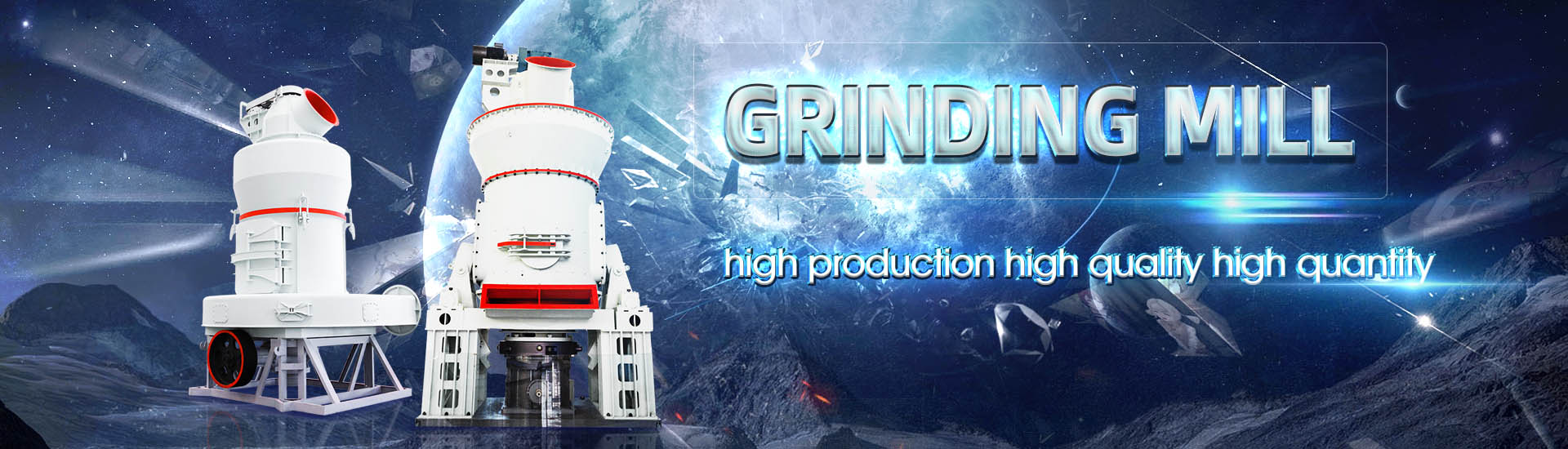
Cement raw material processing technology and related equipment
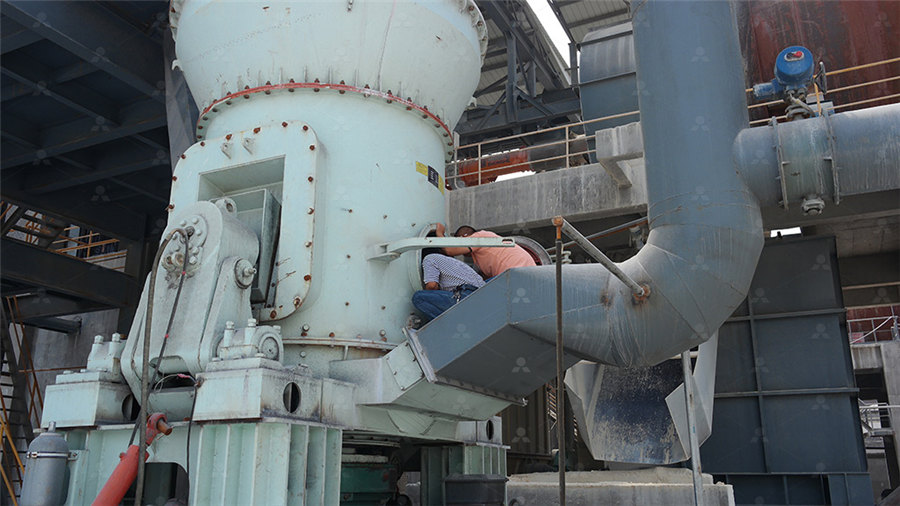
Modernizing cement manufacturing in China leads to substantial
2022年11月17日 The cement manufacturing process mainly includes four steps: resource extraction, raw material preparation, clinker calcination, cement grinding 17,18, and fossil fuel Producing cement consumes both large quantities of raw materials and fuel, and produces substantial CO2 emissions The use of alternative fuels and raw materials in cement Guidelines for CoProcessing Fuels and Raw Materials in Cement This article provides an overview of the main technologies for carbon dioxide capture in the cement industry at home and abroad, with a focus on the current application status of oxygen Cement Technology2023年11月1日 As grinding processes consume most of the power, grinding technology has a major impact on total electric energy demand: Cement plants which use modern grinding The cement plant of tomorrow ScienceDirect
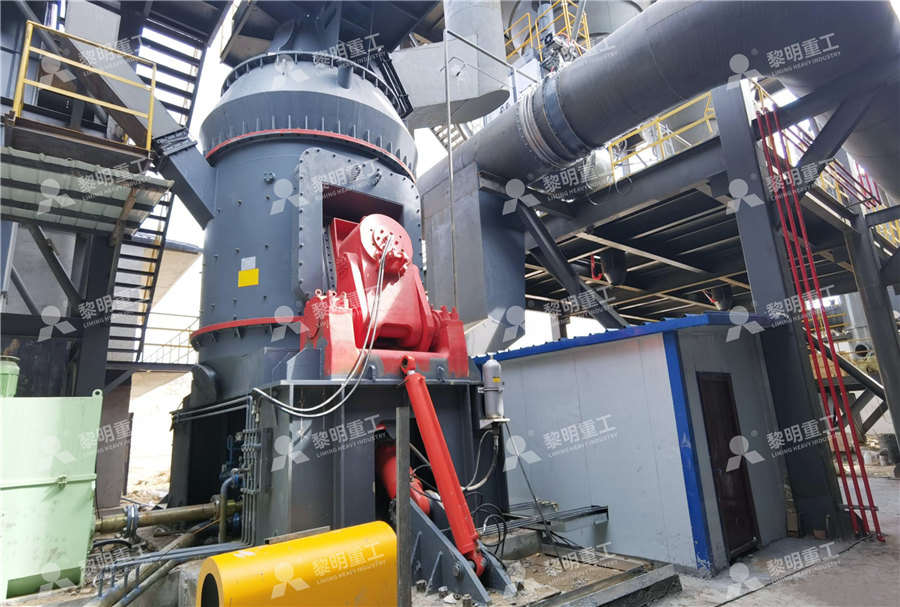
A practical guide to improving cement manufacturing processes
There are 4 stages of cement production that help maintain consistent raw material quality with minimal chemistry deviation, from quarry to silo to customer The Quarry: The cement 2021年11月17日 There are four main types of processes used in cement manufacture: Dry Process, Semidry Process, Semiwet Process, and the Wet process In all these processes, Cement Manufacturing—Technology, Practice, and Development2019年1月21日 The idea of alternative binders is to introduce different raw materials in clinker and cement manufacturing processes that will emit less CO 2 and utilize less energy without compromising the efficiency and quality of Recent Progress in Green Cement Technology Utilizing There are four main types of processes used in cement manufacture: Dry Process, Semidry Process, Semiwet Process, and the Wet process In all these processes, the following steps Cement Manufacturing—Technology, Practice, and Development
.jpg)
Cement Analysis and Production Information Thermo
Learn about technologies and equipment used in the cement process including elemental online analyzers, xray analyzers, belt scales, weigh belt feeders, level sensors and indicators, impact weighers, stack emission gas detectors, and Ideally the material should always have the same degree of preparation, but due to the kiln operation itself and normal fluctuations of the raw material properties, fuels, ambient conditions and others, this is not the case Variations in the raw Kiln Control and Operation INFINITY FOR CEMENT Figure 811 (left) Modern Xray spectrometer use in cement analysis (right) Specimen preparation equipment for cement and related materials include borate flux, mortar and pestle weighing dish, sieves, dessicator and the resulting Everything you need to know about Analytical 51 Preblending of Raw Material In recent years, the improvement of quality with greater raw material utilization and optimum applications of processing plants is being striven after more and more in the sector of raw material beneficiation Greater and greater fluctuation in properties of raw materials such as ores, limestone and, in particular,Raw Material Homogenization and Storage INFINITY FOR CEMENT EQUIPMENT
.jpg)
INFINITY FOR CEMENT EQUIPMENT
1 Introduction and composition of Portland cement 2 Raw materials 3 Production of cement clinker 4 Characterisation of Portland cement clinker 5 Grinding fineness of cement 6 Tests of cement quality 7 The hydration of Portland cement 8 The nature of hardened cement paste 9 Portland cements and related blended cements 10 Admixtures and In the past, the wet process was preferred for the production of high quality cement, since homogenization of the slurry resulted in a thorough mixture of the raw material components Progress in the fields of aerodynamics and pneumatics has enabled the cement industry to pneumatically homogenize the dry cement raw mix [164]Pneumatic homogenization of raw mix INFINITY FOR CEMENT EQUIPMENT2023年11月21日 The recycling of waste materials and raw materials will be further promoted to reduce waste emissions during the production process The upgrade of production line equipment will reduce noise and dust emissions, adopt more environmentally friendly materials and processes, and strive to achieve green and sustainable developmentTrend Analysis Of Cement Production Line Design Cement EquipmentSection 1: Cement Manufacturing Process Raw Material Extraction and Preparation Types of raw materials used (limestone, clay, etc) Extraction and transportation methods Word count: 1000; Raw Material Proportioning and Grinding Techniques for proportioning and grinding raw materials Equipment used in this stage Word count: 1000Comprehensive Guide to Cement Kilns: Processes, Types,
.jpg)
Full article: Review of HighPressure Technology in Terms of
2024年10月1日 The main goal of comminution operation in mineral processing technology is to produce a material with the appropriate particle size and a level of useful component liberation This predetermines to some extent the mineral recovery and the overall effectiveness and productivity of the entire process of raw materials beneficiationWith our marketleading MULTICOR cement processing solutions, we help you meet the defining challenges in today’s marketplace, by dramatically reducing your CO2 emissions in line with new regulations – and ensuring the quality and competitive pricing of your product through the valueadded efficiencies of our unique and innovative approachCement processing equipment QlarThe principal raw materials for cement manufacturing are: Limestone; Silica and alumina from basalt , shale or sand; Iron from iron ore or steel mill scale Sand stone; Pumice (volcanic ash for Portland Pozzolana cement ) Gypsum General Properties of Raw Material Sources Limestone; The basic raw material of the cement production is limestoneCement Manufacturing Process INFINITY FOR CEMENT EQUIPMENTA: Portland cement: Portland cement is made by heating limestone with small quantities of other materials (such as clay) to 1450°C in a kiln, in a process known as calcination The resulting hard substance, called ‘clinker,’ which is then Basic Cement Technology INFINITY FOR CEMENT
.jpg)
Prehomogenization INFINITY FOR CEMENT
Prehomogenization In past cases, where the main component of the cement raw material (usually limestone), showed con siderable fluctuations in the CaC03content, and as long as relatively low quantities of raw materials were AGICO Cement supplies cement equipment for cement raw material production as you Skip to content +86 s about blog contact EN ES Menu Menu Home; Cement Equipment Raw Material Preparation Of Cement Raw Material Cement Mill, Multistage cyclone preheaters and precalciners in a cement plant improving the thermal efficiency of the energyintensive process of cement manufacturing This chapter discusses the role of preheaters and precalciners in improved pyroprocessing and related material, operation, and environment benefits to the overall cement kiln operation Everything you need to know about Preheaters and Precalciners2016年11月30日 R Murthy and Santhosh Kumar M elaborate on the use of stackers and reclaimers used in cement industry for feeding raw materials Stacking raw materials/fuels and reclaiming them is an essential part of cement industry Stacking of raw material is done in order to have sufficient raw material to feed the plant during any unforeseen supply stoppageRaw material stacking and reclaiming Indian Cement Review
.jpg)
Everything you need to know about cement Materials Preparation and Raw
Sucre, Luis, “Raw material control,” World Cement, October 1998, pages 6063 Tschudin, M, “Online control of the blending bed composition using PGNAA in Ramos Arizpe (Mexico),” Proceedings of VDZ Congress ’93 on Process Technology for Cement Manufacture, Bauverlag GmbH, Wiesbaden and Berlin, 1995, pages 259266Previous Post Next Post Contents1 Select your Favorite Type of 7 Different types of Vertical Mill11 1 Fuller 12 2 FLSmidth (atox Ok)13 3 Loesche GmbH LM (VRM)14 4 Gebr Pfeiffer MPS (VRM)15 5 thyssenkrupp Polysuis ( RDRM)16 6UBE Japanese vertical mill17 7 (CNBM ) Chinese vertical mill Select your Favorite Type of 7 Different types of Select your Favorite Type of 7 Different types of Vertical Mill76 4 Cement Manufacturing—Technology, Practice, and Development Fig 42 Modern dry process cement production process 424 Manufacturing of Cement Clinker The prepared raw material is called the “kiln feed” and is fed to the kiln In the kiln, this kiln feed is subjected to a thermal treatment process which consists ofCement Manufacturing—Technology, Practice, and DevelopmentLuoyang Building Material and Architectural Design and Research Institute (LCDRI) was founded in 2000, is a subcompany of AGICO CEMENT, after tenyear develoment, LCDRI has already become a National grade professional firstclass design and research institute that provides scientific research and development of newtype cement dry process production, engineering Cement Plant Manufacturer Cement Equipment Manufacturers
.jpg)
Cement manufacturing process PPT Free Download SlideShare
2014年6月10日 Evolution of the cement Process • Wet process easiest to control chemistry better for moist raw materials • Wet process high fuel requirements fuel needed to evaporate 30+% slurry water • Dry process kilns less fuel requirements • Preheater/Precalciner further enhance fuel efficiency allow for high production ratesBy taking optimization measures such as reducing the initial roll gap of the roller press, strictly controlling the moisture content of raw materials, controlling equipment air leakage, adjusting the internal structure and grading of the grinding material, the system crust was improved, the system resistance was reduced, and the production capacity of the grinding system increased from Cement TechnologyComparison of Raw Material Preparation Technology Vertical Raw Material Grinding System Vertical mill is a kind of air swept mill, which integrates drying, grinding and product classification It has the characteristics of less system Raw Material Preparation in Cement Manufacturing 2020年6月5日 Limestone calcined clay cements (LC3) are blended cements that combine clinker, limestone, calcined clay and gypsum The availability of the materials required to produce LC3 and the good Limestone calcined clay cements (LC3): raw material processing,
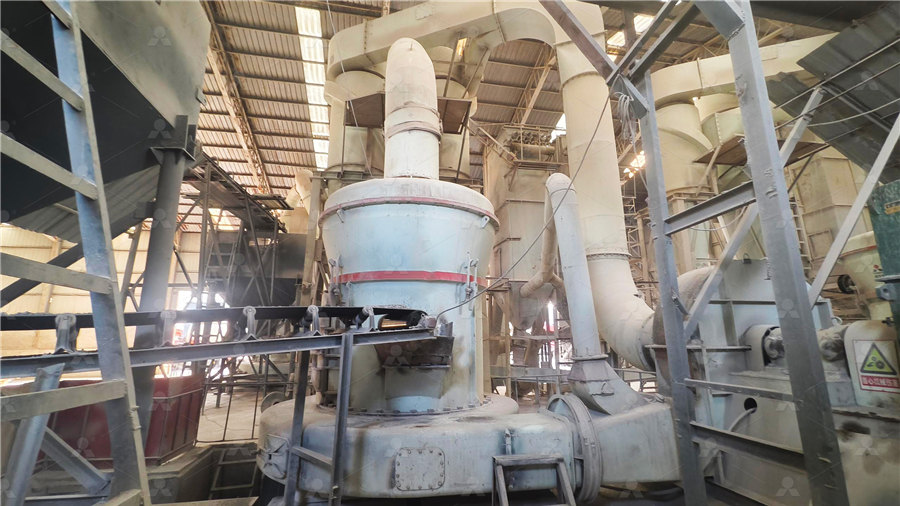
Cement Plant Raw materials INFINITY FOR CEMENT EQUIPMENT
Bulk material handling is a major activity and bins for raw materials, intermediate products and finished cement must reliably provide controlled flows of materials upon demand The tonnages of material to be stored at various process stages are outlined by Deolalkar in Chapter 13 of his book (Deolalkar,2009), while his Chapter 16 discusses the features of materials handlingsystemsRaw Materials in Cement Manufacturing Raw materials for cement manufacture include all the types of materials listed in Table 842 Of these, the lime sources, usually carbonates, are the most important Only a representative sampling of some of the most widely used raw materials are shown here Table 842 Raw Materials in Cement Everything you need to know about Application of Thermal TO buy the Most Important Books in Cement Industry + more than 30 excel sheets related to cement industry + Manuals and efficiency in utilization of raw materials Industrial Information Technology Applications of process automation have now embraced the concept of what is known as “Industrial Information Technology,” an Everything you need to know about Automation and Optimization The use of alternative fuels in both combustion and production processes is known as coprocessing in cement manufacturing Waste is now being used to substitute primary fuel sources like coal, petroleum, and gas in the combustion process They are usually from combustible municipal waste, refusederived fuels, biomass, or nonhazardous industrial and commercial Sustainable Clinker and Cement Production by Using Alternative Fuels
.jpg)
The cement raw material blending process and its control system
This paper focuses on modelling and solving the ingredient ratio optimization problem in cement raw material blending process A general nonlinear timevarying (GNLTV) model is established for 2020年1月1日 Energy efficiency through modern dryprocess technology, the use of other fuels to replace coal and pet coke within the cement kiln heating process, the substitution of clinker with other mineral Assessment on Cement Production Practice and Potential Cement The power used for the actual grinding process while grinding raw materials, depends mainly on the hardness of raw materials and the type of mill used, ie ball mill or vertical roller mill Typically, the motor of the ball mill consumes about 14 – 15 kWh/ ton of raw mix whereas the VRM motor uses 7 – 8 kWh/ tonModern Processing Techniques to minimize cost in Cement 2014年12月31日 An insight into the criteria for the design of the plants for raw materials handling, storage and homogenisation in the cement industry Raw materials used in cement plants have a great influence on the investment for a Raw material handling and storage Indian Cement
.jpg)
Loesche Technology Always a Step Ahead: Loesche
2014年11月6日 Several examples of this are deployed in Klingenberg, Europe’s first coal dustfired largescale power plant in Berlin for coal grinding with a raw coal rate of approx 12 t/h 1934 Loesche mills are increasingly also used 2019年8月27日 The major raw materials used as a source of CaO for cement manufacturing are limestone, chalk, marl, etc These raw materials by virtue of their natural occurrence contains other mineral impurities eg, MgO, SiO 2, Al 2 O 3, Fe 2 O 3, alkali compounds, and sulfidesThese impurities play an important role to influence the cement manufacturing Cement Manufacturing and Process Control SpringerLinkRaw Material Extraction: The primary raw materials used in cement production are limestone, clay, and marl These materials are typically extracted from quarries through drilling and blasting Crushing and Prehomogenization : The extracted raw materials are crushed to reduce their size and then blended to ensure a consistent chemical compositionCement Plant Process Optimization: Unlocking Efficiency and 2015年12月9日 Raw materials are used to produce the main cement elements (Mohsen, 2015) • Quarry The process of obtaining raw materials for cement manufacturing involves mining and quarrying natural materials (PDF) Cement Manufacturing ResearchGate
.jpg)
The Cement Production Process
Developments in grinding technology have largely been in the dry process technology, and have broader application than ‘raw’ and ‘finish’ milling in cement plants Modern grinding and separating plant incorporating technological improvements is also used for grinding phosphate rock, chemical fertilisers, coal for power stations, limestone and other materials2022年11月28日 Cement kiln coprocessing (CKC) is a promising technology for solid waste treatment, which can achieve both goals of energy saving for cement production and environment protection for waste reduction, and further development of this technology is desired, so it is necessary to highlight its research gaps between science and technology In this study, a Technological opportunity identification of cement kiln coprocessing Raw Materials Required for Cement Production; Cement Manufacturing Process Chapter 10: Production Process and Technology Detailed Process Flow; The Comprehensive Guide to Cement Plant Costs: An InDepth Look at Equipment, Workforce, and Material Costs Next How to Start a Cement Factory: A Comprehensive Guide2022年1月1日 In addition, particulate matter such as PM10 and PM25 is also released from the process of manufacture of cement from the process of extraction to the process of packing and loading [31] In addition,136 tonnes of NOx, 4,833 tonnes of SO2, 183 tonnes of VOCs, including toxic dioxins, furans and PCBs, and 320 kg of mercury is released by cement industry in 2010 Environmental impact of cement production and Solutions: A
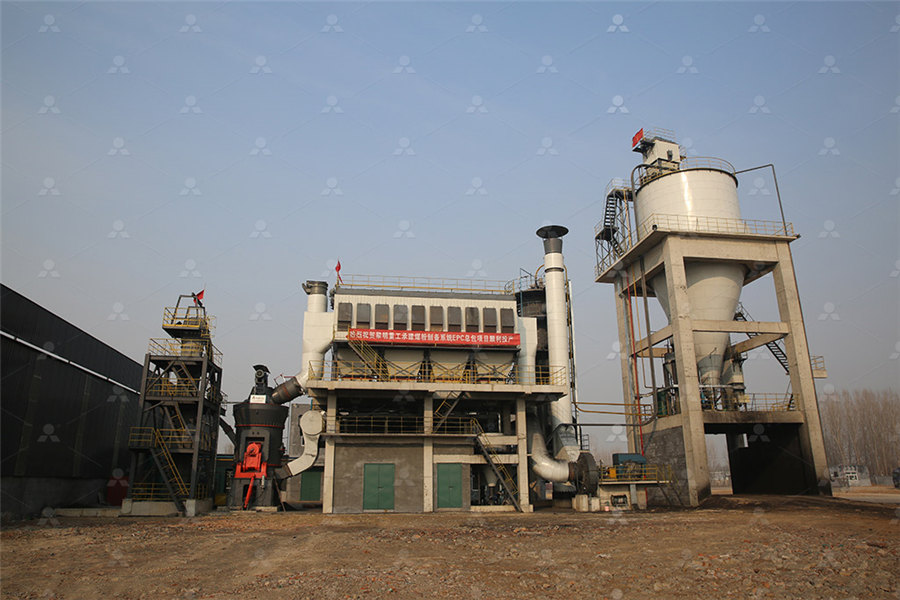
Manufacturing of Portland Cement – Process and Materials
4 天之前 The manufacture of Portland cement is a complex process and done in the following steps: grinding the raw materials, mixing them in certain proportions depending upon their purity and composition, and burning them to sintering in a kiln at a temperature of about 1350 to 1500 ⁰C During this process, these materials partially fuse to form nodular shaped clinker by