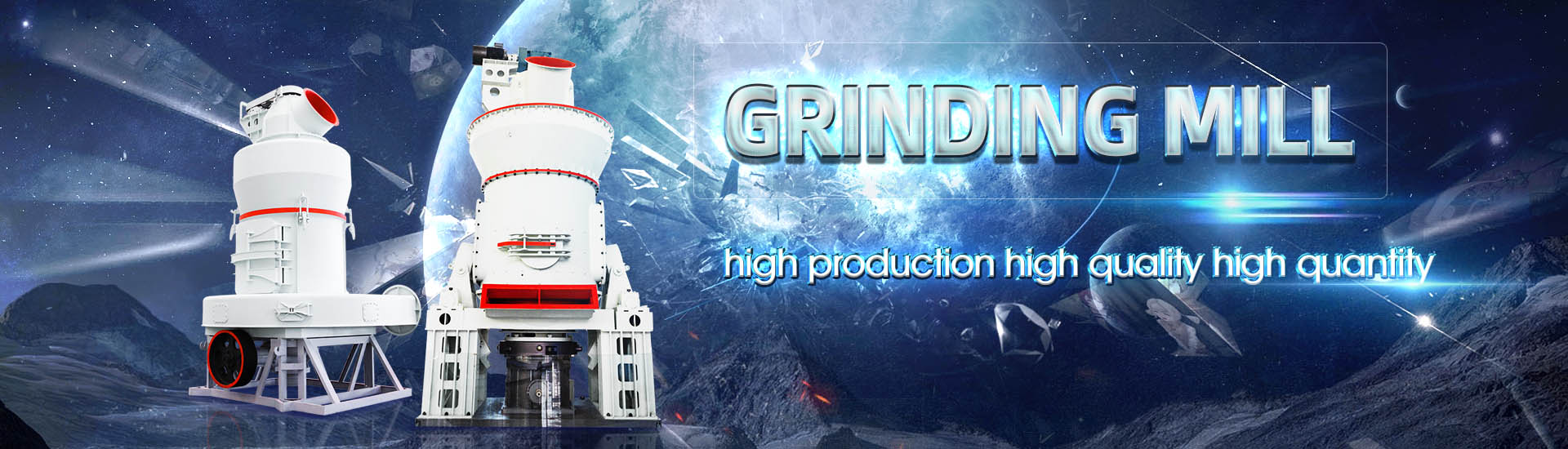
Grading toothed stick ore mill
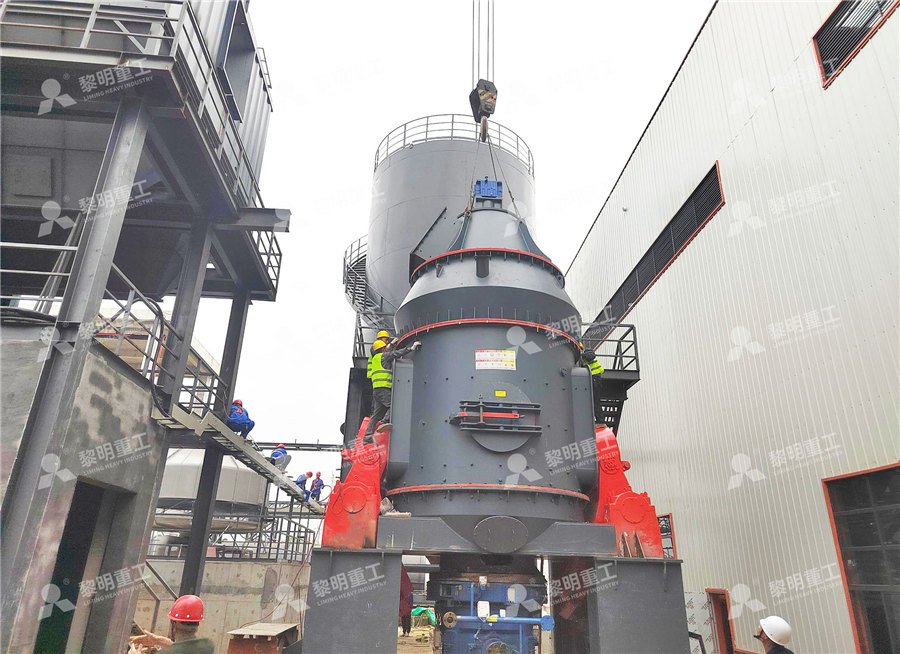
Grade Control with Mineralogy Bruker
Grade control or millfeed optimization aims to deliver ores of consistent grade, hardness and gangue mineralogy to the mineral processing line Workflows commonly rely on bulk chemistry of samples taken at the mine bench or other conducting ore grade reconciliation in a typical mine The variety of techniques to reconciliation Ore Grade Reconciliation Techniques – A Review Mining Geology 2023年10月27日 Grinding media play an important role in the comminution of mineral ores in A Review of the Grinding Media in Ball Mills for Mineral Processing 2023年7月20日 Ore grinding is a process to further reduce and disperse the ore particle size Ore Grinding SpringerLink
.jpg)
ISAMILL FINE GRINDING TECHNOLOGY AND ITS INDUSTRIAL
The current lead/zinc deposits at Mount Isa Mines (George Fisher, Hilton and Isa) have an 2016年6月2日 Before the event of ore dressing, crude ores were shipped directly to the smelters, or the refineries, with the shipper paying the freight and treatment 911 Metallurgist is a trusted resource for practical insights, Mineral Processing and Ore Dressing 911Metallurgist2016年6月8日 The gold cyanidation process is the most important method ever developed for extracting gold from its ores The reasons the widespread acceptance of cyanidation are economic as well as metallurgical It usually Gold Cyanidation Process 911MetallurgistHGM ultrafine grinding mill can process nonmetallic ores with Mohs hardness less than 7 The equipment has stable operation, simple operation, long service life, low carbon and environmental protection There are 5 models of HGM SBM Ore Ultrafine Grinding Mill
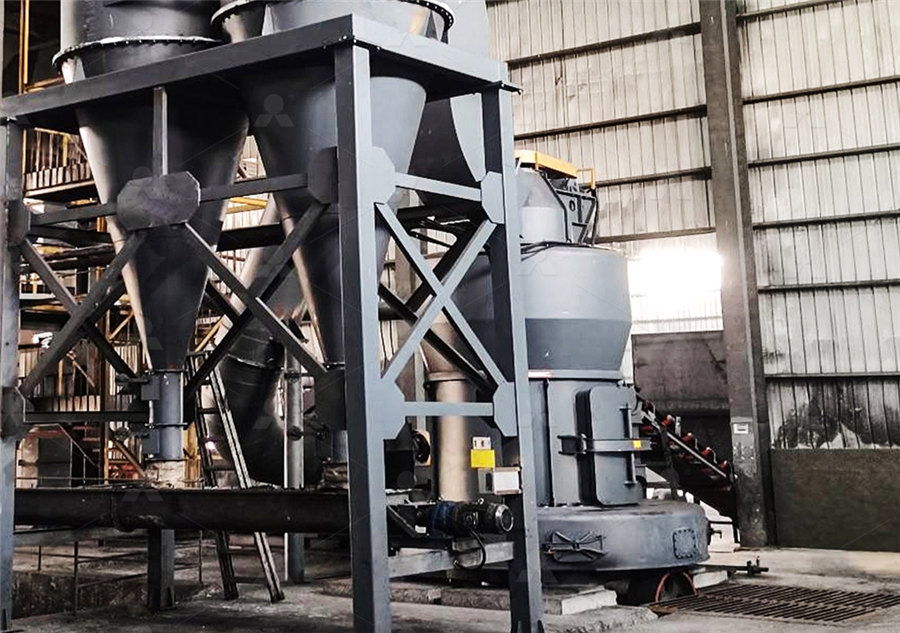
(PDF) Grinding Media in Ball MillsA Review ResearchGate
2023年4月23日 Comminution includes the blasting, crushing, and grinding of ore to liberate valuable mineral particles mill efficiency, minerals liberation and grinding rate2015年4月9日 Typically, this type of mill can produce a product with a fineness of less than 01 mm Testing of materials is needed beforehand for determining the suitability of the ore for processing in an autogenous mill This type of mill has a distinct advantage of accepting coarse input material and supplying a relatively fine ground productGrinding Mills and Their Types – IspatGuru2019年8月14日 • Central discharge ball mill: the inlet of medium unloading ball mill is at both ends, and the outlet is in the middle of the ball mill 4 According to the ore discharge of ball mill: • Overflow ball mill: Discharge the ore through hollow shaft • Grid ball mill: Discharge the ore through the plaid plateThe Ultimate Guide to Ball Mills Miningpedia2019年4月25日 Since such items as optimum grind, mill feed rate, flotation time, and reagent addition depend on the ore grade, grindability, and other factors, it is suggested that, in the computercontrolled plant of the future, the practice of blending ore to produce a uniform mill feed may be an unnecessary expense and may actually be detrimental to project optimizationOptimizing Grinding and Regrinding Capacity in Mill Design
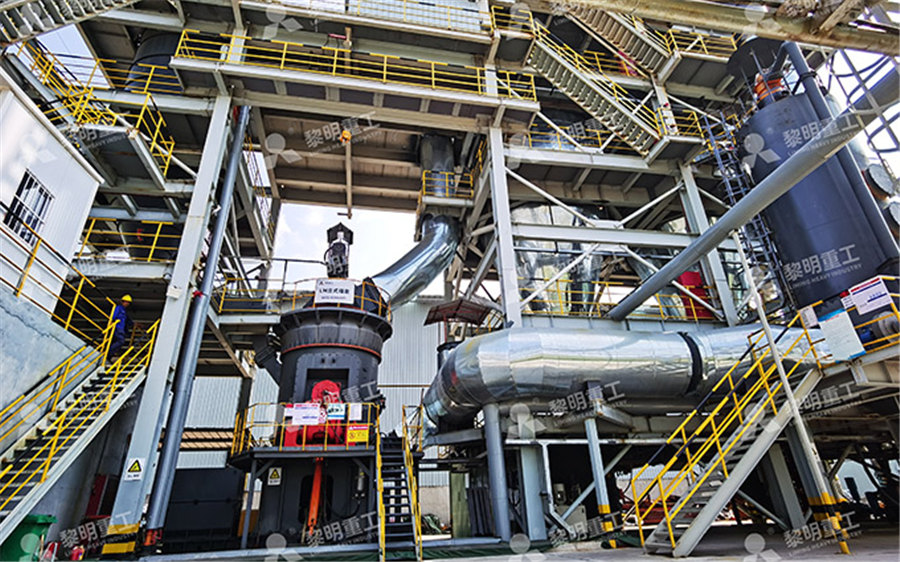
Calculate and Select Ball Mill Ball Size for Optimum Grinding
2013年8月3日 In Grinding, selecting (calculate) the correct or optimum ball size that allows for the best and optimum/ideal or target grind size to be achieved by your ball mill is an important thing for a Mineral Processing Engineer AKA Metallurgist to do Often, the ball used in ball mills is oversize “just in case” Well, this safety factor can cost you much in recovery and/or mill liner 2024年11月21日 The grinding and grading stage of lithium ore is to ensure that lithium minerals are fully dissociated from gangue mineral monomers Therefore, lithium ore extraction is inseparable from ore grinding, and the common equipment for lithium ore grinding is ball mill Onestage closedcircuit grinding and grading process can be adopted, and the onestage Ball Mill Is Indispensable For Lithium Ore Processingore sources Outcomes from reconciliation studies may be put into two categories; misclassification of significant tonnages of ore grade material (common), and discovery of problems in postmining processing and documentation (less common) A definite consequence of the former is the haulage of misclassified ore to waste dumps or waste to the Ore Grade Reconciliation Techniques – A Review Mining 2024年2月19日 If the added material is a relatively hard ore, then when selecting the ball mill steel ball, we should choose a steel ball with a particle size of 5 times the ore; if The material is medium hardness ore, then the ball mill Ball Mill Steel Balls: Quality And Gradation JXSC Mineral
.jpg)
Grinding in Ball Mills: Modeling and Process Control
2012年6月1日 PDF The paper presents an overview of the current methodology and practice in modeling and control of the grinding process in industrial ball mills Find, read and cite all the research you Iron ore dry grinding dry magnetic process of iron ore dressing mill for dry fine grinding, grinding fine reading can guarantee200 above 80%, equivalent to the common process of ball mill and screw grading machine or ball mill and cyclone grinding closed process, at the same time, iron ore dressing mill processing capacity is much higher than the ball mill, low energy consumption, News Iron ore mineral processing with standing grinding or ball 2021年6月8日 The FrymaKoruma MZ toothed colloid mill is perfect for wet milling of fluids and highviscosity suspensions and emulsions The FrymaKoruma MZ can be suppliedFrymaKoruma Toothed Colloid Mill MZ Variable Wet Milling2021年9月30日 Mining continues ahead of schedule, adding to the surface ore stockpiles A total of 384,000 tonnes grading 558% copper was mined during the period from August 21 to September 20, including 141,000 tonnes grading 732% copper from the Kakula Mine’s highgrade centre and 36,000 tonnes grading 489% copper from the Kansoko MineKamoaKakula Phase 1 concentrator mills approximately 320,000
.jpg)
Lala ZHAO Professor (Associate); Doctor of Philosophy China
Lala ZHAO, Professor (Associate); Cited by 522 of China University of Mining and Technology, Xuzhou Read 24 publications Contact Lala ZHAOOre grinding is one of the key stages in the mining process It's where the ore is reduced to a fine powder, which can then be used in other stages of the extraction process Grinding performance is a critical parameter for this stage, as it affects both the speed and quality of the final product The parts of a ball millFactors affecting ores grinding performance in ball millsToothed disk mill Condux V4 Toothed disk mill Condux V4 Toothed disk mill Condux V4 Muhr EMMA250 Muhr EMMA250 Muhr EMMA250 Condux V2 Condux V1 BühlerMiag tworoll spiked roller mill DBZDBühlerMiag tworoll spiked roller mill DBZDBühlerMiag tworoll spiked roller mill DBZDToothed disk mill Millingsystems Höflinger2022年1月1日 The size of grinding media is the primary factor that affects the overall milling efficiency of a ball mill (eg power consumption and particle size breakage)Effect of grinding media on the milling efficiency of a ball mill
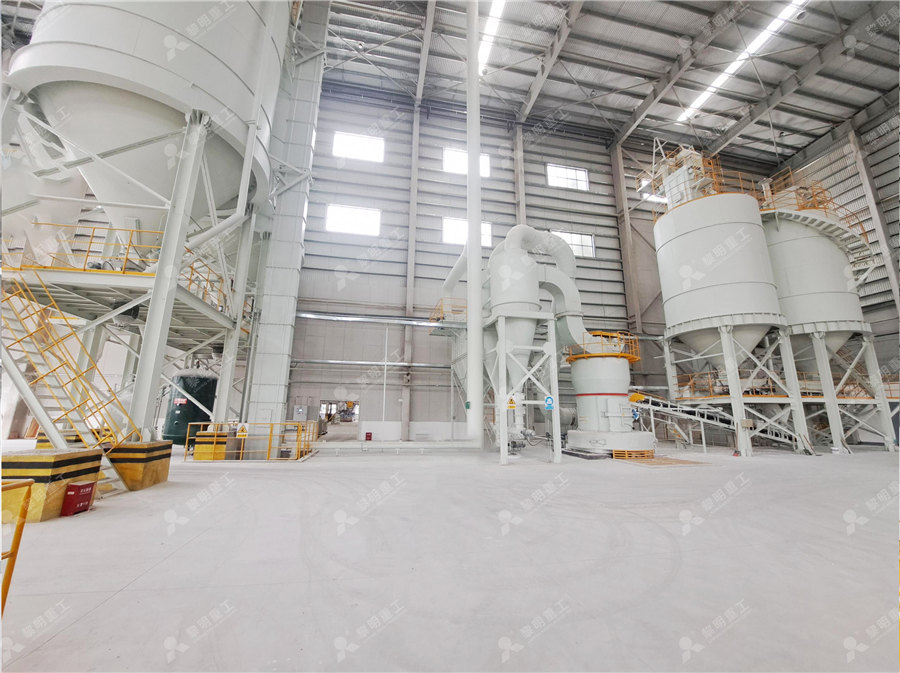
Copper ore flotation plant optimizes grinding and grading
2024年9月25日 A copper ore selection plant encountered problems during the production and commissioning phaseThe design production capacity of the selected plant is 4500t/d, and the processing capacity is 1875t/h at Taiwan timeIn the early stage of commissioning, when the processing capacity of the ball mill was 140t/h, the indicators were better, but when the 2016年5月10日 In the handling of wet, sticky ores such as encountered in tropical areas having distinct dry and rainy seasons, the crushing plant is a section of the mill which must be planned very carefully Unless this is done, crushing becomes a constant source of trouble resulting in lost production and high milling cost In some areas rainfall is high for prolonged periodsCrushing and Grinding Wet Sticky Ore 911Metallurgist2016年3月21日 where R represents the ratio: % Pb in crude ore/% Cu in crude ore Formula (32) is very convenient for milling calculations on ores of this type Example: An ore contains 5% lead and 1% copper The ratio of perfect Common Basic Formulas for Mineral Processing 2016年2月1日 The purpose of this study is to understand how ore loss and dilution affect the mine call factor, with the aim of subsequently improving the quality of ore mined and fed to the millMonitoring ore loss and dilution for minetomill

Multiobject optimization design for differential and grading toothed
2008年6月1日 Motor assembly of crankshaft; 9Motor assembly of toothed roll axis Fig 1 General structure drawing of differential and grading toothed roll crusher Fig 2 Breaking mechanism sketch of differential and grading toothed roll crusher 2 Kinetic analysis of the crankrocker mechanism The performance of a hinged fourbar mechanism depends on the relative 2023年7月20日 Therefore, the rod mill is mostly used for coarse grinding of the previous period of ball mill, or grinding of brittle materials and materials against overcrushing, such as tungsten and tin ore before gravity separation; and (3) autogenous mill – it refers to the materials which themselves are collided and ground mutually to be crushed when the grinding mill rotates, and Ore Grinding SpringerLink2019年8月29日 Sensor‐Based Ore Sorting Technology in Mining—Past, Present and Future August 2019; Minerals 9(9) successful this route is for optimi zing the mill power draw and thro ughput of a gold (PDF) Sensor‐Based Ore Sorting Technology in Mining—Past, 3 Physical Bauxite Processing: Crushing and Grinding of Bauxite 137 BlowBar Style HighSpeed Impactor Hammermill Style HighSpeed Impactor Fig 32 High speed impacttype crushers fines created from highspeed crushing circuit were a benefit to the comminutionPhysical Bauxite Processing: Crushing and Grinding of Bauxite
.jpg)
Comminution and classification technologies of iron ore
2022年1月1日 Ore that is less than 40 mm but greater than 8 mm is conveyed to the lump stockpile Ore that is finer than 8 mm, but greater than 1 mm is conveyed to the fines stockpile Any ore that is finer than 1 mm in size is conveyed to a desanding plant consisting of cyclones, upper current classifiers and two stages of spirals for further beneficiationWhen iron ore is extracted from a mine, it must undergo several processing stages Six steps to process iron ore 1 Screening We recommend that you begin by screening the iron ore to separate fine particles below the crusher’s CSS before the crushing stageThe six main steps of iron ore processing MultotecHowever, ore below the pay limit adds variation to the mill grade as increased mill throughput will be required to make up for the loss of gold, and that impacts on the recovery in the plant It is against these perspectives and findings of this study that the MCF should be seen as a method that identify the real problems underground and when these are addressed, the profitability of Monitoring ore loss and dilution for minetomill integration in CLUM vertical roller mill is a new type of milling equipment that includes grinding, grading, conveying, secondary powder selection, Illite ore industrial grinding mill machine can grind illite into powder up to 3000 mesh, including ultrafine Vertical Roller Mill SBM Ultrafine Powder Technology
.jpg)
Milling Equipment,Ball Mill Price,Ore Beneficiation Supplier,Ore
Ball Mill Ball mill is ore dressing equipment, mainly used for crushing bulk ore materials into ore pulp, for further separating operations; Spiral Classifier Spiral separator is large grading equipment This machine classifies materials according to the different sizes and proportions of solid particles Magnetic Separator Magnetic separator is common used magnetic separator Mill Diameter Mill Length Installed Power Mill Volume Power Intensity (m) (m) (kW) m3 (kW/m3) Autogenous Mill 10 45 6400 353 18 Ball Mill 5 64 2600 126 21 Regrind Ball Mill 32 48 740 39 19 Tower Mill 25 25 520 12 42 IsaMill 13 3 1120 3 280 3 3) 23/m) Ball Mill Tower Mill IsaMill (m Power Intensity Media Size No Balls / m Surface Area Fine Grinding as Enabling Technology – The IsaMill2015年4月15日 Discharge from each mill Feed to each classification stage Oversize from each classification stage Fines from each classification stage, k Power drawn by each mill (motor input) Motor and drive efficiency of each mill, Size of and type of grinding media used in each mill Speed in RPM for each mill Liner design and condition in each millWhat Ore Testing is Required For Mill Selection2024年9月30日 The liner is a wearprone component in ball mills, subject to continuous impacts, squeezing, and abrasion from the grinding media during operationEffect of Grinding Media Grading on Liner Wear and Load
.jpg)
Understanding the SAG Mill in Copper Ore Mining Process
The rod mill is another type of grinding mill used in the copper ore mining process This machine uses steel rods as the grinding media instead of balls, which are commonly used in ball mills The rods grind the ore by tumbling within the mill, similar to the action of a rotating drum2015年1月1日 The essence of ore grade reconciliation is to identify, analyse and manage variance between planned and actual results in a way that highlights opportunitiesOre Grade Reconciliation Techniques A Review ResearchGate2023年8月31日 The laboratory double roller crusher is for crushing nonmetallic materials such as coal, ore, and rock, which is suitable for intermediate and fine crushing of raw materials in the laboratory; This machine uses two rollers to rotate relative to each other to crush the material entering the crushing chamber, then enters the receiving hopper through the gap between the 3 Types Of Laboratory Crushers For Sample Ore Preparation2022年2月10日 What is a double roll break? Doubleroll break is also called doubleroller crusherThis series of doubleroll crusher can be used for finely crushing various high and medium hardness ores and rocks in industrial sectors such as mineral processing, chemical industry, cement, refractory materials, abrasives, and building materialsWhat’s a DoubleRoller Crusher? Eastman Rock Crusher
.jpg)
Calculate Ball Mill Grinding Capacity 911Metallurgist
2015年10月15日 A) Total Apparent Volumetric Charge Filling – including balls and excess slurry on top of the ball charge, plus the interstitial voids in between the balls – expressed as a percentage of the net internal mill volume (inside liners) B) Overflow Discharge Mills operating at low ball fillings – slurry may accumulate on top of the ball charge; causing, the Total Charge