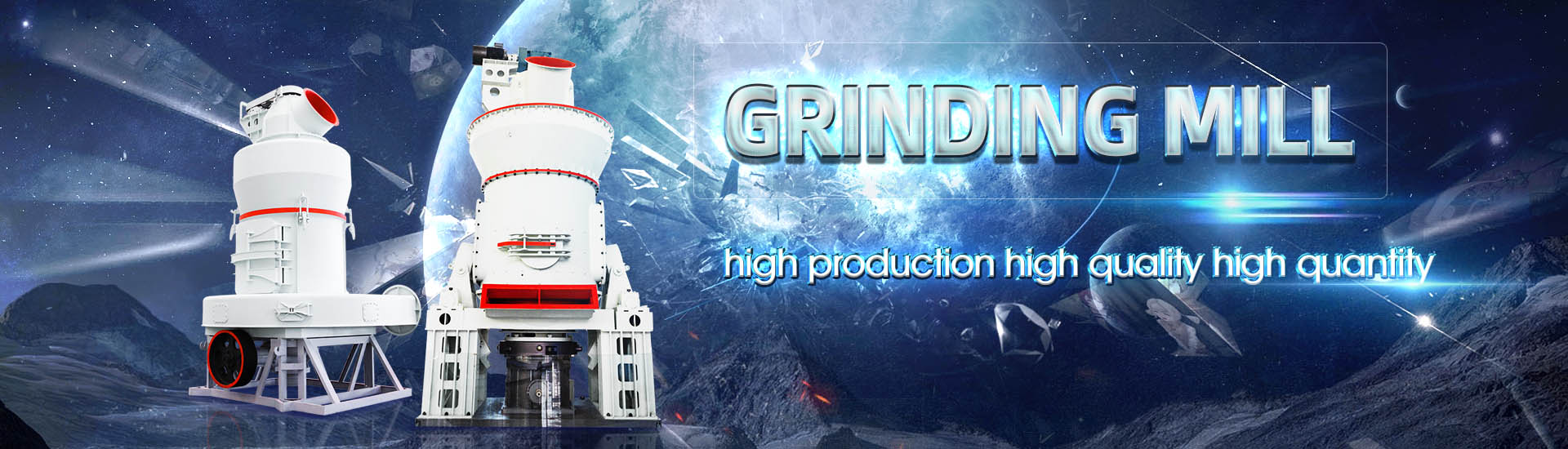
Boiler plant coal mill bidding
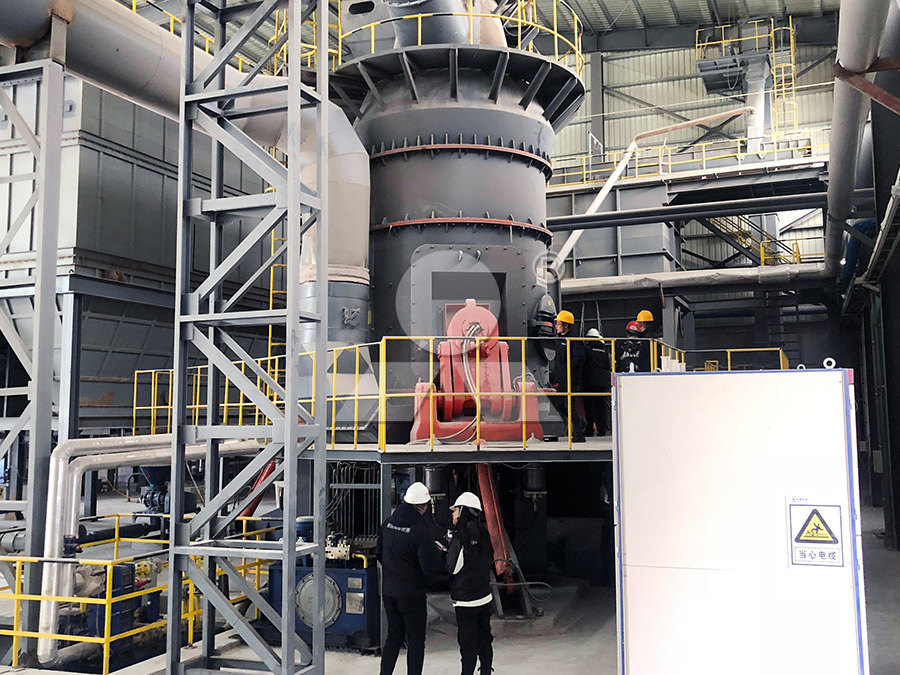
Coal mill pulverizer in thermal power plants PPT
2012年11月17日 The document discusses coal mill/pulverizers used in thermal power plants It describes how pulverized coal is dried, ground, circulated, and classified within the mill to produce a fine powder that is then transported to Abstract: Fuel and firing system purposely to deliver light fuel oil or coal as one of the primary elements of fuel in an ideal condition for combustion to take place in the boiler combustion Analysis of the Coal Milling Operations to the Boiler Parameters2020年4月2日 This present deals with the aim of estimating the heat losses occurring in thermal power plant boilers and hence finding suitable ways for reducing it, hence allowing plants to achieve moreAnalysis of the Coal Milling Operations to the Boiler Coal can be burned in a number of ways Depending on the characteristics of the coal and the particular boiler application, the designer may chose pulverized coal (PC) firing, cyclone firing, Coal Preparation Systems for Boilers SpringerLink
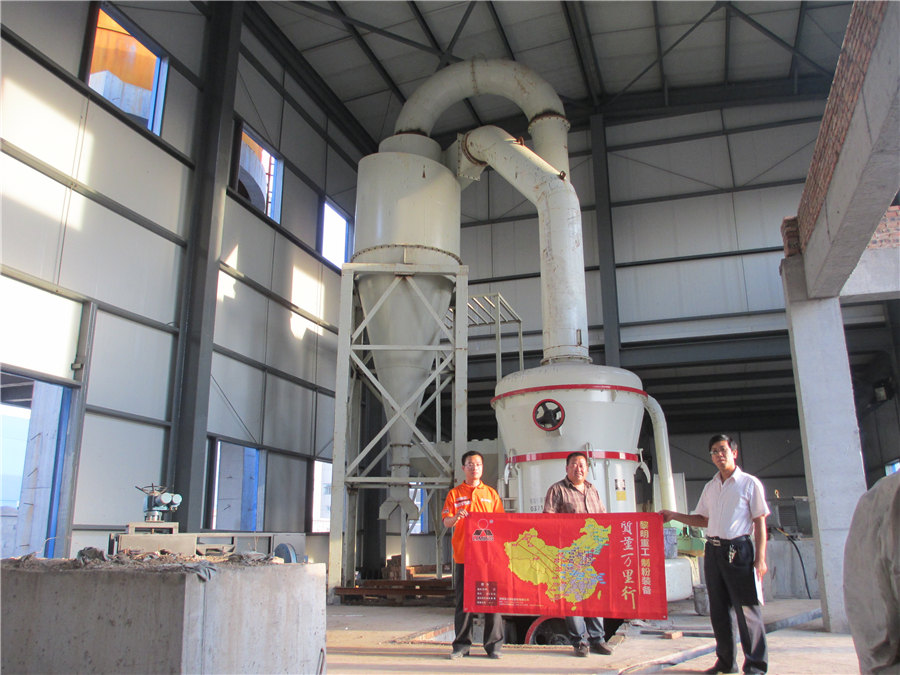
Combustion optimization of a coalfired power plant boiler using
2023年7月15日 Artificial intelligence modeling for a coal fired boiler combustion optimization Reduce NOx emissions, lower emissions compliance cost, minimize net unit heat rate Combustion optimization of a pulverized coalfired boiler is a complex process requiring indepth knowledge of combustion, operation of boiler firing system and other factors affecting Comprehensive Approach to Performance Improvement and 2021年4月30日 This recommended practice applies to 300 MW to 600 MW pulverized coalfired boilers with a balanced draft, including natural circulation and forced circulation; subcritical and 27772021 IEEE Recommended Practice for Operation of 300 • Initially Malaysia’s coal fired power stations only used Bituminous coals • Increasing cost has lead to increasing use of lower rank coals which are cheaper and readily available • Existing COAL FIRED BOILER PRINCIPALS Energy Commission
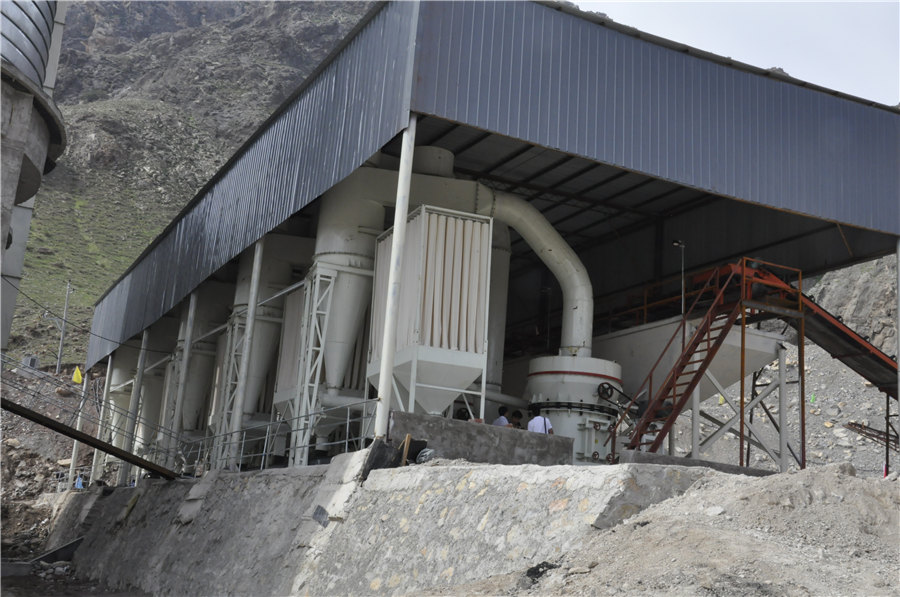
MODELLING AND COMBUSTION OPTIMIZATION OF COALFIRED
A 300 MW coalfired power plant boiler is DG1025/175II4 type subcritical param eters, tangential combustion, natural circulation drum boiler The boiler adopts a single furnace,Doosan owns core technologies and carries out ongoing development with extensive boiler portfolio that includes conventional PC, oil/gas, downshot and fluidized bed models for Boiler Doosan Enerbilityif any running Coal Mill pipe temperature goes low, below 60 C it will flash an alarm called “Any coal mill pipe temperature low” Thus we were able to execute the project and established automation for remote monitoring and measurement of Measurement and Control of Coal Pipe Temperature of Coal Mills of PF BoilerA Study on 500 MW Coal Fired Boiler Unit’s Bowl Mill Performance through Coal Sampling and Characterization: CPRI’s Experience M G Anandakumar* and M Venkateswara Rao Training Division, Central Power Research Institute, Bengaluru , Karnataka, India; mgananda@cpri ISSN (Print) : 09730338 Vol 18(2)/165170, December 2022A Study on 500 MW Coal Fired Boiler Unit’s Bowl Mill
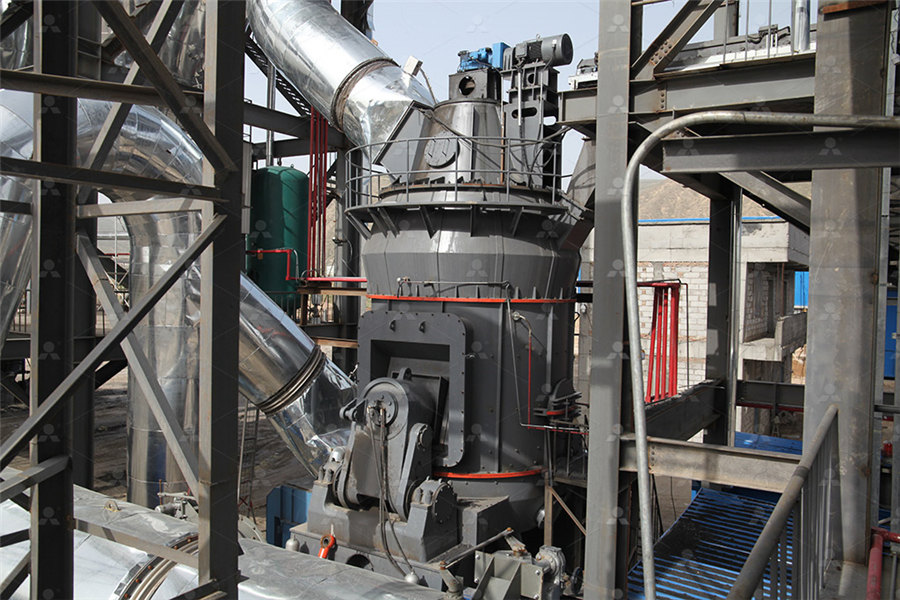
Combustion optimization of a coalfired power plant boiler using
2023年7月15日 Most electricity generation and heat supply in China come from the combustion of fossil fuel at power plants and occupy over 50 % of Chinese coal consumption annually [1]Coalfired power plants play the dominant role with their capability of stable and reliable operation, short period of construction and low investment compared with other forms of power Boiler Conventional pulverized coal (PC) boilers are used in most thermal power plants as the most common way of burning coal in different types of boiler Recent market requests higher steam conditions in order to minimize OPEX Doosan has met this needs by boilers to ultrasupercritical oncethrough boilers with ecofriendly power generationBoiler Doosan Enerbility2022年5月1日 Process model of the Coalfired Power Plant Source: (CoalFired Power Station, Diagram Stock Image C024/7686, nd) OPTIMISATION OF THE INSTALLED BOILER AND TURBINE Coal mills are largescale industrial equipment designed to pulverize coal into fine particles suitable for combustion in boilers These mills are typically used in thermal power plants to grind coal to the desired fineness, facilitating efficient combustion and maximizing the Coal Mill in Thermal Power Plant: Enhancing Efficiency and
.jpg)
Research Progress of Flexible Peak Shaving Technology for Coal
2023年9月21日 and the coal quantity in each coal mill is low, commissioning three coal mills can lead to more stable boiler combustion, reduced impact of load fl uctuations on boiler parameters, and decreased powerCoal Mill Rejects Handling System for PF Boiler Free download as Power point Presentation (ppt) System deployed at coal handling plant IND VN CN KR JP MENU MENU Home; Corporate Who We Are The Configuration of the Coal Mills of boiler units is in two rows on either side of the boiler with one stream of three mills and another stream Case Study – Coal Mill Rejects Handling System for PF BoilerCoalfired power plant Kenneth Storm, in Industrial Process Plant Construction Estimating and ManHour Analysis, 2019 811 Equipment descriptions—Coalfired boiler pressure parts sheet 1 Coalfired power plants produce electricity by burning coal in a boiler to produce steam The steam produced, under pressure, flows into a turbine, which spins a generator to create CoalFired Boiler an overview ScienceDirect TopicsPulverized coal fired boilers the total losses account to about 12 to 14 % Roughly 50% of the losses can be tuned to the optimum and the other 50 % is governed by fuel properties like hydrogen in fuel, moisture in fuel and ambient air conditions The main two losses in boiler that can be tuned by operator are carbon loss and dry gas loss There are a few minor losses in How to Run a Coal Fired Boiler at the Best Efficiency
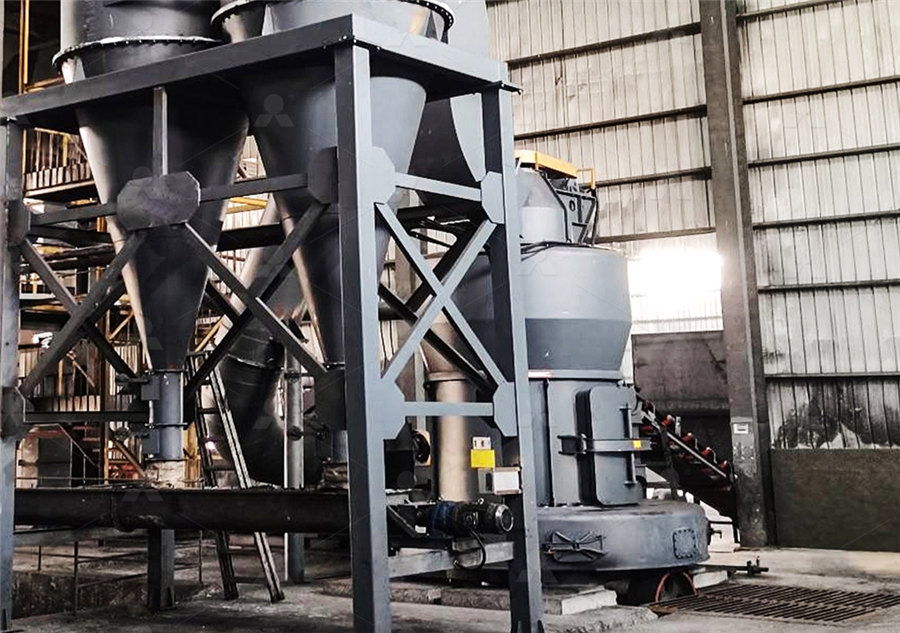
FSSS (Furnace Safeguard Supervisory System) POWER
Protection and interlock of oil /Coal System BOILER START UP SEQUENCE How Flue Gas Exit Temperature Impacts Coal Mill Performance :Newer Older: MAHARASHTRA STATE BOILER OPERATION ENGINEERING EXAM 2013 In thermal power plant each boiler uses pulverized coal as main fuel for combustion High The mill plant consists of two major sections They are 1 Bowl mills 2Design and Modify of Mill Discharge Valve Using in Thermal Power Plant Coal Feed Systems For Boiler and Coal Milling Plant Gravimetric and Volumetric Systems Belt and Chain Type Feeders Q Stock Equipment Company established in 1929 Q First Gravimetric Coal Feeder (1957) designated as ASME Historic Coal Feed Systems For Boiler and Coal Milling Plant if any running Coal Mill pipe temperature goes low, below 60 C it will flash an alarm called “Any coal mill pipe temperature low” Thus we were able to execute the project and established automation for remote monitoring and measurement of Measurement and Control of Coal Pipe Temperature of Coal Mills of PF Boiler
.jpg)
(PDF) Pulverized CoalFired Boilers: Future Directions of Scientific
2023年1月13日 The paper provides an outlook on future directions of research and the possible applications for pulverized coalfired boilers One potential direction for future research is to focus on the ways 2022年6月1日 Coal pulverizer Power Plant #boiler #mechanical coal mill Operation maintenance Question Answer for interviews #thermalpowerplantcoal pulverizer plant Coal Mill working and operation #boiler #coal 2008年7月1日 This is recognized, for instance, by IEA Bioenergy (2006), in the EC Biomass Action Plan (2005), and by a number of European Union member states and other governments, which have introduced specific policy instruments to encourage energy recovery from biomass and, in some cases, cofiring activities at both existing and future coal fired power plantsDirect injection advances biomass cofiring in large coal fired plants 2014年6月16日 14 • Once the coal is in plant it has to undergo some preparatory processes before being fed into the boiler • First the coal goes to the crusher house where the coal is crushed manually into a size of about 20mm This coal is then passed further some part of it is fed into the plant while the other is stored • Generally most of the power plants store a coal for the Coal based power plant PPT Free Download SlideShare
.jpg)
Guilin Hongcheng HMM Series Bowl Coal Mill Promoting Efficient,
2 Steps for using coal powder for boilers 1)Coal powder preparation: Select suitable coal as raw material based on the combustion requirements and coal quality characteristics of the boiler; The raw coal is crushed into small pieces by a crusher and then sent to a coal mill for grinding to prepare coal powder that meets the requirements of boiler combustion2020年8月12日 PDF This study shows the performance of a currently running vertical roller coal mill (VRM) in an existing coalfired power plant In a power plant, Find, read and cite all the research you An investigation of performance characteristics and energetic From boiler optimizations for coal power plants to services for industrial operations, GE provides extensive boiler service solutions See how we modernize boilers Multiple failures of the mill’s boiler smelt spout were Industrial and Utility Plant Boiler Services GE Vernova 2024年6月6日 What is Coal Conveyor in Thermal Power Plant The coal conveyor in thermal power plant systems is crucial for transporting coal from storage areas to the boilers, ensuring a consistent and reliable fuel Coal Conveyor in Thermal Power Plant Handing Systems
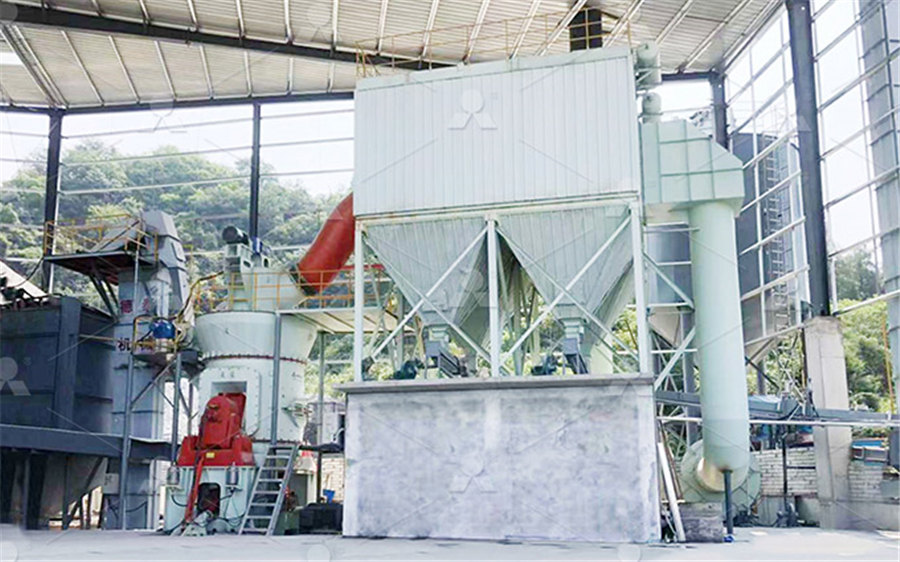
Prospects for upgrading coalfired power plants ICSC
411 Mill upgrade at Talcher power plant 23 412 Rotary classifier upgrade 24 413 Fuel switch in fan mills 26 414 Mill inerting 26 722 Modes of repowering coalfired boilers 65 723 Prospects 70 8 Conclusions 73 9 References 76 Appendix 1 84 Appendix 2 A 320 MW gross subcritical coalfired power plant is modeled using the unit model library has been developed for The two streams are then mixed and connected with the fire side of the boiler The coal stream is also fed to the fire side of the boiler While this boiler subflowsheet does not contain a specific coal mill model, Subcritical CoalFired Power Plant Flowsheet (steady state and Thermalbased power plants can produce electricity from coal or other fuel sources The coalfired process requires three different steps to turn energy released from burning coal to generating electricity for consumption Coal fired power plants, while producing power, require a lot of water and produce a lot of pollutants like ash and CO2 Learn how the process works as well as How Does a Coal Power Plant Work? Bright Hub Engineeringcovery boiler (1R), one 600 psig kraft recovery boiler (2R), one 1500 psig coalCase study: Paper mill power plant optimization—balancing steam venting with mill demand RICARDO B SANTOS and PETER W HART ABSTRACT: Most Power departments are tasked with generating steam to support mill wide operations, generCase study: Paper mill power plant optimization—balancing
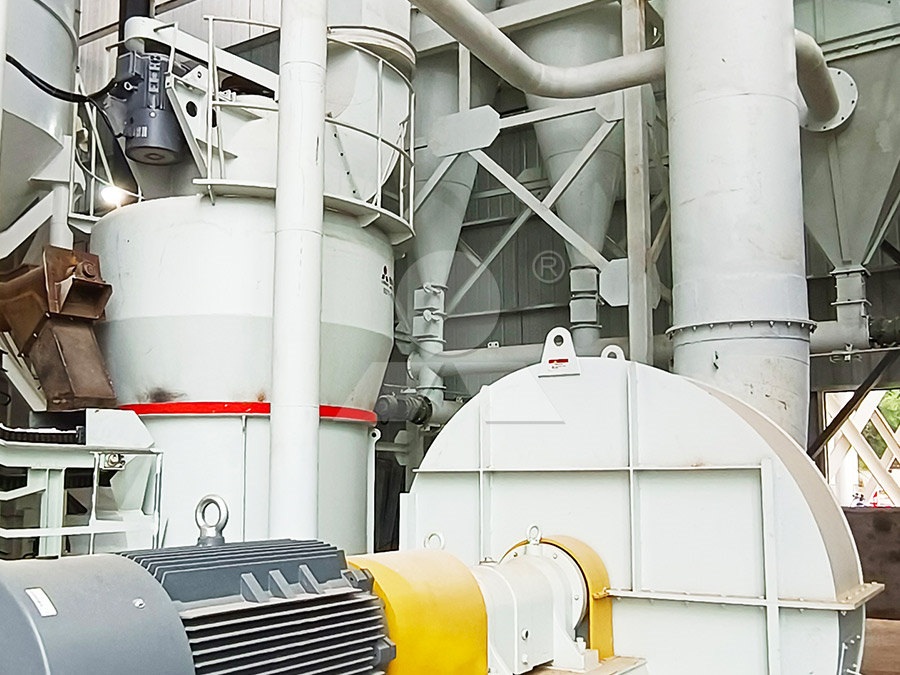
INVESTIGATION ON CLASSIFICATION EFFICIENCY FOR COALFIRED POWER PLANT
angle on the classification efficiency in CoalFired power plants The gas flow inside the coal mill was solved by the realizable k ε turbulence model (RKE) with a detailed 3D classifier geometry meanwhile the discrete phase model was used to solve the coal particles flow The steepest classifier blade angle of 40 o achievedFig3: Auto Ricemill plant 5 to 6 tons/h Study on Comparison of Boiler Efficiency Using Husk and Coal as Fuel in Rice Mill j Mill: Boiled and dried paddy is sent in mill and dehusking process Study on Comparison of Boiler Efficiency Using Husk and Coal as 2017年1月1日 Coal reserves at Mui and Taru in Kitui and Kilifi counties in Kenya are estimated to provide over 400 million tons Being new discoveries, their properties were investigated using the ASTM (PDF) Influence of coal quality to the boiler efficiency and IEA Clean Coal Centre – Optimising fuel flow in pulverised coal and biomassfired boilers 7 612 Yeongheung power plant 46 613 Chinese Control Group’s Datong power plant 48 614 TPP Niederaussem 50 62 Biomass cofiring power plants 51 621 EDF Poland – Rybnik power plant 51 622 Gelderland power plant 53 63 Summary 55Optimising fuel flow in pulverised coal and biomassfired boilers
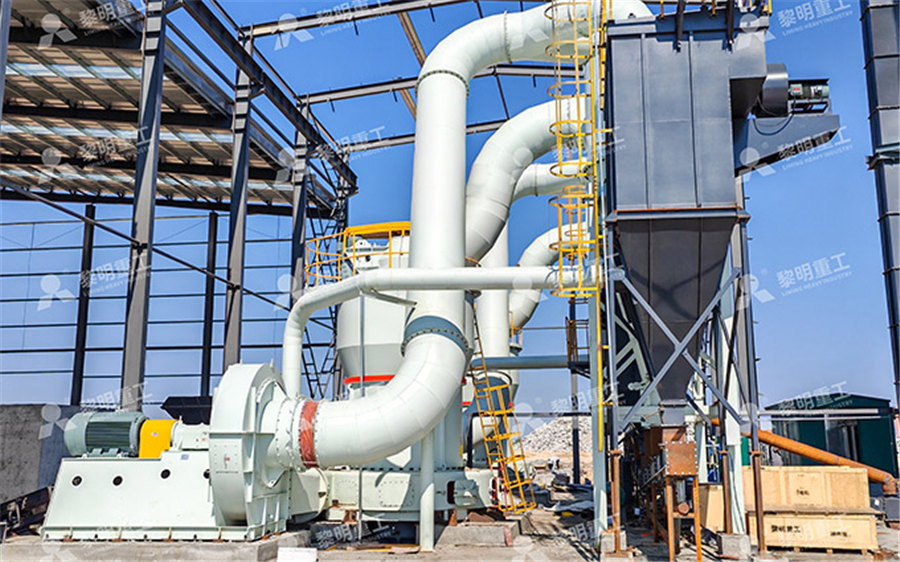
Understanding Coal Power Plant Heat Rate and
2015年2月1日 Advanced coal plant emissions controls are the norm, and PRB coal is in use to some extent at most power plants in the US, and the Environmental Protection Agency (EPA) has proposed standards 2 Characteristic of frontfired pulverized coal boiler The numerical simulation was performed for the frontfired pulverized coal boiler, with a natural circulation The nominal temperature of live and reheated steam produced in the boiler is equal to 540°C at the pressure equal to 135 MPa and 25 MPa of live and reheated steam respectivelyCoal combustion modelling pulverized coalfired boilerA well designed, operated and maintained boiler house is the heart of an efficient steam plant However, a number of obstacles can prevent this ideal The boiler house and its contents are sometimes viewed as little more than a necessary inconvenience and even in today’s energy conscious environment, accurate steam flow measurement and the correct allocation of costs Introduction to the boiler house Spirax SarcoCoal Mills are the Heart of a Coal Fired Plant Conditioning coal for proper combustion (Fineness, fuel distribution, throughput) Delivering 100% of fuel to the boiler Profoundly influencing ability to generate power economically • Rehydration is exothermic and dried coal that is stagnate anywhere in the coal mill canMill Inerting and Pulverizer/Mill Explosion Mitigation

Auxiliary Power Analysis of a Coalbased Thermal Power Plant
1834 by increasing steam pressure to145 psig [9] Presently the efficiency of a coal based power plant is of the order of 40% Process description of a coalfired power plant In a coalfired power coal is burnt to produce electricity In a coalfired plant, pulverisers are used to mill the coal to a fine powder for burning in the combustion Introduction The main Function of the Pulveriser in thermal power plant is to crush/grinding the raw coal coming from coal handling system through coal feeder into a predetermined size in order to increase the surface area of the coal If the coal is not pulverised, the coal might not burn completely, thus resulting in wastage of fuelPulveriser in Thermal Power Plant Bowl Mill Ball MillCombined operation mode of subcritical Wflame boiler and coal mill optimized numerical simulation Lun Ma *, Qingyan Fang, used in coalfired power plant boilers, such as reburning Combined operation mode of subcritical Wflame boiler and coal mill Request PDF On Aug 1, 2017, Marek Pronobis and others published Optimisation of coal fineness in pulverisedfuel boilers Find, read and cite all the research you need on ResearchGateOptimisation of coal fineness in pulverisedfuel boilers
.jpg)
Modeling and Parameter Identification of Coal Mill
2009年9月20日 PDF The coal mill used in the coalfired power plants is modeled in view of the controller design rather than the educational simulator pulverized coal to the boiler burne r Fig 1 shows a 2023年3月15日 TechnoEconomic Analysis of Cofiring for Pulverized Coal Boilers Power Plant in Indonesia The utilization of cofiring (coalbiomass study aims to investigate the technical and economic aspects of cofiring by conducting a pilot project of three PC boiler plants and capturing several preliminary figures before being TechnoEconomic Analysis of Cofiring for Pulverized Coal Boilers