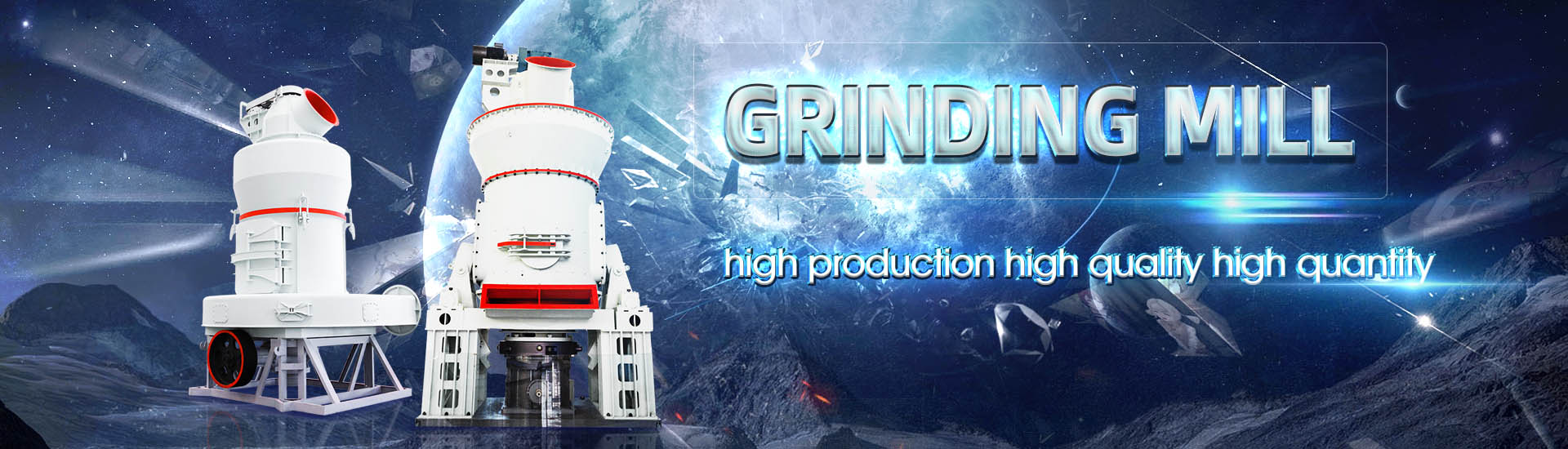
Measures to improve the ratio of slag vertical mill
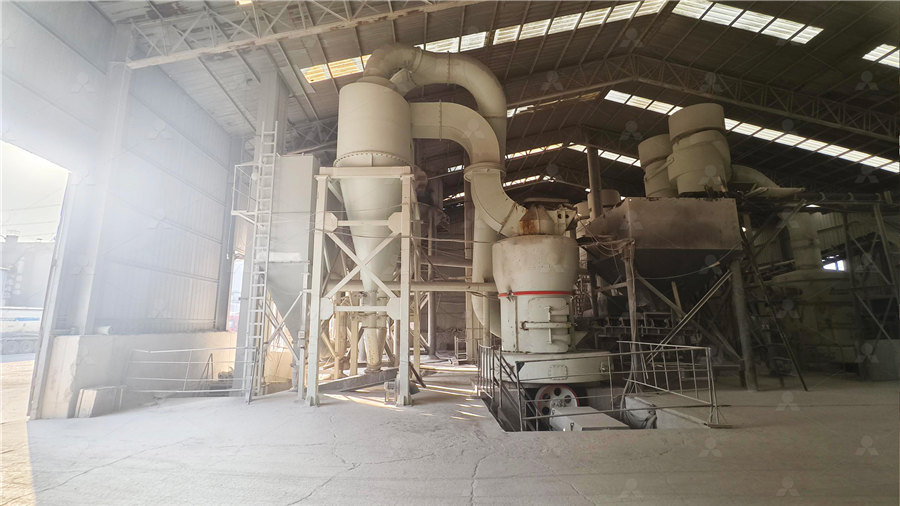
Analysis of vertical roller mill performance with changes in material
2022年5月31日 By increasing the metaparticle size ratio, the crushing rate firstly increases and then decreases, with an increase in metaparticle size ratio from 11 to 12 leads to an 18% 2017年4月1日 In this study, pilot scale tests were performed with a mobile verticalrollermill grinding plant to investigate the relationships between operational parameters The Operational parameters affecting the vertical roller mill slag in roller grinding mills (vertical airswept grinding mills) is a technology introduced by Loesche The first use of a Loesche mill, with a grinding track diameter of only 11 metres, was used as 2 µm 5 µm LoescheCounteractive measures of the VRM, as eg higher grinding pressure, are used to increase the share of very fine particles (diameter below 5 μm) if necessary Advanced cement additives, SikaGrind® for vertical roller mills
.jpg)
PROCESS OPTIMISATION FOR LOESCHE GRINDING PLANTS
a vertical roller mill (VRM) • Surpasses the classic methods if the controlled process demonstrates significant disturbances • A high degree of attention to the process states is required in order kind of measures to apply By not matching targets, with too high a proportion of residues, it becomes increasingly necessary to work on comminution as follows: • Check maximum feed BALL MILLS Ball mill optimisation Holzinger Consulting2022年1月23日 This work concentrates on the energy consumption and grinding energy efficiency of a laboratory vertical roller mill (VRM) under various operating parameters For Analysis and Optimization of Grinding Performance of Vertical 2012年3月1日 Numerous optimization measures have ensured that the vertical roller mills installed in the Buzzi Unicem/Dyckerhoff Group have a high level of availability This article Operating experience with a vertical roller mill for grinding
.jpg)
GRINDING Grinding options for slag and pozzolan PEC
mills This compares with the compression mechanism, as well as attrition, utilised in both highpressure grinding rolls (HPGRs) and vertical roller mills (VRMs) The Bond Ball Mill Work Request PDF On Sep 1, 2016, Deniz Altun and others published Operational parameters affecting the vertical roller mill performance Find, read and cite all the research you need on ResearchGateOperational parameters affecting the vertical roller mill 2012年3月1日 Vertical roller mills are the mills traditionally used for processing granulated blastfurnace slag and for grinding composite cements From the energy aspect they are superior to grinding plant Operating experience with a vertical roller mill for vertical slag mill is typically designed to deal with industrial waste residues generated by the blastfurnace ironmaking Due to its high physical and chemical activity, and potential hydraulicity, the slag has been widely as admixture matters in the cement industry And the slag can replace the cement in the concrete to improve the quality and durability of the concreteGGBS Vertical Roller Mill
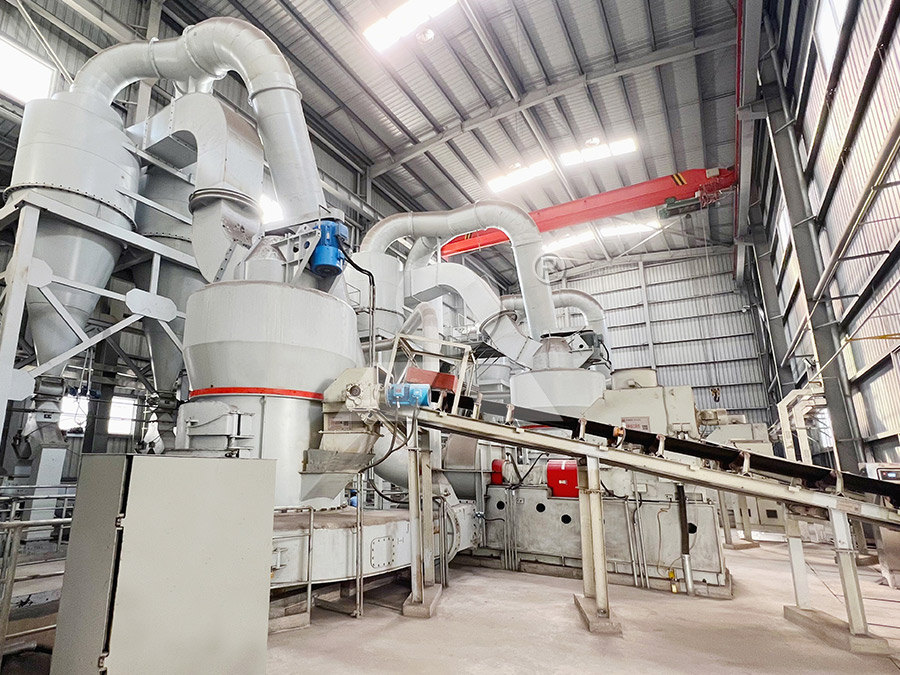
How to stabilize the vertical roller mill material dam ring?
2016年5月10日 To stabilize the vertical mill grinding table, we must do a good adjustment of dam height , which is the basis of a vertical mill grinding table, the key of vertical mill normal operation Chaeng will introduce you to describe how to establish stable abrasive bed Material thickness can be adjusted to adjust the height of dam, retaining ring material vertical mill is a 2023年12月4日 A vertical roller mill (VRM) is a grinding equipment used for the size reduction of minerals, It is also used to grind slag and nonmetallic ores The VRM decreases the number of equipment in the grinding circuit by combining the drying, crushing, grinding, and particle segregation in one unit Numerical Investigation of Vertical Roller Mill Operation Using 2013年5月1日 Raw fly ash (RFA) was modified by a selfdeveloped new dry energysaving vertical grinding mill This was beneficial to improve the particle morphology and distribution of RFA and enhanced its Study on Particle Characteristics of Cement by Vertical Roller Mill 2018年12月10日 In this paper, the measures to decrease slag formation are first discussed based on the massbalance calculation, and then the present and future states of slag valorization in Japan are reviewedMeasures to Decrease and Utilize Steelmaking Slag
.jpg)
SikaGrind® for vertical roller mills
Slag Cements are wellrecognized in many countries with traditional and powerful steel production High chemical resistance, low heat of hydration and sustainability are strong arguments for Slag Cements The main disadvantage of Slag Cement is the slow strength development Slag (ASTM C 989 and EN 15167) or Slag cement (ASTM C 595 and EN 1971)Granule morphology of granulated blast furnace slag powders prepared with vertical mill (GBFSV) and close circuit ball mill (GBFSB) respectively were observed with SEMThe Vertical Mill Slag MicroPowders' Particle Size Distribution 2013年1月15日 Frequent slag sampling and analysis is still the most common method used to investigate and improve slag operation in electric arc furnaces (EAFs) for lowalloyed carbon steelmaking(PDF) Understanding the Properties of Slags ResearchGateSlag Cements are wellrecognized in many countries with traditional and powerful steel production High chemical resistance, low heat of hydration and sustainability are strong arguments for Slag Cements The main disadvantage of Slag Cement is the slow strength development Slag (ASTM C 989 and EN 15167) or Slag cement (ASTM C 595 and EN 1971)SikaGrind® for vertical roller mills
CFB石灰石脱硫剂制备64.jpg)
Ten Ways to Improve the Grinding Efficiency of Your
2019年4月22日 2 More crushing and less grinding to reduce the feed size into mill The larger feed size, the more work that the ball mill needs to do on the ore2024年10月25日 Using the HGM series Micro Powder Grinding Mill to grind slag into ultrafine powder and mix it with silicate cement, a new type of slag silicate cement can be prepared This new type of cement can not only reasonably control the fineness of cement, but also achieve the optimal ratio of silicate cement and slag powder, thereby improving the performance of cementSlag Ultrafine Powder Processing TechnologySlag Cements are wellrecognized in many countries with traditional and powerful steel production High chemical resistance, low heat of hydration and sustainability are strong arguments for Slag Cements The main disadvantage of Slag Cement is the slow strength development Slag (ASTM C 989 and EN 15167) or Slag cement (ASTM C 595 and EN 1971)Picture: Loesche GmbH, Germany CEMENT SikaGrind® FOR VERTICAL ROLLER MILL2022年1月23日 This work concentrates on the energy consumption and grinding energy efficiency of a laboratory vertical roller mill (VRM) under various operating parameters For design of experiments (DOE), the response surface method (RSM) was employed with the VRM experiments to systematically investigate the influence of operating parameters on the energy Analysis and Optimization of Grinding Performance of Vertical
.jpg)
The Complete Guide to Tunnel Slag Treatment sbmchina
2023年4月26日 Vertical Grinding Mill; Ultrafine Grinding Mill; Effective measures to improve the quality of tunnel slag parent rock: Firstly, before excavation, Analysis of mix ratio of concrete with tunnelslag sand 1 Selection of preparation strength and water cement ratio2007年2月1日 First Polysius slag roller mill in China The first Polysius roller mill for slag grinding in China is in operation since 2002 in Anshan in the province of Liaoning The grinding plant of the Angang Group Slag Development Company is exactly the same size as the one which has been in operation since 1995 just a few hundred kilometres away in KoreaSlag grinding with the Polysius Roller Mill in ChinaOptimize the homogenization measures of packaging cement and improve the multipoint feeding mode of homogenization warehouse; The outflow cone angle of homogenized powder storehouse was changed from 60 ° to 70 ° in the past, and the flow effect generated by the gravity of powder itself was used to homogenize powder in the storehouseHow to improve cement plant process for better cement qualityHLM series slag vertical roller mill produced by HCMilling(Guilin Hongcheng) can be widely used in slag grinding treatment The whole set of slag grinding treatment process includes crushing, drying, grinding, grading, transportation, collection, storage and other steps, which can realize the complete production and processing of slag from large particles to finished fine powderNews Application Of Slag Grinding Mill Introduction To
.jpg)
Vertical roller mill for raw Application p rocess materials
Fig2 Schematic process flow of vertical roller mill for grinding of raw materials Vertical roller mills are adopted in 20 cement plants (44 mills) in Japan Results Table Energy saving effect of the vertical roller mill Ball mill Specific power Cost estimationSlag grinding unit Processing material: slag produced in the ironmaking process in blast furnaces Final product: ground granulated blastfurnace slag (GGBS or GGBFS) Output: 3002,000 thousand tons/year Fineness: specific surface area of product≥420 m 2 /kgSlag Grinding Plant GGBS Plant One Stop Solution CNBM The slag grinding process is introduced The basic control forms of vertical mill are presented by analyzing the dynamic characteristics of material layer in slag vertical millMaterial layer control based on slag vertical mill's ResearchGate2021年9月1日 Slag from the conventional steelmaking process is one of the main byproducts of the iron and steel industry The production of each ton of steel generates 150200 kg slag [1], which is rich in (PDF) Phases Reconstruction and Foaming
.jpg)
Measures to Decrease and Utilize Steelmaking Slag
2018年12月10日 To improve the distribution ratio, the ratio of phosphorus contents between slag and steel (L P = (% P) in slag /[% P] in steel), the decrease in the activity of P 2 O 5, and the increase in the activity of FeO are important measures to be consideredAs the activity of P 2 O 5 is mainly controlled by the basicity—the ratio of CaO and SiO 2 content in slag—and the Vertical Mill Renovation Measures Lower the height of the retaining ring Under the premise of not changing the roll skin and the disc liner, the height of the retaining ring is adjusted from 105mm to 85mm according to the wear amount of the disc liner, so that the hardtogrind material can be removed in time and the thickness of the layer is reducedHow To Improve Output Of Vertical Mill56 CEMENT INTERNATIONAL 4 2/2012 4 VOL 10 ZUSAMMENFASSUNG Vertical roller mills are the mills traditionally used for processing granulated blastfurnace slag and for grinding compositeOperating experience with a vertical roller mill for grinding This vertical slag mill can be installed in a slag powder production line with an output range from 45t/h to 300t/h It also reduces the vibration of the vertical mill, realizes automatic control of the program, and effectively improves the processing safetySlag Mill Vertical Slag Mill Provider SINOMALY
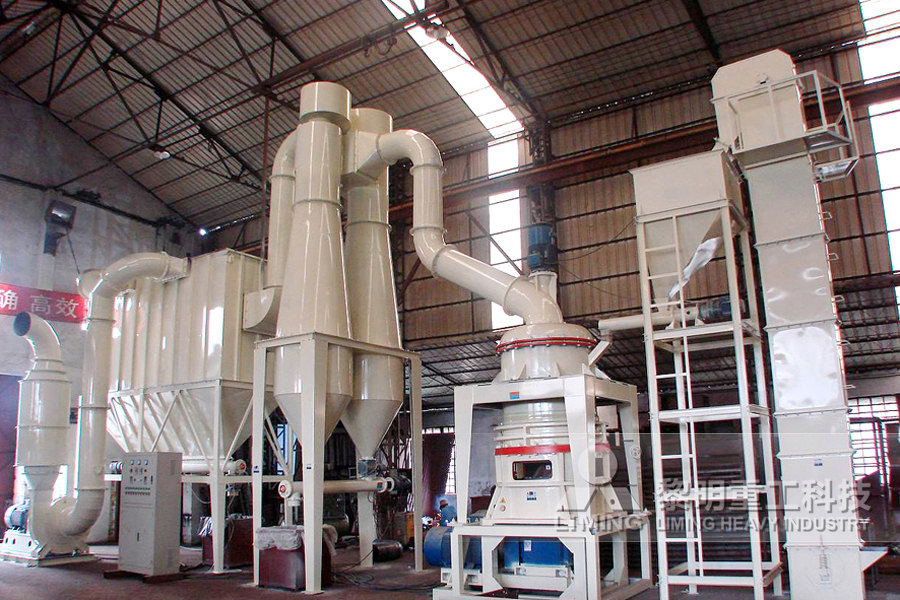
Grinding Process Optimization Featuring Case Studies and
Fig 1 Flowsheet of modular vertical roller mill 5000 R4 The required throughput rates were achieved in short time All fineness figures met the target values as well without any2022年5月12日 The process of producing slag micro powder with vertical mill has been relatively mature in recent years and has developed rapidly The fineness of the vertical micropowder mill can be directly adjusted freely at 1503000 mesh, and the content of 2um can reach 60%Slag grinding mill micro powder production line SBM Ultrafine making slag: one is to decrease the generation of slag [4, 5], and the other is the development of a method for reuse In this paper, the measures to decrease the slag formation are first discussed based on the massbalance calculation Then, the present and future states of slag valorization in Japan are reviewed Measures to Decrease Slag Measures to Decrease and Utilize Steelmaking Slag2007年11月1日 The first industrialscale vertical roller mill for slag cement, an MPS 3750 C, went into operation in Hannover 25 years ago 1 and is still in operation today (Figure 3) The capacity of this mill ranges from 60t/h slag with 4100cm²/g to 70t/h CEM III A or 45t/h CEM III B with slag content between 50–80% and fineness of 3600cm²/g and 4300cm²/gMPS vertical roller mills for slag and slag cements
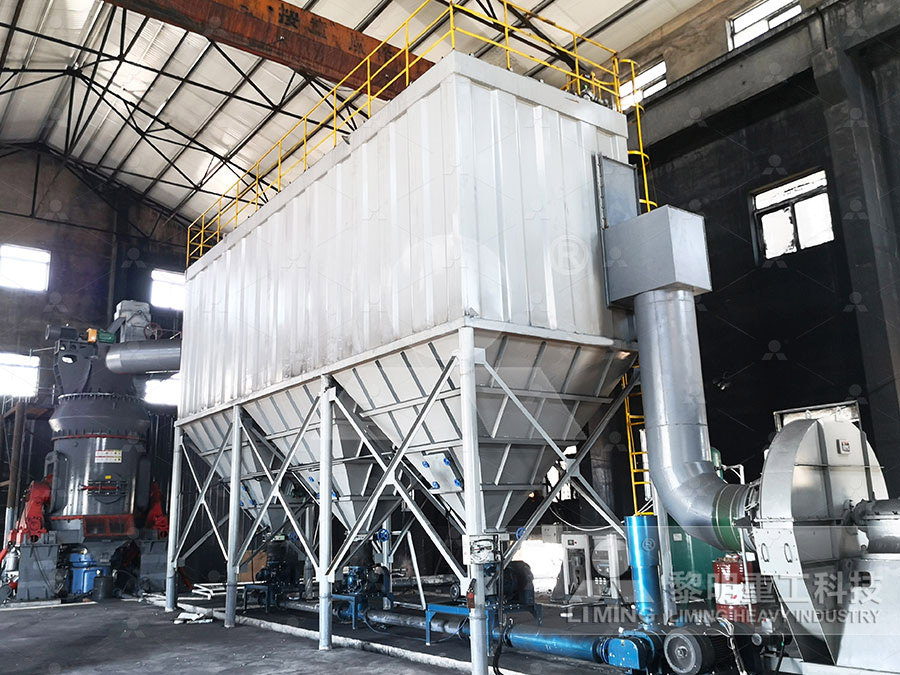
The important role of vertical roller mills in the cement industry
It is widely used in clinker grinding production of cement plant and slag grinding plant CHAENG can provide various types of vertical cement mills with productivity of 50250t/h The biggest advantage of CHAENG is to have a large casting base and large machining workshops, which greatly shortens the delivery cycle of cement vertical millMapei has recently carried out an industrial trials on a vertical mill type LM 35 2+2 with the purpose of testing MAGA/VM 10, one of the newly developed cement grinding additives for vertical rollers mill The present industrial test has been performed with the objective of enhancing the compressiveImprovement of cement performances through the use of 2019年12月1日 In this paper, the mechanical properties of magnesia slag cementitious materials under different ashslag ratios are studied and analysed Magnesium slag and fly ash are prepared by composite methodStudy on the Effect of AshSlag Ratio on Mechanical Properties of The production of slag powder can not do without grinding mill LM slag vertical grinding mill is professional slag grinding equipment designed according to the characteristics of slag It adopts that the roller can grind material on the transmission arm directly, meanwhile the roller do not contact directly with transmission armThe application of High costperformance ratio LM vertical mill in slag

Slag vertical mill
Slag vertical mill is mainly applied in metallurgical and cement industries and is the highend equipment for treatment of slag and crushed coal DHHI continually improves the talents recruiting, cultivation, use and encouragement systems to realize professional, a Loesche mill, with a grinding track diameter of only 11 metres, was used as long ago as 1935 However, the breakthrough in grinding this type of material on the vertical roller mill did not take place until the beginning of the 1990’s 1935 The first Loesche mill for grinding cement clinker, an LM 11, was commissioned in Joao Pessao, Brazil2 µm 5 µm Loesche2015年1月1日 Steel slag is an industrial byproduct of steel industry It possesses the problem of disposal as waste and is of environmental concern The results were compared with conventional concrete Steel slag to improve the high strength of concrete ResearchGate2023年4月23日 ciency include mill design, liner design, mill speed, charge ratio, and grinding media properties The authors also indi cated that circuit efficiency is determined by how well the power applied (PDF) Grinding Media in Ball MillsA Review ResearchGate
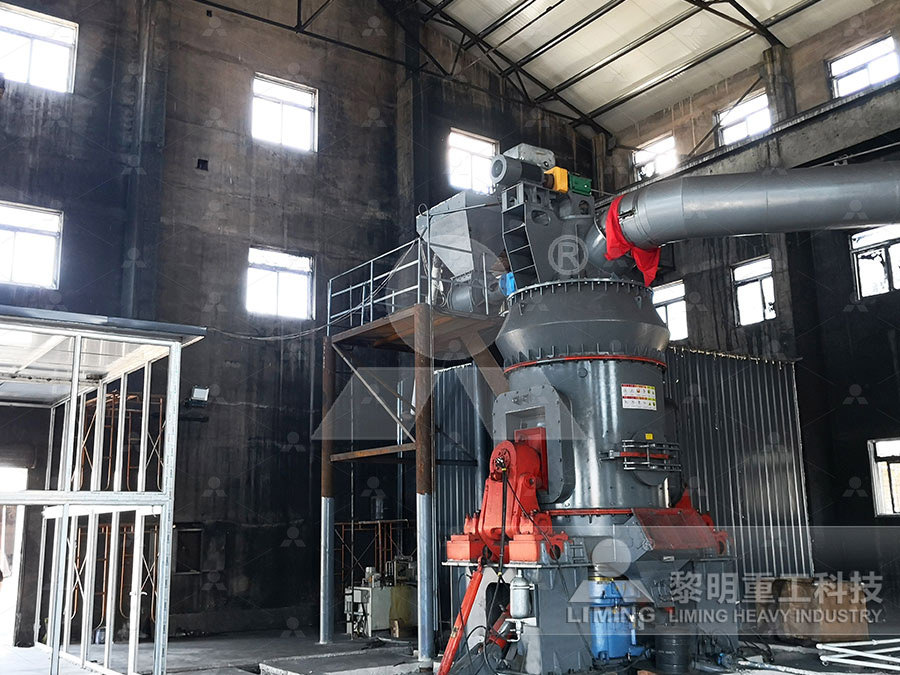
An approach to improve the reactivity of basic oxygen furnace slag
2023年5月23日 The construction industry is one of the greatest CO 2 emitters Cement, as an essential ingredient of concrete which is the most widely used building material, contributes around 5–8% of global anthropogenic CO 2 emissions, and most of the emissions come from clinker production [1], [2]Industrial wastes such as blast furnace slag, silica fume and fly ash