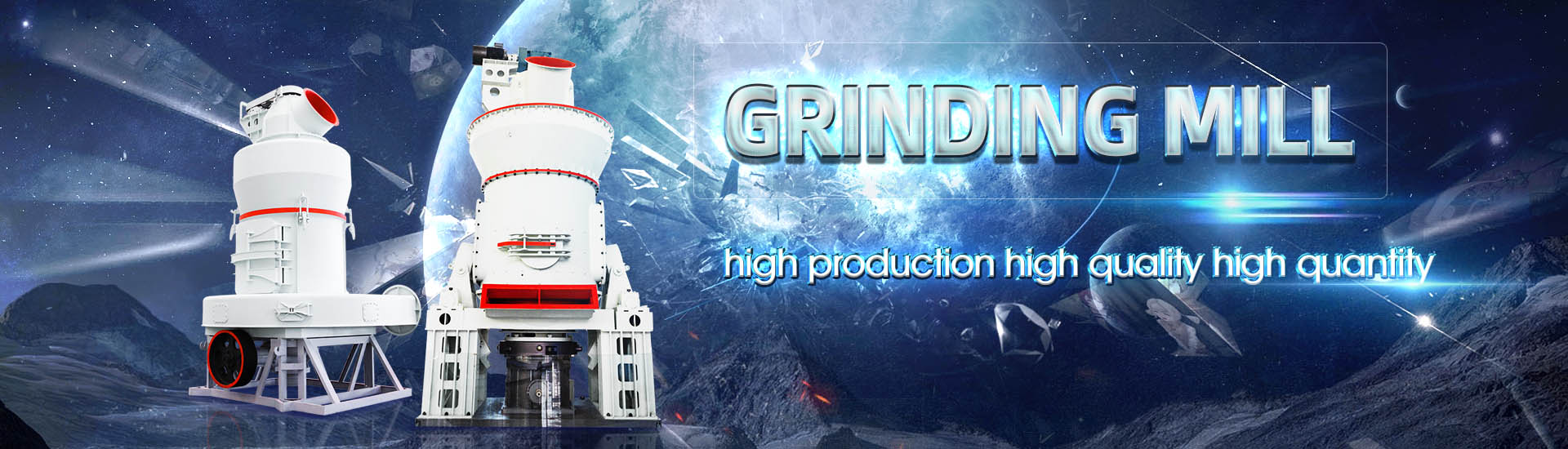
SS grinding lime 0 ore mill length
.jpg)
SAG Mill Grinding Circuit Design 911Metallurgist
The design of large mills has become increasingly more complicated as the size has increased and there is little doubt that without sophisticated design procedures such as the use of the Finite Element method the required factors of safety would make large mills prohibitively expensive In the past the design of small mills, 展开The aspect ratio (mill diameter/mill length) of autogenous and semi autogenous mills varies widely and can be as high as three or as low as 05(PDF) Toward a Simple Approach Determining Single Stage SAG entirely possible for a relatively ‘soft’ ore with Axb ~70 to have similar SAG milling Ecs requirements as a relatively competent ore with Axb ~40, depending on the cumulative SAG Mill Design and Benchmarking Using Trends in the JKTech Semiautogenous grinding mills (SAG mills) are tumbling mills that most commonly have a shell diametertolength ratio of around two With this high aspect ratio, SAG mills generate both Semiautogenous grinding (SAG) mill liner design and development
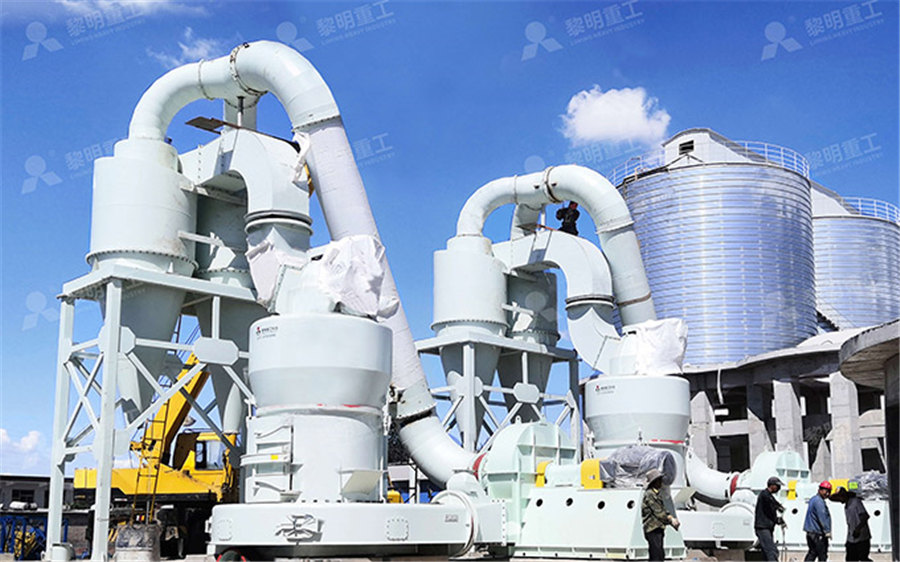
OneMine Mako Single Stage Sag Mill Comminution Circuit
2019年1月1日 The comminution circuit comprises primary crushing single stage SAG milling with recycle crusher (1oCR SSSAC) The mill reached design throughput and grind size 2016年1月1日 Based on their higher throughput and coarser grind relative to AG mills, it is more common for SAG mills to be used as the primary stage of grinding, followed by a second stage Comminution Circuits for Gold Ore Processing ScienceDirect2022年4月1日 Best practice ore hardness measurement requires measuring the SAG hardness to grind the ore from a feed size F 80 of 152 mm to a transfer size T 80 of 17 mm, using the Keys to best practice comminution ScienceDirectIt is performed in cylindrical steel vessels that contain a charge of loose crushing bodies—the grinding medium—which is free to move inside the mill, thus comminuting the ore particles Grinding Mill an overview ScienceDirect Topics
.jpg)
Design of the 40 foot SAG Mill Installed at the Cadia Gold Copper
This includes the primary crusher, coarse ore stockpile, conveyors, grinding mills, recycle crushing and ancillaries (ie lime addition, ball addition) The SAG mill cost $122 million, Lime Manualpdf Free download as PDF File (pdf), Text File (txt) or read online for free This document discusses lime handling systems and provides recommendations for designing efficient and practical lime systems It covers Lime Manual PDF PDF Mill (Grinding) CalciumMinerals 2020, 10 ‐‐ ‐ Optimization of Operating Parameters on Dry Grinding of Calcite An 8 x 7 diaphragm type ball mill grinding 05″ copper ore to 96% passing 65 mesh when 45 to 55 percent of its internal volume is filled with grinding mediaMill HP is proportional to the effective grinding length of the mill Mill Grinding Mills 911Metallurgist
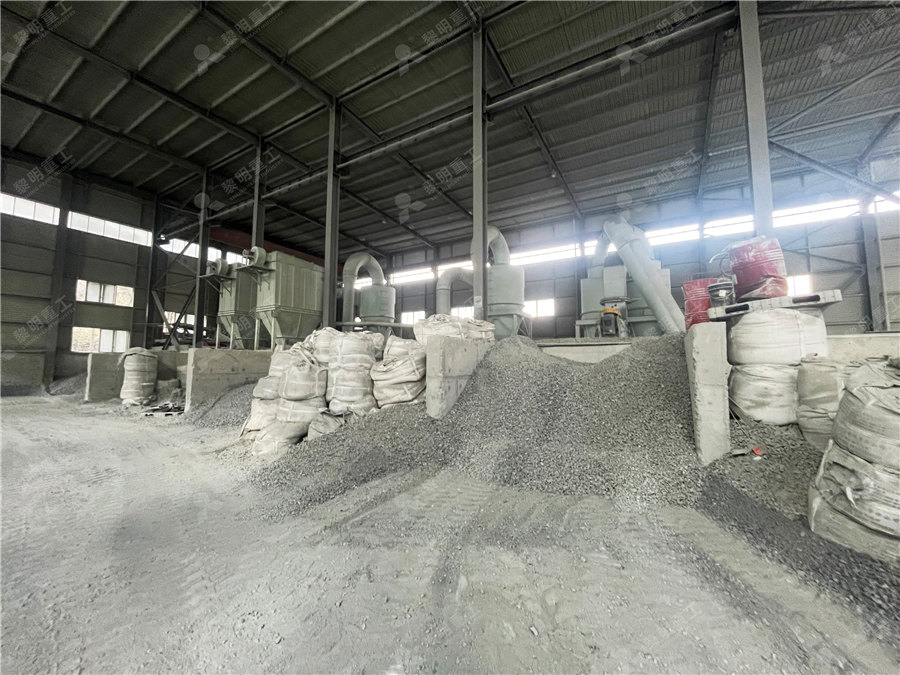
SBM Ore Ultrafine Grinding Mill
HGM ultrafine grinding mill can process nonmetallic ores with Mohs hardness less than 7 The equipment has stable operation, simple operation, long service life, low carbon and environmental protection There are 5 models of HGM ultrafine grinding mill, 2015年4月9日 Maximum rod length is about 6 to 7 meters, otherwise there is a risk of the rods bowing The drum diameter is limited to 06 or 07 times the length of the mill Rod mills are used for grinding hard minerals This type of mill is normally used as the first stage of a milling process to provide a reduced size feedstock for a further milling processGrinding Mills and Their Types IspatGuru2018年6月18日 Ore pretreatment methods for grinding: journey and prospects, Mineral Processing and Extractive Metallurgy Review, DOI: 101080/2018 To link to this article: https://doior g/10 Ore Pretreatment Methods for Grinding: Journey and Prospects48"X 96" Denver ball mill 50 HP (37 kW) ZW63519 used Manufacturer: Denver Used Denver ball mill with diameter of 48" and length of 96" (12 x 24 m) Left hand mill, rotates counter clockwise and pinion shaft is on the right sidePreviously used in a lime slaking system 18" x 24" TroUsed Lime Mill for sale AllisChalmers equipment more
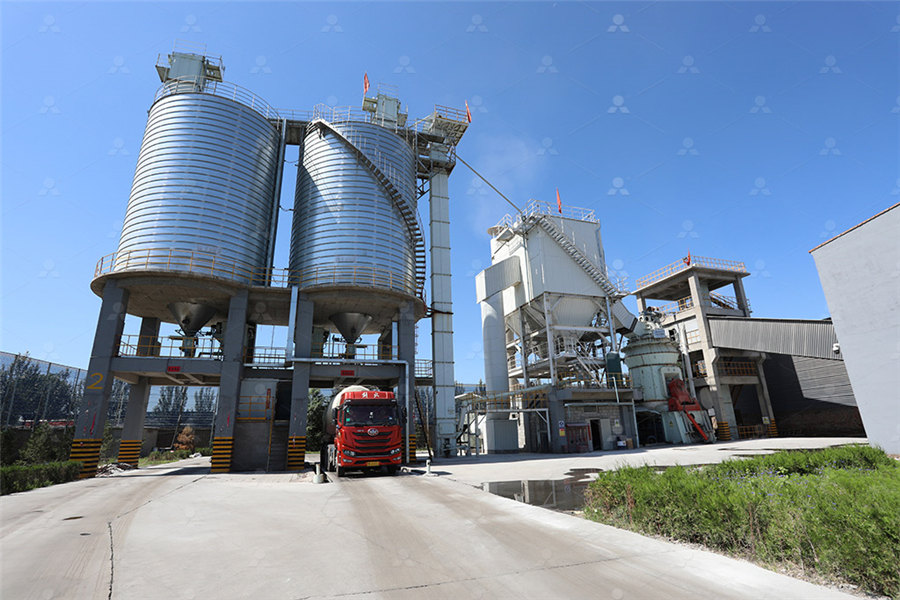
Factors Affecting Ball Mill Grinding Efficiency
2017年10月26日 The following are factors that have been investigated and applied in conventional ball milling in order to maximize grinding efficiency: a) Mill Geometry and Speed – Bond (1954) observed grinding efficiency to be a function of ball mill diameter, and established empirical relationships for recommended media size and mill speed that take this factor into 2018年8月8日 that the best grinding media set includes a grinding medium with a diameter of 1 mm and a length 0–0045 mm However, by grinding copper ore ore grinding in an electromagnetic mill (PDF) Grinding Kinetics Adjustment of Copper Ore Grinding in The results of the analyses clearly shows that using a sieve of +180µm and its bottom 180µm, the best time for grinding 05kg of Itakpe iron ore with 3kg of grinding media and a mill speed of 92 rpm is 8 minutes, yielding 1710% fines and 8290% coarse, 08 mill critical speed measured 1520% fines and 8480% coarse(PDF) Estimation of Grinding Time for Desired Particle Size The damp mill is a kind of ball grinding machine, widely applied in iron ore pelletizing plants a damp mill is mainly used for the damp grinding of iron ore to provide materials for the pelletizing disc Cylinder Length(mm) 6500: Damp Mill – Ball Grinding Machine Iron Ore
.jpg)
How to choose a limestone grinding mill SANDMINE
2024年1月18日 How to choose a limestone grinding mill limestone has a long history of quarrying Limestone is the primary raw material for manufacturing cement, lime, and carbide and is an essential flux limestone 2022年4月20日 Lime is divided into quick lime and slaked lime HGM Series Ultrafine Grinding Mill – 150~2500 mesh YGM Series Raymond Mill – 80~600 mesh Share this article What processing equipment is required for rectorite Limestone crushing and grinding production line2016年10月12日 By making the length of a grate mill and of the cylindrical portion of a conical mill smaller than the diameter, by increasing the circulating load round the closed circuit so as to pass the ore more rapidly through the mill, by adopting two and even threestage grinding, each stage having its own system of classifiers, andClosed Circuit Grinding VS Open Circuit Grinding5 Ball mills are used for wet grinding iron ore, gold/copper ore, nickel ore and other ores, as well as lime/limestone for flue gas desulphurisation systems, coal and other raw materialsSIZE REDUCTION BY GRINDING METHODS By ResearchGate
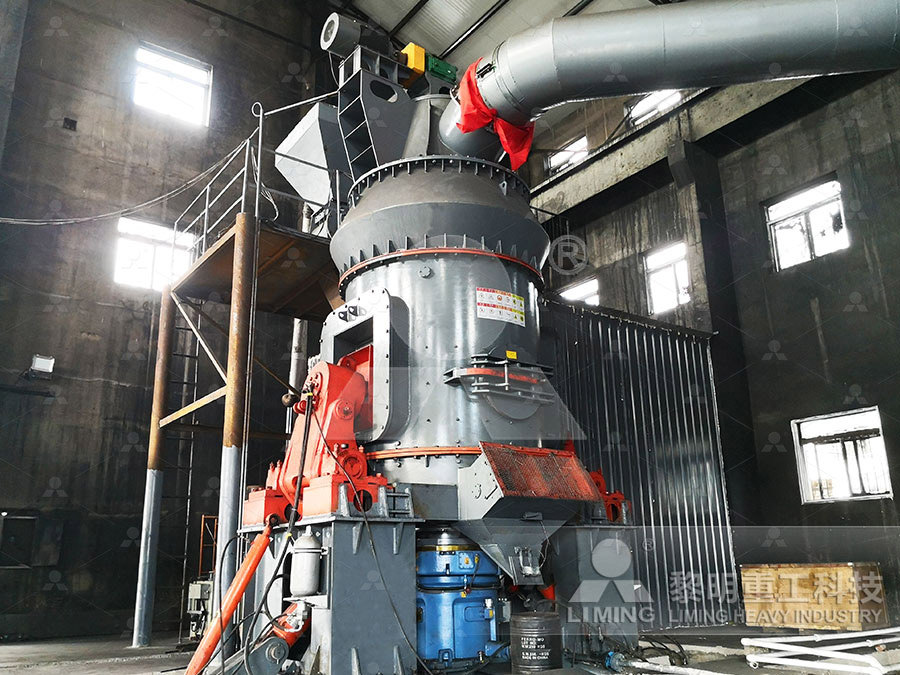
Closed and Open Circuits Ball Mill for Cement, Limestone, Iron ore
We bring forth a highly advanced Ball Mill, specifically engineered for both wet as well as dry cement grinding applications Classified depending on the circuit design, bearing, grinding type and drive, the selection is made on the basis of the product fineness, quality, and nature of raw material, site conditions and specific requirementsOptimization of stirred mill parameters for fine grinding of PGE bearing chromite ore, Particulate Science and Technology, DOI: 101080/2020 To link to this article: https://doi Optimization of stirred mill parameters for fine grinding of PGE Output: 0 t/h 25 t/h Motor power: 19 kW 160 kW Machine length: 4,300 mm 12,275 mm Introductions of High pressure suspension grinding mill: Dingbo High pressure suspension grinding mill is suitable for processing various nonflammable and Limestone mill, Limestone grinding mill All DirectIndustryPregrinding:it refers to adding a grinding machine in front of the cement ball mill to increase the output of the original grinding system by a large margin This method features large investment and relatively complex process but it can increase the output of cement ball mill by up to 50%Ball Mill For Cement Grinding – Cement Ball Mill Ball Mill
R)8OC`6F[ZIB.jpg)
Design of the 40 foot SAG Mill Installed at the Cadia Gold Copper
This includes the primary crusher, coarse ore stockpile, conveyors, The SAG mill cost $122 million, whilst the SAG mill motor PHYSICAL PROPERTIES OF CADIA ORES Laboratory test work data, shown in Table 1, indicated hard and competent ores (monzonite, monzodiorites and volcanics), although not necessarily of such competency as to create concern2023年4月13日 The effect of ball size and interstitial filling on the performance of dry ball mill grinding was investigated for a limestonetype brecciated uranium ore The optimum grinding was obtained with the combination of different balls (127–375 mm) and interstitial filling of 50% (20% ball filling ratio at fixed material filling ratio = 4%) The net power consumption in a ball mill is Optimization of Ball Mill Grinding of a LimestoneType Brecciated 2019年12月15日 429 VertiMills Vertical mills were first designed in the 1950s for applications in fine and ultrafine grinding in Japan Lately, the vertical mill is making progress toward primary grind application and shown promise in energy reduction relative to ball mills, typical to what is normally seen in regrinding applications (Mazzinghy et al 2014)Beneficiation of Gold and Silver Ores SpringerLink2023年9月19日 Limestone grinding mill Material: Limestone Finished product particle size: 01730044mm Processing capacity: 8176t/shift Applicable materials: calcium carbonate crushing processing, gypsum powder Limestone Grinding Mill That You Need To Know
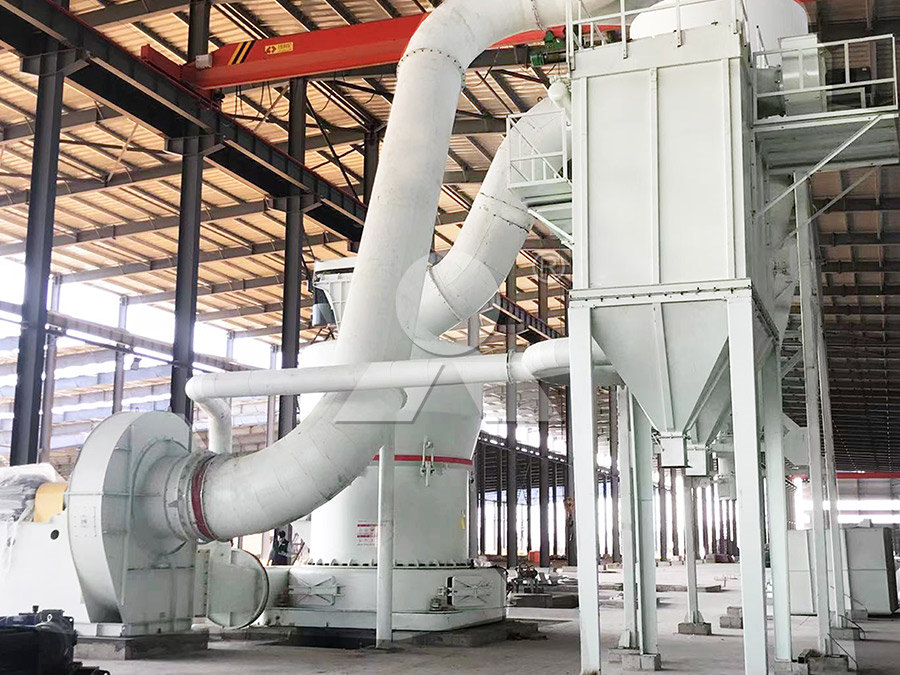
Estimation of Grinding Time for Desired Particle Size Distribution
from the ores The grinding of ore is a highly energyintensive process [1–4] In this process, the size of the particle obtained depends on the energy consumption of the ball mill The major challenge encountered in the process of iron ore grinding is to maintain the desired product particle size distribution (PSD) with sufficient2022年5月22日 Stirred ball mill power Pm, kW 021 019 018 Specific grinding work, W f , kWh t − 1 446 802 1515 Solid mass concentration: 20%; mill filling ratio: 70%(PDF) EnergyModel and Life CycleModel for Grinding Processes 2010年10月1日 The batch ball mills used in the tests were mild steel (MS) and stainless steel (SS) with MS or SS balls, respectively Slurry was purged by selected gas (CO 2 or N 2) for 5–10 min prior to sealing the mill and grinding to a grinding fineness of P 80 – 75 μm Flotation tests were carried out with an Outokumpu type flotation machine in a 4 L flotation cell equipped with The effect of grinding environment on flotation of sulphide poor PGE oresDrum Length: 11000mm Drum Speed Density of slurry lime: 13–15 0/Bel Capacity: 15–20 M3/h Motor model and Power: Y132S4 55KW Reducer model and speed ratio: XWD61 47 Products Center ZJH mainly focus on producing and supply laboratory and pilot scale type of ore dressing equipment for Mining and Mineral Processing IndustryLime Slaking Drum ZJH minerals
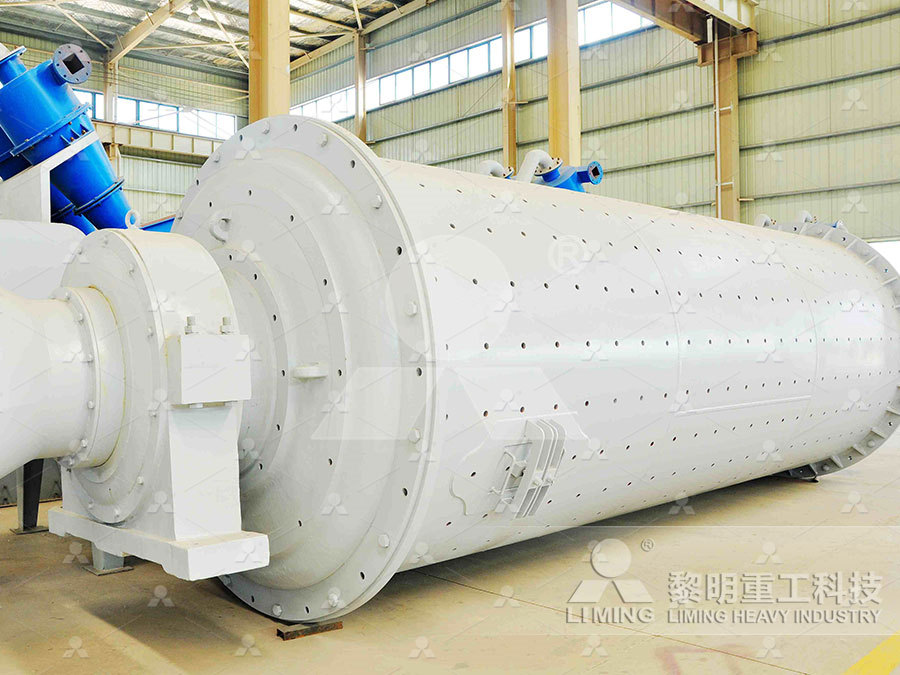
Lime Ball Mill JXSC Machine
2019年12月5日 The lime ball mill can superfinely grind lime or coal ash, consists of feeding part, which increases the contact surface of the ball ore, strengthens the grinding effect, 0075089: 0652: 185: 585: Ф900×3000: 36: 27: ≤20: 0075089: 11 grinding balls of up to 150 mm (6 in) in diameter These actions apply crushing, attrition and abrasion comminution processes to reduce primarycrushed ores down to ballmill sized feed Feed ore with a top size of up to 200 mm (8 in) and water enter the feed end of a SAG mill through a feed chute; the ore is milled in the shell andSemiautogenous grinding (SAG) mill liner design and development2015年6月1日 The use of balls in the grinding of ores is a length of 30 cm with a w all thickness 7, percent solid: 35, grinding time: 6 0 min, mill speed: 75 rpm, ore A and ball type: High steel An investigation of the corrosive wear of steel balls in grinding (2017) [27], proposed a relation for batch dry ball mill grinding as Eq 3 Beeck (1970) [30] proposed Eqs 4 and 5 for industrial dry ball mill grinding based on data collected from dier ent cement plants in Germany and the US, respectively, as Shoji et al [26] proposed for batch dry ball mill grinding with D = 06 m as EqOptimization of Ball Mill Grinding of a Limestone‐Type Brecciated
.jpg)
Estimation of Grinding Time for Desired Particle Size Distribution
sample is calculated The present investigation focuses on utilizing the calculated retention time of the iron ore as a standard grinding reference time to the laboratory ball mill for optimizing the grinding time of each ore The desired P 80 (150 μm) with an acceptable range of hematite liberation (>75%) was obtained in the laboratory ball 2013年4月16日 ABSTRACT In this study, ultrafine grinding of a refractory silver ore tailings was studied A laboratory scale pintype vertical stirred mill and ceramic beads were employed for the grinding testsInvestigation of some parameters affecting the Ultrafine grinding 2 More crushing and less grinding to reduce the feed size into mill The larger feed size, the more work that the ball mill needs to do on the ore To achieve the specified grinding fineness, the workload of ball mill will be increased inevitably, and then, the energy consumption and power consumption will be increased accordingly10 Ways to Improve the Grinding Efficiency of Your Ball Mill2020年1月1日 Application of the proposed method in a 975 × 488 m SAG mill indicated that the liner wear profile along the liner length was nonuniform and the highest wear occurred between 125 m and 275 m The study of the lining layer abrasing wear in the semiautogenous
.jpg)
Overview of Lime Slaking PDF Calcium Mill (Grinding)
Overview of Lime Slaking Free download as PDF File (pdf), Text File (txt) or read online for free The document discusses factors that affect the lime slaking process Lime slaking involves mixing calcium oxide (quicklime) with water to produce calcium hydroxide Key factors include the chemical composition and particle size of the limestone raw material, as well as the 2019年4月16日 for grinding lime stone or ores go up to over 1800 t/h depending on material and target product size In the ore industry, compressive comminution is mainly known fr om high pressure grinding(PDF) LEARNING FROM OTHER INDUSTRIES; WHY THE VRM2013年5月1日 Effect of ball mill grinding parameters of hydrated lime fine several parameters affect the performance of ore grinding the −0074 mm content in the grinding product increased Effect of ball mill grinding parameters of hydrated lime fine grinding Investigation on the particle size and shape of iron ore pellet feed using ball mill and HPGR 909 areas of 500–1600 cm2 g1The concentrate must therefore be reground in order toInvestigation on the particle size and shape of iron ore pellet feed
.jpg)
Effect of ball mill grinding parameters of hydrated lime fine grinding
2013年5月1日 Operational grinding parameters have marginal effect on fineness of particle Real surface area enhancement did not occur on the external surfaces, but in the inner surfaces due to lime hydration process conditions The ball mill load and speed are the most important parameters rather than material charged volume The undersize percentages of 297, 53 and