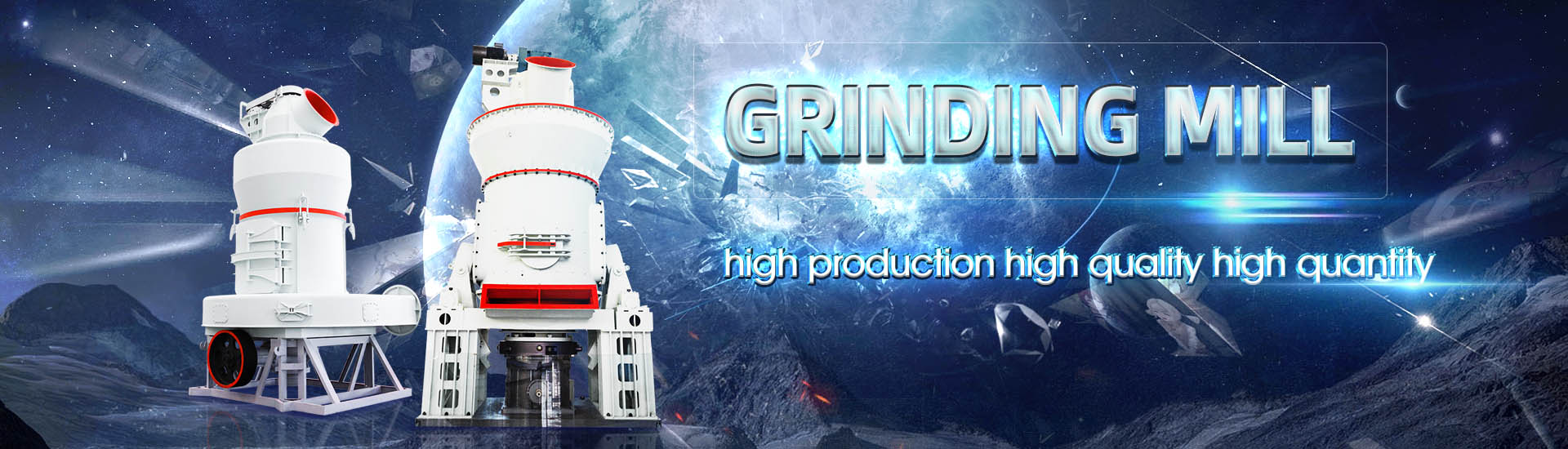
Design of Limestone Secondary Dust Removal System in Cement Plant
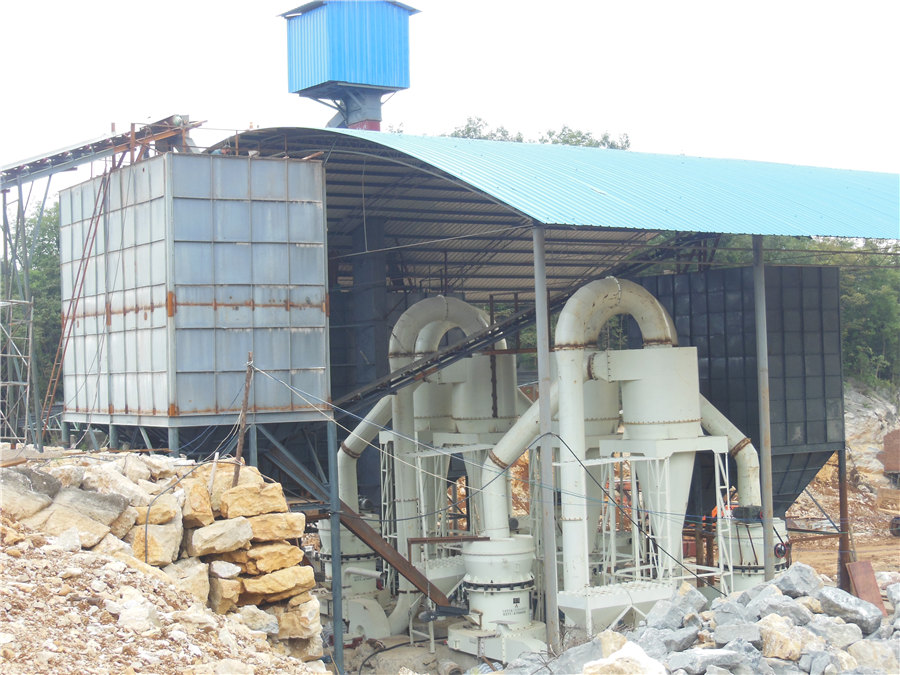
Design of Dust Removal System for Concrete Mixing Plant
This article explores the source of dust in concrete stations from the aspects of material feeding and storage in the concrete production process, analyzes the characteristics of dust, and proposes a design idea to improve the efficiency of dust removal in concrete production based 2018年3月1日 From the beginning of the plant operation up to the end of 2015, the dust removal was rely on electrostatic precipitator (EP) system Whenever limestone from specific quarry zones wereImprovement of cement plant dust emission by bag 2018年3月1日 Whenever limestone from specific quarry zones were incorporated into Raw Mill (RM) feed or there was an upset condition, the dust emission increased significantly Beside Improvement of cement plant dust emission by bag filter systemFrom the beginning of the plant operation up to the end of 2015, the dust removal was rely on electrostatic precipitator (EP) system Whenever limestone from specific quarry zones wereImprovement of cement plant dust emission by bag filter system
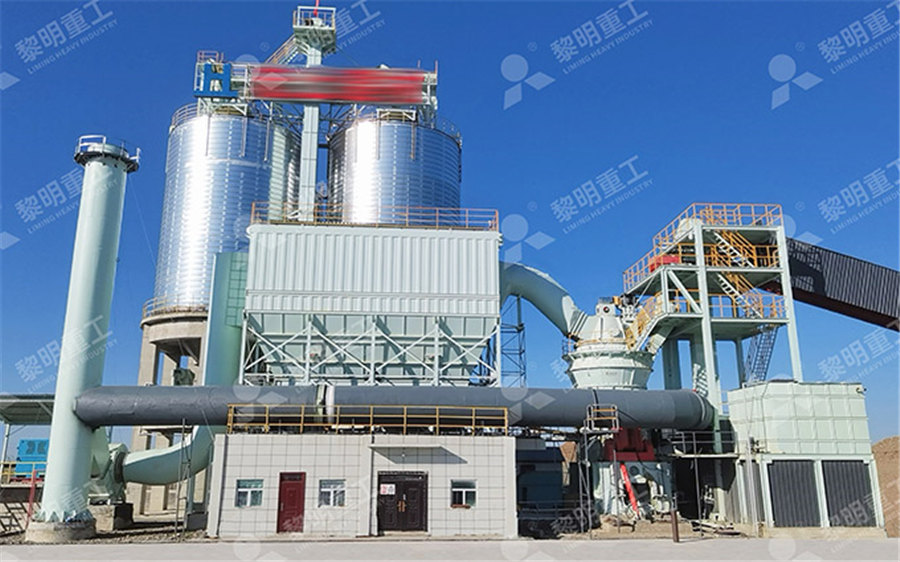
Recycling of Basalt and Limestone Cutting Dust in Concrete Mix
2023年5月1日 Objectives: The goal is to integrate stone cutting waste into the concrete manufacturing industry to reduce environmental degradation Methods/Analysis: Two types of This paper introduces the design of crushing and dust removal of limestone acceptance pit in a 5 000 t/d cement EPC project in Cambodia, and probes into the basic idea and specific process Design of crushing and dust removal of limestone receiving pit in remove and recycle the dust as this reduces cement loss and the adverse effects of cement dust to the environment Loading processes, however, have equipment like dustless loading spouts Design Of A De Dusting System In A Cement Manufacturing 2018年11月1日 A strategy for the effective recycling of quarry dust does not only reduce waste generation and disposal, but also addresses protection of the environment The Italian Quarry limestone dust as fine aggregate for concrete
.jpg)
AIR POLLUTION CONTROL CONTROL OF DUST EMISSION IN
A system of 12” Industrial lMachinery screw conveyors below the electrical precipitators transfers dust to either of two dust handling installations In one, for low alkali material, the dust is The main goal of this research project is to evaluate the efficiency of limestone powder as a partial cement replacement, in order to reduce energy consumption and CO 2 emissions This study Evaluation of the Efficiency of Limestone Powder in Concrete and Second, a cement plant does not contain a low pressure steam cycle, as in a coal power plant or natural gas combined cycle system The low pressure steam loop is often considered an energy source for the post combustion capture of CO 2 Third, the cement plant uses its exhaust gases for direct heat exchange to dry the incoming raw mealCement Plant an overview ScienceDirect Topics2020年7月14日 Aiming to solve the dust pollution in mechanized excavation face, the integrated vortex ventilation and dust removal system is designed based on swirling jet flow theory The design principles and technological parameters Study of integrated vortex ventilation and dust
.jpg)
Crushing Plant Design and Layout Considerations 911 Metallurgist
Good geotechnical information is essential to crushing plant siting and design Installing a primary crushing plant on solid rock reduces the cost of concrete and structural steel Life of Mine/Expansion Plans The life of the mine is a key element in the design of any crushing plant Shortterm mine livesPLANT DESCRIPTIONS ASH GROVE LIME PORTLAND CEMENT CO Chanute, Kansas Plant MONARCH CEMENT CO Humboldt, Kansas Plant DEWEY PORTLAND CEMENT CO Tulsa, Oklahoma Plant AIR POLLUTION CONTROL CONTROL OF DUST EMISSION IN CEMENT PLANTS May 1967 PORTL+ND CIZhlENT ASSOCIATION RESEARCH ANTD AIR POLLUTION CONTROL CONTROL OF DUST EMISSION IN CEMENT 2020年9月29日 SYSTEM DESIGN IN A TURKISH CEMENT PLANT VIA NEURAL AND NEURO Efficient way to control and limit primary and secondary and consists of a mixture of homogeni zed limestone, clay s lag Performance analysis of novel air pollution forecasting system design PDF On Apr 1, 2016, Akshey Bhargava and others published Design of Bag Filter for the Control of Dust Emissions for a Cement Plant Find, read and cite all the research you need on ResearchGateDesign of Bag Filter for the Control of Dust Emissions for a Cement Plant
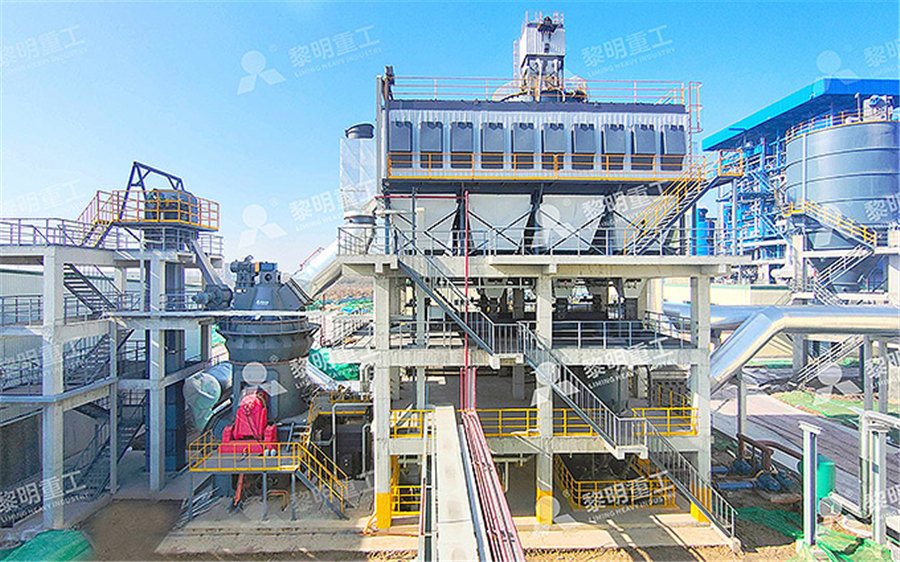
Dust Emission Monitoring in Cement Plant Mills: A Case Study
2021年8月28日 This paper presents aspects of monitoring material dust emissions from stationary emission sources (monthly dust measurements performed on cement mill stacks—mill outlet and separator outlet) Additionally, the Portland cement mill technological process (its component parts), as well as the solutions regarding the reduction of the air emissions level, An industrial cyclone dust collector or cyclone dust filter, industrial cyclone separator, dust collector cyclone separator, is one of the most important dust collection devices just like baghouse dust collector, ESP electrostatic precipitator in the cement production line It is mainly used in the raw material crushing and clinker production systems of cement plant to collect and remove Cyclone Dust Collector For Cement Plant Industrial Cyclone 2020年7月4日 Map Key 00 Limestone Quarry and Crushing plant 01 Limestone Stockpile 02 Additives Hopper 03 Additives Storage 04 Electrostatic Precipitators are used in cement plants particularly for removal of dust from the exit gases of cement kilns and from the exhaust air And has extensive experience in the design and BASIC CEMENT PLANT LAYOUT – Process Cement Forum The Cement 2015年9月1日 For a welldeveloped, efficient and feasible system, it is necessary to produce power generation enormously with a reduction in harmful emissions like Carbon dioxide (CO 2), Carbon monoxide (CO Design of cement plant waste heat recovery
.jpg)
Cement Dust Collectors Selection Dust Control
2020年11月13日 Dust is the main pollutant from the cement industry Many links in the cement production process, such as raw material crushing, raw meal grinding, clinker calcination, cement grinding, etc, have different degrees of 2023年6月15日 Here, we describe an integrated pilot plant for hightemperature flue gas dust removal and denitration, which was established on a 1000 MW coalfired unit of a power plant Based on the actual engineering flue gas test, the basic technical performance of the integrated pilot plant and the effect of synergistic removal of other pollutants were studiedIntegrated technology for dust removal and denitration of high Cement kiln dust was used successfully as a cover material instead of clay at a sanitary landfill located at a Californian cement plant (Crosby and others, 2000) In the early 1900s, cement plant employees began disposing of household waste at the company’s onsite landfillEverything you need to know about Cement Kiln Dust Generation 2012年4月30日 Cement is an essential component of infrastructure development It is also the most important input of construction industry, mainly in case of the government’s infrastructure and housing (PDF) Process Automation of Cement Plant ResearchGate
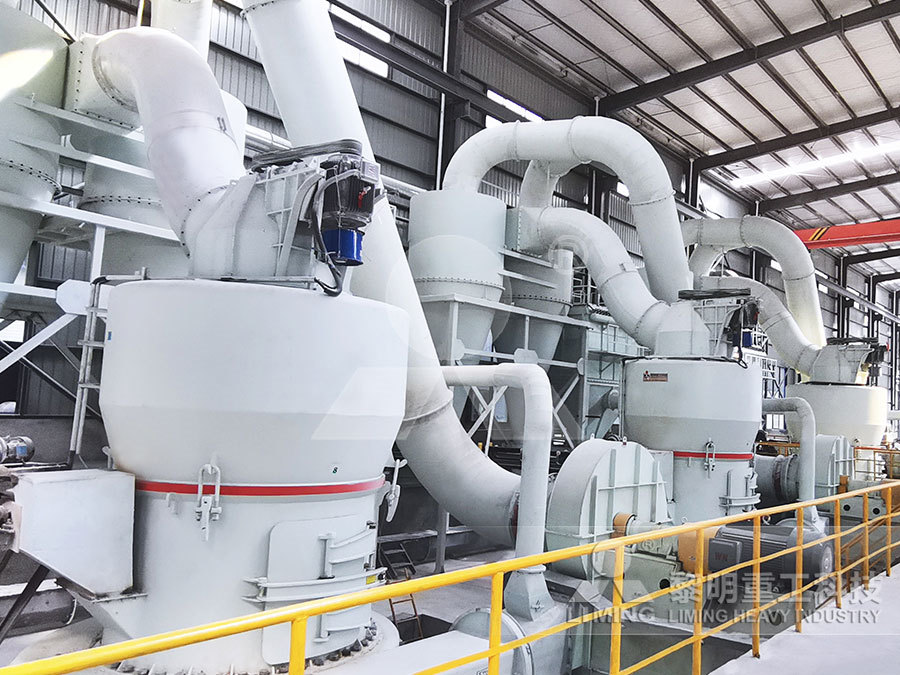
(PDF) Environmental Hazards of Limestone Mining and
2020年2月18日 It was found that water samples analysed from the vicinity of limestone quarry and cement plant showed an elevated levels of pH, EC, TDS, total hardness, alkalinity, calcium and sulphate PPC type baghouse dust collector is widely used in building materials, cement, metallurgy, machinery, chemical industry, and refractory industry, especially for dust collection system of cement plant crusher, cement packaging machine, warehouse top, clinker cooler, and various cement grinding machine (or dust removal system), it has a wide applicationBaghouse Dust Collector Pulsejet Dust Filter In Cement Plant2015年8月1日 Cement production, which is highly dependent on the availability of natural resources, will face severe resource constraints in the future This is especially true for the cement industry in China(PDF) Analysis of material flow and consumption in cement production 2021年6月3日 A large amount of dust is formed as one of the primary byproducts during the blast furnace ironmaking process Besides iron and carbon, it contains a variety of valuable metals such as zinc, lead, and indium widely applied in many industry fields However, it is difficult to recycle and reutilize blast furnace dust (BFD) due to complex composition, fine particle size, A Review on Recycling and Reutilization of Blast Furnace Dust as a
.jpg)
Everything you need to know about Crushers in Cement industry
The roller crusher is one possibility as secondary crushers another is the simultaneous drying (or partial drying) and reduction in an impact or hammer crusher The displayed crushing system is mainly used for mixtures of limestone with large portions of sticky clay System 6: Primary and Secondary Roller CrushersCement silo dust collector usually has the characteristics of multistage filtration, automatic dust removal, highefficiency dust removal, and low noise, which can effectively reduce dust and pollutant emissions in industrial production, and Cement Dust Collector Industrial Dust Removal 2021年10月22日 4) In the dust collector of secondary crushing and one or two screening units, a chain conveyor is set to transport powder, so that the dust discharged from dust collector does not enter the production system to cause secondary dust, and at the same time reduce the content of stone powder in aggregate productsConfiguration and design of 1000tph limestone aggregate production plantDesign Factors Dust Collecting in Cement Plant Silo System Aug 18, 2017 Keywords: cement silo,source of dust,dust collecting With the development of new dry cement production technology in the direction of large scale, Design Factors Dust Collecting in Cement Plant Silo
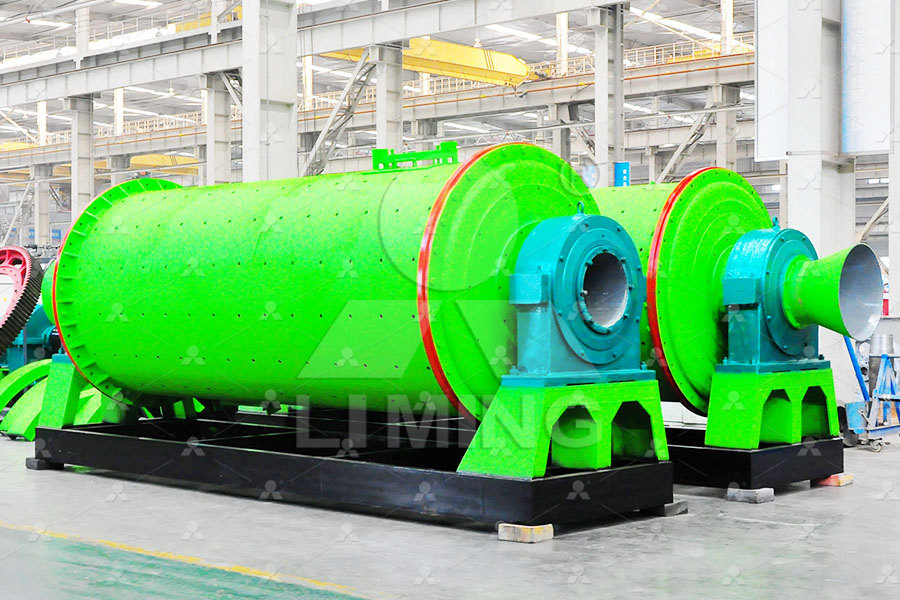
STANDARD TECHNICAL SPECIFICATION FOR RETROFIT OF WET LIMESTONE
214 Integration of FGD system with the power plant units 49 215 Liquidated damages (LD) 49 Section3: System Description and Scope 31 General description of wet limestone FGD system 50 311 Flue gas system 50 312 Absorber system 50 313 Limestone unloading, crushing storage system 年3月1日 In an EP system, dust resistivity is a critical factor in determining the effectiveness of this dust removal system [6] Improvement of cement plant dust emission by bag filter system ArticleApplication of ESP for gas cleaning in cement industry2024年7月4日 Ground cement is then transferred to silos for storage through conveyors, creating more high levels of dust, cement dust, cement dust exposure, and silica dust Step #5: Packaging Loading Packaging and loading stations with weighing devices are used in bagging, packing, and transferring the cement to trucks creating cement dust and cement dust exposureCement Dust Explosion Hazards, in Cement Manufacturing Industriesaddressing critial topics such as maintenance and plant reporting, alongside a detailed appendix with essential process calculations Contents Section A – Process summaries 1 Introduction 10 1 The basics of cement manufacture – 2 History of cement manufacture – 3 Portland cement in today’s world 2 Raw materials management system The Cement Plant Operations Handbook International Cement
.jpg)
MODIFIED CHUTE DESIGN FOR SLAG REMOVAL IN CEMENT
In cement industries they have a problem on removal of slag inside the chute The slag depositions formed inside of the chute sharpen edges In the mixing zone the additives like fly ash, clinker, gypsum, limestone, and additive slag feed by Portland cement, kiln, sulfur, sulfur dioxide, sulfur oxides, SO2, formation, control, technology ABSTRACT This report presents the chemical and physical factors governing the generation of sulfur dioxide (SO2), its transformation into other sulfur compounds, and the removal of sulfur oxides within the cement kiln systemFormation and Techniques for Control of Sulfur Dioxide and Other Deep decarbonisation of industry: The cement sector Cement sector overview Cement is the binding agent of concrete, the most widely used construction material in the world The cement sector is a major greenhouse gas emitter, responsible for about 7% of CO 2 emissions globally (1), and about 4% in the EUDeep decarbonisation of industry: The cement sector Europa2021年11月1日 Limestone calcined clay cement (LC 3) is one such recently developed ternary blended cement in which the alumina from the calcined clay and the carbonate from the limestone also react with each other, along with the traditional pozzolanic reaction of calcined clay and the filler effect of limestone, creating a synergy between the three primary components (clinker, Limestone calcined clay cement and concrete: A stateoftheart
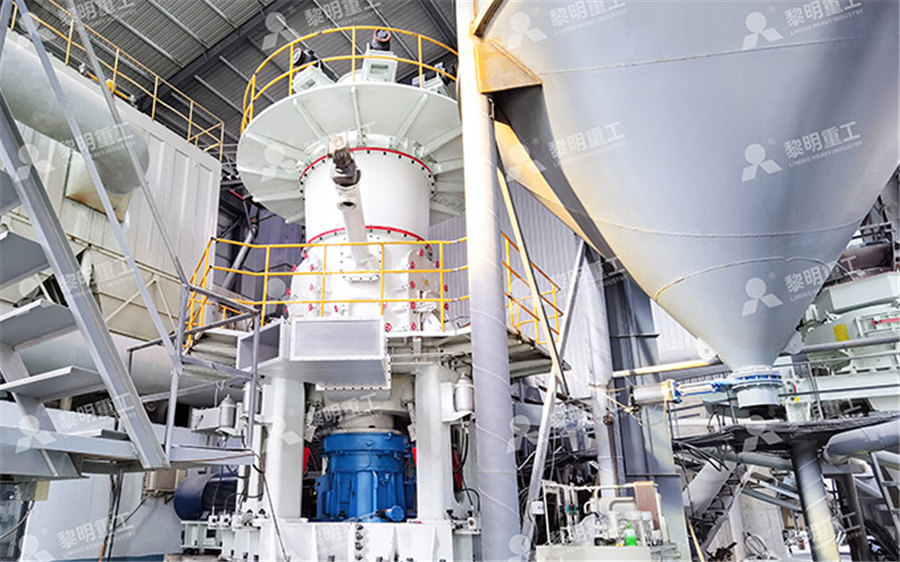
The Use of Limestone in Portland Cement: A State
2003年6月5日 Required water:cement ratio to achieve a slump of 60 to 70 mm in concretes made with different cements Cement E contained a limestone not conforming to the EN 1971 criteria2024年11月6日 The decarbonization of the concrete industry is an ongoing pursuit One solution towards this goal is the use of limestone powder in portland cement Waste eggshell has tremendous potential as an alternative calcite filler in cement due to its similarities with limestone In this research, the feasibility of adding 15% and 35% ground eggshell in portland cement to Assessment of waste eggshell powder as a limestone alternative 4) In the dust collector of secondary crushing and one or two screening units, a chain conveyor is set to transport powder, so that the dust discharged from dust collector does not enter the production system to cause secondary dust, and at the same time reduce the content of stone powder in aggregate productsConfiguration and design of 1000tph limestone aggregate production plantKakaras a,b a Chemical Process and Energy Resources Institute Centre for Research and Technology Hellas, 4th km NR PtolemaisKozani, 50200 Ptolemais, Greece Laboratory of Steam Boilers and Thermal Plants, National Technical University of Athens, 9 Heroon Polytechniou Street, 15780 Zografou, Greece c Titan Cement Company SA, Group RD and Quality Integration of calcium looping technology in existing cement plant
.jpg)
Flow diagram of the limestone scrubbing method
The results show that the dust removal efficiency is 2843–5130% when demisters are put into operation alone; the larger the inlet dust concentration of demisters is, the higher the dust The paper represents a case study regarding the conversion of ElectroStatic Precipitators (ESP`s) into Fabric Filters (FF) Seven cement production companies were established in Egypt during the period 1927 to 1980 and 6 new companies were established to cope with the increasing cement demand in 1980, s the cement production market share in Egypt indicate Design of Bag Filter for the Control of Dust Emissions for a Cement Plant2014年5月12日 During cement production process, part of the fuel can be burned in preheater, so it is necessary to supply additional air (tertiary air), which should be taken from the clinker cooler [1](PDF) Numerical calculation of tertiary air duct in the cement 2023年5月27日 The use of limestone powder to replace part of the cement clinker to produce Portland limestone cement (PLC) has become increasingly popular Portland limestone cement is popular for three reasons 1) When burning to form cement clinker, it consumes a lot of energy and releases a lot of carbon dioxide2 Major Roles of Limestone in Cement Manufacturing
.jpg)
(PDF) Optimization of accelerated weathering of limestone for
2024年3月7日 The plant costs were estimated and the costs per tonne of CO2 emissions avoided and per tonne of cement product determined View fulltext Last Updated: 13 Mar 2024