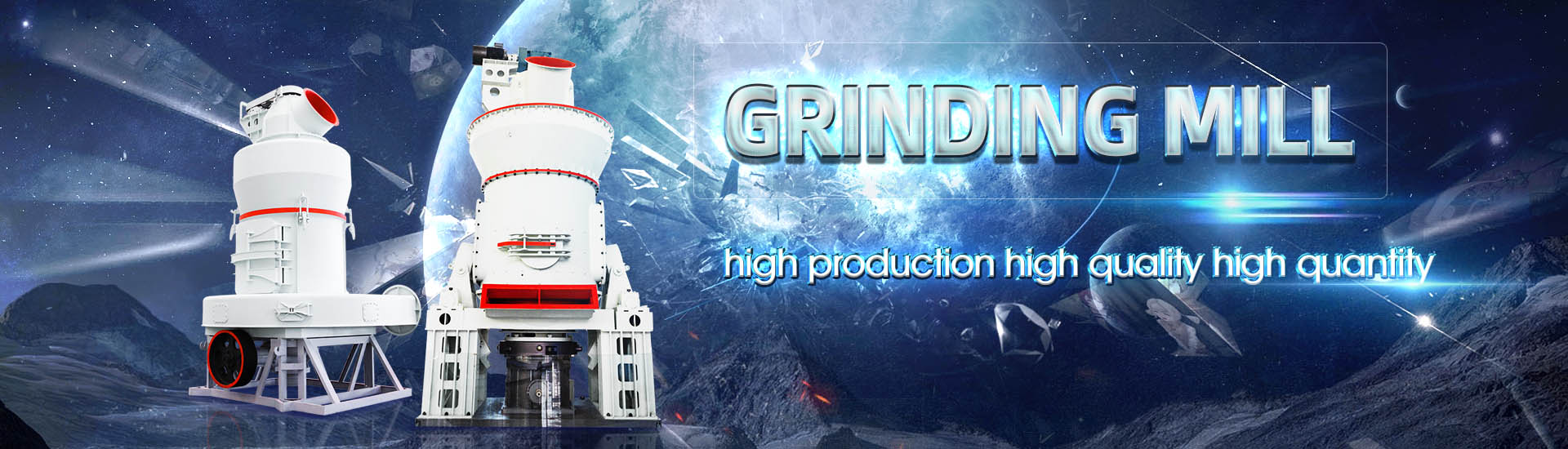
HOME→Main production area of limestone for power plant desulfurization Main production area of limestone for power plant desulfurization Main production area of limestone for power plant desulfurization
Main production area of limestone for power plant desulfurization Main production area of limestone for power plant desulfurization Main production area of limestone for power plant desulfurization
.jpg)
Analysis of limestone for flue gas desulfurization in a power plant
The Thermo ScientificTM ARLTM QUANT’X EnergyDispersive Xray Fluorescence (EDXRF) Spectrometer is used to control the quality of limestone used for flue gas desulfurization (FGD) in coalfired power plantsTo remove the SO₂, the flue exhaust from a coalfired power plant is commonly bubbled through a mixture of lime or limestone and water The resultant reaction typically captures 95 % or more Analysis of limestone for flue gas desulfurization in a power plant2015年10月30日 This study investigated that status of domestic and international furnace desulfurization and desulfurization characteristics of (PDF) A Review of Desulfurization Technology using 2021年7月15日 milling plant producing limestone flour for wet limestone FGD and limestone sand for fluidised bed boilers Conducting the desulphurisation process during fuel (PDF) Limestone Sorbents Market for Flue Gas ResearchGate
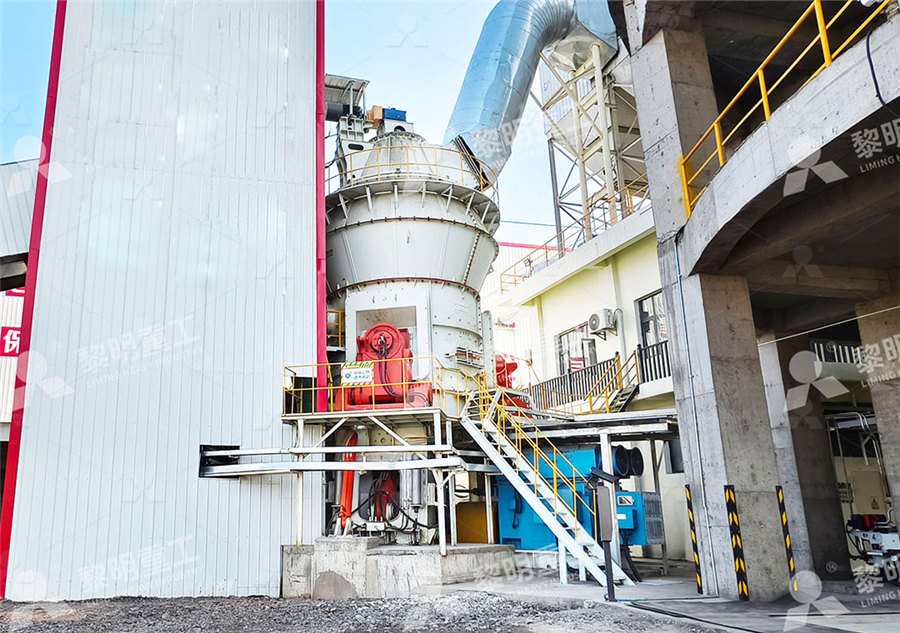
Status of Flue Gas Desulphurisation (FGD) systems from coalfired
2015年3月15日 This paper presents a general review of the Flue Gas Desulphurisation (FGD) technologies used to abate sulphur emissions from coalfired power plants, and exposes the 2022年1月15日 Global statistics showed in 1998 that wet limestone desulfurization was the main technology used in flue gas desulfurization in power plants, accounting for 83% of flue gas Summary of research progress on industrial flue gas 2017年7月1日 In this study, we investigated the production of precipitated calcium carbonate (PCC) particles from desulfurization gypsum (DG) waste using a new experimental apparatus Enhancing the recovery of gypsum in limestonebased wet flue 2022年5月15日 This study illustrates the application of the developed methodology to real research to support managers in selecting the most appropriate limestone supplier for a Coal Limestone supplier selection for coal thermal power plant by
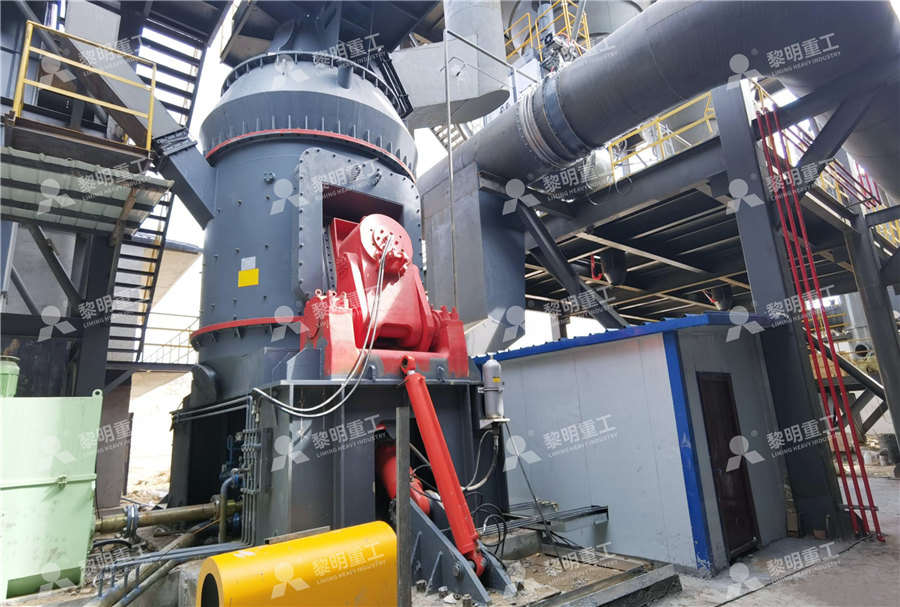
Feasibility Analysis and Key Issues of Using Limestone Sludge in
2021年1月14日 The results show that the limestone sludge in recycled water is possible to be used as a desulfurizer Due to the large amount of impurities and lower reactivity of limestone 2021年1月1日 The results show that the limestone sludge in recycled water is possible to be used as a desulfurizer Due to the large amount of impurities and lower reactivity of limestone Feasibility Analysis and Key Issues of Using Limestone Sludge in According to the desulfurization process period, it can be divided into the coal power plant desulfurization, desulfurization furnace and flue gas desulfurizationAccording to the temperature of desulfurization medium, there are three ways for desulfurization mainly including wet, dry and semidryAt present, flue gas desulfurization is the main method in the most coalfired power Power plant desulfurization2022年1月6日 This study aims to perform energy, exergy, economic and emissionremoval performance analysis of wet flue gas desulphurisation (FGD) systems in a coalfired power plant with 660MW capacityA wet type flue gas desulphurization system used in a
.jpg)
Summary of research progress on industrial flue gas desulfurization
2022年1月15日 In the industrial production of China, the processing of phosphate rock, volcanic eruptions, kerosene combustion and aluminum smelting will lead to flue gas emissions containing a large amount of SO 2SO 2 is a highly irritating gas Because SO 2 is freely soluble in water and enters the respiratory tract, it can generate corrosive sulfurous acid, sulfuric acid, and sulfate 2017年7月1日 With the intent of increasing the specific surface area of limestone and consequently the gypsum production, the raw limestone was treated in a highenergy mill The performance of such micronized limestone in terms of gypsum production and SO 2 removal were then evaluated by means of a bench scale desulfurization testEnhancing the recovery of gypsum in limestonebased wet flue 2020年2月18日 It was found that water samples analysed from the vicinity of limestone quarry and cement plant showed an elevated levels of pH, EC, TDS, total hardness, alkalinity, calcium and sulphate (PDF) Environmental Hazards of Limestone Mining and2021年6月1日 Taking a 200 MW coalfired power plant in North China with a limestonegypsum wet desulfurization system transformation project as an example, the effect of energysaving transformation of the Technical Transformation and Energy saving Analysis of Desulfurization

Experimental study on the treatment of desulfurization
2022年7月25日 Nowadays, the limestone–gypsum wet flue gas desulfurization (WFGD) technology has become the main method for flue gas desulfurization in coalfired power plants This technology has the advantages of high maturity, stable operation, and good adaptability to the different flue gas components and boiler loadsfor Thermal Power Plants" (GB132232011) are shown in Table 1 From the perspective of Chinese energy demand, coalfired power generation will still occupy the main position of electricity production for a period of time in the future, so the control of pollutant emissions from coalfired power plants is the top priority of air pollutionResearch progress of flue gas desulfurization and denitrification 2019年3月13日 Sulfur dioxide (SO 2) is one of the main air pollutants from many industries Most coalfired power plants in China use wet flue gas desulfurization (WFGD) as the main method for SO 2 removal Presently, the operating of WFGD lacks accurate modeling method to predict outlet concentration, let alone optimization methodFull article: Modeling and optimization of wet flue gas desulfurization 2024年1月10日 Flue gas desulfurization (FGD) is a critical process for reducing sulfur dioxide (SO2) emissions from industrial sources, particularly power plants This research uses calcium silicate absorbent Modeling based on machine learning to investigate flue gas
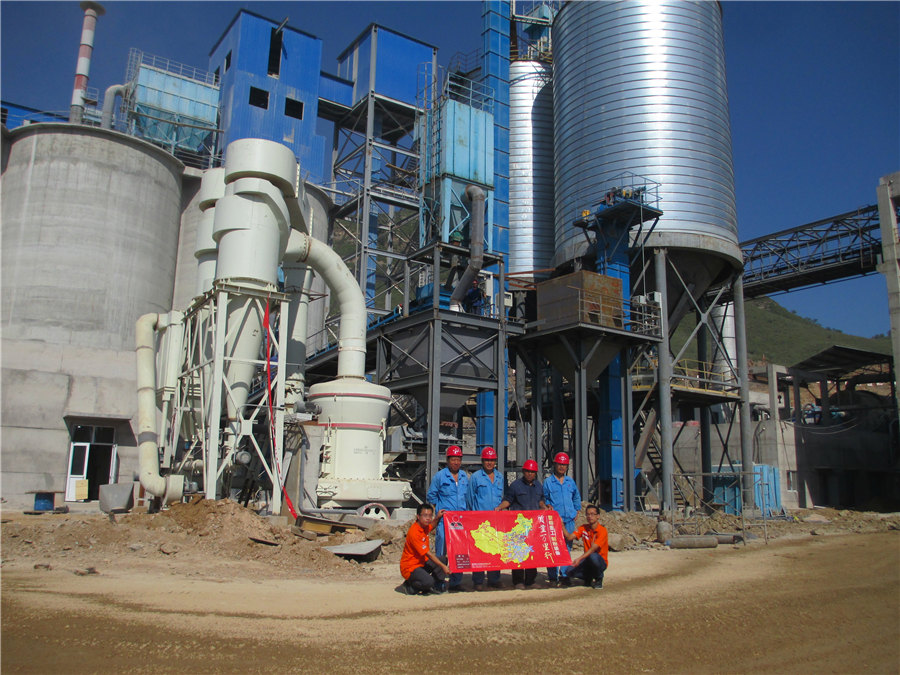
Flue Gas Desulfurization (FGD) Working Thermal
Limestone preparation system in flue gas desulfurization (FGD) consists of following subsystems: 1 Limestone Handling System Limestone will be delivered to the limestone storage shed by truck Limestone will be delivered 2012年1月1日 This study indicates that red mud from alumina plant is a favorable additive for improving the desulfurization performance of limestone, and the effect of red mud on limestone’s desulfurization activity is due to superposition of improvement in solidstate ionic diffusion and surface chemical reactionExperimental Study and Mechanism Analysis of Modified Limestone 2019年3月30日 Main operating conditions affecting SO2 a model of limestone/gypsum wet flue gas desulfurization The operation mode of boilers of power plant in China is different to that of other (PDF) Progress of Desulfurization and Denitration Technology of 2014年7月1日 Atmospheric emissions, including particle number and size distribution, from a 726 MWth coalfired power plant were studied experimentally from a power plant stack and fluegas plume dispersing in Chemical composition and size of particles in emissions of a
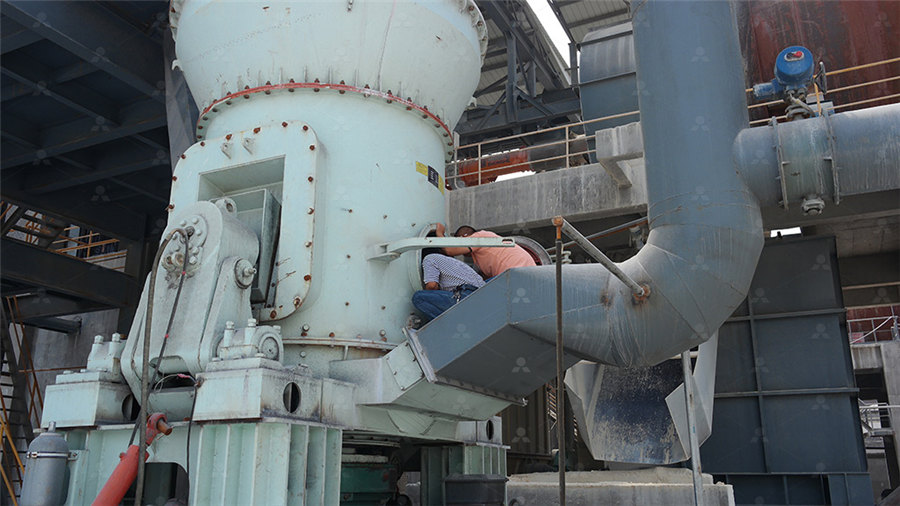
Flue Gas Desulfurization Technologies for CoalFired Power
The control of sulfur dioxide emissions from thermal power plants is examined in light of the recent advances made in developing commercial processes for this appli cation Beginning with a discussion of some of the more recent developments in the conventional wet and dry scrubbing technologies, the paper provides a description of the results of the recent fullscale 2001年5月19日 Warych et al [43, 44] established a model of the thermal power plant flue gas desulfurization process based on the thin film theory, which simulated the SO 2 absorption process and limestone Model of the Wet Limestone Flue Gas Desulfurization2008年11月1日 In this paper, a model of limestone/gypsum wet flue gas desulfurization (WFGD) system was developed based on unsteady theory The models of processes of absorption section and oxidation section were developed and incorporated into the WFGD integral model The submodel of motion of slurry drops, absorption of SO 2, dissolution of limestone and crystallization A model for performance optimization of wet flue gas desulfurization 2021年11月1日 Flue gas desulfurized gypsum mainly comes from thermal power plants, smelters, and largeenterprise boilers, and contains industrial byproducts produced through a wet desulfurization combustion process, where SO 2 gas and lime slurry react under strong oxidation conditions The main component of this gypsum is calcium sulfate dihydrate, which also Production and resource utilization of flue gas desulfurized
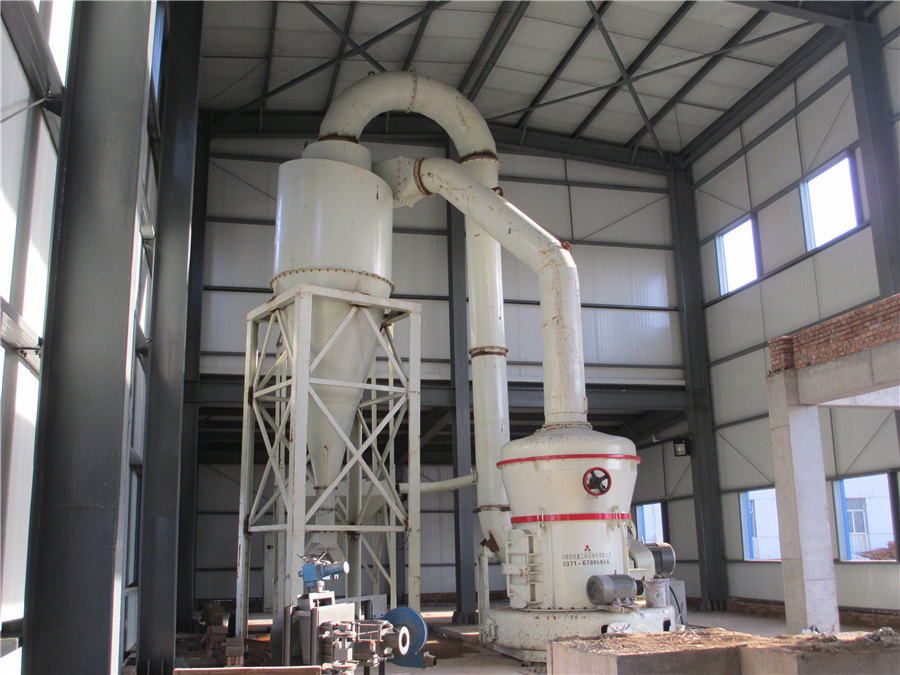
Recent advances in flue gas desulfurization gypsum processes
Frandsen JBW, Kiil S, Johnsson JE Optimisation of a wet FGD pilot plant using fine limestone and organic acids Chem Eng Sci, 56 (2001), pp 3275–3287 [Google Scholar] Gao Y, Xie X, Zou P, Liang X, Yang Y, Li Z, Wang H, Xiao T, Cai W Study on Additives for Wet Limestone FGD, AsiaPacific Power and Energy Engineering Conference APPEEC (2011)Therefore, it is necessary to desulfurize and denitrify the power plant flue gas to avoid causing air pollution and affecting the safety of life and production around the power plant Power plant flue gas desulfurization and denitrification Power plant desulfurization, denitrification and 2021年5月21日 Since the beginning of the 1990s, due to international regulations on air quality, a large number of flue gas desulphurisation (FGD) installations have been constructed in the Polish coalfired power industry Limestone Sorbents Market for Flue Gas 2024年3月20日 Desulfurization wastewater is industrial wastewater with a high salt content, high metal ions, and high hardness produced by flue gas desulfurization of the limestonegypsum method in coalfired power plants Current Status of Zero Liquid Discharge Technology for
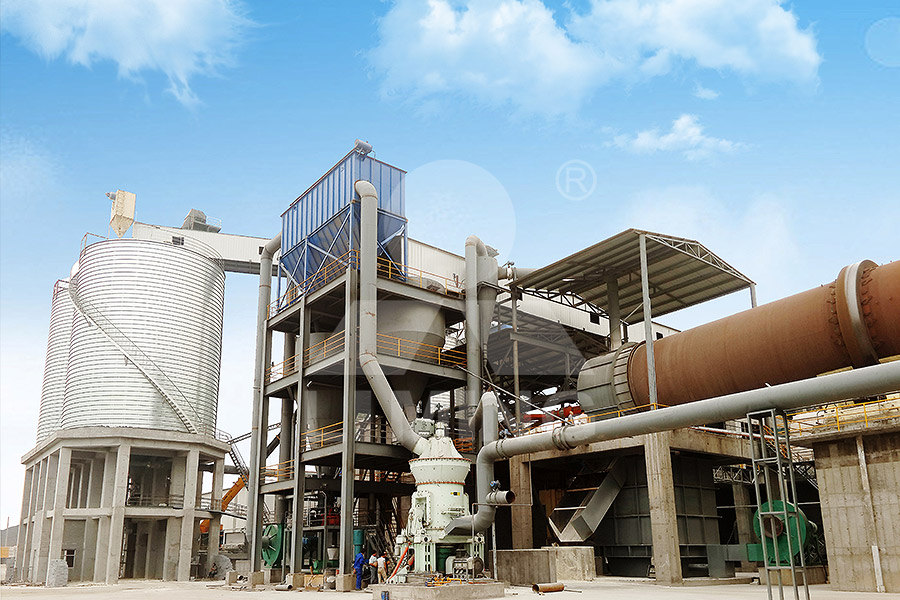
Mitsubishi Power Flue Gas Desulfurization (FGD) Plants
Max Capacity 1,050 MW Max Inlet SO 2 Concentration 80,000 mg/Nm 3 (Coal fired) Max SO 2 Removal Efficiency 99% High Reliability The flue gas desulfurization (FGD) plant removes sulfur dioxides (SO 2) from flue gas produced by boilers, furnaces, and other sourcesMitsubishi Power effectively contributes to the prevention of air pollution through its wet limestone 2009年5月27日 To supply a clear emission picture of power sector, since 2005, Henan had shut down 978 million kW of small thermal power units, and by the end of 2008, all of its coalfired power units had been Model Predictive Control of a Wet Limestone Flue Gas Desulfurization 2022年7月14日 The specific surface area, pore distribution, and other physicochemical parameters were analyzed by XRD and SEM, which explained the changes of products and carbide slag before and after desulfurization The test results show that carbide slag and limestone have almost the same desulfurization effectDesulphurization mechanism and engineering practice of carbide 2021年7月15日 main component of limestone, for limestone sorbent in this power plant reached 16 million tpy and the actual sorbent with own limestone milling plant of production capacity 200,000 tpy;(PDF) Limestone Sorbents Market for Flue Gas ResearchGate
.jpg)
Evaporation and concentration of desulfurization wastewater with
2019年7月22日 The reduction of wet desulfurization wastewater is one of the important tasks of coalfired power plants, and it is important for achieving “zero emissions” Evaporation and concentration (EC) with waste heat is an effective way to reduce wastewater Here, two typical types of industrial desulfurization wastewater are used to study the change rule of pH and total 2020年12月1日 Power generation from coal combustion comprises a majority of electrical energy produced worldwide, with a share of 381% in 2017 Such coalbased power plants have to comply with stringent and steadily tightening emission limits, mainly focused on sulfur dioxide (SO 2), nitrogen oxides (NOx), dust concentration and mercuryForced oxidation wet Effect of ammonia and ammonium compounds on wetlimestone 2017年1月1日 The surface area and total pore volume above 255 m²/g and 00094 cm³/g respectively, and density below 268 g/cm³ are required for a limestone sample for defluoridation from 10 mg/L [F]0 to 1 Evaluation of limestone impurities in the desulfurization process Limestone powder (kiln dust) smaller than 45μm is sent to the limestone powder silo, and the limestone powder is discharged into the limestone slurry tank by the impeller feeder, and the process water is added to prepare 30% limestone Limestonegypsum Desulfurization Process in
.jpg)
Zeroliquid discharge technologies for desulfurization
2022年11月1日 Desulfurization wastewater from limestone FGD systems has high salt concentrations, Table 1 shows the main ion concentrations in desulfurization wastewater from a power plant in Anhui Province, China and the latter is used in the production of gypsum The main components of chloride solution include MgCl 2, 2023年8月22日 The production of FGD gypsum, which is a byproduct of flue gas desulfurization (FGD) in power plants, has been the subject of numerous LCA and LCCA studies These studies aim to evaluate the environmental and economic impacts of producing FGD gypsum and compare them with the impacts of other building materialsA comprehensive review of flue gas desulphurized gypsum: Production Currently, desulfurization technologies can be categorized into three main types: wet flue gas desulfurization (FGD) [11], [12], [13], semidry desulfurization [14] and dry desulfurization [15]Wet flue gas desulfurization is widely employed in largescale desulfurization processes due to its high efficiency and low energy consumption [16]However, it poses a significant environmental Recent advances in process and materials for dry desulfurization 2014年3月1日 But with the reduced power hour and risen price of limestone, the current desulfurization system power price policy of China cannot compensate the running cost of the desulfurization system in Cost and Benefit Analysis of Desulfurization System in Power Plant
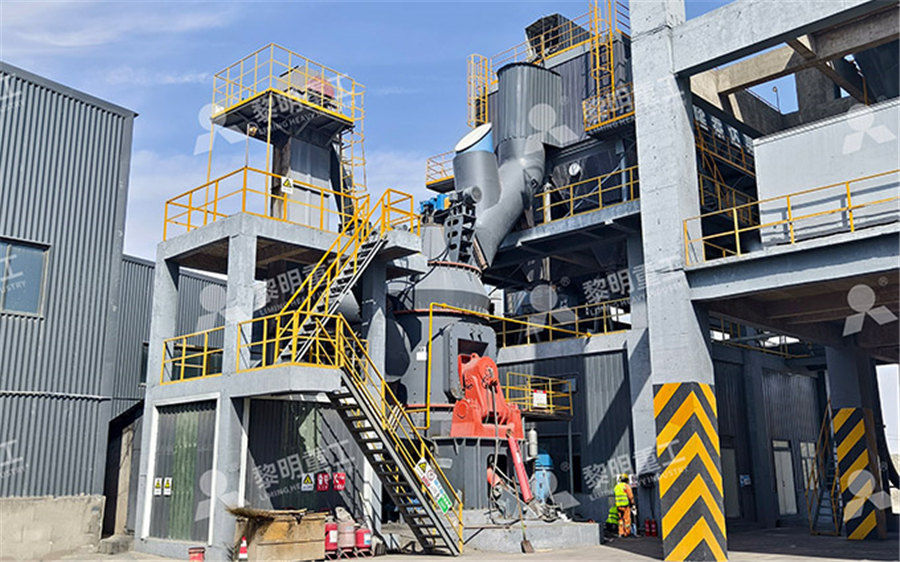
Preliminary Study of Dry Sorbent Injection and Limestone Forced
PDF On Sep 23, 2020, Alfian Muhammad Reza and others published Preliminary Study of Dry Sorbent Injection and Limestone Forced Oxidation Comparison for Coal Fired Steam Power Plant Retrofit 2024年9月30日 Coalfired power plants account for a large share of the power generation market in China The mainstream method of desulfurization employed in the coalfired power generation sector now is wet flue gas desulfurization This process is known to have a high cost and be energy/materially intensive Due to the complicated desulfurization mechanism, it is Sustainable Operation Strategy for Wet Flue Gas Desulfurization 652 Flue Gas Desulfurization Flue gas desulfurization (FGD) is a very common method for gas claning adopted in a gas processing plant In this process, the flue gas with acid vapors is scrubbed to remove it as a byproduct Most of the FGD processes use alkali to scrub the flue gas Many designers of FGD adopt the limestone gypsum processFlue Gas Desulfurisation an overview ScienceDirect TopicsMWe Medupi coalfired power plant, using publicly available data, to determine whether affordable SO 2 abatement could be implemented on coalfired power plants in South Africa The Medupi power plant has been chosen for this comparative study because Eskom’s financial loan conditions require the implementation of an SO 2Nextgeneration, affordable SO abatement for coalfired power
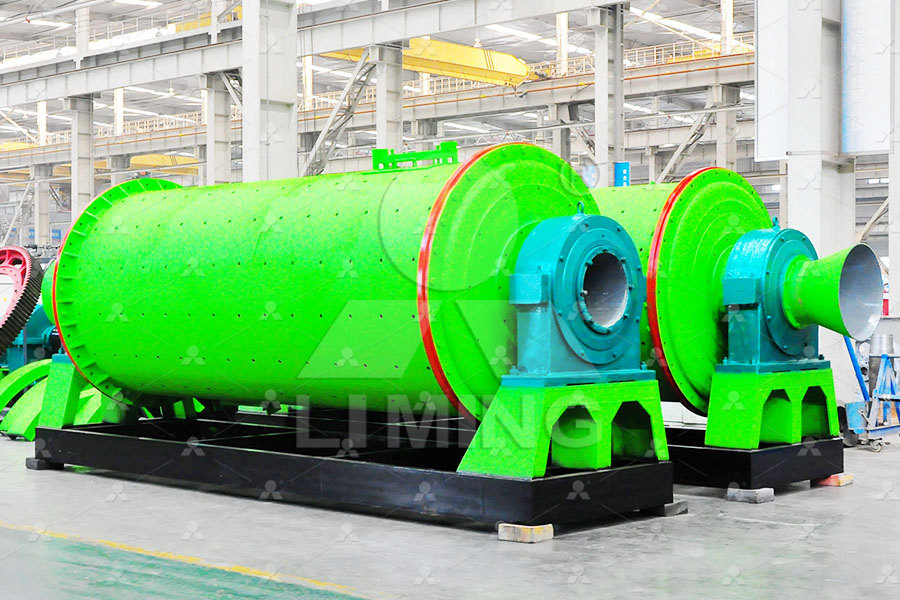
Geochemical Assessment of Antalo Limestone for Cement
2022年4月22日 standard (EN 197) limestone used as a main constituent in cement production shall meet the following requirements i) The Cacao 3 content shall be ≥ 75% by m ass