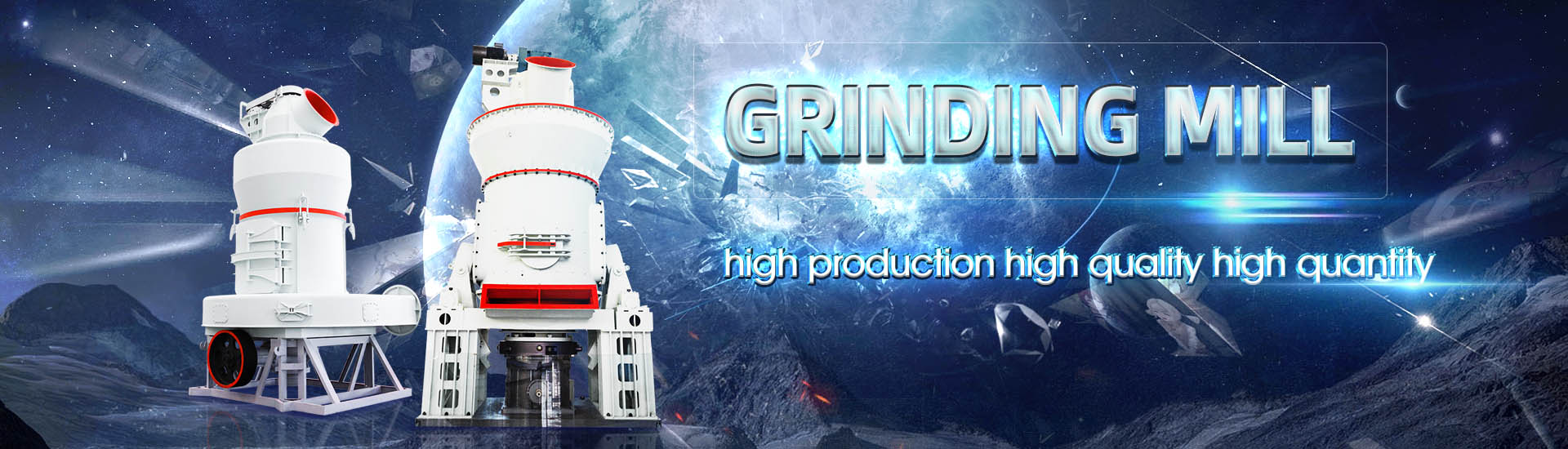
Water atomized iron oxide process
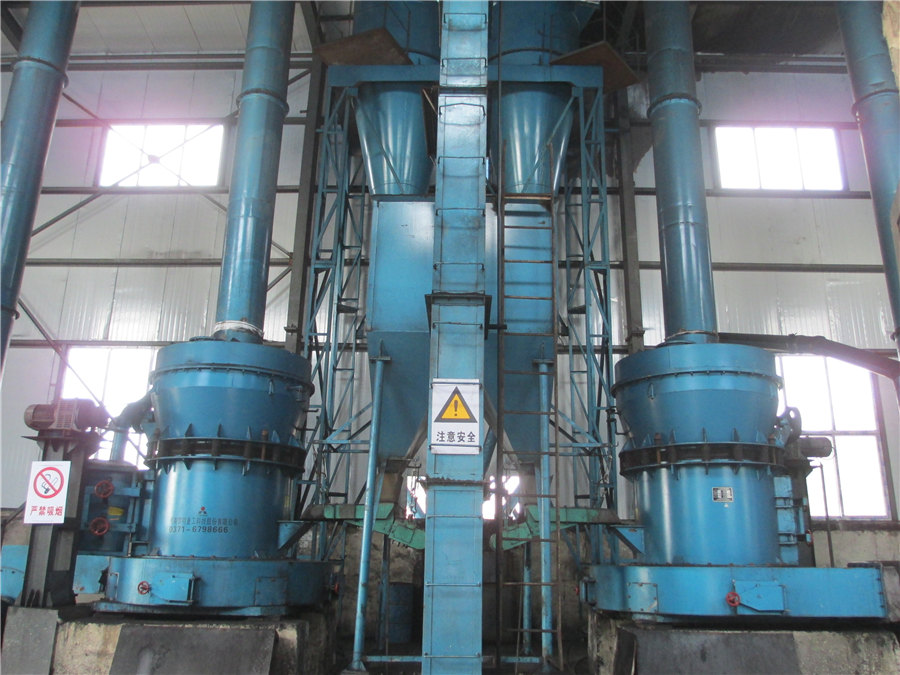
Reduction of surface oxide layers on wateratomized iron and steel
2020年10月1日 The reduction of surface oxide layers covering commercial wateratomized iron and steel powder grades have been investigated using model thermogravimetric reduction 2020年11月3日 In this study, sintering was investigated for wateratomised iron powder compacted at three different pressure levels, with and without admixed graphite Electron back Full article: Sintering behaviour of compacted wateratomised iron The powder grades are predominantly manufactured by wateratomization, yielding powder particles with highly irregular morphology and good compressibility, making the powder ideal Gothenburg, Sweden 2020 Chalmers2022年10月25日 In the study, two systems are selected: carboncoated iron nanopowder and iron nanopowder without any coating The base powder in both cases is micrometresized Carboncoated iron nanopowder as a sintering aid for water
.jpg)
Characteristics and Sintering of Fine Wateratomized and Carbonyl
The activation energy of the reduction of the surface iron oxide layer could be determined for both wateratomized and carbonyl powder, and nitrogen and carbonremoval processes could also 2020年6月25日 In this study, the surface chemistry of iron and steel powder was investigated by combined surface and thermal analysis The progressive reduction of oxides was studied using model sintering cycles in hydrogen Evolution of surface chemistry during sintering of 2020年8月1日 The reduction of surface oxide layers covering commercial wateratomized iron and steel powder grades have been investigated using model thermogravimetric reduction cycles in hydrogen The(PDF) Reduction of surface oxide layers on water 2020年6月30日 From the powder metallurgical field, it is known that wateratomized prealloyed iron powders with strong oxide forming elements like, Cr and Mn form, besides the dominant Ferich thin oxide film, minor amounts of Effect of atomization on surface oxide composition in
.jpg)
A comparative study of water and gas atomized low alloy steel
2020年12月1日 Water atomized powder had more frequent spatter ejection due to oxygen content This work reports a study of the differences between laser processing of water and 2023年1月27日 The extent to which the carbon residue from the BJAM process influences oxide reduction during sintering is not yet known Reduction of surface oxide layers on wateratomized iron and steel powder in hydrogen: Supersolidus liquid phase sintering of wateratomized behaviors of individual iron oxides including Fe2O3, Fe3O4 and FeO The wateratomized iron powder contained a significant amount of iron oxides, mainly Fe3O4 and FeO, which were formed as a partiallycontinuous surface layer and an inner inclusion During hydrogen reduction, a significant weight loss in the iron powder occurred in the initial Hydrogen Reduction Behavior of Oxide Scale in Wateratomized Iron Advances in atomisation techniques for the formation of metal powders JJ Dunkley, in Advances in Powder Metallurgy, 2013 111 Atomisation This may be defined as breaking liquid into droplets Items like fire sprinklers, crop sprayers, aerosols and so on utilise atomisation methods for cold liquids There is a very extensive literature on this surveyed in Yule and Dunkley 2 and Atomisation an overview ScienceDirect Topics
43.jpg)
Characteristics and Sintering of Fine Wateratomized and Carbonyl Iron
I Surface analysis of fine wateratomized iron powder and sintered material J Wendel, R Shvab, E Hryha, L Nyborg Accepted for publication in Surface and Interface Analysis, ECASIA 2017 special issue II Sintering behaviour of fine wateratomized iron powder – effect of initial green state J Wendel, S Manchili, E Hryha, L NyborgThe reduction of surface oxide layers covering commercial wateratomized iron and steel powder grades have been investigated using model thermogravimetric reduction cycles in hydrogen TheReduction of surface oxide layers on wateratomized iron and II Oxide reduction and oxygen removal in water atomized iron powder: a kinetic study J Wendel, S K Manchili, E Hryha, L Nyborg Journal of Thermal Analysis and Calorimetry, 2020, Vol 142, 309320 DOI: 101007/s10973020097246 III Evolution of surface chemistry during sintering of water atomized iron and lowalloyed steel powderSWATHI KIRANMAYEE MANCHILI Chalmers2016年6月5日 This process is applied to lowcost wateratomized iron powder with the goal of understanding the effects of printing parameters and sintering schedule on maximizing the green and sintered Binderjetting additive manufacturing with water atomized iron
.jpg)
Full article: Sintering behaviour of compacted wateratomised iron
2020年11月3日 Influence of surface oxide layer on sintering process of lead Powder Metall 1978;21 (open in a new window):188–194 Manchili SK, Wendel J, Zehri A, et al Effect of nanopowder addition on the sintering of wateratomized iron powder Metall Mater Trans A Phys Metall Mater Sci 2020;51 (open in a new window):4890–49012022年1月1日 No significant solid oxide shell was observed on the particle surfaces • Thermal contraction or gas entrainment alone are unlikely to lead to porosity • Carbon monoxide/dioxide are too slowmoving to form bubbles in the process • Water breakdown, leading to hydrogen gas in the drops is a likely cause of poresParticle morphology of water atomised iron‑carbon powdersOxide reduction and oxygen removal in wateratomized iron powder and compacts J Wendel, S K Manchili, E Hryha, L Nyborg Proceedings of World PM 2018 An extended version of this paper was published in Journal of Thermal Analysis and Calorimetry (see Paper II) c Analysis of iron oxide reduction kinetics in the nanometric scale using Gothenburg, Sweden 2020 Chalmers2024年3月20日 Electrochemical production of iron metal can support a decarbonized process for steelmaking Here, we report a lowtemperature, electrochemical cell that consumes lowcost and abundant iron oxide, salt, Electrochemical chloriron process for iron production
.jpg)
CHANGES IN OXIDE CHEMISTRY DURING CONSOLIDATION OF Cr/Mn WATER ATOMIZED
importance of efficient surface iron oxide layer reduction at the lowest possible temperature The reason is that if the iron oxide layer is not fully reduced at low temperatures, intensive interparticle necks development after about 900°C will lead to enclosure of residue of this iron oxide layer inside interparticle necks IndisputablyThe reduction of surface oxide layers covering commercial wateratomized iron and steel powder grades have been investigated using model thermogravimetric reduction cycles in hydrogenOverview of asreceived wateratomized iron powderoxide reduction, shown to be applicable for silver oxide [14], nickel oxide [15], iron ores and pure iron oxides [16,17] as well as for water atomized iron powder [18] In this way, the effects of powder chemistry and initial surface oxide condition on the reduction kinetics could be revealedReduction of surface oxide layers on wateratomized iron and 2020年7月1日 A promising method of improving the densification of powder metallurgical steel components is to blend nanopowder with the otherwise typically used micrometresized powder The higher surfacetovolume ratio of nanopowder is hypothesized to accelerate the sintering process and increase the interparticle contact area between the powder particles This is Effect of Nanopowder Addition on the Sintering of WaterAtomized Iron
.jpg)
Characterization of Surface Oxides on WaterAtomized
2013年3月1日 Water atomized steel powder particles are covered by heterogeneous surface oxide, formed by thin (~ 6 to 8 nm) iron oxide layer covering most of the powder surface, and particulate features formed 2022年1月1日 Water atomisation can produce metal powders faster and at lower cost than gas atomisation, but it is well known that the powder particles are irregular and may contain a large number of poresThe current study analyses three iron‑carbon alloys with different superheats, produced as powder by water atomisation and compares the particle shapes and porosity in Particle morphology of water atomised iron‑carbon powdersthe most produced and consumed of the global powder metallurgy market Iron powder is [3] produced mainly by reduction of iron oxide (providing so called sponge iron) and by means of water atomization Water atomized and sponge iron powder are most commonly used hence powder for structural PM componentsRole of nanopowder as sintering aid in the densification of water The laser powder bed fusion (LPBF) technology was adapted for use with nonspherical lowcost wateratomized iron powders A simplified numerical and experimental modeling approach was applied to determine—in a first approximation—the operation window for the selected powder in terms of laser power, scanning speed, hatching space, and layer thickness The operation Laser Powder Bed Fusion of WaterAtomized IronBased Powders: Process
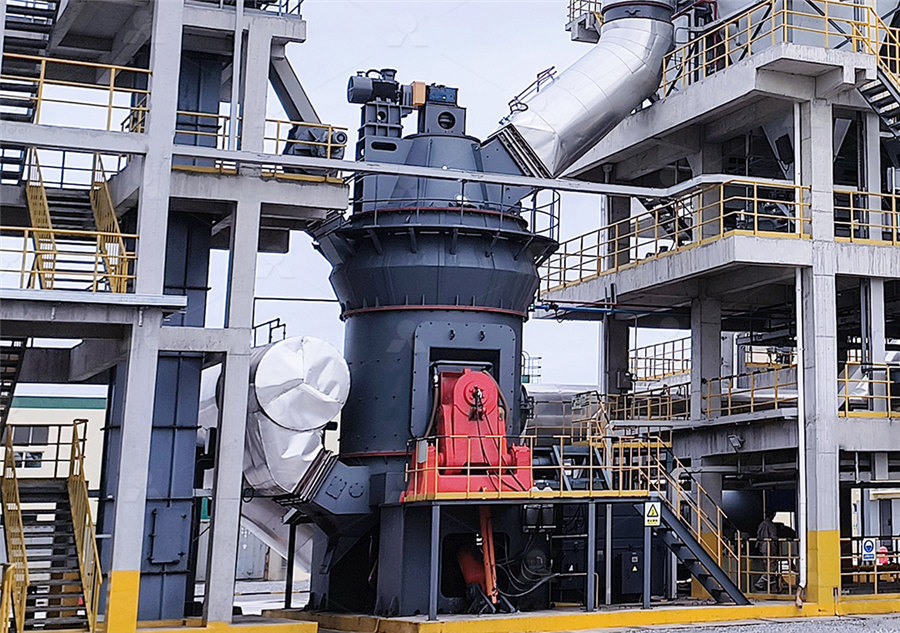
Particle morphology of water atomised ironcarbon powders
The production of metal powders by water atomization is a wellestablished process, which can be used to produce a wide range of particle sizes for different applications In general, there is a lack of detailed knowledge about what process parameters that affect the powder properties for water atomized metal powdersWhile the surface oxide of iron nanopowder follows a single step reduction process, the actual reduction process of Fe2O3 undergoes a twostep process to form metallic iron To study sintering, compacts from micro/nano bimodal powder mixtures were prepared to understand the influence of nanopowder addition on densification behaviourNanopowder as sintering aid for wateratomized ferrous powder2020年12月1日 Oxide films concentrated on the particle surface might also decrease the degree of wetting with previous powder layers and the substrate, which can lead to defect formation Laser directed energy deposition of wateratomized iron powder : process optimization and microstructure of singletracks Opt Laser Technol, 112 (2019), A comparative study of water and gas atomized low alloy steel 2020年6月30日 Iron nanopowder could be used as a sintering aid to wateratomised steel powder to improve the sintered density of metallurgical (PM) compacts For the sintering process to be efficient, the inevitable surface Analysis of Iron Oxide Reduction Kinetics in the
.jpg)
Synthesis, Properties, and Applications of Iron Oxides: Versatility
2021年5月18日 21 Iron (III) Oxides Iron (III) oxide is, of course, a compound that exhibits four different crystalline polymorphs: αFe 2 O 3, βFe 2 O 3, γFe 2 O 3, and εFe 2 O 3Hematite and maghemite usually appear in nature, while beta and epsilon structures are generally synthetic oxides [10, 11]In general, the iron (III) oxides anions arrange in closepacked structures, important to reduce the oxidizing effects that occur during the water atomization process[3] These two limiting factors influence which type and volume of raw materials are allowed to be used for producing water atomized powder Figure 1 Schematic of the water atomization process[1]Economic Additive Manufacturing using Water Atomized Stainless 2023年2月1日 [8] J Wendel, SK Manchili, E Hryha, L Nyborg, Reduction of surface oxide layers on wateratomized iron and steel powder in hydrogen: effect of alloying elements and initial powder state Supersolidus liquid phase sintering of wateratomized lowalloy 2022年10月25日 The reduction of surface oxide layers covering commercial wateratomized iron and steel powder grades have been investigated using model thermogravimetric reduction cycles in hydrogenCarboncoated iron nanopowder as a sintering aid for wateratomized
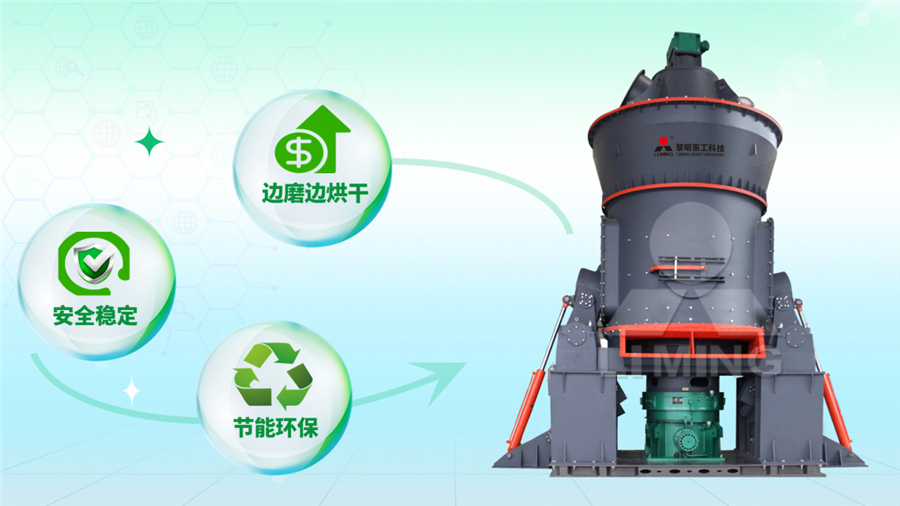
Characterization of oxide on the wateratomized FeMn powder
2014年3月15日 The low compressibility of the unreduced wateratomized Fe031Mn powder may due to the high oxygen content and the quenching effect of water atomization Hard phase of iron and manganese oxides formed in the process of water atomization lead to high hardness and poor pressing performance of the unreduced powder [34], [35]Download scientific diagram Relative density and densification parameter of wateratomized iron powder (ASC 300) compacts with varying amounts of nanopowder from publication: Sintering of Relative density and densification parameter of wateratomized iron 2020年6月1日 known that wateratomized prealloyed iron powders with strong oxide forming elements like, Cr and Mn form, besides the dominant Ferich thin oxide film, minor amounts of oxide particles(PDF) Effect of atomization on surface oxide 2020年6月30日 From the powder metallurgical field, it is known that wateratomized prealloyed iron powders with strong oxide forming elements like, Cr and Mn form, besides the dominant Ferich thin oxide film, minor amounts of Effect of atomization on surface oxide composition
.jpg)
the water atomizing process 2 Total Materia
The wateratomizing process, as practiced there, can be followed on the flowsheet shown in Figure 2, and is described in detail on the next page Figure 2: Flowsheet for the Höganäs WaterAtomizing Process The raw material for 2020年6月25日 Wateratomized iron and steel powder is commonly used as the base material for powder metallurgy (PM) of ferrous components The powder surface chemistry is characterized by a thin surface oxide layer and more thermodynamically stable oxide particulates whose extent, distribution, and composition change during the sintering cycle due to a Evolution of surface chemistry during sintering of wateratomized iron 2022年10月25日 In the present case, a thin iron oxide layer is sandwiched between the carbon coating and the iron core of the CC NPs, as shown by the XPS and HRTEM analyses During the heating cycle, the iron oxide is expected to be reduced for the sintering of the nanopowder to proceed in the lower temperature regime for the nanopowderCarboncoated iron nanopowder as a sintering aid for wateratomized 2023年3月1日 Reduction of surface oxide layers on wateratomized iron and steel powder in hydrogen: effect of alloying elements and initial powder state Thermochim Acta , 692 ( 2020 ) , Article , 101016/jtca2020Supersolidus liquid phase sintering of wateratomized lowalloy
.jpg)
Oxide reduction and oxygen removal in wateratomized iron
Oxide reduction and oxygen removal in wateratomized iron powder: a kinetic study 1 3 closertoequilibrium,especiallyifthereactionshavevastly2013年3月1日 Semantic Scholar extracted view of "Characterization of surface oxides on wateratomized steel powder by XPS/AES depth profiling and nanoscale lateral surface analysis Reduction of surface oxide layers on wateratomized iron and steel powder in process Four widely used steels (316L, H13, P20 and 18Ni300) have been Characterization of surface oxides on wateratomized steel The iron nanopowder is covered by a 3–4 nm thick iron oxide layer, while the carbon‑coated iron nanopowder is encapsulated with several nanometric carbon layers Thermogravimetry conducted inCarboncoated iron nanopowder as a sintering aid for wateratomized 2020年6月30日 The reaction kinetics for the reduction of surface oxide of iron nanopowder in hydrogen was investigated using nonisothermal thermogravimetric (TG) measurements and a model was proposed to understand the reduction Iron nanopowder could be used as a sintering aid to wateratomised steel powder to improve the sintered density of metallurgical (PM) Analysis of Iron Oxide Reduction Kinetics in the Nanometric Scale