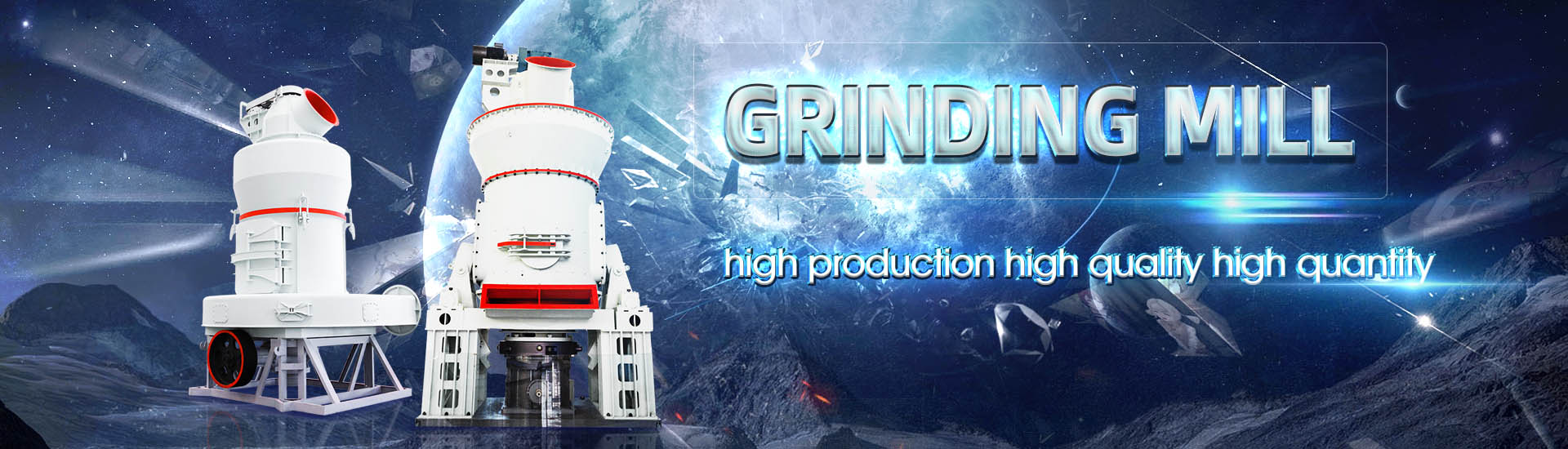
Wet material alumina iron oxide alumina iron grinding mill
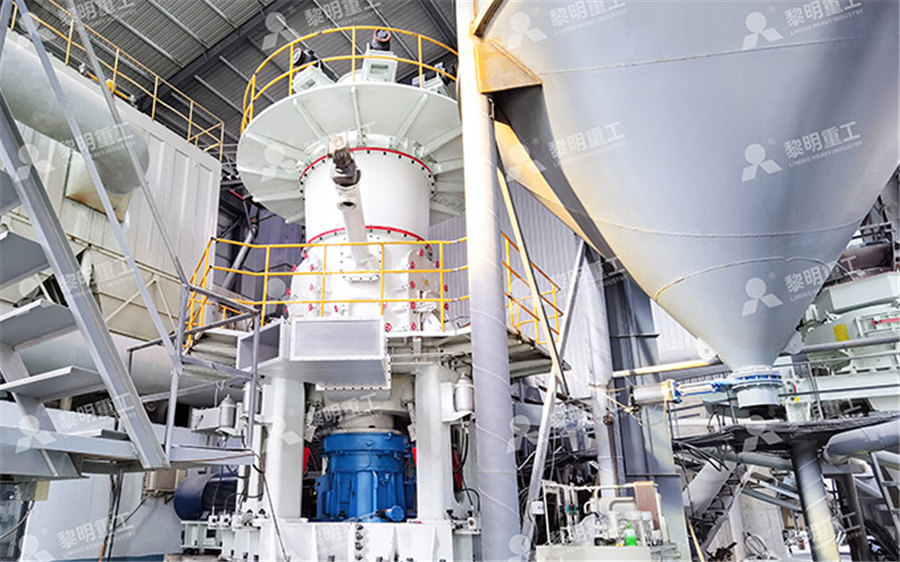
(PDF) High reactive nano zerovalent iron produced via wet milling
In this paper, high specific surface area zerovalent Fe (0) nanoparticles with unusual morphology and high reductive activity were prepared using a chemical reductive reaction of iron chloride 2023年12月1日 Powder synthesis, spark plasma sintering, microstructure and mechanical properties The aim is to prepare Fe–Al 2 O 3 ceramicmatrix composites with a high Fe Ironalumina composites: From discrete iron particles to 2006年4月1日 Highly stable Fe/Al2O3 nanocomposite, which was Fe nanoparticles coated with a thin shell of alumina, has been successfully fabricated by a simple wet chemistry procedure Highly stable aluminacoated iron nanocomposites synthesized by GNPGraystar’s Alumina Grinding Media is high grade milling media produced by isostatic pressing and fired at high temperature These feature high hardness, high density, low wear TECHNICAL DATA SHEET Alumina Grinding Media
CFB石灰石脱硫剂制备96.jpg)
Synthesis and characterization of ironalumina composites as
2022年11月1日 Three iron oxide doped alumina composites containing different weight percentages of iron (10–30%) were synthesized as novel photocatalysts Structural Finally, nZVI can also be produced by wet milling of conventional iron powder In the latter case, stable dispersions of iron nanoparticles in an aqueous solution with an average size of 100 nm Improvements in nanoscale zerovalent iron production by milling The planetary ball mill is promising in that it makes grinding to submicron sizes possible by imparting high energy to the ground powder In this context, there is a need to under stand Modeling and Simulation of Ultrafine Grinding of Alumina in a introducing an abrasive material such as fine alumina powder during the milling process As the amount of the introduced alumina was increased, a progressive shattering of the flakes was High reactive nano zerovalent iron produced via wet milling
.jpg)
Optimization of pelletization process for iron ore with high alumina
around 1015% and with pellet porosity of 3235%At basicity of range of 0405 it is found that the silicate phase distribution throughout the pellet is homogeneous and the silicate phases cover the2024年9月10日 Limestone provides the necessary calcium oxide (lime) that reacts with other materials during the Cement manufacturing process Notably, the Limestone used in Cement should not contain free Silica Clay and shale Cement Manufacturing Process: Know Extraction, High reactive nano zerovalent iron produced via wet milling through abrasion by alumina This method is based on the reduction of iron oxide nanoparticles milling process has been previously reported [33] In that study, tungsten carbide vials were used and no hard abrasive material such as alumina was introduced In this case, the (PDF) High reactive nano zerovalent iron produced via wet Maheshwari® A 999 aluminum oxide beads have a very Alumina grinding ball of high alumina content is an ideal ball mill grinding media as it can improve grinding efficiency without contaminating the product Highdensity alumina grinding ball, being noncorrosive and economical, is ideal for both, wet and dry milling Alumina brick Alumina Grinding Media Balls India Business Directory
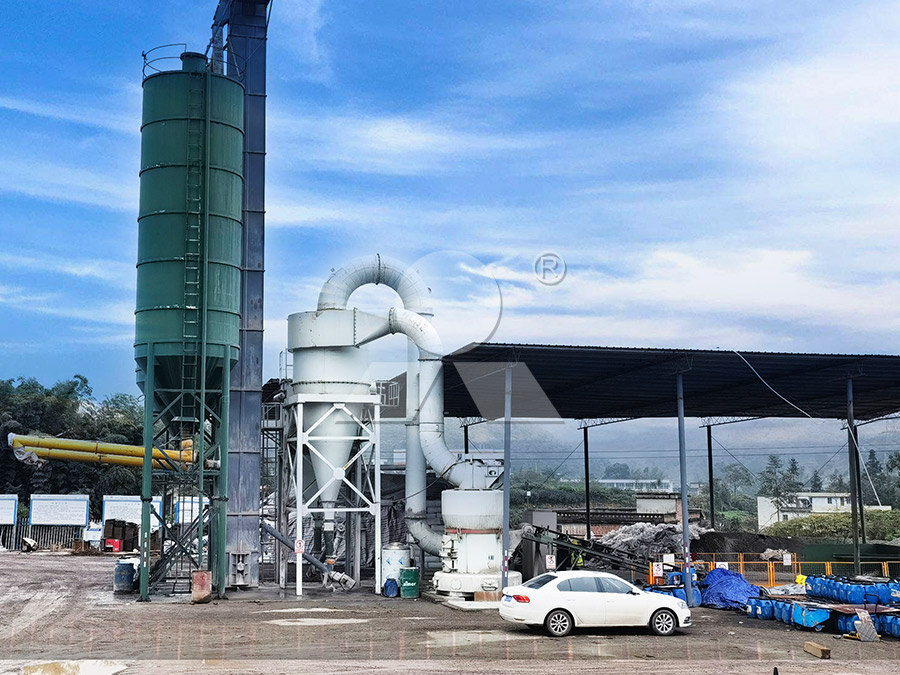
A comparison of wear rates of ball mill grinding media
2016年1月1日 One of the most popular milling machines is the cement mill, which is used to crush raw materials such as lime, silicate, alumina and iron oxide using grinding balls [3]Other grinding ball like alumina grinding ball itroduced : 1: 92% Medium alumina grinding ball series : A) Al2O3 : 92% B) Mosh hardness: 8 grade C) Color : white or brown 2: 75% Medium alumina grinding ball series : A) Al2O3 : 75% B) Mosh hardness: 8 grade C) Bulk density ≥ 315 g/cm3 D) Color : white or brown 3: 60% Medium alumina grinding Wear Resistant 92% 95% Alumina Ceramic Grinding Balls Price 2021年6月16日 Aluminum and aluminum alloys are among the most used metals in fabrication,construction, and in the creation of good all around you It is such a useful and versatile metal, but there are some special considerations you need to make when working with it We have put together this expert guide to fabricating, grinding, and finishing aluminum to Ultimate Guide – Aluminum Fabrication, Grinding Empire 2010年7月1日 According to [2], cast iron with major composition of 95% elemental iron is used to manufacture local cornmill plates The paramount drawback of this material, however, is its susceptibility to Corrosion of Cast Iron Mill Plates in Wet Grinding ResearchGate
.jpg)
Ultimate Guide to Aluminum Oxide Grinding Wheels RUISHI
2024年2月20日 A: You can purchase aluminum oxide grinding wheels online or at your local hardware store They are commonly found in the abrasive tools section or grinding accessories department Q: Can aluminum oxide grinding wheels be used on a bench grinder? A: Yes, aluminum oxide grinding wheels are compatible with bench grindersChina Wet Grinding Machine wholesale Best Price Wet Pan Mill Zimbabwe Grinding Wet Pan Mill Mining Machinery in South Afcia Used Before Mining Separator US$ 32003300 / sets Lithium Iron Phosphate, Ink, Alumina, Oxide Controlling Mode: Electric Control System Automatic Grade: AutomaticWet Grinding Machine MadeinChina2023年4月23日 the grinding media reduces energy and material consumption in a ball mill Different performances are achieved when different sizes and shapes of grinding media are used [ 12 ](PDF) Grinding Media in Ball MillsA Review2024年2月9日 Selecting the appropriate materials, from Zirconium Oxide and Alumina to Silicon Nitride and Tungsten Carbide, significantly affects the grinding process's outcome Whether for pharmaceuticals, materials science, Material Matters: How to Choose the Right Grinding
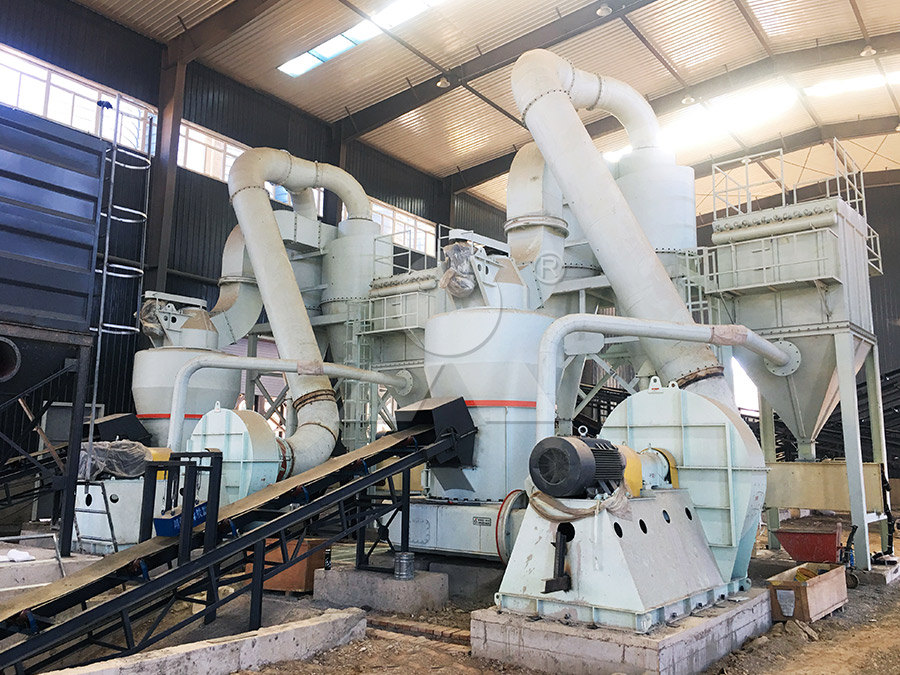
Ball Mill Success: A StepbyStep Guide to Choosing
2024年8月8日 Unlock the secrets to ball mill efficiency with our comprehensive guide on choosing the right grinding media Learn how material composition, size In contrast, steel balls may introduce iron contamination but are preferred in 2014年6月1日 Moreover, andesite aggregate contains high amounts of silica, alumina, and iron oxide [29]; these elements may react with the cement paste and form additional CSH gel, which can increase the Impact of organic matter, iron oxides, alumina, silica and drying China Alumina Oxide Balls wholesale High Alumina Grinding Bead Aluminum Oxide Ceramic Balls for Wet Grinding US$ 08515 / kg 50 kg (MOQ) ZIBO QIMINGXING NEW MATERIAL INCORPORATED CO, Wear Resistance 92% 95% Customized Alumina Oxide Mill Ball for Polishing Machines US$ 0612 / kg 1000 kg Alumina Oxide Balls MadeinChinatively Effect of parameters like temperature of reduction, time of reduction, particle size of raw material, sintering and grinding on the iron powder synthesis is well studied Mill scale iron powder with > 99% degree of metallization, 97% Fe (T), > 96% Direct Reduction Recycling of Mill Scale Through Iron Powder
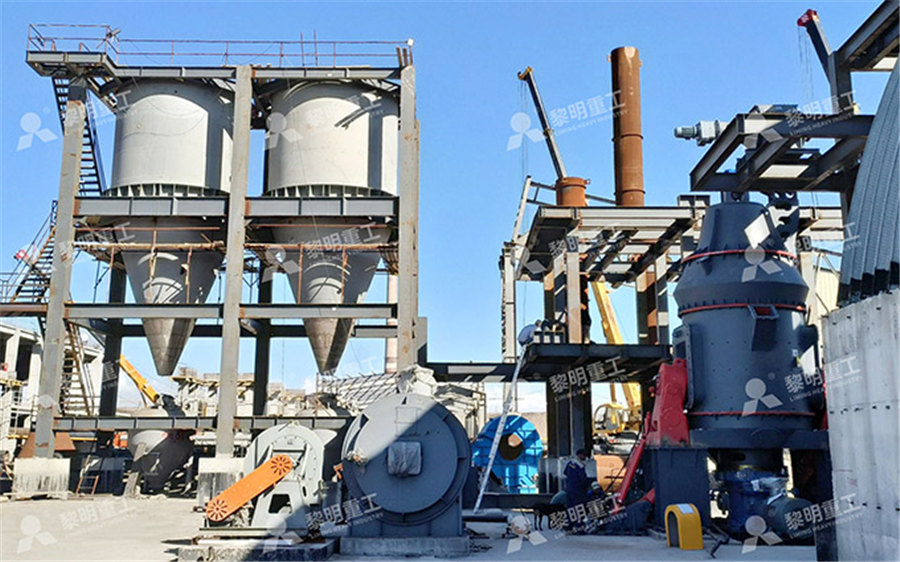
(PDF) corrosion of mill plates in wet grinding ResearchGate
2010年12月31日 In wet grinding, the cast iron material would wear faster than in dry gr inding due to corrosivewear m echanism in the former since corrosivewear strongly depends on oxide layer formation and 2011年2月1日 Request PDF Iron oxide and alumina nanocomposites applied to FischerTropsch synthesis Nanocomposites composed of nanoparticles of iron oxide and aluminium oxide (Fe(2)O(3)Al(2)O(3)) with a Iron oxide and alumina nanocomposites applied to FischerTropsch M185 GRINDING MILL WET OR DRY GRINDING Any material that can be broken by impact can be ground in a SWECO Grinding Mill Basically, the VibroEnergy Mill consists of a grinding compounds, catalyst carriers and iron oxide for magnetic tape production Title: 4201lr GRINDING MILL TO SUBMICRON PARTICLE RANGE THURNEGNPGraystar’s Alumin Grinding Media is used in wet grinding (batch and continuous ball mills), ceramic glaze grinding, and in dry grinding of resins, ceramic raw materials, and other mineral products info@GNPGraystar Northern Office 37 John Glenn Dr Amherst, NY 14228 7167596600 Southern Office 9 Simmonsville Rd Bluffton, SC 29910TECHNICAL DATA SHEET Alumina Grinding Media
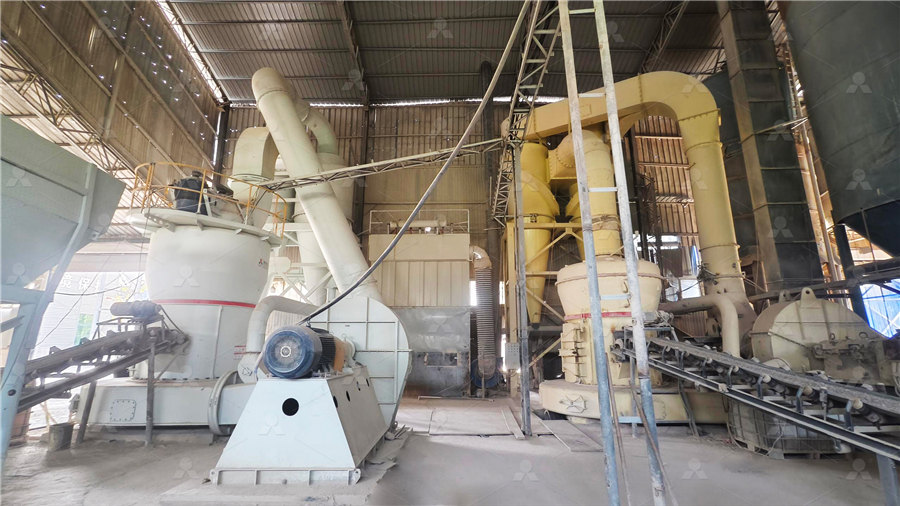
Preparation of iron oxide nanoparticles by mechanical milling
2011年1月1日 Fokina et al (2004) found a technical solution to the problem of continuous feeding of the material into the mill by developing the industrial scale planetary mill operating in a continuous mode Fields of possible applications of these novel devices include recycling of hard alloys, powder metallurgy, recycling of solid waste, ceramic and chemical industries and Download scientific diagram Process flow sheet for Pelletization using wet grinding process from publication: Iron Ore Pelletization Technology and its Environmental Impact Assessment in Eastern Process flow sheet for Pelletization using wet Wheels are a blend of aluminum oxide and zirconia alumina, which removes more material and lasts three times as long as our General Purpose Grinding Wheels They are also known as Type 27 wheels, raisedhub wheels, and grinding discs Wheels are designed for grinding metal surfaces and removing weld seams The 1/8" thick wheels can also be used for notching and Aluminum Oxide/Zirconia Alumina Blend Grinding WheelsAlumina ceramic grinding balls have the characteristics of high strength, high hardness, high wear resistance, high specific gravity, small size, hightemperature resistance, corrosion resistance, ironfree, nonpolluting, etc, and are widely used in ceramics, glazes, glass, etc The grinding of nonmetals is the grinding medium of ball mills, pot mills, vibration mills, etcHow to choose the size, filling amount and ratio of alumina
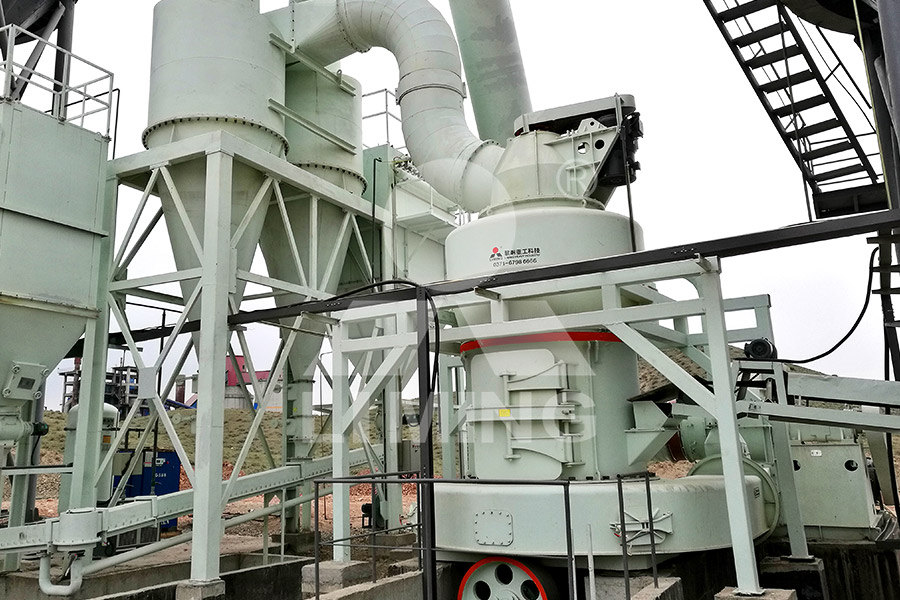
ATTRITOR GRINDING MILLS AND NEW DEVELOPMENTS
also be introduced to the mill during the grinding process to achieve the ultimate dispersing or coating on the dry solid particles II GENERAL FEATURES AND OPTIONS • Various types of Attritors can be used in wet or dry grinding process • A series of metalcontaminationfree machines are specially designed for the ceramic industryMaterial composition of a sample from a tailings dump was analysed 3110 mass% of silica and 765 mass% alumina Wet highintensity magnetic separation (WHIMS) and reverse flotation (RF) were investigated The adsorption of starch on iron oxide was then investigated by infrared analysis of the concentrate produced after starch dosingRemoval of Silica and Alumina as Impurities from LowGrade Iron 2023年7月18日 Cracks were observed in the aluminum oxide phase, which is expected to diminish the mechanical properties of the material It was evident that, with higher iron oxide content in the material, the reducibility of the iron oxide increased, forming an alumina phase surrounding the FeAl intermetallic particles, which were fragile and contained cracksStudy of Aluminum–Iron Oxide Composites Obtained by Die2021年11月15日 Alpha alumina (03µm size) and gamma alumina (005µm size) slurries (or suspensions) are popular for final polishing, either in sequence or singularly MasterPrep alumina suspension utilizes alumina made by the solgel process, and it produces better surface finishes than alumina abrasives made by the traditional calcination processGrinding and Polishing Guide Buehler Metallography
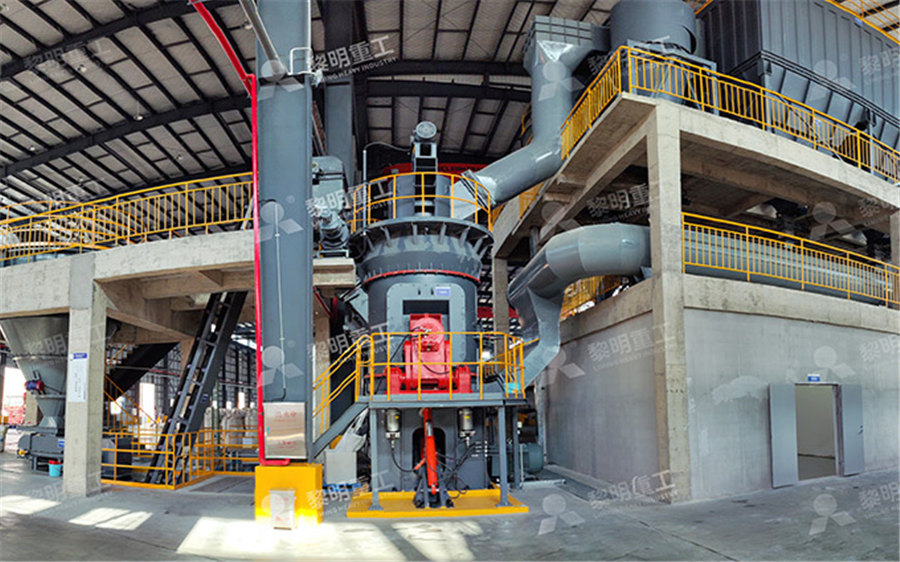
Enhancing Alumina Production Efficiency with Wet Grinding and
It really boils down to what you’re looking to achieve If you’re after precision and efficiency, wet grinding takes the win But for operations where cost and simplicity are key, dry grinding might be your goto Key Benefits of Wet Grinding for Alumina Efficiency Wet grinding isn’t just a process; it’s a game changer in alumina ID : MPT2016R00118AB1 Abstract: Depletion of high grade iron ores with low alumina and silica content has forced the steel industry to utilize low grade iron ores with high gangue contentOptimization of pelletization process for iron ore with high alumina 2020年5月21日 Iron ore pellets are largely characterized by inherent physical and chemical properties of the ore Alumina and silica play important roles in determining the productivity of a Blast Furnace On average, one percent increase in iron content improves productivity by 2% and reduces coke consumption by 1% Therefore higher iron ore feed content to blast furnace is A Study on HighGrade Iron ore Beneficiation to Reduce Alumina Alumina grinding balls are widely used in ball mills as abrasive media for ceramic raw Polyamide Jar for Rapid Mill; Porcelain Jar for Rapid Mill; Grinding Machines Jar Rolling Mills 1 – 32 litres; Jar and Bottle Roller 0,1 – 5 litres; Alumina (Al2O3) Grinding Balls Baan Machines
.jpg)
GRINDING MILL TO SUBMICRON PARTICLE RANGE SWECO
Wet or dry grinding With or without particlesize classification Closed or opencircuit processing From small lab batches to full production grinding SWECO wet grinding mills have working capacities as small as 1 pint and as large as 182 gallons and dry grinding with chamber capacities up to 17 cu ft The key feature of every SWECO Attrition mill fine grinding of refractories vs conventional fine grinding methods are compared to relative cost/energy effectiveness, speed, temperature control, and particle size distribution characteristics Available ceramic media, appropriate iron contaminationfree linings, and auxiliary equipment for specific refractoryAttrition Mill Grinding of Refractories Union Process2020年1月31日 The influence of change in grinding media shape on the grinding behaviour of trace quantities of quartz within an environment of calcite in a small continuous wet ball mill has been studied using Influence of Media Geometry on Wet Grinding of a Planetary Ball Mill2001年9月24日 The experimental material was an alumina hydrate (gibbsite), Al 2 O 3, 3H 2 O provided by Aluminium Pechiney (Gardanne, France) Some physical and chemical properties of that material are given in Table 1The initial particles are agglomerates formed by an association of large platelet shaped crystallites, constituted by a series of pseudohexagonal platesWet batch grinding of alumina hydrate in a stirred bead mill
.jpg)
Wet Ultrafine Grinding Machine Ball Mill Jet Mill
Zhengyuan is China grinding machine manufacturer Designed with totallynew machine structure, optimized machinery size, uniquely designed machinery parts, and simplified production process, wet ultrafine grinding machine has higher performance We offer ball mill, impact mill, jet mill and powder processing equipment Our superfine grinding equipment suits for processing non Alumina hydrate is available in wet as well as dry form Fine hydrate: Alumina trihydrate (ATH) contain 3 molecules of water On exposure to heat above 220°C, alumina hydrate decomposes into aluminium oxide (alumina) and water This irreversible, endothermic reaction process makes alumina hydrate an effective flame retardantAlumina hydrates Hindalco2024年5月2日 Gibbsitetype bauxite is the main material for alumina extraction by Bayer process globally, while the iron in red mud is difficult to use for the high alumina content Therefore, the efficient separation of iron and alumina is the premise for the resource utilization of red mud In this work, the separation of iron and alumina in red mud containing 4745% Fe and 1158% Efficient Separation of Iron and Alumina in Red Mud Using 2006年10月1日 The latter are then treated to give large quantities of finegrained (less than 021 mm) iron ore tailings (IOTs) (Dey et al 2012) However, the high content of aluminium oxides (610 wt%) and Processing of aluminarich Indian iron ore slimes Request PDF