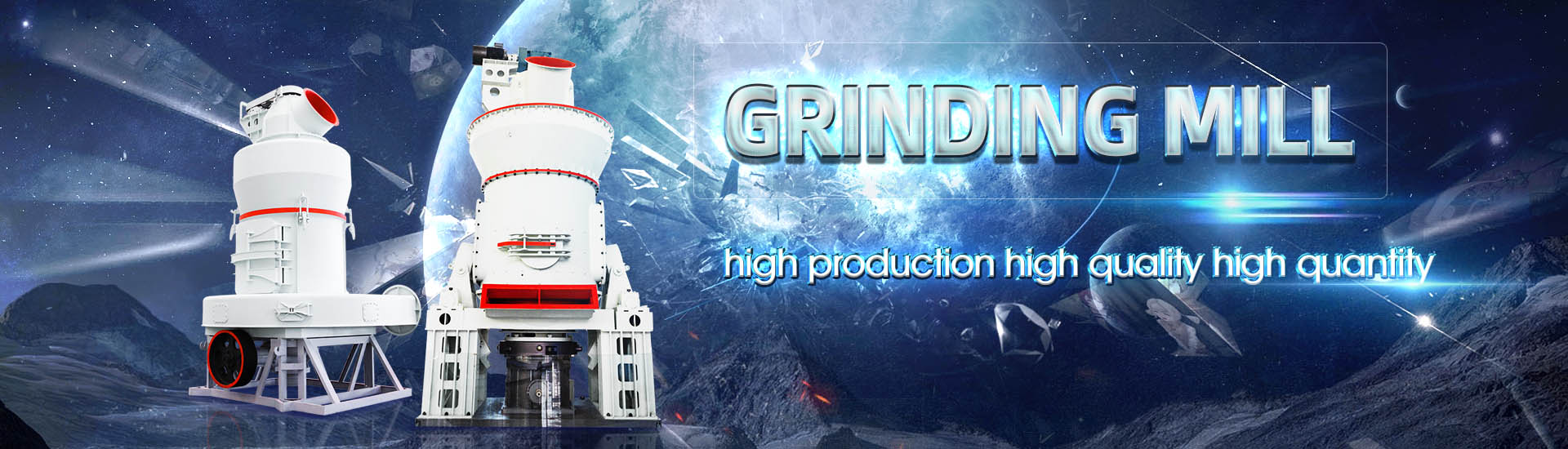
How to process aluminum ash, overhaul slag, and aluminum electrolyte into finished products
.jpg)
Research Progress of Electrolytic Aluminum Overhaul Slag Disposal
2023年4月25日 This article analyzes and summarizes the composition and hazards of the overhaul slag and the current development status of domestic and international electrolytic Coal gangue is a byproduct of the production of coalassociated minerals, Review of Research on the Pr2023年8月1日 Herein, a synergistic disposal strategy, ie, adopting the overhaul slag as a raw material together with aluminum oxide in the aluminum electrolysis process to produce Al–Si Dissolution behavior of overhaul slag from aluminum reduction 2022年12月12日 Preparation of high performance building materials from aluminum ash and carbide slag The compressive strength and flexural strength of bricks are 75 MPa and 36 Comprehensive performance study of aluminum ash and calcium
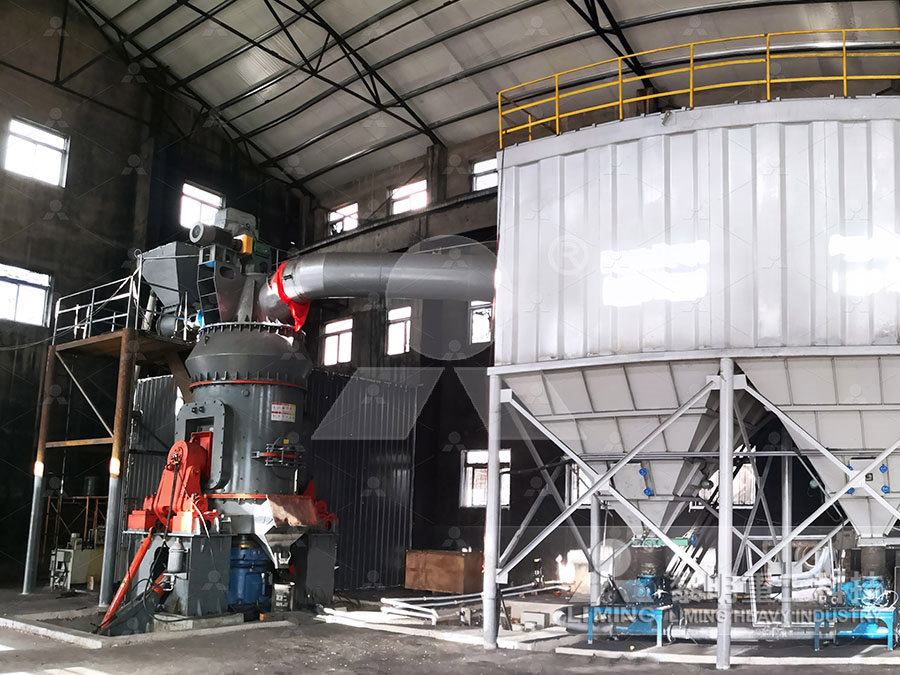
A Review of Secondary Aluminum Production and Its Byproducts
2021年7月30日 Salt slags generated from both primary and secondary aluminum production need to be recycled/treated as they are considered hazardous byproducts This review paper 2024年2月1日 The electrolytic aluminum industry generates a large amount lithium (Li)containing electrolytic aluminum slag (EAS) annually, and this can result in severe Efficient lithium recovery from electrolytic aluminum slag via an With the rapid development of aluminium smelting industry in China, millions of tons of hazardous wastes such as carbon slag, overhaul slag and aluminum ash are generated every yearPresent situation of production, utilization and disposal of Original aluminum ash (OAA) can be prepared into original aluminum ash spray powder (OAASP) through hydrolysis treatment, and the original aluminumRecycling and Utilization of the Electrolytic Aluminium Ash and Slag
.jpg)
Aluminum: Recycling and Carbon/Environmental Footprint
2020年8月18日 In their article “Alumina and Silica Produced by Chlorination of Power Plant Fly Ash Treatment,” Kaplan et al propose a process of chlorinating fly ash (using either chlorine 2024年5月23日 Treatment techniques include roasting, calcination, vacuum distillation, flotation, water leaching, acid leaching, alkali leaching, complexation leaching, and alkali fusion Waste The recycling of carbonrich solid wastes from aluminum 2023年4月25日 This article analyzes and summarizes the composition and hazards of the overhaul slag and the current development status of domestic and international electrolytic 电解铝大修渣处置研究进展2023年9月1日 Lithium (Li)bearing aluminum electrolyte slag is an inevitable byproduct of the aluminum industry, and improper disposal or stacking it may lead to potential environmental hazards This study employed hydrometallurgical Clean Process for Selective Recovery of Lithium
2FD{P}PC]854]XQ.jpg)
A Review of Secondary Aluminum Production and
2021年7月30日 Secondary aluminum production is required for the conservation of the environment It can significantly reduce greenhouse gas emissions and energy consumption and reduce the consumption of alumina Molten aluminum obtained from either of these sources is cast into ingots, billets or into a final shape Sand, permanent mold and die casting, convert the molten metal into final form requiring minimal machining Low to high volume Aluminum Production and ProcessingThe process of casting aluminum Casting is the original and most widely used method of forming aluminum into products Technical advances have been made, but the principle remains the same: Molten aluminum is poured into a mold to duplicate a desired pattern The three most important methods are die casting, permanent mold casting and sand Processing 101 The Aluminum AssociationAbout 2 million tons of aluminum slag are generated during the process of primary aluminum smelting, fabrication and processing, and waste aluminum recycling in China The main components in the aluminum slag are metallic aluminum, alumina, aluminum nitride, fluoride salts, chloride salts, as well as theTechnical Report International Aluminium
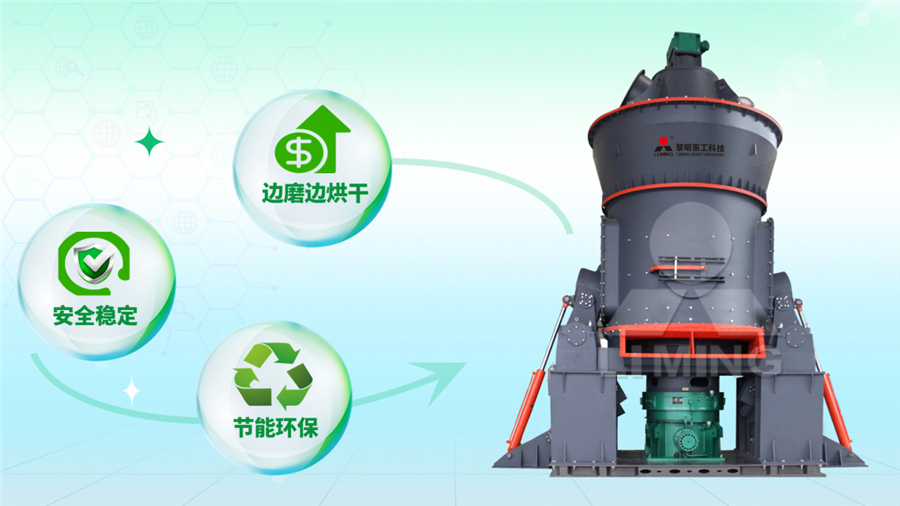
Fluorineretaining agent for overhaul slag of aluminum
2020年1月2日 The invention discloses a fluorineretaining agent for overhaul slag of an aluminum electrolytic cell The fluorineretaining agent comprises the following components of, by mass, 80100 parts of calcium sulfate, 6080 parts of calcium oxide, 5070 parts of calcium hydroxide and 3060 parts of calcium chloride The invention further discloses a method for 2022年2月26日 Blast furnace slag can be processed into the following materials by various processes In China, blast furnace slag is usually processed into water slag, slag gravel, expanded slag and slag beadsWater slag is the process of putting the hotmelt blast furnace slag into water for rapid cooling, which mainly includes slag pool water quenching or furnace front What is Blast Furnace Slag and How to Process It?2021年10月1日 Meanwhile, when the highlithium alumina is added into the aluminum electrolytic cell, Li 2 O reacts with cryolite to form lithium fluoride, which will lead to the continuous enrichment of lithium fluoride in the aluminum electrolyte with the A novel approach for lithium recovery from waste lithium 2024年6月29日 Aluminum electrolyte is a necessity for aluminum reduction cells; however, its stock is rising every year due to several factors, resulting in the accumulation of solid waste Currently, it has become a favorable material for the resources of lithium, potassium, and fluoride In this study, the calcification roasting–twostage leaching process was introduced to extract Stepwise extraction of lithium and potassium and recovery of
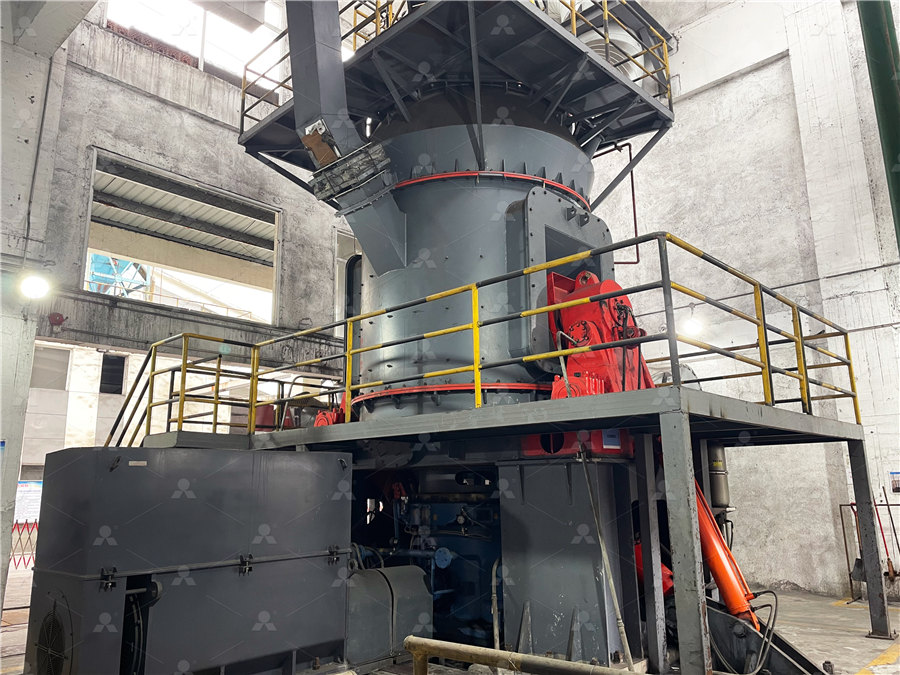
Chapter 2 Production and Processing of Aluminum The
of the cell Carbon anode blocks are suspended on steel rods, and dip into the electrolyte As the electric current flows through the electrolyte, it breaks down the dissolved alumina into its component elements as metallic aluminum and oxygen gas The oxygen reacts with the carbon anodes, forming bubbles of CO and CO 2 gas Liquid aluminum2024年6月4日 Aluminum ash slag can be divided into primary aluminum ash and secondary aluminum ash according to the different degrees of treatment Primary aluminum ash usually refers to the primary aluminum melting and casting, scrap aluminum melting, melt transfer and purification and debris removal process output of the floating slagAssessing Environmental Impact of Aluminum Ash Disposal in A consumer tosses aluminum products, such as beverage cans, in a recycling bin A recycling company collects aluminum products and transports them to a treatment facility The scrap aluminum is sorted and cleaned The scrap metal Aluminum Processing Production Explained HARBORaluminum electrolysis overhaul slag and secondary aluminum ash, through which the contained toxic substances have realized safe and rapid leach ing from slags and have been rendered completely harmless, allowing the tailing to be turned into building materials The products and tailings after disposal meet theThe Development of Aluminum Industry and Technology in China
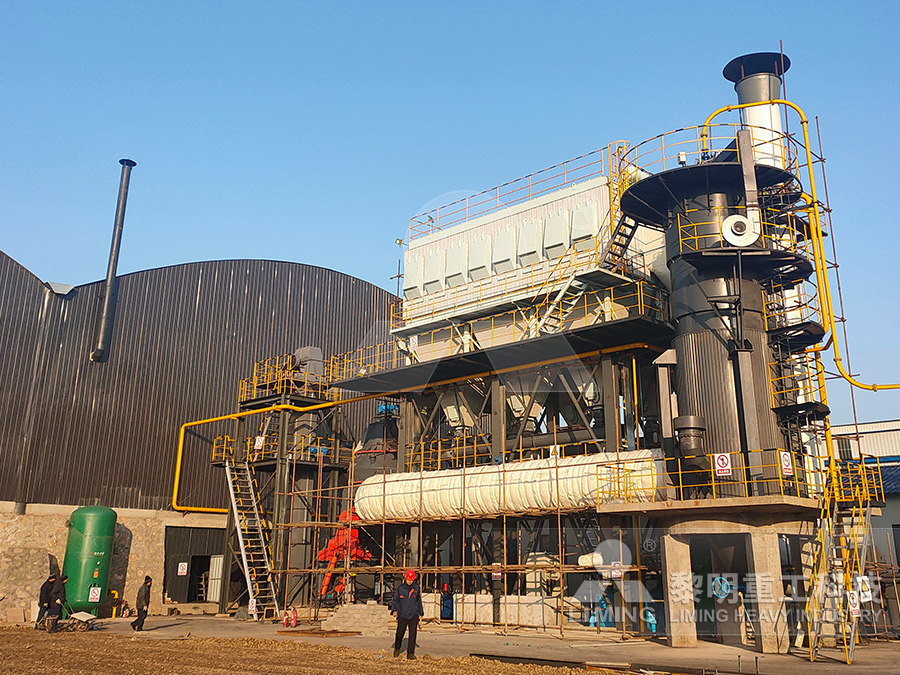
Selective preparation of lithium carbonate from overhaul slag by
2024年5月1日 The reason is that the lithium content in the overhaul slag is relatively low, and the minimum amount of sulfuric acid is enough to completely transform the lithium compound into NaLi(SO 4) More aluminum compounds are converted to NaAl (SO 4) 2, when m(H 2 SO 4)/m(overhaul slag) increase from 10 to 142022年2月5日 Effect of Temperature Under the conditions of liquid–solid ratio of 3:1 mL/g, time of 2 h, and stirring speed of 400 r/min, the influence of temperature on the removal effect of nitrogen, fluorine, and chlorine impurities in the washing process of aluminum dross was exploredRemoval of Fluorine, Chlorine, and Nitrogen from Aluminum The main components of aluminum ash include single aluminum, aluminum oxide (Al 2 O 3), aluminum nitride (AlN), aluminum carbide (Al 4 C 3), fluoride and chlorinated salts, silicon, iron and other oxide (Kang et al 2022) Aluminum ash slag can be divided into primary aluminum ash and secondary aluminum ash accordingAssessing Environmental Impact of Aluminum Ash Disposal in Handbook Aluminum, 2022 This Handbook / Guidance Note has been prepared to identify and flag issues a prudent underwriter ought to consider and evaluate relating to the aluminum industry risk selection, determination and calculation of loss estimates when deciding whether to accept a risk and, if so, on what termsChapter 2 Production and Processing of Aluminum 21 Extraction of Aluminum
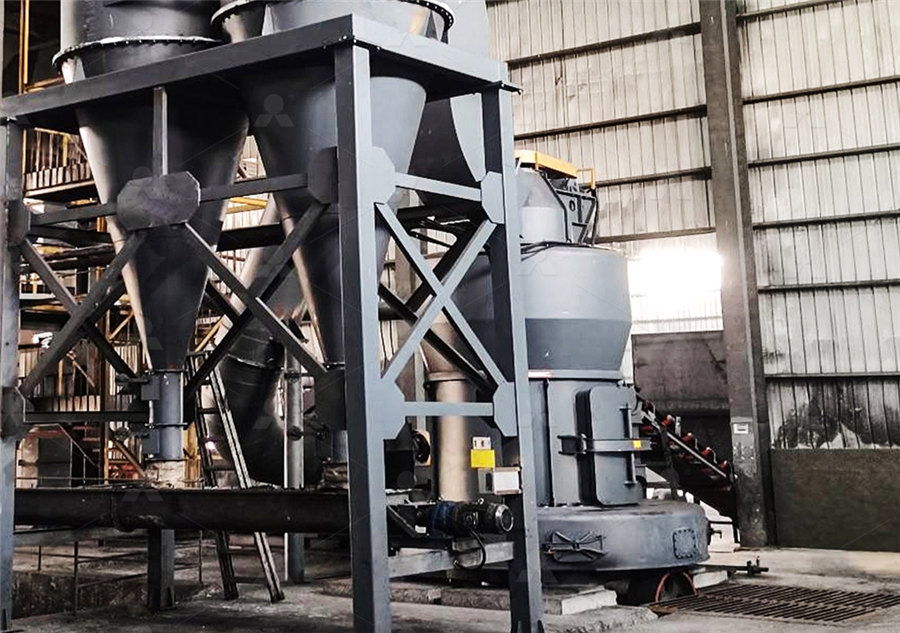
Dissolution behavior of overhaul slag from aluminum reduction
2023年8月1日 The full alumina dissolution process in aluminum electrolysis cells was investigated using an improved computational fluid dynamics (CFD) model based on the previous researches by consideration of 2021年8月9日 3 Correctly select and use refining agent to fully separate aluminium and dross In the process of smelting aluminum and aluminum alloys, in addition to its own inclusions, aluminum can easily form alumina or subalumina with oxygen, resulting in a layer of scum on the surface of the aluminum liquid, which has a certain degree of wettability with the aluminum meltHow to reduce burning loss effectively in aluminum melting2023年4月25日 大修渣作为电解铝行业的主要固体废弃物,含有大量的危害物质,如何对其无害化处理并高效回收其中有价值物质,是近些年铝行业亟待解决的难题。本文分析总结了大修渣的成分、危害及目前国内外电解铝大修渣处置的发展状况,并指出了我国电解铝行业危险废物处置的发 电解铝大修渣处置研究进展2018年10月1日 Their process consists of four steps: 1) crushing initial black dross by a jaw crusher into pieces smaller than 1 mm, and the recovery of aluminum metal through screening, 2) ball milling the material to sizes less than 100 μm and recovery of remaining aluminum metal, 3) recovery of soluble salts at atmospheric pressure through washing dross with water at 90 °C, Hazardous aluminum dross characterization and recycling
.jpg)
How to Process Slags (with detailed process)? Fote
2023年2月15日 Slag bricks Slag brick production process Slag brick is made by mixing, watering, grinding and pressing slag and limestone In the production process of slag brick, the particle size of the slag is generally smaller than 8 2021年5月1日 Aluminum Slag Separation Process Analysis Through a Vibratory Machine in the Foundry Process May 2021 International Journal for Innovation Education and Research 9(5):104120(PDF) Aluminum Slag Separation Process Analysis With the rapid development of aluminium smelting industry in China, millions of tons of hazardous wastes such as carbon slag, overhaul slag and aluminum ash are generated every year In order to promote the refined management of hazardous wastes in China, an indepth research had been done, the current generation process link, pollution characteristics, utilization and Present situation of production, utilization and disposal of 2024年4月17日 Recycling plays an important role in today's world due to its considerable contributions to mitigating energy concerns and environmental challenges One of them is dross recycling from aluminum (Al) cast houses Unlike other recyclable materials, dross has an abundance of components, including rare earth elements, heavy metals, ferrous, and recycled Aluminum dross: aluminum metal recovery and emerging
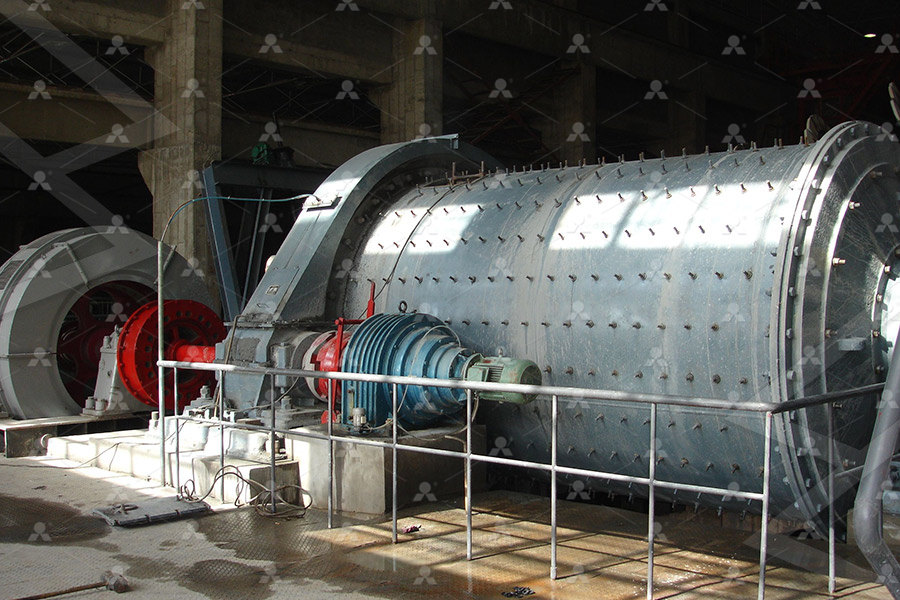
A novel approach for extracting lithium from overhaul slag by low
2024年2月1日 Overhaul slag contains a rich variety of substances that need to be purified and cleaned, so this paper considers H 2 SO 4 as an additive to extract valuable substances On this basis, the extraction mechanism of lithium, fluoride and aluminum from overhaul slag using sulfuric acid roasting water leaching process was proposed2015年2月1日 Download Citation Aluminum extraction from coal ash by a twostep acid leaching method To improve aluminum extraction efficiency, a twostep acid leaching process was proposed to dissolve Aluminum extraction from coal ash by a twostep acid2023年10月1日 The aluminum electrolyte is the core part of the electrolytic production process of aluminum In contrast, lithiumrich aluminum electrolytes can cause problems such as reduced production temperature, decreased alumina solubility, increased precipitation at the bottom of the electrolytic cell, and poor stability in the aluminum electrolytic cell [7,8]A novel approach for ultrasonic assisted organic acid leaching of 2022年12月26日 Aluminum processing, using plastic processing methods to process aluminum ingots into materials, the main methods are rolling, extrusion, stretching and forging Aluminum products have been serialized, and can produce eight types of products, including plates, strips, foils, pipes, bars, profiles, wires and forgings (free forgings, die forgings)How to choose the right Aluminum Fabrication Process
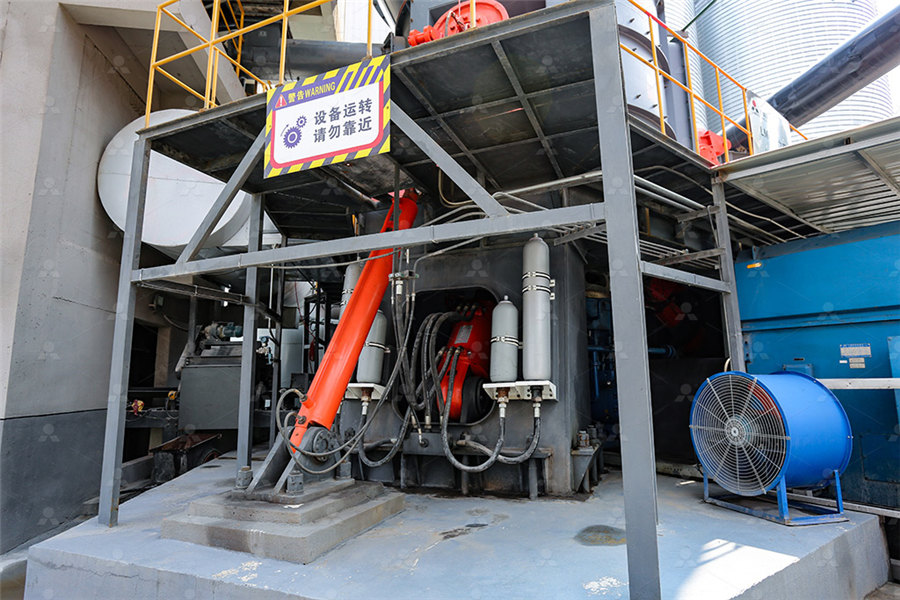
Sustainable Recovery of Fluorine from Waste Aluminum Electrolyte
2023年8月2日 The highvalue, green and harmless purification of aluminum electrolysis comprehensive solid waste can not only reduce its harm to the environment and soil but also separate and recover the highvalue rare elements This study aims to develop a process for recovering and treating waste aluminum electrolytes by sulfuric acid roasting The results of 2024年2月1日 Overhaul slag contains a rich variety of substances that need to be purified and cleaned, so this paper considers H 2 SO 4 as an additive to extract valuable substances On this basis, the extraction mechanism of lithium, fluoride and aluminum from overhaul slag using sulfuric acid roasting water leaching process was proposedA novel approach for extracting lithium from overhaul slag by low 2023年10月1日 The main treatment methods of waste aluminum cryolite electrolyte can be divided into two categories: combined thermalwet treatment and hydrometallurgical process To recover valuable elements such as lithium from waste aluminum electrolyte, Wu et al (2021) mixed Na 2 CO 3 with waste aluminum electrolyte and roasted them at 650 °C for 25 h, and Efficient extraction and recovery of lithium from waste aluminum aluminum processing, preparation of the ore for use in various products Aluminum, or aluminium (Al), is a silvery white metal with a melting point of 660 °C (1,220 °F) and a density of 27 grams per cubic cm The most abundant metallic element, it constitutes 81 percent of Earth’s crust In nature it occurs chemically combined with oxygen and other elementsAluminum processing History, Mining, Refining, Facts
.jpg)
Research on the Preparation Parameters and Basic Properties of
Materials 2023年5月20日 Due to chemical corrosion and erosion by molten aluminum liquid and electrolyte, the carbon anode of the aluminum electrolytic cell would fall off into the electrolyte during the primary aluminum electrolysis process to produce spent anode carbon (SCA), which has been listed as one of the typical hazardous solid wastes in the National Hazardous Waste Regeneration of raw materials for aluminum electrolysis from How To Separate Cold Aluminum Ash And Aluminum Slag Oct 17, 2020 The waste ash generated after aluminum is aluminum melting furnace aluminum, and waste ash is divided into hot and cold aluminum ash and cold aluminum slag depending on the output time The waste has a considerable amount of aluminum ash content and can be separated and recycledHow To Separate Cold Aluminum Ash And Aluminum Slag2020年7月5日 Experiments were conducted to investigate the process of aluminum and lithium extraction from highalumina coal fly ash (HCFA) generated from coalfired power plants located in northern China The presence of mullite and other aluminosilicates lead to low reactivity of coal fly ash An activation pretreatment that destroys an inert composition of coal is necessary The Activation Pretreatment and Leaching Process of HighAlumina
.jpg)
Extraction of Aluminum from Coal Fly Ash Using Pressurized
2021年6月30日 This study aims to extract aluminum from coal fly ash using pressurized sulfuric acid (H2SO4) leaching and to investigate the dissolution mechanism during the leaching process2020年6月17日 During the aluminum smelting, when the radius of A1203 is reduced from 01mm to 0001mm, the required standing time is increased from 5s to 138h, that is, it is unfavorable for the slag to float or sink Aluminum alloys are usually allowed to stand for 20 to 30 minutes, but the slag removal effect is still very limitedAluminium Slag Removal Methods alalloycastingSpent aluminum electrolyte slag is a byproduct produced during the electrolysis of aluminum and contains elements such as F, Al, Na, and Li It is a toxic and harmful substance with a stable and complex structure As a consequence of fluorine pollution and low lithium recovery efficiency in the traditional hydro metallurgy process, a novel cleaner production technology was developed Cleaner Process for the Selective Extraction of Lithium from Spent