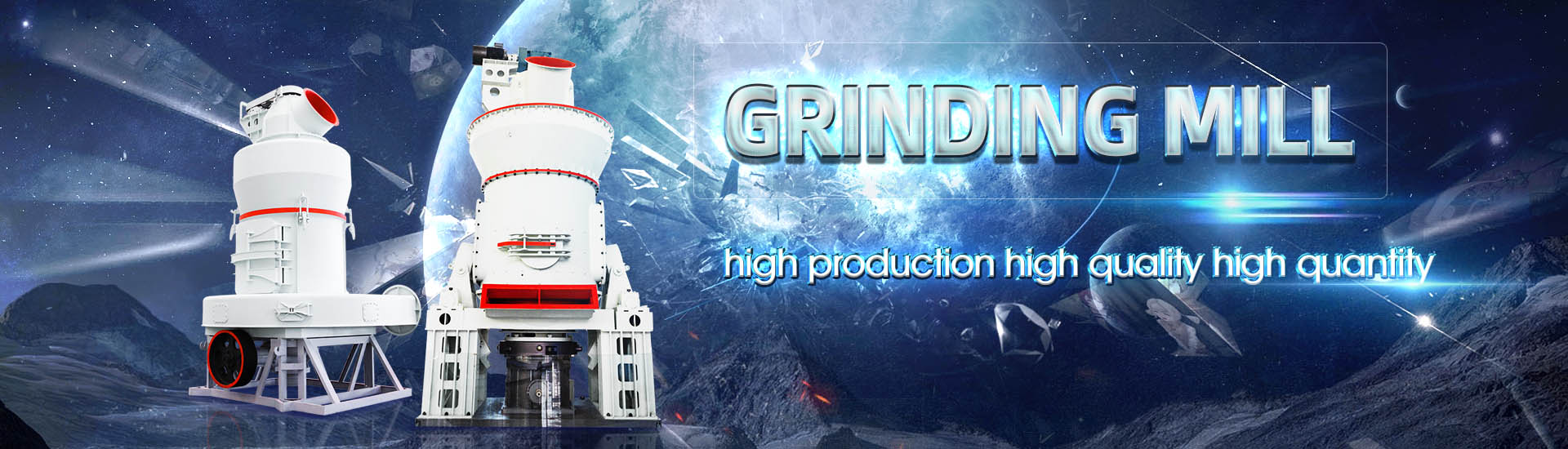
How much is the speed of the silica mill
.jpg)
Comparative Study on Improving the Ball Mill Process Parameters
2021年2月19日 The optimum process parameters setting concluded that balls to powder weight ratio are 20:1, the optimum ball mill working capacity is 2 L while the optimum speed of the ball mill is 105 rpm Using SEM characterization, the improved particles of silica sand presented a 2008年8月26日 The size reduction and mechanochemical effect of silica take place simultaneously as the jet mill is an energy intensive grinding mill The minimum particle size Mechanochemistry of silica on jet milling ScienceDirectTwo types of silica powder with different structures, one crystalline (C1) and one amorphous (A1) were mechanically treated using a planetary type mill Three different rotation speeds (100, Mechanical modification of silica powdersSince the speed of revolution of the mill has a very great effect on the rate of grinding, the first factor to be studied should be the speed of the mill A set of experimental results relating to the The Mechanism and Grinding Limit of Planetary Ball Millingt J

Parameter Optimization of Ball Milling Process for Silica
2019年3月1日 The results of signaltonoise analysis obtained the optimum parameter values in a row are: 100 rpm for milling speed parameter, 15: 1 for BPR parameter and 120 minutes for 2019年12月13日 Parameter Optimization of Ball Milling Process for Silica Sand Tailing To cite this article: Sukanto et al 2019 IOP Conf Ser: Mater Milling Speed [rpm] C 100 160 205 PAPER OPEN ACCESS Parameter Optimization of Ball Milling The optimum condition of the silica sand milling that was obtained shows that the rotating mass is the most important parameter which affects milling time It is also found that 1500 RPM of rotational speed with 16 mm ball diameter and 222 g (PDF) EXPERIMENTAL STUDY OF THE EFFECT OF BALL 2020年7月2日 When the mills charge comprising 60% of small balls and 40% of big balls, mill speed has the greatest influence on power consumption When the mill charge is more (PDF) Effects of Ball Size Distribution and Mill Speed and Their
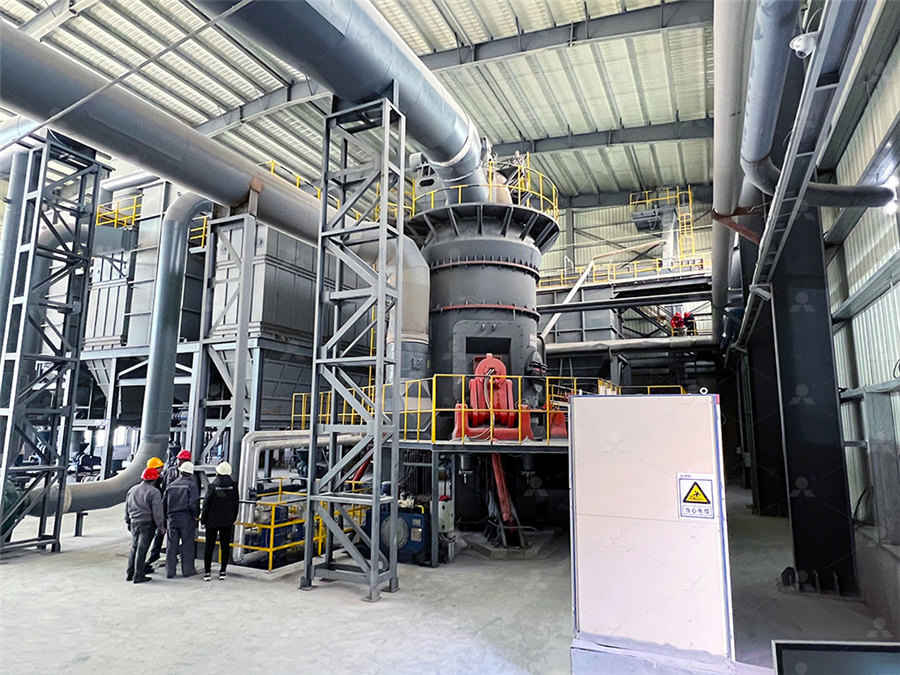
Process Breakthrough Makes Fumed Silica EasyTo
2022年8月1日 Thanks to an innovation in the production process of fumed silica by Evonik Resource Efficiency GmbH, standard fumed silica technology routinely used by the coatings industry can now undergo wetting and dispersion 2023年8月10日 Features of silica sand rod mill: Feed particle size: ≤50 mm Cylinder speed: 35 r/min Used to remove magnetic impurities in silica sand and improve the purity of silica sand When the magnetic field intensity is Silica Processing Plant 4 Major Stages to Make Silica 2019年6月4日 Silica particles improve thermal and electrical isolation [5][6][7] and increase the Young's modulus, resulting in reduced elongation of the composite material [6](PDF) The Effects of SilicaBased Fillers on theAlthough Chastain said this might not matter much on a small project, it can have a significant impact on an interstate project Furthermore, poor milling quality is going to cause compaction numbers to fluctuate “Say we’re doing a thin lift Maximize Milling with these Best Practices AsphaltPro
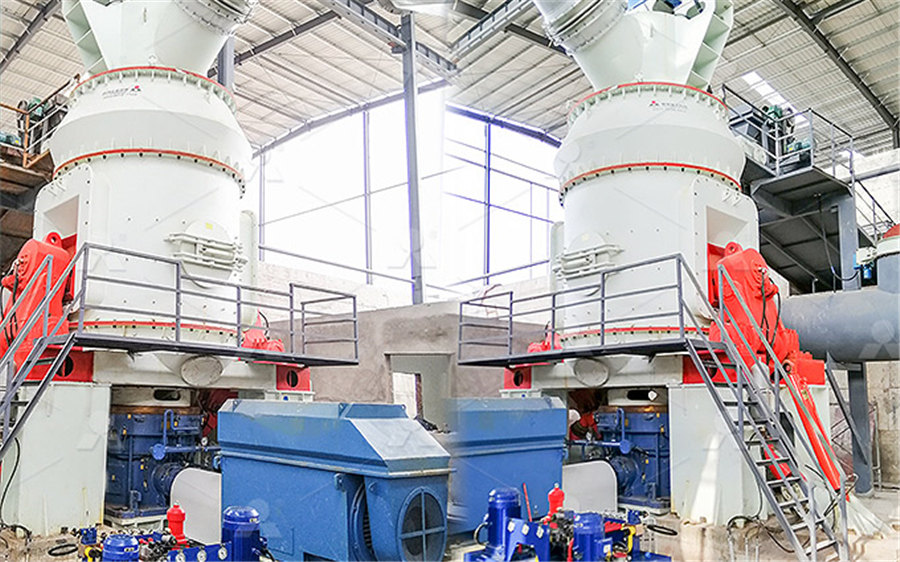
EVERYTHING YOU NEED TO KNOW ABOUT THE CHEMISTRY OF
Introduction of water into the mill along with the feed results in the formation of a slurry After grinding, dry kiln feed or slurry is drawn from storage and fed into the rotary kiln CHEMICAL AND PHYSICAL The higher the ratio, the harder the burning Iron has a favorable influence on the speed of reaction between lime and silica; Silica Modulus (SM) Kiln Speed should be such that volumetric loading is within the range 1015% and heat transfer is maximized Precalciner kilns generally rotate at 3545 rpm Under normal conditions, kiln should be run with as high rpm as possible Cement Mill FeedingClinkerization Cement Plant Optimization2008, Minerals Engineering Fine grinding of silica was carried out in a jet mill, varying operational parameters such as feed rate, classifier rotational speed and grinding pressureEffect of operational parameters on the breakage mechanism of silica 2023年1月12日 In this study, silica nanoparticles (SiO2 NPs) were fabricated using a handmade ball mill as a novel, simple, rapid, costeffective, and green approach The sol–gel method was also used to produce these NPs as a comparative method The SiO2 NPs produced by both methods were characterized using highresolution transmission electron microscopy Facile, fast, and green preparation of highpurity and quality silica
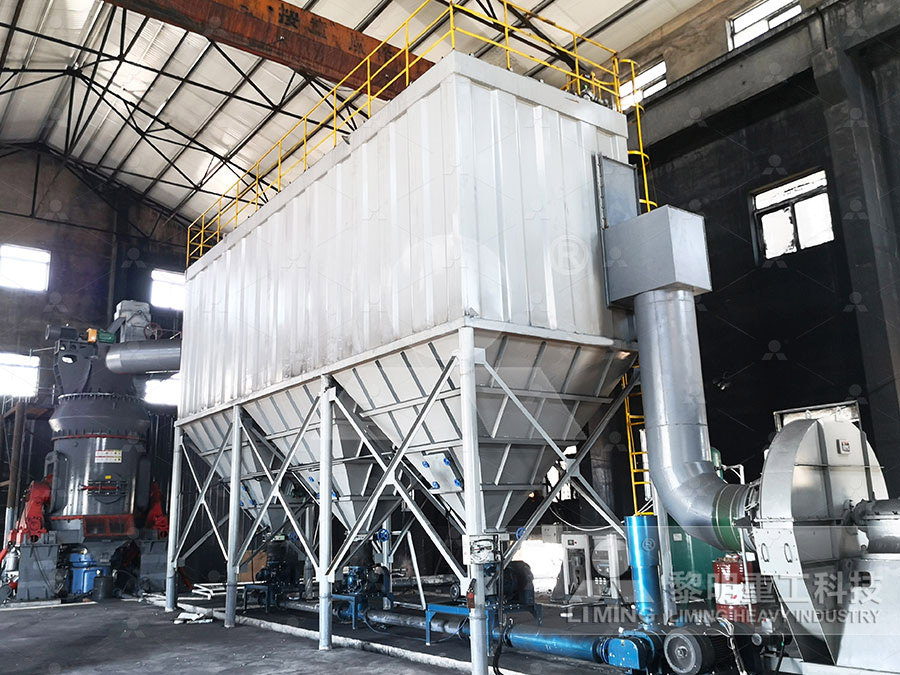
Abstract and Figures ResearchGate
2020年1月13日 The industrial dynamic matrix controller commissioned on the AG mill with a variable speed drive resulted in a 66% reduction in power and a 40% reduction in load standard deviation These are the The work input to a mill increases in proportion to the speed, and ball mills are run at as high a speed as is possible without centrifuging Normally this is 70–80% of the critical speed Read moreBall Mill an overview ScienceDirect TopicsSome of the most commonly used desiccants include silica gel, molecular sieves, clay, and calcium chloride Silica gel packets are useful for regular packaging and can hold up to 40% of their weight in water vapor Molecular sieves are particularly suitable for use in conditions where precise pore size is necessary because of their uniform pore How Much Desiccant Do I Need? The Ultimate Guide Jalon2024年2月13日 Feed Rate, Spindle Speed (RPM), Cutting Speed (Surface Speed), and Chip Load The variables that you need to determine for your operations are your spindle speed (RPM) and feed rate (IPM) In doing this, CNC Feeds Speeds Formula (How to Calculate Feed
.jpg)
Selected Advances in Modelling of Size Reduction in Ball Mills
2023年9月22日 To meet these two requirements, researchers have focused on two tasks The first task is establishing the optimum values of various mill design and operating variables, such as the mill speed, ball load, particle load, and ball diameter [4,5,6,7,8,9,10,11]2017年5月14日 The silica (SiO2) Find, read and cite all the research you need on 113 g media weight and 8 hr milling period at 400 rpm mill speed The SiO2 NPs obtained were characterized by CHARACTERIZATION OF SILICA NANOPARTICLES Shear is required to obtain functionality The dispersion equipment used has as much of an effect on the viscosity obtained as the concentration of fumed silica This must be taken into account when formulating products or altering processing conditions Vigorous intank movement must be maintained as the viscosity risesImprove Fumed Silica Processing with High Shear Mixing SilversonDIFFERENT MILLS REQUIRE DIFFERENT AMOUNTS OF MEDIA •BASED UPON WORKING VOLUME OR TOTAL VOLUME •Mills such as the Immersion Mill have a fixed amount determined by size of the basket •Steel Ball Mill 333% •Open Head Sand Mill 3545% •Ceramic Pebble Ball Mill 50% •Dry Grind Batch Attritor 4560% •Wet Grind Batch Attritor 3845% •Continuous How to Choose the Correct GRINDING MEDIA PCI Mag
.jpg)
(PDF) EXPERIMENTAL STUDY OF THE EFFECT OF BALL DIAMETER
Impact Factor (JCC): 88746 SCOPUS Indexed Journal NAAS Rating: 311 Experimental Study of the Effect of Ball Diameter, Rotating Mass and Input Grain Size of Silica Sand on the Efficiency of Milling in Vertical Vibrating Mill 359 Varying the rotational speed has different effects depending on the ball’s diameter and the mass of the rotating mass2019年3月1日 The potential waste generated from each ton of fresh oil palm fruit conversion into CPO consists of palm oil mill effluent (POME), which accounts for 67%, empty fruit bunches (EFB), which account Production and characterization of precipitated silica from 2019年9月10日 where [c] represents the activity or concentration of a reactant, k the rate constant [mol(mol/m 3) – n /(m 2 s)], n the order of the reaction, E A the activation energy (kJ/mol), R the gas constant (kJ/mol/K), and T the temperature (K)A is the specific surface area (m 2) and (1−Q/K) the chemical affinityRates are expressed in mol s –1 Measured quartz Frontiers An Overlooked Silica Source of the Modern Oceans: 2018年5月24日 Silica and its role in the production of iron and steel Silicon, the element, because the transformation velocity of quartz to cristobalite is much faster than to tridymite Above around 1470 deg C, tridymite is converted to cristobalite which melts at 1713 deg CSilica and its role in the production of iron and steel
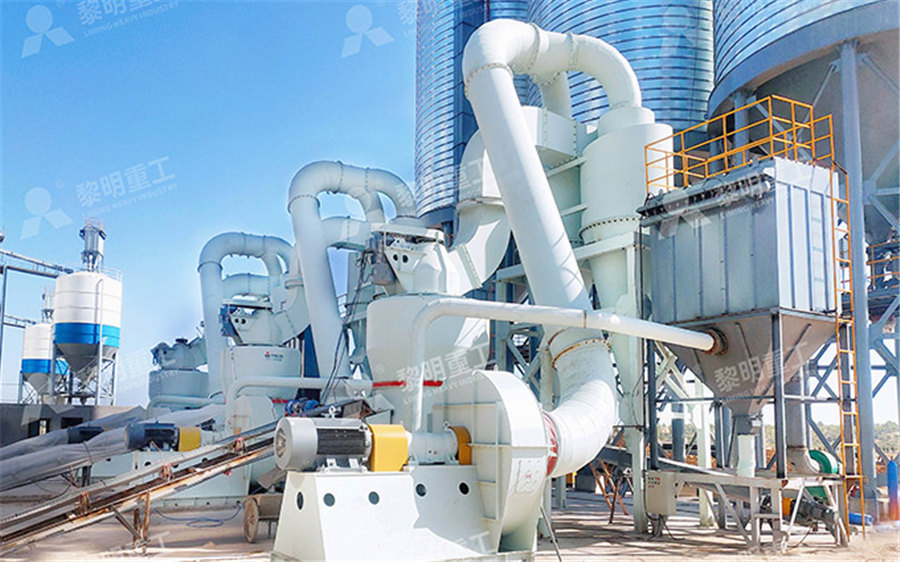
Effect of operational parameters on the breakage mechanism of silica
The number of impulses in the jet mill depended on the geometry of the chamber, the nozzle configuration and physical properties of the colliding particles The jet mill transfers specific grinding energies of 10–40 kW h/ ton per cycle, which 2022年9月30日 HighSpeed Disperser: An Updated Practical Guide By Herman Hockmeyer Updated on September 30, 2022: Thanks to popular demand, we’ve updated this guide to highspeed dispersers to serve as a helpful resource for Practical Guide to HighSpeed Dispersions2008, Minerals Engineering Fine grinding of silica was carried out in a jet mill, varying operational parameters such as feed rate, classifier rotational speed and grinding pressureEffect of operational parameters on the breakage mechanism of silica 2017年7月26日 We will consider an ore with a ball mill work index varying between 16 and 13, feeding into a single stage ball mill operation with one million kilowatts per day consumed power For the particular mill configuration, a performance graph, Fig (21), has been constructed according to Bond’s methodsHow Ball Mill Ore Feed Size Affects Tonnage Capacity
.jpg)
Ball Mill Grinding Capacity Calculator 911 Metallurgist
Rotational Mill Speed, expressed as a percentage of the critical centrifugation speed of the mill Mill rpm : L/D : Effective Length to Diameter Ratio % Solids in the Mill : Ore Density, ton/m3 : Slurry Density, ton/m3 : Balls Density, ton/m3 : Charge % Filling : A) Balls % Filling : B)2015年6月2日 NS was made using various procedures such as chemical precipitation process, solgel technique, vaporization with high temperature, and speed of the vertical rotating mill and planetary and ball (PDF) Synthesis of silica nanoparticles from malpe beach sand End Mill Feeds and Speeds The most important aspect of milling with end mills is to run the tool at the proper RPM (revolutions per minute or spindle speed) and IPM (inches per minute or feed rate) We have broken these recommendations down into material categories so you can make better decisions with how to productively run your end millsMilling Speeds And Feeds: Charts Data 6gTools2008年4月1日 Fine grinding of silica was carried out in a jet mill, varying operational parameters such as feed rate, classifier rotational speed and grinding pressureEffect of operational parameters on the breakage mechanism of silica
.jpg)
IMPROVING THE PAPER RECYCLING PROCESS OF OLD
be of much help in the future development of the pulp and paper industry is nanotechnology Papermaking industry is already a leader in terms of the amounts of nanoparticles used 3 In this respect, colloidal silica nanosized particles have been extensively applied in papermaking Papermakers employ nanosilica and related2020年6月24日 HCH superfine grinding mill is for micron powder processing, it has the mechanical performance such as rolling, grinding and impact, fineness of the final powder can be adjusted arbitrarily How Much Is The Silica Grinding Mill?2021年6月29日 The research focuses on the mill speed as Find, read and cite all the research you need on ResearchGate Home; 2017), silica fume (Behnood and Golafshani, 2018), and Effects of Mill Speed and Air Classifier Speed on Performance of Use this desiccant calculation chart to determine how much desiccant you may need This is only an estimate The desiccant calculation chart below is specifically for estimating how much clay or silica gel desiccant you need This does not apply to molecular sieve desiccantDesiccant Calculation Chart How Much Desiccant Do You Need?
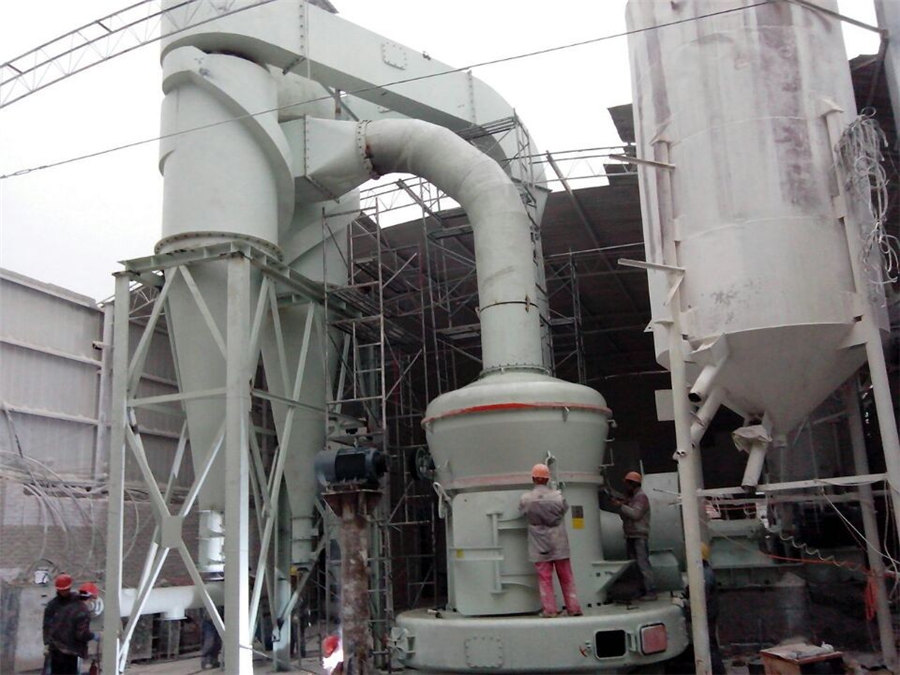
Full article: How Advancing are Mesoporous Silica
2022年4月22日 The average particle size of the silica powders was around 70 nm, which decreases with increasing ballmilling time or mill rotational speed Citation 55 Finally, Utama PS, Yamsaensung R, Sangwichien C Silica gel 2019年3月1日 In the present paper, the influence of silica, which is present in the passenger car tires granulate, on both devulcanization and subsequent revulcanization, is investigatedImplications of the Use of Silica as Active Filler in 2015年6月19日 The basic parameters used in ball mill design (power calculations), rod mill or any tumbling mill sizing are; material to be ground, characteristics, Bond Work Index, bulk density, specific density, desired mill tonnage capacity DTPH, operating % solids or pulp density, feed size as F80 and maximum ‘chunk size’, product size as P80 and maximum and finally the type of Ball Mill Design/Power Calculation 911MetallurgistSince the speed of revolution of the mill has a very great effect on the rate of grinding, the first factor to be studied should be the speed of the mill A set of experimental results relating to the grinding of silica sand using of 4 mm steel balls at three speeds, namely, 6 Hz, 805 Hz and 1167 Hz, are given in Fig 4The Mechanism and Grinding Limit of Planetary Ball Millingt
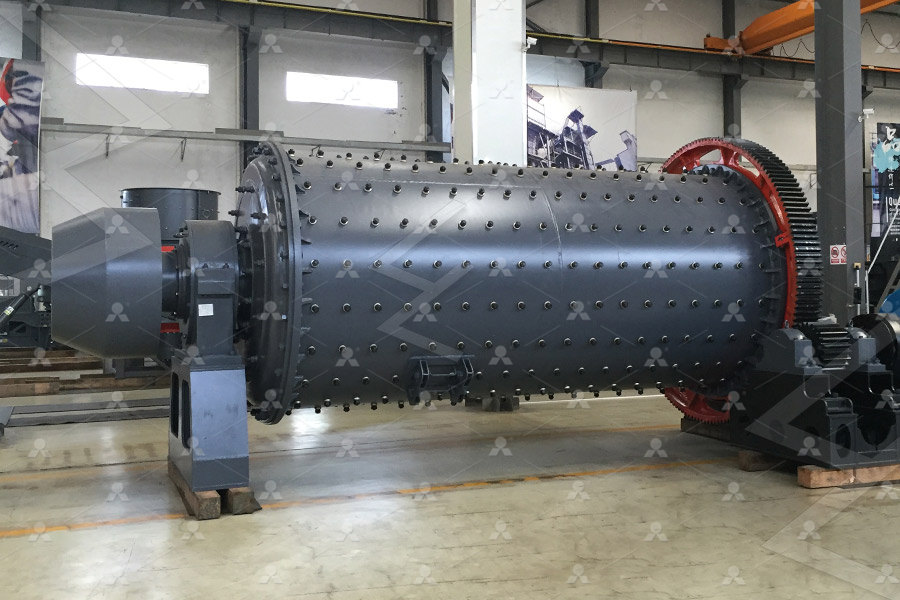
How does the speed of ball mill affect productivity
Lowspeed mills operate at around 6001200 revolutions per minute (RPM), while highspeed mills typically operate at around 3000 RPM or higher While there are definite benefits to using a highspeed ball mill over a lowspeed mill, it's important to note that not all products are best suited for highspeed milling2014年4月30日 Lastly, the elevated presence of silicon (Si) in PMS may result from high silica content observed in some paper mill effluents (Latour et al, 2014)(PDF) Silica removal in industrial effluents with high silica 2021年4月29日 Most of the pulp and paper mill wastes in developing countries adopt recycling for lower grade paper; recycling being the only used pulp and paper mill waste utilization method The scope and technology for utilization of the different wastes for other industrial applications are practically not available and not attempted (Raut et al 2012 ; de Alda 2008 )Pulp and paper mill wastes: utilizations and prospects for high 2019年12月9日 Abnormalities and Failures of Rolling Mill Rolls satyendra; December 9, 2019; 6 Comments ; banding, Barrel, Fire cracks, Pressure cracks, Roll failure, Roll hardness, Roll journal, Roll neck, Saddle spall (decreasing solidification speed with Abnormalities and Failures of Rolling Mill Rolls – IspatGuru
.jpg)
Tower Mill Operating Work Index 911Metallurgist
2016年6月3日 The normal top size of balls in a Tower Mill is 25mm For ultrafine grinding, much smaller media can be utilized A summary of some of the ultrafine applications follows: Silica from 37 microns average to 17 microns average particle size