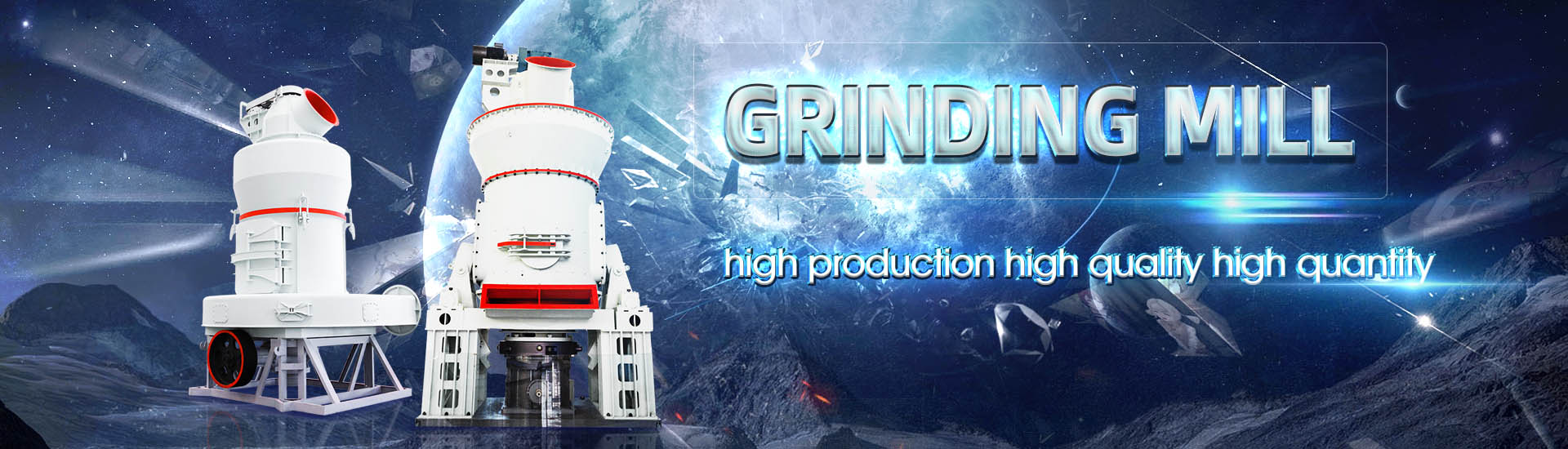
Where can I buy pulverized coal machine system
.jpg)
Coal Crushers Coal Pulverizers Mills Williams Crusher
Coal is crushed to desired fineness between spheres or cylindrical rollers After that, air from the boiler is heated to around 330°C (650°F) The raw coal is then fed into the pulverizer where it is ground into fine coal particles 展开From our original E/EL ballandrace type pulverizers for lower capacity applications, to the latest BW Roll Wheel™ pulverizer capable of grinding up to 230,000 pounds of coal per hour Reliable Coal Pulverizers and Mills » Babcock WilcoxOur Pulverized Coal Preparation Production Line is composed of Raw Coal Storage Transportation System, Grinding System, Dust Collecting System, Electrical Instrument Pulverized Coal Preparation Pulverized Coal Grinding Plant Coal MHI group offers a full lineup of pulverizer / mill systems from small to high capacity Pulverizers (coal pulverizer) are used to pulverize pieces of coal into fine particles (100μm) before placing Boilers machinery : Coal Pulverizer Mitsubishi Heavy Industries, Ltd
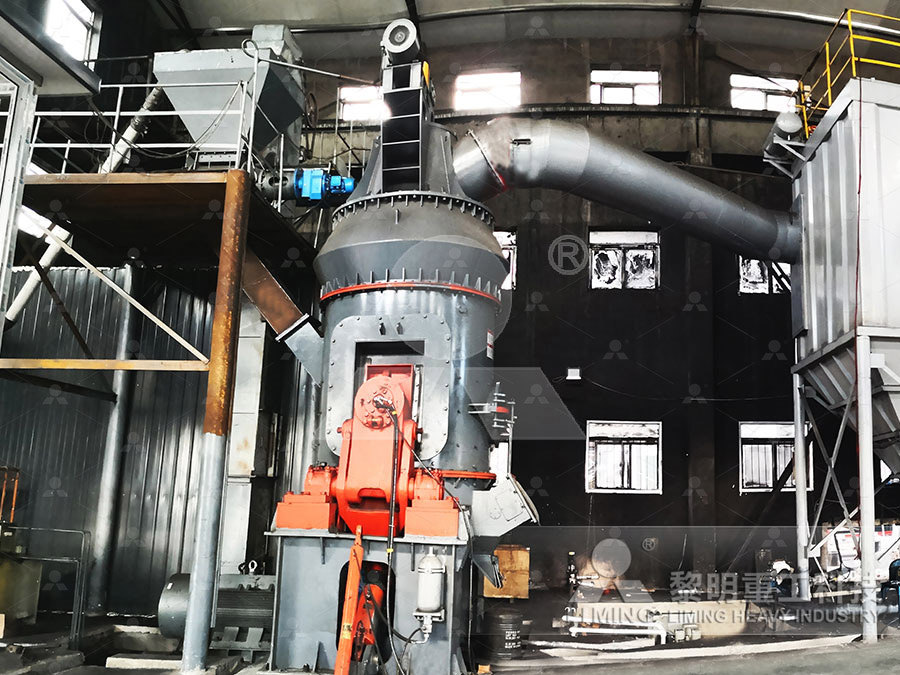
Coal Pulverizer – Power Plant Pall Corporation
Pulverization of coal is currently the favored method of preparing coal for burning Mechanically pulverizing coal into a fine powder enables it to be burned like a gas, thus allowing more A verticaltype pulverizer bites into coal between a rotating table and roller to pulverize the coal through the action of crushing and grinding Mitsubishi Power offers a varied lineup from small Pulverizers Mitsubishi PowerMechanically pulverizing coal into a fine powder enables it to be burned like a gas, thus allowing more efficient combustion Transported by an air or an air/gas mixture, pulverized coal can be Coal PulverizerPulverized Coal Injection (PCI) using the denseflow method The Küttner developed and perfected denseflow method offers several advantages over a lowerdensity system Higher Pulverized coal injection (PCI) Iron Steel Kuettner Group
CFB石灰石脱硫剂制备96.jpg)
Pulverized Coal Injection Systems Danieli Corus
High rates of pulverized coal injection reduce the required amount of expensive metallurgical coke Drawing upon experience gained during the installation of over 65 PCI systems started We’re a world leader in coal pulverizing and boiler mill operations for horizontal and vertical boiler mills—committed to highefficiency performance, reduced maintenance costs, and longer time Boiler Mill and Coal Pulverizer Performance GE Steam PowerCoal injection system Reduced pollution Coal grinding and injection systems are nonpolluting systems Injecting pulverized coal into a blast furnace reduces the overall pollution made by coke production Increased productivity Installation of a coal injection system can increase productivity through improved operation of the blast furnacePulverized Coal Injection Ammermannthe burnout of the coal Combustion of coal produces the heat required as well as various solid residues and gaseous pollutants such as ash, SO2 and NOx During combustion, coal particles undergo the following four welldefined steps (as illustrated in Figure 1): coal particle drying, and then heatingup to the pyrolysis reaction temperature;Fundamentals of pulverised coal combustion ICSC
.jpg)
Bulk Coal Delivery Center Farms Coal
Whether you’re looking for a new way to start to heat your entire home, or searching for a supplement to the system you already have – look to anthracite coal It’s convenient It’s costeffective It’s clean And if you’re considering Pulverized coal can be used as a reducing agent by injecting it through the tuyeres Coke has been replaced up to 250 kg/THM with pulverized coal [26] Coals for PCI are usually cheaper noncoking thermal coals Important properties of the coals are: • content of volatiles and moisture • chemical composition (S, P, alkalis, ash) •Pulverised Coal an overview ScienceDirect Topics2022年11月27日 In a pulverized coal system, the coal is ground into a fine powder using grinding mills, then blown into the furnace, where it is burned This allows for more efficient and complete combustion of the coal, which can improve the overall efficiency of the power plantAdvantages and Disadvantages of Pulverized Coal FiringIndustry trends which could increase the probability of fires and explosions in coal pulverizing systems are: l The increased use of coal by utilities which have no prior pulverized coal experience 2 The increased use of lower rank, higher volatile content coals 3Fire and Explosion Prevention in Coal Pulverizing Systems
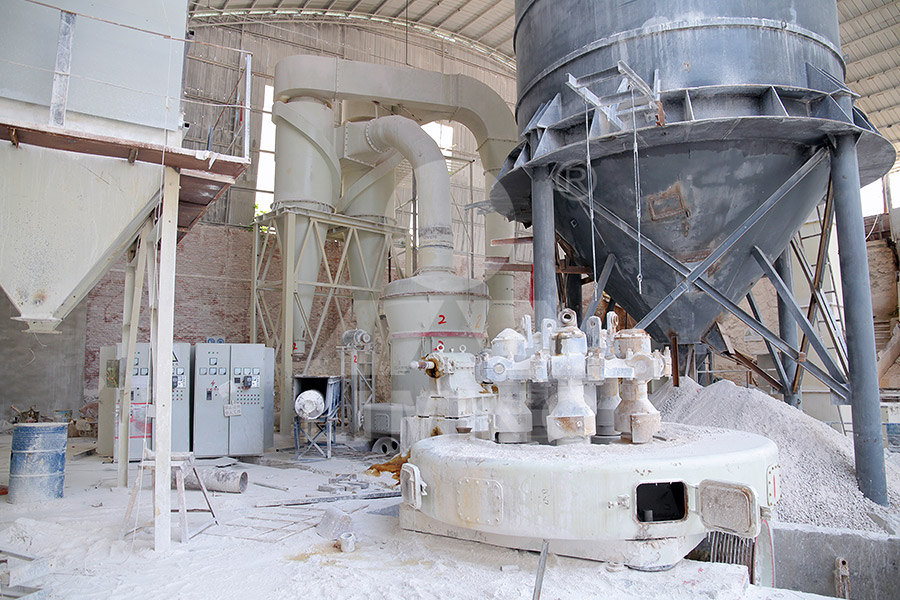
Pulverized Coal Burner JXSC Machine
Pulverized coal burner is a new kiln heating equipment with many advantages such as high heat utilization rate, energy saving environmental protection It is suitable for various annealing furnaces, metal heating furnaces, quenching furnaces, melting furnaces, forging furnaces, and other related heating furnaces The coal burner fits the coal burning system of the middle and 2024年1月11日 With a vertical roller mill (VRM) VRMs consist of a rotating table or bowl and rollers 1 To grind the coal, feed raw or initially crushed coal into the mill which is then ground between the rotating components; 2 Finally, hot air removes moisture, carries the pulverized coal out, and a classifier segregates the particles; Here is all you need to know about the VRM:How to Process Coal into Pulverized Coal in 5 Steps?Gas turbine combined cycle Shigehiro Shiozaki, Akira Yamada, in Advances in Power Boilers, 2021 637 Gasifier facilities 6371 Coal pulverizing and feeding system The purpose of the coal drying system is drying and grinding the raw coal for stable transportation of pulverized coal to gasifier and stable/highefficiency gasification at the gasifierCoal Pulverizers an overview ScienceDirect Topics1996年12月4日 Coalfired boiler systems will continue to be major contributors in the future New pulverized coalfired systems routinelyinstalled today generate power at net thermal cycle efficienciesranging Technology Development for Advanced Pulverized CoalFired
.jpg)
WorldProven Coal Pulverizer Technology Debuts in the US
of 11,380 Btu/lb The coal's ultimate analysis is shown in Figure 1 The original fuel system consisted of three springloaded, MB type, vertical spindle mills, each gravimetric belt feeder, seal air fan, 1800 rpm primary air fan, and four mill outlets supplying pulverized coal to one of the three horizontal rows of (4) dualfuel burnersA pulverized coalfired boiler is an industrial or utility boiler that generates thermal energy by burning pulverized coal (also known as powdered coal or coal dust since it is as fine as face powder in cosmetic makeup) that is blown into the firebox The basic idea of a firing system using pulverised fuel is to use the whole volume of the furnace for the combustion of solid fuelsPulverized coalfired boiler WikipediaDanieli Corus supplies tailormade solutions for the global steel industry Using proven, proprietary technology, we help our clients achieve maximum performance Our solutions contribute to maximum performance with respect to reliability and economic benefits for Blast Furnace Ironmaking and BOF Steelmaking operationsPulverized Coal Injection Systems Danieli Corus2015年10月19日 The paper presents experimental and numerical investigation of pulverized coal combustion process analysis and optimization The research was conducted on the frontfired pulverized coal boiler with dedicated lowNOx furnace installation In order to find optimal boiler operating conditions the acoustic gas temperature measurement system and mass flow A Combustion Process Optimization and Numerical Analysis for
.jpg)
Performance enhancement of a solarassisted pulverized coal
2023年12月1日 Some academics have made significant contributions to optimizing the behavior of SPCP systems Bame et al [2] identified the optimal integration configuration of an SPCP system with a low solar energy sourceZhai et al [27] applied the genetic algorithm to optimize the area of the solar trough collectorWu et al [28] optimized the solar field layout and the flow Features and Benefits 1Efficient Handling: Pulverized coal screw conveyors help maintain a consistent and reliable flow of coal, which is crucial for the efficient operation of combustion systems 2Dust Control: Properly designed screw conveyors can help minimize dust emissions during the transport of pulverized coal 3Without causing segregation or degradation: The Pulverized Coal Screw Conveyor Dahan Conveyor Manufacturer2018年10月21日 Fig 1 Pulverized coal combustion and gas composition in raceway The extent of combustion (combustion efficiency), and hence the amount of unburnt material transported out of the raceway, depends on several parameters which include (i) properties of the coal, such as the VM content, particle size and density, and (ii) operating conditions, for example, blast gas Understanding Pulverized Coal Injection in Blast Furnace2022年10月27日 Abstract— The article presents an original electrical ignition technology based on intensifying the electrochemical and ionization processes in the zone where the electrical discharge influences a pulverized coal mixture The experience gained from applying this technology at operating power facilities is described During the electrical ignition system’s A Pulverized Coal Fuel Electrical Ignition System and Its
.jpg)
Calculation Method of Pulverized Coal Mass Flow Into Coal and
2019年1月1日 For coal and gas dualfired boiler, pulverized coal mass flow and gas volume flow into furnace are important criteria for boiler operation adjustment, and they are important input parameters for Fig 1 Pulverized coal injection station III INITIAL CONSIDERATIONS P The pulverized coal injection vessel can be modelled as if it were a pressurised tank where the principles of mass conservation and ideal gas law can be used However, neither the vessel nor the four control valves have a linear behaviour easy to be modelledAdvanced Dynamic Models for a Pulverized Coal Injection Plant2018年6月1日 This paper presents an online measurement system for pulverizedcoal concentration based on the method of ultrasonic attenuation in the gassolid two phase flow(PDF) Online Measurement System of PulverizedCoal through the millis the mass of pulverized coal in the grinding zone, kg; B sz is the mass flow of pulverized rejects, kg s1; k c is the conversion coefficient of raw coal to pulverized coal, %; Both raw coal and pulverized coal coexist in the grinding Optimization of the pulverized system of the coalfired power
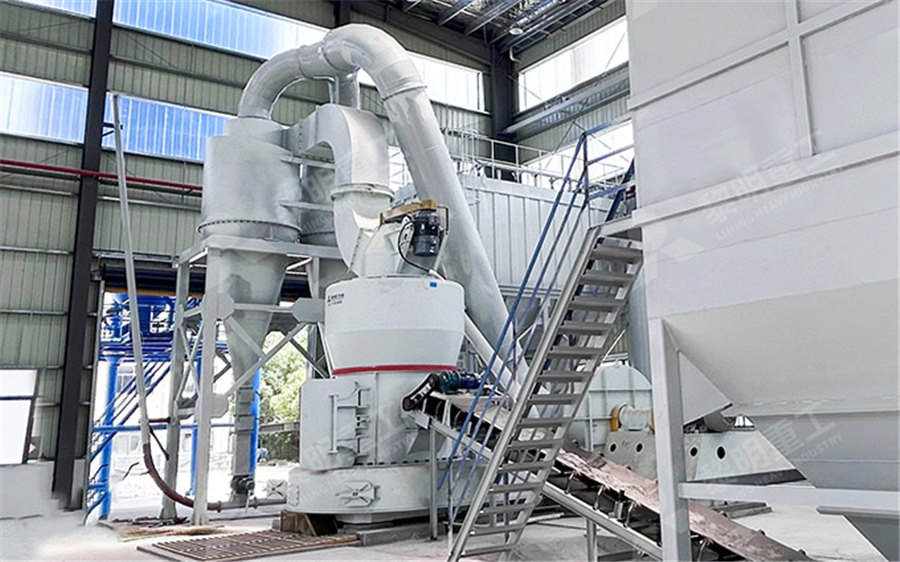
Schematic diagram of the pulverized coal combustion furnace
In order to obtain better flame image characteristics, they developed a series of detection systems for 2D flame measurement based on the pulverized coal and ash concentration in the flame [4 2012年2月24日 The solidfuel firing method can't handle load fluctuations well It's also not stable enough for large thermal power plants The flue gases have a lot of ash, making it hard to separate from the exhaust So, nonpulverized coal firing isn't practical for large boilers The main drawback is that itPulverized Fuel Firing of Boiler Electrical4U2014年11月14日 It then discusses live storage in vertical bunkers or silos The document also covers different types of stoker firing systems used to burn coal, including travelling grate stokers and spreader stokers Finally, it summarizes pulverized coal firing and the unit and central systems used to grind, dry and feed pulverized coal to boiler furnacesCoal and ash handling systems PPT Free Download SlideShare2012年3月27日 The results are reported of an energy analysis of a biomass/coal cofiring based power generation system, carried out to investigate the impacts of biomass cofiring on system performance The power generation system is a typical pulverized coalfired steam cycle unit, in which four biomass fuels (rice husk, pine sawdust, chicken litter, and refuse derived fuel) and Energy Analysis of a Biomass Cofiring Based Pulverized Coal
.jpg)
Understanding pulverised coal, biomass and waste combustion –
2015年1月5日 A comprehensive and up‐to‐date review of major coal combustion aspects such as oxy‐fuel combustion, co‐combustion of coal and biomass, emissions from pulverized coal furnaces, numerical Pulverized Coal Injection Systems Market size was USD 4355 million in 2024 and market is probable USD 5606 million by 2032, exhibiting a CAGR of 430% Home; Industries Buy Now Buy Now Buy Now Pulverized Coal Injection Systems Market Request For FREE Sample PDF Pulverized Coal Injection Systems Market Size, Share Report年7月8日 Pulverized coal firing: Stoker firing: 1 Coal is to be supplied in powder form to furnace 2 Powder form of coal burns like a gas 3 It can be used for large capacity more than 100 MW) power plantPulverized Coal System Advantages and Disadvantages2021年11月4日 Test methods for grindability and abrasion testing: Full scale ring and ball mill, Hardgrove mill [30,31], BCURAroll mill, Rotating electrode ball wear tester [32], Dropweight test machine [28 Technique to Investigate Pulverizing and Abrasive Performance of Coals
.jpg)
of Coals in Mineral Processing Systems
impacting machines, eg, hammer and beater mills [2] Energies 2021, 14, x FOR PEER REVIEW 3 of 16 ) LB 5 :/áéáMáZá6áß ;, (1) # LB 6 :)á$ ; (2) where G is the coal grindability within the specified system, M means the mechanical properties of the coal, é is the coal porosity, q determines the hard particles mechanicalFiring system of a frontal pulverized coalfired boiler The general scheme of analysed boiler with lowNOx furnace system is depicted in Figure 1 The lowNOx combustion system is characterized by air and fuel staging The pulverized coal supplies boiler by 12 swirl lowNOx burners (burner level I and II) dividedCoal combustion modelling pulverized coalfired boilerMachine learning (ML) and deep learning (DL) have become increasingly important in various fields due to their ability to analyze large amounts of data and extract patterns and insights that can The schematic process flow of pulverized coal power plant2022年1月26日 Pulverized coal particle velocity [m/s] and erosion of the channel [kg/m 2 s], M1, coal 3 +1 Input data used for calculations for all six dust ducts for each subsequent millNumerical Study of the Erosion Process and Transport of Pulverized Coal
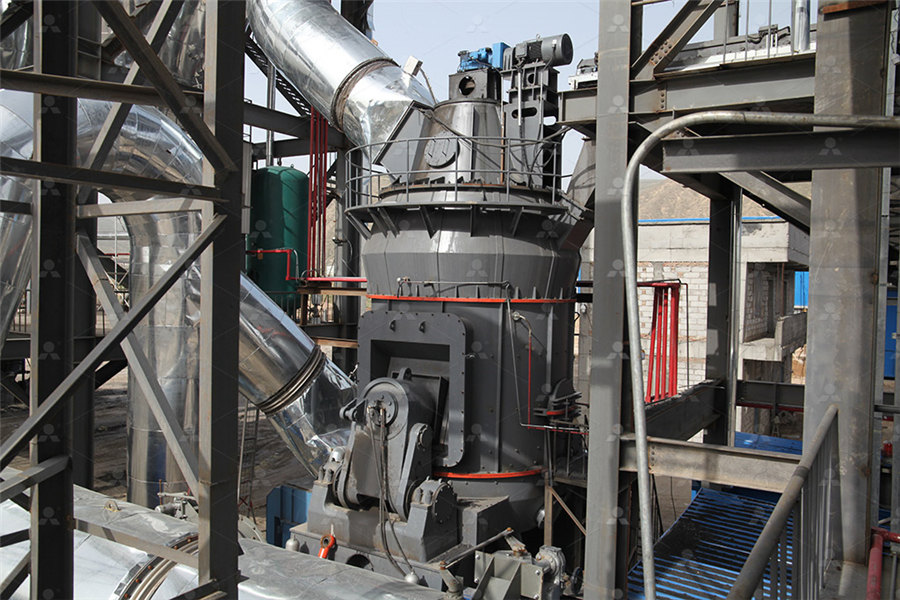
Plasma Ignition System to Start Up Pulverized Coal Boilers
2022年9月1日 Plasma Ignition System to Start Up Pulverized Coal Boilers: Experimental Simulation and FullScale Test September 2022; Journal of Engineering Thermophysics 31(3):375383;2019年2月14日 The aim of present paper is to review various aspects of pulverized coal combustion such as oxyfuel combustion, cocombustion of coal and biomass, emissions from pulverized coal furnaces, ash formation and deposition, and carbon capture and sequestration (CCS) technologies to outline the progress made in these aspectsA complete review based on various aspects of pulverized coal Recent improvements to the coal storage and feeding system and the distributor have further stabilized the system’s feed rates, which in turn has further stabilized the system’s injection rates Highest sustained injection rates over 200 kg/thm, reducing the consumption of metallurgical coke to as low as 300 kg/thmProducts › Ironmaking and steelmaking › Pulverized Coal NEW TECHNOLOGIES OF PULVERIZED COAL COMBUSTION PARTIAL REPLACEMENT OF COAL1 A N Alekhnovich2 Translated from Élektricheskie Stantsii, No 10, October 2021, pp2–7DOI: 1034831 EP2021108310001 In case of pulverized coal combustion, reduction in CO 2 emissions in commonly used technologies isNEW TECHNOLOGIES OF PULVERIZED COAL COMBUSTION
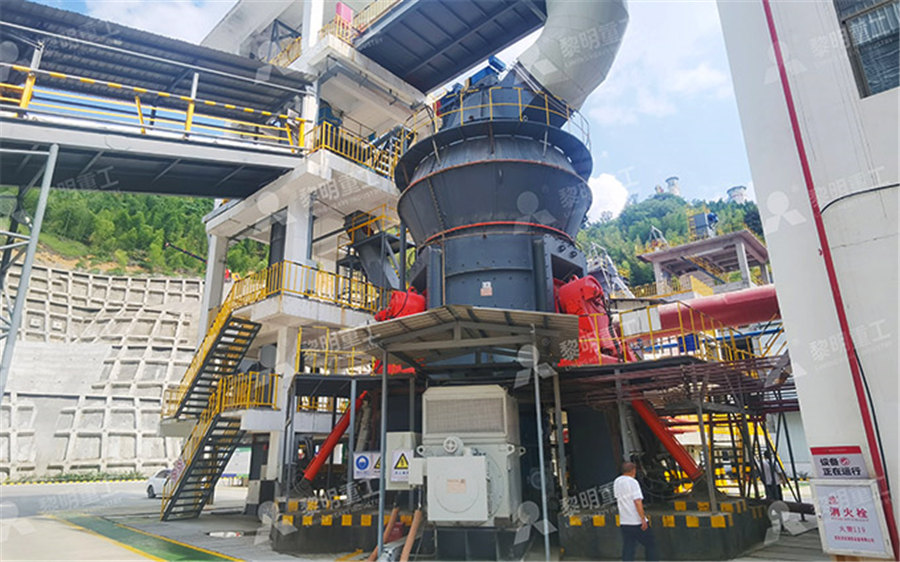
Coal Preparation Systems for Boilers Springer
of coal preparation systems Pulverized coal (PC) firing is the dominant method used in modem power sta tions So, most of this chapter will focus on coal preparation systems for PC boilers and their design Fluidized bed (FB) firing is developing very quickly and find ing its way to wider applications in largescale commercial boilers