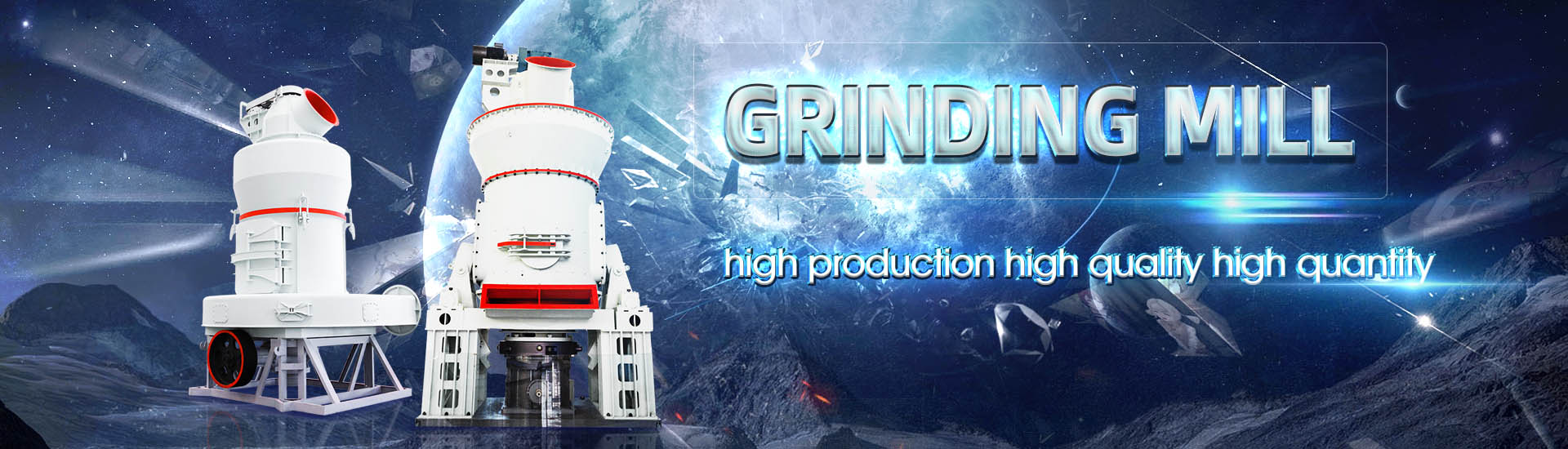
Sintered Ore Grinding Mill
.jpg)
Iron Ore Processing: From Extraction to Manufacturing
2024年4月26日 Grinding Mills: Grinding mills, such as ball mills and rod mills, are commonly used for grinding iron ore These mills contain grinding media (steel balls or rods) that tumble and impact the ore, causing it to break into 2017年3月24日 Sintering is a thermal agglomeration process that is applied to a mixture of iron ore fines, recycled ironmaking products, fluxes, slagforming agents, and solid fuel (coke) The Iron Ore Sintering: Process Taylor Francis Online2017年2月16日 Sintering is a thermal agglomeration process that is applied to a mixture of iron ore fines, recycled ironmaking products, fluxes, slagforming (PDF) Iron Ore Sintering: Process ResearchGate2023年7月20日 Ore grinding is a process to further reduce and disperse the ore particle size In the mineral processing industry, ore grinding is the particle size preparation before the Ore Grinding SpringerLink
制粉项目-2023.11.17.jpg)
Oreblending optimization model for sintering process based on
2012年3月1日 The oreblending optimization model, programmed by Access and Visual Basic, is applied to practical production in steel mills and the results prove that the present model can 2019年6月11日 According to the US Environmental Protection Agency, the sintering process converts finesized raw materials, including iron ore, coke breeze, limestone, mill scale, and flue dust, into an agglomerated product, Sintering: A Step Between Mining Iron Ore and 2022年1月1日 To operate viably and sustainably, there is a need to reduce costs and energy consumption, particularly of the energyintensive grinding required for lowgrade magnetite Comminution and classification technologies of iron ore2024年3月16日 The performance and yield of the sintered ore are affected by a variety of factors throughout the automated, continuous, multistation, multiinput, and multioutput sintering Application of deep learning in iron ore sintering process: a review
.jpg)
Recent advances in iron ore sintering Taylor Francis
2016年8月24日 Sintering is the most economic and widely used agglomeration process to prepare iron ore fines for blast furnace use Owing to the depleting reserves of traditional high grade iron ore, there have been considerable TowerMill is a vertical agitated media mill developed in Japan in the 1950s Until now, TowerMills have been used in ferrous and nonferrous mines for processes of ore grinding, flue gas desulfurization (FGD), limestone grinding for TowerMill industrial material preparation technology, 2017年9月1日 With the continual depletion of high grade simple ore bodies, more complex, finely disseminated ore bodies are being processed, which has led to an increase in the prevalence of fine grinding (Sinnott et al, 2006)This has been evident in the platinum group element (PGE) industry in South Africa, where the Bushveld Complex hosts 70% of global Fine grinding: How mill type affects particle shape characteristics 2017年9月1日 In this case, the ball mill, which produces more elongated particles, may be preferred over the stirred mill Differences in product shapes are attributed to the different grinding methods used in Fine grinding: How mill type affects particle shape characteristics
.jpg)
EFFECTS OF MILL ROTATIONAL SPEED ON THE BATCH GRINDING KINETICS OF
EFFECTS OF MILL ROTATIONAL SPEED ON THE BATCH GRINDING KINETICS OF A UG2 PLATINUM ORE By DINEO MOKGANYETJI MAKGOALE Submitted in accordance with the requirements for the degree of MAGISTER TECHNOLOGIAE in the subject ENGINEERING: CHEMICAL at the UNIVERSITY OF SOUTH AFRICA SUPERVISOR: Prof FRANCOIS 2023年7月10日 The present literature review explores the energyefficient ultrafine grinding of particles using stirred mills The review provides an overview of the different techniques for size reduction and the impact of energy requirements on the choice of stirred mills It also discusses the factors, including the design, operating parameters, and feed material properties, EnergyEfficient Advanced Ultrafine Grinding of Particles Using The Planetary Ball Mill PM 100 is a powerful benchtop model with a single grinding station and an easytouse counterweight which compensates masses up to 8 kg It allows for grinding up to 220 ml sample material per batchPlanetary Ball Mill PM 100 RETSCH highest fineness2016年10月28日 the mineralogical features in grinding of ironore products dusts and mill scale, Eisele and Kawatra, 2003), be sintered (mainly iron ore, but also the other materials such asIron Ore Sintering: Raw Materials and Granulation ResearchGate
.jpg)
Sintered aluminum oxide grinding ball LAARMANN Webshop
The high quality LAARMANN Sintered aluminum oxide grinding balls are usable for Planetary Ball Mills Aluminium oxide Aluminium oxide (British English) or aluminum oxide (American English) is a chemical compound of aluminium and oxygen with the chemical formula Al 2 O 3It is the most commonly occurring of several aluminium oxides, and specifically identified as aluminium(III) 2023年10月17日 3 Ultrafine Powder Grinding Mill Ultrafine powder mill (threering / fourring mediumspeed micropowder mill) feed particle size ≤25 mm, production capacity 0545 t/h, production fineness 1503500 mesh,it is a highefficiency and lowconsumption ultrafine powder processing equipment that successfully replaces the traditional jet mill and complex process How to choose a suitable ore powder grinding mill?Planetary Ball Mill BM 1400+ (4 Grinding Stations) charcoal, hair, catalysts, chemicals, alloys, bones, metal oxides, iron ore, ceramics, polymers, bentonites, pigments etc Zirconium Oxide, Tungsten Carbide Sintered Aluminum Oxide) The grinding jars are marked with capacity and materials are marked on the grinding jars, which is easy Versatile Planetary Ball Mill Upto 4 Grinding Stations2022年2月28日 Comparing dry and wet grinding curves in a ball mill in the same condition (an equal amount of materials and grinding media has been used on each pair of wetdry experiments) (Fig 17) indicated two significant differences at higher power values of wet grinding, specifically when speed exceeded 06 critical speed and for higher ω Pmax in the Grinding SpringerLink
.jpg)
Attrition Grinding Mill Design 911Metallurgist
2017年6月9日 As part of its mission to advance minerals technology, the Federal Bureau of Mines has conducted investigations to determine the feasibility of producing subsievesize material by an attrition grinding method The Bureaupatented technique involves the intense agitation of a slurry composed of the material to be ground, a granular grinding medium, and a The comminution of the material to be ground takes place through impact and friction between the grinding balls and the inside wall of the grinding bowl respectively the mortar The grinding can be performed dry or wet In addition to comminution Ball Mills are also the ideal and reliable lab assistants for mixing and homogenisingBall Mills – fritschThe Planetary Ball Mill PM 200 is a powerful benchtop model with 2 grinding stations for grinding jars with a nominal volume of 12 ml to 125 ml The extremely high centrifugal forces of Planetary Ball Mills result in very high pulverization Planetary Ball Mill PM 200 RETSCH laboratory China Vertical Shaft Impact Crusher (PCL1100) and China Make Mineral Ore Making Machine,Make Mineral Ore to Sand of metallurgy slag, especially carborundum, sintered » Free Online Chat Ma’aden Magnesite Project – Scribd Vertical Shaft Kiln A Vertical Shaft Kiln is utilized for the production of sintered or deadvertical shaft for sintered ore – Grinding Mill China
.jpg)
(PDF) Grinding Media in Ball MillsA Review ResearchGate
2023年4月23日 grinding media in a grinding mill with about 2630 wt% chrome by Chen et al [37] using a phosphate ore in a modified ball laboratory ball mill whose electrochemical potential could be controlledAfter cooling, the sintered pellets are screened on a rotary screen and the under sized pellets below 6 mm are recycled to the grinding mill Sintered pellets of +6 mm size are tran sported and stored in a shed for smelting trials The chemical composition of sintered pellets and their crushing strength is given in Table2 4USE OF SINTERED PELLETS IN PRODUCTION OF HIGH CARBON FERRO 2024年11月21日 The grinding and grading stage of lithium ore is to ensure that lithium minerals are fully dissociated from gangue mineral monomers Therefore, lithium ore extraction is inseparable from ore grinding, and the common equipment for lithium ore grinding is ball mill Onestage closedcircuit grinding and grading process can be adopted, and the onestage Ball Mill Is Indispensable For Lithium Ore Processing2014年10月1日 In a test performed in the Loesche test center in Germany, copper slag grinding saved 229% energy in an airswept model and 344% energy in an overflow model [13,14]Copper Ore Grinding in a Mobile Vertical Roller Mill Pilot Plant
.jpg)
Energy Use of Fine Grinding in Mineral Processing
2013年12月18日 Fine grinding, to P80 sizes as low as 7 μm, is becoming increasingly important as mines treat ores with smaller liberation sizes This grinding is typically done using stirred mills such as the Isamill or Stirred Media Detritor While fine grinding consumes less energy than primary grinding, it can still account for a substantial part of a mill’s energy budget Overall A crushing plant delivered ore to a wet grinding mill for further size reduction The size of crushed ore (F 80) was 40 mm and the SG 28 t/m 3 The work index of the ore was determined as 122 kWh/t A wet ball mill 1 m × 1 m was chosen to grind the ore down to 200 micronsGrinding Mill an overview ScienceDirect TopicsTable 1: Power Intensity of Different Grinding Devices Ball Mill is a 56m D x 64m L @ 26MW Tower Mill is a 25m D x 25m L @ 520KW Table 2: Mill Comparison of Media Size, Power Intensity, number of grinding media The ability to use smaller media is probably the dominant impact on grinding efficiency ItFine Grinding as Enabling Technology – The IsaMillEffect of mill type on ore grinding performance Ball mills are widely used in the mining and metallurgical industries for the grinding of ores and other materials There are a wide variety of mill types available, each with its own advantages and disadvantages The Factors affecting ores grinding performance in ball mills
.jpg)
(PDF) LEARNING FROM OTHER INDUSTRIES; WHY THE
2019年4月16日 Conference: Applying a Successful Technology from the Cement Industry: Advantages of Grinding Ore in a VerticalRollerMill; At: Antalya, Türkey2021年11月8日 Illite ore industrial grinding mill machines include ultrafine grinding mills, vertical roller mills, highpressure mills, wet stirring mills, coarse mills, and so on It can be applied to different illite grinding operation requirements and meet Illite Ore Industrial Grinding Mill Machine SBM Ultrafine 2018年11月25日 Based on further studies as well as initial studies, the equation which has been proposed for calculating the optimum moisture (W) as a function of the nature, composition and granulometry of the iron ore is W = 228 + 0427 L + 0810 A – 0339S + 0104D + 0036 E where L is the ore weight loss during heating in grams, A is % Al2O3 in ore, S is % SiO2 in ore, D is Theory and Practice of Sintering of Iron ore – IspatGuru2008年5月1日 Illustration ora laboratory jet mill system (Selshin Enter prise, 1991) Fine grinding of brittle minerals and materials by jet mill
.jpg)
Planetary Ball Mill Torontech
When the planetary ball mill is initiated, the motor propels the central sun wheel into motion, and the grinding jars, situated on the sun wheel, revolve about their individual axes The direction of the sun wheel's motion is opposite to that of the grinding jars in a 1:2 ratio2013年4月16日 ABSTRACT In this study, ultrafine grinding of a refractory silver ore tailings was studied A laboratory scale pintype vertical stirred mill and ceramic beads were employed for the grinding testsInvestigation of some parameters affecting the Ultrafine grinding 1 Grindability: The grindability of the ore affects the efficiency of the grinding mill Harder ores require more energy and longer grinding times, which can impact the mill's performance and operational costs 2 Media andliner Wear: The condition of the grinding media and liners affects the mill's efficiencyUnderstanding the operation of grinding mills in the mining and Rod Mill The rod mill is loaded with steel bars as grinding media and comprises five parts: cylinder shell, feeding system, discharge system, main bearing, and transmission system It is suitable for both dry and wet grinding to meet customer needs Materials with a Moh's Hardness of 5512 can all be handled by our millOre Grinding Mill
.jpg)
Modeling and application of stirred mill for the coarse grinding
2022年5月23日 Grinding experiments were conducted in a laboratoryscale stirred mill on a lowgrade PGE bearing chromite ore HighPressure Grinding Rolls (HPGR) product of −1 mm was used as feed material to 2024年6月11日 In this study, the evolution behavior of the particle size distribution during the grinding process was examined with fractal theory According to the distribution index k of the Rosin–Rammler–Benne model, the Effect of Solid Concentration on Particle Size Request PDF On Mar 15, 2015, Mathis Reichert and others published Research of iron ore grinding in a verticalrollermill Find, read and cite all the research you need on ResearchGateResearch of iron ore grinding in a verticalrollermill1983年6月1日 The relationship between the grinding characteristics of polymetallic complex ore and its component minerals, pyrrhotite, sphalerite, and quartz, under the action of abrasion was studied, based on Breakage characteristics for ores for ball mill modelling
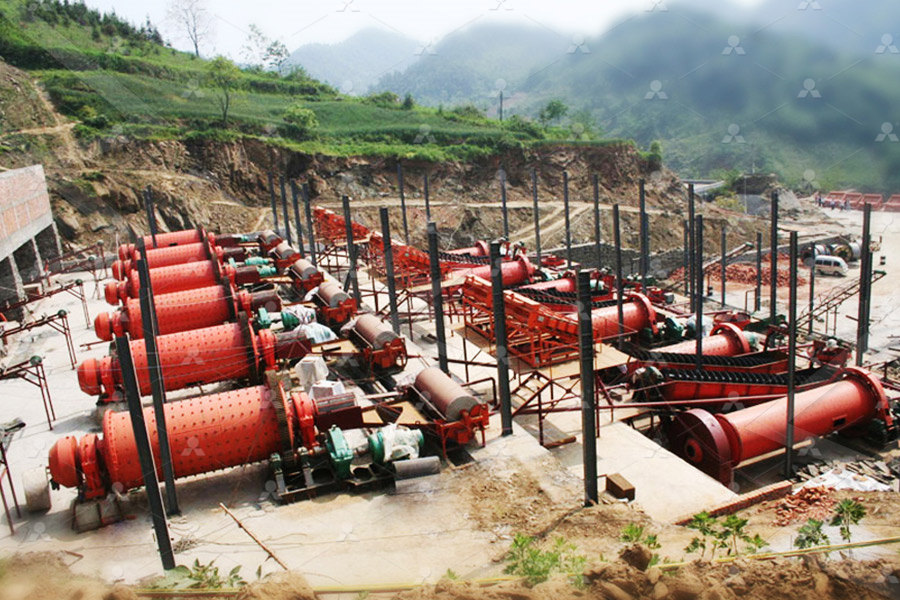
Different Effects of Wet and Dry Grinding on the Activation of Iron Ore
2021年1月1日 Compared to traditional drymilling, wet grinding shows higher efficiency and can avoid dust generation Since most of IOTs are directly discharged into the river or exposed to rainwater, wet A Review of the Grinding Media in Ball Mills for Mineral Processing, 2023 The ball mill is a rotating cylindrical vessel with grinding media inside, which is responsible for breaking the ore particles Grinding media play an important role in the comminution of mineral ores in these millsBallmill grinding kinetics of master alloys for steel powder Experimental study of clinker grinding in a ball mill and the behavior of the grinding media inside the equipment using DEM Amanda Aparecida de Lima Santos1 Amanda Cristina Gomes Machado1 Suellen Mendonça Nascimento1 Received: 7 March 2022 / Revised: 17 June 2022 / Accepted: 4 August 2022 / Published online: 18 August 2022Experimental study of clinker grinding in a ball mill and the 2015年7月29日 As you increase the volume of the through put, the time that the ore has to react to the grinding media is lessened As you add ore to the mill you are also adding WATER and changing density which affects the slurry rheology and workings of the grinding action inside that mill This water is one of the main controls that you have over your grindEffect of Water Density on Grinding Mill 911Metallurgist
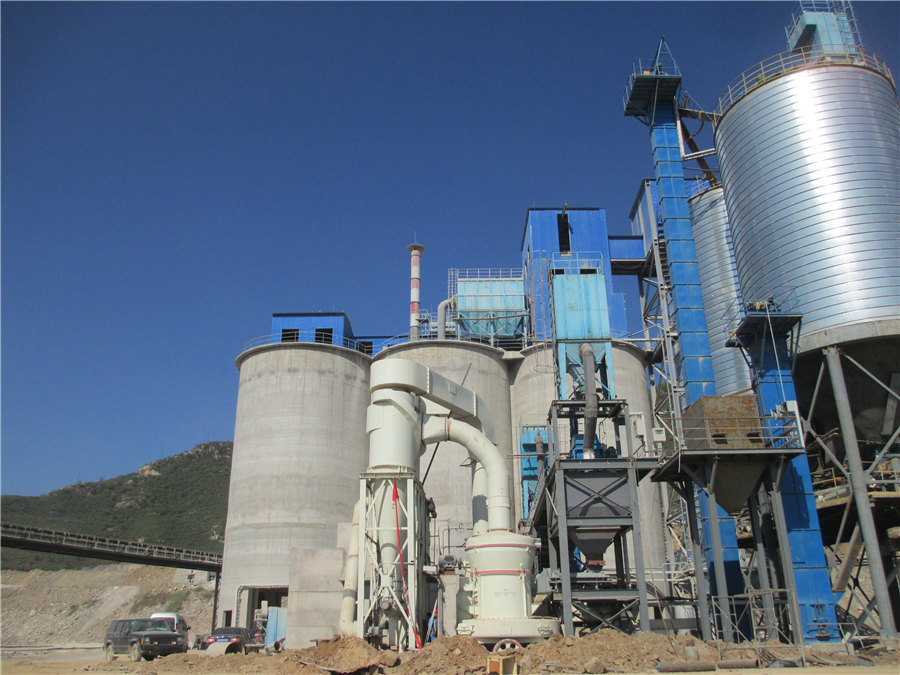
Lump premium may head into negative territory as iron ore fines
2020年8月19日 An enduse source in Shanxi province said they ground a small amount of PBL into fines due to a preference for sintered ore "We have the grinding facility at mill site and the cost is only around Yuan 67/wmt, but we have yet to Refractory Gold Ores S Ellis Kalgoorlie Consolidated Gold Mines Kalgoorlie, WA Abstract Since early 2001, Kalgoorlie Consolidated Gold Mines (KCGM) has successfully operated an ultra fine grinding (UFG) circuit to supplement its roaster capacity for the treatment of the refractory gold flotation concentrate A second UFG mill was installed inUltra Fine Grinding A Practical Alternative to Oxidative