Mill It describes the mill's technical parameters, components, structure, working principles, and installation process Key aspects include grinding rollers that can be removed for Coal, lignite or petcoke are ground in the Pfeiffer vertical mill by using available hot process gases The grinding plant can be inerted The raw coal is dried while being ground in the mill even if feed moisture exceeds 25% The feed size that can be handled is up to 100 mm, making twostep precrushing unnecessaryCoal mills for all requirements Gebr Pfeiffer2019年11月21日 Jigging process is one of the most effective gravity separation methods used to deal with coarse ore with large density difference, which mainly utilizes the flow of vertical alternating medium (usually water or air) caused by strong vibration to make ore particles stratified according to relative density and collect light and light minerals by appropriate methods, thus 5 Factors That Affects the Jigging ProcessMPS vertical mill from Pfeiffer is the ideal allrounder Grinding of coal, petcoke, clay, limestone, quicklime, gypsum, and many other materials built to last, reliable and energyefficient is the optimum solution when it comes to performing several process steps in one unit Advantages of the MPS vertical mill Low capital expenditure Coal mill, gypsum mill, clay mill, etc Pfeiffer MPS mills

ATOX® Coal Mill FLSmidth Cement
Our ATOX® Coal Mill has large rollers with great grinding capability of virtually all types of raw coal The rollers work harmoniously with a highlyefficient separator and feed sluice to consistently and reliably deliver coal meal to your desired fineness and moisture levelThe crushed small pieces of quicklime are sent to the silo by the elevator, and then sent to the mill grinding chamber for grinding evenly and quantitatively by the vibrating feederFine powder processing can choose LM vertical mill, MTW European mill, 5X European intelligent mill; The ultrafine powder processing generally adopts LUM ultrafine vertical mill, MW ring roller micro quicklime processing plant, quicklime grinding machine, quicklime 2021年3月12日 1 Introduction Two mill systems are employed for most coal grinding applications in the cement industry These are, on the one hand, vertical roller mills (VRM) that have achieved a share of almost 90% and, on the other MPS mills for coal grinding AYS EngineeringThe quality of the quicklime is largely dependent on the efficiency of the grinding process, which is where the vertical mill comes into play The vertical mill, also known as the vertical roller mill, has emerged as a leading piece of equipment for the production of quicklime due to its advanced technology and operational excellence 2 Vertical mill: The preferred equipment for quicklime production
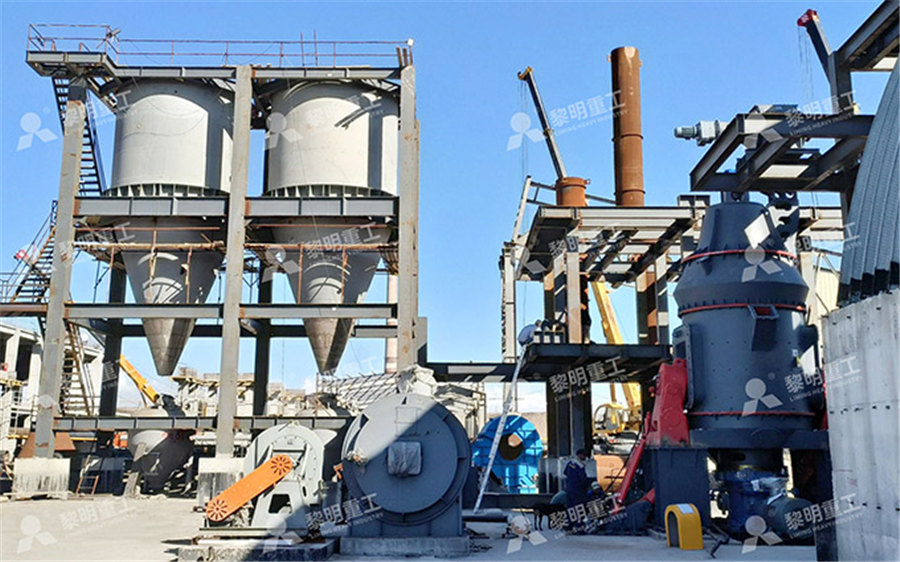
Vertical Grinding Mill (Coal Pulverizer) Explained
Introduction This article concerns itself with vertical grinding mills used for coal pulverization only (coal pulverizers), although vertical grinding mills can and are used for other purposes The 3D model in the saVRee database represents a 2023年10月3日 Rocker Arms: The function of the rocker arm device of the cement vertical roller mill is to transmit the pressure provided by the hydraulic cylinder to the grinding roller, so that it can be transformed into the grinding force act on the material bed The rocker arm device is mainly composed of upper rocker arm, lower rocker arm, rocker arm shaft, bearing and What is a vertical roller mill (VRM)? A Comprehensive Guide to Vertical Coal Mill is specially used for ultrafine grinding of raw coal and bituminous coal materials in cement, power plants, iron and steel plants and other fields The GRMC coal vertical mill produced by CHAENG adopts special structural design and production process, which is energysaving and environmentally friendlycoal grinding machine CHAENGMill connection: the circulating fan is connected to the explosionproof bag dust collector and the inert gas supplement pipe: the inert gas supplement pipe is connected to a heat source system that supplements the low oxygen content heat source gas to the pulverized coal vertical mill to control the low oxygen in the extracorporeal circulation system The limiting oxygen content What is the process flow of vertical mill to produce pulverized coal?
.jpg)
Coal mill pulverizer in thermal power plants PPT SlideShare
2012年11月17日 20 131Fineness Fineness is an indicator of the quality of the pulverizer action Specifically, fineness is a measurement of the percentage of a coal sample that passes through a set of test sieves usually designated at 50, 100, and 200 mesh A 70% coal sample passing through a 200 mesh screen indicates optimum mill performance The mill wear and 2020年11月10日 jigging as a process of repeated fluidization and defluidization of a bed in which the upward fluid velocity continuously varies along the operating cycle [ 51Jigging: A Review of Fundamentals and Future DirectionsCLS Attritors – Stirred Vertical Ball Mill Lime Slaker The patented CLS Attritor Stirred Vertical Ball Mill Lime Slaker operates in continuous processing mode and has been used successfully in power generating plants for flue gas desulphurization (FGD) The Attritor will slake the lime as well as grind the inert grit, eliminating grit separation andVertical Ball Mill Vertical Media Mill Union Process2014年1月1日 Two mill systems are employed for most coal grinding applications in the cement industry These are, on the one hand, vertical roller mills (VRM) that have achieved a share of almost 90% and, on (PDF) MPS mills for coal grinding ResearchGate
.jpg)
An investigation of performance characteristics and energetic
2020年8月12日 This study shows the performance of a currently running vertical roller coal mill (VRM) in an existing coalfired power plant In a power plant, the coal mill is the critical equipment, whose The Vertimill® is globally recognized as an energy efficient grinding mill Through a low total cost of ownership, it brings substantial improvement to the profitability of concentrators During the years, Vertimill® technology has proven to be Vertimill® Metso2022年5月31日 Analysis of vertical roller mill performance with changes in material properties and operating conditions using DEM Author links open overlay panel Chang Liu a, Meshless modeling of the breakage process of a coal prism within vertical roller mills 2nd International Conference on Advanced Materials, Beijing, CHINA (2013), pp Analysis of vertical roller mill performance with changes in Liming Heavy Industry: Explore the green innovation road of "dual carbon" powder making together! Grinding mill, MTW European Type Trapezium Mill,
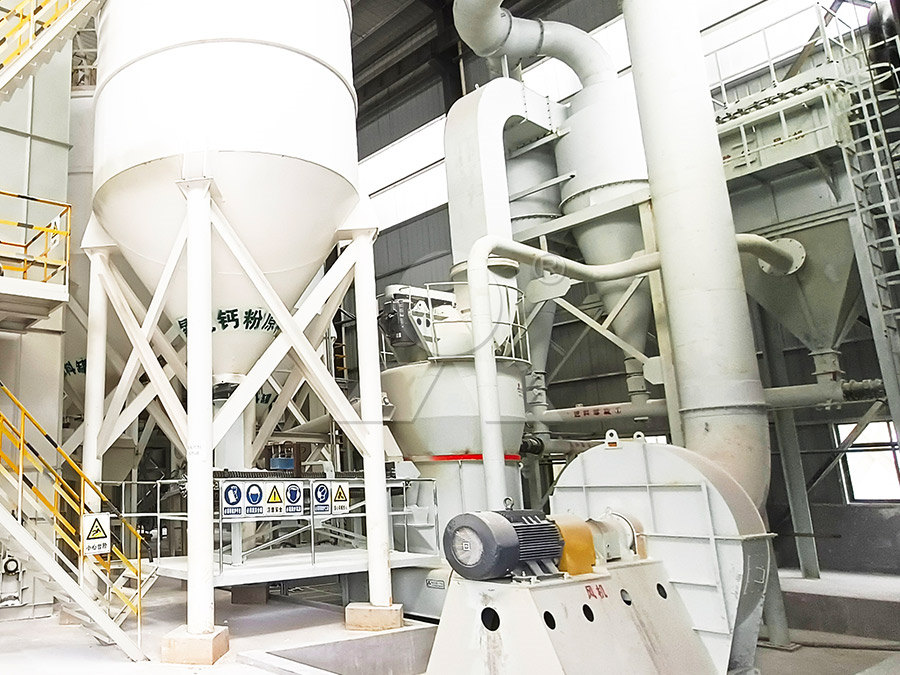
News, conferences and events Pfeiffer
The quicklime to be used at this factory is produced in the company’s own kilns and ground in an MPS 180 B Pfeiffer vertical roller to the fineness required to the suit the process The MPS mill, increasing the existing grinding capacity of the factory, competed successfully against ring roll mills that the company already has in operation thereCoal: Turkey: Bilim Makina, Elazig: MPS 2500 BK: Petcoke: Egypt: Helwan (Bejing Triumph) MPS 3350 BK: Coal / petcoke: Quicklime: Czech Republic: Cementarny a Vapenky Mokra: KLV 05/1000/5,0: Quicklime: Guatemala : More than 2800 Pfeiffer vertical mills grinding various materials worldwideProven vertical mill solutions References Gebr PfeifferFig2 Schematic process flow of vertical roller mill for grinding of raw materials Vertical roller mills are adopted in 20 cement plants (44 mills) in Japan Results Table Energy saving effect of the vertical roller mill Ball mill Specific power Cost estimationVertical roller mill for raw Application p rocess materialsCement Milling Process Vertical Roller Mill English VersionOn this occasion I will explain about the Vertical Roller Mill for cement grinding processTheCement Milling Process Vertical Roller Mill English Version
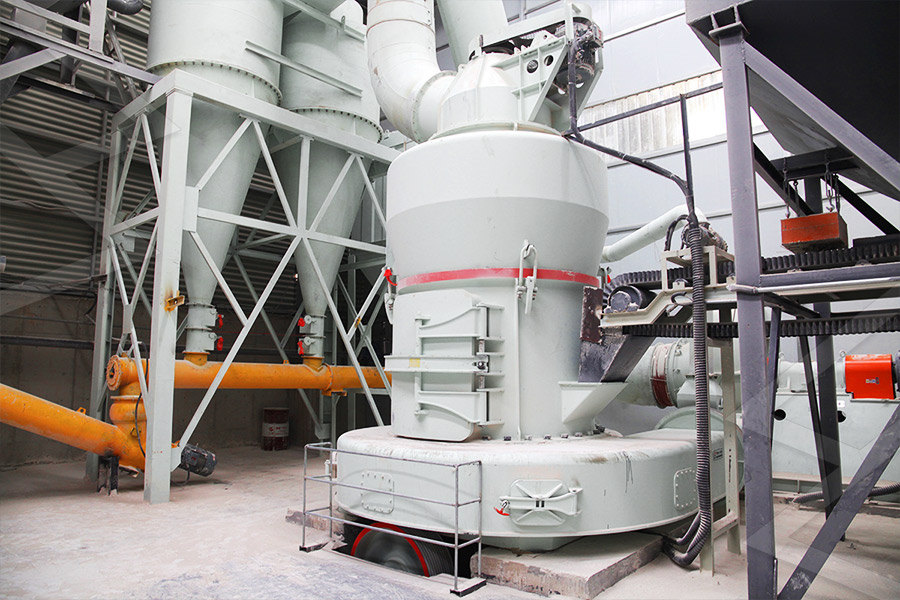
vertical roller mill, vertical slag mill, vertical coal mill, Superfine
Vertical Roller Mill Vertical roller mills are mainly engaged in three major fields of coal powder, slag and nonmetallic ore Divided into: vertical coal mill, vertical slag mill, vertical roller mill, and ultrafine vertical mill (ultrafine powder processing) One machine is multipurpose, it can be used for grinding, grading, crushing, drying, etcThe MPS ZGM coal mill is a type of coal mill that operates at a speed of 50300r/min This equipment is used to prepare and process auxiliary materials for blast furnace ironmaking It provides suitable coal powder for the blast furnace ironmaking systemMPS ZGM Coal MillGrinding Equipment YingYong MachineryVertical Coal Mill, also known as coal mill, for superfine grinding of raw coal, soft coal specifically for cement, power plant, steel mill and other fields Its special design structure and production process creates the higher production efficiency with lower energy consumption, less dust, lower noise than ball mill, which meets national standard of energy saving industryVertical Coal Mill Great Wall• Mill motor speed • Mill air flow/mill differential pressure • Temperature after the mill • Pressure before the mill • Grinding stock feed • Classifier speed • Mill fan speed • Water spraying • Hot gas • Fresh air Manipulated variables Disturbance variable Process measured value RelauchLMmaster 6 250814 11:47PROCESS OPTIMISATION FOR LOESCHE GRINDING PLANTS
.jpg)
Jigging: A Review of Fundamentals and Future
2020年11月10日 The process of particle segregation in jigs is, by definition, linked to the vertical oscillatory motion of the jigging bed caused by the pulsation strokes Some authors have found it appropriate to consider jigging as a Vertical roller mills are mainly engaged in three major fields of slag, coal powder, and nonmetallic ore Divided into: vertical roller mill, vertical slag mill, vertical coal mill, and ultrafine vertical millvertical roller mill, vertical coal mill, vertical slag mill, superfine Download scientific diagram Technical specifications of vertical roller coal mill from publication: An investigation of performance characteristics and energetic efficiency of vertical roller Technical specifications of vertical roller coal millOur main products include ultrafine vertical roller mill, ultrafine grinding mill, stone powder production Raymond Mill for Coal Powder Making The Raymond mill is widely used for grinding coal into fine the customer using our HGM grinding mill as a stone dust making machine to process quicklime (calcium oxide) and calcium SBM Ultrafine Powder Technology Industrial Grinding Mill,
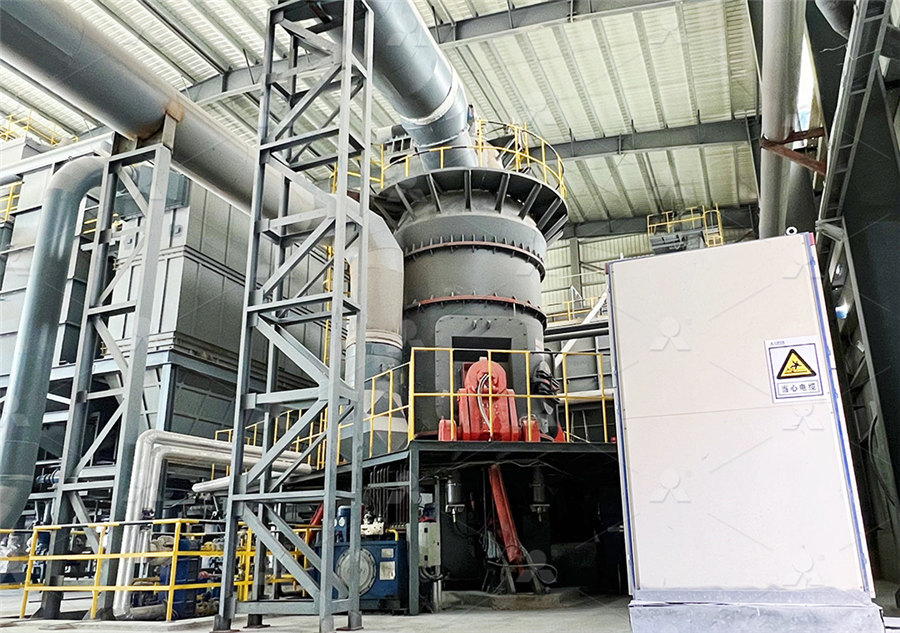
LM series vertical mill
An ordinary mill is unable to be used for production of the coal and therefore the grinding process of the vertical mill has gradually become mature Vertical Coal Mill Series; LM(Y) Premilling Vertical mill; LMX(GX) Fine powder vertical mill; Models: LM130K: LM150K: LM170K: LM190K: LM220K: LM280K: Plate diameter(mm) 1300: 1500: 1700: 1900:2023年7月27日 Jigging separation process is quite simple, its equipment has high processing capacity, it is extensively used for coarse or mediumgrained ore, and it is mostly used for coal (Fig 1), tungsten ore, tin ore, gold ore, rare metal ore (eg, tantalite, niobium ore, titaniumzirconium ore, and thorium ore), iron ore, manganese ore, and nonmetallic oreJigging Separation SpringerLink2020年8月12日 To understand the performance of a vertical roller coal mill, the real operational tests have been performed considering three different coal sources Obtained results indicate that grinding pressure, primary air (PA) temperature and mill motor current have a tendency to rise by increasing coal feeding mass flow rates for all used coalAn investigation of performance characteristics and energetic Coal pulverisers’ performance optimisation is an important process in power generation plants Pulveriser operation is costly; The objective of this dissertation was to investigate the effect of coal feedstock property variation on the vertical spindle coal pulverising mill’s performance to facilitate optimal plant performancePerformance optimisation of vertical spindle coal pulverisers
.jpg)
Coal Mill in Cement Plant Vertical Roller Mill AirSwept Ball Mill
The ball mill is a traditional coal pulverizer machine, which has been widely used since it was invented In the cement plant, the new dry process cement manufacturing requires the moisture content of coal powder to be 05% ~ 15%, while that of raw coal is 15% ~ 40%