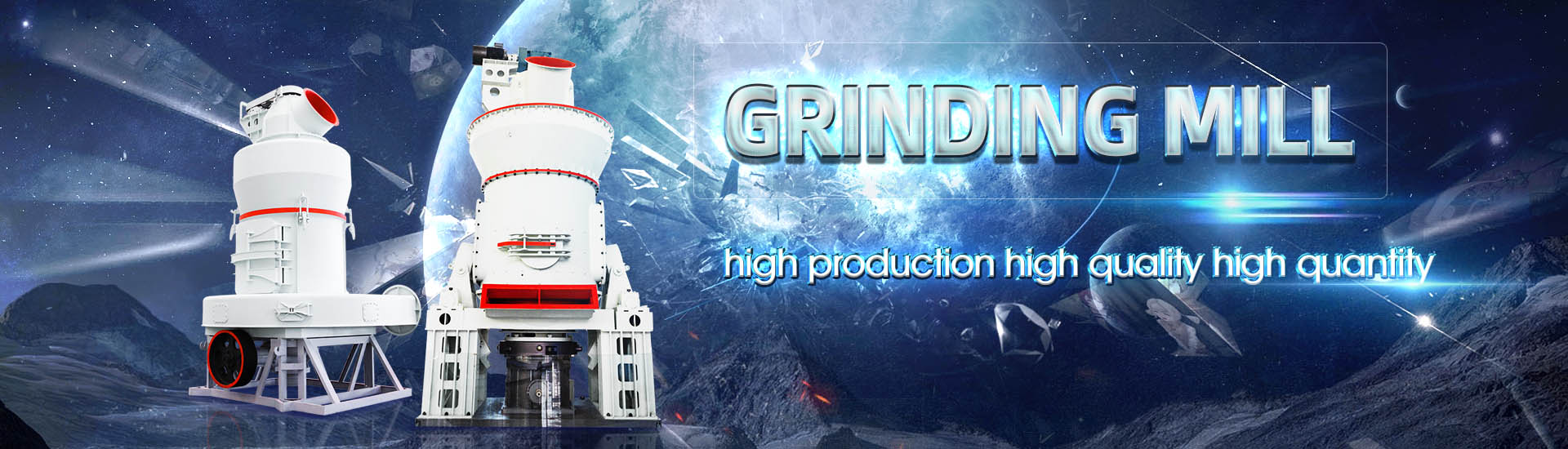
Electrical Energy Efficiency of Vertical Mills for Raw Materials in Cement Production
.jpg)
IMPROVING THERMAL AND ELECTRIC ENERGY EFFICIENCY AT
Improving Thermal and Electric Energy Efficiency at Cement Plants: International Best Practice v This report was produced in cooperation between IFC, SNIC (Sindicato Nacional da Indústria do Cimento), ABCP (Associação Brasileira de Cimento Portland), and INT (Brazil’s National 2022年5月9日 By initiating a CL for an industrial cement vertical roller mill (VRM), this study conducted a novel strategy to explore relationships between VRM monitored operational Modeling of energy consumption factors for an industrial cement 2016年10月5日 1 Introduction Cement is an energyintensive industry in which the grinding circuits use more than 60 % of the total electrical energy consumed and account for most of the manufacturing cost []The requirements for the EnergyEfficient Technologies in Cement GrindingGrinding raw materials needs lots of energy Tube mills had been used for grinding, but the energy efficiency level was lower Therefore, the introduction of highly efficient grinding equipment was anticipated Descriptions The vertical roller mill has high energy efficiency and the installation space is smaller compared with tube millsVertical roller mill for raw Application p rocess materials
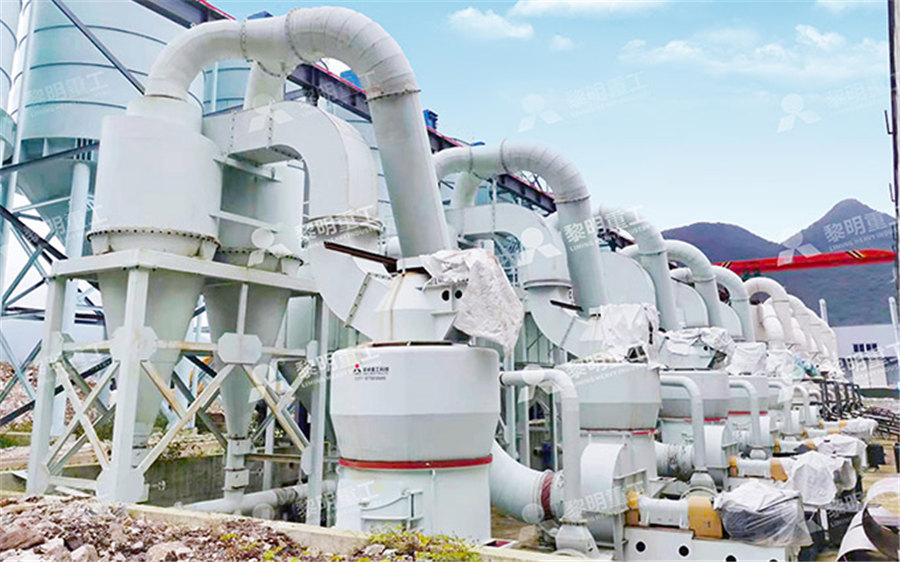
An overview of energy savings measures for cement industries
2013年3月1日 Energy efficiency measures for raw materials preparation, clinker production, products and feedstock changes, general energy efficiency measures, and finish grinding have been surveyed It was found that the largest recorded amounts of thermal energy savings, electrical energy savings and emission reductions to date are 34 GJ/t, 35 kW h/t and 21254 Table 2 Energy Efficiency Measures for Raw Materials Preparation in Cement Plants More information can be found in the description of the measures below Energy Efficiency Measure (for raw materials production) (1) Fuel Savings (GJ/t) Electricity Savings (kWh/t) Estimated Payback Period (years) CO 2 Savings (kgC/t)Energy Efficiency Improvement Opportunities for the Cement Improving Thermal and Electric Energy Efficiency at Cement Plants: International Best Practice iii LIST OF FIGURES Figure 1: Cement Production Process Flow Schematic and Typical Energy Efficiency Measures 2 Figure 2: Rotary Cement Kiln (Dry Process with Cyclonic Preheaters) 4 Figure 3: Schematic Depiction of Control Points and Parameters in a Kiln System Control IMPROVING THERMAL AND ELECTRIC ENERGY EFFICIENCY AT CEMENT 2020年9月29日 Raw materials chemistry Cement manufacture requires a source of calcium, such as CaCO 3 or CaMg (CO 3) 2, which comprises almost 80–90% of the total and the rest is iron oxide (Fe 2 O 3, Fe 3 O 4), quartz (SiO 2), and clay/bauxite (Alsilicates) (Aïtcin and Flatt Citation 2015; Hewlett Citation 2003; Peray and Waddell Citation 1986)Traces of Na 2 O, K 2 An overview of alternative raw materials used in cement and
.jpg)
SALSTMs: A new advance prediction method of energy consumption
2022年2月15日 According to statistics, the electrical energy consumed in the cement raw materials grinding accounts for about 26% of the total electrical energy consumption in cement enterprises [9] To reduce energy cost and sustain the competitive advantages, it is important to adopt the better production scheme to improve the efficiency of energy in the cement cement industry reveals prospects to integrate vertical roller mills for cement grinding and use Organic Rankine Cycle (ORC) at the clinkerisation stage Adopting these techniques could reduce the electrical energy intensity of clinkerisation by 51% and cement grinding electrical intensity by 30%, surpassing benchmarks While limited toBenchmarking of Energy Consumption and CO2 Emissions in Cement 2021年1月1日 India is the world's second largest producer of cement and produces more than 8 per cent of global capacity Due to the rapidly growing demand in various sectors such as defense, housing, commercial and industrial construction, government initiative such as smart cities PMAY, cement production in India is expected to touch 550–600 million tones per Review on vertical roller mill in cement industry its 2012年6月1日 Cement production in the world is currently about 16 billion ton per year About 2% of the electricity produced in the whole world is used during the grinding process of raw materials [1] While total electrical energy consumption for cement production is about 100 kWh/ton of cement, roughly two thirds are used for particle size reduction [2]Reducing energy consumption of a raw mill in cement industry
.jpg)
POWERING THE CEMENT INDUSTRY CEMBUREAU
example, results in an increase in electrical energy demand of 5 kWh/t clinker Other ways of improving energy efficiency Still, there is a potential to improve cement technology in order to further increase energy efficiency Besides the efficiency of the installed equipment, the flexibility of production is of increasing interestBackground: Energy Challenges in Cement Production Cement production is a multifaceted process that encompasses several stages, each with its own set of energy demands and challenges The process begins with the extraction of raw materials, followed by grinding, heating in kilns, and finally, finishing operations These stages are not onlyOptimization of Energy Consumption in ElectricPowered Modular Cement 2015年12月1日 Comminution and especially cement grinding still account for the majority of the electrical energy demand of cement production As Fig 12 shows, between 60% and depending on cement properties up to 70% of the roughly 100–110 kWh of electrical energy per ton of cement are used for comminution processes [5] , [45] Process technology for efficient and sustainable cement production80 mm e raw materials were mixed in a certain proportion and fed into a vertical roller mill (LOESCHE mill) e raw vertical roller mill has four rollers, 3000 KW main drive, 48 m table diameter Modeling of energy consumption factors for an industrial cement
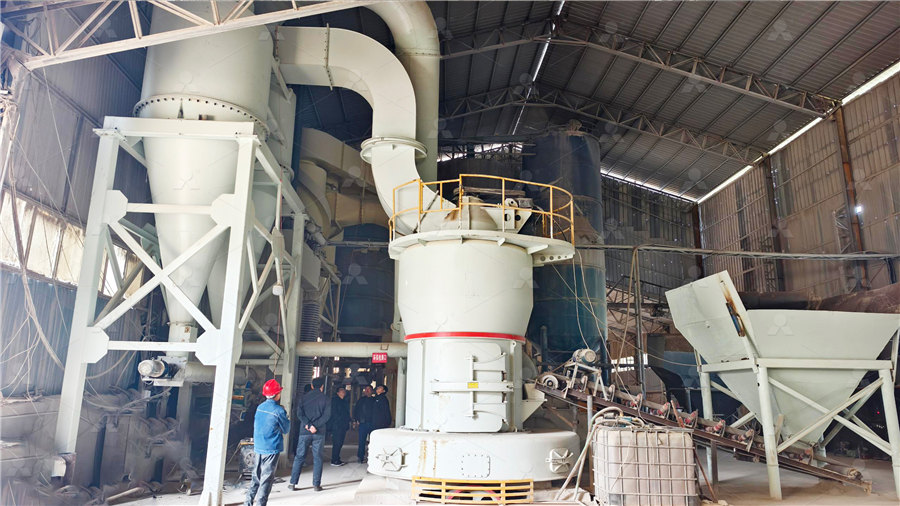
Reducing energy consumption of a raw mill in cement industry
2012年6月1日 Cement production in the world is currently about 16 billion ton per year About 2% of the electricity produced in the whole world is used during the grinding process of raw materials [1]While total electrical energy consumption for cement production is about 100 kWh/ton of cement, roughly two thirds are used for particle size reduction [2]2021年2月1日 World cement production is about 42 billion tons in 2019 and cement plants consume about 2 percent of world electrical [15] In RMG, it takes about 30–40 min for the raw materials to enter the vertical mill (VM) and be fully Electricity consumption is a major energy efficiency indicator in cement raw materials grinding A case study on energy and exergy analyses for an industrialscale 2020年3月1日 Manufacturing cement requires energy intensive processes; and consumes almost 15% of the total demand for energy in industry [3]On average, to produce one ton of cement, 34 GJ of thermal energy (in dry process) and 110 kWh of electrical energy are needed [4, 5]Furthermore, manufacturing a ton of cement releases 073–099 tons of CO2 [6] which A decision support tool for cement industry to select energy efficiency 2021年7月5日 1 Introduction Cement manufacturers face economic and environmental challenges due to their highenergy consumption Periodic data collection on industry and other energyconsuming industries is crucial to setting objectives for energysaving studies (Madlool, Saidur et al, Citation 2013)Atmaca and Yumrutaş (Citation 2014) suggested that an Evaluation of optimization techniques for predicting exergy efficiency
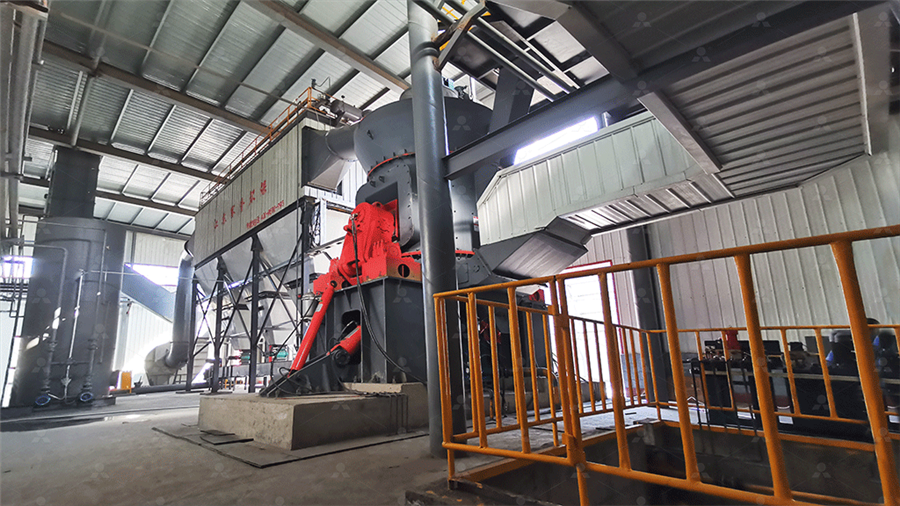
POWERING THE CEMENT INDUSTRY CEMBUREAU
example, results in an increase in electrical energy demand of 5 kWh/t clinker Other ways of improving energy efficiency Still, there is a potential to improve cement technology in order to further increase energy efficiency Besides the efficiency of the installed equipment, the flexibility of production is of increasing interest2018年7月1日 In that case, the real data showed that the increase in production rate was 368% and 28Days strength of the cement improved by 29% As a result, the simulation outputs were found to be in agreement with the real data hence the efficiency of the cement production, both quality and energy, for a given circuit was improvedEnergy and cement quality optimization of a cement grinding circuit2022年5月9日 Cement production is one of the most energyintensive manufacturing industries, and the milling circuit of cement plants consumes around 4% of a year's global electrical energy production It is well understood that modeling and digitalizing industrialscale processes would help control production circuits better, improve efficiency, enhance personal training systems, Modeling of energy consumption factors for an industrial cement 2011年5月1日 The energy used for the actual grinding process depends mainly on the hardness of raw materials and the type of mill used (ie ball mill or vertical roller mill) Typically, an electrical motor of the ball mill uses about 14–15 kWh/tonne of raw mixA critical review on energy use and savings in the cement industries
.jpg)
Uses of alternative fuels and raw materials in the cement industry
2013年7月1日 In this sense, the cement industry has a high potential to manage all of these tendencies as an integrated system to save energy, reduce GHG emissions, and recover waste materials [19], [20]To this end, the cement sector is presently focused on the diversification of energy sources, especially those used for waste treatment, and many factories can potentially 2011年7月1日 At the same time, the cement industry is facing challenges such as cost increases in energy supply, requirements to reduce CO 2 emissions, and the supply of raw materials in sufficient qualities and amounts The World Business Council for Sustainable Development and its Cement Sustainability Initiative, comprising cement producers worldwide, has initiated the Sustainable cement production—present and future2022年12月1日 Electricity can be saved if raw materials and coal are ground in advanced roller mills like horizontal, highpressure, and highefficiency roller mills If a vertical/horizontal roller replaces a traditional ball mill, the energy saving is estimated to be 6–7 kWh/ton of raw materials ( Madlool et al, 2012 )Review on energy conservation and emission reduction 2021年11月10日 Cement factories require large amounts of energy 70% of the variable cost goes to energy—33% to kiln thermal energy and 37% to electrical energy This paper represents the second stage of a broader research study which aims at optimising electricity cost in a cement factory by means of using artificial intelligence After an analysis of the different tools that Methodological development for the optimisation of electricity
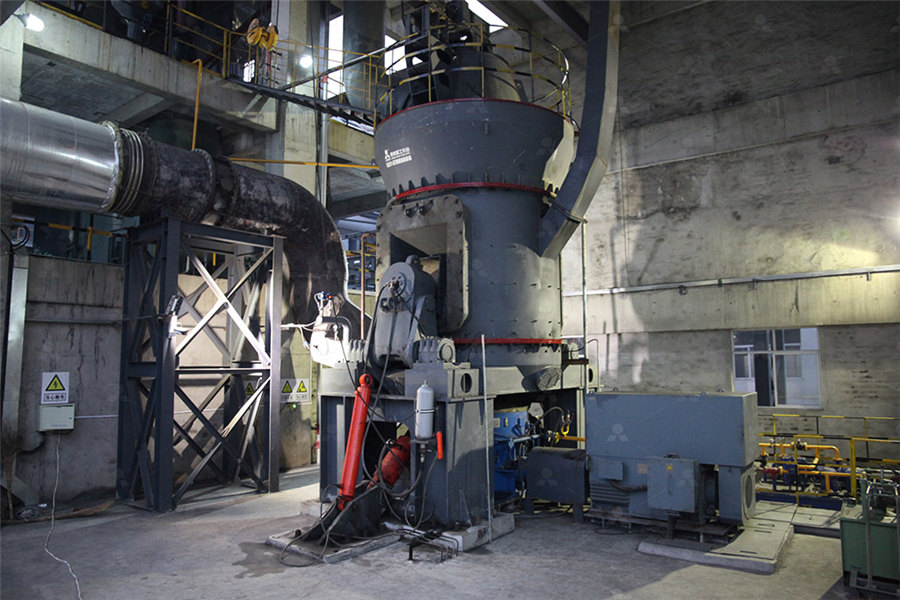
Investigating energy saving and climate mitigation potentials in cement
2023年7月1日 Cement is one of the most consumed construction materials in the world [1]The total cement production in 2020 was estimated at 41 Billion tonnes (Bt), of which China produced 22 Bt of cement, accounting for more than half of the global production; followed by India and Vietnam with the production of 340 and 96 Million tonnes (Mt) in the same year, respectively [2]CEMENT 4 SikaGrind® FOR VERTICAL ROLLER MILLS Pilot Mill (Picture: Loesche GmbH, Germany) The production of Portland Cement (OPC, CEM I) with Vertical Roller Mills can demand the following benefits from a Grinding Aid: ́ Increased production rate, energy saving ́ Higher fineness, faster strength development ́ Reduced vibration, less wearSikaGrind® for vertical roller mills2023年11月10日 Cement industry releases a large number of harmful gases into the atmosphere This industry provides around 13% and 8% of the world's total greenhouse gas emissions and anthropogenic carbon dioxide to the environment, respectively (Olivier et al, 2012; Fischedick et al, 2014)It has been estimated that one ton of clinker production releases 09–1 Design of solar cement plant for supplying thermal energy in cement The cost of energy as part of the total production costs in the cement industry is significant, typically at 20 to 40% of operational costs, warranting attention for energy efficiency to improve the bottom lineEnergy Efficiency Improvement and Cost Saving Opportunities for Cement
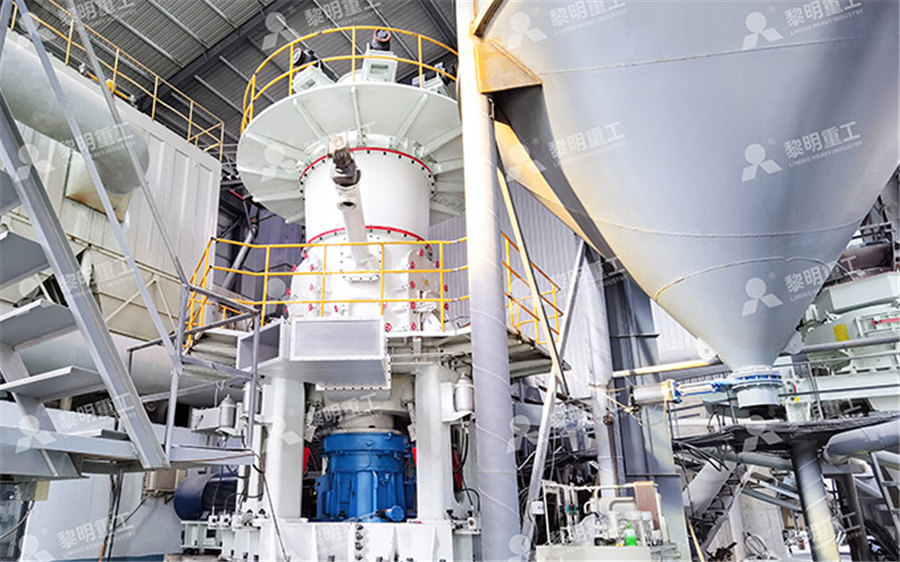
A case study on energy and exergy analyses for an industrialscale
2021年2月1日 World cement production is about 42 billion tons in 2019 and cement plants consume about 2 percent of world electrical energy in the grinding process [1], [2]The total electrical energy that is consumed in cement companies is about 100 kWh per 1000 kg of cement, and twothird of this amount just consumes in raw material and cement mill units [3]2017年10月20日 From the depository the raw materials are transferred to the vertical roller mill with a capacity of 170 t/h and appropriate raw Heat transfer in cement production with raw mill considering the minimum temperature Heat Integration in a Cement Production IntechOpen2006年12月1日 In order to produce raw materials preparation, clinker and rotary kilns are widely used in cement plants The objective of this study is to perform energy and exergy analysis of a raw mill (RM) and raw materials preparation unit in a cement plant in Turkey using the actual operational data The RM has a capacity of 829 tonmaterial hourlyEnergy and exergy analyses of a raw mill in a cement production2017年4月1日 Cement production is an energy intensive process in terms of electrical kiln system design and production capacity and the moisture content of the raw materials Most cement industries have not been able to generate power from waste heat recovery due to the before directing to the vertical raw mill and coal mill for drying The generation of power from a cement kiln waste gases: a case
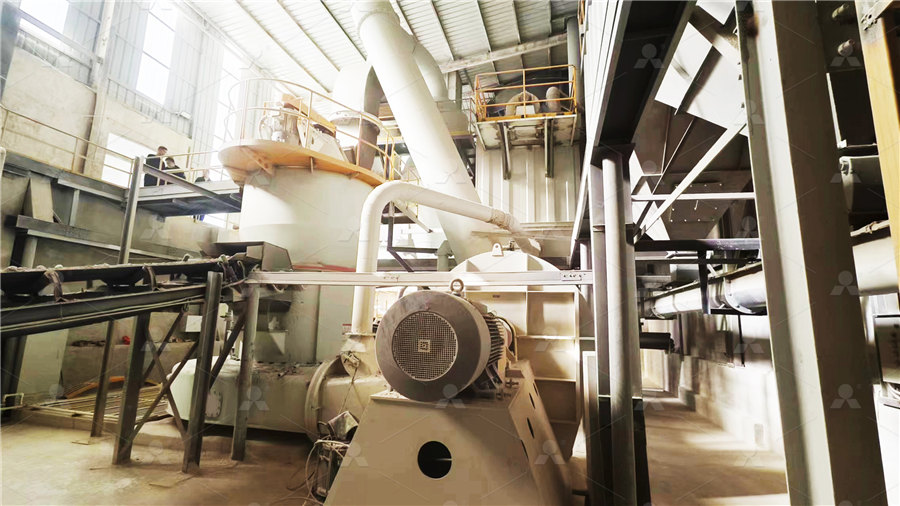
Waste materials coprocessing in cement industry: Ecological efficiency
2013年3月1日 The Portland cement production begins with the raw material extraction, where the limestone Specific consumption of electrical energy: 80–150 kWh/ton cement, 70% into milling systems Evaluating the effects of heavy metals in the waste coprocessor when used as alternative fuels and raw materials in cement industry MSc 2022年9月16日 Carbon Steel vs Stainless Steelmaking Processes Steel production via electric arc furnaces (EAFs) is a very energyintensive process that accounts for almost 25 pct of the total crude steel production worldwide [] Although the technology has a history of over 100 years, a full understanding of the process has not yet been accomplished, and industrial operations still Modeling and Energy Efficiency Analysis of the Steelmaking 2020年3月6日 The GRMK vertical cement mill of CHAENG adopts a new generation of cement grinding technology, which integrates grinding, drying and powder selecting functions It can save 30% of power per ton The important role of vertical roller mills in the cement industry2020年9月9日 In the analyzed cement industry, hydraulic binders are produced through a dry process: the raw materials are converted into a finely ground powder through the action of mills; then, the obtained raw meal is treated with a baking procedure in a rotary kiln (internal temperature reaches about 1600 [℃]), giving rise to clinkerOptimization of the Clinker Production Phase in a Cement
.jpg)
Review of Innovative Energy Savings Technology for the Electric
2014年8月20日 A review of the energy innovations for the electric arc furnace (EAF) steelmaking route is discussed Preheating of scrap using vertical and horizontal shafts that have been commercially successful in lowering the energy consumption to as much as 90 kWh/t reaching almost the operational limit to heating input scrap materials into the EAF is discussed Bucket 2024年11月23日 Cement Extraction, Processing, Manufacturing: Raw materials employed in the manufacture of cement are extracted by quarrying in the case of hard rocks such as limestones, slates, and some shales, with the aid of blasting when necessary Some deposits are mined by underground methods Softer rocks such as chalk and clay can be dug directly by Cement Extraction, Processing, Manufacturing Britannica