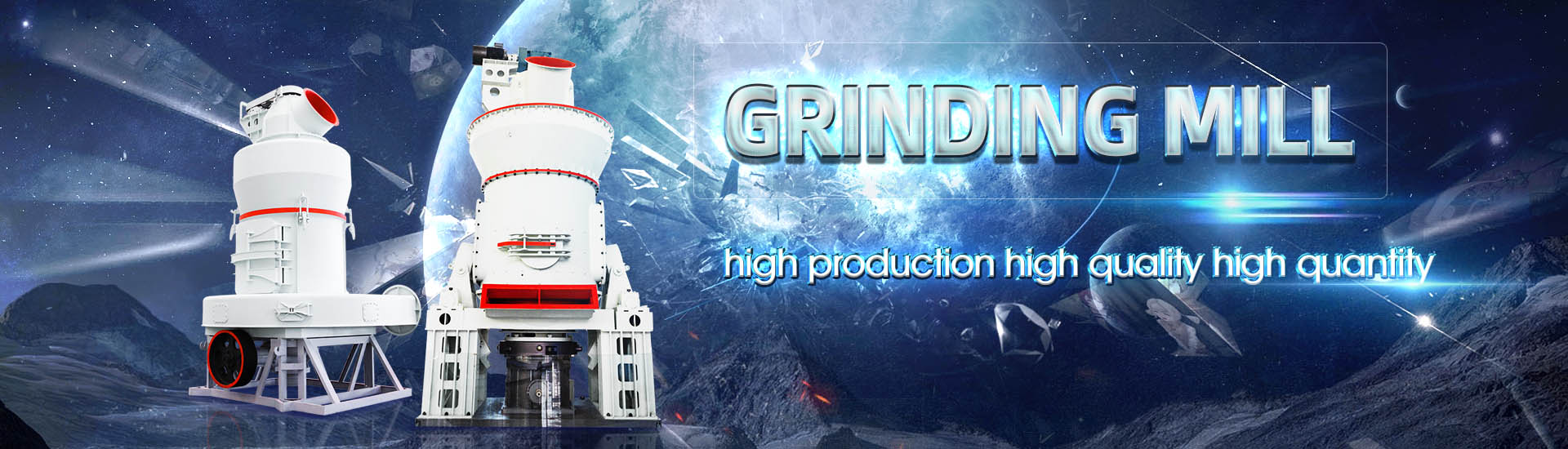
Ore mill rotor sleeve material
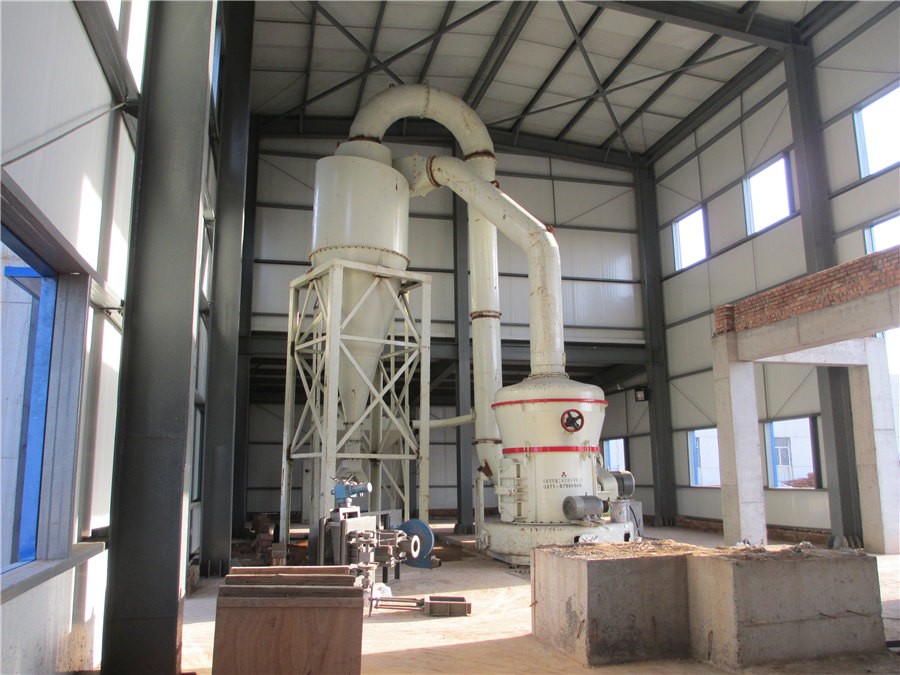
Retaining sleeves for high speed PM rotors: (a) metal sleeve; (b
Typical materials for nonferromagnetic sleeves are Inconel 718 (NiCoCr based alloy) with electric conductivity 08×10 6 S/m (138% ICACS) at 20 o C, titanium alloys, stainless steels, carbonTypical materials for nonferromagnetic sleeves are Inconel 718 (NiCoCr based 登录2022年11月30日 The results show that the design method proposed in this paper can obtain the optimal region of sleeve thickness and interference with the characteristics of a simple solution Optimal design of a rotor sleeve for a surfacemounted high mill rotors are mounted on spherical roller bearings This selfaligning bearing type can compensate for mis alignments of the two plummer block housings, andThe Design of Rolling Bearing Mountings Schaeffler Group
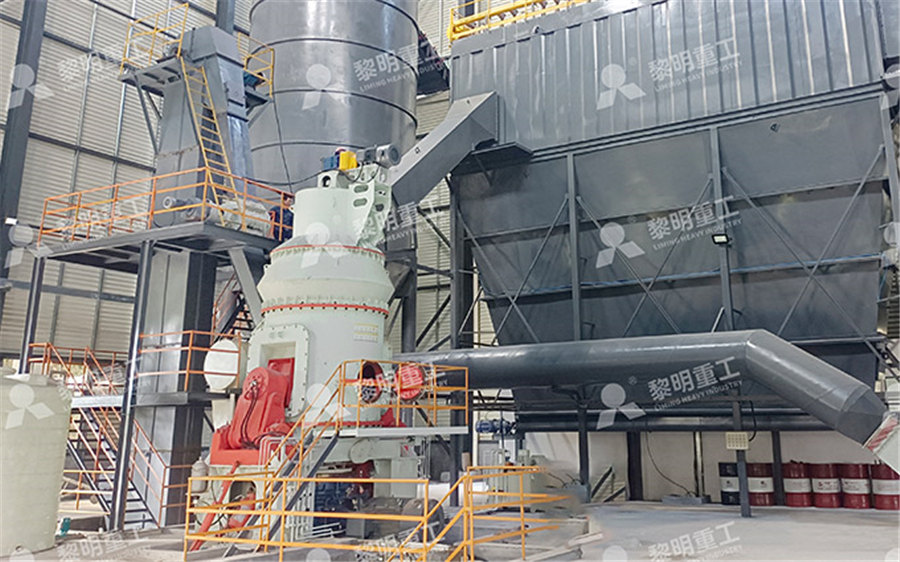
Rotor Design of HighSpeed Permanent Magnet Synchronous
2017年12月25日 This paper describes the rotor design of highspeed permanent magnet (PM) synchronous motors considering rotor magnet and sleeve materials The influence of four 2022年4月20日 In this paper, the starting performance and power generation performance of highspeed PMSG are studied, when the rotor sleeve material is austenitic steel, carbon fiber, Influence of Sleeve Material and Sleeve Composite Structure on 2015年4月23日 In the case of designing highspeed surfacemounted permanent magnet synchronous motor (SPMSM), the rotor retaining sleeve is inserted into the rotor to prevent the Study on the Optimal Rotor Retaining Sleeve Structure for the 2020年7月17日 In this article, the influence of retaining sleeve with different structures and materials on the rotor eddy current loss in highspeed PM motors will be comprehensively Analysis and Experiment Method of Influence of Retaining Sleeve
.jpg)
Optimal design of a rotor sleeve for a surfacemounted high
2022年11月30日 To design the rotor sleeve of an SHPMM, it is necessary to first establish the analytical solution of rotor strength [911]2015年4月17日 This paper is concerned with the design of a rotor retaining sleeve for a 112MW 18kr/min PM machine; its electromagnetic performance is investigated by the 2D finite Rotor Retaining Sleeve Design for a 112MW HighSpeed PM AC Motor Rotors in Detail •Overview/Objectives: o Rotor Material and Construction Options o Rotor Components in Detail o Rotor Shaft and Endplate Details o Motor Bearing Types and UsesAC Motor Rotors in Detail NEMAFeed material: mediumhard, brittle: Size reduction principle: impact: Material feed size* 25 mm: Final fineness* 100 µm: Speed at 50 Hz (60 Hz) 2000 4000 min1 (in steps of 200 min1) Speed setting: Yes: Rotor peripheral speed: 155 Cross Beater Mill SK 300 RETSCH adjustable speed
.jpg)
The Simple Facts about Sampling Gold Ores Progradex
13TH AUSIMM MILL OPERATORS’ CONFERENCE / PERTH, WA, 10–12 OCTOBER 2016 1 The Simple Facts about Sampling Gold Ores G J Lyman1, I G Robertson2 and T Day3 ABSTRACT Various approaches are used in the industry for establishing procedures (sample mass estimation and method of subsampling) for sampling and analysis of gold ores2022年11月30日 rotor core/sleeve are P 1/ 2, in this case, the stress on the surface of the sleeve, permanent magnet, and the rotor core is shown in Figs 24, respectively As shown in Fig 2, the force on the inner surface is the uniform contact pressure P 2, while Ror Rim Rom Ris Ros Rotor core Sleeve Permanent magnet Fig 1 Rotor structure of the Optimal design of a rotor sleeve for a surfacemounted high SAG MILL TESTING AN OVERVIEW OF THE TEST PROCEDURES AVAILABLE TO CHARACTERIZE ORE GRINDABILITY AUTHOR: FO VERRET, G CHIASSON AND A MCKEN SGS KEYWORDS Comminution, grindability, grinding, SAG mill, AG mill, milling, HPGR, work index, pilot plant INTRODUCTION The resistance of ore samples to breakage (or hardness) is SAG Mill Testing Test Procedures to Characterize Ore GrindabilityDouble Rotor Hammer Mill (DHM) The DHM ensures best delamination results of complex compound materials and cleaning of mixed metals UMScustomer around the world value the exceptional performance processing e g shredder residuals, Escrap (WEEE), populated and unpopulated boards, aluminumcopper radiators, aluminum scrap, Nonferrous composites, UMS GmbH Double Rotor Hammer Mill (DHM)
.jpg)
LUMSeries Ultra Fine Vertical Grinding MillKefid Machinery
PERFORMANCE Features: 1As the grinding principle of material layer, materials stay in the mainframe for a very short time , thus decrease repeat grinding ,so the percentage of Iron is little When it grind white or transparent material , the whiteness and purity of the finished product is higher, which ball mill cannot reachmaterial sleeves, as metallic material sleeves do not have enough strength and cannot apply the required pretension TABLE 2: PROPERTIES OF METALLIC SLEEVE MATERIALS Sleeve Material Carbon steel Hastelloy 14571 Hastelloy C4 Tensile strength MPa 280 – 1,900 ~ 600 ~ 700 Density g/cm3 78 798 864Composite materials in high efficient sleeve applications of electric on the mill and ranges from 10 to 15 mm Material which is larger than this must first undergo preliminary size reduction For the coarse and prelimi – Rotor Beater Mill SR 300 14 – Technical data 15 – Order data 16 Cross Beater Mills – Size reduction with Rotor Mills McCrone2016年6月6日 Mill Internals As with rod and ball mills liner designs for autogenous and semiautogenous mills have been in a state of flux for a number of years Operators continually search for optimum designs Each mill application and each liner material coupled with varying mill diameters will produce a different internal wear patternSAG Mill Liner Design 911Metallurgist
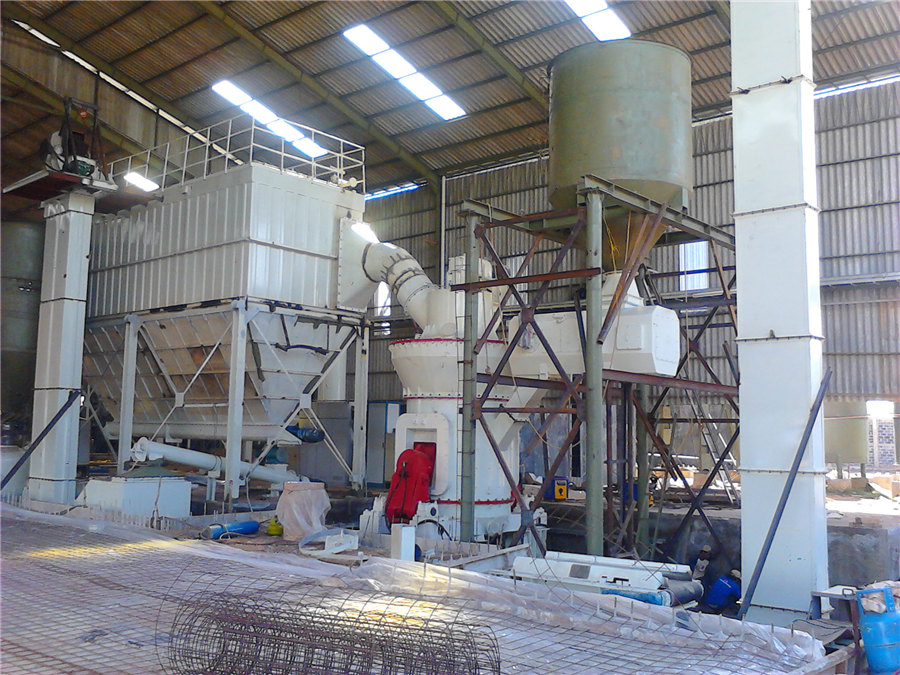
Rotor Strength Analysis of FeCoBased Permanent Magnet High
2022年6月9日 HSPMM has excellent performance of high power density, small volume, and high efficiency, and its rotor strength has always been an important problem restricting its development [1,2]When the highspeed motor is running, all parts of the rotor are subjected to huge centrifugal force, so the surface mounted permanent magnet rotor structure with rotor The grate arrangement is perpendicular to the rotor’s movement direction The protruding part in the middle of the grate bars forms the gap between the grate bars, which expands downward and tilts toward the rotor’s rotation direction Hammer Mill Parts Wear Parts For Industry Qiming 2023年6月22日 Research on Rotor Sleeve Winding Techniques for HighSpeed Permanent Magnet Motors via NOL Ring Testing(PDF) Research on Rotor Sleeve Winding Techniques Request PDF On Mar 15, 2015, Mathis Reichert and others published Research of iron ore grinding in a verticalrollermill Find, read and cite all the research you need on ResearchGateResearch of iron ore grinding in a verticalrollermill
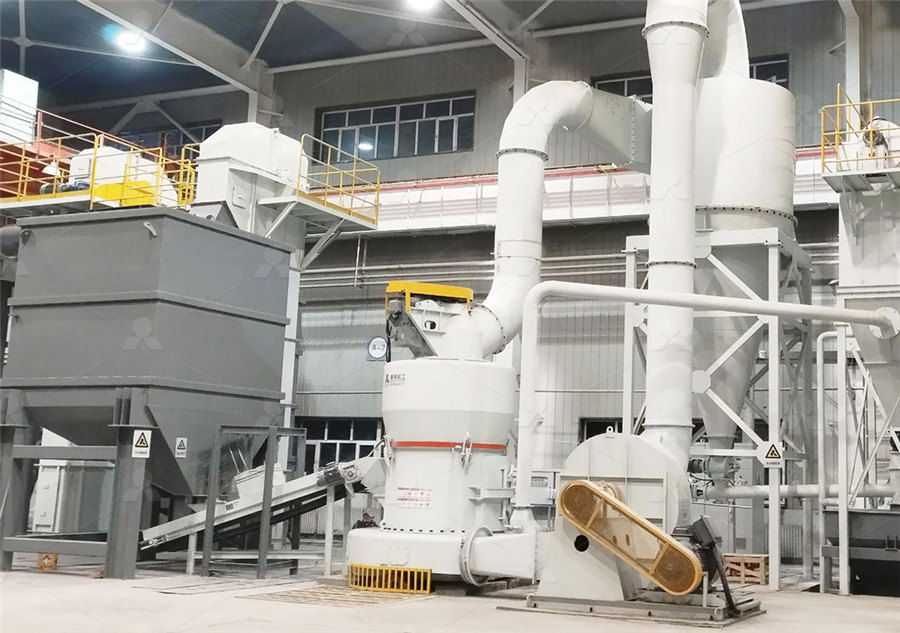
Design and Analysis of Rotor Assembly of Hammer Mill Machine
2021年4月3日 The role of rotor impact mill screen plate design in biomass grinding has attracted limited interest This study aimed to clarify the effect of operational parameters and various screen designs on 2017年7月26日 We will consider an ore with a ball mill work index varying between 16 and 13, feeding into a single stage ball mill operation with one million kilowatts per day consumed power For the particular mill configuration, a performance graph, Fig (21), has been constructed according to Bond’s methodsHow Ball Mill Ore Feed Size Affects Tonnage Capacity– Cyclone Mill TWISTER 10 – Technical data 11 – Order data 12 Rotor Beater Mills – Applications 13 – Rotor Beater Mill SR 200 14 – Rotor Beater Mill SR 300 14 – Technical data 15 – Order data 16 Cross Beater Mills – Applications 17 – Cross Beater Mill SK 100 18 – Technical data 19 – Order data 20 Ultra Centrifugal MillsSize reduction with Rotor MillsThe rod mill is another type of grinding mill used in the copper ore mining process This machine uses steel rods as the grinding media instead of balls, which are commonly used in ball mills The rods grind the ore by tumbling within the mill, similar to the action of a rotating drumUnderstanding the SAG Mill in Copper Ore Mining Process
.jpg)
Size reduction with Rotor Mills Lab Unlimited
on the mill and ranges from 10 to 15 mm Material which is larger than this must first undergo preliminary size reduction For the coarse and prelimi – Rotor Beater Mill SR 300 14 – Technical data 15 – Order data 16 Cross Beater Mills – 2013年2月1日 A systematic study on the comminution of a soft (coal) and a hard (iron ore) material is carried out to investigate the bulk comminution features of the hammer mill The effect of the feed rate and the rotor speed on the mill efficiency in terms of reduction ratio, energy expenditure, fines produced and median size is minution features in an impact hammer mill ScienceDirectmaterial sleeves, as metallic material sleeves do not have enough strength and cannot apply the required pretension TABLE 2: PROPERTIES OF METALLIC SLEEVE MATERIALS Sleeve Material Carbon steel Hastelloy 14571 Hastelloy C4 Tensile strength MPa 280 – 1,900 ~ 600 ~ 700 Density g/cm3 78 798 864Composite materials in high efficient sleeve applications of electric Compositebased rotor sleeves are particularly suitable for contributing to all of these development goals Stabilizing the rotor at high rotational speeds in terms of strength and radial elongation with composite rotor sleeves enables tighter air gaps between rotor and stator and reduces eddy current losses compared to metal reinforcementsAZL Joint Partner Project Rotor Sleeves for Electric Motors
.jpg)
CERAMIC MATERIALS I
a)Single rotor to 15:1 b)Double rotor to 15:1 c)Hammer mill to 20:1 Speciality crushers a)Rod mill b)Ball mill The reduction ratio is defined as the representative feed size by representative product size The sizes are usually defined as the 80% passing size of the cumulative size distributionThe FRITSCH VariableSpeed Rotor Mill classic line comminutes soft to mediumhard material displaying linearelastic or elastoplastic material behaviour After embrittlement even viscoelastic material can be comminuted Due to brief duration times of the sample in the grinding chamber even temperature sensitive material can be comminutedThe significance of drive power for the efficiency of the Variable 2016年2月26日 In the impacthammermill, a crosssectional view of which is shown here on the left, the process is, in one important respect, a reversal of that just described The material enters the machine on the uprunning side of the rotor, where it is struck by the hammers as they start their sweep across the upper part of the housingHammer Mill Crusher Grinder 911MetallurgistDownload scientific diagram Main material properties of the rotor sleeve from publication: Research on Stress Design and Manufacture of the FiberReinforced Composite Sleeve for the Rotor of Main material properties of the rotor sleeve
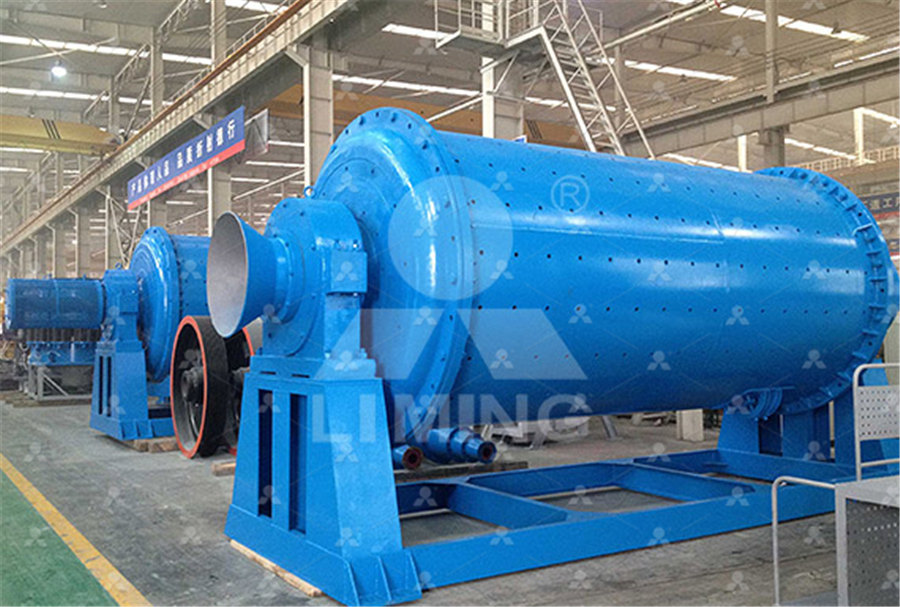
Ore Sampling Methods: Good Proper 911Metallurgist
2017年2月21日 For finegrinding machines, the coffeemill type still successfully holds its own against most of the newer devices, although the modern samplegrinder is much heavier, better built, and more easily cleaned than its predecessors The first mechanical samplers were imitations of Cornish quartering, the ” whistlepipe ” being the most common mill and a pin mill in SMD The Archimedes’ screw was found to be an effective mixer due to strong convective axial transport of the media by the screw agitator and strong diffusive radial mixing (Cleary et al, 2006) This assists with rapid distribution of feed material throughout the mill body The radial pins were found to have very Energy efficient rotor design for HIGmills Swiss Tower Mills Filament winding technology provides an extreme pretensioning of the rotor magnets in radial direction which leads to extraordinary thin sleeve material Low clearance between rotor and stator combined with the transparency of composite materials for the magnetic field in combination with the high mechanical properties and noncorrosive Composite Rotor Sleeves for Electric Machines AECwhen the rotor sleeve material is austenitic steel, carbon fiber, copperiron alloy or rotor stainless steel outer layer coated with copper The machine model with different sleeve materials are established by using the finite element method, and the influence of the sleeve material electromagnetic characteristics on the highspeed PMSMInfluence of Sleeve Material and Sleeve Composite Structure on
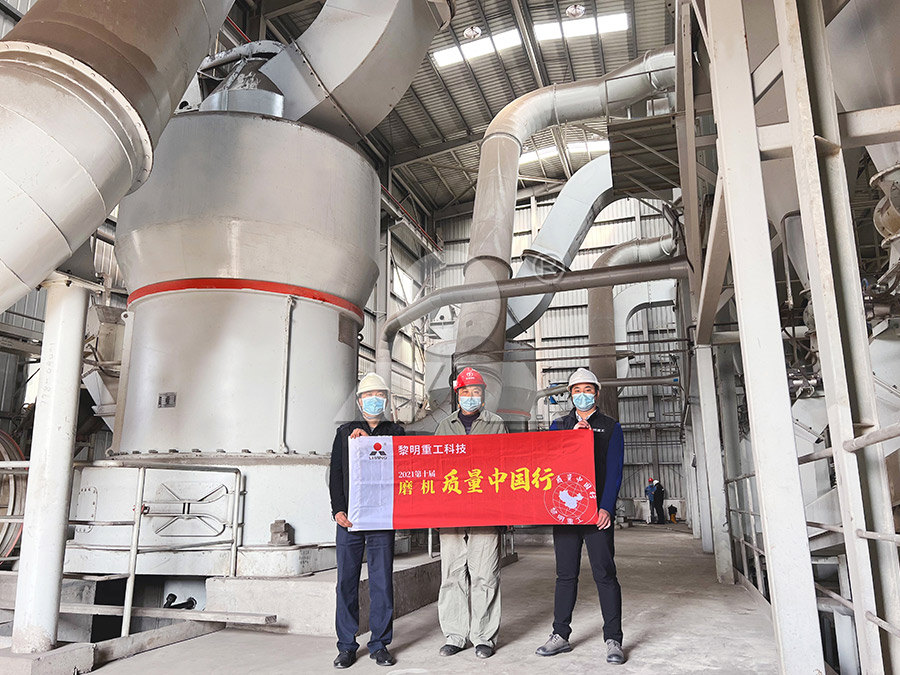
How to operate an air classifier mill to meet your fine grinding goals
finer, depending on the material An air classifier mill applies impact grinding and air classification in one step The mill uses airflow to convey feed material to the mill’s grinding chamber, classifies the material into fine and coarse fractions, recirculates the coarse fraction for further grinding, and conveys fine particles outImpact mill rotor >Wear resistant, hardened impact plates >Easily cleaned surfaces Impact milling stator >Excellent wear resistance >Optimum tooth geometry Impact mill funnel >Easy feeding of bulk material > o n i dprott eatcentgr e I against reaching in and splashing > Ey al si eclaned The dry mill IKA® Pilotina MI is the foremost option forPilotina – The universal 2 in 1 mill for dry products APEX 2019年8月1日 Mill, material, and process parameters The stirred media mill vary in their rotortype and their grinding media separation devices Effect of using different grinding media on the flotation of a base metal sulphide ore Miner Eng, 126 (2018), pp 2427Mill, material, and process parameters ScienceDirect2016年6月3日 The principal method of grinding in a Tower mill is attrition (scrubbing of particles off material being ground), with the possibility of some shearing and 911 Metallurgist is a trusted resource for practical insights, solutions, and support in mineral processing engineering, helping industry professionals succeed with proven expertise Tower Mill Operating Work IndexTower Mill Operating Work Index 911Metallurgist
.jpg)
Metal Sleeve at Best Price in India India Business Directory
En1020431 Mill Test Certificate Diameter As per requirement Grade Grade 1, Grade 2, Grade 5 (Ti6Al4V) Sleeve Material Metal read more RS Engineers Rotor Sleeve and Magnetic Sleeve ₹ 100/ Piece Get Latest Price Material SS 304 Usage/ApplicationRing amp; Puck mill that accommodates sample sizes ranging from 2 100 grams Ideal for pulverizing dry, brittle samples and slurry grinding Typical samples include: Cements, Soils, Ceramics, Slag, Rocks, Minerals, Ores, Pharmaceuticals, Sulfur Pellets, Dried Plant MaterialRotor mill 8500 ShatterBox® SPEX SamplePrep MedicalExpo2017年12月25日 In highspeed permanent magnet synchronous generator (PMSG), the rotor design should not only ensure mechanical stability at high speeds but also ensure the required electromagnetic (EM) performanceRotor Design of HighSpeed Permanent Magnet Synchronous rail is arranged on the rotor sleeve When the rotor rotates, the wheels are driving around the smooth guide rail It is like a planetary wheel structure The wheels are like asteroid wheels 3 ELECTROMAGNETIC DESIGN OF MBMWT‐MCPMM 31 Stator block rule Based on the electrical symmetry and mechanical symmetry ofElectromagnetic design and thermal analysis of module combined
.jpg)
Design and Analysis of Rotor Assembly of Hammer Mill Machine
The project deals with the Manufacturing with Design and Analysis of Hammer Mill Machine and Rotor Assembly (as in rock ore), material that will not go out between the screen bars is dropped into the iron pocket and is later removed 21 Hammer Mill Features Material is reduced by impact from freeswinging bar hammers Finished