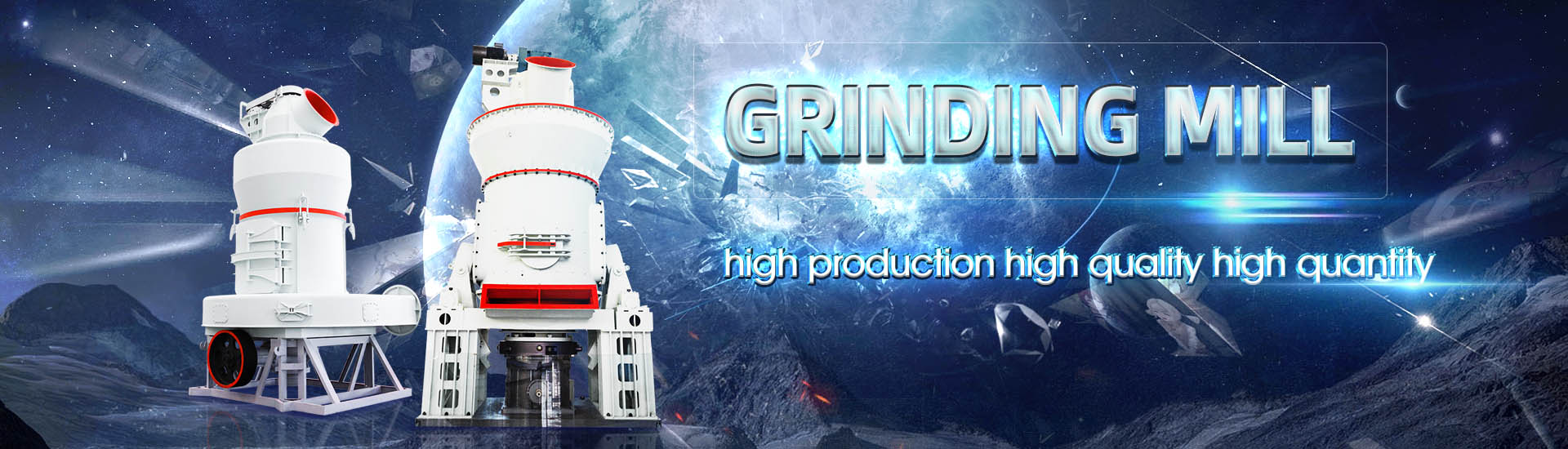
The principle of anthracite lignite grinding mill
.jpg)
The Effects of BallMill Grinding Parameters on Lignite
2023年9月9日 This study aims to investigate the variations in the morphology of lignite samples under different grinding conditions such as grinding time and powder/grinding media ratio (U) The results of these analyses showed that Thus, the MPS coal grinding mill with a high drying capacity is very suitable for grinding lignite with feed moistures of as much as 45 % Depending on this high feed moisture the mill rating Reprint from ZKG 3 Gebr Pfeiffer2003年3月1日 This paper presents the experimental results on the Hardgrove and Bond grindabilities of the Hungarian lignite and its isolated textural components It is shown that for Selective grindability of lignites and their application for producing 2017年9月1日 We investigated whether the vertical roller mill can be efficiently used in the beneficiation of lowgrade magnesite and whether it can improve upon the separation indices [PDF] Fine grinding: How mill type affects particle shape
.jpg)
Research on the grinding characteristics of lignite based on
2022年9月30日 Aiming to explore the limitation of Hardgrove Grindability Index (HGI) and broken behavior of lignite, coal samples were ground for different minutes in the Hardgrove 2021年8月12日 The most important factors in ball milling pretreatment of lignocellulosic biomass are the type of feedstock, chemical concentration, the rotational speed of pots, grinding time, Ball milling as an important pretreatment technique in The principle of application of compressive force on a layer of particles instead of individual particles causes tremendous changes in the shape of particles and the concept of grinding Grinding Mill an overview ScienceDirect Topics2014年1月1日 Two mill systems are employed for most coal grinding applications in the cement industry These are, on the one hand, vertical roller mills (VRM) that have achieved a share of (PDF) MPS mills for coal grinding ResearchGate
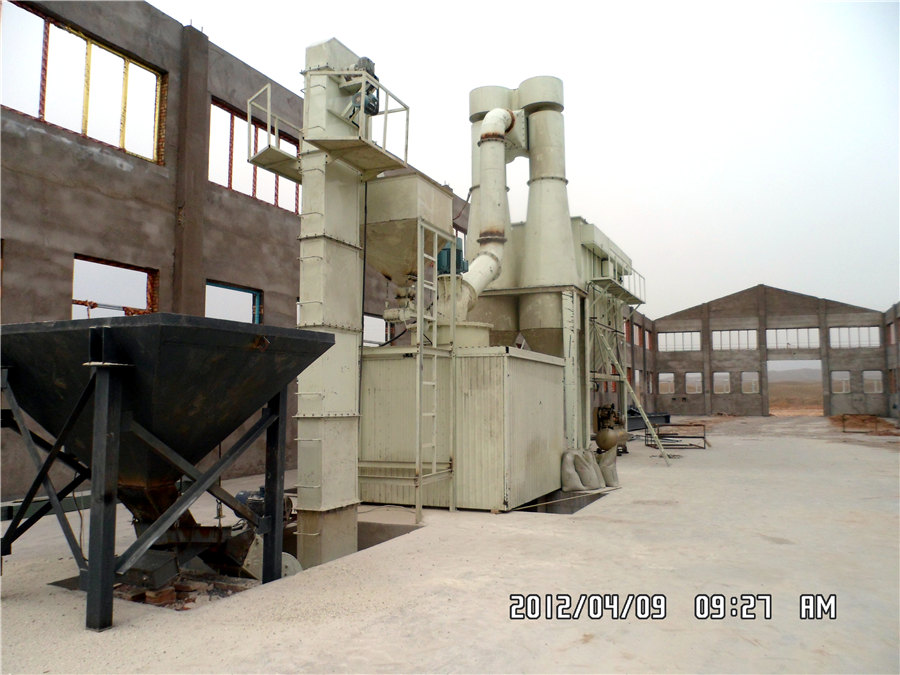
COAL GRINDING IMPS: more than meets the eye Gebr Pfeiffer
Gebr Pfeiffer SE (GPSE) describes its vertical roller mills for coal grinding and provides a case study of an MPS225BK installed at CBR’s Lixhe cement works in BelgiumGrinding principle The feed material is ground in a Loesche roller grinding mill, between the rotating grinding table and the individually guided grinding rollers The compressive force Loesche Grinding Technology for the Power IndustryR Roller Mill Xiao Xiao1, Huang Lilong2 and Xu Kuangdi3 1Changsha Research Institute of Mining and Metallurgy, Changsha, China 2Changsha Research Institute of Mining and Metallurgy, Changsha, China 3Chinese Academy of Engineering, Beijing, China Roller mill is a type of grinding equipment for crushing materials by pressure between two orRoller Mill Springer2019年10月17日 In this post, we're going to learn more about rod mill We'll cover it from two aspects: 1 Working principle 2 Structure Let's dive right in! 1 Working Principle of Rod Mill Rod mill is a common equipment for grinding The Working Principle and Structure of Rod Mill
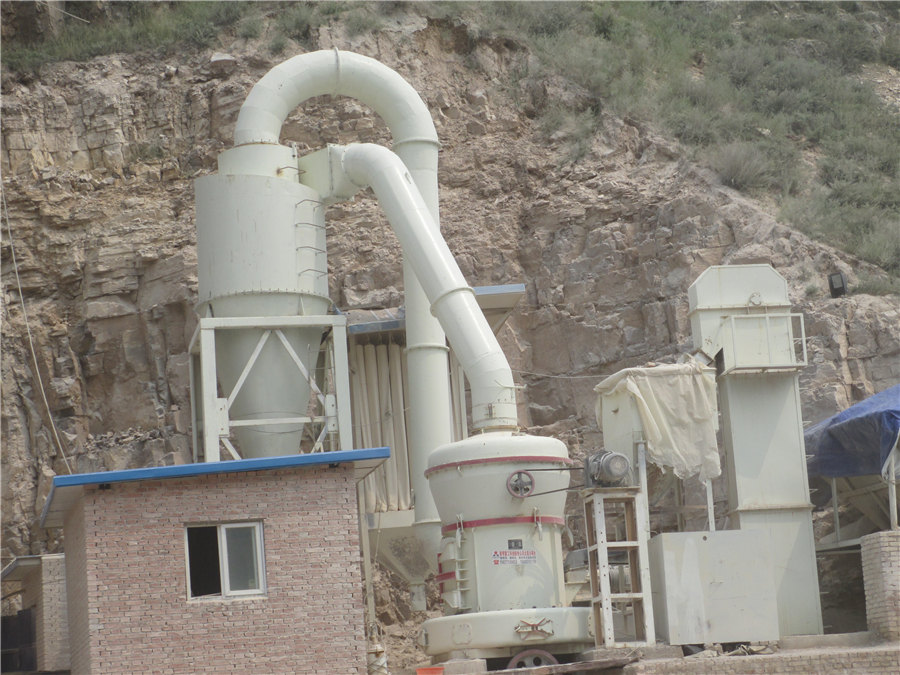
Grinding Machine: Definition, Parts, Working
2021年5月5日 Grinding Machine Working Principle: In brief, we can say the working of the Grinding Machine is the Workpiece is fed against the rotating abrasive wheel The action of rubbing or friction generates between wok price 2024年5月15日 The working principle of the grinding mill【EVERGRINDING】 The sander is an efficient, fine grinding equipment Working principle: The highspeed rotating rotor structure is driven by the motor to impact the grinding medium zirconia beads and materials at a very high linear speed In this process, the grinding medium carries out fine grinding of the material The working principle of the grinding mill【EVERGRINDING】Working principle and characteristics of vertical mill Working principle The working principle of a vertical mill involves the rotation of a grinding table with rollers attached to it Raw materials are fed into the table and ground between the rollers and table The ground materials are then blown by hot air through an outlet in the mill's Working principle and characteristics of vertical mill2023年3月15日 Energy Efficiency: Advances in grinding mill technology have led to the development of energyefficient machines that can perform the same tasks with lower energy consumption, minimizing costs and environmental impact Conclusion Grinding mills have come a long way since their humble beginnings as primitive toolsThe Evolution and Importance of Grinding Mills in Modern Industry
.jpg)
Grinding Mill an overview ScienceDirect Topics
Grinding Mills Barry A Wills, James A Finch FRSC, FCIM, PEng, in Wills' Mineral Processing Technology (Eighth Edition), 2016 71 Introduction Grinding is the last stage in the comminution process where particles are reduced in size by a combination of impact and abrasion, either dry, or more commonly, in suspension in waterUnderstanding the operational principles and factors that influence mill performance is crucial for optimizing mill operations and achieving the desired particle size for downstream processes By considering these factors, mining companies can enhance the productivity and costeffectiveness of their grinding mill operationsUnderstanding the operation of grinding mills in the mining and 2022年10月17日 Low speed: At low speed, the mass of balls will slide or roll up one over another and will not produce a significant amount of size reduction High Speed: At highspeed balls are thrown to the cylinder wall due to centrifugal force and no grinding will occur Normal speed: At Normal speed balls are carried almost to the top of the mill and then fall into a Ball Mill; Principle, Working, and Construction » PharmagudduThe principle objective for controlling grinding mill operation is to produce a product having an acceptable and constant size distribution at optimum cost To achieve this objective an attempt is made to stabilize the operation by principally controlling the process variablesGrinding Mill an overview ScienceDirect Topics
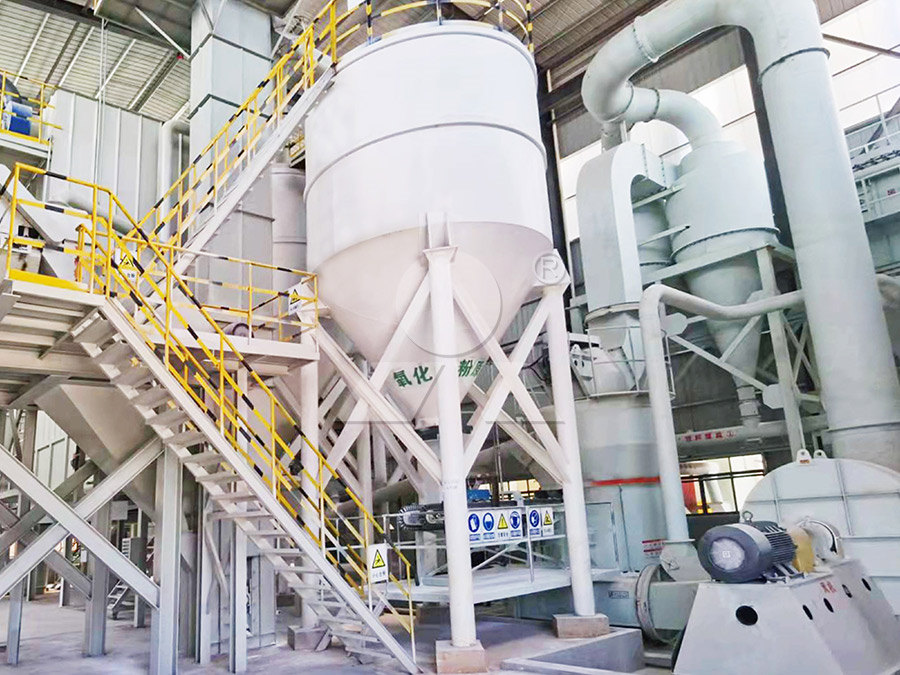
VRM In Cement Plant Maximize Energy Saving CNBMSINOMA
Low grinding power consumption, system power consumption is reduced by 20% The air leakage coefficient of the mill is low, the safety is strong, and the O2 content of the fan is less than 8% by using the exhaust gas from the kiln tail Wide range of applications, bituminous coal, anthracite, lignite, petroleum coke, and so on Free InquiryA vertical roller mill, also known as a vertical grinding mill or vertical mill, is a comprehensive grinding equipment integrating crushing, drying, grinding, grading, and conveying Vertical grinding mills can be widely used in electric power, Energysaving and Efficient Vertical Roller Mill Fote 2012年6月1日 As the cylinder starts to rotate, the grinding balls inside the cylinder crush and grind the feed material, generating mechanical energy that aids in breaking bonds, activating the catalyst, and Grinding in Ball Mills: Modeling and Process Control2020年10月9日 This method simulates the particles size, mill power, and qualified particles quality of crushed particle, which reveal the grinding strength and energy consumption of the SAG mill In this paper Operation Analysis of a SAG Mill under Different Conditions Based on
.jpg)
Grinding Mills — Types, Working Principle Applications
2018年8月17日 Extreme temperatures, impact velocity, mill load, grinding media, ore types, and applications are some of the factors to be considered while installing new linersIt could be used to grind bituminite, meagre coal, and anthracite lignite with high moisture under some conditions Vertical mill adopts low speed, big roller diameter, high loading force design It has the widest adaptability to coal types and variation in coal properties, big grinding surface ability, low rolling resistance, low energy consumption, stable output, etcVertical mill for coal pulverizing in power plant Geckointech2023年9月9日 The average roughness (Ra) values of particles increased from 609 nm to 1079 nm upon increasing the grinding time from 2 min to 16 min Due to these findings, it can be suggested that lignite samples became rounder with increasing grinding times, and roughness analyses made in a 10 × 10 μm surface area with an Atomic Force Microscope (AFM) The Effects of BallMill Grinding Parameters on Lignite 2023年9月9日 The average roughness (Ra) values of particles increased from 609 nm to 1079 nm upon increasing the grinding time from 2 min to 16 min Due to these findings, it can be suggested that lignite The Effects of BallMill Grinding Parameters on Lignite Morphology
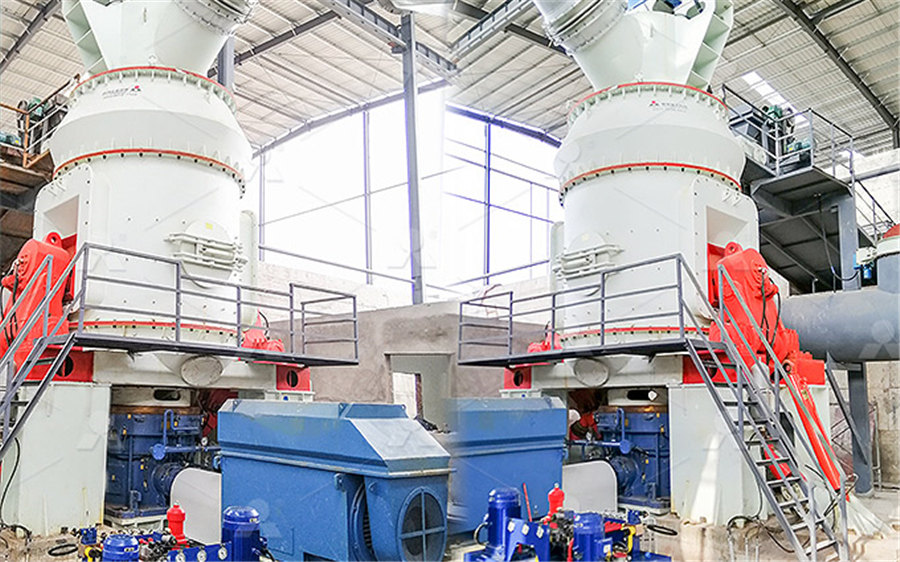
Reprint from ZKG 3 Gebr Pfeiffer
So far, the biggest mill for lignite coal grinding will be delivered to Cemindo’s Bayah plant in Indonesia This MPS 4500 BK has been ordered for grinding lignite with a maximum moisture of 37% and it is able to produce a throughput rate of minimum 100 t/h at a residue of 15% R009 mm The installed power for the mill main drive is 1300 kWRead this indepth blog to learn about the working principle of Vertical Grinding Mill, its application, and its advantages +91 226796 9655 sales@macawberindia 130131, Hindustan Kohinoor Complex, LBS Road, Vertical Grinding Mill: How it Works, Application And 2023年10月31日 The determined specific surface area of lignite, coking coal, and anthracite [21] Figures available via license: Creative Commons Attribution 40 International Content may be subject to copyrightRemoval of Pyridine from Aqueous Solutions Using Lignite, 2015年12月15日 DOI: 101016/JFUEL201509028 Corpus ID: ; Effects of different drying methods on the grinding characteristics of Ximeng lignite @article{Zhu2015EffectsOD, title={Effects of different drying methods on the grinding characteristics of Ximeng lignite}, author={JieFeng Zhu and Jianzhong Liu and Junhong Wu and Jun Cheng and Zhihua Wang Effects of different drying methods on the grinding characteristics
.jpg)
The Working Principle and Types of Grinding Revealed
The principle of grinding precision machining: Grinding is an abrasive precision machining method that uses a lapping tool and abrasive to grind off a thin layer of metal from the surface of the workpiece based on fine machining Define grinding: Grinding is a unit operation that reduces solid matter into smaller particles Define grinding process:2011年2月1日 Download Citation A comparison of the results obtained from grinding in a stirred media mill lignite coal samples treated with microwave and untreated samples Various studies have been carried A comparison of the results obtained from grinding in a stirred 2013年1月1日 Principles of Modern Grinding Technology explains the principles that led to rapid improvements in modern grinding technology over recent decades Removal rates and quality standards have (PDF) Principles of Modern Grinding Technology ResearchGate2023年8月12日 The structure and working principle of the grinding head of wheat flour machine The wheat flour mill, commonly known as the grinding head, is the core component of the flour machine The wheat flour mill is responsible for grinding wheat and other grains and plays a key role in the quality and output of flour So what is its structure like?The structure and working principle of the grinding head of
.jpg)
A comparison of the results obtained from grinding in a stirred
2011年2月1日 It was found that as a result of microwave treatment of lignite coals with 850 W for 12 min and 600 W for 23 min in microwave oven, inherent structural moisture may be removed completely from lignite coals Grinding tests were carried out in stirred media mill for 5, 15, and 30 s of grinding period in order to determine the specific rate of 2023年9月9日 The average roughness (Ra) values of particles increased from 609 nm to 1079 nm upon increasing the grinding time from 2 min to 16 min Due to these findings, it can be suggested that lignite samples became rounder with increasing grinding times, and roughness analyses made in a 10 × 10 μm surface area with an Atomic Force Microscope (AFM) The Effects of BallMill Grinding Parameters on Lignite Morphology2023年8月29日 A typical sand mill comprises a cylindrical vessel filled with grinding media, a rotating shaft, and an electric motor The vessel, usually made of stainless steel or wearresistant materials, houses the grinding media The rotating shaft, powered by the electric motor, drives the grinding media to move within the vesselSand Mill: Enhancing the Efficiency of Grinding DispersionCOMPARISON OF GRINDING MILLS TYPE OF MILL MEDIA SIZE RPM TIP SPEED (fpm) Ball Mill 1/2” and larger 1050 Attritor 1/8” to 3/8” 75450 6001000 Sand Mill/Horizontal mill 1/64” to 1/8” 8001200 20003000 HSA Attritor 1mm 3mm 4001800 26002700We will discuss the principle of the Attritor and its applications
.jpg)
Research on the grinding characteristics of lignite based on grinding
2022年9月30日 Mark Duffy produced a complete set of grinding data on a pilotscale tower mill Here these data are analyzed in terms of grinding kinetics The results show that the data can be fitted with a 2023年1月16日 The objective of this research is to design and construct a hammer mill for grinding leonardite charcoal (Lignite, class J) The conditions for the design and construction of the grinder are Optimum Design of Hammer Mill for Grinding Leonardite2021年1月22日 To investigate the effects of grinding media shapes on the grinding kinetics of ball mill cement clinker, the grinding effects with ϕ20 mm balls and ϕ20 × 20 mm cylinders on six different size An innovative approach for determining the grinding media 2011年2月1日 It was found that as a result of microwave treatment of lignite coals with 850 W for 12 min and 600 W for 23 min in microwave oven, inherent structural moisture may be removed completely from lignite coals Grinding tests were carried out in stirred media mill for 5, 15, and 30 s of grinding period in order to determine the specific rate of A comparison of the results obtained from grinding in a stirred
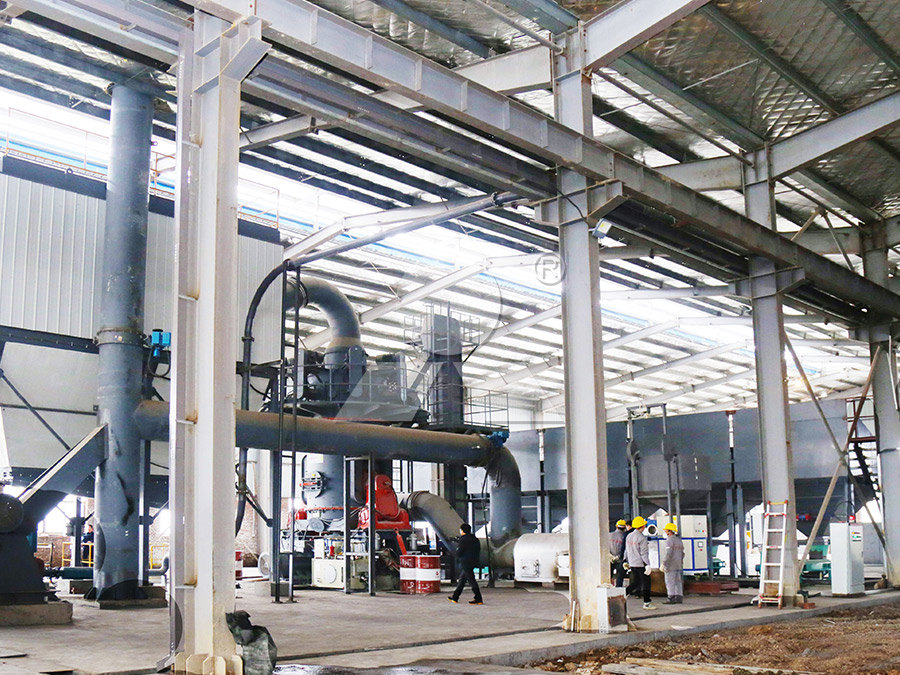
Loesche Grinding Technology for the Power Industry
as centre of excellence for coal and biomass mill application in the power utility industry 2002 Coal grinding plant (LM 232 D) for grinding wood pellets for power stations 1992 Central coal grinding plant (LM 263 D) for the production of lignite (brown) coal dust 1985 Delivery of first selfinerting coal grinding plantThe attritor mill offers many advantages over traditional grinding mills and is widely used in various industries such as ceramics, chemicals, food, and pharmaceuticals In this article, we will delve into the workings of the attritor mill, its advantages, and applications What is an Attritor Mill? An attritor mill, also known as a stirred ball mill, is a type of milling equipment used for What is The Working Principle of Attritor Mill? ball mills supplierAttrition Mill Grinding of Refractories John E Becker UNION PROCESS, INC Akron, Ohio Ceram Eng Sci Proc, 16[1] 11526 (1995) The principles and applications of wet and dry grinding refractory materials in the Attritor, a highenergy stirred ball Attrition Mill Grinding of Refractories Union Process2017年11月7日 Part 1 video global technology Structure and principle of operation Limestone Grinding Mill: Crushers may be used to reduce the size, or change the formStructure and principle of operation Part 1 Limestone Grinding Mill